Оглавление:
Ременные передачи
Передачи фрикционного сцепления гибких звеньев (ремней) со шкивами, применяемые в машиностроении, называют ременными.
Классификация ременных передач. По типу ремней передачи делят на плоскоременные (рис. 4.50 а, б), клиноременные (рис. 4.50, в) и круглоременные (рис. 4.50, г, д), В последнее время получают распространение зубчато-ременные передачи. В зависимости от расположения валов передачи бывают с параллельными, пересекающимися и перекрещивающимися осями валов. Передача с параллельными валами, показанная на рис. 4.50, называется открытой. Передачи других типов применяют значительно реже.
По способам натяжения ремня имеются передачи, в которых натяжение создается путем предварительного упругого растяжения ремня (рис. 4.50), с помощью натяжного ролика (рис. 4.51, а), весом груза (рис. 4.51, б) или весом электродвигателя (рис. 4.51, в). В зависимости от линейных скоростей v ремня передачи делят на обыкновенные ( < 30 м/с), скоростные (
<60 м/с) и сверхскоростные (
< 100 м/с).
Области применения. Ременные передачи обычно применяют в качестве понижающих на быстроходных ступенях приводов при мощностях < 50 кВт, линейных скоростях ремня
= 5-15 м/с
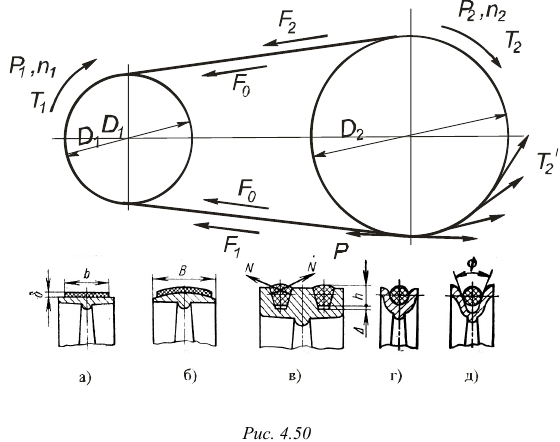
и передаточных отношениях 4. Предельные значения передаточных отношений: для обыкновенных плоскоременных передач
= 5; для плоскоременных с натяжным роликом и клиноременных передач
= 10. Чаще применяют клиноременные передачи.
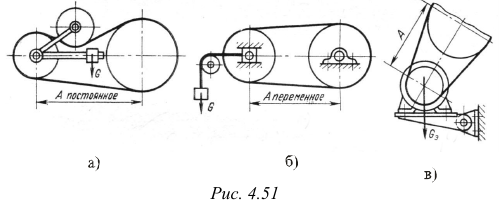
Однако появление плоских ремней из новых синтетических материалов, плоских зубчатых ремней, также саморегулируемых приводов с автоматическим натяжением ремней создает большие перспективы для широкого использования плоскоременных передач.
Типы приводных ремней. Приводные ремни должны иметь:
- малую остаточную вытяжку;
- высокую статическую и усталостную прочность при работе с большими скоростями и на шкивах малого диаметра;
- высокий коэффициент трения;
- стойкость в отношении воздействия щелочей, кислот, минеральных масел.
Для обыкновенных плоскоременных передач применяют стандартные кожаные, прорезиненные, хлопчатобумажные и шерстяные плоские ремни. Перечисленным требованиям в большей степени удовлетворяют кожаные ремни, однако они дефицитны и их обычно заменяют прорезиненными или хлопчатобумажными. Шерстяные ремни преимущественно используют в приводах, работающих с большими перегрузками. Большое влияние на качество работы передач и долговечность ремней оказывает способ сшивки их концов. Поэтому в быстроходных передачах применяют специальные бесконечные (не имеющие сшивки) тонкие текстильные ремни.
Весьма перспективны плоские полиамидные ремни. Они могут работать в широком диапазоне скоростей и нагрузок, хорошо воспринимать перегрузки. Их недостатком является пониженное сцепление с металлическими шкивами. Лучшим сцеплением обладают полиамидные ремни с кожаными или прорезиненными обкладками.
Клиновые ремни (рис. 4.52). По стандартам выпускают приводные клиновые ремни общего назначения, для сельскохозяйственных машин и вентиляторные для двигателей автомобилей, тракторов, комбайнов. Поперечные сечения клиновых ремней характеризуются размерами (рис. 4.52, а). В каждом из перечисленных стандартов установлены размеры однотипных ремней нескольких поперечных сечений. Например, в соответствии с ГОСТ 1284 выпускают ремни шести нормальных сечений, которые в порядке возрастания размеров обозначаются буквами
и четыре разновидности узкого сечения
.
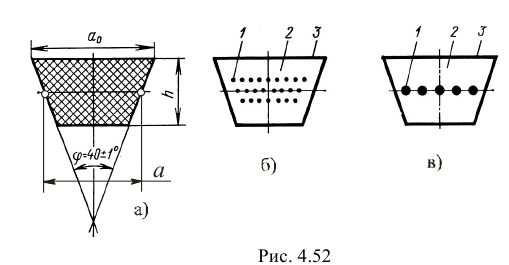
Клиновые ремни состоят из несущего слоя 1 (кордткань, рис. 4.52, б или кордшнур, рис. 4.52, в), резинового заполнителя 2 и защитной обертки 3. Кордшнуровые ремни более прочные и могут работать на шкивах меньшего диаметра. Выпускают также клиновые ремни повышенной гибкости с гофрированной внутренней поверхностью, поликлиновые ремни и др.
Геометрия передачи. Обыкновенные ременные передачи рассчитывают по углу обхвата ремнем меньшего шкива (рис.4.53). Так как отрезок
, то из треугольника
угол
Переводя значение угла в градусы, получим

С уменьшением углов обхвата снижается надежность сцепления ремня со шкивами. Поэтому рекомендуется принимать 150° для плоскоременных и
90° для клиноременных передач.
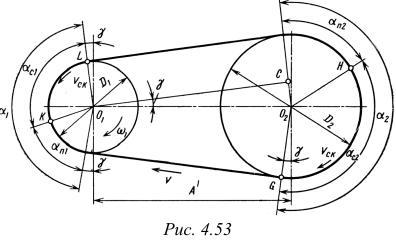
Длина ремня без припуска на сшивку концов равна сумме прямолинейных участков и дуг обхвата:

