Оглавление:
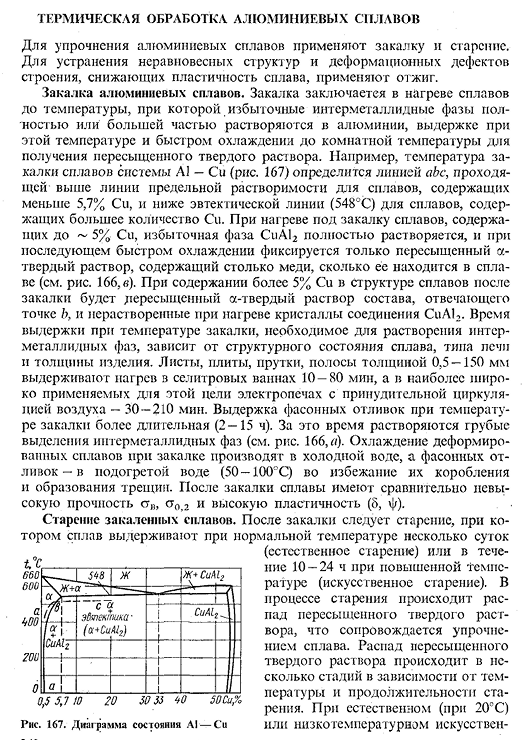
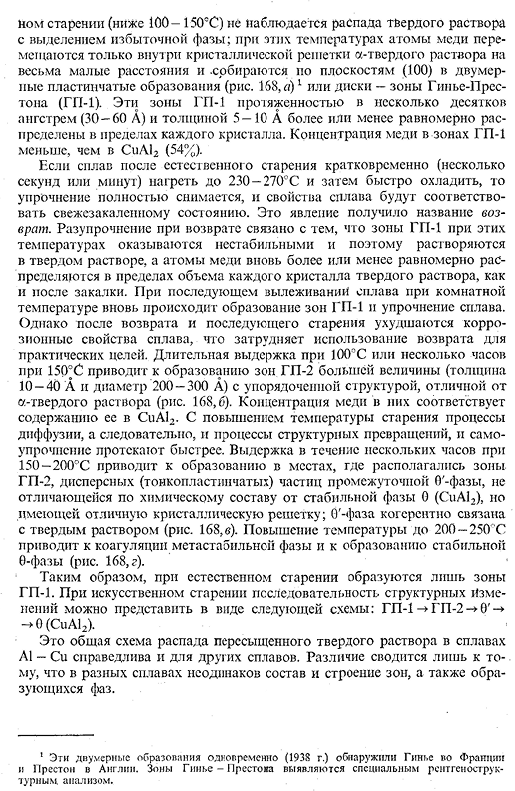
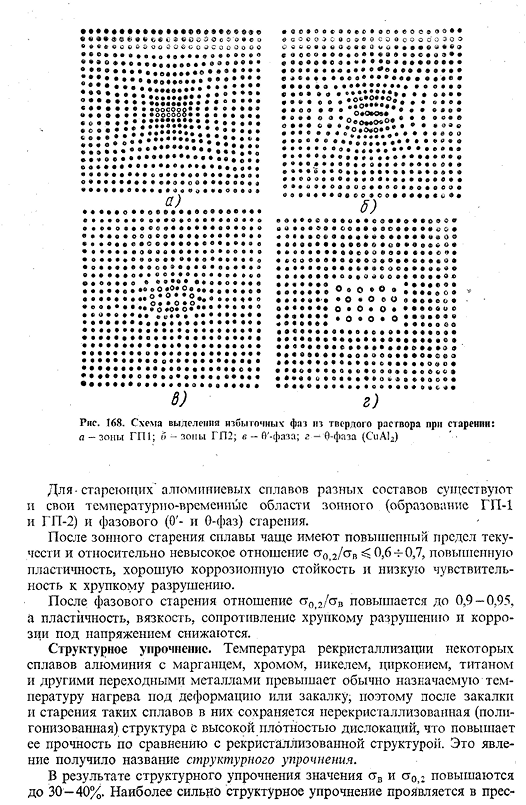
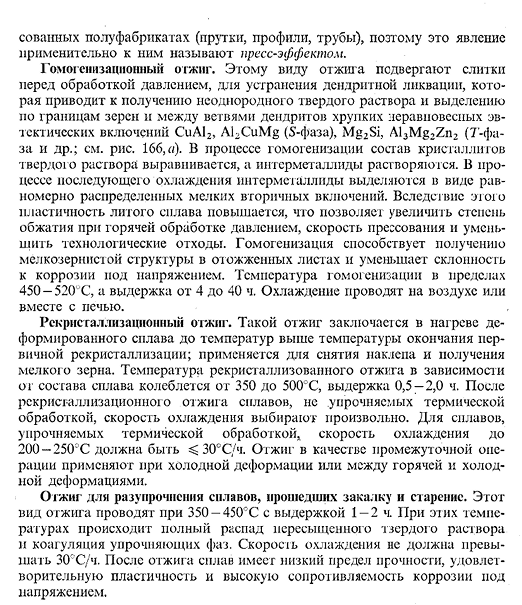

Термическая обработка алюминиевых сплавов
- Термическая обработка алюминиевого сплава Для отверждения алюминиевого сплава используются закалка и старение. Отжиг применяется для снижения пластичности сплавов, устранения неравновесной структуры и структурных деформационных дефектов. Упрочнение алюминиевых сплавов.
Закалка включает нагрев сплава до температуры, при которой избыток интерметаллической фазы полностью или почти растворяется в алюминии, выдерживание его при этой температуре и быстрое охлаждение до комнатной температуры с получением пересыщенного твердого раствора. Например, температура закалки сплава на основе A1-Cu (рис.167) определяется линией abc и превышает верхний предел растворимости сплава, содержащего Cu, менее чем на 5,7% и
опускается ниже эвтектической линии (548°C) сплава, содержащего много Cu. Людмила Фирмаль
Закалка закаленного сплава, содержащего до 5% Cu, вызывает полное растворение избыточной фазы CuA12 с последующим быстрым охлаждением, фиксируется только пересыщенный α-твердый раствор, и в сплав входит медь (см. Рисунок, 166 с).При содержании более 5% Cu в структуре сплава после закалки происходит пересыщение твердого раствора с соответствующим составом в точке B. кристаллы соединения CuAl2 чрезмерно растворяются при нагревании. Время выдержки при температуре закалки, необходимой для растворения фазы интерметаллического соединения, зависит от структурного состояния сплава, типа печи и толщины изделия. Листы, плиты, прутки, полосы толщиной 0,5-150 мм выдерживают соляные ванны в течение 10-80 мин, а наиболее широко применяются электропечи с принудительной циркуляцией воздуха-нагрев в течение 30-210 мин.
Выдержка формованного изделия при температуре отверждения более длительная (2-15 часов).За это время крупный осадок интерметаллической фазы растворяется (см. рис. 166, а).Охлаждение деформированных сплавов при быстром охлаждении происходит в холодной воде, а отливки, сформированные в горячей воде (50-100°С), предотвращают коробление и растрескивание. После закалки сплав проявляет относительно низкую сверхпроводящую прочность, StO2 и высокую пластичность(6, f).
- Дисперсионно твердеющий сплав. После закалки проводят старение, и сплав выдерживают в течение нескольких дней при комнатной температуре (естественное старение) или при высоких температурах в течение 10-24 часов (искусственное старение).В процессе старения происходит разложение пересыщенного твердого раствора, которое сопровождается упрочнением сплава. Распада пересыщенных твердых растворов происходит в несколько этапов, в зависимости от температуры и срока созревания. Естественная (20°C) или низкая температура искусственная Триста сорок Рисунок 167.Фазовая диаграмма разложение AI-Siyom при старении (ниже 100-150°С) твердого раствора не наблюдается с выделением избытка phase.
At при этих температурах атомы меди перемещаются в кристаллической решетке твердого раствора на очень короткое расстояние, и в плоскости (100) они собираются в 2-мерное пластинчатое образование(рис.168, а)1 или диск—гиниплеровскую зону(ГП-1).При длине в несколько десятков Ангстрем (30-60 А) и толщине в 5-10 а эти зоны ГП-1 распределены почти поровну внутри каждого кристалла. Концентрация меди в зоне GP-1 ниже, чем CuA12(54%). 1 в то же время (1938) эти 2-мерные структуры были открыты Гинье во Франции и Престоном в Англии. Зона Гвинея-Престо идентифицируется с помощью специальной рентгеновской дифракции. Анализ. Если сплав после короткого периода естественного старения (несколько секунд или минут) нагревают до 230-270°С, а затем быстро охлаждают, то упрочнение полностью исключается,
и свойства сплава соответствуют состоянию только что затвердевшего. Людмила Фирмаль
Это явление называется возвращением. Размягчение при возврате связано с тем, что при этих температурах зона ГП-1 становится неустойчивой и растворяется в твердом растворе, а атомы меди распределяются почти поровну, как и после закалки в объеме каждого кристалла твердого раствора. Затем, когда сплав выдерживается при комнатной температуре, снова образуется зона GP-1 и сплав затвердевает. Однако после возврата и последующего старения коррозионные свойства сплава снижаются, что затрудняет использование возврата в практических целях. Длительная выдержка при 100°С или часах при 150°С приводит к образованию крупных зон ГП-2 (толщина 10-40 а и диаметр 200-300 а) с упорядоченной структурой, отличной от структуры α-твердых растворов (рис.168, 6).Концентрация меди в них соответствует содержанию CuA12.
As температура старения повышается, диффузионный процесс, а следовательно, и процесс структурных изменений, и самотвердеющие, протекают быстрее. При воздействии 150-200°С в течение нескольких часов, где расположена зона ГП-2, образуется промежуточная дисперсия o ’фазы (toinplate) частицы, химический состав которой отличается от стабильной фазы 0 (CuA12), но отличная кристаллическая решетка; o’ фаза последовательно связана с твердым ростом Вор (рис. 168, в).При повышении температуры до 200-250 ° C метастабильная фаза затвердевает и образуется стабильная фаза 0(рис. 168, г). Так, с естественным вызреванием, только зона GP-1 formed. In в случае искусственного старения последовательность структурных изменений определяется ГП-1 — » ГП-2-> 0 ’-«-> 0(CuA12) можно представить в виде схемы. Эта общая схема разложения пересыщенных твердых растворов сплавов A1-Cu справедлива и для других сплавов. Разница сводится к тому, что состав и структура зон, а также образующихся фаз не одинаковы в разных сплавах.
Да. О Да. О Да. Да. е. О, да. Рисунок 168.Схема выделения избыточной фазы из твердого раствора при старении: а-зона GP1; б-зона GP2. в-Б фазы; Р ^ 0 фазы(CuA12) При старении алюминиевых сплавов различного состава также наблюдается температурно-временная область зоны (образование ГП-1 и ГП-2) и старение фазы (фаза О ’и 0). После вызревания зоны, прочность выхода сплава высока, коэффициент st0> 2 / stv <0.64-0.7 относительно низок, дуктильность улучшена, коррозионная устойчивость улучшена, и чувствительность к хрупкой трещиноватости понижена. После вызревания участка, коэффициент cr0-2 / stv поднимает до 0.9-0.95, но уменьшает дуктильность, твердость, сопротивление к хрупкой трещиноватости, и корозию под напряжением.
Структурное упрочнение. Температура рекристаллизации некоторых сплавов алюминия, включая марганец, хром, никель, цирконий, титан и другие переходные металлы, превышает обычно предписанную температуру нагрева для деформации или упрочнения. Поэтому после закалки и старения таких сплавов они сохраняют свою рекристаллизационную (полигональную) структуру при высоких плотностях дислокаций, а их прочность возрастает по сравнению с рекристаллизованной структурой. Это явление называется структурным упрочнением. В результате структурного упрочнения значения SHW и SG 0,2 увеличиваются до 30-40%.Структурное упрочнение наиболее сильно проявляется в прессованных полуфабрикатах (прутках, профилях, трубах), поэтому это явление называют пресс-эффектом.
Гомогенизационный отжиг. Слитки подвергают этому виду отжига перед обработкой давлением, чтобы исключить сегрегацию дендрита и привести к разделению гетерогенных твердых растворов и хрупких неравновесных эвтектических включений CuA12, AbCuMg (S Фаза), Mg2Si, Al3Mg2Zn2 (7 фаза); см. рисунок, а). в процессе гомогенизации состав микрокристаллов в твердых растворах выравнивается и интерметаллические соединения восстанавливаются. dissolved. In в процессе последующего охлаждения интерметаллические соединения выделяются в виде мелких вторичных включений, равномерно distributed. As в результате повышается пластичность литого сплава, что приводит к более высокой степени сжатия и скорости прессования при горячей обработке и уменьшению отходов в процессе.
Гомогенизация способствует получению мелкозернистой структуры в отожженной пластине и снижает склонность к коррозии под напряжением. Температура гомогенизации колеблется от 450 до 520°C, время выдержки составляет от 4 до 40 часов, охлаждение производится на воздухе или с помощью печи. Рекристаллизационный отжиг. Такой отжиг заключается в нагреве деформированного сплава до температуры, превышающей температуру в конце первичного recrystallization. It используется для удаления затвердевших и получения мелких частиц. Температура Рекристаллизационный отжиг в диапазоне 350-500 С, в зависимости от состава сплава, время выдержки составляет 0,5-2,0 часа, после рекристаллизационного отжига сплав не затвердевает при термообработке, скорость охлаждения выбирается произвольно. Для сплавов, закаленных термической обработкой, скорость охлаждения до 200-250C должна составлять 30°C / ч.
отжиг-используется между низкотемпературной деформацией или высокотемпературной деформацией и низкотемпературной деформацией, в качестве промежуточной операции. Отпуск для размягчения закаленных и состаренных сплавов. Этот тип отжига выполняется при 350-450°С с выдержкой 1-2 hours. At при этих температурах пересыщенный твердый раствор полностью разлагается и затвердевшая фаза затвердевает. Скорость охлаждения не должна превышать 30°C / ч. после отжига сплав имеет низкую прочность на растяжение, достаточную пластичность и высокую устойчивость к коррозии под напряжением.
Смотрите также:
Материаловедение — решение задач с примерами
Деформируемые алюминиевые сплавы, упрочняемые термической обработкой | Сплавы на основе титана |
Деформируемые алюминиевые сплавы, не упрочняемые термической обработкой | Алюминий и его сплавы |