Оглавление:
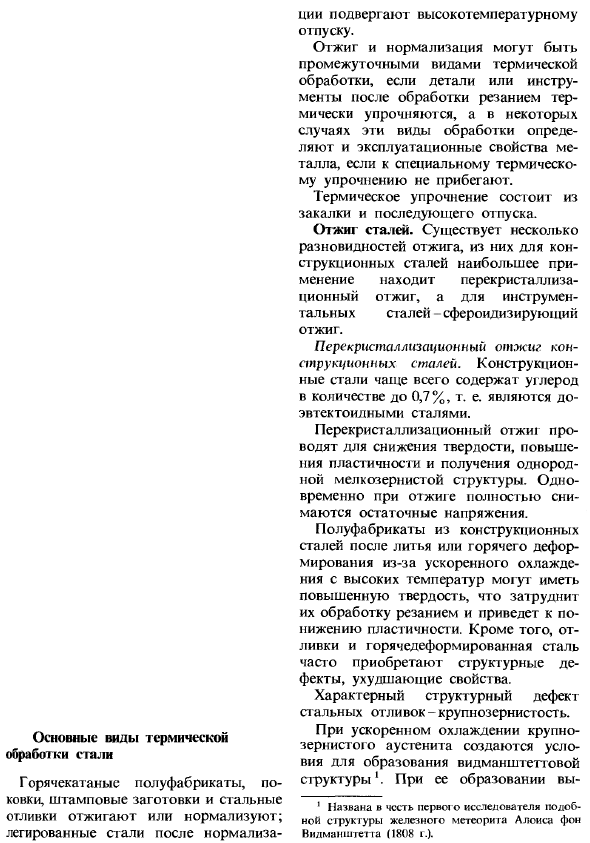
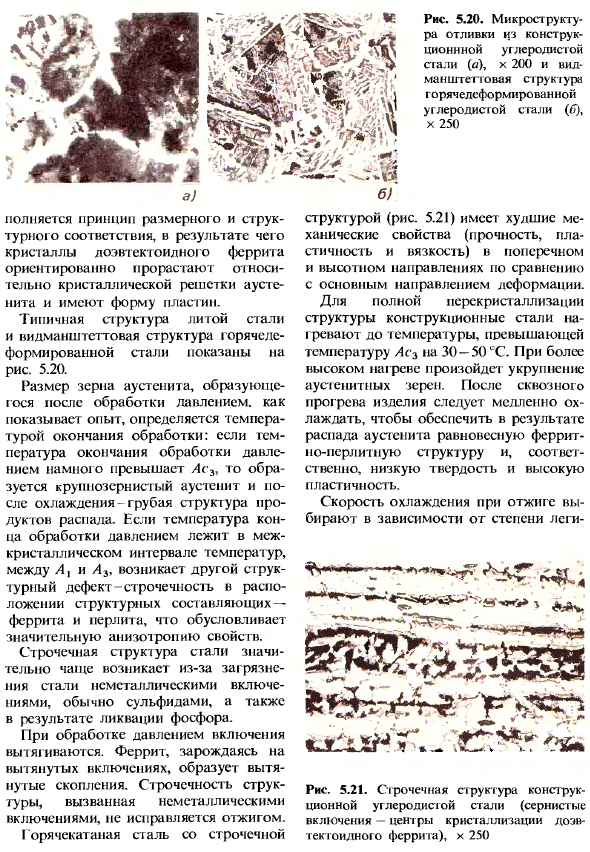
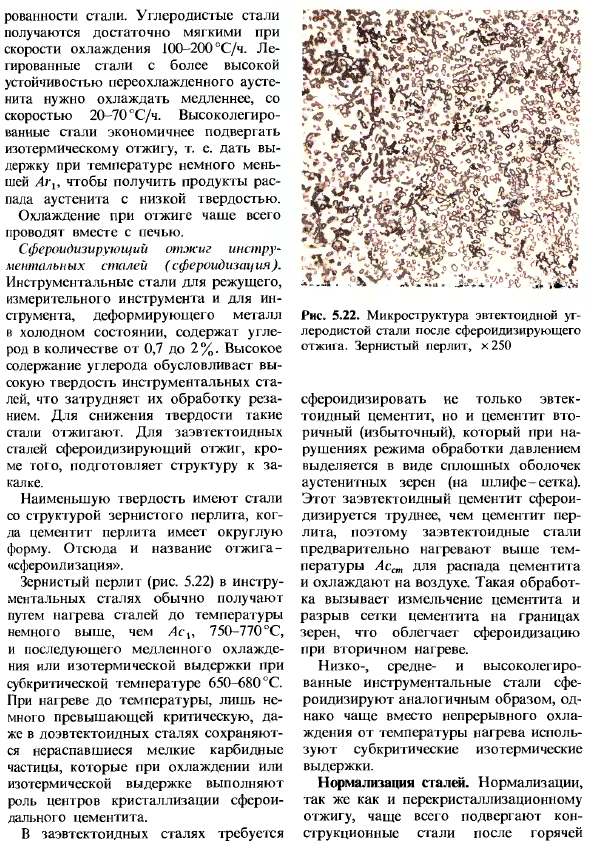
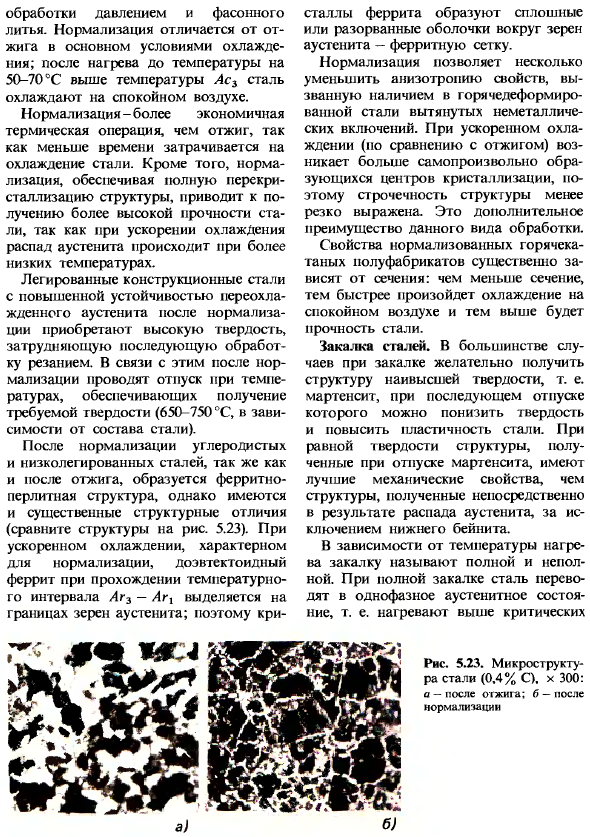
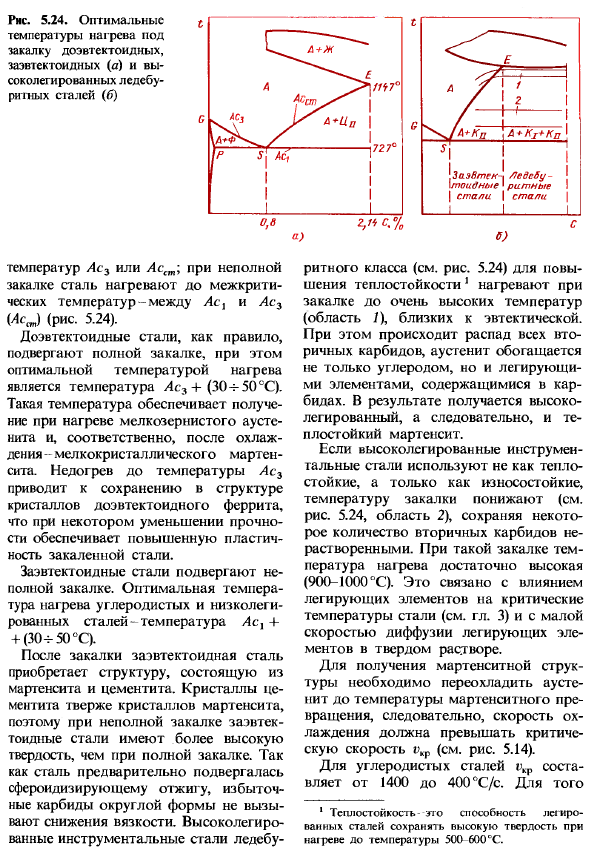
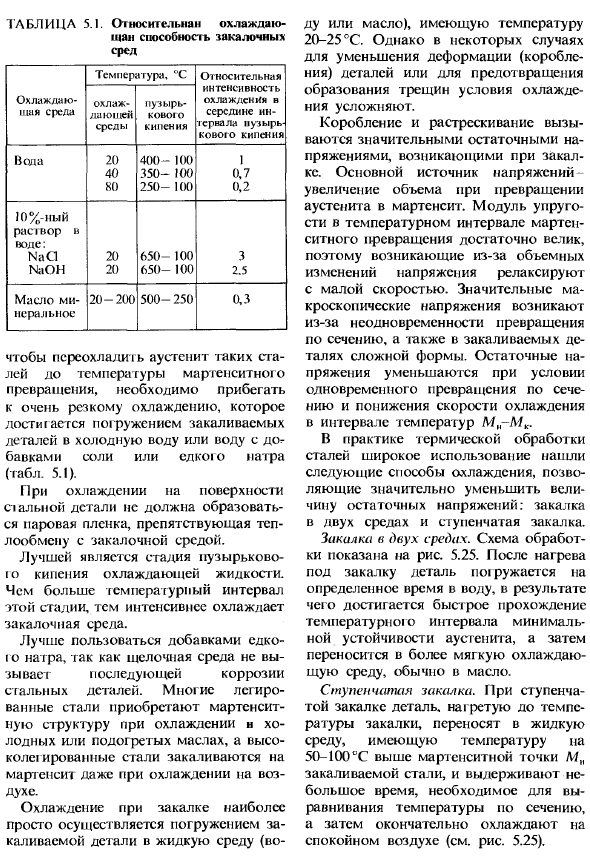
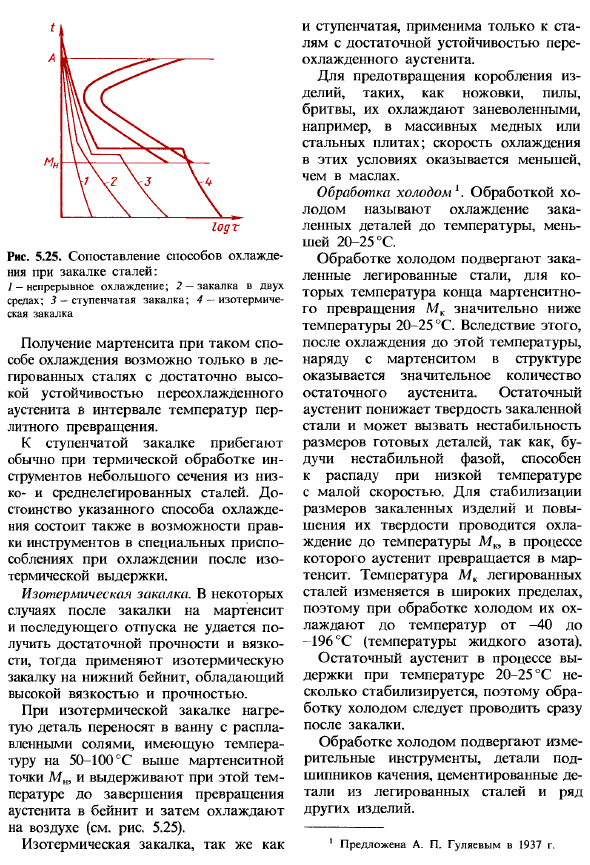
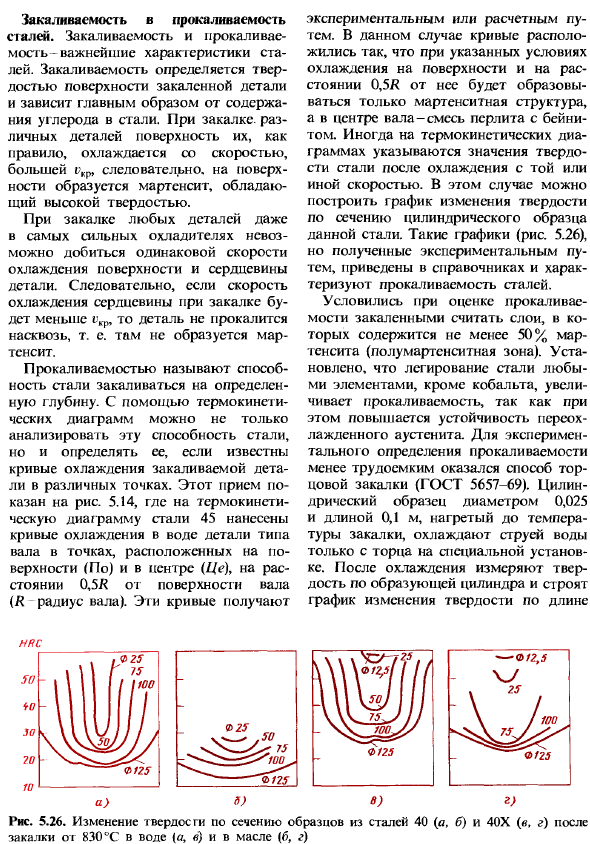
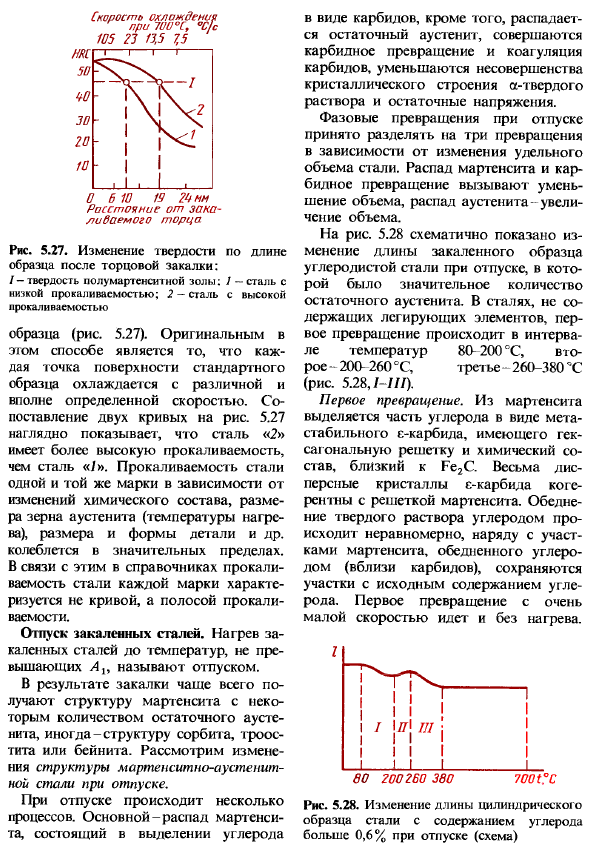
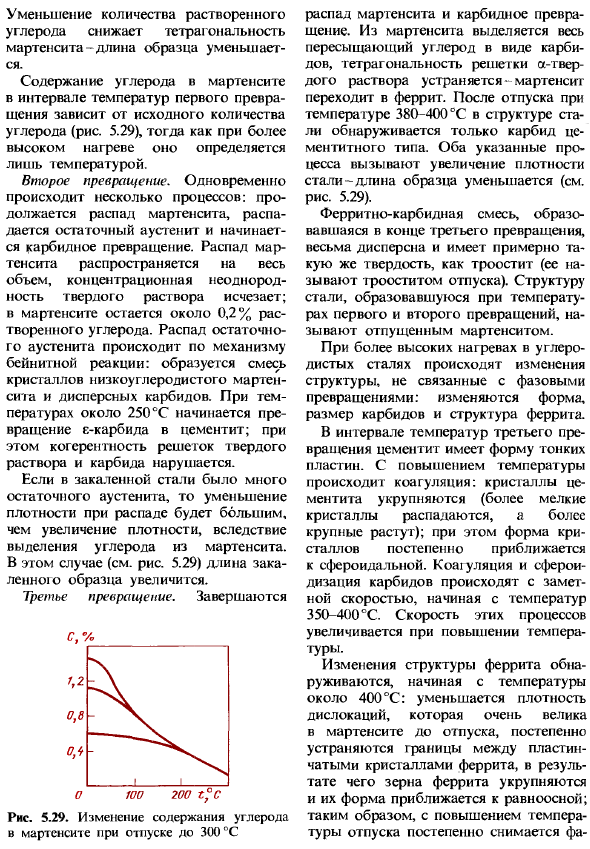
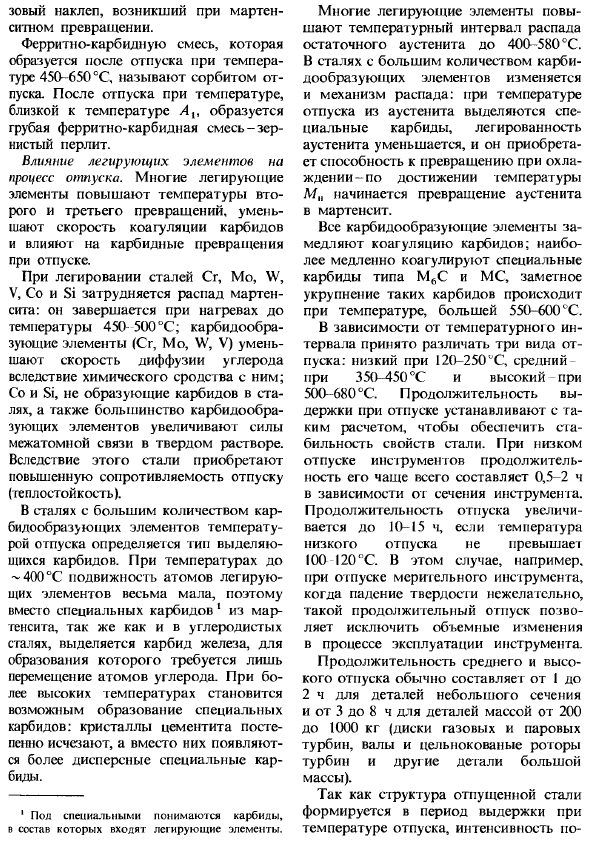