Принцип действия ременной передачи. В ременных передачах нагрузка передается только за счет удельных сил трения , которые возникают на поверхностях обхвата шкивов натянутым ремнем (см. рис. 4.69). В состоянии покоя ремень (рис. 4.69) испытывает по всей длине одинаковое натяжение
называемое начальным (предварительным) натяжением, и соответственно получает начальное относительное удлинение
.
При холостом ходе натяжение и относительная деформация ремня практически не изменяются. Поэтому можно считать, что при холостом ходе скорость ремня и окружные скорости обоих шкивов равны, т.е.
.
При работе передачи с нагрузкой, для преодоления момента сопротивления возникающего на ведомом шкиве, натяжение ведущей ветви должно увеличиться до
, а ведомой ветви — уменьшается до
.
Из условия равновесия сил, действующих на ведомый шкив, имеем
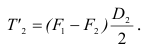
Но крутящий момент

поэтому разность натяжений ведущей и ведомой ветвей можно выразить через окружное усилие
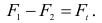
Изменение натяжений ветвей ремня в передаче, работающей с нагрузкой, приводит к соответствующему увеличению относительной деформации ведущей ветви от до
и к уменьшению относительной деформации ведомой ветви от
до
:

Как видно из формулы (4.75) , длина ремня не зависит от нагрузки. Следовательно, изменение относительных деформаций ведущей и ведомой
ветвей равны. Сложив почленно эти равенства и учитывая, что
получим
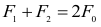
Так как ремень имеет замкнутый контур, то изменение относительных деформаций его обоих ветвей возможно только в том случае, если при работе передачи ремень будет проскальзывать по шкивам. Действительно, как показывают опыты, на некоторой дуге обхвата ведомого шкива (рис. 4.53) ремень постепенно удлиняется. При этом отдельные сечения ремня начинают перемещаться со скоростью, превышающей линейную скорость шкива
. Одновременно с этим, на дуге
обхвата ведущего шкива ремень укорачивается и начинает скользить по ободу в направлении, обратном вращению шкива, т.е. в пределах дуги
линейная скорость ремня оказывается меньше линейной скорости ведущего шкива
. Такое скольжение, обусловленное упругими свойствами материала ремней, называют упругим скольжением и оно неизбежно для ременных передач.
Дуги и
и соответствующие им углы
и
называют дугами и углами скольжения. Таким образом, полные углы обхвата шкивов
и
делятся на углы скольжения
и
и углы покоя
и
т.е.
. На обоих шкивах дуги покоя находятся со стороны набегающей ветви.
В состоянии покоя и при холостом ходе . При работе передач с нагрузкой

По мере увеличения нагрузки углы скольжения возрастают при соответствующем уменьшении углов покоя. В пределе, когда углы скольжения становятся равными углам обхвата , наступает сначала частичное, а затем и полное скольжение ремня по ведущему шкиву, которое называют буксованием.
При буксовании полезная нагрузка не может быть передана. Поэтому работоспособность ременных передач зависит от надежности сцепления ремня со шкивами, которую называют тяговой способностью ремней.
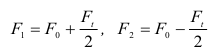
Для определения натяжений ветвей ремня в ременных передачах можно использовать формулу Эйлера
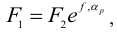
где — расчетный угол обхвата в радианах. Если принять
то формула (23.7) даст отношение предельных значений
и
на границе буксования. При
получим отношение
и
соответствующее рабочему режиму передачи.
При набегании ремня на шкивы на каждый элемент его массы в пределах угла обхвата
действует центробежная сила
. Поэтому ветви ремня испытывают также натяжение
от воздействия центробежных сил:

где — вес ремня длиной в 1 м;
— ускорение свободного падения.
Полные натяжения ведущей и ведомой
ветвей
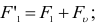
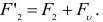
Воздействия центробежных сил особенно сказываются при > 10 м/с, а также зависят от способа натяжения и вида передачи, что учитывают с помощью коэффициента
.
Напряжения в ремнях. Если натяжения и окружное усилие
отнести к площади поперечного сечения ремня, то получим соответствующие напряжения: напряжения от начальных натяжений

полезные напряжения от окружного усилия
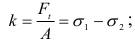
напряжения в ведущей ветви
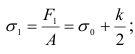
напряжения в ведомой ветви
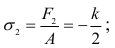
напряжения от центробежных сил
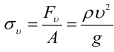
(в последней зависимости — плотность ремня).
Кроме того, на дугах обхвата в ремне возникают напряжения изгиба . Так как модуль упругости
для материала ремней имеет неопределенное значение, то приведенная формула не позволяет найти точную величину напряжений изгиба. Однако она показывает, что
уменьшается с уменьшением толщины
ремня и с увеличением диаметров шкивов. Но так как с увеличением
и
возрастают габариты передач, то следует по возможности применять более тонкие ремни, если даже для сохранения требуемой площади поперечного сечения потребуется некоторое увеличение ширины ремней.
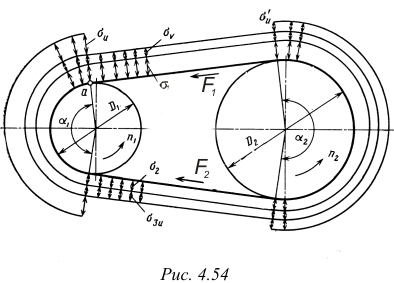
На рис. 4.54 изображена диаграмма распределения напряжений по длине работающего ремня. Так как при
, то максимальные напряжения возникают в точке а набегания ведущей ветви ремня на ведущий шкив:

Так как через точку а последовательно проходят все сечения, то при работе передачи ремни испытывают многократно повторяющиеся переменные и даже знакопеременные напряжения. В силу этого ремни подвержены усталостному разрушению.
Кинематика ременных передач (см. рис. 4.50). При нормальных нагрузках упругое скольжение ремня < 0,02 и в приближенных расчетах его можно не учитывать. Поэтому для ременных передач передаточное отношение обычно вычисляют по формуле

