Оглавление:
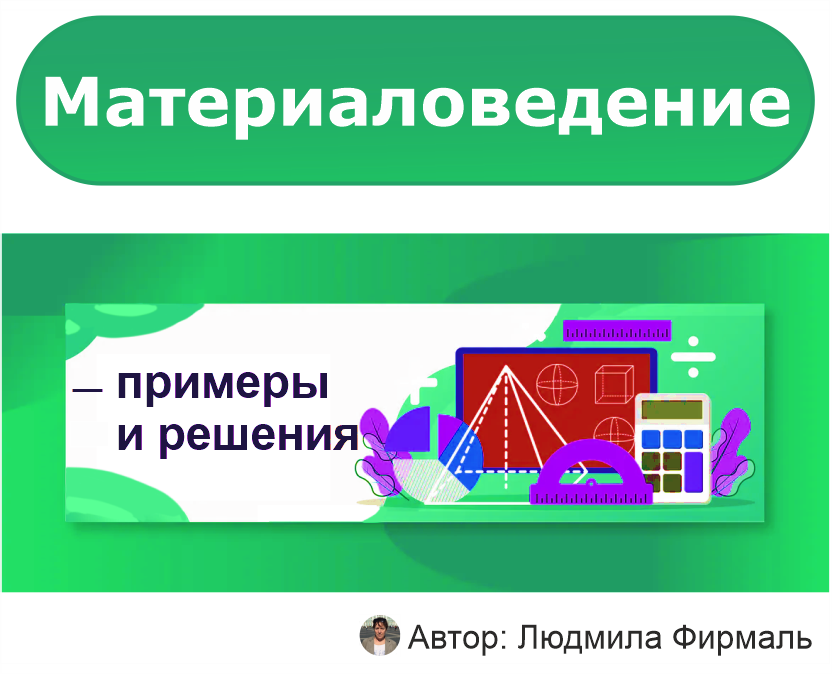
Прежде чем изучать примеры решения задач, нужно знать теорию, поэтому для вас я подготовила краткий курс теории вместе с примерами решения.
Эта страница подготовлена для студентов любых специальностей и охватывает полностью предмет «материаловедение».
Если что-то непонятно — вы всегда можете написать мне в WhatsApp и я вам помогу! |
Введение в материаловедение
Материаловедение относится к числу основополагающих учебных дисциплин для специальностей машиностроительного профиля. Это связано, прежде всего, с тем, что получение, разработка новых материалов, способы их обработки являются основой современного производства.
Проектирование рациональных и конкурентоспособных изделий, организация их производства невозможны без достаточного уровня знаний в области материаловедения, которые являются важнейшим показателем образованности современного дипломированного специалиста. Кроме того, материаловедение служит базой для изучения многих специальных дисциплин.
Материаловедение — это наука, изучающая связь между составом, строением и свойствами материалов, а также их изменения при различных внешних воздействиях (тепловом, механическом, химическом и т.д.). Основная практическая задача материаловедения — изыскание оптимального состава и способа обработки материалов для придания им заданных свойств.
При чтении лекций и при выполнении задач и домашнего задания предусматривается использование этой статьи.
Изучив дисциплину «Материаловедение», студент должен знать:
- основные свойства материалов, обеспечивающие качество технологических процессов и изделий машиностроения, в том числе свойства специальных сплавов (коррозионно-стойких, жаростойких и жаропрочных сплавов, а также инструментальных материалов);
- основные типы кристаллических решеток и их дефектов, структуру сплавов, общие закономерности диаграмм фазового равновесия и диаграмму «Железо — цементит»;
- классификацию металлов, сплавов и неметаллических материалов.
Студент должен владеть:
- методами определения оптимальных и рациональных режимов термообработки, упрочнения материалов;
- методами анализа причин возникновения дефектов в материалах;
- методами проведения стандартных испытаний по определению показателей физико-химических свойств используемых материалов и готовых изделий;
- методами определения качества и состояния сплавов на основании анализа их структуры.
Возможно эта страница вам будет полезна:
Предмет материаловедение |
Примеры решения задач на «анализ двойных диаграмм»
К выполнению домашнего задания предъявляются следующие требования:
- домашнее задание выполняется на формате А4 в печатном виде;
- титульный лист;
- на первой странице указываются номер задания и через тире буквенный индекс варианта, помещается текст содержания задания с указанием названия диаграммы, химического состава заданного сплава и температуры;
- на второй странице слева вычерчивается в масштабе диаграмма так, чтобы справа было место для изображения кривой охлаждения. Для построения кривой охлаждения заданного в варианте сплава необходимо на оси концентраций найти точку, соответствующую составу сплава. Из этой точки восстановить ординату заданного сплава так, чтобы она охватывала диапазон температур от оси концентраций до области жидкого состояния. Ордината сплава должна отчетливо выделяться на диаграмме. Точки пересечения ординаты с линиями диаграммы являются критическими точками заданного сплава (температурами начала или окончания фазовых превращений). Правее диаграммы необходимо вычертить оси «Температура -Время» для построения кривой охлаждения. На ось ординат следует также нанести критические точки заданного сплава в градусах Цельсия;
- на последующих страницах необходимо произвести общее описание заданной диаграммы, описание процесса кристаллизации, указанного в варианте сплава, и определить состав и количество фаз на 1 килограмм сплава.
Цели и задачи изучения диаграмм состояния
Диаграмма состояния представляет собой графическое изображение зависимости температур фазовых превращений в сплавах от их состава.
Цель изучения диаграмм состояния сплавов:
- научиться по диаграмме состояния устанавливать, какие процессы происходят в сплавах при их охлаждении, какие при этом образуются фазы и структуры сплавов разного состава;
- научиться анализировать процессы фазовых превращений в зависимости от изменения температуры сплава;
- выявлять взаимосвязь механических и технологических свойств сплавов от соответствующего фазового и структурного состояния.
По диаграммам состояния можно устанавливать не только температуры фазовых превращений в сплавах любого состава, но и качество и количество фаз в разных областях диаграммы состояния.
Однако этим не исчерпывается практическая значимость диаграмм состояния сплавов. В частности, разбирая процессы, происходящие при охлаждении сплава, по диаграмме состояния можно выявить, в какой форме проявляются образующиеся фазы при охлаждении сплава.
Фазой называется однородная часть системы, образованная компонентами сплава, которая во всех своих точках имеет одинаковые составы, строение и свойства. Жидкая фаза представляет собой раствор расплавленных компонентов.
Твердые фазы являются зернами, имеющими определенную форму, размер, состав, структуру и свойства. Это могут быть твердые растворы, химические соединения, зерна чистых компонентов, не образующих с другими компонентами ни твёрдых растворов, ни химических соединений.
Форма проявления фаз называется структурой сплава. Возможность по диаграмме состояния прогнозировать структуру, образующуюся из сплавов разного состава, имеет очень большое практическое значение, так как в двухфазных сплавах не фазы, а именно структуры сплавов определяют их механические свойства. Так, например, стали и белые чугуны состоят из одних и тех же фаз, но свойства этих сплавов сильно различаются именно потому, что структуры этих сплавов разные.
Имеются тысячи разработанных диаграмм состояния сплавов. Все их выучить механически невозможно. Поэтому специалист должен уметь мысленно представить те процессы, которые происходят в сплавах и образуют их структуру и свойства, чтобы оптимально воздействовать на технологический процесс.
Для этого необходимо:
- ясное понимание особенностей строения основных фаз в сплавах, которыми являются твердые растворы, химические соединения, чистые компоненты;
- знание, как эти фазы обозначаются;
- знание признаков этих фаз;
- умение по диаграмме состояния определить состав и количество фаз;
- умение логически мыслить.
Для выработки навыка разбора процессов, происходящих при охлаждении конкретного сплава, необходимо обязательно выполнение следующих действий: строить кривую охлаждения разбираемого сплава; против участков кривой охлаждения схематично изображать состояние фаз (структуру) сплава; письменно объяснять процесс, происходящий в сплаве при рассматриваемых температурных условиях.
Правило фаз
При рассмотрении процессов превращения в диаграммах равновесного состояния сплавов широко применяется так называемое «правило фаз», дающее возможность проверить правильность построения диаграмм и теоретически обосновать направление протекания процессов превращения для установления равновесного состояния системы, которое определяется следующими переменными факторами: температурой, давлением и составом фаз системы (концентрацией).
Число переменных величин (концентрация фаз, температура, давление), которые могут изменяться независимо друг от друга, называется числом степеней свободы или вариантностью системы.
Число степеней свободы зависит от количества компонентов, числа фаз в системе и переменных внешних условий — температуры и давления. Так как давление в практических условиях изменяется в небольших пределах, не оказывая существенного влияния на процессы превращения, то основным переменным фактором является только температура и тогда уравнение «правила фаз» имеет вид

где — число степеней свободы (вариантность системы),
— число компонентов в системе,
— количество фаз, находящихся в равновесии при рассматриваемых условиях.
Если число степеней свободы системы равно нулю (), то такое равновесие называют нонвариантным (безвариантным). Это означает, что сплав с данным числом фаз может существовать только при определенных условиях: при постоянной температуре и определенной концентрации всех находящихся в равновесии фаз. Если
, то такая система называется моновариантной (одновариантной), т. е. чтобы не нарушилось равновесное состояние фаз, можно изменить либо концентрацию фаз, либо температуру. Когда
, система бивариантна (двухвариантна). Наличие одной или двух степеней свободы позволяет изменять одну или две переменных без изменения числа фаз.
Правило отрезков
При анализе строения и свойств сплавов рассматривается состав фаз и их количественное соотношение. Для определения количества фаз и их концентрации в любой точке двухфазной области диаграммы состояния сплавов служит «правило отрезков (рычага)».
На рис. 2.1 приведена диаграмма состояния сплавов с неограниченной растворимостью в твердом состоянии. При температуре сплав состоит из
-твёрдого раствора и жидкой фазы. Для определения массового или объемного соотношения фаз и их состава для сплава
при температуре
проводим через данный температурный уровень горизонтальную линию (коноду) до пересечения с ближайшими линиями диаграммы
и
, ограничивающими двухфазную область. Проекции точек пересечения
спроектированные на ось концентрации
показывают состав (концентрацию) фаз: жидкая содержит
, твердая —
.
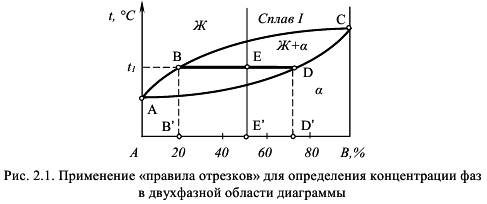
Отрезки, лежащие на температурной горизонтали (коноде) между точками концентрации фаз и средней точкой, соответствующей концентрации исходного сплава
обратно пропорциональны количеству этих фаз:

Иными словами, количество фазы, например жидкости, характеризуется величиной противолежащего отрезка , а количество кристаллов
-твёрдого раствора — величиной противолежащего отрезка
С помощью правила отрезков можно определить не только фазовый состав сплава, но и количественное соотношение структурных составляющих, например избыточных кристаллов и эвтектики.
Для определения количественного соотношения фаз:

Для определения веса фаз на 1 килограмм сплава:

Общий обзор диаграмм состояния
Как известно, вид диаграммы состояния зависит от характера взаимодействия компонентов в жидком и твердом состояниях, возможности образования устойчивых и неустойчивых химических соединений, протекания тех или иных нонвариантных превращений. Различные варианты простейших (или типовых) диаграмм состояний как диаграмм равновесия систем безымянных компонентов и
приведены ниже.
Диаграмма состояния для сплавов, образующих смеси из чистых компонентов
Общий вид диаграммы для случая, когда оба компонента сплава в жидком состоянии неограниченно растворимы, а в твердом — не растворяются, не образуют химических соединений и не имеют полиморфных превращений, представлен на рис. 2.2а. Фазы: жидкость — , чистые компоненты
и
. Линия
— линия ликвидус; линия
— линия солидус. На линии АС начинают выделяться кристаллы
; на линии
— кристаллы
; на линии
из жидкости концентрации С одновременно выделяются кристаллы
и
. Эвтектическая смесь двух видов кристаллов, одновременно кристаллизующихся из жидкости, называется эвтектикой.
Диаграмма состояния для сплавов с неограниченной растворимостью в твердом состоянии.
На рис. 2.26 приведена диаграмма состояния для сплавов с неограниченной растворимостью компонентов друг в друге в жидком и твердом состоянии, имеющих одинаковые типы решеток, небольшую разницу атомных радиусов (до ) и сходное строение наружных электронных оболочек, т. е. близость химической природы металлов.
Линия — линия ликвидус; линия
— линия солидус; фаза а представляет собой неограниченный твёрдый раствор замещения компонентов
и
, зерна этой фазы имеют единую кристаллическую решетку, но у сплавов разного состава число атомов компонентов
и
в элементарных ячейках решетки различно.
Диаграмма состояния для сплавов с ограниченной растворимостью в твердом состоянии, с эвтектикой.
На рис. 2.2в приведена диаграмма состояния для сплавов с ограниченной растворимостью компонентов друг в друге в твердом состоянии, с эвтектическим превращением. Ограниченные твердые растворы на основе компонентов и
образуются, когда последние заметно отличаются строением и размером атомов, кристаллической структурой и физико-механическими свойствами. Ограниченные твердые растворы могут образовываться по типу замещения и внедрения.
Линия — линия ликвидус; линия
— линия солидус; фаза а является твердым раствором компонента
в кристаллической решетке компонента
; фаза
представляет собой твёрдый раствор компонента
в кристаллической решетке компонента
. Кривые
и
— линии ограниченной растворимости в твердом состоянии (сольвус), отражающие характер изменения растворимости компонентов друг в друге в зависимости от температуры. Растворимость компонента
в компоненте
уменьшается с понижением температуры (линия
). Растворимость компонента
в компоненте
не зависит от температуры (линия
).
— линия эвтектического превращения
. Смесь получившихся в результате данной реакции ограниченных твёрдых растворов
и
называется эвтектической (эвтектикой). Сплавы, расположенные между точкой максимальной растворимости
и эвтектической точкой
, называют доэвтектическими, а сплавы, расположенные между
и
, — заэвтектическими.
Диаграмма состояния для сплавов с ограниченной растворимостью в твердом состоянии, с перитектикой.
На рис. 2.2г показана диаграмма состояния для сплавов с ограниченной растворимостью в твердом состояния с перитектическим превращением. Диаграммы такого типа образуют металлы с небольшой разницей в строении атомов и их размеров, но заметно отличающиеся друг от друга температурами плавления.
Линия — линия ликвидус; линия
— линия солидус; линия
— линия перитектического превращения, которое заключается в том, что жидкость реагирует с ранее выпавшими кристаллами
и образует новый вид кристаллов
. Структура двухфазного сплава представляет собой смесь, в которой фаза, выделившаяся ранее (
-фаза), окружена фазой, выделившейся позднее (
-фаза).
Диаграмма состояния для сплавов, образующих химические соединения
Такая диаграмма получается (рис. 2.2д), когда сплавляемые компоненты образуют устойчивое химическое соединение , не диссоциирующее при нагреве вплоть до температуры плавления и образующее промежуточную фазу постоянного состава. Химическое соединение считается устойчивым, если оно плавится без разложения.
При концентрации, соответствующей химическому соединению , отмечается характерный перелом на кривой свойств. Это объясняется тем, что некоторые свойства химических соединений обычно резко отличаются от свойств образующих их компонентов. Обычно такие диаграммы состояния характерны для систем, образованных металлами и элементами, которые обладают и металлическими, и неметаллическими свойствами.
В ряде диаграмм состояния сплавов, образующих химические соединения (рис. 2.2е), могут возникать промежуточные фазы переменного состава (-фаза), имеющие сравнительно широкие области существования. Эти фазы представляют собой твердые растворы замещения или внедрения в кристаллической решетке химического соединения. Для этих фаз обычно характерны свои кристаллические решетки, отличные от кристаллических решеток компонентов.
Помимо устойчивых химических соединений, которые плавятся (кристаллизуются) при постоянной температуре, в диаграммах могут образовываться и неустойчивые химические соединения, распад которых происходит, не доходя до температуры плавления.
Диаграмма состояния для сплавов с полиморфным превращением одного из компонентов. Полиморфизм (греч.) — многоформие, способность веществ иметь различную кристаллическую структуру в зависимости от внешних условий — температуры и давления.

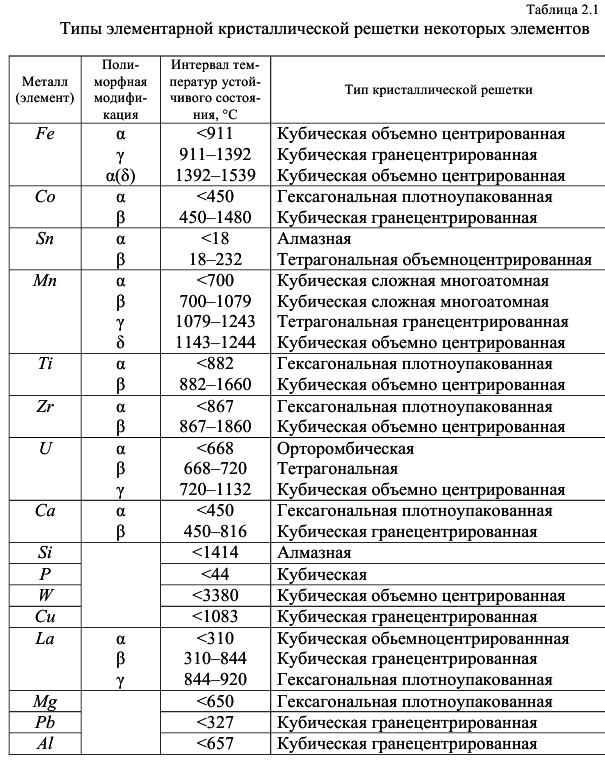
При полиморфическом превращении изменяется не только форма элементарной ячейки, но и характер и свойства кристаллов.
Полиморфизмом обладают многие металлы ( и др.), неметаллы (
и др.) и промежуточные фазы (
и др.). Разные полиморфные модификации обозначаются буквами греческого алфавита —
,
,
и т. д. На диаграмме состояния каждая полиморфная модификация имеет свою область существования и образующиеся твердые растворы на их основе отделены друг от друга двухфазными областями.
В табл. 2.1 приведены типы элементарной кристаллической решетки и температурные инервалы их существования для некоторых металлов и неметаллов.
Простейшая диаграмма состояния системы с рядом у-твёрдых растворов между высокотемпературной модификацией компонента и компонентом
показана на рис. 2.2ж. Линии
и
— линии начала и конца полиморфного превращения
. В сплавах участка
—
подобное превращение до конца не доходит и при комнатной температуре они сохраняют двухфазную структуру
Сплавы, лежащие правее точки
, полиморфного превращения не испытывают и при всех температурах ниже солидуса имеют структуру
-раствора.
Диаграмма состояния сплавов с полиморфными превращениями компонентов и эвтектоидным превращением
Диаграмма состояния сплавов, у которых высокотемпературные модификации компонентов обладают полной взаимной растворимостью, а низкотемпературные
— ограничены, приведена на рис. 2.2з.
По аналогии с линией эвтектического превращения и эвтектической точкой
на рис. 2.2в линию
называют линией эвтектоидного превращения, a
— эвтектоидной точкой. Смесь кристаллов ограниченных растворов
(на основе низкотемпературной модификации полиморфного компонента
) и
(на основе низкотемпературной модификации полиморфного компонента
), которая образуется в твердом состоянии по реакции
получила название эвтектоида.
Сплавы, расположенные левее эвтектоидной точки , называют доэв-тектоидными, а сплавы, расположенные правее
, — заэвтектоидными.
Возможно эта страница вам будет полезна:
Методические указания по материаловедению |
Описание диаграммы состояния
Диаграммы состояния систем конкретных компонентов (например, «Железо — углерод», «Медь — алюминий» и др.) редко являются простейшими (типовыми) диаграммами. Они, как правило, являются сложными (комбинированными) диаграммами, в строении которых нужно уметь выделить простейшие (типовые) части их.
На рис. 2.3 приведена сводная таблица так называемых геометрических образов различных превращений, т.е. показано расположение линий диаграмм, характерное для различных случаев взаимодействия компонентов и фаз.
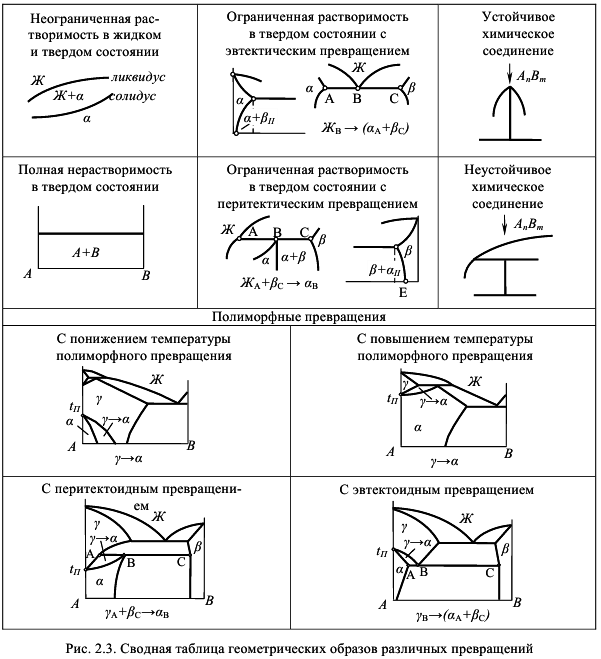
В этом подразделе задания студент, изучив простейшие (типовые) диаграммы состояния (рис. 2.2) и ориентируясь по сводной таблице геометрических образов (рис. 2.3), должен дать общий анализ заданной диаграммы состояния, т. е. ответить на следующие вопросы:
- Растворяются ли компоненты в жидком состоянии и как (ограниченно или неограниченно)?
- Растворяются компоненты в твердом состоянии, образуя ограниченные или неограниченные твердые растворы, или не растворяются, образуя смеси чистых компонентов, химических соединений и т.п.? Если образуются твердые растворы, то нужно их перечислить.
- Образуют ли компоненты устойчивые или неустойчивые химические соединения? Если образуют, то нужно перечислить их формулы и химические составы.
- Перечислить все нонвариантные превращения, протекающие в заданной системе (эвтектические, эвтектоидные, перитектические, перитек-тоидные и др.), дать при этом словесное описание сути этих превращений, написать их уравнения, указать температуру и химические составы участвующих фаз.
Возможно эта страница вам будет полезна:
Учебник по материаловедению |
Построение кривой охлаждения заданного сплава и описание процесса кристаллизации
Сначала необходимо указать, до какой температуры сплав охлаждается, находясь в жидком состоянии (точка ликвидус), и на графике в координатах «Температура — Время» от любой точки, расположенной на оси ординат выше точки ликвидус, провести до нее круто падающую кривую. Это будет первый участок кривой охлаждения.
Затем для каждого температурного интервала, образованного критическими точками, а также для интервала под нижней критической точкой:
- описать процесс кристаллизации, который начинается при достижении сплавом данной критической точки;
- пользуясь правилом фаз, установить, идёт ли описываемый процесс в интервале температур или при постоянной температуре;
- на кривой охлаждения изобразить новый ее участок в рассматриваемом интервале температур, идущий под другим углом, нежели предыдущий, если процесс идёт при изменении температуры, или изобразить горизонтальную площадку, если процесс идёт при постоянной температуре;
- написать уравнение рассматриваемого процесса;
- описать структуру, которая сформировалась в сплаве к моменту окончания рассматриваемого процесса.
После рассмотрения последнего температурного интервала (под нижней критической точкой) ответ на этот пункт задания следует завершить описанием структуры сплава, сформировавшейся к моменту окончания последнего превращения.
Для правильного описания процесса кристаллизации заданного сплава надо, опираясь на знание типовых диаграмм и ориентируясь по таблице геометрических образов (рис. 2.3), правильно установить, каким фазовым превращениям соответствуют линии диаграммы, пересекаемые ординатой заданного сплава.
Применяя «правило фаз» (2.1) определить можно ли менять внешний фактор, не нарушая равновесие фаз. При — нонвариантная система и, следовательно, чтобы сохранить равновесие фаз, охлаждать сплав нельзя, процесс идёт при постоянной температуре (на кривой охлаждения — горизонтальная площадка) и при строго определенных (единственных) концентрациях фаз, участвующих в этом процессе.
Если число степеней свободы (моновариантная система) или
(бива-риантная система), то процесс идёт в интервале температур и на кривой охлаждения началу данного процесса соответствует точка перегиба (изменение наклона кривой).
Первичной кристаллизации (образования твёрдых фаз из жидкого состояния) соответствуют три типовые кривые охлаждения (рис. 2.4, 2.5,2.6).
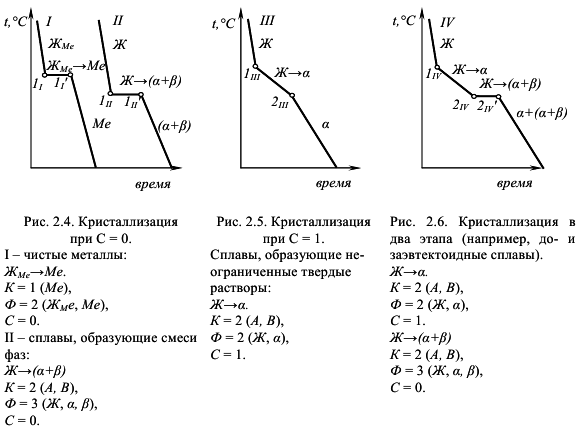
Точки 1 соответствуют началу кристаллизации. Выше этих точек сплавы охлаждаются по физическим законам (без тепловых эффектов). Площадки обусловлены выделением скрытой теплоты кристаллизации, которая уравновешивает отвод тепла от системы.
Охлаждение в интервалах и
также сопровождается выделением теплоты, которой не хватает для сбалансирования отведенного от системы тепла. Поэтому в точках
и
наблюдается перегиб в сторону замедления охлаждения. Точки 2 соответствуют окончанию процесса первичной кристаллизации.
Дальнейшее охлаждение чистых металлов идёт по физическим законам. Также охлаждаются сплавы, состоящие из компонентов, нераство-ряющихся друг в друге в твердом состоянии. Большинство других сплавов по мере охлаждения претерпевают фазовую перекристаллизация, образуя смеси фаз или вторичные выделения.
Вопрос о возможности вторичных выделений решается легко. Если линии диаграммы, показывающие состав охлаждающихся твёрдых фаз, наклонны (состав их фаз изменяется с падением температуры), то в сплаве образуются вторичные выделения. Надо правильно решить вопрос о том, какие именно вторичные фазы выделяются. Вторичные выделения сопровождаются тепловым эффектом, поэтому на кривой охлаждения температуре начала выделения вторичных кристаллов соответствует перегиб.
Если линии диаграммы, показывающие состав охлаждающихся твёрдых фаз, вертикальны (состав фаз не изменяется с падением температуры), то вторичных выделений в сплаве не происходит.
При определении структуры сплава, сформировавшейся к моменту достижения конца данного температурного интервала, а также окончательной структуры сплава, образовавшейся после последнего превращения, нужно четко отличить структурный состав (структуру) сплава от фазового состава.
- Фазами, как известно, называют однородные части системы, имеющие одинаковый состав, строение, свойства и отделенные от других частей системы поверхностью раздела.
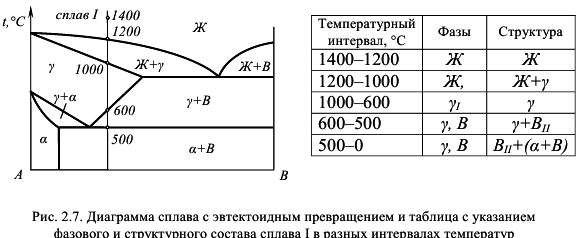
Под структурными составляющими понимают отдельные, обособленные части сплава, имеющие при рассмотрении под микроскопом однообразное строение с присущими им характерными особенностями.
Структура характеризуется видом, формой, величиной, относительным количеством, распределением составляющих по объему или в плоскости шлифа.
Структурная составляющая может состоять из одной, двух и более фаз. Формирование структуры прослеживается легче всего по превращениям, указанным на кривой охлаждения. Нужно следить за тем, какая (или какие) фаза участвует в фазовом превращении. Могут быть различные варианты.
Например, двухфазный сплав, достигнув критической температуры, испытывает фазовое превращение. При этом фазы, взаимодействуя, расходуются полностью и образуется новая фаза. Возможен и другой путь. Одна фаза превращается в смесь фаз, а другая переходит в область низких температур как структурно свободная составляющая. Приведем пример (рис. 2.7).
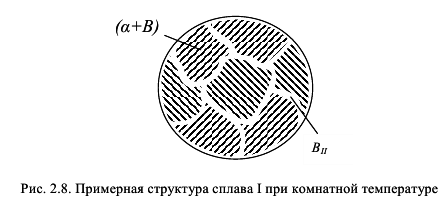
В интервале сплав был однофазным. При охлаждении от
до
из у-твёрдого раствора выделяются вторичные кристаллы компонента
. При
имеет место эвтектоидное превращение
. Вторичные кристаллы
в реакции участия не принимают. После завершения реакции они оказались на границе раздела эвтектоидных колоний (рис. 2.8). Таким образом, структура сплава при температуре ниже
состоит из вторичных кристаллов компонента и эвтектоида:
.
Возможно эта страница вам будет полезна:
Рефераты по материаловедению |
Анализ состояния сплава при заданной температуре
На ординате, соответствующей заданному (согласно варианту задания) сплаву, нанести точку, отвечающую указанной в таблице температуре. Обозначить ее любой буквой. Написать ответ на первую часть вопроса: из каких фаз состоит сплав при заданной температуре. Название фаз выписать из области диаграммы, в которую попадает горизонтальная линия (конода), соответствующая заданной в варианте температуре.
Для определения количественного соотношения фаз необходимо провести горизонталь (коноду) до пересечения с ближайшими линиями диаграммы. Конечные точки этой горизонтали обозначить какими-либо буквами и спроектировать на ось концентраций для определения состава (содержания компонентов и
в процентах).
Для определения веса фаз на 1 килограмм сплава необходимо воспользоваться формулой (2.4). Длины отрезков не следует измерять линейкой. Необходимо воспользоваться осью концентраций, т. к. при нахождении составов фаз были спроектированы конечные точки коноды на эту ось и определены их абсциссы в соответствующем масштабе.
Возможно эта страница вам будет полезна:
Лабораторные по материаловедению |
Основные понятия о материаловедение
Одним из важнейших и широко применяемых строительных материалов в транспортном, гражданском и промышленном строительстве являются стали. Студентам необходимо знать и уметь использовать основные механические и технологические свойства сталей, которые в значительной мере определяются его структурой.
В материаловедение студенты на основе анализа диаграммы состояния «железо — цементит исследуют фазы,структурные составляющие, микроструктуру доэвтектоидной, эвтектоидной и заэвтектоидной углеродистой стали, изучают механические свойства стали:
- статическую прочность, твёрдость, пластичность и ударную вязкость
- устанавливают связь между содержанием, структурой углерода и механическими свойствами стали.
В процессе изучения задач по материаловедению студенты вырабатывают навыки анализа фазового и структурного составов стали, характера взаимодействия компонентов в твёрдом состоянии и последовательности фазовых превращений в сталях.
Данная страница с теорией и практикой поможет будущим инженерам строительных специальностей, изучающим дисциплину «Материаловедение. Технология конструкционных материалов» получить более глубокое представление решении задач по материаловедению.
Микроскопический анализ металлов и сплавов
Микроскопический анализ металлов и сплавов заключается в исследовании микроструктуры и пороков сталей с помощью оптического или электронного микроскопа.
С помощью микроанализа можно определить количество, форму, размеры отдельных фаз, их взаимное расположение , имеющиеся включения ,микродефекты, следовательно, судить о свойствах металлов и сплавов.
Исследованию подвергаются микрошлифы, приготовленные определённым способом.
Микроскопический анализ состоит из следующих этапов: а) приготовления шлифов, б) травления шлифов, в) исследования микроструктуры металлов и сплавов.
Микрошлифом называют небольшой образец металла, имеющий особо приготовленную поверхность для микроанализа.
После соответствующей шлифовки и полировки образцы подвергают травлению определённым химическим реактивом для выявления микроструктуры сплава.
Микроскопическое исследование приготовленных указанным способом шлифов осуществляется с помощью металлографического микроскопа, который в отличие от биологического позволяет рассматривать прозрачные тела в отражённом свете.
Структура сталей в равновесном состоянии
Сталями называют железоуглеродистые стали с содержанием углерода до
Основой для определения структурных составляющих железоуглеродистых сплавов в равновесном состоянии является диаграмма состояния системы «железо — цементит»( )(рис. 1 и 2).

