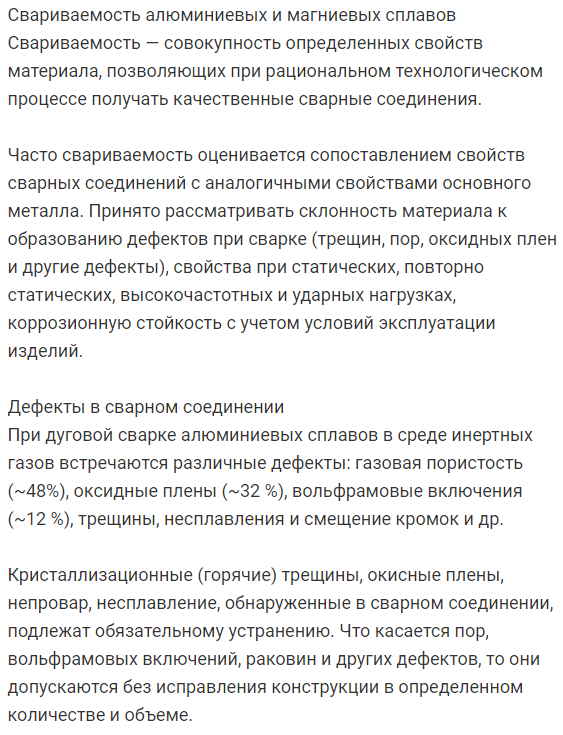
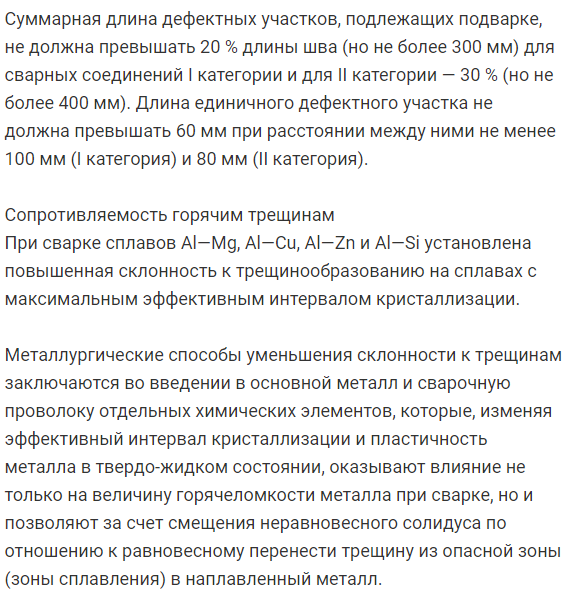
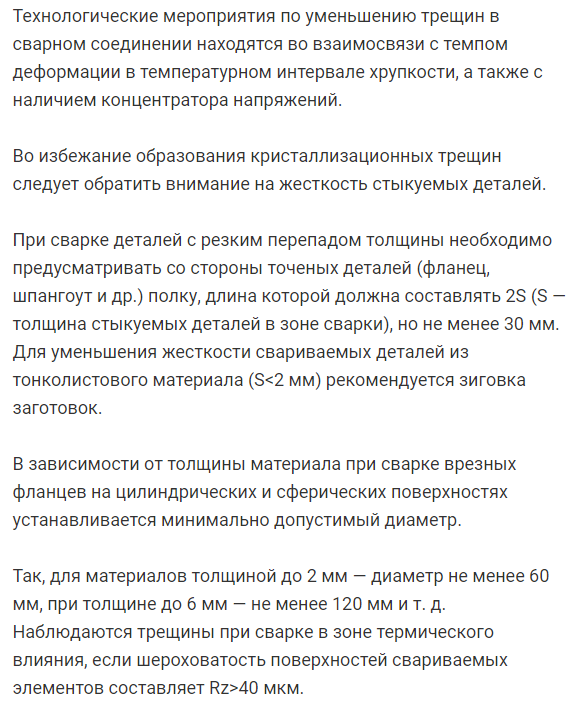
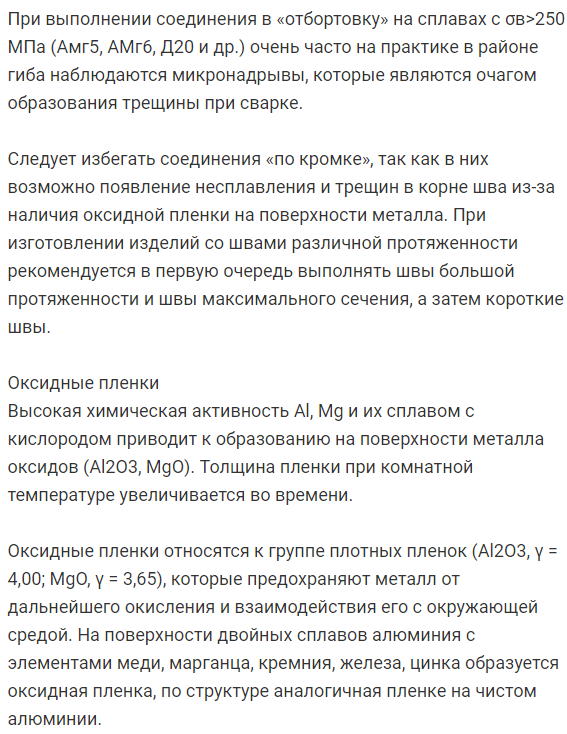
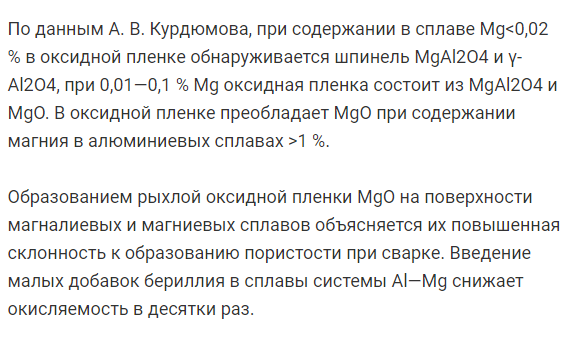
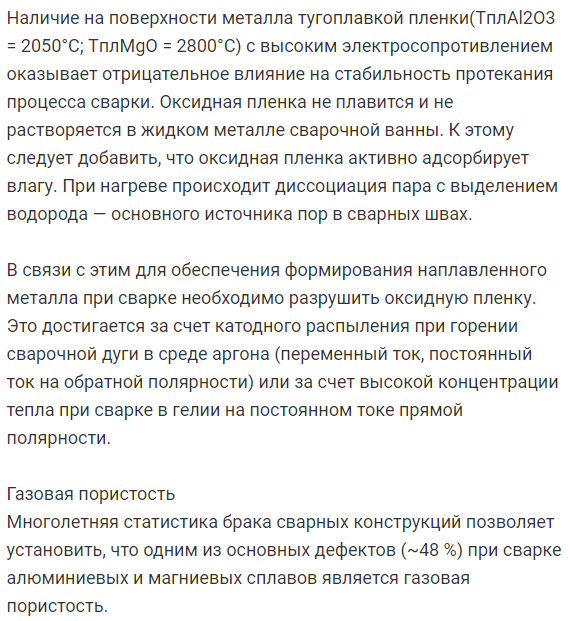
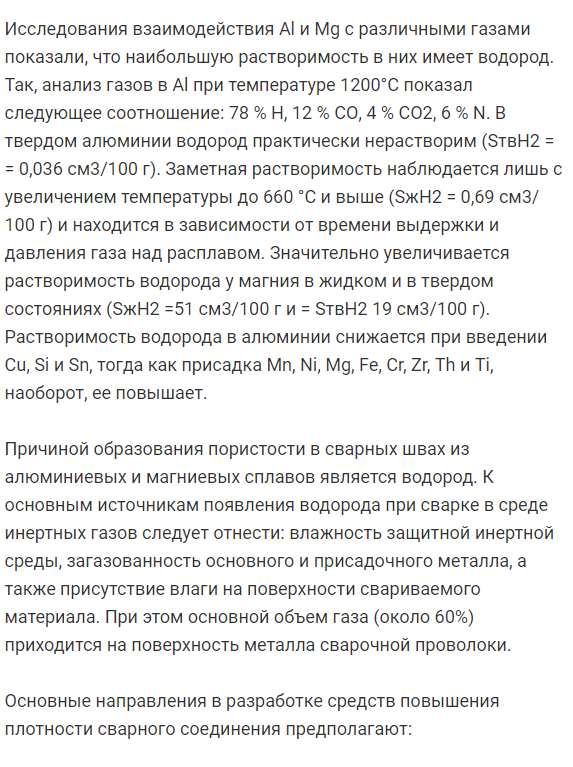
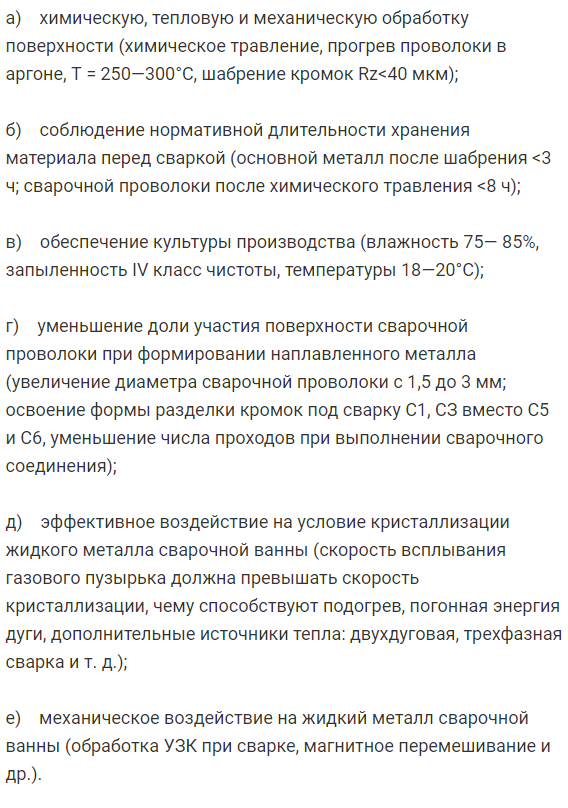
Свариваемость алюминиевых и магниевых сплавов
Свариваемость — это комбинация специфических свойств материала, которые могут дать сварные соединения высокого качества с разумным техническим процессом.