При точных расчетах следует пользоваться формулой
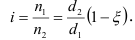
Основными критериями работоспособности ременных передач являются тяговая способность и долговечность ремней. Кроме того, важной характеристикой качества ременной передачи служит КПД.
Следовательно, методы расчета ременных передач должны обеспечивать создание таких передач, которые при достаточно высоких КПД будут обладать требуемой долговечностью и надежным сцеплением ремней со шкивами. В настоящее время основным методом расчета ременных передач является расчет по тяговой способности ремней.
Исходные положения расчета по тяговой способности. Расчет ремней при этом методе сводится к определению площади поперечного сечения ремня из расчета на растяжение [см. формулу (4.84)]. При этом допускаемые напряжения
и ряд параметров ременных передач назначают таким образом, чтобы обеспечить оптимальную тяговую способность и усталостную прочность ремня:

где — площадь поперечного сечения ремня (
и
— соответственно ширина и толщина ремня);
— окружное усилие.
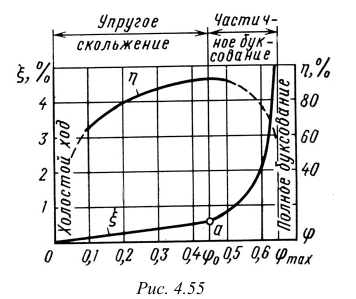
В качестве основной характеристики тяговой способности принят коэффициент тяги, равный отношению окружного усилия
к сумме начальных натяжений обеих ветвей ремня 2
или отношению полезных и начальных напряжений:
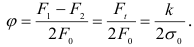
Влияние полезной нагрузки на изменение коэффициента тяги и относительного скольжения
показывают кривые скольжения (рис. 4.74), полученные опытным путем для различных ремней.
При построении кривых скольжения начальное натяжение поддерживалось постоянным , а величина полезной нагрузки менялась. Рост полезной нагрузки вызывает увеличение коэффициента тяги, но сопровождается также увеличением дуг скольжения и относительного скольжения
. До некоторой критической точки а относительное скольжение сохраняет небольшие численные значения
и изменяется прямо пропорционально коэффициенту тяги. При дальнейшем увеличении полезной нагрузки дуги скольжения начинают резко возрастать и может возникнуть неустойчивое сцепление ремня со шкивами. Это выражается в том, что даже незначительное увеличение полезной нагрузки способно вызвать буксование ремня. Поэтому правее точки а нарушается пропорциональность между изменениями относительного скольжения и коэффициента тяги, и кривая скольжения круто поднимается вверх.
На том же графике построена кривая КПД , которая показывает, что наибольшего значения КПД достигает при значениях коэффициентов тяги, приблизительно равных
. В зоне частичного буксования
сильно уменьшается (
= 0 при
= 100%).
Характер кривых скольжения не зависит от материалов и размеров ремней, размеров передач и прочих факторов, влияющих на работоспособность ремней. Поэтому с помощью кривых скольжения устанавливают нормы тяговой способности для различных условий эксплуатации ременных передач. Однако численные значения коэффициента тяги и допускаемых напряжений
, а также усталостная прочность ремней зависят от схемы передачи, условий эксплуатации и других факторов (см. ниже). Из формулы (4.86) по критическому значению коэффициента
тяги можно определить полезные напряжения
:

Для ремней, изготовленных из различных материалов,

На тяговую способность и долговечность ремней оказывают большое влияние начальные напряжения . При малых значениях
снижается тяговая способность ремней. При больших значениях
ремни сильно удлиняются и быстро подвергаются усталостному разрушению. Для плоских стандартных ремней принимают
, а для синтетических ремней
.
Тяговая способность и долговечность ремней в большой степени зависят от отношения диаметра меньшего шкива передач к толщине
ремня. Как установлено опытами, с увеличением
при
= const увеличивается
и уменьшается
, а следовательно, повышается долговечность ремней. Опытным путем получена зависимость
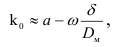
где и
— коэффициенты, зависящие от материала ремня и численных значений
.
Для плоских ремней установлены рекомендуемые и допускаемые отношения . Например, для прорезиненных ремней рекомендуемое отношение
= 40, а допускаемое
= 30.
Для обеспечения достаточной долговечности и тяговой способности ремней фактические отношения должны быть не менее рекомендуемых, а при повышенных требованиях к компактности передач — не менее допускаемых значении, т.е.

Численные значения критического коэффициента тяги и полезных напряжений
зависят также от величины угла обхвата меньшего шкива
, скорости ремня v, характера нагрузки и конструкции передачи. Влияние этих факторов на величину допускаемых полезных напряжений
учитывают с помощью корректирующих коэффициентов, полученных также опытным путем:

где — полезные напряжения с учетом влияния на работоспособность ремня отношения
[формула (4.14)];
— коэффициент, учитывающий влияние угла обхвата,
< 1 при
< 180°,
— коэффициент, учитывающий влияние скорости, его вводят только для передач без автоматического регулирования натяжения ремня (
> 1 при
< 10 м/с;
< 1 при
> 10 м/с);
< 1 — коэффициент режима и динамичности нагрузки;
< 1 — коэффициент, учитывающий способ натяжения ремня и расположение передачи.
Указанные коэффициенты определяют по таблицам и эмпирическим формулам.
Долговечность ремня может быть оценена по числу изгибов за время работы до усталостного разрушения или, упрощенно, по числу пробегов ремня в секунду:

где — скорость ремня, м/с;
— длина ремня, м;
— допускаемое число пробегов ремня в секунду.
На основании опыта для плоскоременных передач установлено: для обыкновенных передач = 5; для передач с натяжным роликом
= 3; для быстроходных передач с текстильными ремнями
= 20 и с полиамидными ремнями
= 50.
Чтобы фактическое число пробегов ремня не превышало допускаемых значений, для обыкновенных плоскоременных передач рекомендуется принимать
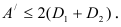
Главной задачей проектного расчета плоскоременных передач является выбор типа ремня и определение размеров его поперечного сечения. Необходимо также найти все геометрические размеры передач, спроектировать шкивы, рассчитать валы и опоры.
Основной целью проверочного расчета является определение допускаемой мощности для передачи, размеры и условия работы которой известны. Необходимо также проверить тяговую способность и долговечность ремня. Не исключаются проверка прочности валов, опор и другие расчеты.
Особенности клиноременных передач. В клиноременных передачах мощность передается одним ремнем или, чаще, комплектом, состоящим из нескольких клиновых ремней. Ремни соединяют с канавками шкивов боковыми поверхностями, а по внутренним поверхностям следует сохранять зазоры (см. рис. 4.50, б). Сцепление клиновых ремней со шкивами определяют с помощью приведенного коэффициента
трения. Если принять угол между боковыми сторонами поперечного сечения ремней
= 40° (см. рис. 4.52, а) то
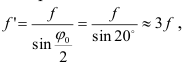
где — коэффициент трения плоских ремней.
Клиноременные передачи, по сравнению с плоскоременными, имеют существенные достоинства. Большое увеличение коэффициента трения обеспечивает высокую надежность сцепления ремней со шкивами. Благодаря этому клиноременные передачи отличаются меньшим относительным скольжением, могут работать с большими нагрузками и передаточными числами при меньших начальных натяжениях ремней, давлениях на валы, углах обхвата и межцентровых расстояниях
.
Вместе с тем эти передачи имеют специфические недостатки. Долговечность клиновых ремней ниже, чем плоских, вследствие большой толщины и значительных боковых давлений . Для равномерного натяжения всех ремней, входящих в комплект, необходимы повышенная точность изготовления ремней и шкивов, а также подбор ремней по длине и ширине сечения
(см. рис. 4.52).
Основные характеристики клиноременных передач:
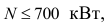