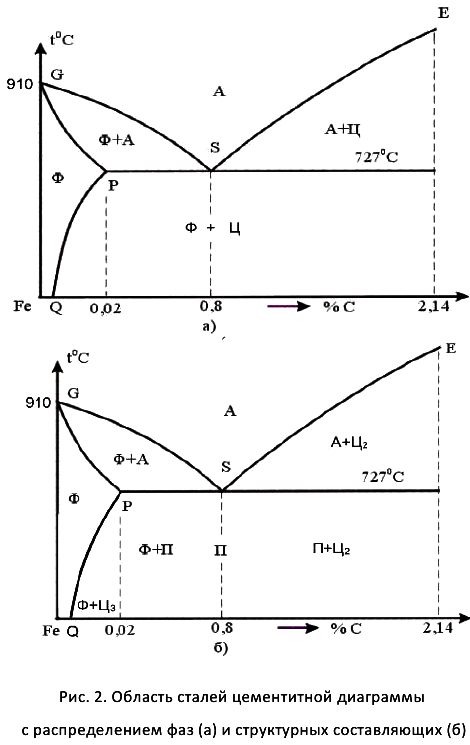
Под равновесным состоянием сплава понимается такое состояние, когда все фазовые превращения в сплаве полностью закончились в соответствии с диаграммой состояния. Оно достигается при очень медленном охлаждении, со скоростью в час, т.е при охлаждении вместе с печью.
Структурными составляющими сталей являются феррит, аустенит, цементит и перлит. Простые структурные составляющие сталей: феррит, аустенит и цементит — являются в то же время их фазами.
Железо известно в двух полиморфных модификациях: в виде — модификации железа (
) и
— модификации железа (
).
Феррит (Ф) — это твёрдый раствор внедрения углерода в a-модификации железа. Он имеет ОЦК-кристаллическую решётку, растворимость в которой мала. Предельная концентрация углерода в феррите составляет при температуре
, а при комнатной температуре —
.
Аустенит (А) — твёрдый раствор внедрения углерода в . Имеет ГЦК-решётку. Максимальная растворимость в нём углерода составляет
при температуре
, при
. Аустенит пластичен, но более прочен, чем феррит.
Цементит (Ц) — сложная структурная составляющая, химическое соединение, карбид железа , с содержанием углерода
. Имеет сложную ромбическую решётку. Цементит очень твёрд (
) и хрупок (
).
Перлит (П) — сложная структурная составляющая, продукт распада аустенита с содержанием углерода , представляющая собой дисперсную эвтектоидную смесь кристаллов феррита и цементита. По своей структуре ( равномерное распределение одной фазы в другой) перлит напоминает эвтектику, но в отличие от эвтектики, образующейся при затвердевании жидкости, перлит получается при распаде твёрдого раствора и поэтому называется эвтектоидом.
Все точки и линии цементитной диаграммы в области сталей имеют следующие обозначения и физический смысл.
Линия — геометрическое место критических точек начала образования феррита вследствие перекристаллизации
в
.
Линия характеризует температуры конца превращения аустенита в феррит.
В соответствии с линиями и
изменяется состав аустенита и феррита при изменении температуры сплава.
Линия — линия перлитовых превращений, представляющая собой геометрическое место точек распада аустенита с образованием перлита.
Точка показывает максимально возможное содержание углерода в
Линия характеризует предельную растворимость углерода в аустените в зависимости от температуры.
Точка показывает максимально возможное содержание углерода в
.
Точка показывает содержание углерода в
при комнатной температуре. (
).
Линия характеризует предельную растворимость углерода в феррите в зависимости от температуры.
Линия показывает изменение растворимости углерода с понижением температуры.
Железоуглеродистые сплавы, содержащие до углерода (с общим количеством примесей до
) называют техническим железом.
Если углерода в техническом железе меньше , то при охлаждении в интервале температур между линиями
и
происходит перекристаллизация аустенита в феррит. Однофазная ферритная структура сохраняется вплоть до комнатной температуры.
При содержании углерода более , после образования феррита, начиная с температуры на линии
, происходит выделение из феррита кристаллов цементита, который получил название третичного цементита (рис.3). Этот процесс вызван уменьшением растворимости углерода в феррите по линии
. Конечная структура будет двухфазной: феррит и третичный цементит, причём цементит располагается в виде прослоек по границам ферритных зёрен (рис.4а). Третичный цементит ухудшает технологическую пластичность железа и его магнитные свойства.
Третичный цементит присутствует при комнатных температурах во всех железоуглеродистых сплавах, содержащих более углерода. Однако его роль в формировании свойств в сплавах с содержанием углерода более
невелика, так как в таких сплавах есть цементит в большем количестве, выделившийся при других фазовых превращениях, поэтому при рассмотрении структуры таких сплавов о третичном цементите не упоминают.
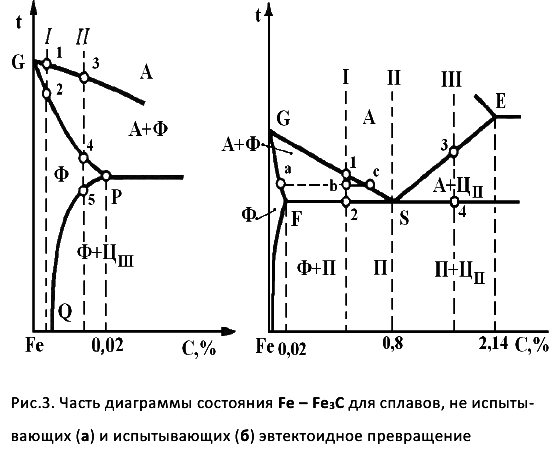
По микроструктуре стали подразделяют на доэвтектоидные, эвтектоидные и заэвтектоидные.
Доэвтектоидные — это стали с содержанием углерода до . Они имеют ферритно-перлитовую структуру (Рис. 46 и 5а).
При
-модификация железа (
) должна переходить в
-модификацию железа (
), однако наличие углерода в кристаллической решётке
расширяет область её устойчивости и аустенит сохраняется при температурах ниже
.
Наименьшая температура, при которой в условиях медленного охлаждения ещё сохраняется аустенит, равна . При этом в аустените содержится
углерода.
При дальнейшем охлаждении происходит распад твёрдого раствора с образованием феррита и цементита. Продукт распада аустенита, содержащего углерода называется перлитом и представляет собой равномерную дисперсную смесь феррита с цементитом.
При охлаждении доэвтектоидных сталей распад аустенита начинается с частичной перекристаллизации в
с образованием феррита, т.е. образующаяся
сохраняет в своей кристаллической решётке не более
углерода (максимальная растворимость углерода в
).
Чем больше углерода содержит аустенит, тем при более низкой температуре начинаются эти превращения при охлаждении доэвтектоидных сталей. За счёт образования феррита оставшийся аустенит обогащаются углеродом, и его состав по мере понижения температуры изменяется по лини . При температуре
аустенит содержит
углерода и при дальнейшем охлаждении распадается образуя перлит.
При температуре ниже линии перлитовых превращений (
) доэвтектоидные стали состоят из феррита и перлита.
Эвтектоидные стали содержат углерода и имеют перлитовую структуру. В них при температуре линии
(
) происходит эвтектоидное превращение, в результате которого из аустенита выделяются феррит концентрации 0,02% углерода и цементит (его называют эвтектоидным). Такую механическую смесь двух фаз называют перлитом. (рис. 4в, 5б и 5в). Эвтектоидное превращение идёт при постоянной температуре и концентрации фаз.
Заэвтектоидные — это стали с содержанием углерода от до
. Их структура: перлит + вторичный цементит(рис. 4г и 5г).
При охлаждении заэвтектоидных сталей по линии из твёрдого раствора (аустенита) выделяется цементит вследствие уменьшения растворимости углерода в
с понижением температуры.
Чтобы отличить цементит, образующийся из жидкого раствора при затвердевании сплавов, содержащих более углерода, от цементита, образующегося при охлаждении аустенита с содержанием углерода более
. принято первый цементит называть первичным, второй — вторичным. Вследствие выделения вторичного цементита уменьшается содержание углерода в оставшемся аустените.
На линии перлитовых превращений аустенит содержит углерода и при дальнейшем охлаждении распадается с образованием перлита.
Следовательно, ниже линии в условиях медленного охлаждения ( в равновесном состоянии) стали состоят из следующих структурных составляющих: феррит + перлит (доэвтектоидные стали); перлит (эвтектоидные стали); перлит + цементит вторичный (заэвтекоидные стали)).
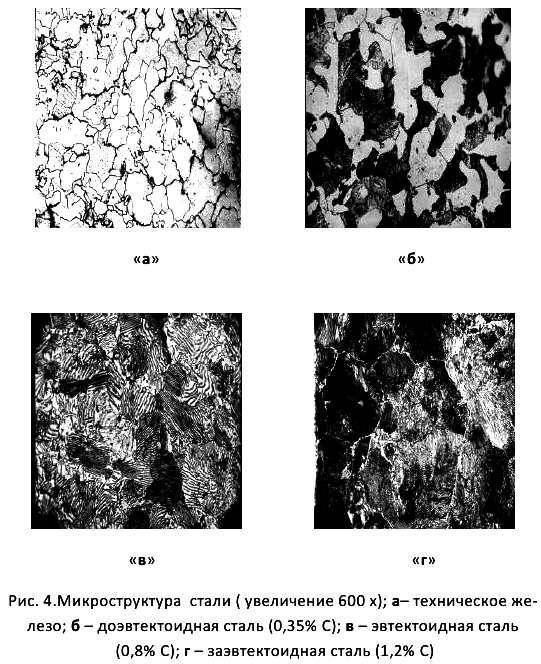
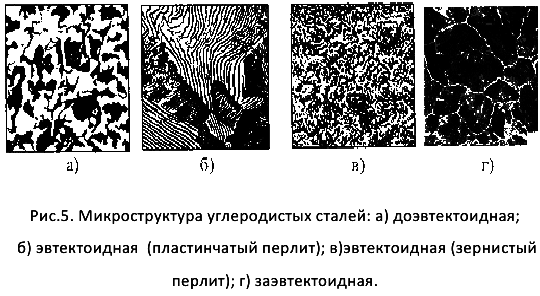
Механические свойства сталей
Механические свойства железа технической чистоты: предел прочности при растяжении (временное сопротивление разрыву) , предел текучести
, твёрдость по Бринеллю
, относительное удлинение
, относительное сужение
, удельная ударная вязкость (сопротивление динамическим нагрузкам)
.
Методы определения твёрдости сталей
Твёрдость — это способность материала сопротивляться внедрению в его поверхность другого более твёрдого тела.
Определение твёрдости является широко применяемым в лабораторных и заводских условиях способом испытаний для характеристики механических свойств металлов.
Твёрдость металлов измеряют путём вдавливания в поверхность металла наконечника, изготовленного из малодеформирующе-гося материала (твёрдая закалённая сталь или алмаз), имеющего форму шарика, конуса или пирамиды).
В результате вдавливания с достаточно большой нагрузкой поверхностные слои металла, находящегося под наконечником и вблизи него, пластически деформируются. После снятия нагрузки остаётся отпечаток
Существует несколько методов определения твёрдости (рис. б).
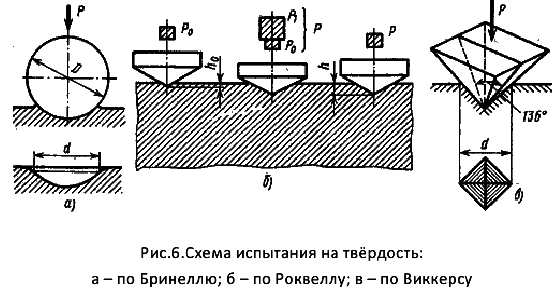
Наиболее распространённым является метод Бринелля , когда в металлический образец под воздействием силы , внедряется шарик диаметром
(рис. 7 и 8). Число твёрдости по Бринеллю
представляет собой отношение нагрузки
к площади поверхности сферического отпечатка
( с диаметром
) и измеряется в
или
.
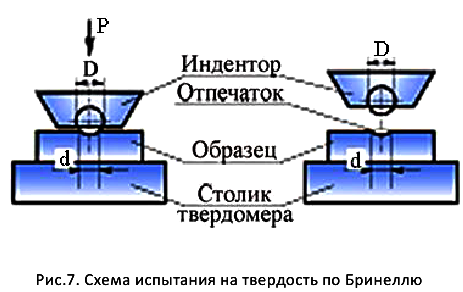
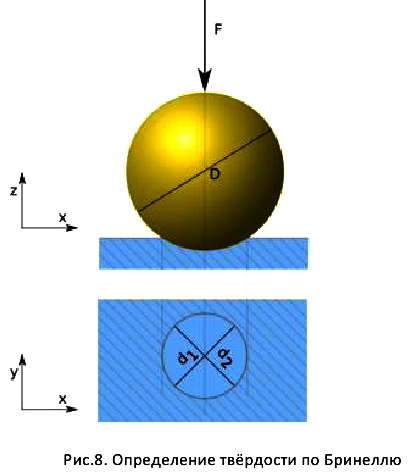

Площадь сферы отпечатка описывается следующим уравнением
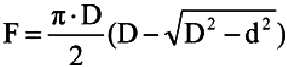
Тогда число твёрдости по Бринеллю определяется по формуле
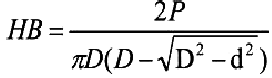
где — нагрузка в
;
— диаметр шарика в
;
— диаметр отпечатка.
В практической работе для определения твёрдости не делают вычислений по формуле , а пользуются таблицами, составленными для установленных диаметров шариков, отпечаток и нагрузок. Шарики применяют диаметром Диаметр шарика и нагрузка выбираются в соответствии с толщиной образца (табл.2). Число твёрдости по Бринеллю, измеренное при стандартном испытании
записывается следующим образом:
Диаметр отпечатка измеряют при помощи отсчётного микроскопа (лупы Бринелля), на окуляре которого имеется шкала с делениями, соответствующими десятым долям миллиметра. Измерение проводят с точностью до в двух взаимно перпендикулярных направлениях. Для определения твёрдости следует принимать среднее значение из полученных величин.
Метод Роквелла
При методе Роквелла (рис. 6) индентором служит алмазный конус (иногда маленький стальной шарик). Числом твёрдости является величина, обратная глубине вдавливания
Имеются три шкалы. При испытании алмазным конусом под нагрузкой твердость определяют по шкале
в единицах
, а под нагрузкой
— по шкале
в единицах
. При вдавливании стального шарика при
твёрдость определяют по шкале
в единицах
.
Метод Виккерса
При методе Виккерса (рис. 6) вдавливаеся алмазная пирамида и измерив диагональ отпечатка () судят о твёрдости (
).
Метод Бринелля применяют для сравнительно мягких металлов, у которых ,а метод Роквелла с использованием шкалы
для твёрдых сплавов ( например, закалённых сталей).
Между различными методами существует определённая корреляция. По соответствующим таблицам, значения твёрдости полученного одним способом, можно определить, какому числу твёрдости другого метода оно соответствует, в том числе и методу Бринелля. Например, .
Измерение твёрдости по технике выполнения значительно проще, чем определение прочности, пластичности и вязкости. Измерения твёрдости выполняются быстро, при вдавливании конуса за 30-60 с, а при вдавливании шарика за 1 — 3 мин.
Поэтому весьма часто для определения прочности пользуются простым, не разрушающим образец, методом — измерением твёрдости.
Для доэвтектоиднах сталей существует довольно точная корреляция между прочностью и твёрдостью, а именно
Влияние углерода на свойства стали
Углерод оказывает определяющее влияние на свойства стали.
Увеличение содержания углерода повышает прочность ( до углерода) и твёрдость стали, однако существенно понижает пластичность и удельную ударную вязкость, повышает порог хладноломкости (рис.9)
С увеличением содержания углерода изменяется структура стали.В равновесном состоянии структура стали представляет смесь феррита и цементита, в которой количество последнего увеличивается пропорционально содержанию углерода.
Зная механические свойства феррита и цементита, можно предположить, как будут меняться механические свойства сталей с изменением содержания углерода. Механические свойства феррита цементита и других структурных составляющих приведены в табл.1.
С увеличением содержания углерода возрастает количество хрупкого и твёрдого цементита, а следовательно повышается хрупкость и твёрдость, понижается пластичность и ударная вязкость стали.
Прочность стали с увеличением количества углерода в начале возрастает, а затем, достигнув максимума примерно при , начинает понижаться.
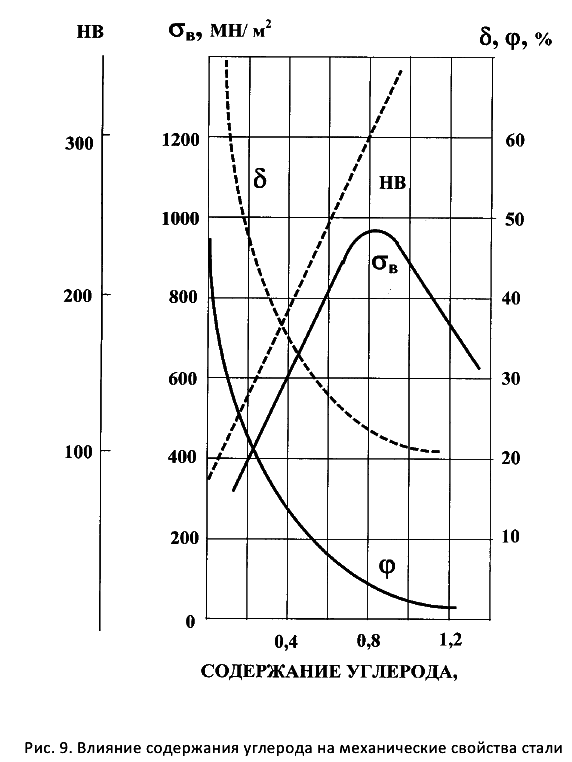
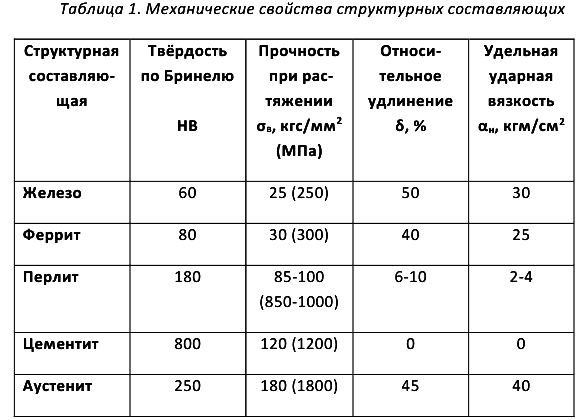
Это объясняется следующим. В доэвтектоидных сталях углерод в виде цементита входит в состав сложной структурной составляющей стали — перлита. При этом цементит располагается в перлите в виде отдельных, не соприкасающихся между собой пластинок, что придаёт перлиту по сравнению с чистым ферритом большие прочность и твёрдость.
Так как с увеличением содержания углерода в доэвтектоидных сталях возрастает количество перлита, то и прочность стали повышается.
В структуре же заэвтектоидных сталей входит вторичный цементит, который располагается оболочками вокруг зёрен перлита (рис.4г, 5г и 10в), образуя хрупкую сетку. Чем больше содержание углерода в заэвтектоидной стали, тем непрерывнее и толще сетка вторичного цементита, тем больше хрупкость стали и меньше её прочность.
Феррит малопрочен и пластичен. Цементит твёрд и хрупок. В связи с этим по мере повышения концентрации углерода повышается прочность и твёрдость, снижаются пластичность и вязкость стали
На механические свойства заэвтектоидных сталей сильное влияние оказывает вторичный цементит, образующий хрупкий каркас вокруг зёрен перлита. Под нагрузкой этот каркас преждевременно разрушается, вызывая снижение прочности сталей, у которых содержание углерода свыше . Именно при таком количестве углерода хрупкая сетка вторичного цементита приобретает сплошной характер.
Углерод изменяет технологические свойства стали: обрабатываемость резанием, давлением, свариваемость.
Увеличение содержания углерода вследствие упрочнения и ухудшения теплопроводности ведёт к снижению обрабатываемости резанием. С увеличением содержания углерода снижается технологическая пластичность — способность деформироваться в горячем и особенно в холодном состоянии. Для сложной холодной штамповки содержание углерода ограничивают .
Углерод затрудняет также свариваемость стали. Сварка средне- и особенно высокоуглеродистых сталей требует применения подогрева, замедленного охлаждения и других технологических операций, предупреждающих образование горячих и холодных трещин.
По микроструктуре углеродистой стали в равновесном состоянии можно определить содержание углерода следующим способом (рис.10).
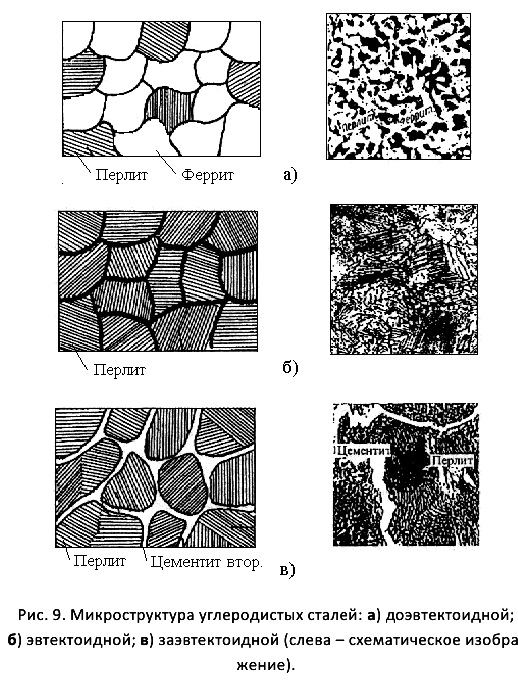
Структура доэвтектоидной стали феррит и перлит. Феррит содержит углерода, а перлит —
.
Поэтому, если известно количество феррита и перлита в общей массе металла, можно определить содержание углерода в стали умножением относительной площади ( в процентах) феррита и перлита, занимаемой каждой из этих структурных составляющих на просматриваемом поле шлифа.
Аналогично рассчитывают содержание углерода в заэвтектоидной стали, имея в виду, что её структура перлит и цементит, а цементит содержит углерода.
Этот расчёт можно произвести по формулам:
а) для доэвтектоидной стали

