Оглавление:
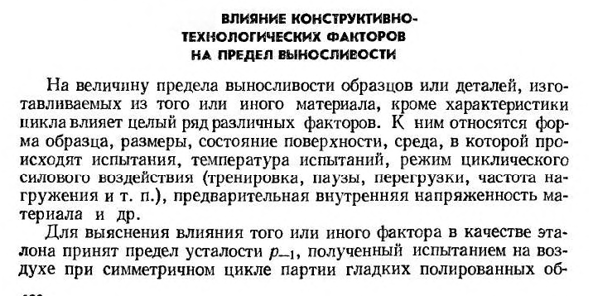

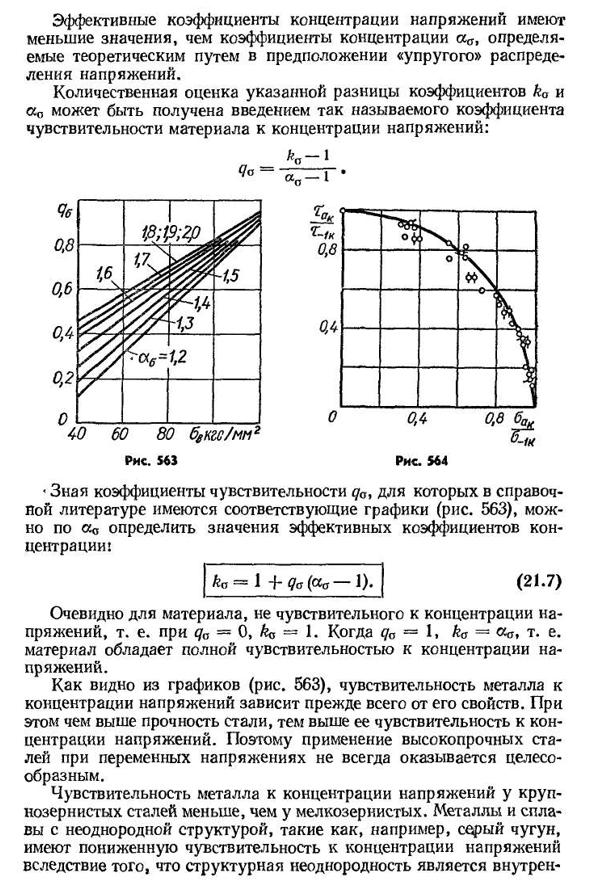
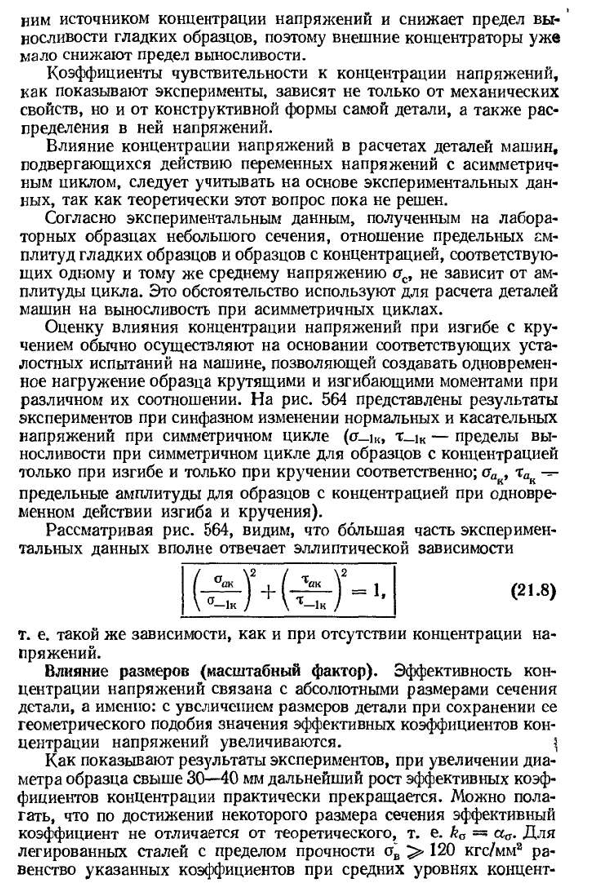
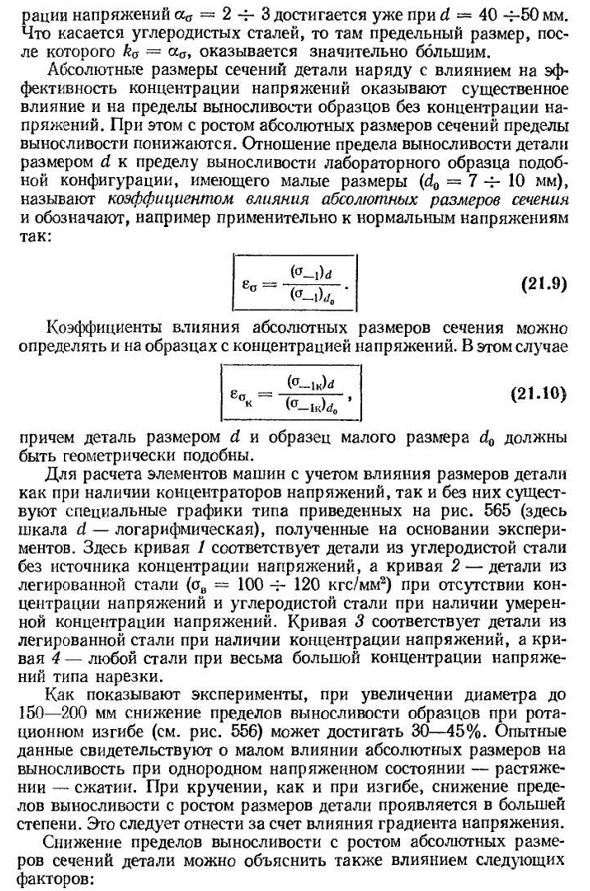
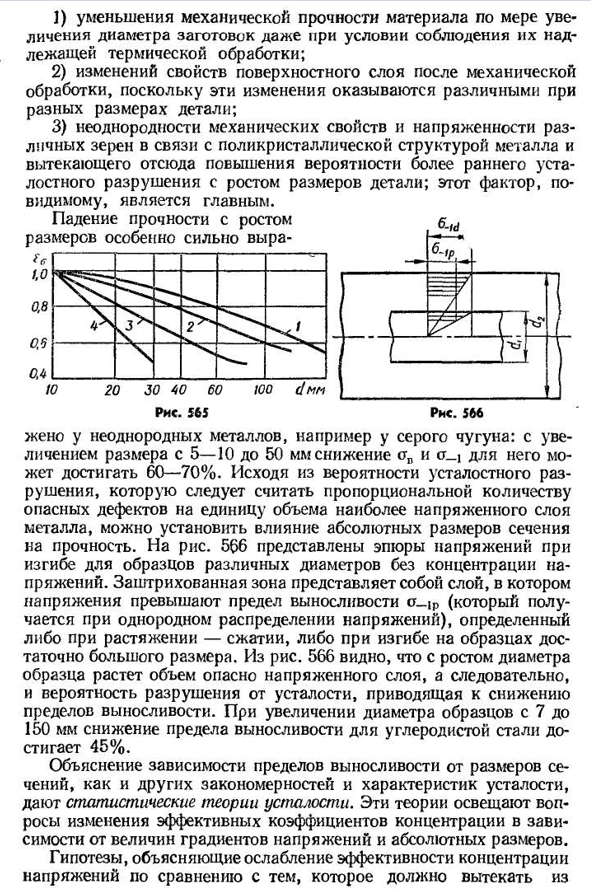
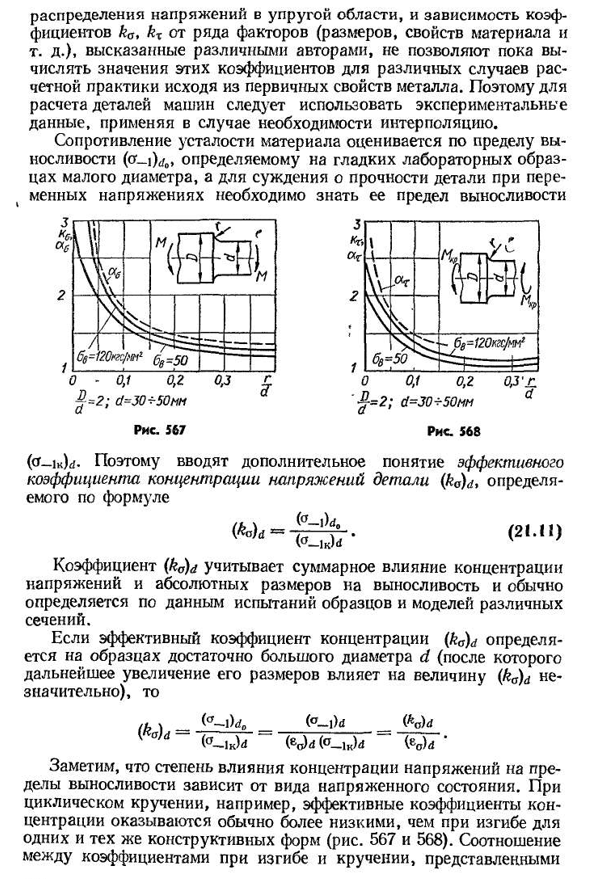
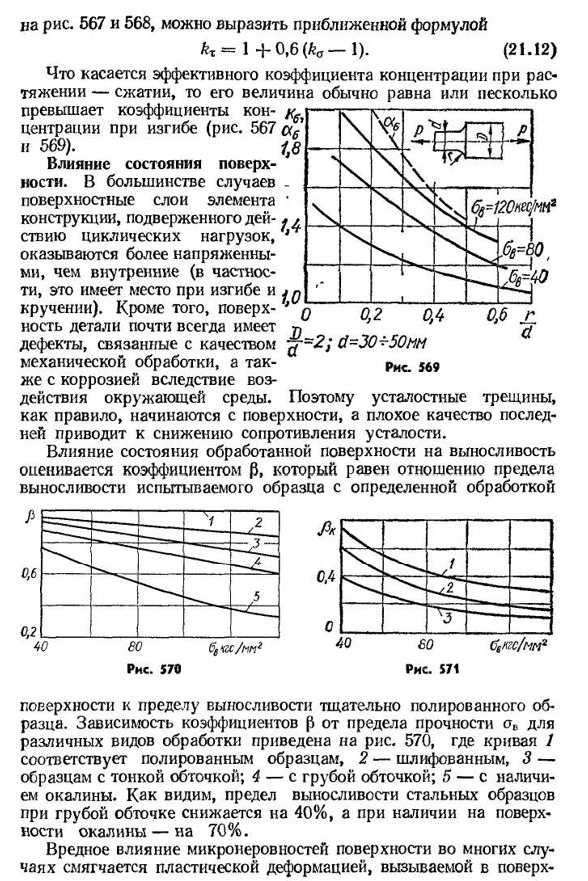
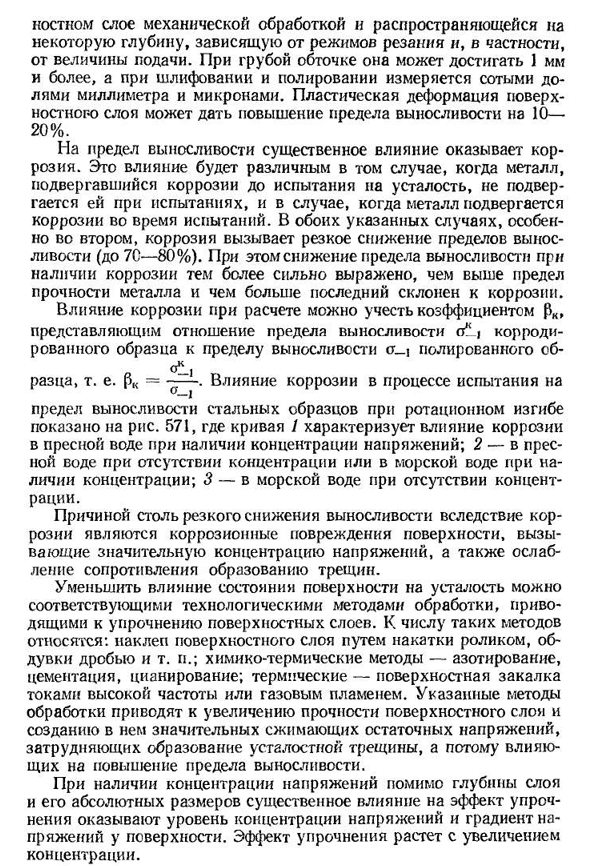
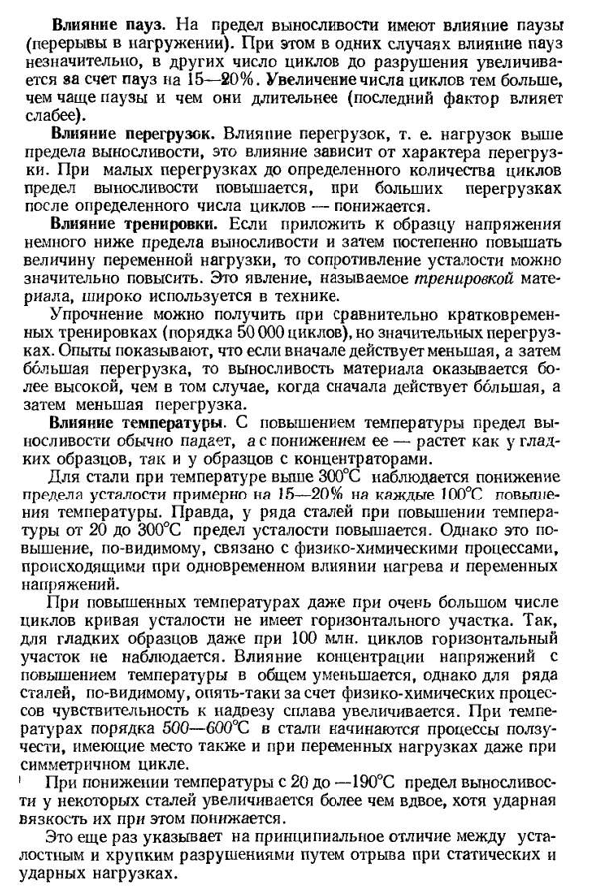

Влияние конструктивно-технологических факторов на предел выносливости
- Структурное воздействие Технический фактор На пределе выносливости Помимо характеристик Nikla, на значения пределов выносливости образцов или деталей, изготовленных из этого материала, влияют многие различные факторы. К ним относятся геометрия, размер образца, состояние поверхности, циклическое силовое воздействие (сверление, пауза, перегрузка, частота нагрузки и др.) в среде, где находится тест, режим температурного тестирования.), Материал пре-напряжения ЕТК. В стандарте использованы пределы усталости, полученные при испытаниях на воздухе в симметричных циклах гладких полированных деталей для выявления влияния таких факторов, как p_i.- 600разное
диаметром 7-10 мм. Затем влияние различных факторов долговечности определяется пределом допуска рассматриваемого образца от стандартного предела выносливости p_i по отклонению предела выносливости p li рассматриваемой партии. Влияние концентрации напряжений. Наиболее важным фактором, снижающим предел выносливости, является концентрация напряжений, вызванная резким изменением поперечного сечения детали. Реальный стресс-редуктор-это ключевой путь, отверстие детали, резка поверхности, малый радиус закругления в местах резких изменений размеров поперечного сечения и т. д. Концентрация напряжений, как правило, способствует возникновению усталостных трещин, что в конечном
итоге приводит к разрушению деталей. Эксперимент показывает, что для Людмила Фирмаль
переменных напряжений предел выносливости, связанный с концентрацией напряжений, больше, чем частное гладкого образца, путем деления предела выносливости на теоретический коэффициент концентрации напряжений a0 (см.§ 33)., — Р. Это несоответствие объясняется тем, что теоретический коэффициент концентрации A0 отражает характер распределения напряжений в идеально упругом материале. В реальных материалах из-за пластической деформации микроплощадки места концентрации напряжений несколько перераспределяются и сглаживаются. Учитывая это, теоретический коэффициент концентрации при рассмотрении усталостных задач, а также предел прочности гладких образцов без концентрации напряжений и имеющих одинаковые