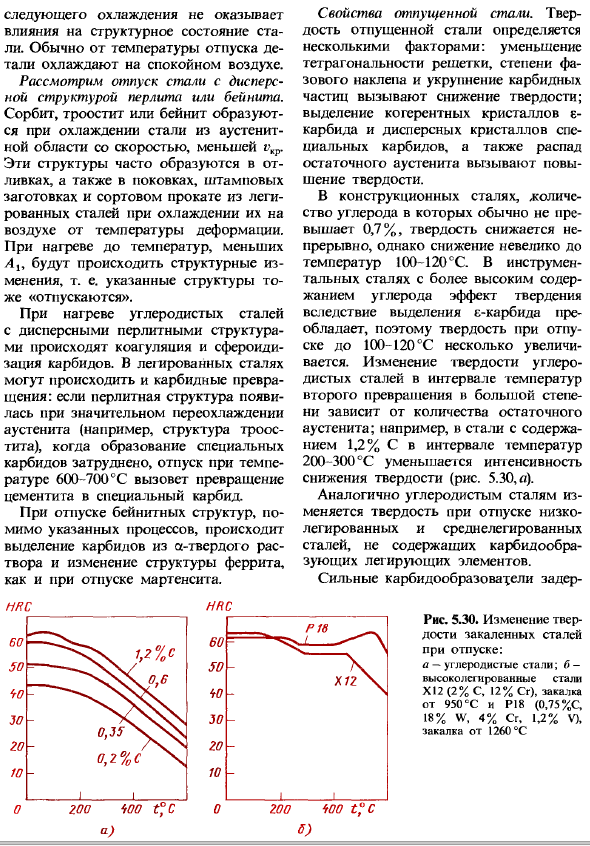
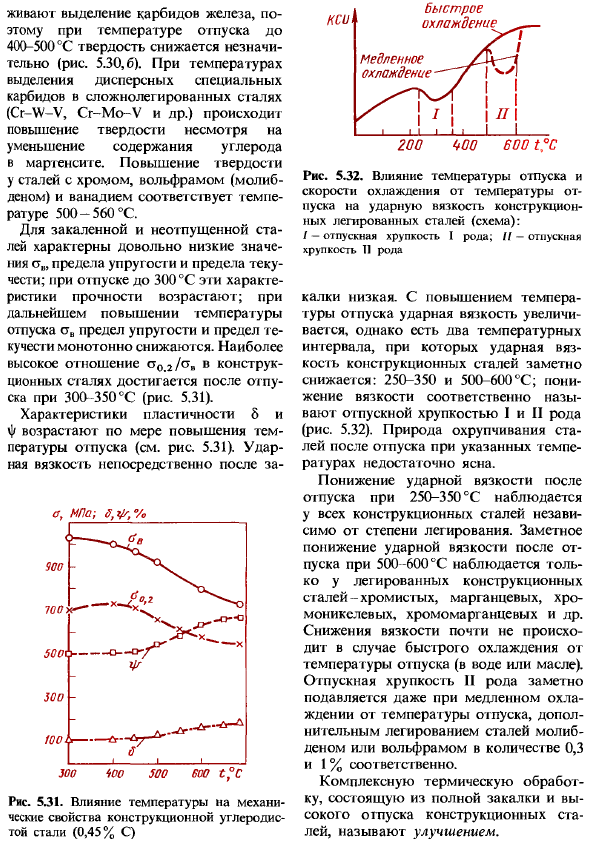

Основные виды термической обработки стали
- Подвергается высокотемпературному отпуску. Отжиг и нормализация могут быть промежуточным видом термообработки, если деталь или инструмент после термообработки является термореактивным, а в некоторых случаях прибегают к специальной термореактивной обработке НС, обработка этих видов также определяет эксплуатационные характеристики металла.
Термореактивность состоит из закалки и последующего отпуска. Сталь отожжена. Существует несколько видов отжига, но наибольшее применение для конструкционных сталей имеет рекристаллизационный отжиг, а для инструментальных сталей-сфероидизационный отжиг.
Рекристаллизованный отжиг конструкционных сталей конструкционные стали часто содержат до 0,7% углерода. Людмила Фирмаль
То есть, они предварительно эвтектоидная сталь. Рекристаллизационный отжиг проводится для снижения твердости, повышения пластичности и получения однородной структуры. microstructure. At в то же время, отжиг полностью удаляет остаточные напряжения. Конструкционные стальные полуфабрикаты после высокотемпературной деформации после литья или ускоренного охлаждения от высоких температур могут иметь более высокую твердость, что усложняет процесс резания и снижает ductility. In кроме того, отливки и горячекатаная сталь часто приобретают структурные дефекты, ухудшающие характеристики.