Свариваемость часто оценивается путем сравнения свойств сварных соединений с аналогичными свойствами основного металла. Учитывая склонность материалов к образованию дефектов во время сварки (дефекты, такие как трещины, поры, оксидные пленки и т. Д.), Статические, многократные статические, характеристики при высокой частоте и ударной нагрузке, а также устойчивость к коррозии с учетом условий эксплуатации изделия Это принято.
Дефект сварного шва. Сварка алюминиевых сплавов со средой инертного газа вызывает различные дефекты: пористость (~ 48%), оксидная пленка (~ 32%), вольфрамовые включения (~ 12%), трещины, плавление и смещение кромок такие как
- Необходимо устранить кристаллические (горячие) трещины, оксидные пленки, отсутствие проплавления и не плавящиеся сварные швы, обнаруженные в сварных соединениях. Для пор, вольфрамовых включений, оболочек и других дефектов конструкция допускается без фиксирования до определенного количества и объема.
Общая длина подлежащего сварке дефекта не должна превышать 20% (но не более 300 мм), а длина сварного шва сварных соединений категорий I и II — 30% (но не более 400 мм). Длина одного дефектного участка не должна превышать 60 мм, а расстояние между ними должно быть не менее 100 мм (категория I) до 80 мм (категория II).
Горячая трещиностойкость
Сварка сплавов Al-Mg, Al-Cu, Al-Zn и Al-Si усилила склонность к образованию трещин в сплавах с максимально эффективным диапазоном кристаллизации.
Металлургические методы снижения склонности к растрескиванию состоят из введения отдельных химических элементов в основной металл и сварочную проволоку и изменения эффективного интервала кристаллизации и пластичности твердого жидкого металла во время сварки. Смещение неравновесного солидуса относительно равновесного, а также величины теплоемкости металла будет перемещать трещину из опасной зоны (зоны плавления) в металл сварного шва.
Технической мерой для уменьшения растрескивания сварного соединения является корреляция между скоростью деформации в диапазоне хрупких температур и наличием концентраторов напряжений.
Необходимо следить за жесткостью соединяемых деталей, чтобы избежать образования трещин кристаллизации.
При сварке деталей с резкой разницей в толщине длина составляет 2S (S — толщина деталей, подлежащих соединению в зоне сварки), но полки от 30 мм и более от вращающихся деталей (фланец, рама и т. Д.) Нужно предоставить. Для уменьшения жесткости деталей, сваренных из листового материала (S <2 мм), мы рекомендуем зиговку заготовки.
В зависимости от толщины материала минимальный допустимый диаметр устанавливается при сварке врезных фланцев на цилиндрических и сферических поверхностях.
Следовательно, в случае материалов с максимальной толщиной 2 мм — диаметром не менее 60 мм, максимальной толщиной 6 мм — не менее 120 мм и т. Д., Если шероховатость поверхности сварного элемента составляет Rz> 40 мкм, Трещины наблюдаются при сварке.
Когда «обработка фланцев» выполняется для сплавов с σв> 250 МПа (Amg5, AMG6, D20 и т. Д.), Микроволны действительно очень часто возникают в области изгиба, и во время сварки возникают трещины.
Избегайте стыковочных соединений. Поскольку на поверхности металла имеется оксидная пленка, сварка и образование трещин могут происходить у основания сварного шва. При изготовлении изделий с различными длинами швов рекомендуется сначала создавать длинные швы и швы с наибольшим поперечным сечением, а затем создавать короткие швы.
Оксидная пленка
- Высокая химическая активность Al, Mg и их сплавов с кислородом приводит к образованию оксидов (Al2O3, MgO) на поверхности металла. Толщина пленки при комнатной температуре увеличивается со временем.