допускаемое число пробегов ремня в 1с
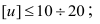

но не более (см. рис. 4.53); число ремней в одном комплекте
, при особо высокой точности шкивов и тщательном подборе ремней
.
Разработано несколько методов расчета клиноременных передач, но общепринятым является расчет по тяговой способности ремней. В приложении к ГОСТ 1284 приведен расчет по мощности, которая может быть передана в заданных условиях работы одним клиновым ремнем:

где — мощность, передаваемая одним ремнем при заданной скорости ремня;
и
— коэффициенты, соответственно учитывающие влияние угла обхвата и характера нагрузки;
— число ремней.
Формулу (4.90) можно применять для проектных и проверочных расчетов. В первом случае определяют число ремней , необходимое для передачи заданной мощности
. Во втором случае из формулы (4.90) находят мощность
, допускаемую для данной передачи, и сравнивают с заданной мощностью
Долговечность клиновых ремней резко снижается с уменьшением диаметров шкивов. Поэтому расчетный диаметр малого шкива нельзя принимать меньше тех значений, которые установлены в приложении 1 ГОСТ 1284.
КПД ременных передач. При работе ременных передач потери энергии вызываются скольжением и деформациями ремня, трением в опорах, а также сопротивлением воздуха движению ремня и шкивов. Установлено, что КПД повышается с увеличением начальных натяжений отношения
и передаточного отношения до тех пор, пока сохраняется прямая пропорциональность между
и
(на участке кривой скольжения
, см. рис. 4.55).
При устойчивом сцеплении ремня со шкивами для рекомендуемых значений и
КПД ременных передач можно принимать равным 0,95 — 0,96.
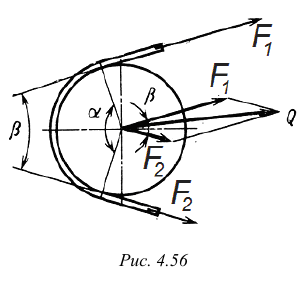
Давления на валы в ременных передачах определяют исходя из следующего: сумма натяжений обеих ветвей ремня в ненагруженной и работающей передаче не изменяется
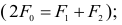
провисание ремня существенно не нагружает валы; натяжения от центробежных сил взаимно уравновешиваются в ремне и даже способствуют разгрузке валов. Поэтому давления на валы (рис. 4.56) можно вычислять по формуле

Шкивы ременных передач. Шкивы бывают: точеными — при малых диаметрах; литыми (из серого чугуна, стального литья, алюминиевых или магниевых сплавов); штампованными; сварными и пластмассовыми. Шкив (см. рис. 4.50) состоит из обода и ступицы, которые соединяют диском (шкив 1) или спицами (шкив 2). Наиболее распространены чугунные литые шкивы. При мм литые шкивы делают с дисками, а при
мм — со спицами. Расчетные значения диаметров шкивов округляют по ГОСТ 17383-73. Рекомендуется диаметр меньшего шкива округлять в большую сторону, а диаметр большего шкива — наоборот. При необходимости выдержать точное значение передаточного отношения диаметры шкивов со стандартом не согласовывают.
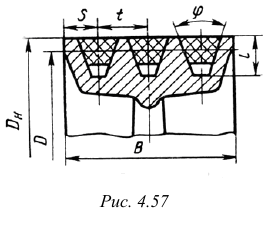
В плоскоременных передачах обод одного шкива (лучше меньшего) делают выпуклым (см. рис. 4.50, б). Эта мера уменьшает опасность сбегания ремня в направлении образующих рабочей поверхности шкива. Выпуклость и ширину шкивов В принимают по стандарту в зависимости от ширины ремня Ь.
Форма обода в поперечном сечении шкивов для клиновых ремней показана на рис. 4.57. Основные размеры шкивов назначают в соответствии с номером сечения ремня по ГОСТ 1284. Порядок и примеры проектирования всех видов ременных передач приведены в пособиях.
Заказать работу по прикладной механике |
Шкивы и натяжные устройства ременных передач
После расчета ременной передачи получают следующие данные: расчетные диаметры малого и большого шкивов, обозначение сечения и число клиновых ремней (или число ребер и ширину поликлинового ремня); модуль, числа зубьев шкивов и ширину зубчатого ремня; толщину и ширину плоского ремня, которые являются исходными при разработке конструкции шкивов и натяжных устройств.
Конструкции шкивов
Шкивы изготовляют литыми из чугуна марки СЧ20 или легких сплавов, сварными из стали, а также из пластмасс. Чугунные литые шкивы вследствие опасности разрыва от действия центробежных сил применяют при окружной скорости до 30 м/с. При более высокой скорости шкивы должны быть стальными. Для снижения инерционных нагрузок, особенно в передачах с большими скоростями, шкивы выполняют из легких сплавов с временным сопротивлением ай > 160 МПа. В серийном производстве применяют также сборные шкивы, составленные из тонкостенных штампованных элементов.
Шкивы состоят из обода, на который надевают ремень, ступицы для установки шкива на вал и диска или спиц, с помощью которых обод и ступица объединены в одно целое.
Внешняя поверхность обода шкива плоскоременной передачи имеет форму кругового цилиндра (рис. 4.58, а). В быстроходных передачах внешнюю поверхность обода одного из двух шкивов следует выполнять сферической (рис. 4.58, 6) или с двумя конусами (рис. 4.58, в).
Таким образом фиксируют ремень на шкивах, предотвращая его сбегание с них при работе передачи. Величину выпуклости принимают (мм):
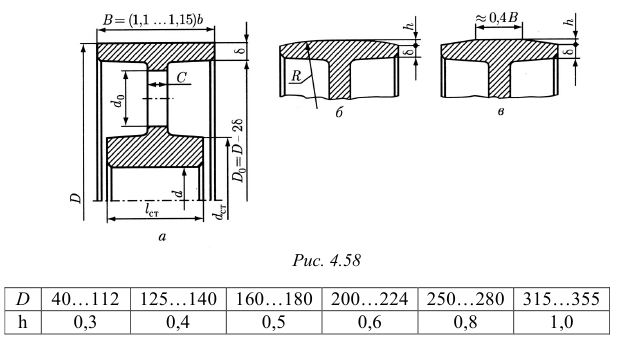
Обод шкива для клиновых ремней нормального (ГОСТ 1284.1-89) и узкого (ТУ 38-105161-84) сечений дан на рис. 4.59, а, для поликлиновых ремней (ТУ 38-105763-84) — на рис. 4.59, 6; размеры (мм) профиля канавок шкивов принимают соответственно по табл. 4.1 и 4.2.
На рис. 4.59 — расчетный диаметр шкива (диаметр окружности по нейтральной линии ремня). Значения расчетного диаметра (мм) принимают из ряда: 50, 56, 63, 71, 80, 90, 100, 112, 125, 140, 160, 180, 200, 224, 250, 280, 315, 355, 400, 450, 475, 500.
Внешний диаметр шкива для передачи:
Клиновыми ремнями