б) для заэвтектоидной стали

где Ф, П и Ц — относительная площадь (в ), занимаемая соответственно ферритом, перлитом и цементитом на поле шлифа.
Экспериментально определив твёрдость по Бринеллю () углеродистой доэвтектоидной стали , можно довольно точно установить прочность этой стали при растяжении (
) по формуле
, а содержание в ней углерода по формуле
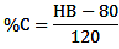
Оформление задач по материаловедению
Задания выдаются индивидуально каждому студенту в соответствии с рабочими программами и учебными планами.
Каждый вариант задания состоит из вопросов и задач по основным разделам дисциплины «Материаловедение».
При выполнении домашнего задания студенты должны проявить знание теоретических основ дисциплины, умение выбирать металлические материалы для изготовления различных изделий и назначать им термическую обработку, а также ознакомиться с особенностями состава, строения и областями применения наиболее распространенных неметаллических материалов.
Для выполнения домашнего задания приводится список рекомендуемой литературы.
К выполнению домашнего задания предъявляются следующие требования:
- домашнее задание выполняется на формате А4 в печатном виде;
- структура отчета по домашнему заданию: титульный лист; лист с вариантом задания с подписью преподавателя; ответы на вопросы домашнего задания; список используемой литературы.
- от студента требуются четко сформулированные ответы на поставленные вопросы, поэтому объем домашнего задания может не превышать 6 листов (страниц);
- диаграмма «Железо — цементит» вычерчивается студентом самостоятельно. Копирование из электронного учебника недопустимо! Диаграмма вычерчивается на листе так, чтобы справа было место для изображения кривой охлаждения заданного сплава. Ордината сплава должна отчетливо выделяться на диаграмме. Правее диаграммы необходимо вычертить оси «Температура -Время» для построения кривой охлаждения. На ось ординат следует также нанести критические точки заданного сплава в градусах Цельсия.
Задачи и правила их решения с примерами
Тема данных задач — «Микроструктура сталей и влияние углерода на механические свойства сталей».
Это стандартная тема которую студенты проходят в течении 1 и 2 курса.
Задача № 1
- изучить диаграмму состояния железоуглеродистых сплавов и начертить её часть , относящуюся к области сталей;
- охарактеризовать фазы и структурные составляющие сталей;
- исследовать типичные равновесные структуры углеродистых сталей;
- исследовать механические свойства стали: статическую прочность, твёрдость, пластичность, удельную ударную вязкость;
- изучить методику определения твёрдости стали по Бринеллю;
- установить влияние содержания углерода на структуру и механические свойства стали;
- определить концентрацию углерода в каждом шлифе сталей;
- ознакомиться с процессом приготовления микрошлифов, устройством металлографического микроскопа и методикой работы на нём.
Решение:
1) Вычертить в масштабе график зависимости механических свойств стали от содержания углерода.
2) Зарисовать микроструктуру феррита, двух доэвтектоидных сталей, эвтектоидной стали и заэвтектоидной стали.
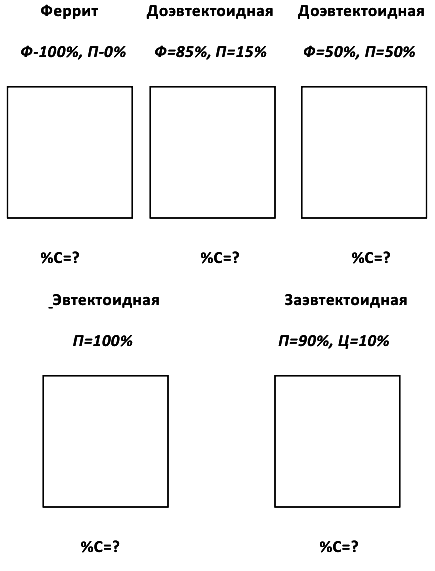
3) Определить содержание углерода в каждой из зарисованных структур стали по следующим формулам для доэвтектоидной стали:
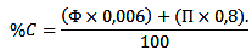
для заэвтектоидной стали:
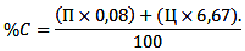
4) Дать определение твёрдости материала.
5) Зарисовать схему определения твёрдости металла по способу Бринелля.
6) Привести таблицу норм испытаний по Бринеллю для стали и чугуна(табл. 5 )
7) Определить твёрдость по Бринеллю () шести стальных образцов с различным содержанием углерода. Результаты испытаний занести в табл 2.
8) Перенести полученные значения твёрдости в табл.3. Рассчитать содержание углерода ()и прочность при растяжении (
) для всех испытанных образцов, используя следующие формулы
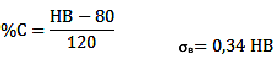
9) Построить график зависимости прочности при растяжении и твёрдости стали от содержания углерода (рис. 11)
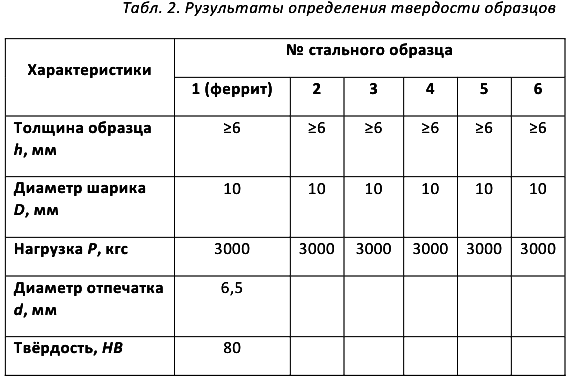
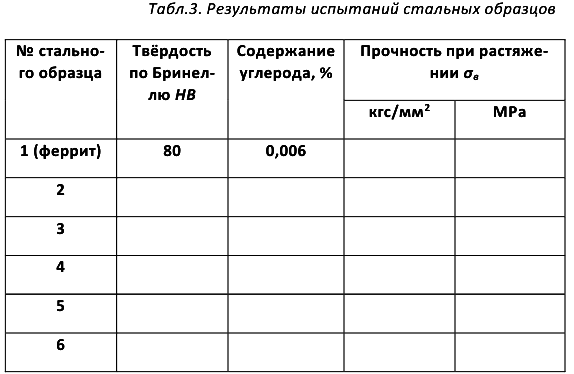
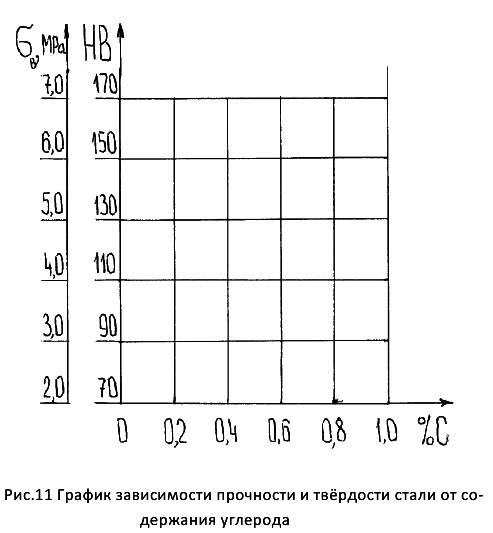
Точность вычислений: содержание углерода — ; прочность —
; твёрдость —
.
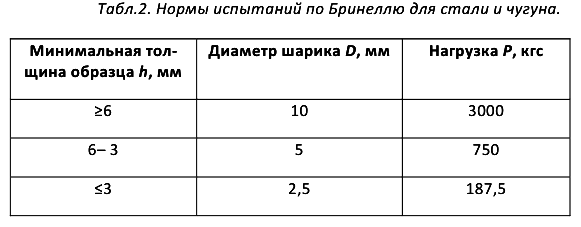
Задача № 2
Вычертите диаграмму состояния железо-цементит, укажите структурные составляющие во всех областях диаграммы.
Опишите превращения, происходящие при охлаждении сплава с указанным количеством углерода, укажите содержание углерода в образующихся фазах.
Какова равновесная структура этого сплава при комнатной температуре и как такой сплав называется?
Решение:
Сплав, содержащий
Указанный сплав отмечен вертикальной линией, на диаграмме железо-цементит.
Диаграмму состояния железо-цементит представим на рисунке 1.
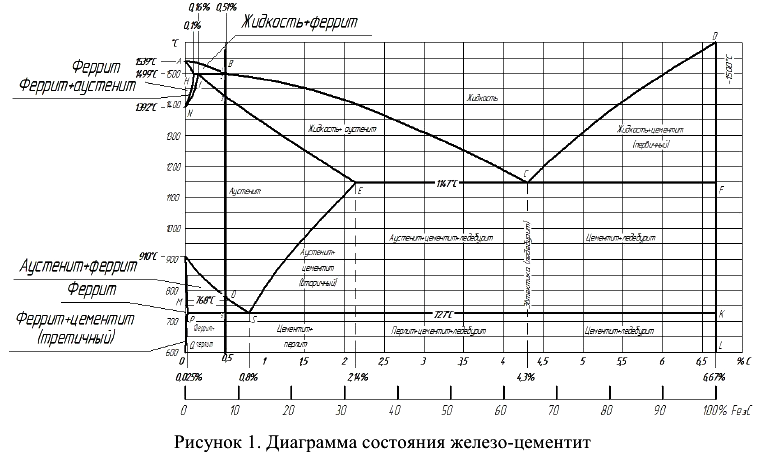
- Сплав, содержащий
углерода-сталь 50
Кривую охлаждения сплава, содержащего представим на рисунке 2.
Опишем процессы, происходящие при охлаждении сплава.
До температуры 1 сплав находится в жидком состоянии, происходит охлаждение расплава.
Правило фаз:
При температуре 1 из расплава начинает выделяться Феррит (Ф). На участке 1-2 сплав будет иметь структуру Ф+Ж.
Правило фаз.
В точке 2 происходит перитектическая реакция Ж + Ф А (участок 2-2′),
От точки 2’до точки 3 сплав находится в состоянии двух фаз — А+Ж.
В точках от 3 до 4 сплав имеет однофазную Аустенитную (А) структуру.
В точке 4 из Аустенита (А) начинает выделяться вторичный Феррит (Ф) и этот процесс продолжается до точки 5.
В точке 5 происходит эвтектоидное превращение, при котором Аустенит распадается на Перлит (П) — механическую смесь Феррита и Цементита (А П (Ф + ЦП), в результате при комнатной температуре сплав имеет структуру Перлита и избыточного Феррита (участок 5-5′).
Ниже точки 5 сплав имеет двухфазную структуру П+Ф, которая охлаждается без ка-ких-либо изменений и без выделения скрытой теплоты.
При комнатной температуре сплав имеет структуру (П+Ф) — перлит +феррит. Сплав, содержащий углерода-доэвтектоидная сталь 50
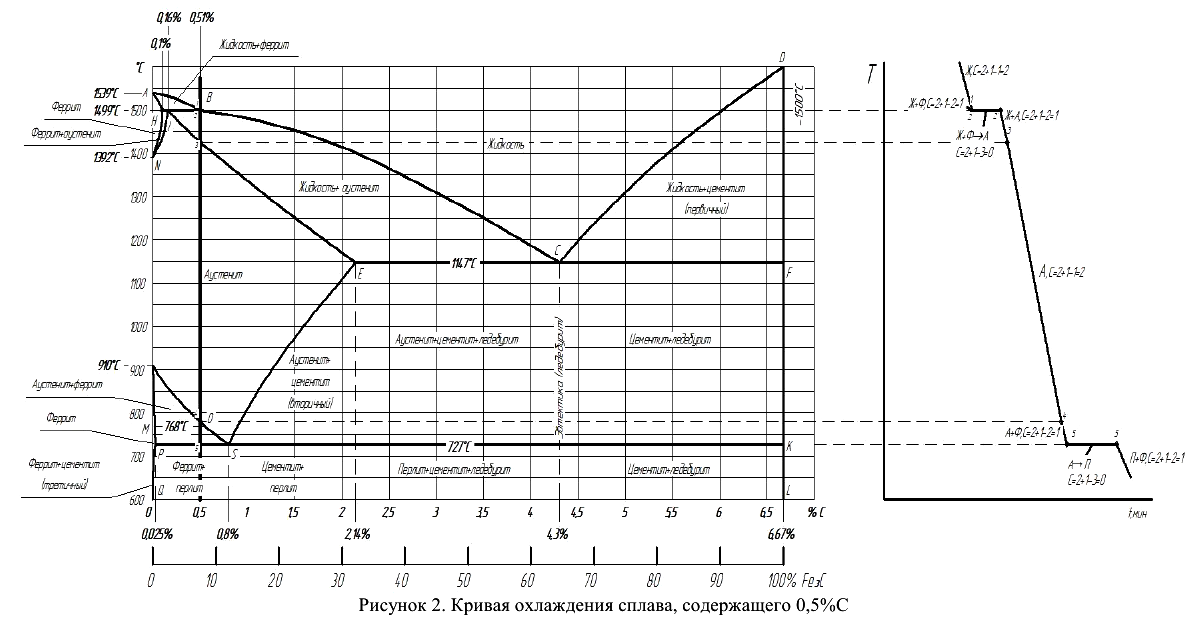
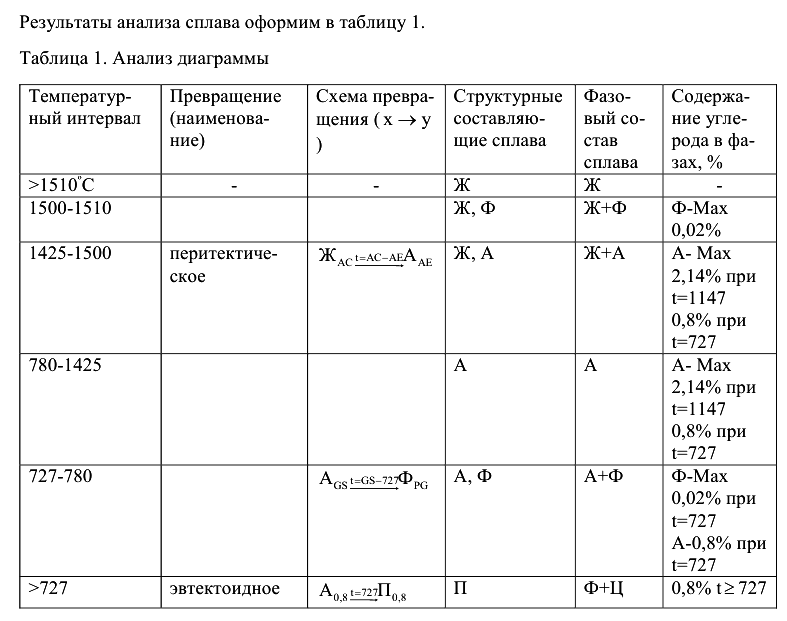
Задача № 3
Изобразите диаграммы состояния двойных систем для случаев образования устойчивых и неустойчивых химических соединений. Дайте необходимые пояснения к диаграммам. Что такое эвтектика?
Решение:
Химическое соединение характеризуется определенным соотношением компонентов, а это отражается на диаграмме вертикальной линией, проходящей на оси абсцисс через точку, отвечающую соотношению компонентов в химическом соединении. Если компоненты и
образуют химическое соединение
, то, следовательно, на n+ m его атомов приходится
атомов
и
атомов
. Определенному атомному соотношению соответствует и определенное соотношение по массе.
Химическое соединение устойчиво, если его можно нагреть без разложения до расплавления, и неустойчиво, если при нагреве оно разлагается. В зависимости от этого могут быть два вида диаграмм. Кроме того, возможно образование нескольких химических соединений между двумя компонентами, а также растворимость на базе химического соединения — эти обстоятельства также находят отражение в диаграмме состояния.
Диаграмма с устойчивым химическим соединением
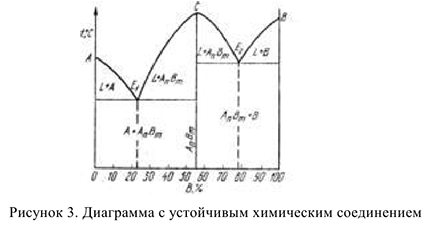
Предположим, что оба компонента образуют одно устойчивое соединение , причем и это соединение, и чистые компоненты не образуют в твердомсостоянии растворов.
Компонентами системы являются вещества и
, а твердыми фазами —
,
и
. Из четырех возможных в этой системе фаз могут сосуществовать три
или
,
.
Это химическое соединение устойчиво, поэтому оно может быть нагрето без разложения до своей температуры плавления (точка ). Химическое соединение плавится при постоянной температуре. Плавление химического соединения при постоянной температуре вполне соответствует правилу фаз. Химическое соединение можно рассматривать как однокомпонентную систему (один компонент — химическое соединение ), тогда при плавлении
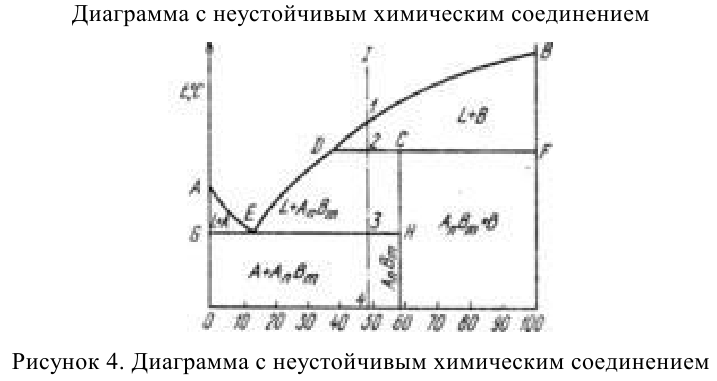
В отличие от диаграммы с устойчивым химическим соединением на рис. 1 приведена диаграмма состояний, где два компонента образуют неустойчивое химическое соединение, которое при нагреве до определенной температуры () разлагается на жидкость и один из компонентов, т. е. не расплавляется полностью.
На линии находятся в равновесии три фазы: жидкость концентрации
, кристаллы компонента
и кристаллы химического соединения
.
При нагреве неустойчивое химическое соединение распадается на жидкость концентрации
и кристаллы
.При охлаждении, следовательно, произойдет обратная реакция:
Реакция эта подобна псритектичсской; жидкость реагирует с ранее выпавшими кристаллами, но образует не новый твердый раствор, как в случае псритектичсской реакции, а химическое соединение.
Процесс кристаллизации сплава в равновесных условиях будет протекать следующим образом. В точке 1 начинается кристаллизация, выпадают кристаллы
, и концентрация жидкости изменяется по кривой 1—
. B точке 2 при постоянной температуре образуется неустойчивое химическое соединение по уравнению, приведенному выше. По окончании реакции в избытке остается жидкость, которая кристаллизуется с выделением соединения
до тех пор, пока концентрация жидкости не достигнет точки
. Тогда оставшаяся жидкость кристаллизуется в эвтектику, состоящую из кристаллов
и химического соединения. Следовательно, на кривой будем иметь две площадки: верхнюю, соответствующую образованию неустойчивого химического соединения, и нижнюю, соответствующую образованию эвтектики
Эвтектика (от греческого eutektos — легко плавящийся) тонкая смесь твердых веществ, одновременно начинающих кристаллизоваться из расплавов при температуре менее , отдельных компонентов или любых других их смесей (рис. Э-1). Примером эвтектики может служить, например, ледебурит.
Задача № 4
Как изменяются структура и свойства стали и
в результате закалки от температуры
и
(объясните с применением диаграммы состояния «железо-цементит»).
Решение:
Исходная структура среднеуглеродистой конструкционной стали до нагрева под закалку — перлит + феррит.
Критические точки для стали :
При нагреве до в стали
не происходят аллотропические превращения и мы имеем ту же структуру — перлит + феррит, быстро охлаждая (т.к. закалка), имеем также после охлаждения перлит + феррит с теми же механическими свойствами (примерно), что и в исходном состоянии до нагрева под закалку. Например, после нормализации:
Если доэвтектоидную сталь нагреть выше , но ниже
, то в ее структуре после закалки наряду с мартенситом будут участки феррита. Присутствие феррита как мягкой составляющей снижает твердость стали после закалки. При нагреве до температуры
(ниже точки
) структура стали
— аустснит + феррит, после охлаждения со скоростью выше критической структура стали — мартенсит + феррит.
Доэвтектоидныс стали для закалки следует нагревать до температуры на выше
. Температура нагрева стали под закалку, таким образом, составляет
. Структура стали
при температуре нагрева под закалку — аустснит, после охлаждения со скоростью выше критической — мартенсит.
Нагрев и выдержка стали при температуре выше
приводит к росту зерна и ухудшению механических свойств стали после термической обработки. Крупнозернистая структура вызывает повышенную хрупкость стали.
Исходная структура высокоуглеродистой инструментальной стали до нагрева под закалку — перлит + карбиды.
Критические точки для стали .
При нагреве до в стали
не происходят аллотропические превращения и мы имеем ту же структуру — перлит + карбиды, быстро охлаждая (т.к. закалка), имеем также после охлаждения перлит + карбиды с теми же механическими свойствами (примерно), что и в исходном состоянии до нагрева под закалку.
Оптимальный режим нагрева под закалку для заэвтектоидных сталей составляет
, т.е. для
. При этом после закалки имеем мелкое зерно, обеспечивающее наилучшие механические свойства стали
.
Нагрев и выдержка стали при температуре
перед закалкой приводит к росту зерна и ухудшению механических свойств стали после термической обработки.
Задача № 5
Для детали задана определенная марка стали. Укажите состав и определите, к какой группе по назначению относится данная сталь. Назначьте и обоснуйте режим термической обработки, объяснив влияние легирования на превращения, происходящие на всех этапах обработки данной стали. Опишите микроструктуру и свойства стали после термической или химико-термической обработки.
Решение:
Данные по маркам сталей:

— Сталь конструкционная подшипниковая, содержащая
Влияние легирующих элементов на свойства стали
Хром замедляет превращение аустенита в перлит и тем самым увеличивает прокаливаемость стали, поэтому, чем крупнее детали подшипников, тем с большим содержанием хрома применяют сталь для их изготовления.
Кроме того, высокая твердость карбидов хрома повышает износостойкость стали. Хром увеличивает устойчивость мартенсита против отпуска, уменьшает склонность стали к перегреву и придаст ей мелкозернистую структуру. Но при высоком содержании хрома трудно получить однородную структуру, поэтому содержание хрома в шарикоподшипниковых сталях обычно не превышает
.
Марганец, как и хром, увеличивает твердость и сопротивляемость стали истиранию. Но одновременно он способствует росту зерна при нагреве, в результате чего при термической обработке может образовываться крупнозернистая структура перегретой стали.
Повышенное содержание марганца и кремния в этой стали объясняется тем, что эти элементы уменьшают критическую скорость закалки, снижая тем самым склонность стали к короблению и тещинообразованию при закалке.
Термическая обработка деталей шарикоподшипника из стали состоит из двух основных операций — закалки и низкого отпуска. Закалку проводят в масле, температура нагрева
с последующим отпуском при
в течение
, что обеспечивает получение твердости не ниже
.
Структура стали после термообработки отпущенный очень мелкоигольчатый мартенсит с равномерно распределенными избыточными карбидами, (рисунок 5.)
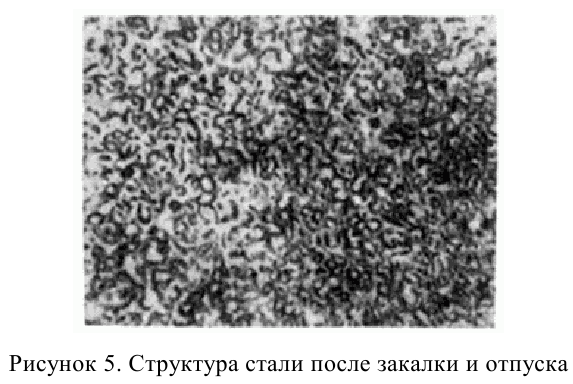
Несоблюдение правильных температурных режимов термической обработки, которые задаются в узких пределах, ухудшает качество подшипников, что отражается на их стойкости в работе.
Задача № 6
Расшифруйте марки заданных материалов; оцените свариваемость материала; опишите процессы, происходящие в зоне шва и околошовной зоне. Отметьте, в чем заключается особенность технологии и техники сварки данного материала. Выберите и обоснуйте метод сварки. Рассчитайте режимы, нарисуйте разделку кромок шва, выберите оборудование для сварки и укажите основные характеристики. Выберите и опишите методы контроля сварного соединения.

Решение:
Сталь — конструкционная легированная, высококачественная; свариваемость стали — ограниченно свариваемая. Рекомендуемые способы сварки: ручная дуговая сварка и аргонно-дуговая сварка под флюсом. Химический состав стали представим в таблице 1. Таблица 1. Химический состав стали
.

Дуговая сварка металла это сварка плавлением, при которой нагрев свариваемых кромок осуществляется теплом электрической дуги. Способ позволяет без замены сварочного инструмента и оборудования (при правильно выбранном сварочном режиме) выполнять швы различных типов и назначения, а также вести сварку в любом пространственном положении и в труднодоступных местах.
Устойчивый процесс сварки обеспечивается непрерывной подачей конца электрода в зону горения дуги без значительных отклонений ее длины. При длинной дуге усиливается окисление электродного металла, увеличивается разбрызгивание, снижается глубина провара, шов получается со значительными включениями оксидов. Основной объем работ выполняют при токе и напряжении дуги
.
Возбуждение (зажигание) дуги 3 (рие.10) происходит при кратковременном замыкании электрической сварочной цепи, для чего сварщик прикасается к свариваемому металлу 1 концом электрода 5 и быстро отводит его на расстояние . В этот момент возникает электрическая дуга, устойчивое горение которой поддерживают поступательным движением электрода (вдоль оси) по мере его плавления. Дугу возбуждают также скользящим движением конца электрода по поверхности свариваемого металла (чирканием) с быстрым отводом его на необходимое расстояние.
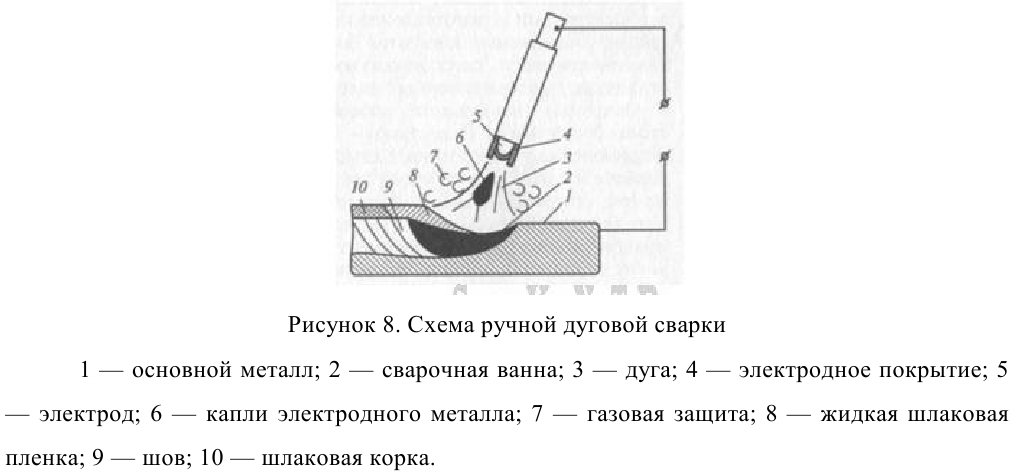
В процессе сварки электрод перемещают: по направлению к изделию по мере плавления электрода; вдоль соединения; поперек соединения для получения необходимых формы и сечения шва.
Процессы, происходящие в зоне шва и околошовной зоне.
Процесс кристаллизации шва начинается сразу после отвода дуги от свариваемого участка. Застывание металла происходит в направлении, обратном отводу тепла в структуру основной поверхности, начиная от краев сварочной ванны к ее центру. Средняя скорость кристаллизации и скорость сварки равны. По границам шва формируются кристаллиты наплавляемого и основного металла, обеспечивающие монолитность строения слоев и прочность соединения.
Образование шва и околошовной зоны.
Остановка начального процесса кристаллизации происходит достаточно быстро, при остывании шва на , то есть до температуры
. После его завершения в структуре металла не происходит никаких изменений до его остывания до
, когда металл начинает выходить из аустенитной формы.
Затем происходит процесс вторичной кристаллизации в структуре строения шва и прилегающем к нему основном металле. Он также протекает в коротком температурном диапазоне. Структура сварного шва становится стабильной по достижении им температуры в .
Кристаллиты сварочного шва имеют столбчатое строение структуры, характерное для процесса литья металла. Этот вид кристаллизации способствует вытеснению газовых и шлаковых фракций.
Рассчитаем режимы дуговой сварки
Исходные данные:
Свариваемый материал:
Тип сварного соединения -встык
Расположение шва в пространстве — вертикальный.
Толщина свариваемых деталей: .
Стыковые соединения с толщиной свариваемых деталей выполняются с односторонней разделкой кромок.
На рисунке 9 приведем эскиз соединения
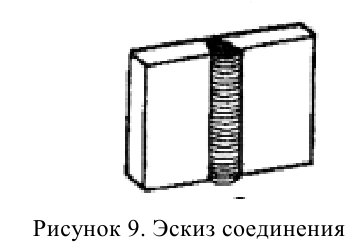
На рисунке 10 представим эскиз разделки кромок
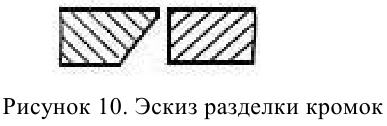
Диаметр электрода выбираем в зависимости от толщины свариваемых деталей. При заданной толщине принимаем
Определим площадь сечения одностороннего стыкового шва выполненного без зазора можно определить по формуле:
где — ширина шва, мм;
— высота усиления шва, мм;
— толщина свариваемого металла, мм;
— величина зазора в стыке, мм.
Площадь поперечного сечения шва найдем из расчетной схемы (рисунок 11).
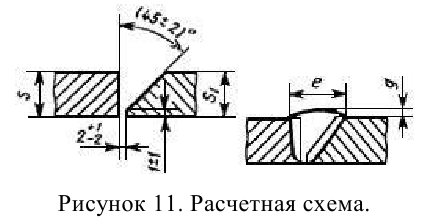
Согласно ГОСТ 5264-80

При определении числа проходов следует учитывать, что сечение первого прохода не должно превышать и может быть определено по формуле:

где — площадь поперечного сечения первого прохода,
;
— диаметр электрода, мм.