Характерными структурными дефектами литой стали являются крупнозернистые. Ускоренное охлаждение крупнозернистого аустенита создает условия для образования структуры Видманштеттена*.- Основные виды термической обработки стали Горячекатаные анисовые полуфабрикаты, поковки, штамповые заготовки и стальные отливки отжигают или нормализуют. Легированная сталь после нормализации- 1 Алоиз фон Вильманштетт назван в честь первого исследователя подобной структуры железа железного камня (1808). Рисунок 5.20.Микроструктура отливок из углеродистой стали (а), Х2 (х) и Wi
- dmannstett *структура горячедеформированные из углеродистой стали(б), х 250 Соблюдается принцип соответствия размеров и структуры, в результате чего кристаллы лейктикоидного феррита растут в форме, ориентированной на аустенитную кристаллическую решетку и имеют форму пластины. Типичная структура литой стали и структура Widmannstätt * горячей стали показаны на рисунке. 5.20. Как показывает опыт, размер зерна аустенита, образующегося после обработки давлением, определяется конечной температурой обработки. Если конечная температура обработки давлением значительно выше Ac3, то образуется крупнозернистый аустенит, а после охлаждения образуется крупнозернистая Струпа продукта распада.
Когда температура в конце обработки давлением находится в межкристаллическом интервале температур между A}и / 13, расположение структурных компонентов-феррита и перлита-вводит еще один структурный дефект структуры, приводящий к значительной анизотропии свойств. Структура проволоки из стали гораздо более вероятна в результате загрязнения стали неметаллическими включениями, обычно сульфидами, и сегрегации фосфора. При обработке давлением образуются включения. Феррит, зарождающийся на вытянутых включениях,
образует вытянутый кластер. Людмила Фирмаль
Структурная структура за счет неметаллических включений не модифицируется отжигом. Горячекатаная сталь Структура (рис. 5.21) обладает худшими механическими свойствами (прочностью, пластичностью и вязкостью) в поперечном и вертикальном направлениях по сравнению с основным направлением деформации. Чтобы полностью перекристаллизовать структуру, структурная сталь on-I плавится при температурах на 30°C выше температуры Ls3.Более высокий нагрев приводит к огрубению зерен аустенита.
После нагрева от конца к концу продукт следует медленно охлаждать, чтобы обеспечить равновесную ферритно-перлитную структуру и, соответственно, низкую твердость и высокую пластичность в результате разложения аустенита. Скорость охлаждения во время отжига выбирается в соответствии со следующими градусами: 5.21.Структурная структура провода стали углерода (содержание серы центр кристаллизации феррита doev-hectoid), содержание стали x 250.Углеродистая сталь получается очень мягкой при скорости охлаждения 100-200°с / ч. легированные стали с высокой
стабильностью переохлажденного аустенита должны охлаждаться медленнее при скорости 20-70°с / ч. высоколегированная сталь подвергается воздействию несколько более низкой температуры, чем Lg, с целью получения более экономичного изотермического отжига, то есть продуктов аустенитного разложения низкой твердости. Охлаждение во время отжига чаще всего производится в печи. Сфероидизирующий отжиг (сфероидизация) инструментальной стали.
Инструментальные стали для режущего, измерительного и холодноформовочного инструмента содержат 0,7-2% углерода. Высокое содержание углерода определяет высокую твердость инструментальной стали, что усложняет обработку резанием. Такая сталь для снижения твердости Запеченные баклажаны. Для сверхэвтектической стали сфероидизирующий отжиг дополнительно подготавливает структуру к упрочнению. Если цементирующий перлит имеет округлую форму, то минимальная твердость наблюдается в сталях с зернистой структурой перлита.
Отсюда и происходит название отжига — «сфероидизация». Гранулированный перлит инструментальной стали (рис.5.22) обычно получают путем нагрева стали до температуры чуть выше 750-770°C и медленного охлаждения или изотермического удержания при температуре ниже 650-680°C. Даже предэвтектоидная сталь, лишь немного превышающая критическое значение, удерживает мелкие, не разлагающиеся частицы карбида и действует как центр кристаллизации сферического цементита путем охлаждения или изотермического удерживания.
Требуется гипер-эвтектоидная сталь 5.22.Микроструктура эвтектоидной углеродистой стали после сфероидного отжига гранулированного перлита, Х250 В дополнение к эвтектоидному цементиту, вторичный (избыточный) цементит также является spheroidized. It выделяется в виде сплошной оболочки из аустенитных зерен (на тонком сечении сетки), с нарушением режима обработки давлением. Этот гипер-эвтектоидный цементит сложнее сфероидизировать, чем перлитный цементит, поэтому сверхэвтектоидная сталь предварительно нагревается при температуре, превышающей температуру разложения цементита.
Он охлаждается в воздухе. Этот процесс приводит к измельчению цементита и разрушению сети цементита на границах зерен, что способствует сферообразованию при вторичном нагреве. Низколегированная, среднелегированная и высоколегированная инструментальная сталь сфероидизируется аналогичным образом, но вместо непрерывного охлаждения от температуры нагрева часто используются подкритические изотермические экстракты.
Сталь есть tempered. As при рекристаллизационном отжиге нормализация чаще всего применяется к конструкционным сталям после горячей обработки давлением и литьем под давлением. Нормализация отличается от отжига главным образом в условиях охлаждения. После нагревать к температуре 50 ~ 70℃более высоко чем температура Ac3, сталь охлажена с нежным воздухом. Благодаря меньшему времени, затрачиваемому на охлаждение стали, это более экономичная тепловая операция, чем annealing.
In кроме того, нормализация, обеспечивающая полную перекристаллизацию структуры, приводит к повышению прочности стали, так как разложение аустенита происходит при более низкой температуре во время ускорения охлаждения. Легированная конструкционная сталь с повышенной стабильностью переохлажденного аустенита после нормализации приобретает высокую твердость, что усложняет последующее machining. In в связи с этим после нормализации отпуск проводят при температуре, обеспечивающей необходимую твердость (650, 750°С в зависимости от состава стали).