абсолютные размеры поперечного сечения, дополнительно выражаются следующим образом: Где o_1 и t_1-пределы прочности для гладких образцов, а o_1k и t_1k-пределы прочности для образцов с концентрацией напряжений. При этом учитывается, что все справедливо из-за касательного напряжения, и только индекс » о «коэффициента должен быть заменен на «Т». 601 эффективный коэффициент концентрации напряжений имеет значение меньшее, чем коэффициент концентрации a^, теоретически определенный в предположении об «упругом» распределении напряжений. Количественную оценку этой разницы в коэффициенте ка можно получить и путем введения в концентрацию напряжений так называемого коэффициента чувствительности материала: * Знать коэффициент чувствительности qG. Таким образом, ссылка имеет соответствующий график(рис. 563), можно получить значение
- эффективного коэффициента концентрации: = = 1Qg(P’G-!) •(21.7) Это очевидно в материалах, которые не чувствительны к концентрации напряжений, т. е. maximum= = 0, Lo=1. Если Qo=1, то ko=т. е. материал обладает полной чувствительностью к концентрации напряжений. Как видно из графика (рис. Чувствительность металла к концентрации напряжений зависит в первую очередь от его характеристик. В то же время, чем выше прочность стали, тем выше чувствительность к концентрации напряжений. Поэтому использование высокопрочной стали с переменным давлением не всегда целесообразно. Чувствительность металла к концентрации напряжений крупнозернистой стали меньше, чем у мелкозернистой стали. Например, металлы и сплавы с неоднородной структурой, такие как серый чугун, подвержены концентрации напряжений из-за того, что структурная неоднородность является внутренней.- 602 уменьшает предел выносливости ровного образца, даже под концентрациями напряжений, поэтому внешний концентратор уже уменьшает предел выносливости немного. Коэффициент
чувствительности к концентрации напряжений зависит не только от механических свойств, как показывают эксперименты, но и от конструктивной формы самой детали и распределения напряжений в ней. Теоретически эта задача до сих пор не решена, поэтому влияние концентрации напряжений на расчет деталей машин, подвергающихся переменным напряжениям в асимметричном цикле, недостаточно изучено экспериментальными данными. Экспериментальные данные, полученные в лабораторных образцах малого поперечного сечения, показывают, что отношение предельных амплитуд образца к гладкому образцу при той же концентрации, что и среднее напряжение переменного тока, не зависит от амплитуды цикла. Это обстоятельство используется для расчета механической части на долговечность несимметричного цикла.
Оценка влияния концентрации напряжений на изгиб при кручении обычно Людмила Фирмаль
производится на основе соответствующих усталостных испытаний на станке, для момента кручения и изгиба му рис в различных соотношениях. 564 экспериментальные результаты по фазовому изменению нормальных и тангенциальных напряжений в симметричном цикле (a_ik, T-iK-к симметричным циклам для образцов только с концентрацией при кручении; предел тока для концентрации образцов при изгибе HAC и одновременном действии кручения). Рассматривая рисунок. 564, мы видим, что большая часть экспериментальных данных полностью соответствует эллиптической зависимости. (21.8) То есть такая же зависимость, как и при отсутствии концентрации напряжений. Влияние размера (масштабного фактора). Эффективность концентрации напряжений зависит от абсолютных размеров сечения детали, т. е. увеличения размеров детали при сохранении геометрического подобия,
а дальнейший рост эффективного коэффициента плотности практически прекращается, когда диаметр образца превышает 30-40мм, так как результаты экспериментов показывают, что значение эффективного коэффициента концентрации напряжений увеличивается. При достижении определенного размера поперечного сечения можно предположить, что эффективный коэффициент не отличается от теоретического, то есть ka=AA. >Для легированных сталей с пределом прочности на растяжение 120кгф/ММА, равенство этих коэффициентов на среднем уровне концентричности- Напряжение тока AA 603rations=2 4-3 уже достигано в d-40 4-50 mm. Что касается углеродистой стали, то она имеет предельный размер, после которого ко-АА становится значительно больше. Абсолютный размер сечения детали наряду с влиянием на эффективность
концентрации напряжений оказывает существенное влияние на предел выносливости образца без концентрации напряжений. Предел прочности поперечного сечения абсолютного размера уменьшается с ростом. На отношение предела выносливости детали размера d к пределу выносливости лабораторных образцов аналогичной конструкции с малыми габаритами (d0-7 4-10мм)оказывают влияние абсолютные размеры сечения.: (21.9)) Коэффициент влияния абсолютного размера сечения и определяет концентрацию давления в образце. В этом деле (21.10)) Кроме того, размер детали d и меньший размер d. образец o должен быть геометрически подобен. При расчете элементов машин, даже при наличии напряжений-амулетов, учитывающих влияние размеров деталей, существует специальный график, как показано на рисунке, без них. 565, полученные в результате эксперимента(здесь шкала
d является логарифмической). Где кривая 1 соответствует участку углеродистой стали без источника концентрации напряжений, а кривая 2 соответствует участку легированной стали (AB— 100 4- 120 кгс / мм2) при отсутствии концентрации напряжений и углеродистой стали при наличии умеренной концентрации напряжений. Кривая 3 соответствует компоненту легированной стали с концентрацией напряжений, а кривая 4 соответствует любой стали с очень высокой концентрацией напряжений режущего типа. Увеличение диаметра до 150-200 мм, как показал эксперимент, снижает предел прочности образца при ротационном изгибе(см. Рисунок). 556) может достигать 30-45%. Экспериментальные данные показали незначительное влияние абсолютных размеров на прочность при равномерном напряженно-растягивающем сжатии. Кручение и изгиб нижнего предела прочности при увеличении размеров детали проявляется
в большей степени. Это должно быть связано с влиянием градиента напряжения. Снижение предела выносливости с увеличением абсолютного размера сечения детали также можно объяснить влиянием следующих факторов: 1)при уменьшении механической прочности материала увеличивается диаметр заготовки, даже если она подвергнута соответствующей термической обработке;2) после обработки изменяются свойства поверхностного слоя, эти свойства снижаются. Особенно сильно снижение прочности при увеличении размеров- Yu20 30AO60yuo (1 мм «Х2^ ^ Рис £65 фиг. Пятьсот шестьдесят шесть Следует учитывать пропорционально количеству опасных дефектов в узле наиболее напряженного слоя металла, например, неровного металла, например серого чугуна, с увеличением размеров от 5 до 10 мм до 50 мм, уменьшение СГВ и