Поликлиновым ремнем

Ширина шкива

где -число канавок на шкиве; значения
(мм) приведены в таблице 4.8 и 4.9.
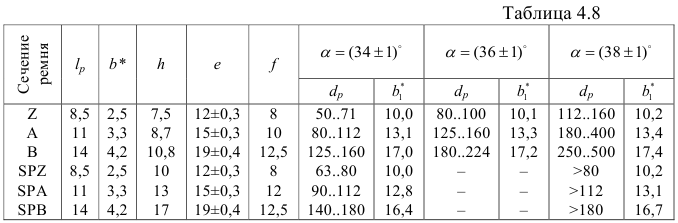
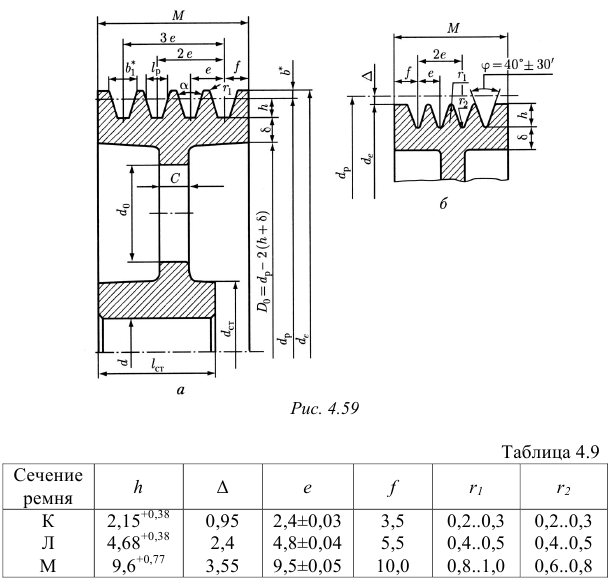
При изгибе ремня на шкивах угол его клина уменьшается. Поэтому угол а клина канавки следует назначать по таблице 4.11.1 в зависимости от диаметра .


Толщина обода чугунных шкивов передач:
Плоскоременных

Клиноременных

Поликлиновым ремнем

Толщина обода стальных шкивов

Конструкция зубчатого ремня и конструктивных элементов (ОСТ 38-05114-76) показана на рис. 4.60, а обода шкива — на рис. 4.60,6 . Некоторые размеры (мм) зубчатого ремня и конструктивных элементов обода шкива приведены в таблице 4.10.
Диаметр делительной окружности , где
— число зубьев шкива.
Диаметр вершин зубьев , где
— поправка, учитывающая нагрузку и податливость каркаса, мм; знак «+» для ведущего шкива, знак «-» — для ведомого.
Значение вычисляют по формуле

где — ширина ремня, мм;
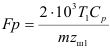
расчетная сила, передаваемая ремнем, Н.
Здесь — вращающий момент на малом шкиве, Н • м ;
— модуль, мм;
— число зубьев малого шкива;
= 1,3…2,2 — коэффициент динамичности и режима работы.
Податливость витков металлотроса каркаса ремня принимают в зависимости от модуля
:

Ширину ремня выбирают из следующего ряда: 12,5; 16; 20; 25; 32; 40; 50; 63; 80; 100; 125; 160; 200.
Диаметр впадин шкива
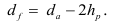
Толщина обода

Зубчатые ремни изготовляют с числом зубьев : 40, 42, 45, 48, 50, 53, 56, 60, 63, 67, 71, 75, 80, 85, 90, 100, 105, 112, 115, 125, 130, 140, 150, 160, 170, 180, 190, 200, 210, 220, 235, 250.
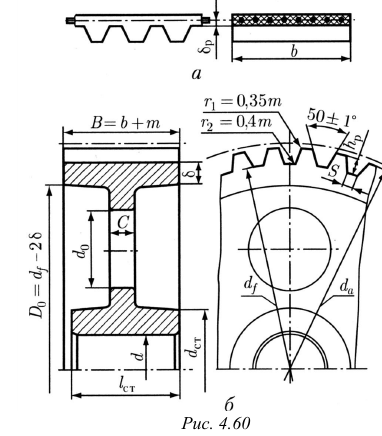
Диаметр ступицы шкивов для любого типа передачи (см. рис. 4.58-4.60): чугунных

стальных

Длина ступицы ориентировочно

Окончательно длину ступицы принимают с учетом результатов расчета шпоночного или шлицевого соединения.
Толщина дисков шкивов для любого типа передачи
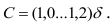
Вычисленные размеры