После нормализации углеродистой стали и низколегированной стали, а также после отжига образуется ферритно-перлитная структура, но имеются существенные структурные различия (сравните со структурой на рис. 5.23). при ускоренном охлаждении, которое является особенностью нормализации, сверхэвтектоидные ферриты выделяются на границах зерен аустенита по мере их прохождения через температурный диапазон Ag3-Arg. So, Кри Ферритная сталь образует непрерывную оболочку или разрывную оболочку вокруг аустенитной зернисто-ферритовой сети.
Нормализация приводит к незначительному снижению анизотропии свойств за счет наличия в горячедеформированной стали удлиненных неметаллических включений. Во время ускоренного охлаждения (по сравнению с отжигом) структура stitching™менее заметна из-за более естественно сформированных центров кристаллизации. Это является дополнительным преимуществом данного вида обработки. Характеристики нормированных горячекатаных полуфабрикатов во многом зависят от площади поперечного сечения.
Чем меньше площадь поперечного сечения, тем быстрее охлаждение мягким воздухом, тем выше прочность стали. Закалка steel. In в большинстве случаев при закалке можно получить самую высокую твердость ткани, то есть мартенсит, а при последующем отпуске снизить твердость и повысить пластичность стали. При равной твердости структура, полученная при отпуске мартенсита, обладает лучшими механическими свойствами, чем структура, полученная непосредственно в результате разложения аустенита, за исключением низшего бейнита.
В зависимости от температуры нагрева, закалка называется полной и неполной. При полном затвердевании сталь переходит в однофазное аустенитное состояние. То есть, сталь нагревается выше критической. 5.23.Микроструктура стали (0,4% с), х 300: А-после отжига; Б-после нормализации РНС. 5.24.Оптимальная температура нагрева для закалки заэвтектоидного, заэвтектоидного (а) и высоколегированные красный Брайт стали (б) Температура AC3 или ACE«; если отверждение не завершено, сталь нагревают до критической температуры между AC3 и Ac3 (Ac3) (рис. 5.24).
Обычно сверхэвтектоидная сталь подвергается полному упрочнению, но оптимальной температурой нагрева является температура Ac3 +(30h-50°C).Эта температура обеспечивает образование тонкого аустенита во время нагрева и, следовательно, после охлаждения. ЛНР Кристалла мартенсита. При переохлаждении до температуры Ac3 тот же феррит удерживается в кристаллической структуре углекислого газа, что несколько снижает его прочность, но повышает пластичность закаленной стали. Во-эвтектоидная сталь подвергается неполной закалке.
Оптимальная температура нагрева для углеродистой стали и низколегированной стали-Ac, 4 — +(ЗОч-50 ° C). После закалки, гипер-эвтектоидная сталь приобретает структуру, состоящую из мартенсита и цементита. Поскольку кристаллы цементита тверже мартенситных кристаллов, то в случае неполной закалки сверхэвтектоидная сталь тверже, чем при полной закалке. Поскольку сталь ранее подвергалась сфероидизирующему отжигу, избыток круглых карбидов не вызывает снижения вязкости.
Высоколегированная инструментальная сталь Для повышения термостойкости, класс ritic (см. Рисунок 5. 24) нагревается до очень высокой температуры (область/), где 1 близок к эвтектике во время quenching. In в этом случае все вторичные карбиды разлагаются, и аустенит становится богатым не только углеродом, но и легирующими элементами, содержащимися в нем. carbides. As в результате высоколегированный, следовательно, может быть термостойким мартенситом.
Если высоколегированная инструментальная сталь используется только как жаропрочная, а не износостойкая, то температура отверждения будет снижена без растворения определенного количества вторичных карбидов(см. Рис. 5). 24, область 2).При такой закалке температура нагрева очень высока (900-1000°C).Это связано с влиянием легирующих элементов на критические температуры стали (см. Главу 3) и медленной скоростью диффузии легирующих элементов в твердом растворе.
Для получения мартенситной структуры аустенит должен быть переохлажден до температуры мартенситного превращения, поэтому скорость охлаждения должна превышать критическую скорость 1> cr(см. рис. 5.14). Для углеродистой стали GCR составляет 1400-400°C / s. In порядок Термостойкость-это способность стали сохранять высокую твердость при нагреве до температуры 500-600°С. Запеченные баклажаны: в случае ультраэвтектической стали сфероидизированный отжиг подготавливает структуру к дальнейшему упрочнению.
Если цемент из перлита имеет круглую форму, то минимальная твердость наблюдается в Стали с зернистой структурой перлита, поэтому название отжига — «сфероидизация». Гранулированный перлит инструментальной стали (рис.5.22) обычно получают путем нагрева стали до температуры чуть выше 750-770°С и выдерживания ее постепенно холодной или изотермической при температуре ниже 650-680°С. Даже предэвтектоидная сталь, которая лишь незначительно превышает критическое значение, сохраняет мелкие нерастворимые частицы карбида и служит центром кристаллизации сферического цементита путем охлаждения или изотермической выдержки.
Требуется гипер-эвтектоидная сталь 5.22 зернистый перлит, Х250, эвтектоидная углеродная микроструктура после отжига В дополнение к эвтектоидному цементиту, вторичный (избыточный) цементит также является spheroidized. It выделяется в виде сплошной оболочки из аустенитных зерен (на тонких участках сетки) и нарушает обработку давлением. Суперэвтектоидная сталь предварительно нагревается до температуры, превышающей температуру разложения цементита.
Этот процесс приводит к дроблению цементита и разрушению цементитной сети на границах зерен, способствуя образованию сфер при вторичном нагреве. Низколегированные, среднелегированные и высоколегированные инструментальные стали также сфероидизируются аналогичным образом, но вместо непрерывного охлаждения от температуры нагрева часто используются подкритические изотермические экстракты.