ои относительно него достигает 60-70%, исходя из вероятности усталостного разрушения. 566 приведены диаграммы напряжений изгиба для образцов различных диаметров без концентрации напряжений. Напряжение в затененной зоне определяется либо растягивающим сжатием, либо изгибом в достаточно крупногабаритном образце из диаграммы распределения напряжений предела прочности o_1p (равномерное напряжение). По мере увеличения диаметра образца 566 мы можем видеть, что объем опасного слоя напряжений увеличивается, вероятность
усталостного разрушения увеличивается, а предел выносливости уменьшается. При увеличении диаметра образца до 7-150мм снижение предела выносливости углеродистой стали достигает 45%. Статистическая теория усталости, как и другие закономерности и свойства усталости, объясняет зависимость пределов выносливости от размеров сечения. Эти теории охватывают проблему изменения эффективного коэффициента концентрации, который зависит от значений градиентов напряжений и абсолютных размеров. По сравнению с тем, что должно вытекать из гипотезы, объясняющей ослабление эффективности концентрации
напряжений Ка зависимости распределения напряжений в упругой области 605, а также коэффициенты, многие факторы (размер, свойства материала и др.) выражаются различными авторами, однако вычислить значение этих коэффициентов для различных случаев практики, рассчитанных на основе основных свойств металлов, не представляется возможным. Поэтому необходимо дополнить детали машины, используемые для расчета экспериментальных данных. Усталостная прочность материала оценивается пределом выносливости (o ’ — Ojo определяется малым диаметром гладкого испытательного образца), для того чтобы определить прочность детали при переменном напряжении, необходимо знать предел выносливости. ( Стадия циклического
нагружения, более подчеркнута, чем внутренняя «(особенно — / ti, это случай изгиба и j l/Vzrkrrautxijr LXR^izrw’.м TLGP номер>Р > nrxv ^2′, d=30+50 мм Рис пятьсот шестьдесят девять P>мне. Четыре 6е=120im/МТФ Кроме того, поверхность детали почти всегда имеет дефекты, связанные с качеством обработки, а также коррозия, обусловленная воздействием окружающей среды, обычно начинается с поверхности, а последняя-с поверхности. Влияние состояния обрабатываемой поверхности на долговечность оценивается коэффициентом Р, который равен отношению предела выносливости испытуемого образца при определенной обработке Так что усталостная трещина,