округляют в ближайшую сторону до значений из ряда стандартных чисел.
Для снижения массы шкивов и удобства транспортирования в дисках иногда выполняют 4…6 отверстий возможно большего диаметра.
В шкивах с диаметром > 200 мм диск следует конструировать в виде конуса (рис. 4.61), что способствует лучшему отводу газов при заливке формы металлом. У медленно вращающихся шкивов обрабатывают только рабочую поверхность и торцы обода, а также отверстие и торцы ступицы. Необрабатываемые нерабочие поверхности для удобства удаления модели шкива из формы выполняют на конус.
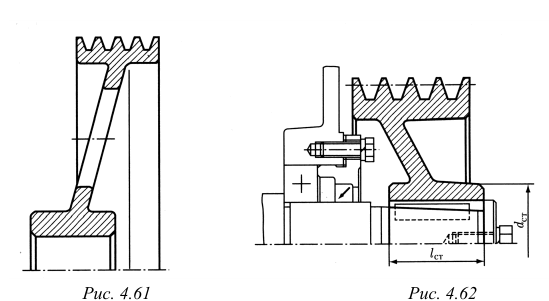
Быстровращающиеся шкивы для лучшей балансировки обрабатывают кругом. В этом случае внутреннюю поверхность обода и наружную поверхность ступицы выполняют цилиндрическими.
Балансируют шкивы путем сверления отверстий на торцах обода.
Так как для удобства надевания и замены ремней шкивы обычно размещают консольно, то их удобно устанавливать на конусные концы валов.
Обод шкива, установленного на консольном участке вала, для уменьшения изгибающего момента следует располагать как можно ближе к опоре (рис. 4.62).
Когда изгибающие моменты от натяжения ремня приводят к нежелательным деформациям вала, шкивы конструируют так, чтобы сила натяжения ремней не передавалась на вал. Для этого их располагают на собственных подшипниках, установленных на специальной крышке-стакане (рис. 4.63).
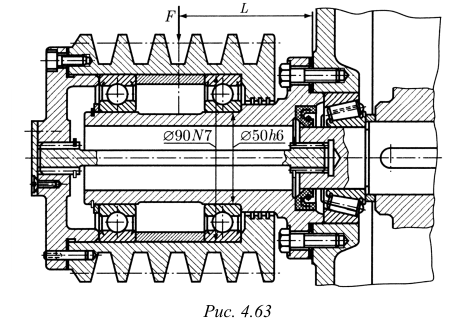
В таких конструкциях целесообразно применять шариковые радиальные подшипники закрытого типа с двумя уплотнениями (тип 180000, ГОСТ 8882-75), смазочный материал в которые заложен при изготовлении.
Для компенсации возможной несоосности осей вращения шкива и входного вала редуктора применен длинный торсионный валик, передающий вращающий момент шлицевыми соединениями (рис. 4.63)
Натяжные устройства
Для компенсации вытяжки ремней в процессе их эксплуатации, компенсации отклонений длины бесконечных плоских, клиновых, поликлиновых и зубчатых ремней, а также для легкости надевания новых ремней должно быть предусмотрено регулирование .межосевого расстояния ременной передачи. Натяжное устройство должно обеспечивать изменение межосевого расстояния в пределах от 0,97а до 1,06а, где а — номинальное значение межосевого расстояния. Наиболее распространены следующие схемы натяжных устройств:
прямолинейным перемещением электродвигателя (или другого узла) (рис. 4.64, а);
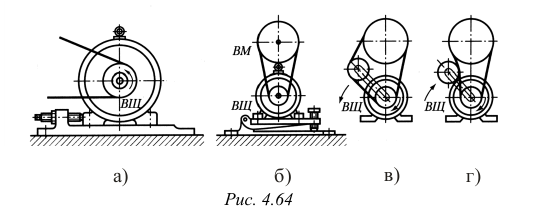
поворотом плиты, на которой расположен электродвигатель (или другой узел) (рис. 4.64, б);
оттяжным (рис. 4.64, в) или натяжным (рис. 4.64, г) роликом. В устройствах, приведенных на рис. 4.64, натяжение ремней создают исходя из условия передачи наибольшего возможного момента. На рис. 4.65 приведены схемы самонатяжных устройств: — окружной силой на шестерне (рис. 4.65, а);
реактивным моментом на корпусе узла (редуктора) (рис. 4.65, б);
реактивным моментом на корпусе электродвигателя
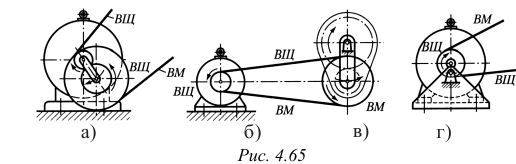