Сталь есть tempered. As отжиг рекристаллизации, нормализация наиболее хорошо приложен к структурной стали после горячей деятельности давлением и инжекционным методом литья. После нагревать к температуре более высокой чем температура 50 ~ 70℃ Ac3, сталь охлажена с слабым воздухом. Из-за короткого времени, необходимого для охлаждения стали, это более экономичная термическая операция, чем отжиг, кроме того, так как при ускорении охлаждения разложение аустенита происходит при более низкой температуре, а нормализация, обеспечивающая полную перекристаллизацию структуры, приводит к повышению прочности стали.
Легированная конструкционная сталь с повышенной стабильностью переохлажденного аустенита после нормализации приобретает высокую твердость, что усложняет последующую механическую обработку, в связи с чем, после нормализации, происходит отпуск при температуре (650, 750°С, в зависимости от состава стали), обеспечивающей необходимую твердость. После нормализации углеродистой стали и низколегированной стали, а также после отжига, образуется ферритно-перлитная структура, но есть важная структура Различия (сравните со структурой рисунка 5.23).
При ускоренном охлаждении, которое является характерной особенностью нормализации, гиперэвтектоидный феррит высвобождается на границе зерен аустенита при прохождении через температурный диапазон Ag3-Arg. Ферритная сталь образует непрерывную оболочку или разрывную оболочку вокруг аустенитной зернистой ферритовой сети. Нормализация приводит к незначительному снижению анизотропии свойств за счет наличия в горячедеформированной стали удлиненных неметаллических включений.
Во время ускоренного охлаждения (по сравнению с отжигом) структура stitch™становится менее заметной из-за более естественно сформированного центра кристаллизации. Характеристики нормированных горячекатаных полуфабрикатов в значительной степени зависят от площади поперечного сечения, и чем меньше площадь поперечного сечения, тем быстрее происходит охлаждение мягким воздухом, тем выше прочность стали. Упрочнение стали: в большинстве случаев удается получить самую высокую твердость ткани, то есть мартенсит, в процессе упрочнения, а с последующим отпуском, снизить твердость стали и улучшить ее ductility.
As результат разложения аустенита непосредственно, за исключением низшего бейнита. В зависимости от температуры нагрева закалку называют полной и неполной, а при полной закалке сталь переходит в однофазное аустенитное состояние. 5.23.После отжига: микроструктура стали (0,4% с), х 300.B после нормализации РНС. 5.24.Оптимальная температура нагрева для закалки заэвтектоидного, заэвтектоидного (а) и высоколегированные красный Брайт стали (б) Температуры АС3 или туз».
Если закалка не завершена, сталь нагревают до критической температуры между AC3 и Ac3 (Ac3) (рис.5.24). Обычно суперэвтектоидная сталь полностью затвердевает, но оптимальной температурой нагрева является Ac3 +(30h ~ 50°C).Эта температура образует мелкий аустенит во время нагрева и, следовательно, после охлаждения. 5.25.Сравнение способов охлаждения при закалке стали: / — Непрерывное охлаждение; 2-усиление в 2 средах. 3-этап лечения; 4〜изотермического отверждения Получение мартенсита этим способом охлаждения возможно только с легированными сталями, в которых стабильность переохлажденного аустенита в интервале температур перлитного превращения достаточно высока.
Обычно ступенчатую закалку применяют при термообработке инструментов малого сечения из низколегированных и среднелегированных сталей. Преимущество данного способа охлаждения заключается также в возможности использования специального устройства перевязочного инструмента при охлаждении после изотермической выдержки. Изотермический hardening. In в некоторых случаях его можно закалить мартенситом, а затем закалить, после чего можно получить НС с достаточной прочностью и вязкостью. Затем на бейнит с высокой вязкостью и прочностью наносят закалку равной вязкости.
В процессе изотермического отверждения нагретую часть переносят в ванну, содержащую расплавленную соль, при температуре на 50-50°С выше точки мартенсита и оставляют при этой температуре до полного превращения аустенита в бейнит(см. рис.5.25). То же, что и изотермическое отверждение И в этапах, его можно только приложить к стали с достаточной стабилностью охлаждать psr! Для предотвращения коробления таких изделий, как ножовки, пилы и бритвы, неблагоприятное охлаждение проводят, например, на больших медных пластинах или железных пластинах.
Скорость охлаждения в этих условиях будет ниже, чем у масла. Холодная Работа 1.Холодная обработка-это охлаждение закаленных деталей до температуры менее 20-25°С. Холодная обработка применяется к закаленным легированным сталям, где температура в конце мартенситного превращения МК значительно ниже температуры 20-25°C. As в результате после охлаждения до этой температуры мартенситом в структуре появляется значительное количество остаточного аустенита. Остаточный аустенит может уменьшить твердость закаленной стали и дестабилизировать размер готовой детали.
Это происходит потому, что это нестабильная фаза и может распадаться на низких скоростях при низких температурах. temperatures. To стабилизируют размер затвердевшего изделия и повышают твердость, охлаждение проводят до температуры, при которой аустенит становится мартенситом. Поскольку температура легированной стали МК сильно меняется, при холодной обработке ее охлаждают до температуры от −40 до −196°С (температура жидкого азота). Остаточный аустенит устойчив в определенной степени при старении при температуре 20-25°С и должен подвергаться холодной обработке сразу после закалки.
Холодная работа применяется к измерительному оборудованию, частям подшипника завальцовки, частям цемента легированной стали, и много других продуктов. Его предложил А. 1937 П. Гуляев Прокаливаемость в прокаливаемости стали. Закаливаемость и закаливаемость являются наиболее важными свойствами стали. Отверждаемость определяется поверхностной твердостью упрочненной детали и зависит в первую очередь от содержания углерода в стали. При закалке различных компонентов, их поверхность, как правило, охлаждается со скоростью, превышающей ГКЛ. Поэтому на поверхности образуется мартенсит высокой твердости.