Поверхности до предела выносливости тщательно полируются образцами. Зависимость коэффициента[3] от прочности на растяжение ОЭ для обработки различных типов показана на рисунке. 570, где кривая соответствует 1 полировальному образцу, 2-полировальному, 3-точному точению образца;4-с грубым точением;5-с наличием окалины. Как видим, предел выносливости стальных образцов при черновом точении снижается на 40%, а при наличии чешуи на поверхности уменьшается на 70%. Во многих случаях неблагоприятное воздействие микро-неровностей
на поверхность смягчается пластической деформацией, вызванной на поверхности- 607 в тонком слое путем обработки и выдвижения на определенную глубину, в частности, величину подачи, в зависимости от условий резания. При грубых оборотах она может достигать более 1 мм, а при шлифовке и полировке измеряется в миллиметрах и микронах. Пластическая деформация поверхностного слоя может увеличить предел выносливости на 10-20%. Предел прочности сильно зависит от коррозии. Этот эффект отличается, если металл не подвергается коррозии во время испытания и если металл подвергается коррозии во время испытания
до испытания на усталость. В обоих этих случаях, особенно во втором, коррозия вызывает резкое снижение предела выносливости (до 70-80%). В этом случае снижение предела выносливости при наличии коррозии более выражено, прочность металла на растяжение увеличивается, а последний более подвержен коррозии. Влияние коррозии на расчет учитывается коэффициентом kk, который представляет собой отношение предела коррозии oLj к пределу прочности o_i полированного образца, т. е. 0K=~. Влияние коррозии при испытании на предел выносливости стальных образцов при испытании на вращательный изгиб показано на рисунке. 571, где кривая 1 характеризует эффект коррозии пресной
в присутствии концентрации напряжений;2-в отсутствие концентрации в присутствии концентрации или в пресной воде в морской воде; 3-в присутствии концентрированной воды. Причиной такого резкого падения долговечности от коррозии является коррозионное повреждение поверхности, которое вызывает не только снижение стойкости к растрескиванию, но и значительную концентрацию напряжений. Можно уменьшить влияние состояния поверхности на усталость соответствующими технологическими методами обработки, что приводит к упрочнению поверхностного слоя. Эти методы приняты путем дуть ролик свернутый в поверхностный слой naklep. Химико-термические методы-азотирование, цементирование, цианирование; термическое упрочнение поверхности током высокой частоты или газовым