Оксидная пленка относится к группе плотных пленок (Al2O3, γ = 4,00, MgO, γ = 3,65) и защищает металл от дальнейшего окисления и взаимодействия с окружающей средой. На поверхности двойного сплава алюминия, содержащего медь, марганец, кремний, железо и цинк, образуется оксидная пленка с такой же структурой, что и у чистого алюминия.
По мнению А. В. Курдюмова, в оксиде обнаруживаются шпинели MgAl2O4 и γ-Al2O4 при содержании Mg в сплаве <0,02%, при 0,01–0,1% Mg оксид состоит из MgAl2O4 и MgO. MgO распространяется по оксидным пленкам, где содержание магния в алюминиевых сплавах превышает 1%.
Образование пленки рыхлого оксида MgO на поверхности магния и магниевых сплавов объясняет повышенную тенденцию к образованию пор во время сварки. Введение небольшого количества бериллиевой добавки в сплав Al-Mg снизит окисляемость в 10 раз. Наличие термостойкой пленки с высоким электрическим сопротивлением (TplAl2O3 = 2050 ° C; TplMgO = 2800 ° C) на поверхности металла отрицательно влияет на стабильность процесса сварки. Оксидная пленка не плавится и не растворяется в расплавленном металле в расплавленной ванне. Необходимо добавить, что оксидная пленка активно адсорбирует влагу. При нагревании выделяется водород, основная причина пор в сварном шве, и пар распадается.
В связи с этим оксидная пленка должна быть разрушена, чтобы обеспечить образование наплавленного металла при сварке. Это достигается катодным распылением (переменный ток, постоянная обратная полярность) во время горения сварочной дуги в аргоновой среде или сильным нагревом при сварке гелием постоянного тока с прямой полярностью.
Многолетние статистические данные о дефектах структуры сварного шва подтверждают, что одним из основных дефектов (~ 48%) в сварных швах из алюминиевых и магниевых сплавов являются поры.
Изучение взаимодействия Al и Mg с различными газами показывает, что водород обладает самой высокой растворимостью. Поэтому анализ газа в Al при температуре 1200 ° C показал следующие соотношения: 78% H, 12% CO, 4% CO2, 6% N. В твердом алюминии водород по существу Нерастворимый (StH2 = 0,036 см3 / 100 г). Значительная растворимость наблюдается только при повышении температуры выше 660 ° С (СЖН2 = 0,69 см3 / 100 г) и зависит от времени выдержки и давления газа в расплаве. Значительно повышается растворимость водорода в магнии в жидком и твердом состоянии (SlH2 = 51 см3 / 100 г и = StvH2 19 см3 / 100 г). Растворимость водорода в алюминии уменьшается при введении Cu, Si и Sn, но добавки Mn, Ni, Mg, Fe, Cr, Zr, Th и Ti увеличиваются наоборот.
Причиной образования пор в сварных швах из алюминиевых и магниевых сплавов является водород. Основными источниками водорода при сварке в среде инертного газа являются влажность защитной инертной среды, газовое загрязнение основного и присадочного металла и наличие влаги на поверхности свариваемого материала. В этом случае большая часть газа (около 60%) попадает на металлическую поверхность сварочной проволоки.
Основными направлениями в разработке средств для повышения плотности сварных соединений являются:
- а) Химическая, термическая и механическая обработка поверхности (химическое травление, нагрев проволоки в аргоне, Т = 250-300 ° С, соскоб края Rz <40 мкм);
- б) Соблюдение стандартного срока хранения материалов до сварки (основной материал после утилизации <3 часа, сварочная проволока после химического травления <8 часов).
- в) Обеспечить продуктивность культуры (влажность 75-85%, запыленность IV класса чистоты, температура 18-20 ° С).
- г) Уменьшение доли поверхности сварочной проволоки при формировании металла сварного шва (увеличение диаметра сварочной проволоки с 1,5 мм до 3 мм и освоение формы режущей кромки для сварки С1, С3 вместо С5 и С6 И уменьшить количество проходов при создании сварных соединений);
- d) Эффективное влияние на условия кристаллизации расплавленной ванны (скорость подъема пузырьков, скорость кристаллизации, обусловленная нагревом, линейная энергия дуги, дополнительный источник тепла: 2 дуги, 3-фазная сварка и т. д.). Должен быть превышен);
- е) Механическое воздействие расплавленной ванны на расплавленный металл (ультразвуковой контроль при сварке, магнитное перемешивание и т. д.).
Смотрите также:
Примеры решения задач по материаловедению
Прямое и обратное прессование. | Листовая штамповка. |
Производство блюмов, слябов и сортового проката. | Пайка титановых сплавов. |