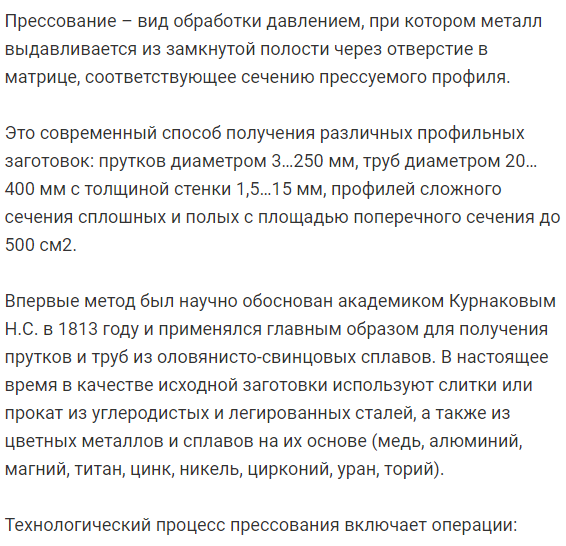
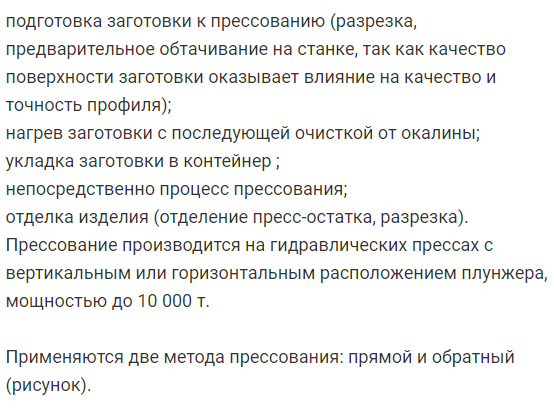
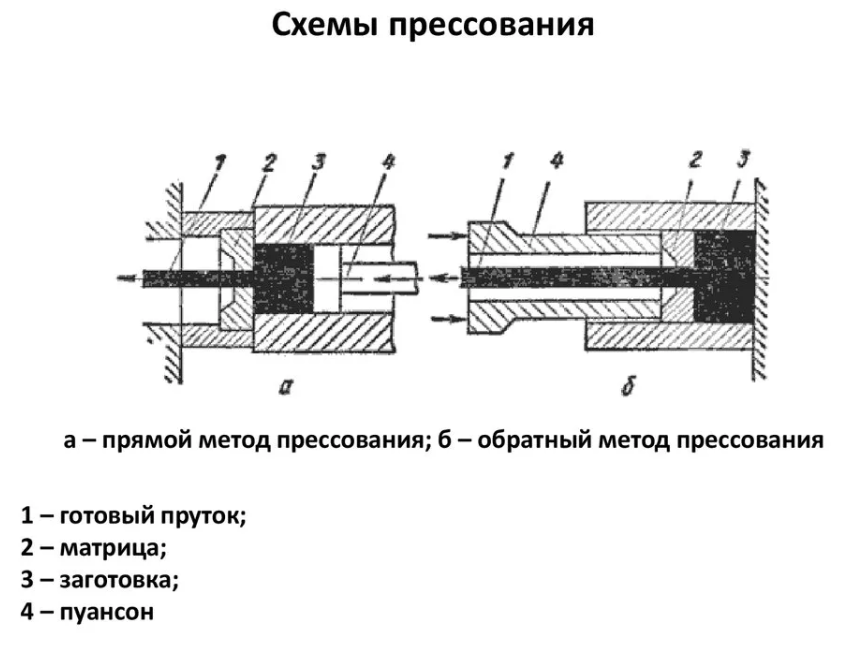
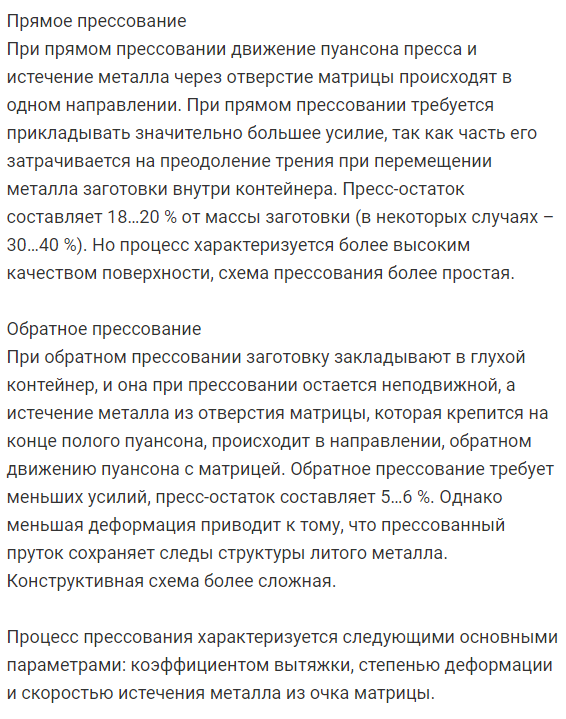
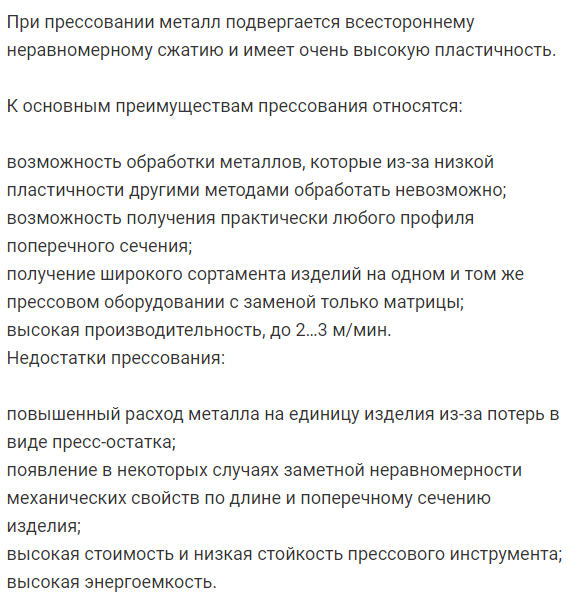
Пресс — это тип обработки давлением, который выдавливается из замкнутой полости через отверстие в матрице, которое соответствует участку профиля, из которого вытягивается металл.
Это новейший способ получить разные профильные заготовки. Стержни диаметром от 3 до 250 мм, трубы диаметром от 20 до 400 мм, толщина стенок от 1,5 до 15 мм, сложные профили поперечного сечения являются сплошными и полыми с сечением до 500 см2.
Впервые этот метод был научно доказан ученым Н.С. Крнаковым и использовался при изготовлении прутков и труб в 1813 году в основном из сплавов олова и свинца. В настоящее время в качестве исходных заготовок используются слитки из углеродистой и легированной стали, а также цветные металлы и сплавы на их основе (медь, алюминий, магний, титан, цинк, никель, цирконий, уран и торий) или слитки.
Технический процесс печати включает в себя следующие операции:
- Подготовка заготовки к прессованию (резка, предварительное вращение станка, поскольку качество поверхности заготовки влияет на качество и точность профиля);
- Нагрев заготовки и последующее удаление накипи.
- Поместите заготовку в контейнер.
- Прямой процесс прессования;
- Отделочные изделия (разделительные и режущие остатки пресса).
- Пресс выполняется гидравлическим прессом с поршнями до 10000 тонн, расположенными вертикально или горизонтально.
Используются два метода прессования: прямой и обратный (рисунок).
При прямом прессовании движение пуансона и вытекание металла из отверстия матрицы происходят в одном и том же направлении. Прямое прессование требует большего усилия, так как часть трения преодолевается при перемещении заготовки из металла в емкость. Баланс пресса составляет 18-20% от массы заготовки (в некоторых случаях 30-40%). Однако процесс характеризуется более высоким качеством поверхности, а способ прессования является более простым.