пламенем. Эти способы обработки усложняют образование усталостных трещин, а следовательно, увеличение прочности поверхностного слоя влияет на увеличение предела прочности, возникает проблема, что в нем возникают значительные сжимающие остаточные напряжения. При наличии концентрации напряжений, помимо глубины слоя и его абсолютного размера, уровни концентрации напряжений и градиенты напряжений поверхности оказывают существенное влияние на эффект упрочнения. Эффект отверждения усиливался с увеличением концентрации. Эффект
паузы. На предел выносливости влияют паузы (перерывы во время нагрузки). При этом в одних случаях эффект паузы незначителен, а в других, благодаря паузе, цикл разрушения увеличивается на 15-20%. Увеличение числа циклов больше, паузы чаще, они удлиняются (последний фактор слабее). Воздействие перегрузки. Если эффект перегрузки, то есть, нагрузка превышает предел выносливости, то этот эффект зависит от характера перегрузки. При небольшой перегрузке, пока определенное число циклов не поднимется до определенного числа, после определенного числа циклов, при большой перегрузке, выносливость повышается. Влияние обучения.
Если напряжение приложено под пределом прочности образца теста, то сопротивление усталости может значительно быть улучшено постепенно увеличивать переменную нагрузку. Это явление называется материальной подготовкой и широко используется в технике. Закаливание можно получить при относительно короткой тренировке (около 50 000 циклов), но со значительной перегрузкой. Эксперименты показали, что долговечность материала выше, чем если сначала действует большая перегрузка, если она мала, то действует большая перегрузка. Влияние температуры. По мере
повышения температуры предел прочности обычно уменьшается, а по мере его уменьшения он увеличивается как в образце с гладким образцом, так и в концентрате. Для стали с температурой выше 300°c предел усталости снижается примерно на 15% при каждом повышении температуры на 100 ° C. Однако большое количество сталей с повышением температуры от 20 ° С до предела усталости 300 ° С увеличивается. Однако это увеличение, по-видимому, связано с физико-химическими процессами, происходящими при одновременном воздействии нагрева и переменного напряжения.
Смотрите также:
Явление усталости материалов | Расчет на прочность при повторно-переменных напряжениях |
Методы определения предела выносливости. диаграммы усталости | Понятие о малоцикловой усталости материалов |