Оглавление:
Здравствуйте, я на этой странице сделала подробное методическое указание по предмету «материаловедение» для студентов любых специальностей. Это методическое указание охватывает полный курс «материаловедения».
Если что-то непонятно, Вы всегда можете написать мне в воцап и я помогу! |
Материаловедение
Материаловедение является одной из основных дисциплин подготовки инженерных кадров. Это обусловлено, прежде всего, тем, что производство, разработка и обработка новых материалов является основой современного производства и во многом определяет уровень его развития и научно-технический и экономический потенциал государства.
Разработка рациональной и конкурентоспособной продукции и организация ее производства невозможны без достаточного уровня знаний в области материаловедения, что является важнейшим показателем подготовки современного сертифицированного специалиста. Кроме того, материаловедение обеспечивает основу для изучения многих специальных дисциплин.
Материаловедение — это наука, изучающая взаимосвязь между составом, структурой и свойствами материалов, а также их изменение под различными внешними воздействиями (тепловыми, механическими, химическими и т.д.). Основной практической задачей материаловедения является поиск оптимального состава и способа обработки материалов для придания им желаемых свойств.
Основы строения и свойств материалов
Разнообразие свойств материалов является главным фактором, предопределяющим их широкое использование в технике. Материалы обладают отличающимися друг от друга свойствами, причем каждое зависит от особенностей внутреннего строения материала. В связи с этим материаловедение как наука занимается изучением строения материалов в тесной связи с их свойствами. Основные свойства материалов можно подразделить на физические, химические, механические, технологические и специальные.
К физическим свойствам относятся магнитные, электро- и теплопроводность, а также такие свойства, как плотность, теплоемкость, температура плавления и др. Химические свойства характеризуют специфику межатомного взаимодействия материала с другими веществами, в том числе с окружающей средой, например коррозию. Среди механических свойств следует назвать прежде всего такие, как прочность, твердость, пластичность, вязкость.
От физических, химических и механических свойств зависят технологические и специальные свойства материалов. К технологическим свойствам относятся литейные, ковкость, свариваемость, обрабатываемость режущим инструментом, а к специальным — жаропрочность, жаростойкость, сопротивление коррозии, износостойкость и др. Среди механических свойств прочность занимает особое место, так как прежде всего от нее зависит не-разрушаемость изделий под действием эксплуатационных нагрузок.
Учение о прочности и разрушении материалов является важнейшей частью материаловедения, поэтому оно представляет для специалистов машиностроения большой интерес не только с точки зрения обеспечения прочности, надежности и долговечности изделий. Оно имеет и очень важное технологическое значение.
Это объясняется тем, что основные, связанные с послойным удалением материала формообразующие и многие упрочняющие операции обработки деталей по своей сути представляют собой дозированное, технологически управляемое разрушение материала, осуществляемое по какому-либо определенному режиму. Особенно это касается современных самых перспективных, так называемых высоких технологий, основанных на применении в качестве инструмента концентрированных потоков энергии, создаваемых лазерным излучением, сфокусированными потоками электронов, а также плазменными потоками.
Таким образом, четкое уяснение современных представлений о природе прочности материалов и тонком физическом механизме их разрушения окажется для специалистов важной теоретической основой не только при выборе подходящих конструкционных материалов для деталей различного целевого назначения и поисках рациональных способов формирования в них требуемых прочностных свойств, но и при разработке технологических процессов обработки материалов, а также при определении видов и рабочих характеристик используемого в производстве технологического оборудования.
Рациональное внутреннее строение металлических сплавов, используемых для изготовления большинства деталей в машиностроении, в основном определяется так называемой дислокационной структурой. Поэтому в данном разделе большое внимание уделяется описанию составных элементов этой структуры и рассмотрению вопросов, связанных с закономерностями ее формирования в сплавах. Это дает дополнительную возможность уяснить те особенности строения конструкционного материала, от которых непосредственно зависит его прочность.
Содержание данной статьи составляет основные положения материаловедения, изучающего специфику строения материалов и его влияние на их различные свойства.
С древнейших времен в качестве конструкционных материалов используются не только металлические, но и неметаллические материалы. Несмотря на успехи, достигнутые в создании неметаллических материалов, все же основными материалами, используемыми в машиностроении, являются и еще долго будут оставаться металлы и их сплавы. В связи с этим первоначально сложилось металловедение как самостоятельная часть материаловедения.
Российские ученые сыграли ведущую роль в развитии металловедения и материаловедения. Одним из них является П. П. Аносов, который в 1831 г. впервые применил микроскоп в разработке методики исследования строения стали. В 1868 г. Д. К. Чернов открытием критических точек в стали установил подлинно научную причину изменения ее свойств при термической обработке, за что получил международное признание.
В 1900 г. на Всемирной выставке в Париже известный французский металлург Г. Монгольфье сказал: «Считаю своим долгом открыто и публично заявить в присутствии стольких знатоков и специалистов, что наши заводы и все сталелитейное дело обязаны настоящим успехом в значительной мере трудам и исследованиям русского инженера Д. К. Чернова, и приглашаю всех выразить ему нашу признательность и благодарность от имени всей металлургической промышленности». А в 1903 г. вышла книга американского металлурга Хоу со следующим посвящением: «Профессору Дмитрию Константиновичу Чернову, отцу металлургии железа».
Возможно эта страница вам будет полезна:
Предмет материаловедение |
Кристаллическое строение и свойства металлов
Характерные свойства металлов, например высокие прочность, пластичность, электро- и теплопроводность и другие, обусловлены их строением на межатомном и внутриатомном уровнях.
Металлы являются телами кристаллическими. Это означает, что атомы в занимаемом ими пространстве расположены строго упорядоченно, находясь в определенных местах на вполне определенных расстояниях друг от друга. При этом атомы не перемещаются друг относительно друга, т. е. они имеют постоянных соседей.
Находясь на своих местах, атомы вследствие термокинетического эффекта совершают колебания частотой с изменяющейся в зависимости от температуры амплитудой.
- В ряде случаев под влиянием локальных тепловых процессов атомы кристаллических тел все же могут перемещаться между соседями в другие положения. Такие перемещения составляют суть явления, называемого диффузией. Диффузия однородных атомов между соседями называется самодиффузией.
Таким образом, сущность кристаллического строения металлов заключается в упорядоченном расположении в них атомов друг относительно друга.
Основные типы кристаллических решеток
Если соединить атомы воображаемыми линиями в трех взаимно перпендикулярных направлениях, то получится пространственная кристаллическая решетка. Ее наименьшим структурным образованием является элементарная ячейка, контур которой представляет какое-нибудь составленное из атомов геометрическое тело, например куб или шестигранную призму. Ячейки,
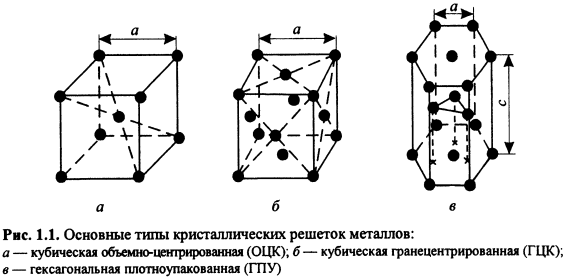
примыкая друг к другу и многократно повторяясь, образуют более крупные образования — зерна или кристаллиты.