Следовательно принимаем 1 проход.
Расчет сварочного тока при ручной дуговой сварке производим по диаметру электрода и допускаемой плотности тока по формуле:

где — допустимая плотность тока,
— площадь поперечного сечения электрода,
;
— диаметр электрода, мм.
Допустимая плотность тока зависит от диаметра электрода и вида покрытия: чем больше диаметр электрода, тем меньше допустимая плотность тока, так как ухудшаются условия охлаждения. Допустимая плотность тока в электроде при ручной дуговой сварке

Напряжение на дуге при ручной дуговой сварке изменяется в пределах и при проектировании технологических процессов ручной дуговой сварки не регламентируется. Поэтому напряжение на дуге принимаем
.
Скорость перемещения дуги (скорость сварки) определяем по формуле:

где — коэффициент наплавки,
— плотность наплавленного металла за данный проход,
(
— для стали);
— сила сварочного тока,
— площадь поперечного сечения наплавленного металла,
.

Результаты расчетов режима сварки представим в таблице 2
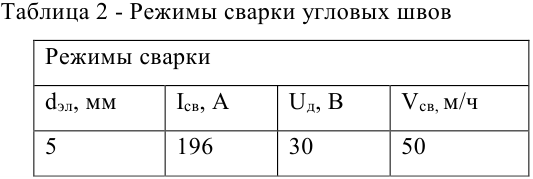
Выбираем оборудование для сварки. Принимаем трансформатор передвижной . Параметры трансформатора: сварочный ток
, номинальное рабочее напряжение
.
— сталь конструкционная легированная, высококачественная. Свариваемость без ограничений. Химический состав стали представим в таблице 3. Таблица 3. Химический состав стали
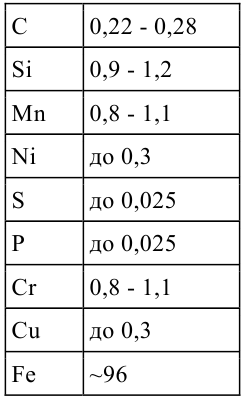
Газовая сварка конструкционной легированной стали
Низколегированные хромокремнемарганцовистые обладают хорошей прочностью, упругостью, хорошо выдерживают вибрационные нагрузки, но менее теплоустойчивы, чем хромомолибденовыс стали. Эти стали содержат и
. При газовой сварке этих сталей хром и кремний частично выгорают, что может привести к появлению в сварном шве оксидов, шлаков и непроваров.
Для предупреждения окисления легирующих добавок сварку проводят нормальным пламенем. Мощность сварочного пламени выбирают из расчета расхода ацетилена
на 1 мм толщины свариваемого металла.
В качестве присадочного металла для неответственные конструкций применяют низкоуглсродистую сварочную проволоку и
, а для ответственных конструкций-сварочную проволоку,
,
,
и
.
Диаметр присадочной проволоки выбирается в зависимости от толщины свариваемого металла и способа сварки. Кромки свариваемых деталей должны быть тщательно очищены от загрязнений и подогнаны под сварку так, чтобы зазор по всей длине шва был одинаковым.
Металлургические процессы при газовой сварке
Металлургические процессы при газовой сварке характеризуются следующими особенностями: малым объемом ванны расплавленного металла; высокой температурой и концентрацией тепла в месте сварки; Большой скоростью расплавления и остывания метла; интенсивным перемешиванием металла гладкой ванны газовым потоком пламени и присадочной проволокой; химическим взаимодействием расплавленного металла с газами пламени.
Основными в сварочной ванне являются реакции окисления и восстановления. Наиболее легко окисляются магний, алюминий, обладающие большим сродством к кислоро-
Окислы этих металлов не восстанавливаются водородом и окисью углерода, поэтому при сварке металлов необходимы специальные флюсы. Окислы железа и никеля, наоборот хорошо восстанавливаются окисью углерода и водородом пламени, поэтому при газовой сварке этих металлов флюсы не нужны.
Водород способен хорошо растворятся в жидком железе. При быстром остывании сварочной ванны он может остаться в шве в виде мелких газовых пузырей. Однако газовая сварка обеспечивает более медленное охлаждение металла по сравнению, например с дуговой. Поэтому при газовой сварке углеродистой стали, весь водород успевает уйти из металла шва и последний получится плотным.
Структурные изменения в металле при газовой сварке
Вследствие более медленного нагрева зона влияния при газовой сварке больше чем при дуговой. Слои основного металла, непосредственно примыкающие к сварочной ванне непрерывны и приобретают крупнозернистую структуру.
В непосредственной близости к границе шва находится зона неполного расплавления. Основного металла с крупной структурой, характерной для не нагретого металла. В этой зоне прочность металла ниже, чем прочность металла шва, поэтому здесь обычно и происходит разрушение сварного соединения.
Далее расположен участок, нерекристализации, характеризуемый так же крупнозернистой структурой, для которого плавления металла, не выше
. Последующие участки нагреваются до более низких температур и имеют мелкозернистую структуру, нормализованной стали.
Для улучшения структуры и свойств металла шва и околошовной зоны иногда применяют горячую проковку шва и местную термообработку нагревом сварочным пламенем или общую термообработку с нагревом в печи.
Расчет режимов газовой сварки
Исходные данные:
Свариваемый материал:
Тип сварного соединения -встык
Расположение шва в пространстве — потолочный.
Толщина свариваемых деталей: 20мм.
Стыковые соединения с толщиной свариваемых деталей 20мм выполняются с односторонней разделкой кромок.
На рисунке 12 приведем эскиз соединения
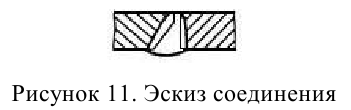
На рисунке 13 представим эскиз разделки кромок
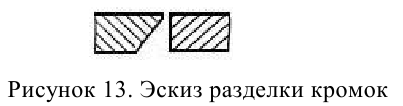
Режимы газовой сварки определяют:
- мощностью сварочного пламени
- углом наклона присадочного материала и мундштука горелки
- диаметром присадочного материала
- скоростью сварки.
Мощность сварочного пламени напрямую зависит от расхода горючего газа и для ацетиленовой сварки ее приближенно можно определить по формуле:
где — мощность пламени, определяема расходом ацетилена,
;
— толщина свариваемого материала,
;
— коэффициент пропорциональности, величина которого зависит от вида свариваемого материала, для низкоуглеродистой стали стали
, принимаем

Угол наклона мундштука сварочной горелки при толщине свариваемых листов , принимаем
Марку присадочной проволоки принимаем .
Подбираем диаметр присадочного материала в зависимости от толщины свариваемых деталей и метода наложения шва. При толщине металла более присадочный материал берут диаметром
.
Принимаем диаметр присадочной проволоки принимаем равным .
Определяем скорость сварки.

где — коэффициент, зависящий от свойств материала,
,
— толщина свариваемого металла,
.
Выбираем способ сварки
Низколегированную сталь сваривают правой сваркой, так как толщина свариваемого материала более
Результаты расчета режима сварки занесем в таблицу 4.
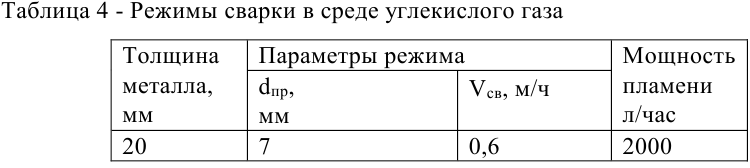
Оборудование для газовой сварки алюминия.
Принимаем ацетиленовый генератор — однопостовой, с одной ретортой, прерывистого принципа действия.
В качестве метода контроля сварного соединения применяем один из методов неразрушающего контроля — внешний осмотр . Внешнему осмотру подвергается сварных соединений. Осмотр выполняется невооруженным глазом или с помощью лупы, используя шаблоны и мерительный инструмент. При этом проверяются геометрические размеры швов, наличие подрезов, трещин, непроваров, кратеров и других наружных дефектов.
Задача № 7
По эскизу детали (рисунок 2) разработать эскизы элементов литейной формы, модельных плит, стержневого ящика и собранной литейной формы. Опишите последовательность изготовления формы одним из методов машинной формовки.
Решение:
Исходные данные
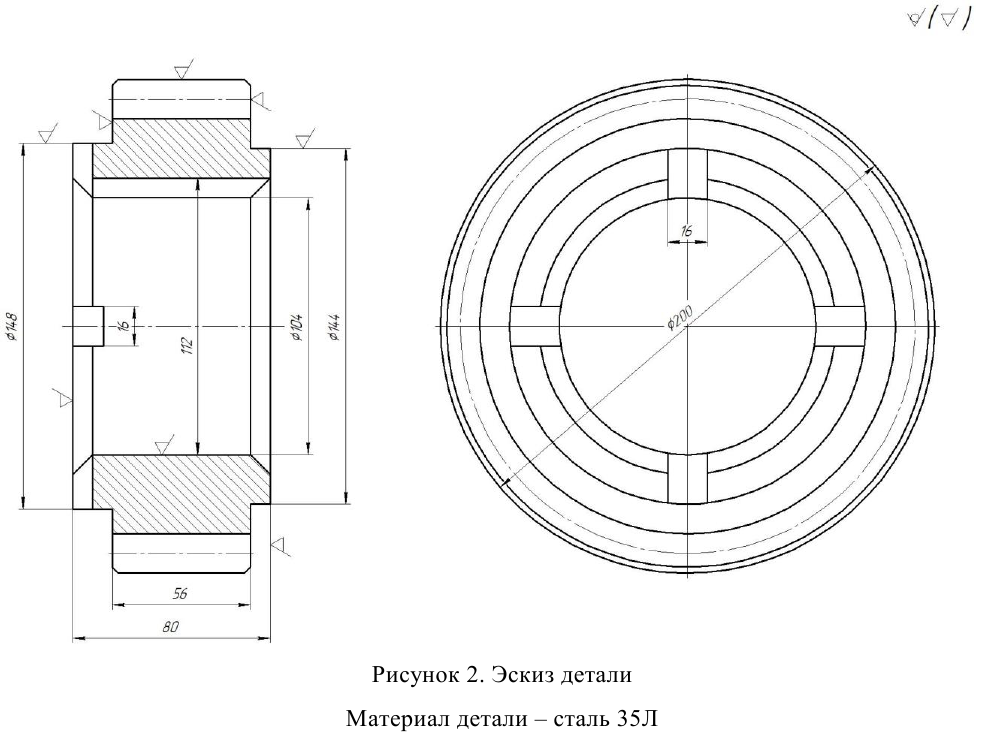
Разработка технологии изготовления литой заготовки
Применяем способ литья — литье в песчано-глинистые формы. Так как деталь имеет простую форму, согласно рекомендациям, принимаем класс точности отливки ряд припусков. В соответствии с ГОСТ 26645-85 это означает, что отливка 8-го класса точности размеров, 8-го класса точности массы.
Оценка технологичности конструкции детали
Заданная деталь имеет небольшие размеры и простое устройство. Это позволяет выполнить ее цельнолитой. Внешнее очертание детали простое и не требует изменений. Замкнутые внутренние полости отсутствуют. Имеющееся сквозное отверстие, выполняется при помощи стержня, имеет достаточные выходы для знаковых частей и стержень надежно фиксируется в форме.
Минимальная толщина стенки 22 мм. Эта толщина вполне обеспечивает благополучное заполнение формы жидким металлом.
Разработка модельно — литейных указаний
Определение положения отливки в форме
Для данной конструкции детали наиболее целесообразно принять положение отливки в форме, как показано на рисунке 3.
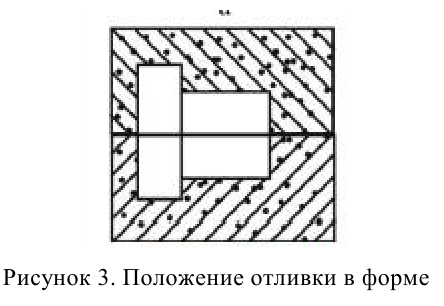
При этом варианте легко устанавливается стержень, имеется возможность его надежного закрепления и контроля всех размеров полости формы.
Определение данных для модельно-литейных указаний и чертежа отливки
Назначаем припуски на механическую обработку, допускаемые отклонения на размеры отливки, припуски на усадку. Допуски на размеры отливки, припуски на механическую обработку выбраны по ГОСТ 26645-85 по 8-му классу точности размеров и 4-му ряду припусков на механическую обработку и литья в песчаные формы отливок, максимальный размер которых менее .
Припуски назначаются на поверхности, подвергаемые механической обработке, и отмеченные на чертеже значком . Значение линейной усадки металла принимаем
.
Результаты определения размеров отливки, модели, стержня сведены в табл. 1.
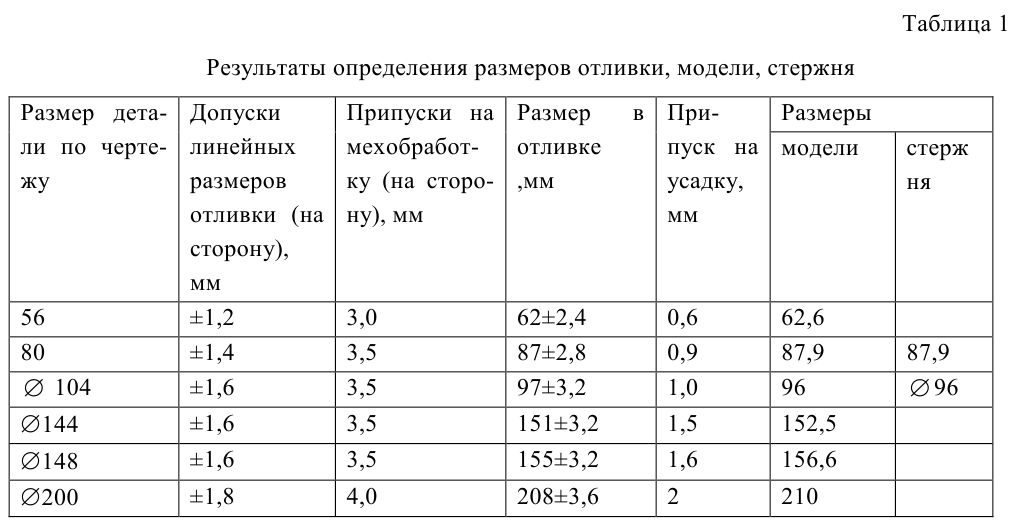
Формовочные уклоны и галтели
Формовочные уклоны на моделях выполняются согласно ГОСТ 3212-80. Для размера модели — уклон
.. Этот уклон выполняется в сторону увеличения размера отливки.
Определение радиуса закругления (галтели)
Толщина сопрягаемых стенок . При этом радиус галтели засчитываем по соотношению:
Результаты определения размеров отливки, модели, стержня
Принимаем радиус галтелей из стандартного ряда. По ГОСТ 2716-44 .
Определение количества стержней, стержневых знаков и их конфигурации
Имеющаяся внутренняя полость отливки может быть выполнена при помощи одного стержня, по положению в форме он будет горизонтальным.
Размеры и уклоны знаковых частей стержней определяем по ГОСТ 3606-80. Размеры и
являются исходными для выбора высоты знака. В соответствии с ГОСТЗ6О6-8О
. Формовочный уклон знака составит
,
.
Боковой зазор между знаком формы и стержнем для модельного комплекта II класса точности из дерева согласно рекомендациям . зазор по высоте согласно этой же таблице
.
Эскиз стержня с расчетными размерами показан на рис. 4.
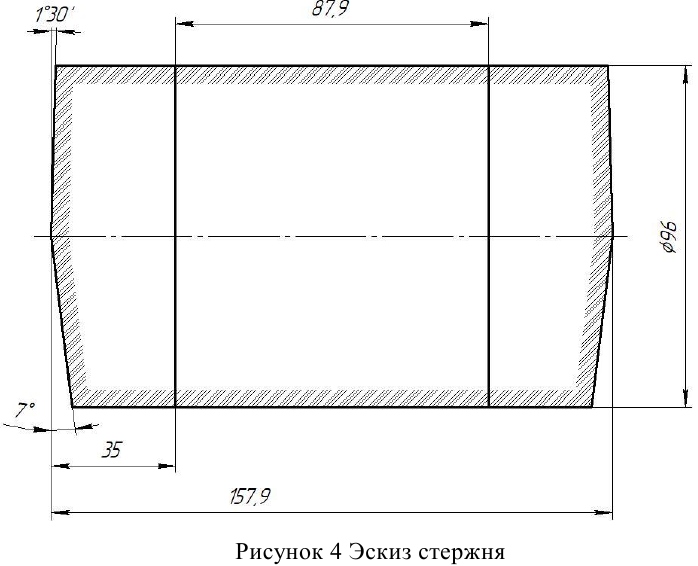
Эскиз стержневого ящика представим на рисунке 5.
На основании расчетов и данных, выбранных по таблицам, выполняем эскиз детали с модельно-литейными указаниями (рис.6) и на его основе составляем эскиз отливки, который изображен на рис. 7.
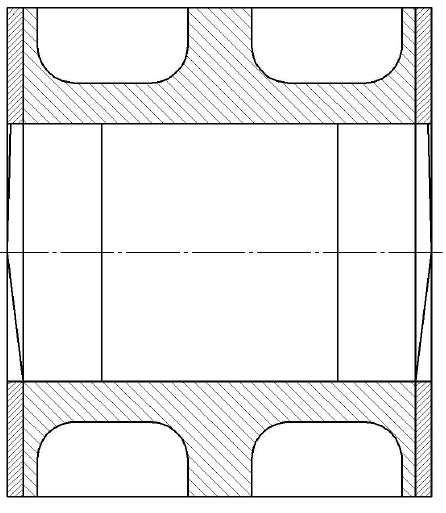
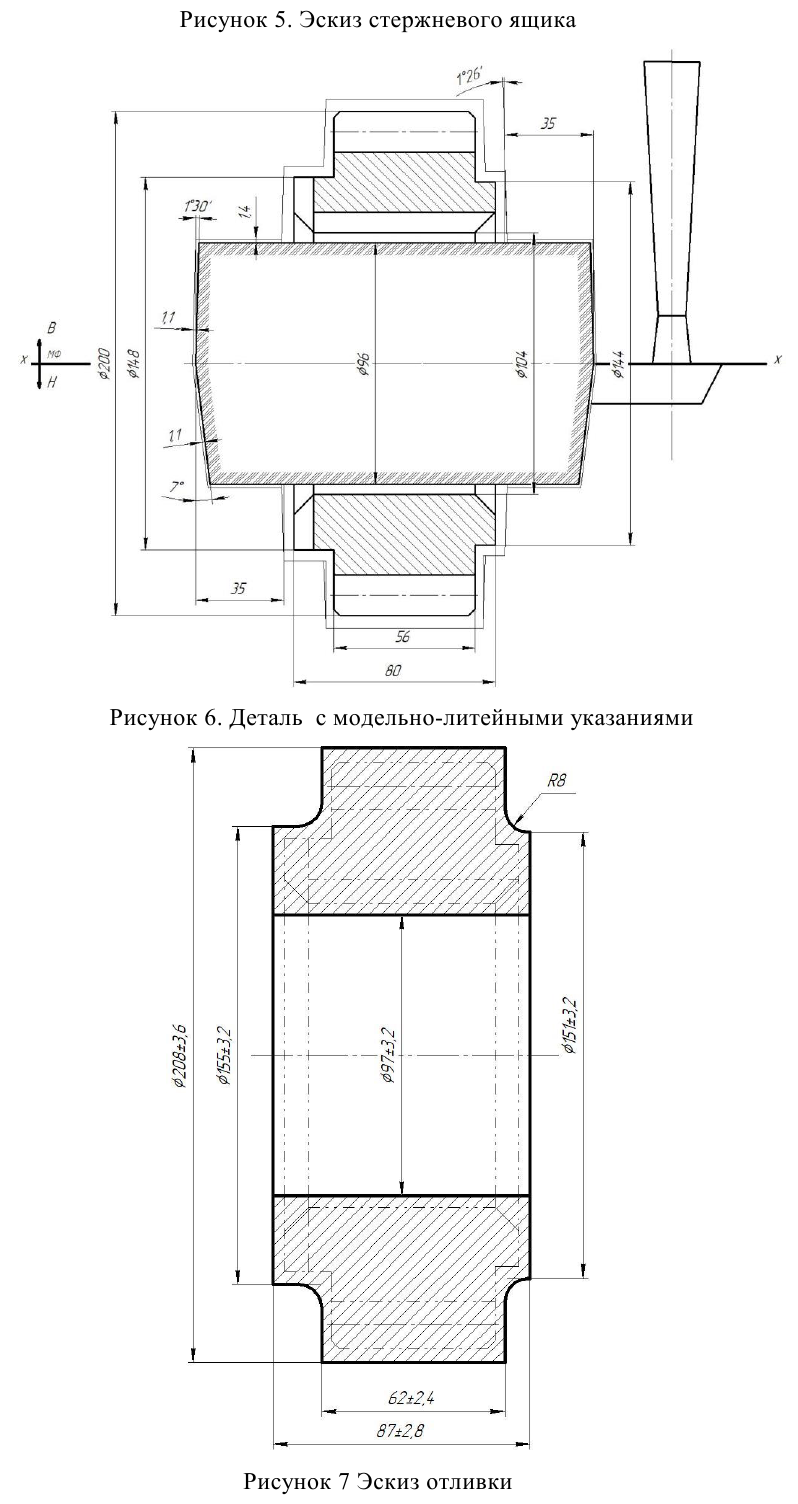
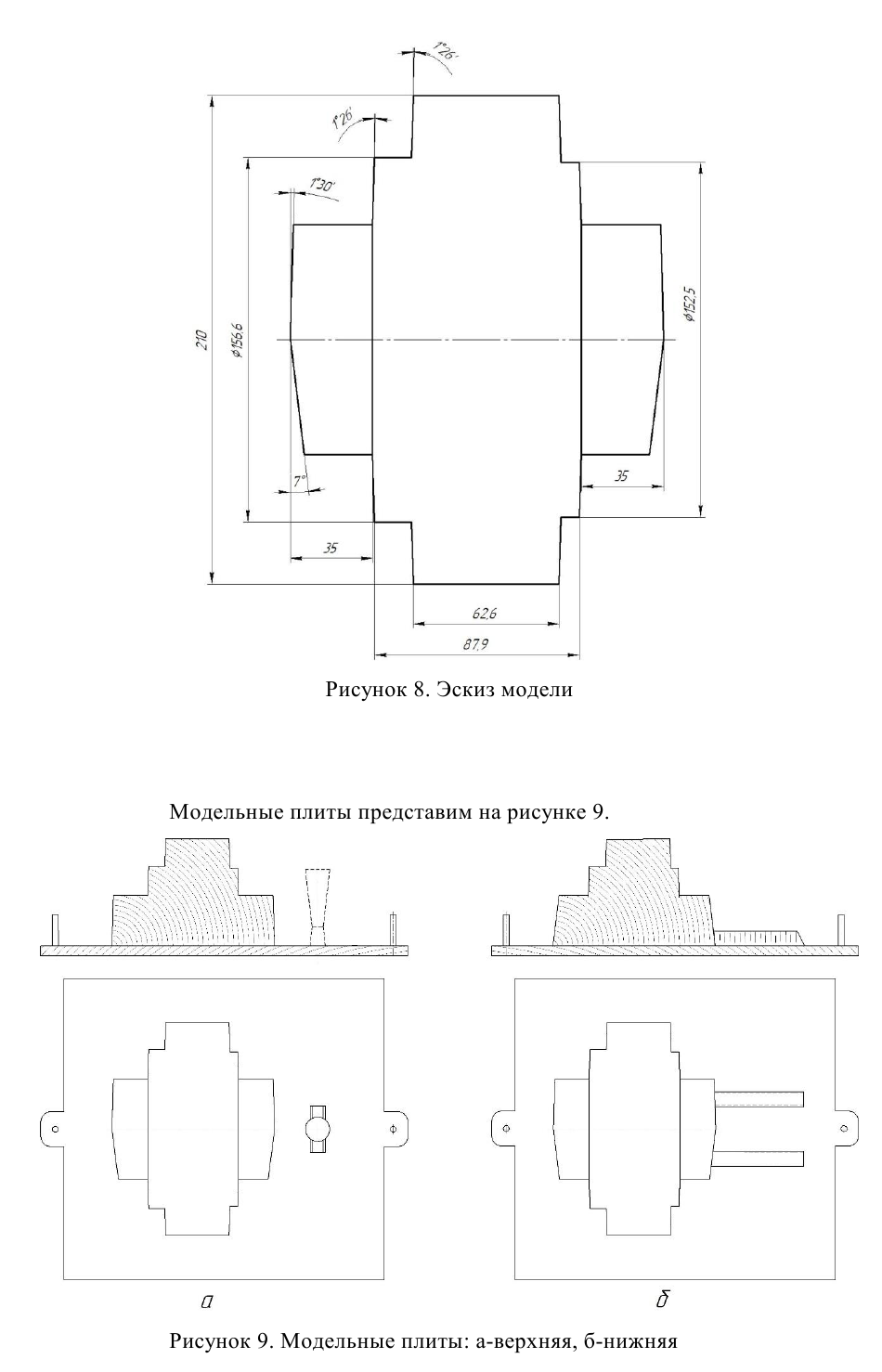
Расчет элементов литниковой системы
Для расчета литниковой системы необходимо определить массу жидкого металла, заливаемого в форму.
Объем полости формы определяем по размеру модели и стержня. Для упрощения расчета принимаем, что полость формы состоит из двух пустотелых цилиндров. На рис. 10 дан упрощенный эскиз полости формы
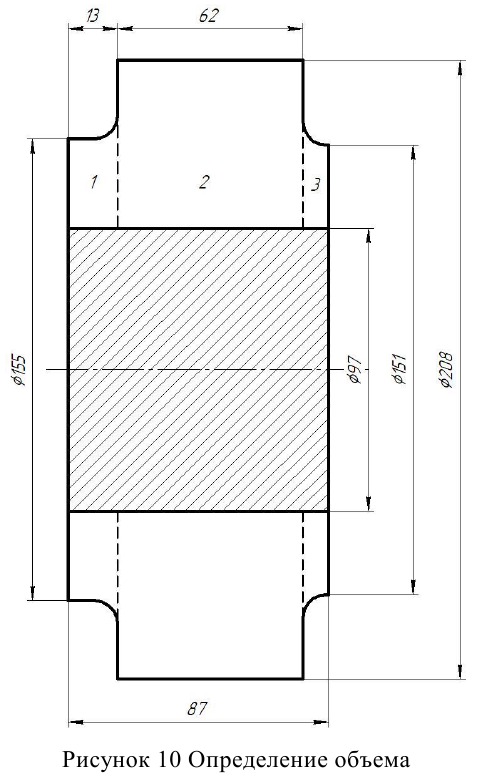

где — общий объем полости формы;
— объемы пустотелых цилиндров. Объем первого пустотелого цилиндра

Объем второго пустотелого цилиндра

Объем третьего пустотелого цилиндра

Таким образом,

Принимая удельную массу жидкой стали , вычисляем массу жидкого металла в форме:
Определим суммарное сечение питателей:
где — масса заливаемого в форму металла, кг;
— коэффициент расхода (общее гидравлическое сопротивление формы движущемуся расплаву);
— объемная масса жидкого металла,
— ускорение свободного падения
— расчетный напор, см.

согласно рекомендациям, принимаем количество питателей:2
Тогда площадь питателя
Руководствуясь ориентировочными соотношениями частей литниковой системы

Площадь поперечного сечения стояка

Площадь поперечного сечения шлакоуловителя,

Определим диаметры элементов литниковой системы.
Площадь поперечного сечсния питателя принимаем трапециевидной формы. Параметры питателя:
Площадь поперечного сечения шлакоуловителя принимаем трапециевидной формы. Принимаем параметры шлакоуловителя. Так как площадь поперечного сечения шлакоуловителя равна , тогда
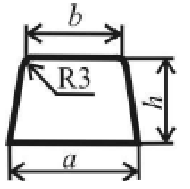

Принимаем поперечное сечение стояка — круглое.
Определим диаметр стояка в нижнем сечении
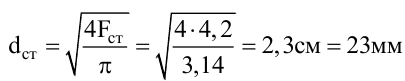
Диаметр верхнего сечения стояка:

Принимаем 30мм.
Выбор размеров опок, составление эскиза формы
Для изготовления формы выбираем опоки прямоугольного сечения. На рис. 11 показана схема расположения отливки в форме, где — длина,
— ширина опоки.
Определяем длину опоки. Согласно рекомендациям

Ширина опоки
Выбираем стандартные длину и ширину:
Высота нижней опоки
Высота верхней опоки
Ближайшая стандартная высота 175 мм. Согласно ГОСТ 2133-75 принимаем нижнюю опоку высотой 175 мм,
Таким образом, для производства литой заготовки — опора должны быть использованы опоки следующих стандартных размеров: верхняя опока и нижняя опока
.
Процесс изготовления форм в парных опоках на машинах идет следующим образом:
- Формовочная смесь транспортным средством (ленточным конвейером, электротсль-фером с бадьей) подастся в бункер, установленный над машиной.
- Пустые верхние и нижние опоки с места выбивки форм подаются к машинам по рольгангам. Как правило, нижнюю полуформу изготовляют на одной машине, а верхнюю на другой. На модель с модельной плитой, закрепленную на столе машины, устанавливают опоку.
- С помощью дозатора опоку заполняют смесью из бункера. Смесь уплотняют. Готовую полуформу снимают с машины и подают на приемное устройство (рольганг), где полуформу отделывают (устраняют дефекты, делают вентиляционные каналы, наносят покрытие) и транспортируют на сборку.
Если форма должна быть высушена, то ее помещают в сушило, после остывания отправляют на сборку.
В массовом производстве легких отливок иногда применяют безопочную формовку, а точнее безопочную заливку, т.к. формовку осуществляют в специальных опоках, которые после изготовления формы снимают. Способ позволяет значительно сократить парк опок и облегчить выбивку отливок.
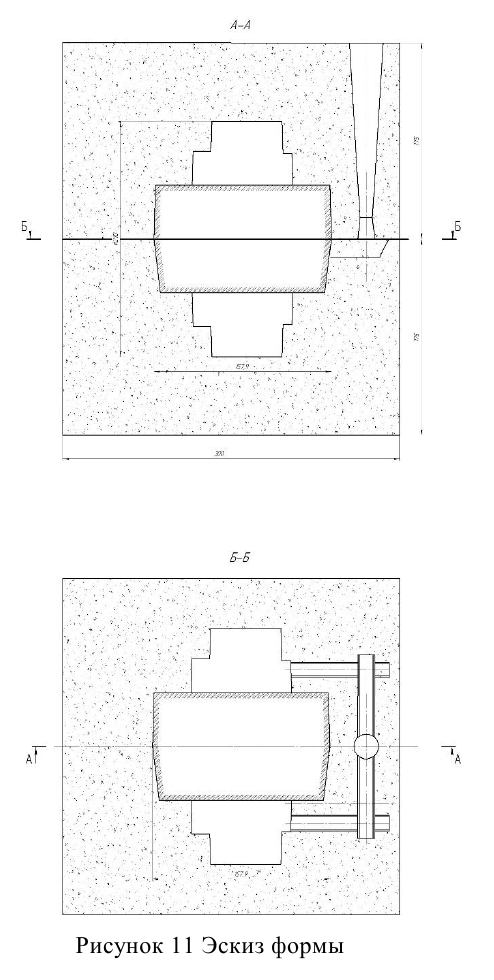
Задача № 8
Опишите микроструктуру и свойства отливок из ковкого чугуна. Приведите примеры маркировки ковкого чугуна по Государственному стандарту. Изложите технологические особенности получения отливок из ковкого чугуна и укажите области их применения.
Решение:
Основной особенностью микроструктуры ковкого чугуна (КЧ), определяющей его свойства, является наличие компактных включений графита, что придаст чугуну высокую прочность и пластичность.
Обсзуглероженный КЧ является единственным конструкционным чугуном, который хорошо сваривается и может быть использован для получения сварноли-тых конструкций.
Детали можно соединять дуговой сваркой в среде защитного газа и стыковой сваркой с оплавлением. Ковкий чугун хорошо поддастся запрессовке, расчеканке и легко заполняет зазоры. Отливки из ферритного КЧ можно подвергать холодной правке, а из перлитного — правке в горячем состоянии.
Применяемый в промышленности ковкий чугун получается в результате графитизи-рующего отжига белого чугуна. Матрица ковкого чугуна может быть, как ферритной, так и перлитной. Основные преимущества ковкого чугуна заключаются в однородности его свойств по сечению, практическом отсутствии напряжений в отливках, высоких механических свойствах и очень хорошей обрабатываемости резанием.
Механические свойства ковкого чугуна регламентируются ГОСТ 1215-79 (табл. 1). В основу маркировки и стандартизации ковкого чугуна положен принцип регламентирования допустимых значений механических свойств при растяжении и
Так же, как в сером и высокопрочном, в ковком чугуне твердость зависит главным образом от матрицы, а прочность и пластичность — от матрицы и графита.
В отличие от чугуна с шаровидным графитом, большое влияние оказывает не только форма, но и количество графита. В связи с этим максимальной прочности можно достичь при дисперсном перлите и малом количестве наиболее компактного графита, а наибольшей пластичности — при феррите и таком же графите.
Кроме свойств, обусловленных ГОСТом, в некоторых случаях представляют интерес и другие свойства, приведенные в табл. 2-4
Влияние химического состава на механические свойства ковкого чугуна проявляется в изменении структуры металла и степени легированности феррита и перлита.
Углерод в ковком чугуне является главным элементом, изменение содержания которого непосредственно определяет механические свойства. Чем выше марка ковкого чугуна, тем ниже должно быть содержание углерода, так как при этом не только уменьшаются количество графита и его размеры, но и улучшается его форма.
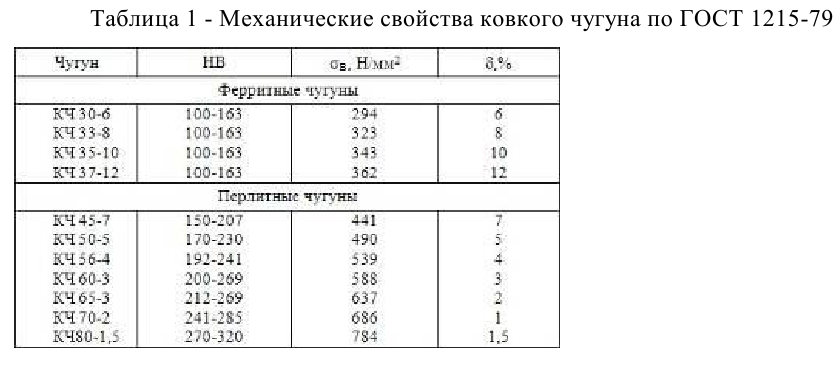
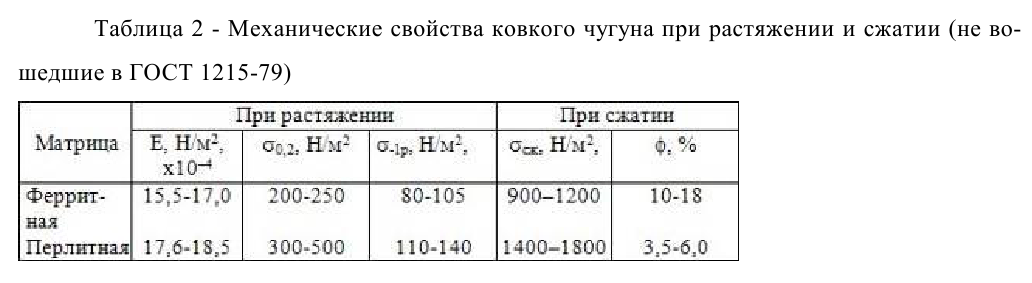
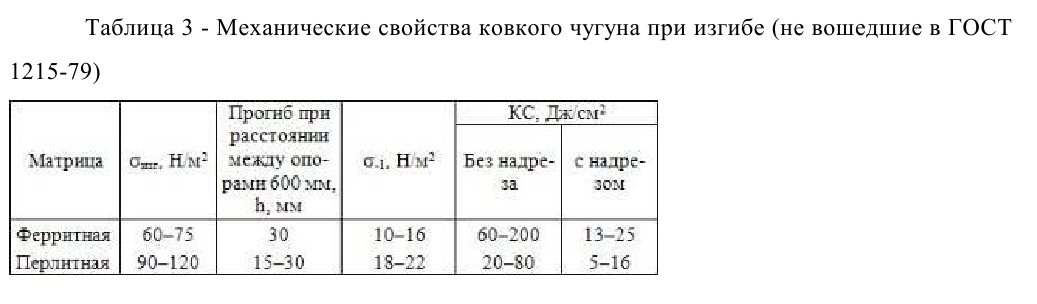
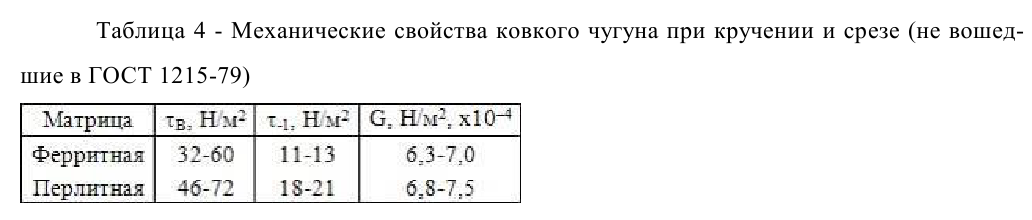
Основные физические свойства ковкого чугуна различных типов приведены в табл.5.
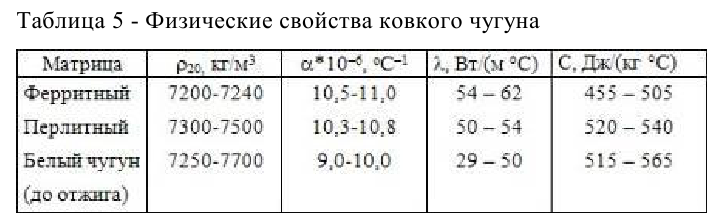
Влияние кремния на свойства ковкого чугуна в целом подобно рассмотренному выше его влиянию на свойства чугуна с шаровидным графитом. Повышение содержания кремния в допускаемых пределах увеличивает предел прочности и твердость и понижает коэффициент температурного расширения вследствие легирования феррита.
Марганец сверх количества, необходимого для связывания серы, оказывая тормозящее влияние на графитизацию и легируя феррит, снижает пластичность ковкого чугуна и повышает при этом прочность и твердость.
Сера, способствуя перлитизации структуры, повышает прочность и твердость ковкого чугуна. В КЧ сера, препятствуя ферритизации структуры, улучшает форму графита. Более совершенная форма графита при повышенном содержании серы делает перлитный ковкий чугун с отношением серы к марганцу в пределах 1,0-2,0 благоприятным конструкционным материалом.
Допустимое содержание фосфора в ковком чугуне обычно принимается до . При повышении содержания фосфора в ковком чугуне механические свойства изменяются подобно механическим свойствам чугуна с шаровидным графитом. Понижение содержания фосфора вызывает смещение порога хрупкости ковкого чугуна в сторону отрицательных температур.
Действие большинства легирующих элементов на механические свойства ковкого чугуна в целом подобно рассмотренному ранее легированию серого чугуна. При этом следует, конечно же, иметь в виду, что технология производства ковкого чугуна предусматривает отжиг.
Маркировка ковких чугунов
По рекомендации ГОСТ 1215—79 маркировка ковкого чугуна содержит первые буквы его названия — КЧ. Следующие за ними две цифры отражают временное сопротивление, иными словами, сопротивление разрушению и деформации — КЧЗО. Третья относится к относительному удлинению — величине пластической деформации материала при растяжении, и обозначается в процентах — КЧЗО-6.
Кроме того, марки ковкого чугуна имеют градацию в зависимости от структуры. Так, к классу ферритных или ферритно-перлитных относятся марки КЧ 30-6; КЧ 33-8; КЧ 35-10; КЧ 37-12. Перлитная структура представлена в ковких чугунах марок: КЧ 45-7; КЧ 50-5; КЧ 55-4; КЧ 60-3; КЧ 65-3; КЧ 70-2; КЧ 80-1,5.
ГОСТ 26358 регламентирует механические свойства марок ковкого чугуна: временное сопротивление разрыву, твердость по Бринеллю , относительное удлинение. Разрешено отклонение только в величине пластической деформации не более
, и то лишь по согласованию с потребителем.
Получение ковкого чугуна
Белый чугун в литом виде вследствие своей высокой твердости и хрупкости не находит широкого применения. Изделия из белого чугуна являются исходным продуктом для получения ковкого чугуна с помощью термической обработки.
Для этой цели используют белый чугун, который содержит и
Исходная структура белого чугуна — перлит и ледебурит. Структура ледебурита встречается во всех белых чугунах, т.е. в железоуглеродистых сплавах с содержанием углерода более , который присутствует в сплаве в форме цементита.
Ледебурит при комнатной температуре представляет механическую смесь перлита и цементита.
Отжиг на ковкий чугун производят в нейтральной среде ( или
) для защиты от обезуглероживания и окисления, в специально предназначенных для этой цели печах непрерывного действия.
Детали укладывают на специальные поддоны, которые размещаются на роликовом поде. Поддоны проталкиваются с определенной скоростью по роликам. Длина камер нагрева первой и второй стадии отжига назначается с таким расчетом, чтобы детали находились в камерах необходимое для данной температуры время. Отжиг на ковкий чугун производится по режиму, показанному на рис. 1.
Первая стадия отжига преследует цель разложения цементита, входящего в состав ледебурита; в перлите цементит сохраняется.
Вторая стадия отжига преследует цель разложения цементита, входящего в состав перлита.
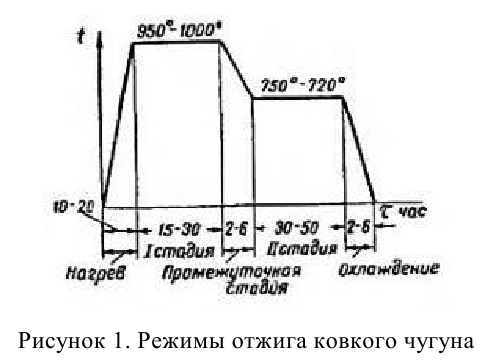
В результате прохождения только одной стадии отжига получают ковкий чугун со структурой псрлит+фсррит+углсрод отжига.
Такой чугун называют перлитным (перлитно-ферритным, рис. 2, а)
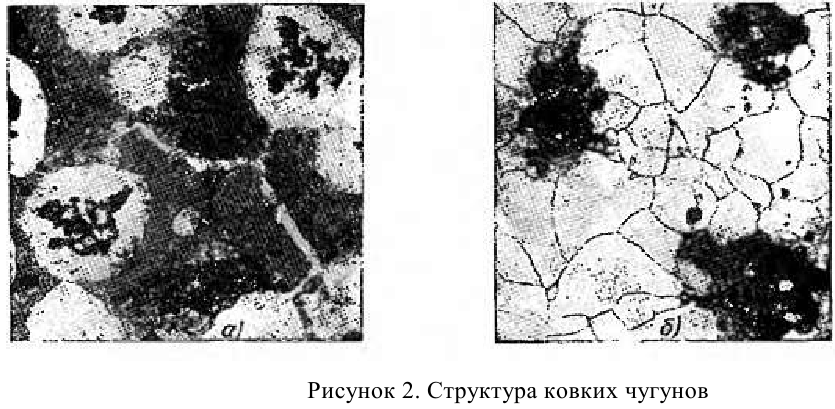
Он обладает хорошими прочностными свойствами, но невысокой пластичностью. Чугун с такой структурой используется в деталях, работающих на изгиб и трение.
Для повышения прочности чугун можно подвергать закалке и высокому отпуску, что улучшает его механические свойства.
После полного цикла отжига структура чугуна состоит из феррита и углерода отжига, т.е. образуется ферритный ковкий чугун фис. 2, б).
Применяют и другой способ получения ковкого чугуна
Нагрев изделий производится в окислительной среде, вследствие чего происходит выгорание углерода с поверхности, вызывающее снижение твердости и некоторое повышение пластических свойств, а также улучшение обрабатываемости.
В центре такой чугун сохраняет структуру белого чугуна. Полученный этим методом чугун называют белоссрдечным в отличие от черноссрдечного, получаемого при отжиге в нейтральной среде по вышеописанному способу.
При таком способе детали из белого чугуна загружают в ящики, пересыпают окалиной или рудой и нагревают в обычных камерных печах.
Отжиг ковкого чугуна является весьма длительной операцией. В настоящее время разработано много способов ускоренного отжига ковкого чугуна — предварительная закалка, отжиг в расплавленных солях при очень высоких температурах и др.
Все эти мероприятия сокращают длительность отжига на ковкий чугун. При плавке в вагранках обычно получают серый чугун, содержащий более углерода. Поэтому чугун с более низким содержанием углерода обычно получают последовательной плавкой в двух печах: вагранке и электропечи.
Шихтовые материалы сначала расплавляют в вагранке, а получаемый из нее расплав сливают в электрическую дуговую печь, где он дополнительно разогревается и доводится до требуемого химического состава. Таким путем удается получить чугун с более низким содержанием углерода и кремния.
На рис.3 показана схема трехфазной дуговой электропечи для получения ковкого чугуна. Через свод в полость печи входят три графитовых электрода 1, которым подводится от трансформатора трехфазный электрический ток. Между электродами и ванной расплава образуется электрическая дуга, служащая источником тепла.
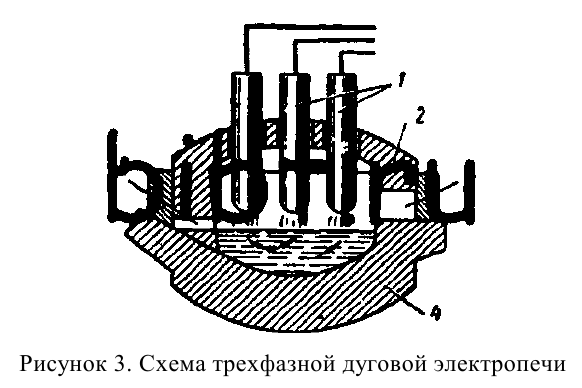
Подина печи 4 опирается на специальное устройство, благодаря чему печь может поворачиваться для слива расплава в разливочные ковши. Свод печи 2 съемный, что облегчает ее ремонт. Движение электрода вверх и вниз осуществляется автоматически в зависимости от электросопротивления дуги. При увеличении расстояния от поверхности расплава до конца электрода сопротивление дуги увеличивается и привод опускает электрод; при уменьшении сопротивления дуги электрод поднимается.
Процесс доводки расплава по химическому составу в такой печи протекает непрерывно. Расплав из вагранки заливается в печь через заливочное окно 3 и после доводки химического состава его сливают в ковши через окно 5 для транспортировки к местам заливки литейных форм. Полученные отливки подвергаются отжигу и называются отливками из ковкого чугуна.
Применение ковкого чугуна
Отливки из ковкого чугуна широко используются во многих отраслях промышленности для широкого спектра номенклатуры деталей ответственного назначения: автомобилестроение, тракторное и сельскохозяйственной машиностроение, вагоностроение, судостроение, электропромышленность, станкостроение, санитарно-техническое и строительное оборудование, тяжелое машиностроение и пр. При этом масса отливок может быть от нескольких граммов до , минимальная толщина стснок отливки
, максимальная для обезуглероженного чугуна
, для графитизированного
, а в отдельных случаях до
.
Можно с уверенностью утверждать, что, обладая механическими свойствами, близкими к литой стали и ЧШГ, высоким сопротивлением ударным нагрузкам при комнатной и низких температурах, износостойкостью, лучшей, чем ЧШГ, обрабатываемостью резанием и свариваемостью, КЧ сохранит в ближайшие годы свое применение, особенно для мелких отливок, сварных конструкций, несмотря на склонность к образованию трещин и энергоемкость получения готовых отливок.
Отливки из ковкого чугуна применяют для деталей, работающих при ударных и вибрационных нагрузках. Из ферритных чугунов изготавливают картеры редукторов, ступицы, крюки, скобы, хомутики, муфты, фланцы.
Из перлитных чугунов, характеризующихся высокой прочностью, достаточной пластичностью, изготавливают вилки карданных валов, звенья и ролики цепей конвейера, тормозные колодки.
Задача № 9
Опишите методику измерения механических свойств металла -упругости, текучести, пластичности и прочности. Запишите определения свойствам. Зарисуйте диаграмму растяжения. Выполните расчеты показателей упругости, текучести, прочности, пластичности. Запишите определения.
Предел прочности , предел текучести
, относительное удлинение
и относительное сужение
определяют при испытании на растяжение. Испытания проводят на разрывных машинах с использованием стандартных образцов с площадью поперечного сечения
и рабочей (расчетной) длиной
.
Чтобы определить прочность металла, работающего на растяжение, изготовляют образец и устанавливают его в зажимы (или захваты) разрывной машины. Для этих целей чаще всего используют машины с гидравлической системой передачи усилия или с винтовой системой.
Растягивающая сила создает напряжение в испытываемом образце и вызывает его удлинение. Когда напряжение превысит прочность образца, он разорвется. В результате проведения испытаний получают диаграмму растяжения (рис. 1). На оси абсцисс указывается значение деформации, на оси ординат — значение нагрузки, которая прилагается к образцу.
Предел прочности — это максимальная нагрузка, которую выдерживает материал без разрушения, отнесенная к начальной площади поперечного сечения образца
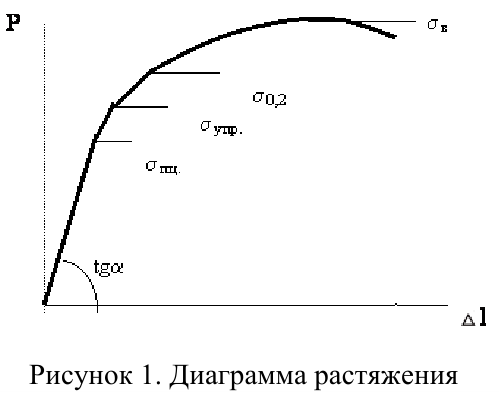
При растяжении образец удлиняется, а его поперечное сечение непрерывно уменьшается. Истинное напряжение определяется делением действующей в определенный момент нагрузки на площадь, которую образец имеет в этот момент.
Истинные напряжения в повседневной практике не определяют, а пользуются условными напряжениями, считая, что поперечное сечение образца остается неизменным.
Предел текучести — это нагрузка, при которой происходит пластическая деформация, отнесенная к начальной площади поперечного сечения образца
Однако при испытаниях на растяжение у большинства сплавов площадки текучести на диаграммах нет.
Поэтому определяется условный предел текучести — напряжение, которому соответствует пластическая деформация
. Выбранное значение
достаточно точно характеризует переход от упругих деформаций к пластическим.
К характеристикам материала относят также предел упругости (апр), под которым подразумевают напряжение, при котором пластическая деформация достигает заданного значения. Обычно используют значения остаточной деформации . Таким образом,
(
— нагрузка, при которой остаточное удлинение составляет
).
Пластичность характеризуется относительным удлинением и относительным сужением
:
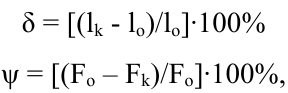
где — конечная длина образца;
и
— начальные длина и площадь поперечного сечения образца;
— площадь поперечного сечения в месте разрыва.
Для малопластичных материалов испытания на растяжение вызывают затруднения, поскольку незначительные перекосы при установке образца вносят существенную погрешность в определение разрушающей нагрузки. Такие материалы, как правило, подвергают испытанию на изгиб.
Исходные данные к заданию №1

Определим механические свойства материала:
Предел прочности на растяжение:
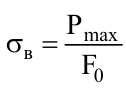
— максимальная нагрузка, выдерживаемая образцом;
— площадь поперечного сечения образца.
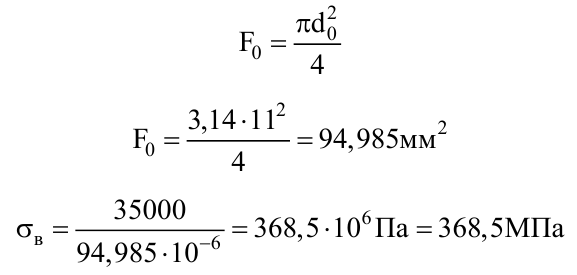
Предел текучести
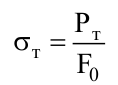
— это нагрузка, при которой происходит пластическая деформация.