Во время обратного прессования заготовка помещается в пустой контейнер и остается неподвижной во время прессования, а утечка металла из отверстия матрицы, прикрепленного к концу полого пуансона, находится в направлении, противоположном движению матрицы и пуансона. Будет происходить Усилие обратного прессования небольшое, а баланс прессования составляет 5-6%. Однако меньшая деформация приводит к тому, что спрессованный стержень сохраняет следы структуры литого металла. Схема дизайна более сложная.
Процесс прессования характеризуется следующими основными параметрами: коэффициент вытяжки, степень деформации и скорость утечки металла из точек матрицы.
При прессовании металл подвергается всестороннему неравномерному сжатию и является очень пластичным.
Основными преимуществами печати являются:
- Возможность обработки металлов, которые не могут быть обработаны другими методами из-за низкой пластичности.
- Возможность получить практически все профили поперечного сечения.
- Широкий ассортимент продукции может быть получен с помощью одного и того же пресса просто путем замены матрицы.
- Высокая производительность, до 2-3 м / мин.
Недостатки прессы:
- Увеличение расхода металла на единицу продукции из-за потерь в виде остатков пресса.
- Появление в некоторых случаях значительной неоднородности механических свойств по длине и сечению изделия;
- Высокая стоимость и низкая долговечность пресс-инструментов.
- Высокая энергоемкость.
Смотрите также:
Примеры решения задач по материаловедению
Производство блюмов, слябов и сортового проката. | Пайка титановых сплавов. |
Центробежное литье. | Особенности свариваемости алюминиевых и магниевых сплавов. |