Ориентировка ячеек в соседних зернах металла различна, а в пределах каждого зерна одинакова. Поэтому в кристаллической решетке зерен существует ближний и дальний порядок. Ближний означает постоянство ближних атомов-соседей у каждого атома, а дальний — удаленных.
Наиболее простой кристаллической решеткой у металлов является кубическая, имеющая две разновидности: кубическую объемно-центрированную (ОЦК) и кубическую гранецентрированную (ГЦК) (рис. 1.1, я, б). У обоих типов этих решеток основу ячеек составляют восемь атомов, образующих куб и находящихся в его вершинах.
Остальные атомы находятся или в центре объема куба (один атом на пересечении диагоналей в решетке ОЦК), или в центре каждой из его граней (шесть атомов в решетке ГЦК). Кристаллические решетки ОЦК имеют альфа-железо, хром, ванадий, вольфрам, молибден, бета-титан и другие металлы. Решетку ГЦК имеют гамма-железо, алюминий, медь, никель, свинец и некоторые другие металлы.
Другой разновидностью кристаллических решеток у металлов является гексагональная плотноупакованная решетка (ГПУ) (рис. 1.1, в). Ячейка этой решетки представляет собой шестигранную призму с центрированными основаниями, между которыми на некотором расстоянии от центров трех граней расположены еще три атома. ГПУ решетку имеют альфа-титан, магний, цинк, кадмий, бериллий и другие металлы.
В ячейках кристаллической решетки всех типов атомы касаются друг друга внешними слоями электронных оболочек. Межатомные силы сцепления, обеспечивающие морфологическую целостность кристаллической решетки, создаются электромагнитным взаимодействием, обусловленным наличием у атомов валентных электронов.
У металлов, находящихся в твердом состоянии, валентные электроны, освобождаясь от своих атомов, движутся между атомами, которые становятся положительно заряженными ионами. Принадлежащие всему зерну и образующие электронный «газ» свободные электроны, взаимодействуя с положительными ионами, обеспечивают целостность кристаллической решетки. Такая межатомная связь в кристаллической решетке получила название металлической. Она может существовать как между одноименными атомами в чистых металлах, так и между разнородными — в сплавах.
Прочность металла зависит от плотности упаковки его кристаллической решетки и особенностей строения его атомов (особенно валентного и подва-лентного слоев электронной оболочки).
Плотность упаковки решетки, главным образом, определяется числом атомов, приходящихся на одну ячейку решетки, и расстоянием между ними (например, у ОЦК два атома на ячейку, а у ГЦК — четыре).
Наиболее характерным расстоянием является параметр решетки, который равен расстоянию между ближайшими атомами, составляющими грань кристаллической ячейки (см. рис. 1.1, а, б, в). У ОЦК и ГЦК решеток этот параметр одинаков по всем трем направлениям в пространстве, а у ПТУ — . Параметры кристаллических решеток металлов составляют от
до
(
).
Следует помнить, что сила взаимодействия между атомами уменьшается из-за их тепловых колебаний. Результирующая сила взаимодействия тем меньше, чем выше температура.
Кристаллографические направления и плоскости
Упорядоченность расположения атомов в кристаллической решетке позволяет четко выделить отдельные кристаллографические направления и плоскости.
Кристаллографическими направлениями являются прямые или лучи, выходящие из какой-нибудь точки отсчета, вдоль которых на определенном расстоянии друг от друга располагаются атомы. Точками отсчета могут служить вершины куба, при этом кристаллографическими направлениями, например, являются его ребра и диагонали граней (рис. 1.2, а). Могут быть и другие интересующие исследователей направления.
Кристаллографическими плоскостями являются плоскости, на которых лежат атомы, например грани куба или его диагональные плоскости (рис. 1.2, б, в, г).
Кристаллографические направления и плоскости принято обозначать индексами Миллера. Для определения индекса како-го-либо направления следует найти координаты ближайшего к точке отсчета атома, лежащего на этом направлении, выраженные через параметр решетки.
Например, координаты ближайшего атома вдоль оси выразятся через 100. Этими цифрами принято обозначать индекс направления вдоль оси
и параллельных ему направлений:
Индексы направлений вдоль осей и
и параллельных им направлений выразятся соответственно через
и
, а направления вдоль диагоналей граней
и диагонали куба получат индексы соответственно
и
(см. рис. 1.2, а).
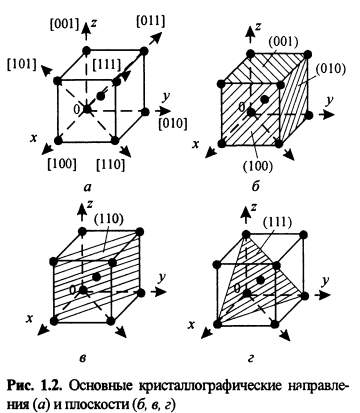
Для определения индекса кристаллографической плоскости следует вначале найти координаты ближайших точек ее пересечения с осями координат, проведенными из точки отсчета Затем обратные величины найденных координат следует записать в обычной последовательности в круглых скобках. Например, координаты точек пересечения с осями координат интересующей нас ближайшей плоскости, параллельной плоскости
(т. е. плоскости верхней грани куба, рис. 1.2, б), являются числа
. Поэтому индекс этой плоскости можно записать так:
Индексы плоскостей, параллельных плоскостям и
, запишутся в виде
и
(рис. 1.2, б). Индекс вертикальной диагональной плоскости куба выразится через
, а индекс наклонной плоскости, пересекающейся со всеми тремя осями координат на удалении одного параметра, примет вид
(рис. 1.2, в, г).
Использование понятий о кристаллографических направлениях и плоскостях и их индексов позволяет описывать различные явления, происходящие в кристаллических телах, а также особенности свойств кристаллических тел вдоль различных направлений и плоскостей.
Дислокационная структура и прочность металлов
Выявляемая в процессе эксплуатации или во время специальных испытаний прочность металлов, называемая фактической или технической, на 2—3 порядка ниже их теоретической прочности. Теоретической прочностью обладает совершенно бездефектный металл, имеющий идеально построенную, однородную во всех ее частях кристаллическую решетку. При его нагружении силой (рис. 1.3, а, б) возникающие касательные напряжения т задействуют, т. е. стремятся разорвать все совершенно одинаковые межатомные связи, пересекающие плоскость сдвига
Из физики твердого тела известна следующая формула для вычисления теоретической прочности: , где
—постоянный для данного металла коэффициент,
— модуль сдвига этого металла. Однако техническая прочность в сотни раз меньше вычисляемой по этой формуле величины. Это объясняется наличием в реальном металле концентраторов напряжений, металлургических дефектов и дефектов кристаллической решетки, важнейшими из которых являются дислокации.