В устройствах по рис. 4.65 сила натяжения ремней автоматически изменяется пропорционально передаваемому моменту. Это способствует сохранению ремней и увеличению их ресурса. Поэтому самонатяжные устройства перспективны. Передачи с автоматическим натяжением нереверсивны.
Натяжение прямолинейным перемещением. Если электродвигатель размещен на полу цеха, то удобно регулировать натяжение ременной передачи перемещением его по двум салазкам, поставляемым вместе с двигателем.
Иногда оказывается более удобным сконструировать и изготовить специальную плиту, которую крепят к полу цеха. В плите выполняют два Т-образных паза, в которые закладывают болты 1 с четырехгранной головкой (рис. 4.66). Электродвигатель устанавливают на плиту, перемещают регулировочным винтом 2, а после окончания регулирования затягивают гайки болтов 1.
Применяют также натяжные устройства, состоящие из двух плит: неподвижной, которую крепят к полу цеха, и перемещающейся по неподвижной при регулировании натяжения ремней. При единичном производстве плиты делают из стальных листов (рис. 4.65), а при серийном — литыми из серого чугуна (рис. 4.66).
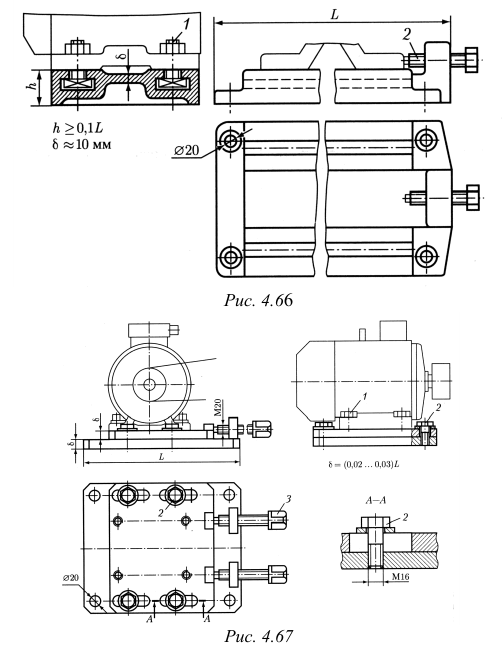
Электродвигатель крепят к верхней плите винтами 1. Для винтов 2 в верхней плите выполнены удлиненные пазы, а в нижней — резьбовые отверстия. По окончании регулирования винты 2 затягивают. Перемещают верхнюю плиту по нижней толкающими винтами 3 (рис. 4.67 и 4.68), тянущими 4 (рис. 4.69, а) или винтами 5 (рис. 4.69, б), которыми можно перемещать верхнюю плиту в обоих направлениях.
Передачи поликлиновыми и зубчатыми ремнями чувствительны к перекосу осей валов. В этих случаях для более точного направления верхней плиты в нее запрессовывают две короткие шпонки, располагая их у концов плиты. В нижней плите выполняют длинные пазы (рис. 4.70). Чтобы уменьшить момент от сил натяжения ветвей ремня, шпонки и шпоночные пазы располагают как можно ближе к шкиву.
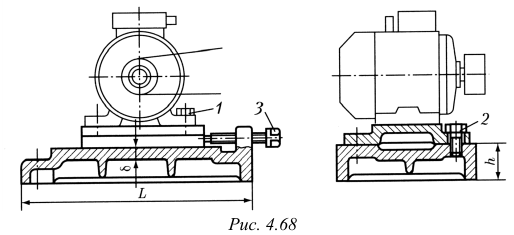
Натяжение качающимися плитами. На качающуюся плиту устанавливают электродвигатель или любой другой узел ременной передачи. При конструировании качающейся плиты необходимо ось качания располагать так, чтобы угол (рис. 4.71) был близок к прямому. Если этот угол близок к 180°(угол
), то межосевое расстояние при повороте плиты изменяется мало и регулирование неэффективно. Качающиеся плиты встраивают в станины (рамы) приводных устройств (рис. 4.91 -4.94).
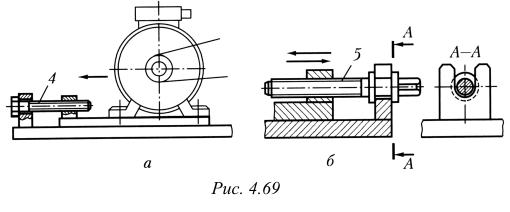
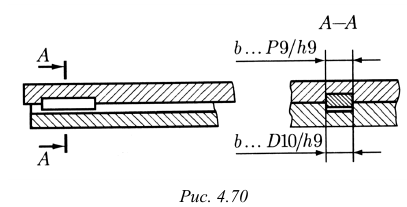
На рис. 4.72 натяжное устройство состоит из неподвижной и качающейся плит. Неподвижная плита прикреплена к полу цеха.
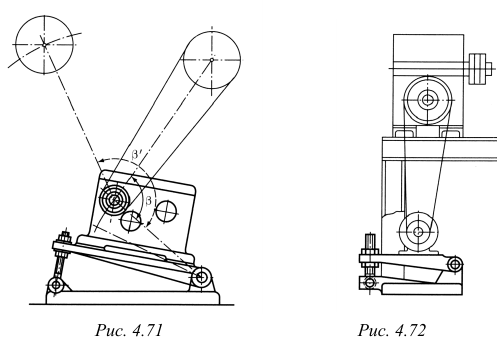
На рис. 4.73 и 4.74 натяжные устройства встроены в раму, сконструированную из швеллеров.
Натяжное устройство по рис. 4.75 установлено на редукторе. Натяжение ремней в этом случае выполняют откидным шарнирным болтом (рис. 4.75, а), двумя шарнирными болтами с правой и левой резьбой и стяжкой, также имеющей правую и левую нарезку (рис. 4.75, б), или установочным винтом (рис. 4.75, в).