Предел упругости:
— нагрузка, при которой остаточное удлинение составляет
.
Определим показатели пластичности: относительное удлинение:

где — конечная длина образца,
— начальная длина образца

-относительное сужение

— площадь поперечного сечения в месте разрыва,
— начальная площадь поперечного сечения образца
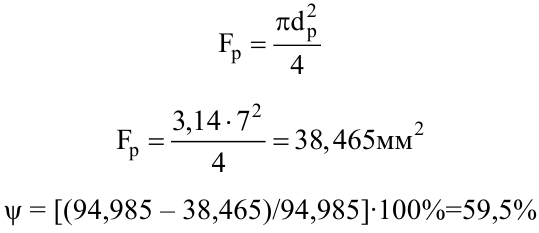
Задача № 10
Опишите технологический процесс выполнения закалки алюминиевых сплавов (AЛ28) Запишите цель процесса, технологию выполнения.
Закалка алюминиевых сплавов заключается в нагреве их до температуры, при которой легирующие компоненты, находящиеся в интерметаллидных фазах, полностью или частично растворяются в алюминии, выдержке при этой температуре и быстром охлаждении до низкой температуры ().
В результате такой обработки структура, свойственная температуре нагрева, может быть получена при комнатной температуре, так как при быстром охлаждении распад твердого раствора (выделение интерметаллидных фаз) не успевает происходить.
Содержание легирующих компонентов в алюминиевом твердом растворе после закалки значительно превышает их предельную равновесную концентрацию при комнатной температуре, т.е. при комнатной температуре твердый раствор пересыщен (и, как правило, в очень сильной степени). Так, если сплав нагреть до температуры t3, выдержать некоторое время, необходимое для полного растворения 9-фазы
в алюминии, и охладить в воде до комнатной температуры, то твердый раствор, содержащий
, в результате быстрого охлаждения будет сохранен или, как часто говорят, зафиксирован при комнатной температуре.
Поскольку равновесная растворимость меди в алюминии при низких температурах составляет около , твердый раствор в закаленном сплаве
Си пересыщен медью более чем в 20 раз.
Пересыщенный твердый раствор легирующих компонентов в алюминии, который получают в сплавах в результате закалки, определяет повышение прочности после закалки и возможность дальнейшего упрочнения при старении.
Рассмотрим основные принципы выбора режима закалки алюминиевых сплавов. Температура нагрева под закалку должна обеспечить как можно более полное растворение интерметаллидных фаз в алюминии.
Если содержание легирующих компонентов в сплавах не превышает их предельной растворимости при эвтектической температуре (например, в сплавах
, то легирующие компоненты практически полностью могут быть растворены при нагреве под закалку; температура нагрева в этом случае должна быть выше критической точки tv. Если содержание легирующих компонентов превышает предельную растворимость, т.е. в структуре сплава в равновесных условиях имеются включения эвтектических или первичных кристаллов интерметаллидных фаз (например, в сплаве с
), то полное растворение интерметаллидных фаз невозможно.
В этом случае ориентиром для выбора температуры нагрева под закалку служит температура солидус (как правило, температура плавления наиболее легкоплавкой эвтектики); нагрев проводят до температуры на ниже линии солидус.
При закалке литейных алюминиевых сплавов следует иметь в виду, что в структуре сплавов может быть неравновесная эвтектика. Поэтому температура нагрева под закалку литейных сплавов не должна превышать температуры плавления неравновесной эвтектики. Приведенные выше соображения по выбору температуры гомогенизации полностью относятся к выбору температуры нагрева под закалку литейных алюминиевых сплавов. Температура нагрева под закалку различных промышленных сплавов колеблется в пределах от до
.
Выдержка при температуре нагрева под закалку должна обеспечить растворение интерметаллидных фаз, поэтому она зависит от величины частиц и характера их распределения. В деформированных изделиях интерметаллидные фазы находятся в основном в виде мелких вторичных кристаллов (сплав уже подвергнут гомогенизации и ряду технологических нагревов), а в отливках — в виде довольно грубых эвтектических включений.
Отсюда различная продолжительность выдержки при температуре нагрева под закалку: для деформируемых сплавов она измеряется десятками минут, а для литейных — часами или даже десятками часов.
Охлаждение при закалке следует проводить с такой скоростью, которая обеспечит отсутствие распада твердого раствора в процессе охлаждения. Эта скорость должна быть больше некоторой определенной для каждого сплава критической скорости охлаждения , которая определяется как наименьшая скорость охлаждения сплава, при которой распад твердого раствора в процессе охлаждения еще не происходит.
В промышленности большинство алюминиевых сплавов при закалке охлаждают в воде (как правило, в холодной, иногда в подогретой). Скорость охлаждения тонкостенных изделий в холодной воде значительно превышает критическую скорость охлаждения любого алюминиевого сплава, т.е. удовлетворяет главному требованию, предъявляемому к охлаждению при закалке.
Однако охлаждение в воде не может рассматриваться как оптимальный вариант закалки во всех случаях. Очень высокая скорость охлаждения при закалке в воде приводит к образованию больших внутренних напряжений, которые обусловливают коробление изделий.
Это особенно проявляется в крупногабаритных изделиях сложной конфигурации (штамповки, панели), правка которых после закалки -весьма трудоемкая и дорогостоящая операция. Выбор для каждого сплава охлаждающих сред, обеспечивающих охлаждение со скоростью больше критической, но меньше, чем в воде, — актуальная задача.
После закалки сплавы, обладая повышенной по сравнению с отожженным состоянием прочностью, сохраняют высокую пластичность. Однако роль закалки, как уже отмечалось, не ограничивается ее непосредственным влиянием на свойства.
Обусловливая получение пересыщенных твердых растворов легирующих компонентов в алюминии, закалка обеспечивает возможность дальнейшего повышения прочности при старении.
AЛ 28 — алюминиевый литейный сплав, относится к системе — сплав алюминия с магнием. Согласно ГОСТ 1583-93 данный сплав не подвергается термической обработке:
Полный химический состав сплава представим в таблице 1.
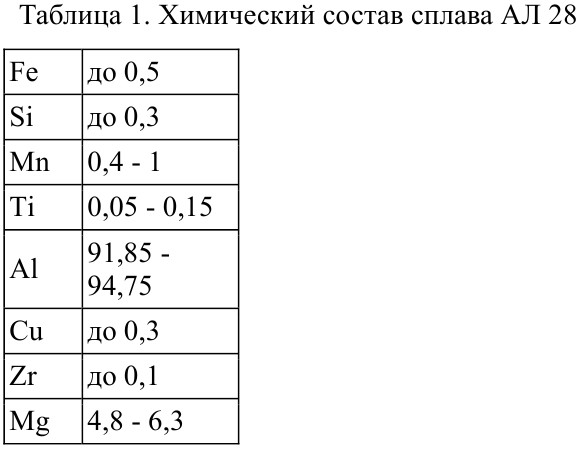
Сплавы этой системы относятся к группе термически не упрочняемых, высокие свойства их достигаются вследствие увеличения концентрации магния в пересыщенном твердом растворе.
Задача № 10
Выполните выбор материала для изготовления судовой металлической мебели. Ответ обосновать. Записать маркировку и расшифровку выбранного материала.
Судовая металлическая мебель является мебелью специального назначения. Основными ее преимуществами являются прочность, долговечность, ремонтопригодность. Помимо этого, металлическая мебель — самая гигиеничная.
Металлическая мебель относится к негорючей судовой мебели, что позволяет резко сократить пожароопасность в судовых помещениях и снизить опасность отравления токсичными продуктами горения в случаях возникновения пожара.
Мебель, как правило, изготавливается из алюминиево-магниевого сплава, из штампованной тонколистовой стали, нержавеющей стали для камбузных, медицинских, служебных, хозяйственных или жилых помещений.
Примем для изготовления судовой мебели наиболее дешевый алюминиево -магниевый сплав . Алюминиево-магниевый сплав обладает высокими антикоррозионными свойствами, что является приоритетным свойством для судовой мебели.
Алюминий в судостроении, в виде алюминиево-магниевых сплавов, получил широкое распространение. И потому часто носит различные имена: морской алюминий, корабельный алюминий, судовой алюминий, лодочный алюминий.
Все эти названия связаны это с отличной коррозийной стойкостью алюминиево-магниевых сплавов (с содержанием магния от 3 до 6 %) как в пресной воде, так и морской воде. Безусловным важным качеством судового алюминия является хорошая свариваемость и хорошие прочностно-механические свойства.
— алюминиевый деформируемый сплав.
Сплав применяют для изготовления малонагруженных конструкций: легких переборок, трубопроводов, арматуры, бачков, а также для внутренней отделки судов; хорошо свариваются контактной и аргонно-дуговой сваркой, несколько хуже газовой.
Полный химический состав представим в таблице 1.
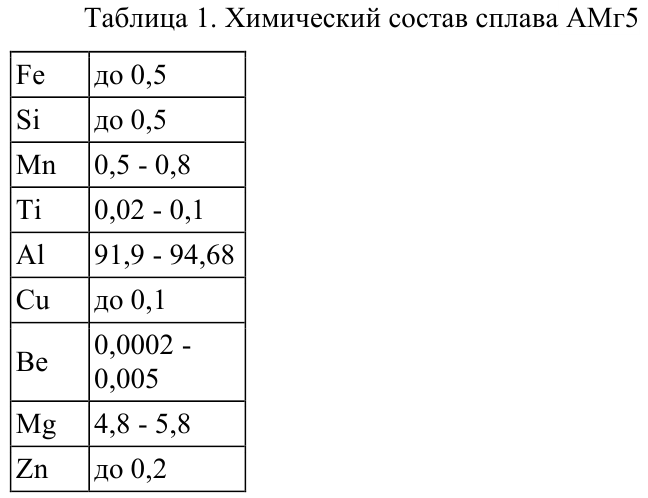
Задача № 12
Выполните расшифровку марки сплава: Выполните расшифровку марки сплава
-бронза оловянная литейная, содержащая олова
цинка
свинца
никеля
остальное медь
КЧ 35 — 5 — ковкий чугун, предел прочности при растяжении — , относительное удлинение при растяжении —
БрКМц 3-1 — бронза безоловянная, обрабатываемая давлением, содержащая кремния марганца
меди
08Х18Г8Н2Т — сталь коррозионно-стойкая, содержащая углерода
хрома
марганца
никеля
титана
Л92 — латунь, обрабатываемая давлением, содержащая меди
остальное цинк.
40ХН2МА — сталь конструкционная легированная, высококачественная, содержащая углерода
никеля
молибдена
ВСт 5 — сталь обыкновенного качества, порядковый номер сплава 5, содержащая углерод с гарантированным химическим составом и свойствами.
У13- Сталь инструментальная углеродистая, содержащая
Задача № 13
Определите по эмпирической формуле скорость резания при подрезке торца с диаметра до диаметра
у заготовки из стали
с пределом прочности
. Заготовка — отливка с коркой. Резец токарный подрезной торцовый, оснащенный пластинкой из твердого сплава
Глубина резания подача
период стойкости резца
Геометрические параметры резца: форма передней поверхности — радиусная с фаской
Рассчитаем скорость резания по эмпирической зависимости в соответствии с заданными условиями обработки [1]:
где — коэффициенты, зависящие от свойств инструментального и обрабатываемого материала
— поправочный коэффициент, определяется по формуле:
— коэффициент, учитывающий материал заготовки
— коэффициент, учитывающий состояние поверхности
— коэффициент, учитывающий материал инструмента
— коэффициент, учитывающий много инструментальную обработку
— коэффициенты, учитывающие геометрию резца
Ответ:
Задача № 14
На токарно — винторезном станке обтачивается заготовка из серого чугуна, твердость которого
твердосплавным резцом.
Глубина резания подача
скорость резания
Геометрические параметры резца: форма передней поверхности — плоская,
Определите по эмпсрической формуле силу резания мощность
. Достаточна ли мощность станка для работы с указанными режимами резания.
Определяем тангенциальную составляющую силы резания:
где — коэффициенты, зависящие от свойств инструментального и обрабатываемого материала [1, стр. 273];
— поправочный коэффициент, определяется по формуле:
— коэффициент, учитывающий материал заготовки
-коэффициенты, учитывающие геометрию резца [1, стр.275]
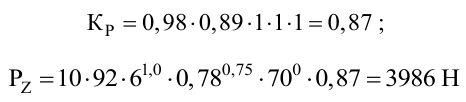
Определим мощность резания.
Мощность резания определяется по формуле:
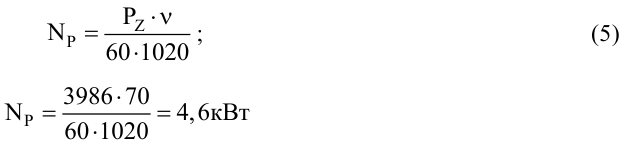
Мощность станка согласно паспортным данным составляет:
Эффективная мощность станка:
где
— кпд станка, принимается
Так как мощность резания меньше эффективной мощности станка , то данный станок применим при заданных режимах резания.
Задача № 15
Напишите в общем виде уравнение кинематической цепи главного движения и уравнение кинематической цепи подач. Пользуясь этими уравнениями, посчитайте максимальную частоту вращения шпинделя и минимальную продольную подачу токарно-винторезного станка . Начертите кинематическую схему станка
в положении цепей согласно заданию.
Уравнение кинематического баланса цепи главного движения в общем виде можно записать:
где — частота вращения шпинделя, об/мин;
— частота вращения электродвигателя, об/мин;
и
— диаметры ведущего и ведомого шкивов клинорсмснной передачи, мм;
— коэффициент проскальзывания ремня;
— общее передаточное отношение коробки скоростей.
Уравнение кинематической цепи продольной подачи в общем виде:

— передаточное отношение звена увеличения шага;
— передаточное отношение гитары сменных колёс;
— передаточное отношение коробки подач;
— длина делительной окружности реечного колеса.
Определим максимальную частоту вращения шпинделя. Выбираем зубчатые пары, имеющие наибольшее передаточное отношение.

Определим минимальную продольную подачу

Начертим кинематическую схему станка в положении цепей согласно заданию. Кинематическую схему представим на рисунке 1.
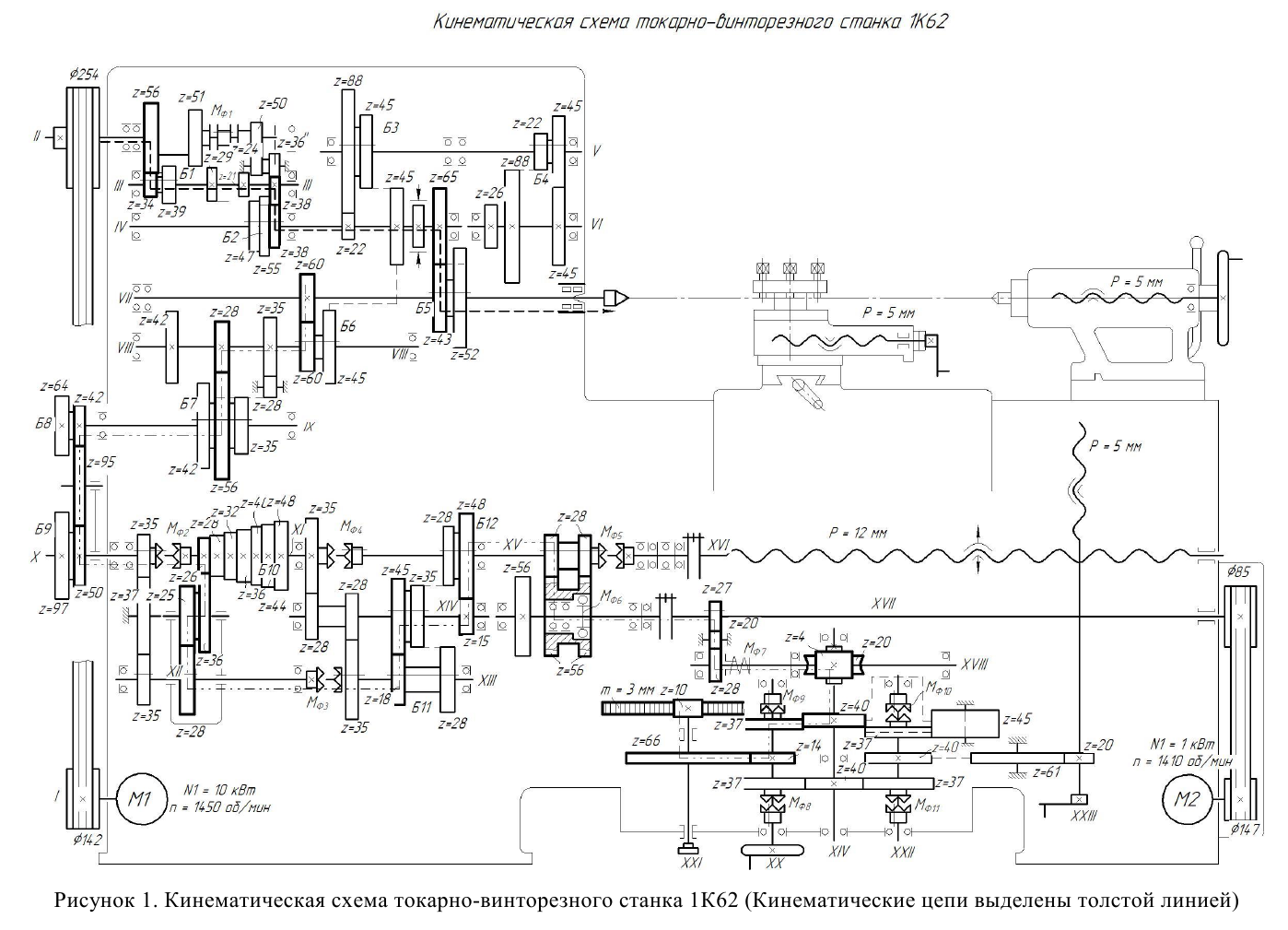
Задача № 18
Начертите схему сверления отверстия и укажите на ней элементы резания при сверлении. Дайте определение глубины резания подачи
скорости резания
машинного времени.
Схему сверления представим на рисунке 2.
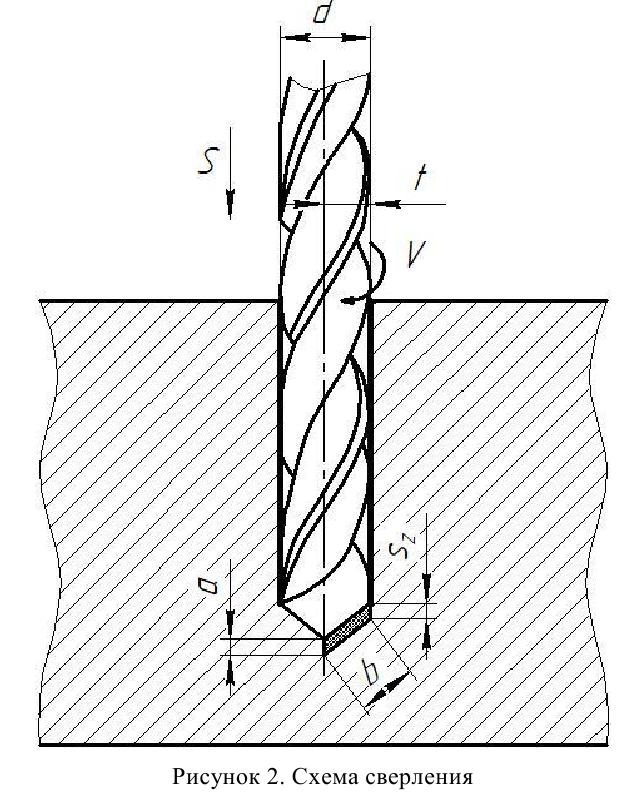
Каждый зуб сверла срезает слой металла шириной и толщиной
данные параметры определяются по формулам:
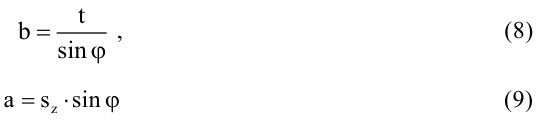
глубина резания, [мм] — расстояние между обрабатываемой и обработанной поверхностями, измеренное по нормали к последней. Кстати готовые на продажу задачи тут, и там же теория из учебников может быть вам поможет она.
При сверлении отверстий в сплошном материале за глубину резания принимают половину диаметра сверла:

Скорость резания За скорость резания при сверлении принимают окружную скорость точки режущей кромки, наиболее удаленной от оси сверла. Скорость резания связана с диаметром сверла и частотой его вращения зависимостью:
где — диаметр сверла, мм;
— частота вращения сверла, об/мин.
Подача — равна осевому перемещению сверла за один оборот. При сверлении подачу на оборот назначают в зависимости от диаметра сверла и обрабатываемого отверстия d:
Подача на зуб определяется по формуле:
где — число зубьев сверла.
Готовые задачи по материаловедению
На этой странице я собрала задачи с решением по всем темам материаловедения, надеюсь они вам помогут.
Если что-то непонятно — вы всегда можете написать мне в WhatsApp и я вам помогу! |
Пример № 1
Механизм и физическая сущность процесса кристаллизации.
Решение:
Любое вещество может находиться в трех агрегатных состояниях: твердом, жидком, газообразном. Возможен переход из одного состояния в другое, если новое состояние в новых условиях является более устойчивым, обладает меньшим запасом энергии.
С изменением внешних условий свободная энергия изменяется по сложному закону различно для жидкого и кристаллического состояний. Характер изменения свободной энергии жидкого и твердого состояний с изменением температуры показан на рисунке 1.
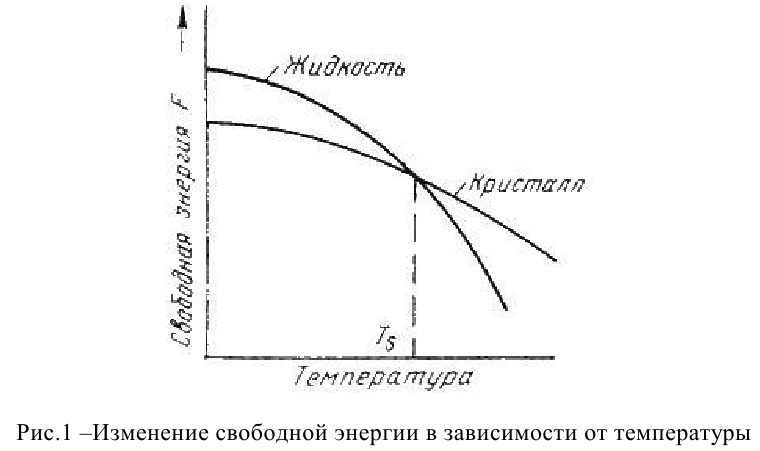
В соответствии с этой схемой выше температуры вещество должно находиться в жидком состоянии, а ниже
— в твердом.
При температуре равной жидкая и твердая фаза обладают одинаковой энергией, металл в обоих состояниях находится в равновесии, поэтому две фазы могут существовать одновременно бесконечно долго. Температура
— равновесная или теоретическая температура кристаллизации.
Для начала процесса кристаллизации необходимо, чтобы процесс был термодинамически выгоден системе и сопровождался уменьшением свободной энергии системы. Это возможно при охлаждении жидкости ниже температуры . Температура, при которой практически начинается кристаллизация называется фактической температурой кристаллизации. Охлаждение жидкости ниже равновесной температуры кристаллизации называется переохлаждением, которое характеризуется степенью переохлаждения
:
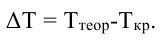
Степень переохлаждения зависит от природы металла, от степени его загрязненности (чем чище металл, тем больше степень переохлаждения), от скорости охлаждения (чем выше скорость охлаждения, тем больше степень переохлаждени).
При нагреве всех кристаллических тел наблюдается четкая граница перехода из твердого состояния в жидкое. Такая же граница существует при переходе из жидкого состояния в твердое.
Кристаллизация — это процесс образования участков кристаллической решетки в жидкой фазе и рост кристаллов из образовавшихся центров.
Процесс перехода металла из жидкого состояния в кристаллическое можно изобразить кривыми в координатах время — температура. Кривая охлаждения чистого металла представлена на рисунке 2.
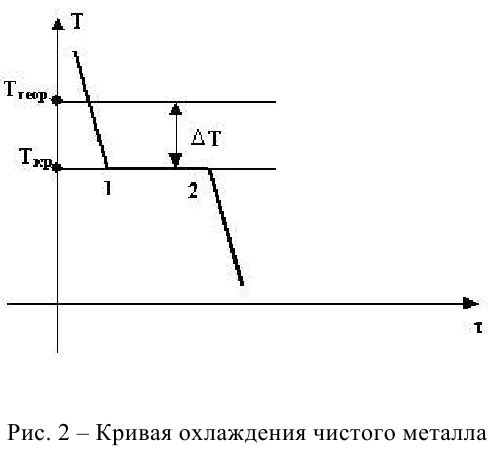
— теоретическая температура кристаллизации;
— фактическая температура кристаллизации.
Процесс кристаллизации чистого металла:
До точки 1 охлаждается металл в жидком состоянии, процесс сопровождается плавным понижением температуры. На участке 1 — 2 идет процесс кристаллизации, сопровождающийся выделением тепла, которое называется скрытой теплотой кристаллизации. Оно компенсирует рассеивание теплоты в пространство, и поэтому температура остается постоянной. После окончания кристаллизации в точке 2 температура снова начинает снижаться, металл охлаждается в твердом состоянии.
Механизм кристаллизации металлов:
При соответствующем понижении температуры в жидком металле начинают образовываться кристаллики — центры кристаллизации или зародыши. Для начала их роста необходимо уменьшение свободной энергии металла, в противном случае зародыш растворяется.
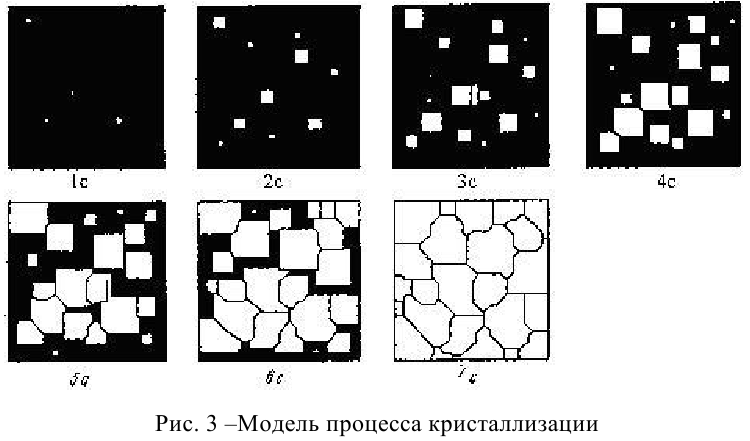
Центры кристаллизации образуются в исходной фазе независимо друг от друга в случайных местах. Сначала кристаллы имеют правильную форму, но по мере столкновения и срастания с другими кристаллами форма нарушается. Рост продолжается в направлениях, где есть свободный доступ питающей среды. После окончания кристаллизации имеем поликристаллическое тело.
Таким образом, процесс кристаллизации состоит из образования центров кристаллизации и роста кристаллов из этих центров.
В свою очередь, число центров кристаллизации (ч.ц.) и скорость роста кристаллов (с.р.) зависят от степени переохлаждения (рисунок 4).
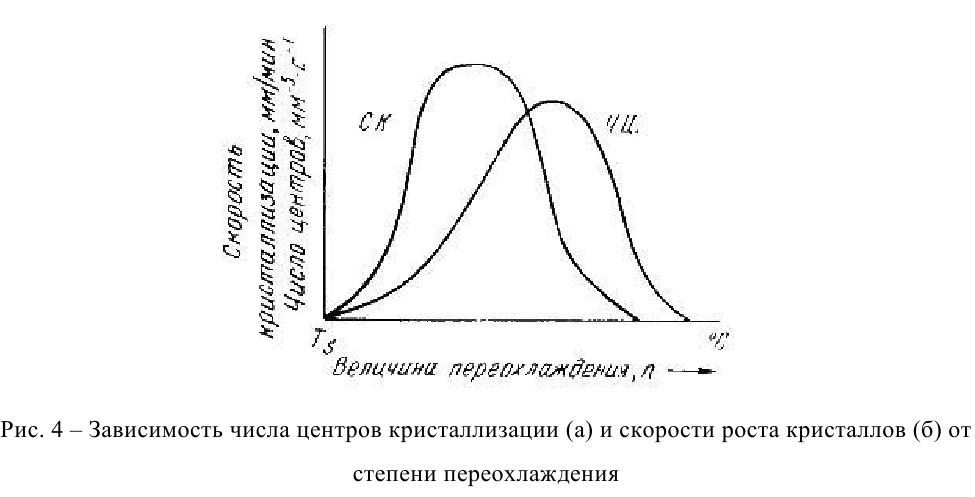
Размеры образовавшихся кристаллов зависят от соотношения числа образовавшихся центров кристаллизации и скорости роста кристаллов при температуре кристаллизации. При равновесной температуре кристаллизации число образовавшихся центров кристаллизации и скорость их роста равняются нулю, поэтому процесса кристаллизации не происходит.
Если жидкость переохладить до температуры, соответствующей т. то образуются крупные зерна (число образовавшихся центров небольшое, а скорость роста — большая).
При переохлаждении до температуры соответствующей т. — мелкое зерно (образуется большое число центров кристаллизации, а скорость их роста небольшая).
Если металл очень сильно переохладить, то число центров и скорость роста кристаллов равны нулю, жидкость не кристаллизуется, образуется аморфное тело. Для металлов, обладающих малой склонностью к переохлаждению, экспериментально обнаруживаются только восходящие ветви кривых.
Пример № 2
Вычертите диаграмму состояния , укажите структурные составляющие во всех областях диаграммы, опишите превращения и постройте кривую охлаждения в интервале температур от
до
(с применением правила фаз) для сплава определенной концентрации. Для этого же сплава определите по правилу отрезков при заданной температуре: процентное содержание углерода в фазах, количественное соотношение фаз.
Решение:
Данные по концентрации углерода в сплаве и по температуре:
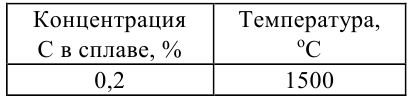
Сплав, содержащий — доэвтектоидная сталь.
Указанный сплав содержит углерода и отмечен вертикальной линией, на диаграмме железо-цементит.
Кривую охлаждения сплава, содержащего представим на рисунке 5.
Опишем процессы, происходящие при охлаждении сплава.
До температуры 1 сплав находится в жидком состоянии, происходит охлаждение расплава.
Правило фаз:
При температуре 1 из расплава начинает выделяться Феррит (Ф). На участке 1-2 сплав будет иметь структуру
Правило фаз.
В точке 2 происходит перитектическая реакция (участок
),
От точки 2′ до точки 3 сплав находится в состоянии двух фаз
В точках от 3 до 4 сплав имеет однофазную Аустснитную (А) структуру.
В точке 4 из Аустенита (А) начинает выделяться вторичный Феррит (Ф) и этот процесс продолжается до точки 5.
В точке 5 происходит эвтектоидное превращение, при котором Аустснит распадается на Перлит (П) — механическую смесь Феррита и Цементита в результате при комнатной температуре сплав имеет структуру Перлита и избыточного Феррита (участок
).
Ниже точки 5 сплав имеет двухфазную структуру, которая охлаждается без каких-либо изменений и без выделения скрытой теплоты.
Выберем температуру в двухфазной зоне
и посредством правила отрезков определим количество данных фаз и содержание в них углерода. Через точку
проведем горизонтальную линию до встречи с основными линиями диаграммы.
Количество жидкости определяется как отношение
Количество феррита определяется как:
Состав жидкости: Состав феррита
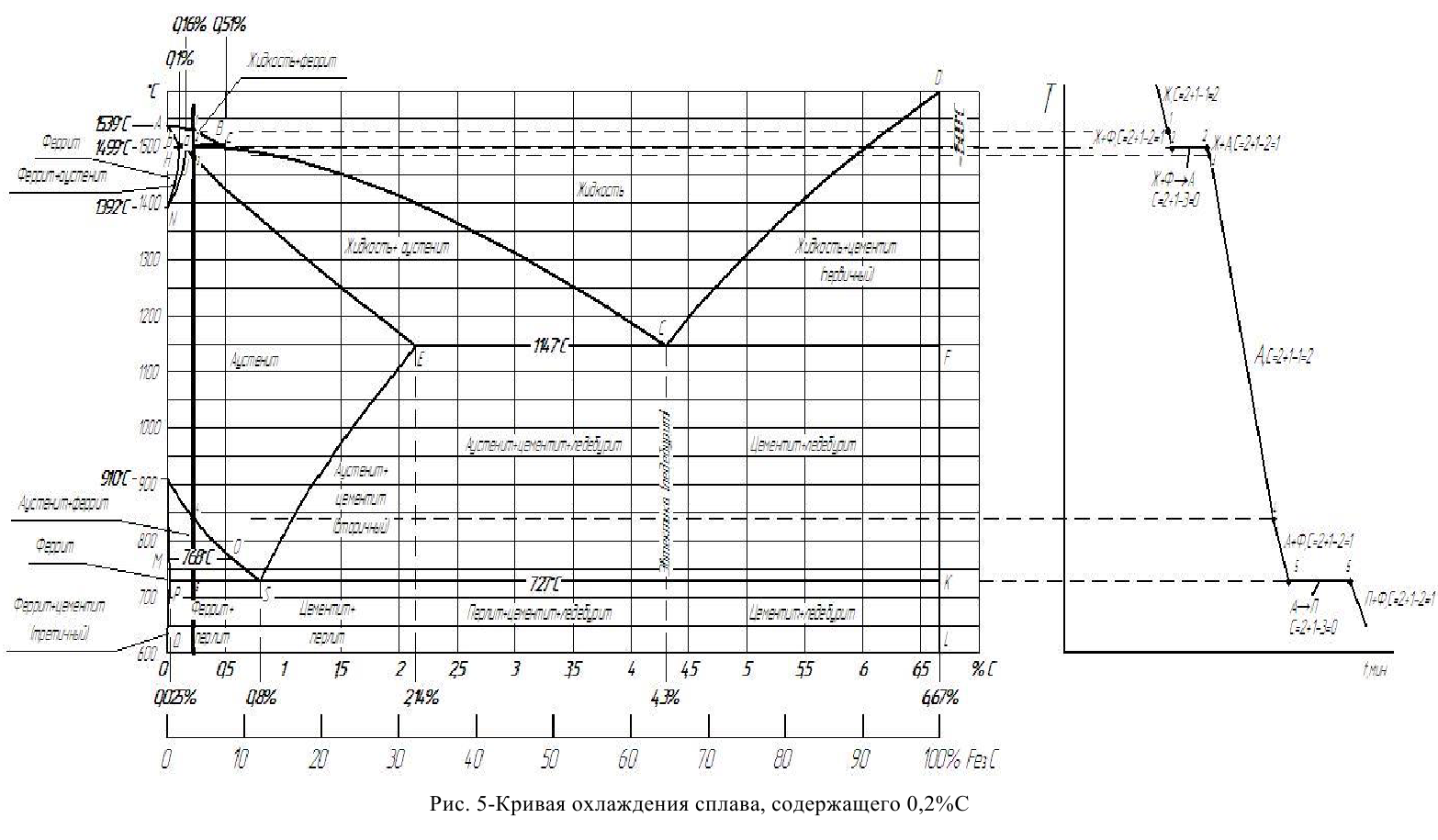
Пример № 3
Требуется произвести поверхностное упрочнение изделий из стали 20. Назначьте вид обработки, опишите технологию, происходящие в стали превращения, структуру и свойства.
Решение:
Сталь 20-конструкционная углеродистая качественная. Содержит .
Для получения необходимого комплекса эксплуатационных свойств сталь 20 подвергают цементации, закалке и последующему низкому отпуску.
Так как сталь 20 является малоуглеродистой, т.е. содержит закалку она не воспринимает, однако, она подвергается упрочняющей химико-термической обработке-цементации. Цементация проводится при нагреве на
в специальных цементационных печах.
Цементация — это поверхностное диффузионное насыщение малоуглеродистой стали углеродом с целью повышения твердости, износоустойчивости. Насыщение поверхности углеродом идет со скоростью
Вид применяемой цементации для стали 20 — цементация в газовом карбюризаторе. Этот процесс осуществляют в среде газов, содержащих углерод.
В случае с газовой цементацией можно получить заданную концентрацию углерода в слое; сокращается длительность процесса, так как отпадает необходимость прогрева ящиков, наполненных малотсплопроводным карбюризатором; обеспечивается возможность полной механизации и автоматизации процессов, и значительно упрощается последующая термическая обработка деталей, так как последующую закалку можно проводить непосредственно из цементационной печи.
Микроструктуру цементованного слоя представим на рисунке 6. На поверхности изделия образуется слой заэвтектоидной стали, состоящий из перлита и цементита. По мерс удаления от поверхности, содержание углерода снижается и следующая зона состоит только из перлита. Затем появляются зерна феррита, их количество, по мере удаления от поверхности увеличивается. И, наконец, структура становится отвечающей исходному составу.
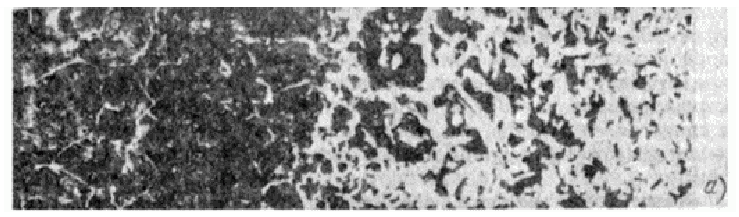