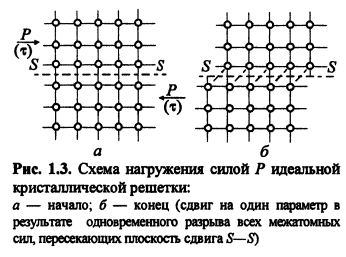
Наличие в металле и его кристаллической решетке перечисленных дефектов при его нагружении силой способствует тому, что все межатомные силы задействуются только на очень малом отрезке упругой деформации, в течение которой сила увеличивается пропорционально деформации. (При деформировании бездефектного металла эта сила продолжала бы возрастать вплоть до разрушения, достигнув при этом теоретического предела.)
Однако при наличии дефектов кристаллической решетки после небольшой упругой деформации происходит пластическая, или, точнее, упруго-пластическая деформация, в течение которой из-за наличия в решетке дефектов под действием приложенной силы разрушается значительно меньшее количество межатомных сил сцепления. При этом начинает действовать принципиально иной, так называемый дислокационный механизм упруго-пластической деформации, развитие которой может завершиться разрушением металла. При наличии в металле металлургических дефектов или концентраторов напряжений разрушение наступает раньше и продолжается в течение значительно более короткого времени.
Изложенное выше показывает, что техническая прочность металла оказывается в сотни и даже тысячи раз меньше теоретической.
Возможно эта страница вам будет полезна:
Примеры решения задач по материаловедению |
Механические свойства материалов и методы их определения
Общие понятия о нагрузках, напряжениях, деформациях и разрушении материалов
Внешние нагрузки, действующие на элементы конструкций и машин, распределены в той или иной мере по некоторой площади или объему.
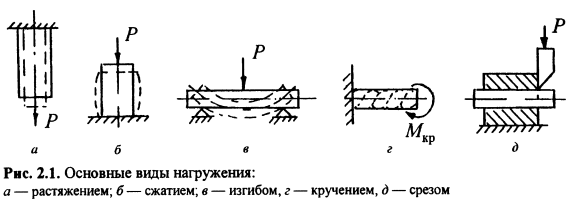
Вследствие этого распределенные нагрузки могут быть поверхностными (например, давление воды или пара на стенку трубы) и объемными (например, силы тяжести, инерции, магнитного притяжения). Однако для упрощения расчетов распределенную нагрузку можно заменить равнодействующей сосредоточенной нагрузкой.
В зависимости от изменения во времени нагрузки подразделяются на статические и динамические. Статические нагрузки, а следовательно и статическое нагружение, характеризуются малой скоростью изменения своей величины. А динамические нагрузки изменяются во времени с большими скоростями, например при ударном нагружении.
В зависимости от характера действия нагрузки подразделяют на растягивающие (рис. 2.1, а), сжимающие (рис.2.1, б), изгибающие (рис. 2.1, в), скручивающие (рис.2.1, г), срезывающие (рис.2.1, г). Изменение нагрузки может иметь периодически повторяющийся характер, вследствие чего их называют повторно-переменными или циклическими (рис. 2.2). В разнообразных условиях эксплуатации конструкций и машин воздействие перечисленных нагрузок может проявляться в различных их сочетаниях.
Под воздействием внешних нагрузок, а также структурно-фазовых превращений в материале конструкции возникают внутренние силы, которые могут быть выражены через внешние нагрузки.
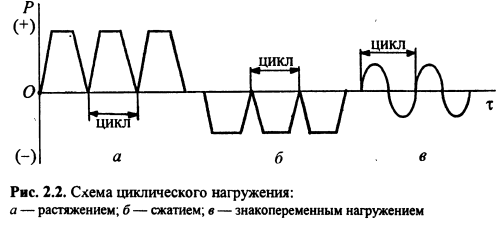
Внутренние силы, приходящиеся на единицу площади поперечного сечения тела, называют напряжениями. Введение понятия напряжений позволяет проводить расчеты на прочность конструкций и их элементов.
В простейшем случае осевого растяжения цилиндрического стержня (рис. 2.3, а) напряжение в поперечном сечении легко определить как отношение растягивающей силы
к площади поперечного сечения
, т. е.
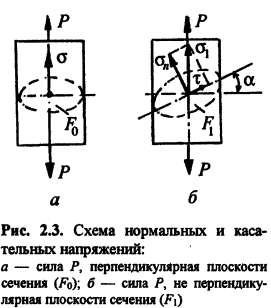
В общем случае, когда сила не перпендикулярна плоскости рассматриваемого сечения
полное напряжение
можно разложить на две составляющие: нормальное напряжение
направленное перпендикулярно данной плоскости, и касательное
, направленное вдоль этой плоскости (рис.2.3, б). На рис. 2.3, б наклонная плоскость
расположена под углом
к плоскости поперечного сечения стержня. Площадь наклонного сечения равна
В плоскости этого сечения действует общее напряжение Разлагая это напряжение по правилу параллелограмма на составляющие, получаем, что нормальное напряжение
а касательное напряжение
Отсюда следует, что максимальное нормальное напряжение возникает при
и равно
(рис.2.3, а), а максимальное касательное напряжение возникает при
и равно
После снятия внешней нагрузки в теле могут оставаться внутренние напряжения. Причиной возникновения внутренних напряжений могут быть также резкие перепады температур и структурно-фазовые превращения, происходящие в процессе технологической обработки материалов.
Существует следующая классификация внутренних напряжений:
- внутренние напряжения первого рода — напряжения, возникающие между крупными частями тела (макроскопические напряжения);
- внутренние напряжения второго рода — напряжения, возникающие между смежными зернами или внутри зерен (микроскопические напряжения);
- внутренние напряжения третьего рода — напряжения, возникающие внутри объема, охватывающего несколько ячеек кристаллической решетки (субмикроскопические напряжения).
Действие внешних сил приводит к деформации тела, т. е. к изменению его размеров и формы. Если на поверхности тела вблизи рассматриваемой точки нанести прямоугольник со сторонами
и
(рис. 2.4, а), то после деформации этот прямоугольник может изменить свои размеры и форму (рис. 2.4, б). Стороны прямоугольника могут увеличиться на
уменьшиться на
или повернуться на угол
по отношению к первоначальному прямому углу’ между сторонами.
Деформация, характеризующая изменение линейных размеров, называется линейной, а деформация, характеризующая изменение углов, — угловой или деформацией сдвига. Линейная или угловая деформация, исчезающая после разгрузки, называется упругой, а остающаяся в теле — пластической (остаточной).
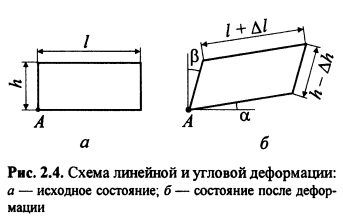
В процессе упругой деформации атомы в кристаллической решетке незначительно смещаются друг относительно друга. Чем больше изменяются расстояния между атомами, тем больше становятся силы межатомного взаимодействия.
При снятии внешней нагрузки под действием этих сил атомы возвращаются в исходное положение, искажения решетки исчезают, а тело принимает первоначальные форму и размеры.
В процессе пластической деформации атомы в кристаллической решетке смещаются на большие расстояния, чем при упругой деформации, причем это смещение становится необратимым. После снятия нагрузки в результате пластической деформации размеры и форма тела изменяются. Смещение атомов при пластической деформации может происходить скольжением (сдвигом) и двойникова-нием.
Скольжение происходит по плоскостям и в направлении с наиболее плотной упаковкой атомов, где расстояния между соседними атомными плоскостями наибольшие, а силы взаимодействия между ними наименьшие, в результате чего сопротивление сдвигу также будет наименьшим. При двойниковании происходит такое смещение части зерна, при котором эта часть занимает зеркально-симметричное положение по отношению к несмещенной части зерна (см. рис. 1.18).
Упругопластическая деформация при достижении достаточно высоких напряжений может завершиться разрушением тела. Процесс разрушения состоит из нескольких стадий: зарождение микротрещин, образование макротрещин, распространение макротрещины по всему сечению тела.
В общем случае различают вязкое и хрупкое разрушения. Вязкое разрушение происходит срезом под действием касательных напряжений и сопровождается значительной пластической деформацией. Для вязкого разрушения характерен волокнистый (матовый) излом детали или образца.
Хрупкое разрушение происходит под действием нормальных растягивающих напряжений, вызывающих отрыв одной части тела от другой без заметных следов макропластической деформации. Для хрупкого разрушения характерен кристаллический (блестящий) излом.
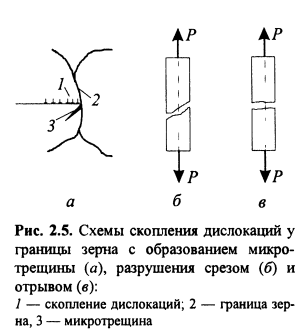
Возникновение микротрещин при вязком и хрупком разрушениях происходит путем скопления дислокаций перед границами зерен (рис. 2.5) или другими препятствиями (неметаллические включения, карбидные частицы, межфазовые границы и др.), что приводит к концентрации напряжений.
При анализе микроструктуры различают транскристаллитное (по телу зерна) и интеркристаллитаое (по границам зерен) разрушения. Разрушение металла в условиях эксплуатации конструкций и машин может быть не только вязким или хрупким, но и смешанным — вязкохрупким.
Возможно эта страница вам будет полезна:
Методические указания по материаловедению |
Испытания на твердость
Твердость — это свойство материала оказывать сопротивление контактной деформации или хрупкому разрушению при внедрении индентора в его поверхность.
Испытания на твердость — самый доступный и распространенный вид механических испытаний. Наибольшее применение в технике получили статические методы испытания на твердость при вдавливании индентора: метод Бринелля, метод Виккерса и метод Роквелла.
При испытании на твердость по методу Бринелля (ГОСТ9012—59) в поверхность материала вдавливается твердосплавный шарик диаметром под действием нагрузки
и после снятия нагрузки измеряется диаметр отпечатка
(рис. 2.10, а). Число твердости по Бринеллю
подсчитывается как отношение нагрузки
к площади поверхности сферического отпечатка

Для получения сопоставимых результатов при определении твердости шариками различного диаметра необходимо соблюдать условие подобия. Подобие отпечатков при разных
и
будет обеспечено, если угол
остается постоянным (рис. 2.10, а). Подставив в формулу (2.2)
, получим следующее выражение:
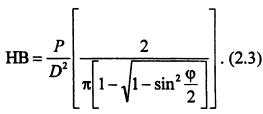
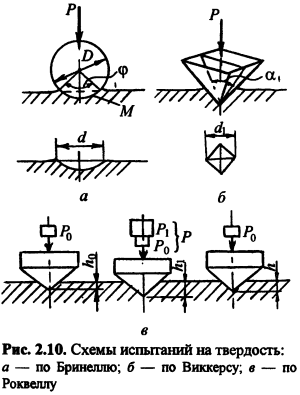
Из формулы (2.3) следует, что значение будет оставаться постоянным, если
и
. Выбор отношения
, а следовательно и нагрузки вдавливания
, зависит от уровня твердости материала. Чем более твердый материал, тем рекомендуется большее отношение
. Исходя из этого в ГОСТ 9012—59 приведены следующие значения отношений
(сталь, чугун, высокопрочные сплавы); 98 (алюминий, медь, никель и их сплавы); 49 (магний и его сплавы); 24,5 (подшипниковые сплавы); 9,8 (олово, свинец).
При
и времени выдержки под нагрузкой 10 с твердость по Бринеллю обозначается символом
с указанием числа твердости. При этом размерность
не ставится, например 200
. При использовании шариков других диаметров (1, 2, 2,5 и 5 мм) изменяется нагрузка вдавливания, а символ твердости
дополняется тремя индексами. Например,
обозначает, что при
и времени выдержки под нагрузкой 30 с число твердости по Бринеллю равно 180.
Метод Бринелля не рекомендуется применять для материалов с твердостью более так как стальной шарик может заметно деформироваться, что внесет погрешность в результаты испытаний.
При испытании на твердость по методу Виккерса (ГОСТ2999—75) в поверхность материала вдавливается алмазная четырехгранная пирамида с углом при вершине (рис. 2.10, б). После снятия нагрузки вдавливания измеряется диагональ отпечатка
Число твердости по Виккерсу
подсчитывается как отношение нагрузки
к площади поверхности пирамидального отпечатка
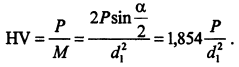
Число твердости по Виккерсу обозначается символом с указанием нагрузки
и времени выдержки под нагрузкой, причем размерность числа твердости
не ставится. Продолжительность выдержки индентора под нагрузкой принимают для сталей 10—15 с, а для цветных металлов — 30 с. Например,
означает, что число твердости по Виккерсу 450 получено при
, приложенной к алмазной пирамиде в течение 15 с.
Преимущество метода Виккерса по сравнению с методом Бринелля заключается в том, что методом Виккерса можно испытывать материалы более высокой твердости из-за применения алмазной пирамиды.
При испытании на твердость по методу Роквелла (ГОСТ 9013—59) в поверхность материала вдавливается алмазный конус с углом при вершине или стальной шарик диаметром 1,588 мм. Однако, согласно этому методу, за условную меру твердости принимается глубина отпечатка. Схема испытания по методу Роквелла показана на рис. 2.10, в.
Вначале прикладывается предварительная нагрузка , под действием которой индентор вдавливается на глубину
. Затем прикладывается основная нагрузка
, под действием которой индентор вдавливается на глубину
. После этого снимают нагрузку
, но оставляют предварительную нагрузку
. При этом под действием упругой деформации индентор поднимается вверх, но не достигает уровня
. Разность (
) зависит от твердости материала; чем тверже материал, тем меньше эта разность.
Глубина отпечатка измеряется индикатором часового типа с ценой деления 0,002 мм. При испытании мягких металлов методом Роквелла в качестве индентора применяется стальной шарик. Последовательность операций такая же, как и при испытании алмазным конусом. Число твердости, определенное методом Роквелла, обозначается символом .
Однако в зависимости от формы индентора и значений нагрузок вдавливания к этому символу добавляется буква , или
, или
, обозначающая соответствующую шкалу измерений. Обозначения твердости и значения нагрузок вдавливания для разных шкал измерений методом Роквелла приведены ниже:
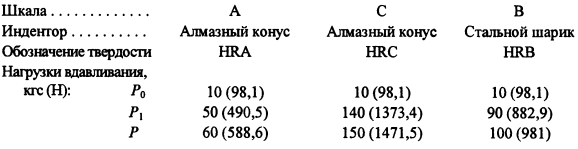
Различие в нагрузке для шкал
и
объясняется тем, что по шкале
измеряют твердость особо твердых материалов и в этом случае во избежание повреждений алмазного конуса рекомендуется меньшая нагрузка вдавливания. Числа твердости по Роквеллу подсчитывают по формулам
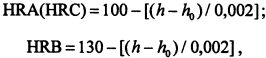
где 100 и 130 — предельно заданное число делений индикатора часового типа с ценой деления Например,
означает, что твердость, определенная методом Роквелла по шкале
при вдавливании алмазного конуса, равна 50 (размерность не ставится).
Преимущество метода Роквелла по сравнению с методами Бринелля и Виккерса заключается в том, что значение твердости по методу Роквелла фиксируется непосредственно стрелкой индикатора, при этом отпадает необходимость в оптическом измерении размеров отпечатка.
Для измерения твердости тонких слоев материалов и даже их отдельных структурных составляющих применяют метод микротвердости (ГОСТ 9450—76). Этот метод по существу не отличается от метода Виккерса, однако при этом используют малые нагрузки вдавливания: 0,049 (0,005), 0,098 (0,01), 0,196 (0,02), 0,49 (0,05), 0,98 (0,1), 1,962 (0,2), 4,9 (0,5)
Возможно эта страница вам будет полезна:
Учебник по материаловедению |
Понятие о металлических сплавах
Сплавы — сложные вещества, получаемые сплавлением или спеканием двух или нескольких простых веществ, называемых компонентами. (При сплавлении компоненты доводят до плавления, а при спекании их порошки смешивают и подвергают давлению при высокой температуре.)
Сплав считается металлическим, если его основу (свыше по массе) составляют металлические компоненты. Металлические сплавы обладают более высокими прочностными и другими механическими свойствами по сравнению с чистыми металлами. По этой причине они получили широкое применение в качестве конструкционных материалов.
В данной главе рассматриваются особенности строения и свойств двойных, или двухкомпонентных, сплавов. Полученные при этом знания и представления послужат теоретической основой для уяснения природы и специфики свойств сплавов, состоящих из трех и большего числа компонентов. Этому благоприятствует то обстоятельство, что основу большинства многокомпонентных сплавов, как правило, составляет какой-нибудь двойной сплав.
Например, основу легированных сталей составляет сплав железа с углеродом. Основа всех многокомпонентных цветных сплавов (латуней, бронз, титановых и других сплавов), как правило, состоит из двух главных компонентов.
Возможно эта страница вам будет полезна:
Рефераты по материаловедению |
Виды двойных сплавов
В зависимости от природы сплавляемых компонентов они, взаимодействуя друг с другом, могут образовать различные по строению и свойствам продукты. Характер взаимодействия компонентов при сплавлении зависит от их положения в таблице Д. И. Менделеева, особенностей строения электронных оболочек их атомов, типов и параметров их кристаллических решеток, соотношения температур их плавления, их атомных диаметров и других факторов.
В зависимости от преобладания тех или иных перечисленных факторов компоненты при сплавлении могут образовывать: смеси своих зерен с пренебрежимо ничтожной взаимной растворимостью; неограниченно или частично растворяться друг в друге; образовывать химические соединения.
Смеси состоят из практически чистых зерен обоих компонентов, сохраняющих присущие им типы кристаллических решеток и прочностные свойства (см. рис. 3.2, б).
При растворении компонентов друг в друге образуются твердые растворы. Получающийся при этом продукт представляет собой зерна, кристаллическая решетка которых построена из атомов обоих компонентов.
Если атомы растворимого компонента замещают в узлах решетки атомы компонента-растворителя, то образующийся раствором замещения (рис. 3.1, а). Такие растворы образуют компоненты с аналогичными типами кристаллических решеток при небольшой разнице их параметров.
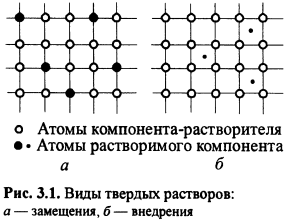
Если растворимый компонент имеет очень малый атомный диаметр, то образуется твердый раствор внедрения (рис. 3.1, б). В этом случае энергозатраты на образование раствора оказываются меньшими, так как атомы растворимого компонента (например, углерода в железе) размещаются в междоузлии ячейки кристаллической решетки растворителя, не вытесняя атомов растворителя из узлов решетки.
- Компоненты с неограниченной растворимостью образуют только растворы замещения. Ограниченная растворимость наблюдается как у твердых растворов замещения, так и у растворов внедрения.
При ограниченной растворимости компонентов за пределами их растворимости образуются или смеси зерен ограниченных твердых растворов обоих компонентов друг в друге (например, компонента в
и компонента
в
), или смеси зерен ограниченного раствора и химического соединения компонентов.
В твердых растворах замещения преобладающей связью между атомами является металлическая. В растворах внедрения вместе с металлической может возникать и ковалентная связь.
Например, каждый атом углерода, растворенный в ОЦК решетке альфа-железа, два валентных электрона отдает на образование металлической связи, а два других — на образование ковалентных направленных трехцентровых ()-связей с двумя ближайшими атомами железа. Ковалентная связь на порядок сильнее металлической. Особенности межатомных связей в зернах твердых растворов предопределяют их прочностные и другие свойства.
Образующиеся при сплавлении двух компонентов химические соединения имеют строго определенный состав. Они представляют собой зерна со специфической кристаллической решеткой, отличной от решеток обоих компонентов. Ячейки решеток химических соединений имеют сложное строение.
Связь между атомами в них сильнее и жестче металлической. Поэтому они являются очень твердыми и хрупкими веществами. Существует несколько видов химических соединений, отличающихся спецификой строения и свойств, которые здесь рассматриваться не будут.
Если образующиеся в сплавах химические соединения оказываются стойкими веществами, не диссоциирующими при нагреве вплоть до температуры плавления, то их принято рассматривать в качестве самостоятельных компонентов, способных образовывать сплавы с компонентами сплава.
В связи с изложенным все существующие металлические сплавы можно разделить на четыре основных вида (рода): 1) смесь зерен компонентов; 2) неограниченные твердые растворы; 3) с ограниченной растворимостью компонентов; 4) с устойчивым химическим соединением.
Возможно эта страница вам будет полезна:
Лабораторные по материаловедению |
Диаграммы состояния двойных сплавов и характер изменения свойств в зависимости от состава сплавов
Диаграммы состояния представляют собой график в координатах состав сплава — температура, на котором отражены продукты, образующиеся в результате взаимодействия компонентов сплава друг с другом в условиях термодинамического равновесия при различных температурах.
Этими продуктами являются вещества, имеющие в зависимости от температуры и состава определенное агрегатное состояние, специфический характер строения и вполне определенные свойства. Их принято называть фазами. Причем фазой считается определенная часть системы, образованной компонентами сплава, которая во всех своих точках имеет одинаковые состав, строение и свойства.
Жидкая фаза представляет собой раствор расплавленных компонентов.
Твердые фазы являются зернами, имеющими определенную форму, размер, состав, специфику строения и свойства. Твердые фазы можно наблюдать в микроскоп. Это могут быть твердые растворы, химические соединения, а также зерна чистых компонентов, не образующих с другими компонентами ни твердых растворов, ни химических соединений.
Диаграмма состояния разделена линиями на области. Отдельные области могут состоять только из одной фазы, а некоторые — из двух, имеющих разные составы, строение и свойства. Анализируя диаграмму состояния, можно составить представление о специфике свойств сплавов данной системы компонентов и характере их изменения в зависимости от состава, а также о возможности термической обработки сплавов и температуре нагрева для ее проведения.
В диаграммах состояния содержится информация, необходимая для создания и обработки сплавов различного назначения. Ниже рассматриваются четыре основных типа (рода) диаграмм состояния.
Диаграмма состояния I рода. Правило отрезков. Данная диаграмма охватывает сплавы, компоненты которых образуют смеси своих практически чистых зерен при ничтожной взаимной растворимости (рис. 3.2). На оси абсцисс отложена процентная доля компонента в сплаве.
Фазовое строение сплавов на диаграмме зависит от температуры. При термодинамическом воздействии компонентов друг на друга снижается температура их перехода в жидкое состояние, достигая некоторого минимума при определенном для каждой пары компонентов составе (рис. 3.2, точка ).
Состав сплава можно определить, спроецировав точку на ось абсцисс (точка
). Сплав двух компонентов, который плавится при минимальной температуре, называется эвтектическим или эвтектикой.
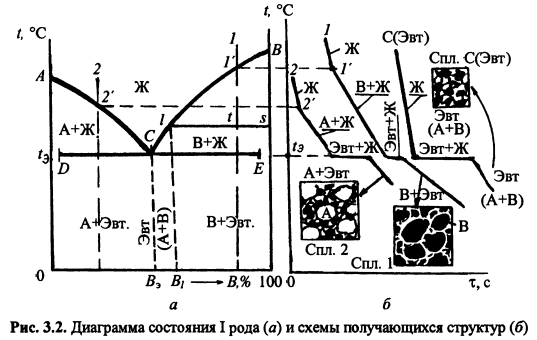
Эвтектика является равномерной смесью одновременно закристаллизовавшихся мелких зерен обоих компонентов. Температура, при которой одновременно плавятся или кристаллизуются оба компонента, называется эвтектической температурой .
На диаграмме состояния температуры, выше которых сплавы находятся в жидком состоянии, лежат на линии , называемой линией ликвидуса (рис. 3.2, а) (от лат. «ликвидус» — жидкий, текучий).
Переход сплавов из жидкого состояния в твердое при кристаллизации происходит в интервале температур, лежащих между линией ликвидуса и эвтектической температурой, которой соответствует линия солидуса (от лат. «солидус» — твердый).
При этом из каждого сплава по мере снижения температуры в твердую фазу переходит вначале тот компонент, количество которого превышает эвтектическую концентрацию (см. рис. 3.2, б).
Поэтому у сплавов левее точки двухфазная область содержит избыточный компонент
и жидкую фазу
, а в заэвтектической области
находятся соответственно твердая
и жидкая
фазы. В обоих случаях фаза
является жидким раствором обоих компонентов.
По мере снижения температуры и приближения ее к состав неза-кристаллизовавшейся фазы приближается к эвтектическому
(рис. 3.2, точка
). При этом чем меньше сплав отличается по составу от эвтектического, тем ниже его точка ликвидуса и тем больше в нем затвердевает эвтектики.
Количественные изменения в сплавах данной системы компонентов (касающиеся состава твердой и жидкой фаз и их долей в единице массы любого сплава) при кристаллизации подчиняются правилу отрезков.
Воспользуемся этим правилом на примере затвердевания сплава (рис. 3.2). Предположим, что нас интересуют составы и число фаз при произвольно взятой температуре, соответствующей изотерме
.
При данной температуре состав жидкой фазы всех заэвтектических сплавов, включая и сплав , будет одинаковым, равный значению
. Состав твердой фазы будет соответствовать
компонента
. Таким образом, при кристаллизации сплавов состав жидкой фазы изменяется по линии ликвидуса от исходного до эвтектического.
Масса твердой фазы при данной температуре определяется величиной отрезка , а жидкой — отрезка
. Если массу всего сплава
выразить через
, то относительные доли твердой
и жидкой
фаз можно представить в виде
и
. Пользуясь этими выражениями, можно вычислить и абсолютные массовые доли каждой из фаз при любой температуре.
В зависимости от состава все сплавы данной системы делятся на доэв-тектические и заэвтектические. Доэвтектические сплавы содержат компонента свыше
. В них он является избыточным компонентом. В заэвтектических сплавах избыточным является компонент В. В них его количество превышает
.
При температурах ниже линии солидуса фазовый состав всех сплавов рассматриваемой системы состоит из зерен обоих компонентов: .
Следует различать присутствующие в любом сплаве мелкие зерна А и В, составляющие эвтектику, и крупные зерна избыточных фаз — компонентов или
соответственно в доэвтектических и заэвтектических сплавах [см. схемы структур на рис. 3.2, б, соответствующие кривым охлаждения сплавов 2,1 и
].
Для более точной оценки прочностных и других свойств затвердевших сплавов целесообразно учитывать наличие эвтектики в их структурно-фазовом составе (рис. 3.2, б). Так, структура доэвтектических сплавов состоит из (см. сплав 2), а структура заэвтектических — из
(см. сплав 1), т. е. имеются крупные и мелкие одноименные зерна.
Количество каждой структурной составляющей, от которого зависят свойства сплава, может быть вычислено по правилу отрезков применительно к эвтектической температуре.
При оценке прочностных и других свойств следует иметь в виду, что та часть сплава, которая представлена эвтектикой, имеет более высокую прочность, чем часть, представленная более крупными зернами избыточной фазы.
Характер зависимости прочности сплавов от их состава представлен на рис. 3.3, а. Здесь в верхней части изображена диаграмма состояний с указанием фазового состава, а под ней показан характер изменения прочности.
Если бы размер зерен у всех структурных составляющих сплавов был одинаков, то прочность изменялась бы строго по линейному закону (см. рис. 3.3, д, линия ).
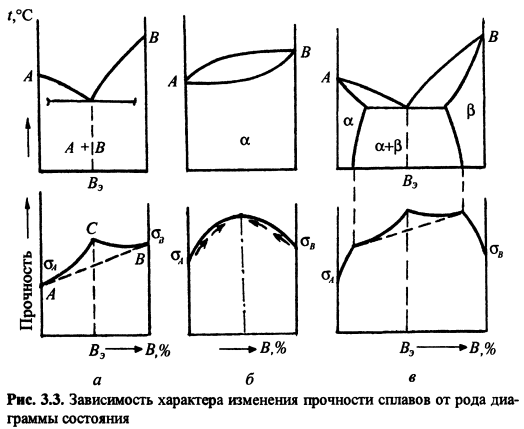
Такое изменение свойств обусловлено законом аддитивности, согласно которому каждая из двух фаз вносит в суммарную прочность сплава часть своей прочности, соответствующую доле этой фазы в сплаве.
В связи с этим прочность любого сплава ст может быть вычислена по формуле , где
— доля фазы
в структуре сплава;
и
— прочности фаз
и
.
Поскольку эвтектическая часть сплава обладает более высокой прочностью, фактическое изменение этого свойства будет происходить по кривой (рис. 3.3, а).
Аналогично с учетом их характера и в зависимости от состава изменяются и другие свойства сплавов. Такой характер изменения свойств рассматриваемых сплавов под действием приложенной силы объясняется тем, что в данном случае полная реакция сплава на внешнее воздействие складывается из реакций зерен обеих фаз.
Диаграмма состояний II рода. Дендритная ликвация. При неограниченной растворимости компонентов друг в друге, имеющих одинаковые типы решеток и сходное строение наружных электронных оболочек, получают диаграммы II рода. На диаграмме можно различить три фазовые области (рис. 3.4, а).
Выше линии ликвидуса находится область жидкой фазы
.
Под ней до линии солидуса расположена двухфазная область
. Фаза а представляет собой твердый раствор компонентов
и
. Зерна этой
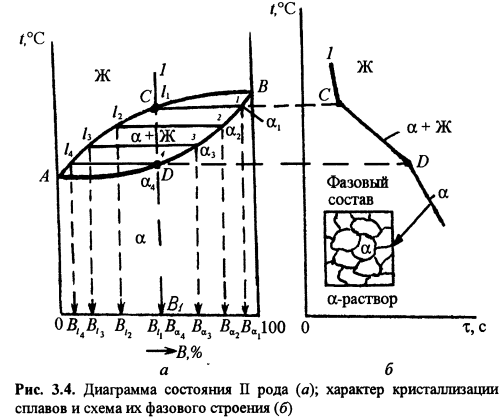
фазы имеют единую кристаллическую решетку. Однако у сплавов разного состава число атомов компонентов и
в элементарных ячейках решетки различно.
Область, расположенная под линией солидуса, является однофазной (фаза а).
В отличие от сплавов смесей зерен практически чистых компонентов каждый из затвердевших сплавов на рассматриваемой диаграмме состояния представляет собой совокупность внешне ничем не отличающихся друг от друга зерен фазы (рис. 3.4, б).
Кристаллизация -фаз в сплавах разного состава происходит в соответствии с правилом отрезков. Если проследить специфику кристаллизации какого-нибудь из сплавов, например сплава 1 (рис. 3.4), то согласно правилу отрезков в двухфазной области составы жидкой и твердой фаз в зависимости от температуры изменяются соответственно по линиям ликвидуса и солидуса (рис. 3.4, а, изотермы 1,2, 3 и 4). Составы жидкой фазы от точки
до
выражаются через
и
, а составы твердой фазы а изменяются от
до
.
Количество сосуществующих при каждой из температур фаз и
определяется соответствующими отрезками изотерм. Причем отрезки, находящиеся слева от вертикали
, определяют количество фазы
. Длины отрезков, находящихся справа, пропорциональны количеству фазы
.
В случае равновесной кристаллизации, происходящей при достаточно малой скорости охлаждения сплава, к концу кристаллизации (изотерма 4) состав окончательно сформировавшейся фазы должен соответствовать исходному составу сплава
, (в данном случае сплава 1). Это обусловлено непрерывно происходящей диффузией между обеими фазами.
В случае ускоренного охлаждения сплава при кристаллизации диффузионные процессы не успевают завершиться. В связи с этим центральная часть каждого зерна оказывается обогащенной более тугоплавким компонентом (в данном случае ), а периферийная — легкоплавким компонентом (
). Это явление называется дендритной ликвацией, снижающей прочностные и другие свойства сплавов. Ее предотвращение возможно за счет медленного охлаждения сплава, обеспечивающего его равновесную кристаллизацию.
В случае возникновения дендритной ликвации она может быть устранена путем длительного, так называемого диффузионного, отжига сплава. Происходящие при этом диффузионные процессы выравнивают химический состав в зернах.
У сплавов — твердых растворов — прочность и другие свойства в зависимости от состава изменяются по криволинейному закону (см. рис. 3.3, б). Чтобы понять характер изменения прочности сплавов в зависимости от состава, необходимо уяснить следующее.
Во время пластической деформации металлического материала внешняя сила должна преодолеть сопротивление передвижению дислокаций, определяемое значением силы Пайерлса—Набарро. Эта сила зависит от интенсивности межатомного взаимодействия в кристаллической решетке сплава.
Атомы растворимого компонента образуют в решетке твердого раствора более прочную металлическую связь с атомами компонента-растворителя, чем в решетках обоих чистых компонентов. Из-за этого сопротивление пластической деформации твердого раствора с увеличением содержания растворенного в нем другого компонента должно возрастать по какому-то криволинейному закону.
Характер хода кривой с максимумом на рис. 3.3, б станет понятным, если исходить из того, что в сплавах слева от максимума решеткой, подвергающейся упрочнению, является решетка компонента , а справа — решетка компонента
. Состав, соответствующий максимуму, является критическим, поскольку роли компонентов как растворителей и растворимых меняются на противоположные.
Мотт и Набарро установили зависимость между пределом текучести сплава — твердого раствора , его составом, модулем сдвига
и размерами атомов компонентов:
, где
— атомная концентрация растворенного компонента;
— параметр, зависящий от атомных радиусов компонентов (
и
— радиусы атомов растворимого компонента и растворителя).
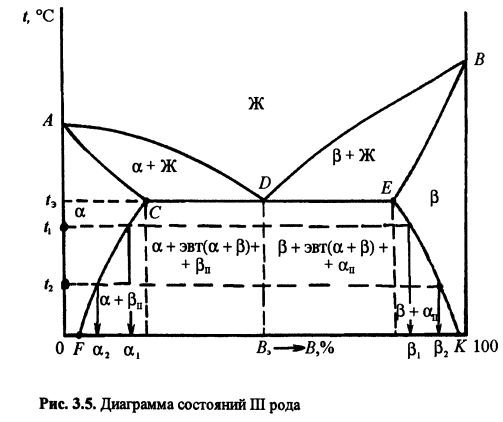
Диаграмма состояний III рода характерна для сплавов, образующихся при сплавлении компонентов, имеющих ограниченную растворимость друг в друге.
Рассмотрим случай, когда за пределами растворимости компонентов образуются механические смеси твердых растворов на основе каждого из них (рис. 3.5). На диаграмме состояний представлены: жидкая фаза Ж (выше линии ликвидуса ); две области
и
(лежащие между линиями ликвидуса и солидуса
); две области ограниченных твердых растворов
и
(лежащие ниже отрезков линии солидуса, соответственно
и
) и двухфазная область
— область
.
Фаза является твердым раствором компонента
в
. Фаза
представляет собой твердый раствор компонента
в
. Взаимная растворимость компонентов друг в друге, как правило, зависит от температуры. Кривые
и
отражают характер изменения растворимости в зависимости от температуры соответственно компонента
в
-фазе и компонента
в
-фазе).
Составы фаз при любой температуре можно определить, опустив на ось концентраций перпендикуляры из соответствующих точек, лежащих на линиях и
. При
и
составы фаз
и
:
и
.
В структурно-фазовом составе сплавов данной системы важное место занимает эвтектика, представляющая собой смесь мелкозернистых фаз и
. Она имеет определенный состав и кристаллизуется при наименьшей для данной системы температуре
, т. е. на линии
. Ниже этой линии находится область двухфазных сплавов. В ней структура доэвтектических сплавов состоит из первичных зерен
-фазы, равномерно распределенных в эвтектике
, и зерен вторичной
-фазы, выделившейся из твердой фазы
при снижении температуры.
Заэвтектические сплавы соответственно состоят из первичной -фазы, эвтектики и зерен вторичной фазы
.
Для уяснения характера обусловленного снижением температуры распада фаз и
, сопровождающегося выделением фаз
и
, заметим, что в доэвтектических сплавах в результате неизбежного при их охлаждении распада имеющейся в них
-фазы (в эвтектике и
) также образуется и вторичная
-фаза (
). Однако на диаграмме состояний это не указывается, так как при выделении фаза
сливается с окружающими ее зернами первичной фазы
и как самостоятельная структурная составляющая не наблюдается. То же можно сказать о
в заэвтектических сплавах.
На рис. 3.3, в показан характер изменения прочности сплавов рассматриваемой системы в зависимости от состава. Как и следовало ожидать, в однофазных областях твердых растворов и
свойства изменяются по криволинейному закону, а в двухфазной области
— по закону аддитивности с учетом влияния имеющейся в сплавах мелкозернистой эвтектики (см. рис. 3.3, в).
Подобным образом изменяются и другие свойства сплавов, охватываемых диаграммой состояний III рода. Характер изменения свойств сплавов в зависимости от состава отражает уровень свойств равновесных сплавов, обладающих минимальной плотностью дислокаций и идеальным металлургическим качеством.
Диаграмма состояний IV рода относится к случаю, когда сплавляемые компоненты при соотношении образуют устойчивое химическое соединение, не диссоциирующее при нагреве вплоть до температуры плавления. В связи с этим его правомерно рассматривать в качестве самостоятельного компонента, способного образовывать сплавы с каждым из исходных компонентов.
Соединение при сплавлении с компонентами
и
в зависимости от их природы может образовывать с ними различные по характеру системы Например (рис. 3.6), компонент
образует с компонентами
и
сплавы, относящиеся к диаграмме состояний 1 рода. В связи с этим фазовый состав любого сплава системы
—
в твердом состоянии должен представлять смесь химического соединения и одного из исходных компонентов.
Уровень свойств сплавов и характер их изменения в зависимости от состава в этом случае должны изменяться по закону аддитивности (см. рис. 3.3, а) с учетом влияния эвтектики.
Характер изменения свойств сплавов в зависимости от состава предопределяется диаграммой состояния. На это положение впервые серьезное
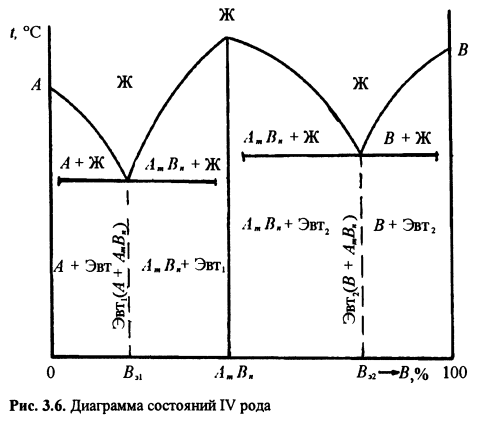
внимание обратил академик Н. С. Курнаков, внесший фундаментальный вклад в методику изучения свойств сплавов.
Заключение по теории сплавов. Уяснив основные положения теории сплавов, нетрудно понять, что можно создавать сплавы различного назначения, целенаправленно закладывая в них такие факторы, которые позволят на последующих этапах технологической обработки формировать в сплавах требуемые дислокационно-фазовые структуры и необходимые комплексы механических и других свойств. Этому будут способствовать сведения, которые можно получить из анализа диаграмм состояний. Остальная дополнительная теория из учебников по материаловедению тут.
В связи с этим особую ценность представляют такие сведения, как поведение сплавов при наличии или отсутствии в них переменной растворимости компонентов или аллотропических превращений при изменении температуры.
Очень важно четко уяснить описанные выше характер и причины изменения свойств сплавов в зависимости от типа диаграммы состояний. Хотя эти свойства и относятся к равновесному состоянию, однако дополнительной обработкой их можно целенаправленно изменять. Причем изменение касается только уровня свойств, а характер изменения, как правило, сохраняется «диаграммный».
Особенно важно подчеркнуть положение, согласно которому в кристаллических решетках твердых растворов интенсивность межатомного взаимодействия значительно выше, чем в решетках составляющих их компонентов. В связи с этим образуются высокостабильные фазы с повышенной прочностью (следствие возросших сил Пайерлса—Набарро), более высоким сопротивлением коррозии (затрудняется вырывание атомов с поверхности детали действием агрессивной среды) и замедленными диффузионными процессами из-за возросшей энергии активации.
Все это имеет определяющее значение при создании легированных сталей и сплавов различного целевого назначения.