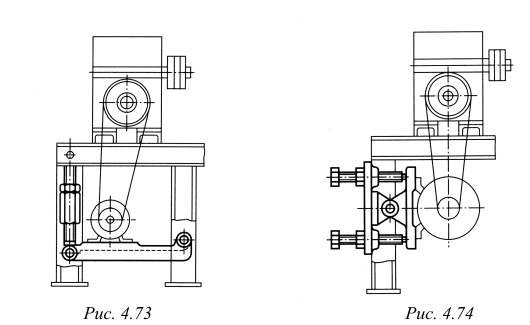
Для условий единичного производства неподвижные и качающиеся плиты конструируют сварными (рис. 4.76 и 4.77).
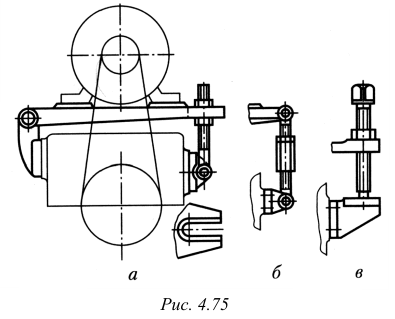
При серийном производстве экономически оправдано изготовлять качающиеся плиты литыми из серого чугуна (рис. 4.78 и 4.79). Толщина стенок литых плит должна быть по возможности везде одинаковой. Для увеличения жесткости целесообразно применение ребер.
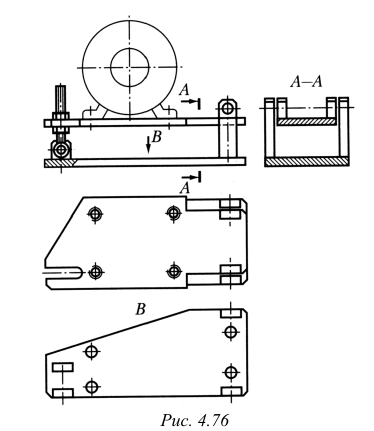
Оси поворота качающихся плит (см. рис. 4.71) выполняют по одному из вариантов, представленных на рис. 4.80. Простейший из них показан на рис. 4.80, а. В этом варианте ось I зафиксирована от осевого смещения установочным винтом 2. Широкое применение находит также осевая фиксация оси шайбой ШЕЗ 3 (рис. 4.80, б, в); на рисунке показаны оси для этих шайб двух исполнений: 6 — без борта, в — с бортом на одном конце.
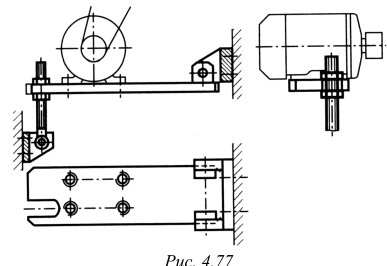
Конструкция шайбы ШЕЗ приведена на рис. 4.81. При установке шайбу заводят в проточку оси до упора, после чего прогибают середину перемычки (рис. 4.81). Допускаемая осевая сила для шайбы на номинальный диаметр оси 14… 17 мм — 5,5 кН [1].
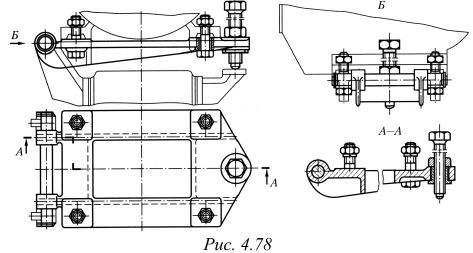
Оси поворота шарнирных болтов (см. рис. 4.71) конструируют по типу, показанному на рис. 4.82.
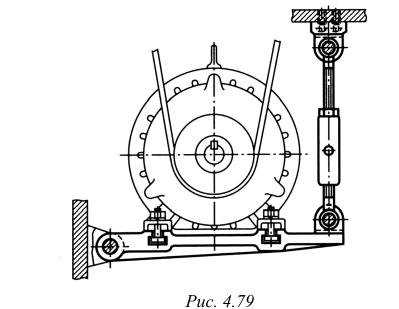
Автоматическое регулирование натяжения ременной передачи производят также силой тяжести электродвигателя и качающейся плиты (рис. 4.83, а) или пружиной (рис. 4.83 б).
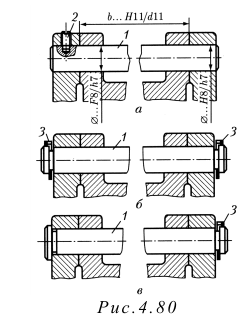
Натяжение роликами. Для плоскоременной передачи большое значение имеет угол обхвата ремня на малом шкиве. Поэтому при относительно большом передаточном числе и малом межосевом расстоянии целесообразно натяжение ремня осуществлять натяжным роликом (рис. 4.84, а). В передачах зубчатым ремнем также целесообразно применение натяжных роликов.
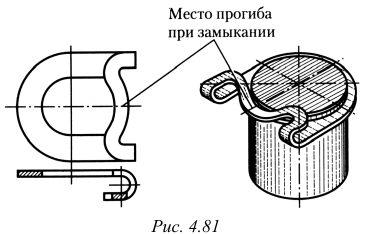
Для передач клиновыми и поликлиновыми ремнями угол обхвата ремня на малом шкиве имеет меньшее значение. Чтобы не вызывать изгиб ремней в другом направлении, в этих передачах лучше применять оттяжные ролики (рис. 4.84, б).
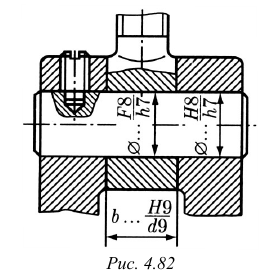
Натяжение осуществляют грузом или пружиной. Конструкцию роликов (1 н а рис. 4.84) выполняют по рис. 4.85. Диаметр натяжного ролика должен быть
где
— диаметр малого шкива. Если ведущий шкив ременной передачи установлен на валу электродвигателя, то удобно конец рычага 2 (см. рис. 4.84) расположить на поверхности этого шкива (рис. 4.86).
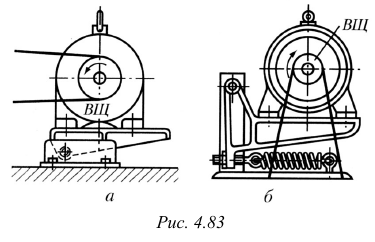
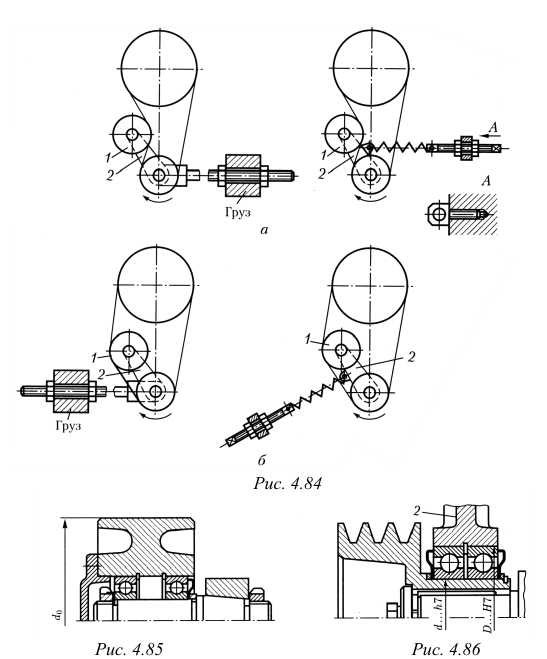
Иногда конец рычага 2 устанавливают на цилиндрической поверхности фланца крышки подшипника (рис. 4.87).
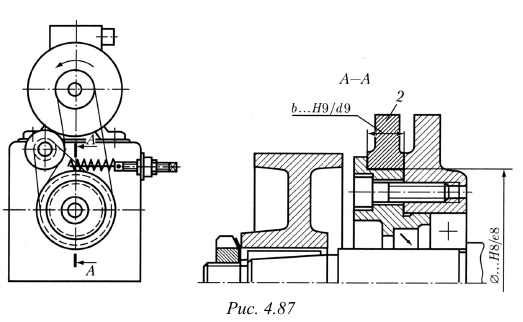
Эта теория взята со страницы лекций по предмету «прикладная механика»:
Возможно эти страницы вам будут полезны: