Оглавление:
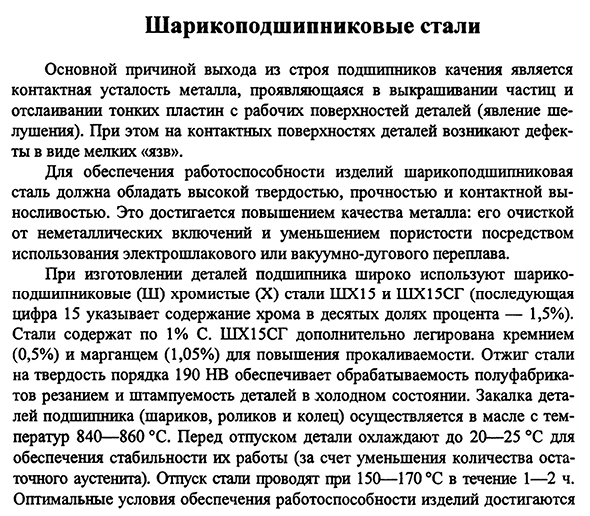


Шарикоподшипниковые стали
- Шарикоподшипниковая сталь Основной причиной выхода из строя подшипника качения является контактная усталость металла, которая проявляется в окрашивании частиц и отслаивании (явление отслаивания) ламелей от рабочей поверхности детали.
При этом на контактной поверхности детали появляется дефект в виде небольшой»язвочки».
Обеспечить выполнение высокопрочного, твердости, контакта стали шарового подшипника продукта. Людмила Фирмаль
Это достигается за счет улучшения качества металла: очистки его от неметаллических включений оболочки и уменьшения пор с помощью электрошлакового или вакуумно-дугового переплава.
Широко используются при изготовлении подшипниковых деталей шарикоподшипниковые (Ш) хромированные (х) стали ШХ15 и ШХ15СГ (на последующем рисунке 15 показано содержание хрома на уровне 1,5%%).
- Сталь составляет 1% C. SHX15SG дополнительно легируется кремнием (0,5%) и марганцем (1,05%) для повышения прокаливаемости. Отжиг стали до твердости около 190НВ обеспечивает обрабатываемость полуфабрикатов резанием и штамповкой деталей в холодном состоянии. Закалку несущих деталей (шариков, роликов и колец) проводят в масле при температуре 840-860 ° С.
отпуск стали проводят при температуре 150-170 ° с в течение 1-2 часов. Достигаются оптимальные условия для обеспечения работоспособности изделия При этом шарик имеет несколько более высокую твердость (62-66HRC)
по сравнению с роликом и кольцом 166 (для стали 61-65HRC WX15). Людмила Фирмаль
Компоненты подшипников качения, испытывающие высокие динамические нагрузки, изготавливаются из стали 20Х2Х4А и 18ХГТ с последующей цементацией и термообработкой. Для компонентов подшипников, работающих в азотной кислоте и других агрессивных средах, используется сталь, содержащая 95×18 0,95% C и 18% SG (см. табл.7.1, 7.3).
Смотрите также:
Износостойкая высокомарганцевая аустенитная сталь | Высокопрочные стали |
Коррозионностойкие (нержавеющие) стали и сплавы | Пружинные стали общего назначения |