Для гарантированного получения мелкоигольчатого мартенсита детали после цементации охлаждают до температуры ниже температуры , а затем нагревают под закалку до температуры
. Температуру нагрева под закалку выбирают для цементованного слоя. Температура Асздля данной стали составляет
. Закалку для стали 20 производят в воде.
Охлаждение в воде заготовок обеспечивает скорость охлаждения цементованного слоя выше критической. Структура поверхностного слоя после закалки — мартенсит, структура сердцевины зависит от размеров детали. Для небольших изделий получаем сквозную прокаливасмость.
Структура мартенсит по всему сечению. С увеличением размеров изделия от поверхности к сердцевине получаем мартенсит —* троостит —* сорбит —* перлит + феррит. Низкий отпуск проводим при температуре . Более высокие температуры применять не следует, так как это приводит к снижению твердости, статической и усталостной прочности, износостойкости цементовано-закаленных изделий.
Охлаждение после отпуска на воздухе. Структура поверхностного слоя — отпущенный мартенсит. С увеличением размеров изделия от поверхности к сердцевине получаем отпущенный мартенсит троостит * сорбит ~~* перлит + феррит.
Твердость поверхности готового изделия . Механические свойства в сердцевине готового изделия
Пример № 4
Коррозионно-стойкий подшипник изготовлен из стали . Расшифруйте состав, укажите к какому классу относится сталь. Опишите режим упрочнения и объясните природу упрочнения.
Решение:
Сталь -Сталь коррозионно-стойкая обыкновенная, содержащая
Сталь является высокоуглеродистой, высоколегированной, качественной, принадлежит к мартенситному классу.
Шарикоподшипниковые стали подвержены воздействию высоких нагрузок переменного характера. Основными требованиями являются высокая износостойкость, прочность, предел выносливости, отсутствие концентраторов напряжений, неметаллических включений, а также их размерная стабильность.
Для обеспечения работоспособности основных деталей подшипников, работающих в условиях высоких контактных напряжений и изнашивания, материал должен иметь повышенную прочность, структурную однородность и твердость
Для обеспечения заданных свойств, изделия из этих сталей закаливают, обрабатывают холодом и однократно отпускают.
Для нагрева под закалку используют соляные ванны и печи с защитной атмосферой, в качестве закалочной среды используют масло. Недостатки такой ТО: а) применение соляных ванн и печей с защитной атмосферой не даст полной гарантии отсутствия окисления; б) возможно перераспределение легирующих элементов в поверхностном слое из-за их внутреннего окисления; в) необходимость тщательной очистки изделий после термической обработки.
Режимы термообработки:
Закалка масло или воздух. Обработка холодом
Отпуск
воздух
В результате данной термообработки сталь имеет следующие свойства свыше
Пример № 5
Для изготовления деталей выбран сплав . Расшифруйте состав, опишите способ упрочнения сплава и объясните природу упрочнения. Укажите характеристики механических свойств сплава.
Сплав (другое обозначение 1110) является алюминиевым деформируемым сплавом, применяемым для лопастей винтов, узлов креплений, строительных конструкций и др.

Примечание: — основа; процентное содержание
дано приблизительно. Титан + Цирконий до
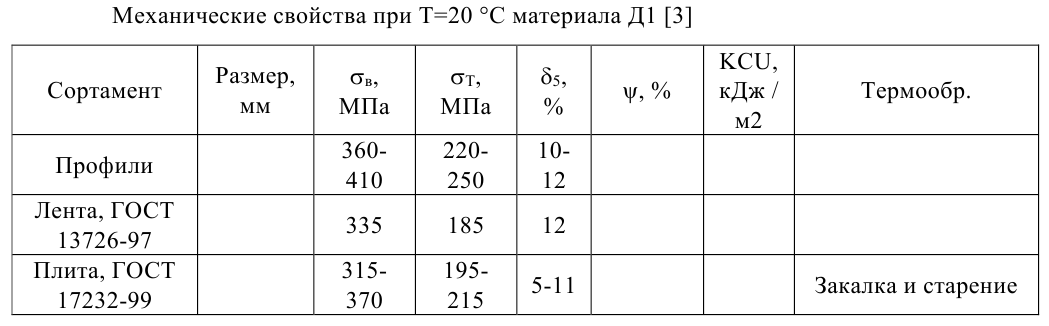
Сплав — относится к системе
Он упрочняется термической обработкой. Сплав хорошо обрабатывается в холодном и горячем состояниях. Температурный интервал горячей деформации
Охлаждение после горячей деформации на воздухе. Прессованные профили имеют пониженную коррозионную стойкость. Сплав хорошо сваривается точечной сваркой. Профили из сплава
могут поставляться в закаленном и естественно состаренном, а так же в отожженном состояниях.
Упрочнение алюминиевых сплавов возможно за счет закалки без полиморфного превращения при наличии в сплаве ограниченной растворимости легирующих элементов. Для получения эффекта закалки алюминиевые сплавы нагревают до температуры выше линии солидус.
Выдержка должна быть такой, чтобы обеспечить полное растворение всех вторичных фаз. После закалки получается пересыщенный твердый раствор. Охлаждение должно вестись интенсивно. Пересыщенный твердый раствор является нестойким и в течение времени начинает распадаться. Процесс распада называется старением.
Процесс распада твердого раствора можно разбить на 4 стадии:
- В кристаллической решетке твердого раствора появляются зоны, обогащенные легирующими элементами. Они представляют области дискообразной формы;
- Зоны увеличиваются в 10 раз, а концентрация легирующих элементов становится такой же, как и в интерметаллидах. Эти зоны называются зонами Гиньс-Престона (ГП);
- На месте этих зон образуются
— фазы. В зонах, обогащенных медью, образуется кристаллическая решетка промежуточная между твердым раствором и упрочняющей фазой;
- Образуется
— фаза.
Механические свойства в процессе старения на разных стадиях меняются по-разному. 1, 2 и 3 стадия сопровождается увеличением прочности, твердости и одновременным снижением пластичности. Это объясняется тем, что в процессе распада твердого раствора происходит искажение кристаллической решетки, т.е. сопротивление перемещению дислокаций увеличивается.
На 4 стадии происходит отделение вторичной фазы от твердого раствора, появляется граница раздела. Искажение кристаллической решетки становится меньше, прочность и твердость падает. Поэтому 4 фазу называют псрестариванием. Если требуются высокие прочность и твердость, то старение оканчивают на 3 стадии. Увеличение температуры старения не вызывает повышения твердости, а лишь ускоряет процесс распада твердого раствора.
Следует учитывать, что некоторые сплавы, особенно сложнолегированные, не достигают максимального упрочнения при естественном старении. Поэтому для получения оптимальных свойств требуется подбор оптимальных температур.
Чрезмерное увеличение температуры старения вызывает коагуляцию вторичной фазы, т.е. увеличение ее размеров и одновременно уменьшение количества ее выделений.
Чем выше температура, тем меньше твердость и прочность, тем ближе свойства к исходному отожженному состоянию. Чтобы снять эффект упрочнения от закалки необходимо применить отжиг с нагревом до температур, близких к температуре закалки, но с последующим медленным охлаждением. Такой отжиг называют отжигом на возврат.
Тсрмомеханическая обработка алюминиевых сплавов:
Для алюминиевых сплавов можно применять практически всс виды т.м.о. Однако чаще всего применяют высокотемпературную т.м.о. и низкотемпературную т.м.о.
Пример № 6
Изложить технологический процесс изготовления фасонных отливок в оболочковых формах. Указать технико-экономические преимущества литья в оболочковые формы и привести примеры его применения.
Решение:
Способ литья в оболочковые формы основан на получении разовых полуформ и стержней в виде оболочек толщиной Их изготавливают путем отверждения на металлической оснастке слоя смеси, в которой связующее вещество при нагреве вначале расплавляется, а затем затвердевает (необратимо), придавая оболочке высокую прочность.
Технология литья в оболочковые формы включает ряд операций, выполнение которых при литье данным способом имеет ярко выраженные особенности. К ним относятся: приготовление специальной песчано-смоляной смеси; формирование на модельной оснастке тонкостенных оболочковых форм и стержней; сборка форм и их подготовка к заливке. Для приготовления оболочковых форм выпускают специальное связующее, представляющее собой смеси фенолформальдегидной смолы с катализатором отверждения смолы, вводимым в количестве
Предварительное формирование оболочки наиболее часто производят, используя поворотный бункер 1, в который засыпают песчано-смоляную смесь 2 (рис. 7, а). На верхнюю часть бункера, снабженную кольцевым каналом 3 для подачи охлаждающей воды, устанавливают моделями вниз и закрепляют нагретую до металлическую модельную плиту 4. На ней закреплена с помощью четырех направляющих колонок 5 плита 6 толкателей
Толкатели, равномерно распределенные по всей плите, выходят на рабочую поверхность, как модели, так и модельной плиты. Их фиксируют специальными хвостовиками в гнездах плиты 6 и закрепляют в ней прижимной плитой 8. Модельная плита с выталкивающим устройством помещена в корпус 9. Для фиксации плиты толкателей в исходном положении на направляющих колоннах 5 установлены пружины 10.
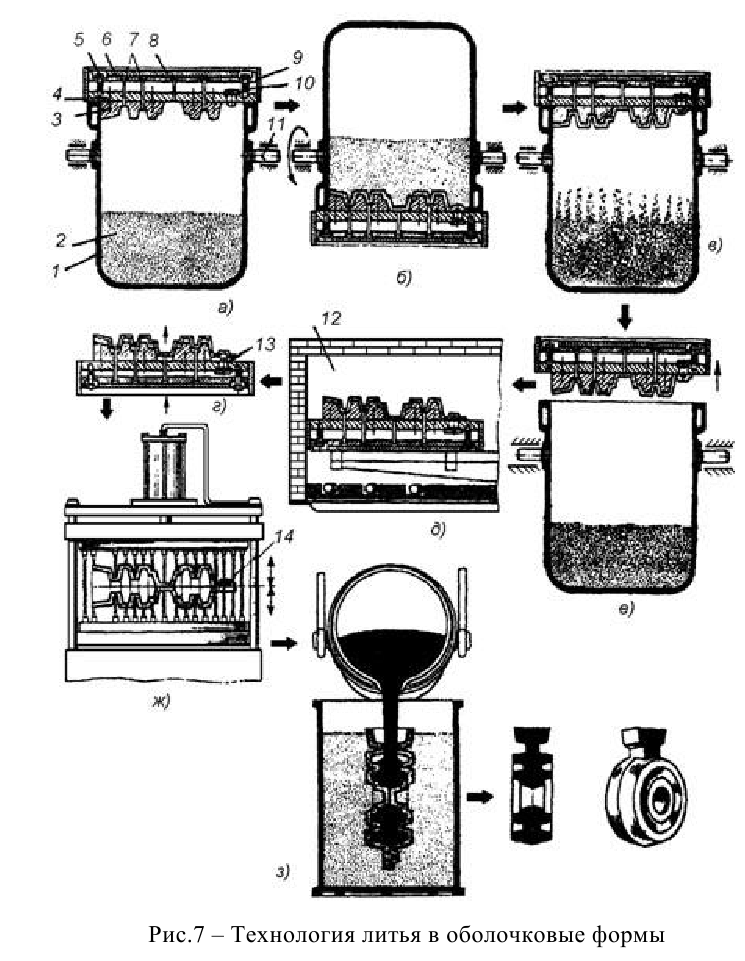
Для предварительного формирования оболочки бункер 1, снабженный цапфами 11 и поворотным механизмом, поворачивают на 1800, и формовочный материал падает на горячую модельную плиту (рис.7, б), уплотняясь под действием гравитационных сил. В прилегающем к плите слое смеси смола плавится (при температуре ), смачивая зерна песка, а затем начинает полимсризоваться, загустевая и отвсрждаясь по мере прогрева до более высокой температуры. За
выдержки смола успевает оплавиться в слое толщиной около
Слой остается на модельной плите после поворота бункера в исходное положение (рис.7, в) и сброса на дно бункера не прореагировавшей, сохранившей свои начальные свойства и пригодной для последующего использования части смеси.
Теперь модельную плиту со сформированной оболочковой полуформой снимают с бункера (рис.7, г) и подают в печь 12 (рис.7, д), где при температуре за
заканчивается полимеризация, и смола приобретает высокую технологическую прочность.
Затем готовую оболочковую полуформу снимают с модельной плиты (рис.7, е) и соединяют с другой полуформой (например, склеиванием) на специальном пневмопрессе (рис.7, ж). Для исключения прорыва расплава, формы с вертикальным разъемом обычно заформовывают (рис.7, з) в опорный наполнитель (песок, дробь и т.п.). Формы небольшой высоты с горизонтальным разъемом в большинстве случаев не заформовывают и заливают на поддонах с песчаной постелью.
В оболочковые формы получают отливки практически из любых промышленных сплавов массой до Преимущества литья в оболочковые формы по сравнению с литьем в песчано-глинистые разовые формы заключаются в следующем:
- уменьшение параметров шероховатости поверхности и существенное улучшение внешнего товарного вида отливок;
- возможность получения отливок с тонким и сложным рельефом, а также толстостенных отливок с литыми каналами малых сечений;
- уменьшение трудоемкости ряда операций технологического процесса (приготовление смеси, изготовление формы, очистка отливок и пр.);
- сокращение в 8-10 раз и более объема переработки и транспортирования формовочных материалов;
- уменьшение металлоемкости формовочного оборудования.
Кроме того, для литья в оболочковые формы характерна меньшая жесткость оболочки, что следует рассматривать как достоинство метода в сравнении с методами литья в кокиль.
Основные недостатки метода литья в оболочковые формы:
- относительно высокая стоимость смоляного связующего;
- сложность модельной и стержневой оснастки;
- повышенное выделение вредных химических веществ в ходе термического разложения смоляного связующего;
- недостаточная прочность оболочек при получении тяжелых отливок;
- склонность к появлению некоторых специфических видов дефектов, сопровождающих низкую
- газопроницаемость литейной формы
Пример № 7
Характер изменения структуры и механических свойств металла при горячей обработке давлением. Укажите наиболее рациональное направление волокон на эскизе продольного сечения кованого (штампованного) коленчатого вала трактора или автомобиля.
Решение:
Обработка давлением основана на способности некоторых металлов и сплавов пластически деформироваться, т. е. под действием нагрузок изменять внешнюю форму и сохранять измененную форму после того, как нагрузки перестают действовать.
Хрупкие металлы и сплавы обрабатывать давлением нельзя, так как они не обладают достаточной пластичностью. Например, чугун как в холодном, так и в нагретом состоянии под давлением разрушается, не изменяя внешней формы, и потому для обработки давлением непригоден.
Некоторые металлы и сплавы, недостаточно пластичные при обычной температуре, при высоком нагреве обладают пластической деформацией и могут быть обработаны давлением. К числу таких сплавов относится сталь.
При пластической деформации изменяется не только внешняя форма металлов, но и внутреннее их строение, а следовательно, и свойства.
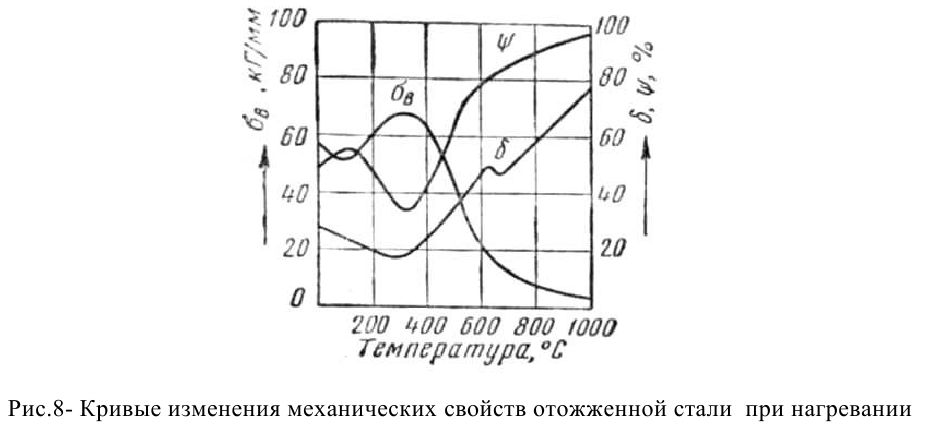
Из рисунка 8 видно, как изменяются механические свойства отожженной стали в зависимости от температуры при нагревании.
Кривая показывает, что прочность стали при нагревании до
повышается, а при дальнейшем нагревании резко снижается. Показатели пластичности
и
, наоборот, при нагревании стали до
понижаются, а при дальнейшем повышении температуры сильно возрастают, что и требуется для обработки давлением.
Из сказанного следует, какое значение при горячей обработке давлением имеет правильное определение температуры нагрева металлов. Однако для успешных результатов обработки требуется соблюдать и другие условия нагрева.
В технике часто используют холодную обработку давлением без нагрева металлов и сплавов: прокатку, штамповку, волочение в холодном состоянии или с нагревом до температуры ниже температуры рекристаллизации.
При холодной обработке давлением также изменяются механические и другие свойства металлов и сплавов.
На рисунке 9 показаны кривые изменения механических свойств низкоуглеродистой стали при холодной прокатке. В результате этого процесса увеличиваются прочность и твердость стали, пластичность, наоборот, уменьшается.
Физико-механические свойства стали при холодной обработке давлением изменяются: уменьшаются электропроводность и сопротивление коррозии.
Изменение свойств металлов, вызванное деформацией в холодном состоянии, называется наклепом, или нагартовкой.
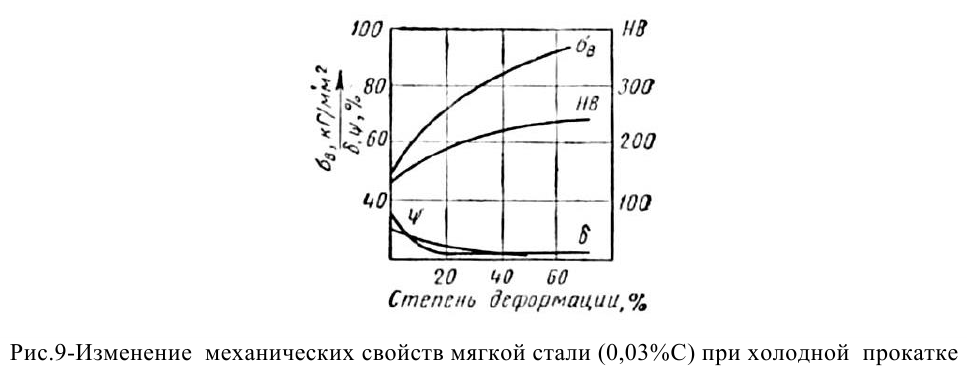
Состояние наклепа объясняется изменением нормальной кристаллической решетки, т. е. сдвигами ее частиц под влиянием внешних воздействий.
Холодной обработке давлением подвергают листовые и полосовые заготовки из низкоуглеродистой стали, из цветных металлов и сплавов. Часто наклеп сообщают проволоке, применяемой для пружин.
Преимущества холодной обработки давлением — чистая поверхность и высокая точность изделий.
Если изменение свойств металла под влиянием холодной обработки нежелательно, наклеп может быть устранен путем нагревания изделий.
Уже при невысокой температуре (для стали ) измененная холодной обработкой кристаллическая решетка частично восстанавливается, и в наклепанном слое понижается прочность и твердость, возрастает пластичность. Эти явления называются возвратом.
При более высоком нагреве происходит рекристаллизация, т. е. образование новых зерен взамен деформированных, частичное восстановление структуры металла и возвращение первоначальных свойств.
Установлено, что наименьшая температура для рекристаллизации железа , меди
, алюминия и магния
, вольфрама
.
Легкоплавкие металлы — олово, цинк, кадмий и другие — имеют низкую температуру рекристаллизации. Например, температура начала рекристаллизации у цинка , свинца
и т. п. Поэтому у таких металлов при обычной температуре явлений наклепа при холодной обработке давлением не возникает.
Температура рекристаллизации не является постоянной для каждого металла и зависит: от степени деформации (чем больше деформация, тем нагревание должно быть выше); от времени выдержки (чем выдержка при температуре рекристаллизации продолжительнее, тем легче протекает процесс рекристаллизации);
от величины зерна (для крупнозернистого металла температура должна быть выше, чем для мелкозернистого).
Сталь обрабатывают давлением преимущественно в нагретом состоянии. Температура, при которой производят горячую обработку стали, значительно превышает температуру ее рекристаллизации, поэтому наклеп, образующийся при обработке, уничтожается вследствие рекристаллизации, и горячекатаная сталь наклепа не получает.
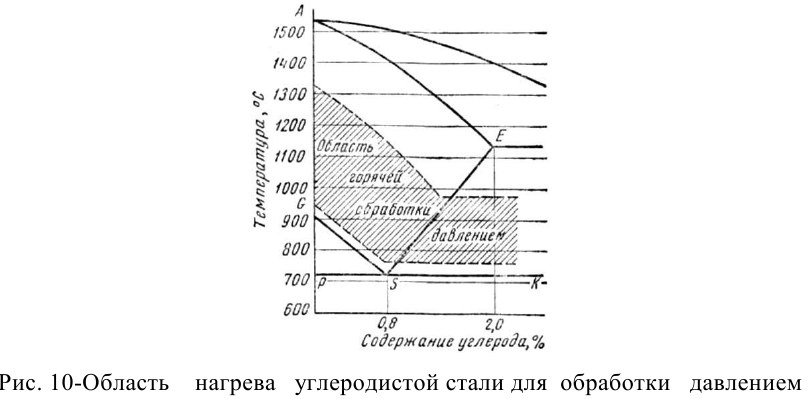
При выборе температуры нагрева для горячей обработки стали давлением следует опасаться ее пережога. В то же время нужно иметь в виду, что если сталь обрабатывать давлением при сравнительно низкой температуре, в ней сохранятся следы наклепа.
Следовательно, для правильного ведения горячей обработки давлением нужно знать, до какой температуры следует нагревать металл и при какой температуре прекращать эту обработку. Правильное определение температуры начала и конца горячей обработки (она установлена Д. К. Черновым) имеет исключительно важное значение для качества изделий.
Температура нагрева для обработки давлением углеродистой стали зависит от содержания в ней углерода.
Из рисунка 10 следует: чем меньше углерода содержит сталь, тем выше должна быть температура ее нагревания для успешной обработки давлением.
Горячая обработка давлением литых металлов способствует улучшению их свойств:
- • химический состав металла становится более равномерным;
- • металл приобретает мелкозернистое строение:
- • пустоты и газовые пузыри завариваются, и металл уплотняется.
Вместе с тем при горячей обработке давлением механические свойства металлов могут оказаться неодинаковыми в различных направлениях (ярко выраженная анизотропность), вследствие образования волокнистой структуры.
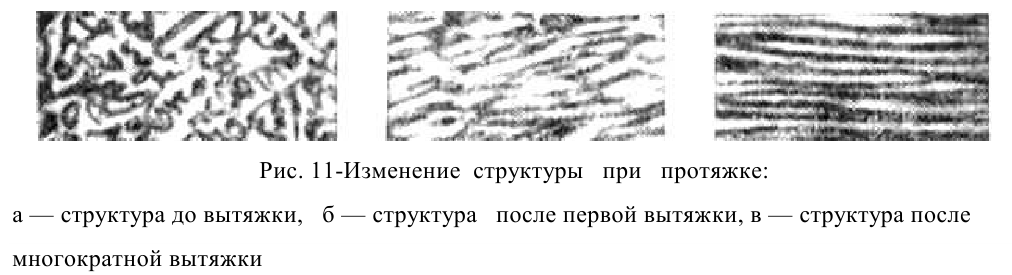
Волокнистое строение является результатом удлинения зерен при вытяжке металла и легко обнаруживается при рассмотрении излома в направлении вытяжки . Эта особенность структуры металла вызывает неодинаковые механические свойства вдоль и поперек направления вытяжки. Расположение волокон очень важно учитывать при обработке давлением. Необходимо добиваться, чтобы усилия, прилагаемые к изделию, были направлены не вдоль, а поперек волокон. Несоблюдение этих условий приводит к понижению ударной вязкости кованых изделий.
Коленчатый вал (коленвал) — деталь кривошипно-шатунного механизма, предназначенная для преобразования усилия от шатунов в крутящий момент. Для уменьшения напряжений в поковках вала направление волокон должно соответствовать конфигурации колен.
В массовом производстве стальных коленчатых валов для получения заготовки используется ковка в закрытых штампах на прессах или молотах посредством нескольких операций. Окончательная ковка коленвала завершается обрезкой облоя с использованием обрезного пресса и горячей правкой под молотом.
При получении заготовки большое внимание уделяется расположению волокон материала, так как этот фактор влияет на механическую прочность коленчатого вала. Чтобы предотвратить перерезание волокон во время механической обработки используют специальные штампы с гибочными ручьями. После этого заготовки коленвала подвергают термической обработке, очищают от окалины и обрабатывают на дробеметной машине, и только после этого отправляют на механическую обработку.
На рисунке 12 представим наиболее рациональное расположение волокон в заготовке коленчатого вала, полученного ковкой
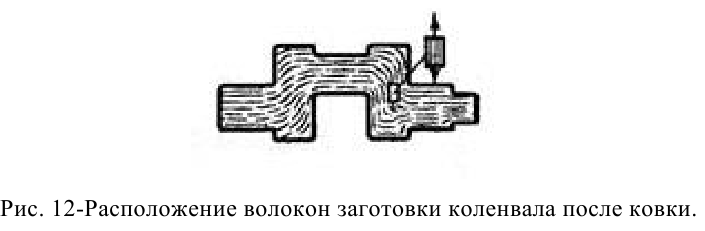
Вопрос 8. Ручная дуговая наплавка плавящимся и неплавящимся электродами, область применения.
Ручная дуговая сварка выполняется плавящимся или неплавящимся (угольным, графитовым, вольфрамовым, гафниевым) электродом. При сварке плавящимся электродом (рис. 13) дуга горит между ним и изделием.
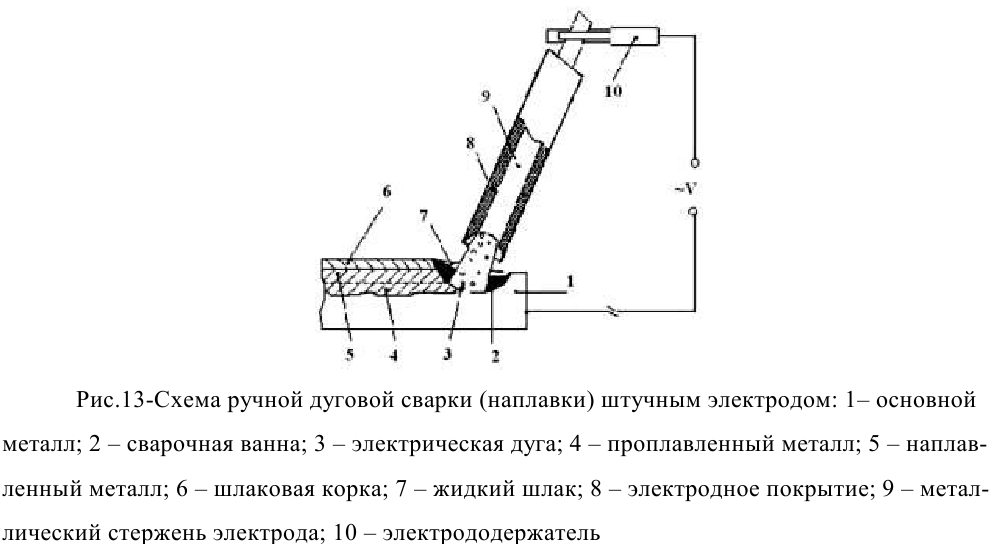
Формирование металла шва осуществляется за счет материала электрода и расплавления основного металла в зоне действия дуги. При сварке неплавящимся электродом для формирования металла шва в зону дуги извне подается присадочный материал.
Наибольшее применение нашла сварка плавящимся электродом, так как ее можно применять во всех пространственных положениях, сваривая черные, цветные металлы и различные сплавы. При этом используются электроды диаметром Однако основной объем работ выполняется электродами диаметром
Электроды классифицируются по материалу, из которого они изготовлены, по назначению, по виду покрытия, по свойствам металла шва, по допустимым пространственным положениям сварки или наплавки, по роду и полярности тока.
По назначению электроды подразделяются на следующие группы:
- для сварки углеродистых и низколегированных конструкционных сталей — У;
- для сварки теплоустойчивых легированных сталей — Т;
- для сварки высоколегированных сталей с особыми свойствами — В;
- для наплавки слоев с особыми свойствами — Н.
По толщине покрытия существуют следующие группы электродов:
- с тонким покрытием — М;-
- со средним покрытием — С;
- с толстым покрытием — Д;
- с особо толстым покрытием — Г.
Покрытия могут быть кислые — А, основные — В, целлюлозные — Ц, рутиловые — Р и прочие — П.
В настоящее время при ремонте техники на железнодорожном транспорте находят наибольшее применение кислые, основные и рутиловые покрытия.
Кислое покрытие состоит в основном из оксидов металла, алюмосиликатов и раскис-лителей. Газовая защита осуществляется за счет сгорания органических составляющих покрытия.
Сварку электродами с кислым покрытием можно производить при помощи постоянного и переменного тока. В процессе сварки сварочная ванна бурно кипит вследствие активного раскисления металла углеродом, что способствует хорошей дегазации металла шва. Поэтому даже при сварке по окалине или ржавчине получаются сравнительно плотные швы, уступающие по характеристикам пластичности и ударной вязкости металла шва электродам с другими видами покрытий. При использовании электродов с кислым покрытием существует склонность к образованию кристаллизационных трещин, большое разбрызгивание металла, значительное выделение в процессе сварки вредных марганцевых выделений. К электродам с кислым покрытием относятся электроды следующих марок: и др.
Основное покрытие состоит преимущественно из мрамора, плавикового шпата, рас-кислителей и легирующих элементов (ферромарганец, ферросилиций, феррованадий и др.). Газовая защита расплавленного металла обеспечивается углекислым газом и окисью углерода, которые образуются в результате диссоциации карбонатов.
Электроды с основным покрытием и ряд других) обеспечивают получение наплавленного металла с малым содержанием газов и вредных примесей, с высокими пластическими характеристиками и ударной вязкостью при нормальной и отрицательных температурах, с хорошей стойкостью против образования кристаллизационных трещин и старения. Поэтому такие электроды предназначаются для сварки конструкций из углеродистых и конструкционных сталей, жестких конструкций из литых углеродистых и низколегированных высокопрочных сталей.
Недостатком этого вида покрытий является повышенная чувствительность к порообразованию при увлажнении покрытия, увеличении длины дуги, при наличии окалины, ржавчины или масла на кромках свариваемых изделий.
Сварка электродами с основным покрытием ведется, как правило, на постоянном токе обратной полярности. Чтобы использовать такие электроды для сварки на переменном токе, в покрытие вводятся компоненты, содержащие легкоионизирующие элементы: калиевое жидкое стекло, кальцинированную соду, поташ и др.
Рутиловое покрытие содержит в основном рутиловый концентрат, различные алюмосиликаты и ферромарганец. Раскисление и легирование металла шва достигается наличием ферромарганца, а газовая защита — целлюлозой. Марки электродов с рутиловым покрытием: и др.
Электроды с рутиловым покрытием обладают высокими сварочно-технологическими свойствами, обеспечивают хорошее формирование шва, имеют небольшое разбрызгивание, легкую отделимость шлаковой корки, малую склонность металла к образованию пор. Сварку можно вести как на постоянном, так и переменном токе.
Перед сваркой и наплавкой необходима прокалка электродов: с рутиловой обмазкой при , с карбонато-рутиловым покрытием при
и с основным -при
. Время прокаливания
часа.
Несмотря на широкое распространение ручной дуговой сварки при производстве сва-рочно-наплавочных работ, она имеет ряд недостатков: сравнительно низкое качество наплавленного металла по причине слабой защиты сварочной ванны от воздействия окружающей среды; большое колебание сварочного тока; значительную вероятность возникновения нспроваров, подрезов и других дефектов соединения; большие потери (до ) присадочного материала на угар, разбрызгивание, огарки; малую производительность из-за невозможности использования высокой плотности тока и перерывов при смене электродов; сложность технологического процесса, что требует длительного времени подготовки сварщиков и др. Все это следует учитывать при выборе способа сварки и наплавки.
Пример № 8
Расшифруйте марки заданных материалов; оцените свариваемость материала; опишите процессы, происходящие в зоне шва и околошовной зоне. Отметьте, в чем заключается особенность технологии и техники сварки данного материала. Выберите и обоснуйте метод сварки. Рассчитайте режимы, нарисуйте разделку кромок шва, выберите оборудование для сварки и укажите основные характеристики. Выберите и опишите методы контроля сварного соединения.
Решение:

— Сталь жаропрочная высоколегированная, мартенситного класса Свариваемость материала — трудносваривасмая. Полный химический состав стали представим в таблице.
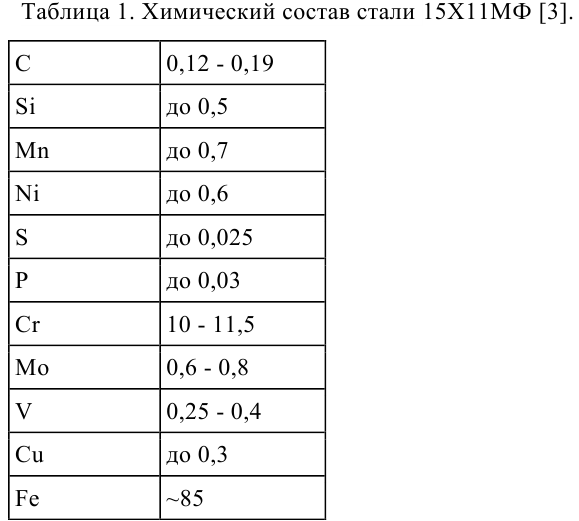
Для стали применяем ручную дуговую сварку. Дуговая сварка металла это сварка плавлением, при которой нагрев свариваемых кромок осуществляется теплом электрической дуги. Способ позволяет без замены сварочного инструмента и оборудования (при правильно выбранном сварочном режиме) выполнять швы различных типов и назначения, а также вести сварку в любом пространственном положении и в труднодоступных местах.
Устойчивый процесс сварки обеспечивается непрерывной подачей конца электрода в зону горения дуги без значительных отклонений ее длины.
При длинной дуге усиливается окисление электродного металла, увеличивается разбрызгивание, снижается глубина провара, шов получается со значительными включениями оксидов. Основной объем работ выполняют при токе и напряжении дуги
.
Возбуждение (зажигание) дуги 3 (рис.14) происходит при кратковременном замыкании электрической сварочной цепи, для чего сварщик прикасается к свариваемому металлу 1 концом электрода 5 и быстро отводит его на расстояние .
В этот момент возникает электрическая дуга, устойчивое горение которой поддерживают поступательным движением электрода (вдоль оси) по мере его плавления.
Дугу возбуждают также скользящим движением конца электрода по поверхности свариваемого металла (чирканием) с быстрым отводом его на необходимое расстояние.
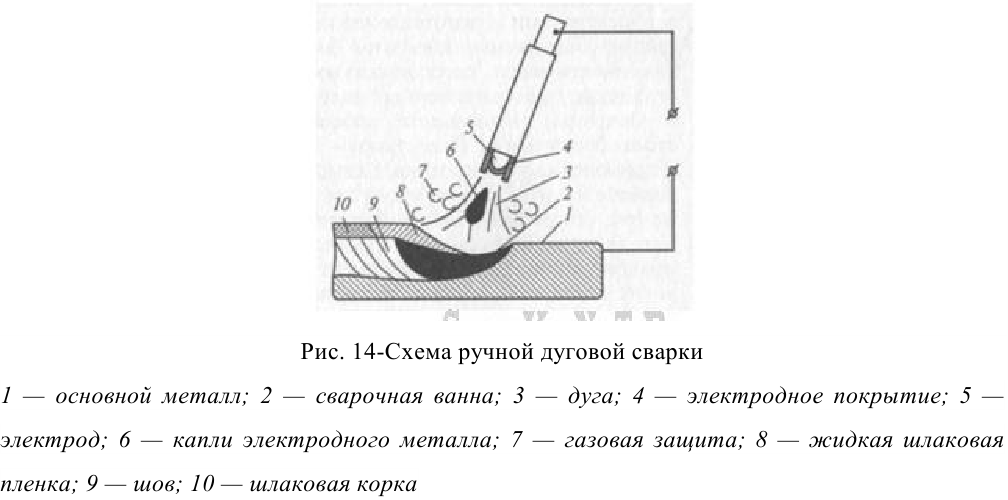
ВСтЛпс — Сталь конструкционная углеродистая обыкновенного качества, полуспокойная, свариваемость материала — без ограничений.
Полный химический состав стали представим в таблице 2
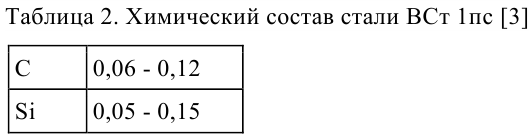
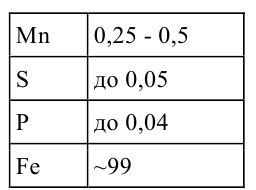
Сталь ВСт 1пс подвергается газовой сварке в среде углекислого газа.
Газовой сваркой могут соединяться почтя все металлы и сплавы, применяемые в настоящее время в промышленности. Наиболее широкое применение газовая сварка получила при строительно-монтажных работах, в сельском хозяйстве и при ремонтных работах.
Для выполнения сварочных работ необходимо, чтобы сварочное пламя обладало достаточной тепловой мощностью. Мощность пламени горелки определяется количеством ацетилена, проходящего за один час через горелку, и регулируется наконечниками горелки. Мощность пламени выбирается в зависимости от толщины свариваемого металла и его свойств. Количество ацетилена в час, необходимое на толщины свариваемого металла, устанавливается практикой. Например, при сварке низкоуглеродистой стали на
толщины свариваемого металла требуется
ацетилена в час. Чтобы узнать требуемую мощность пламени, надо умножить удельную мощность на толщину свариваемого металла в миллиметрах.
Для сварки различных металлов требуется определенный вид пламени — нормальное, окислительное, науглероживающее. Газосварщик регулирует и устанавливает вид сварочного пламени на глаз. При ручной сварке сварщик держит в правой руке сварочную горелку, а в левой — присадочную проволоку. Пламя горелки сварщик направляет на свариваемый металл так, чтобы свариваемые кромки находились в восстановительной зоне на расстоянии , от конца ядра. Конец присадочной проволоки должен находиться в восстановительной зоне или в сварочной ванне.
Скорость нагрева регулируется изменением угла наклона (а) мундштука к поверхности свариваемого металла (рис. 15, а). Величина угла выбирается в зависимости от толщины и рода свариваемого металла. Чем толще металл и больше его теплопроводность, тем больше угол наклона мундштука горелки к поверхности свариваемого металла. В начале сварки для лучшего прогрева металла угол наклона устанавливают больше, затем по мере прогрева свариваемого металла его уменьшают до величины, соответствующего данной толщине металла, а в конце сварки постепенно уменьшают, чтобы лучше заполнить картер и предупредить пережог металла.Рукоятка горелки может быть расположена вдоль оси шва или перпендикулярно к нему. То или иное положение выбирается в зависимости от условий (удобства) работы газосварщика, чтобы рука сварщика не нагревалась теплом, излучаемым нагретым металлом.
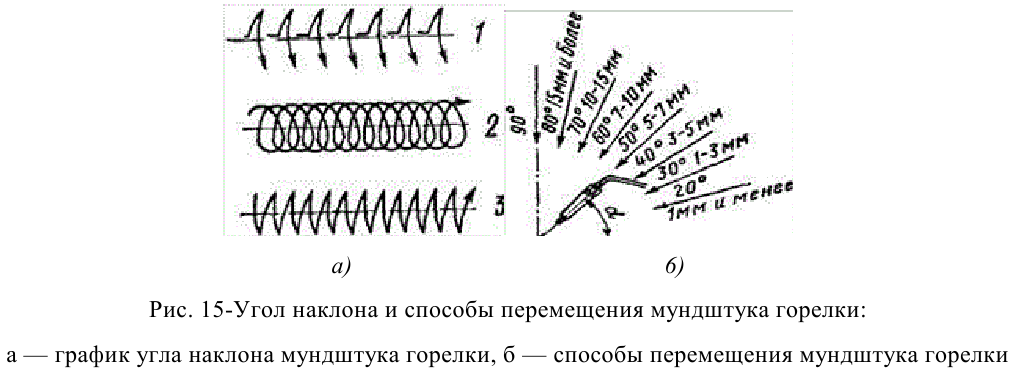
В процессе сварки газосварщик концом мундштука горелки совершает одновременно два движения: поперечное — перпендикулярно к оси шва и продольное — вдоль оси шва. Основным является продольное движение. Поперечное движение служит для равномерного прогрева кромок основного и присадочного металла и получения шва необходимой ширины.
Процессы, происходящие в зоне шва и околошовной зоне:
Процесс кристаллизации шва начинается сразу после отвода дуги от свариваемого участка. Застывание металла происходит в направлении, обратном отводу тепла в структуру основной поверхности, начиная от краев сварочной ванны к ее центру. Средняя скорость кристаллизации и скорость сварки равны. По границам шва формируются кристаллиты наплавляемого и основного металла, обеспечивающие монолитность строения слоев и прочность соединения.
Образование шва и околошовной зоны:
Остановка начального процесса кристаллизации происходит достаточно быстро, при остывании шва на , то есть до температуры
. После его завершения в структуре металла не происходит никаких изменений до его остывания до
, когда металл начинает выходить из аустснитной формы.
Затем происходит процесс вторичной кристаллизации в структуре строения шва и прилегающем к нему основном металле. Он также протекает в коротком температурном диапазоне. Структура сварного шва становится стабильной по достижении им температуры в .
Кристаллиты сварочного шва имеют столбчатое строение структуры, характерное для процесса литья металла. Этот вид кристаллизации способствует вытеснению газовых и шлаковых фракций.
Рассчитаем режимы дуговой сварки:
Исходные данные: Свариваемый материал: Тип сварного соединения -встык Расположение шва в пространстве — нижний. Толщина свариваемых деталей:
.
Стыковые соединения с толщиной свариваемых деталей выполняются с односторонней разделкой кромок.
На рисунке 16 приведем эскиз соединения
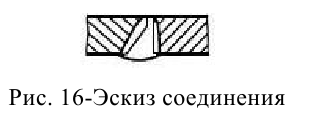
На рисунке 17 представим эскиз разделки кромок
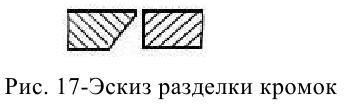
Диаметр электрода выбираем в зависимости от толщины свариваемых деталей. При заданной толщине принимаем
Определим площадь сечения одностороннего стыкового шва выполненного без зазора можно определить по формуле:

где — ширина шва, мм;
— высота усиления шва, мм;
— толщина свариваемого металла, мм;
— величина зазора в стыке, мм.
Площадь поперечного сечения шва найдем из расчетной схемы (рисунок 18).
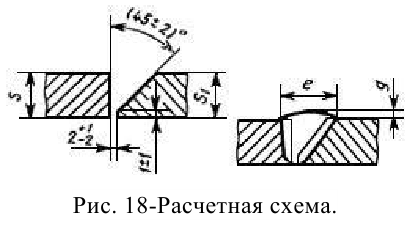
Согласно ГОСТ 5264-80
При определении числа проходов следует учитывать, что сечение первого прохода не должно превышать и может быть определено по формуле:

где — площадь поперечного сечения первого прохода,
;
— диаметр электрода, мм.
Следовательно принимаем 1 проход.
Расчет сварочного тока при ручной дуговой сварке производим по диаметру электрода и допускаемой плотности тока по формуле:
где — допустимая плотность тока,
;
— площадь поперечного сечения электрода,
;
— диаметр электрода,
.
Допустимая плотность тока зависит от диаметра электрода и вида покрытия: чем больше диаметр электрода, тем меньше допустимая плотность тока, так как ухудшаются условия охлаждения. Допустимая плотность тока в электроде при ручной дуговой сварке
Напряжение на дуге при ручной дуговой сварке изменяется в пределах и при проектировании технологических процессов ручной дуговой сварки не регламентируется [4]. Поэтому напряжение на дуге принимаем
Скорость перемещения дуги (скорость сварки) определяем по формуле:
где — коэффициент наплавки,
— плотность наплавленного металла за данный проход,
— для стали);
— сила сварочного тока,
— площадь поперечного сечения наплавленного металла,
.
Результаты расчетов режима сварки представим в таблице 2
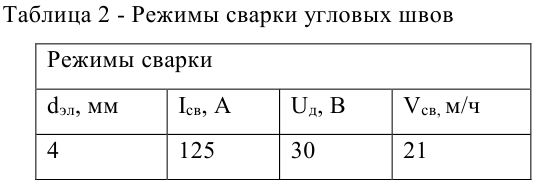
Выбираем оборудование для сварки. Принимаем трансформатор передвижной ТДМ-317.
Параметры трансформатора: сварочный ток номинальное рабочее напряжение
Рассчитаем режимы газовой сварки.
Исходные данные:
Тип сварного соединения -стыковое Расположение шва в пространстве — горизонтальный. Свариваемый материал — ВСт.1 пс Толщина свариваемого металла —
При данном расположении сварного шва разделка ведется только верхней кромки На рисунке 19 приведем эскиз соединения
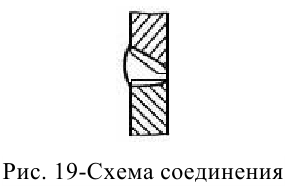
На рисунке 20 представим эскиз разделки кромок
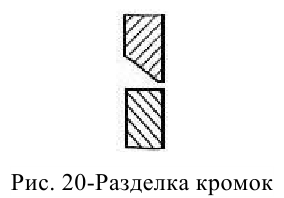
- мощностью сварочного пламени
- углом наклона присадочного материала и мундштука горелки
- диаметром присадочного материала
- скоростью сварки.
Мощность сварочного пламени напрямую зависит от расхода горючего газа и для ацетиленовой сварки ее приближенно можно определить по формуле:
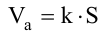
где — мощность пламени, определяема расходом ацетилена,
— толщина свариваемого материала,
;
— коэффициент пропорциональности, величина которого зависит от вида свариваемого материала, для низкоуглсродистой стали стали
принимаем

Угол наклона мундштука сварочной горелки при толщине свариваемых листов , принимаем
Марку присадочной проволоки принимаем .
Подбираем диаметр присадочного материала в зависимости от толщины свариваемых деталей и метода наложения шва. При толщине металла диаметр присадочного материала принимаем равным половине толщины металла
.
Определяем скорость сварки.
где — коэффициент, зависящий от свойств материала,
,
— толщина свариваемого металла,
.

Расход ацетилена принимаем в зависимости от толщины свариваемого металла: при толщине материала расход ацетилена
[4], следовательно, при
. расход кислорода
на
толщины, следовательно расход кислорода составляет
.
Вид пламени принимаем — нормальный.
Выбираем способ сварки:
Так как толщина свариваемого металла более принимаем способ сварки — правую сварку.
После сварки изделие помещают в нагревательную печь, нагрев ведут постепенно. Для низкоуглеродистых сталей температура нагрева достигает . После нагрева изделие выдерживают в печи при этой температуре в течение
на
толщины металла и охлаждают вместе с печью. Такая обработка называется отжигом и применяется для снятия внутренних напряжений.
Результаты расчета режима сварки занесем в таблицу 4.
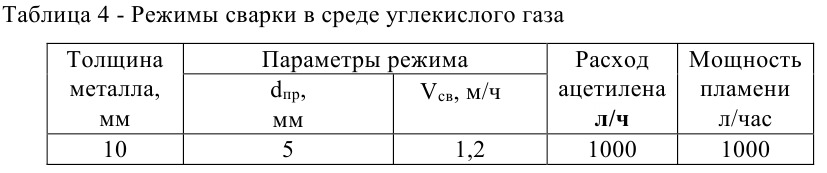
В качестве метода контроля сварного соединения применяем один из методов неразрушающиго контроля — внешний осмотр . Внешнему осмотру подвергается сварных соединений. Осмотр выполняется невооруженным глазом или с помощью лупы, используя шаблоны и мерительный инструмент. При этом проверяются геометрические размеры швов, наличие подрезов, трещин, непроваров, кратеров и других наружных дефектов.