Даже самый сильный охладитель затвердевает деталь, и невозможно добиться одинаковой скорости охлаждения поверхности и сердцевины детали. Поэтому, если скорость охлаждения сердечника при закалке меньше t-KfU, то деталь не выгорит. Мартенсит не образуется. Дымкой называют способность затвердевать до определенной глубины. Используя термодинамические диаграммы, можно не только проанализировать эту способность стали, но и определить, известны ли кривые охлаждения закаленных деталей в различных точках.
Эта техника проиллюстрирована на рисунке. 5.14, на расстоянии 0,5 K от поверхности вала (I-радиус вала) кривая охлаждения в воде валообразной части в точке на поверхности (Po) и центре (Z / e) изображена на кинетической диаграмме стали 45.Эти кривые являются Экспериментально или computational. In в этом случае при указанных условиях охлаждения только мартенситная структура от поверхности образуется на расстоянии 0,5 К от подшипника, а кривая размещается так, что в центре вала находится смесь перлита и бейнита.
Термодинамическая диаграмма после охлаждения с определенной скоростью может указывать на величину твердости steel. In в этом случае можно построить график изменения твердости по поперечному сечению цилиндрического образца этой стали. Такой график (рис. 5.26) получен экспериментально, но он описан в справочниках и характеризует прокаливаемость стали. При оценке calcining™ было решено, что упрочненный слой содержит не менее 50% мартенсита (полутенситная зона). установлено, что легирование некальбальтовыми элементами повышает упрочняющие свойства переохлажденного аустенита для повышения его стабильности.
В связи с экспериментальным определением прокаливаемости оказалось, что метод механического упрочнения не очень трудоемкий (ГОСТ 5657-69).Цилиндрические образцы диаметром 0,025 и длиной 0,1 м, нагретые до температуры отверждения, охлаждаются токами воды только с краев специальных установок. После охлаждения измерьте твердость вдоль шины цилиндра и создайте график изменения твердости по длине один) РНС. 5.26.Изменение твердости по сечению образцов стали 830 (А, Б) и 40х (а, г) после закалки от 40°С в воле (а, в) и в масле (Б, г) Скорость охлаждения при 7004 Н,°С/ с 105 25 13.5 7.5 НМ 1 1 г 50 я Ноль ноль Один \ 30 1 1 20 1 1 10-1. 1 ■ т 1 1 j I Около 6 10 10 20 нм Рисунок 5.27.
Изменение твердости по длине образца после механической закалки: Расстояние от закаленного края Твердость / -полу-мартенситная зола: 1-сталь с низкой прокаливаемостью. 2-закаляющихся сталь Образец (рис. 5.27).Оригинальность этого метода заключается в том, что каждая точка на поверхности стандартного образца охлаждается с различной, четко определенной скоростью. Сравнение 2 кривых на рисунке 2 5.27 ясно показывает, что Сталь «2»более закалена, чем сталь»/».
Прокаливаемость одной и той же марки стали сильно варьируется в зависимости от химического состава, размера зерна аустенита (температуры нагрева), размера и формы детали, etc. In в связи с этим в справочнике обжиг каждой марки стали характеризуется НС кривыми и обжиговыми полосами. Закаленная сталь закаленная. Нагрев до температуры, не превышающей температуру закаленной стали, называется отпуском. В результате закалки чаще всего получают мартенситные структуры, содержащие определенное количество остаточного аустенита, причем иногда это структуры сорбита а, трозита или бейнита.
Рассмотрим изменения структуры мартенситных аустенитных сталей при отпуске. Во время праздников происходят некоторые процессы. Основным из них является распад мартенсита, который заключается в выделении углерода Кроме того, в виде карбидов происходит разложение остаточного аустенита, трансформация карбидов и затвердевание карбидов, а также уменьшение дефектов и остаточных напряжений в кристаллической структуре α-твердого раствора.
Принято разделять фазовые превращения при отпуске на 3 превращения в зависимости от изменения определенного объема стали. Разложение мартенсита и превращение карбидов уменьшают объем, в то время как разложение аустенита увеличивает объем. На рис. 5.28 схематично показано изменение длины закаленного образца углеродистой стали при отпуске со значительным количеством остатков austenite. In сталь с легирующими элементами, первое превращение происходит в интервале температур 80-200°с, 2-е 200-260°с, 3-е 260-380 х (Рисунок 5.28、/ -///)。 Первая трансформация.
Часть углерода выделяется в виде метастабильных электронных карбидов, свободных от мартенсита. Химический состав с гексагональной решеткой близок к Fe2C. Высокодисперсные кристаллы с-карбида находятся в тесном контакте с мартенситной решеткой. Восстановление углерода в твердом растворе происходит неравномерно, и область начального содержания углерода сохраняется вместе с областью мартенсита, где углерод восстанавливается(вблизи карбида).Первое превращение на очень малой скорости происходит без нагрева. 5.28.
Изменение длины цилиндрического стального образца с содержанием углерода более 0,6% при отпуске(см. Рисунок) По мере уменьшения количества растворенного углерода снижается стабильность тетрагональной системы мартенсита и уменьшается длина образца. Содержание углерода в мартенсите в интервале температур начального превращения зависит от исходного количества углерода(рис.5.29), но при высоких температурах оно определяется только температурой. 2-е преобразование. Разложение мартенсита продолжается, остаточный аустенит разлагается и начинается превращение карбида.
Распад мартенсита распространяется по всему объему, и неоднородность концентрации твердого раствора исчезает. Около 0,2%растворенного углерода остается в мартенсите. Разложение остаточного аустенита происходит по механизму реакции бейнита. Образуется смесь низкоуглеродистых мартенситных кристаллов и дисперсных карбидов. При температурах около 250°C происходит превращение карбида электрона в цементит begins. In в этом случае нарушается согласованность решетки твердого раствора и карбида. Если закаленная сталь содержит много остаточного аустенита, то уменьшение плотности при разложении больше, чем увеличение плотности за счет выделения углерода из расплава. martensite.
In этот случай(см. Рисунок 5. 29), длина затвердевшего образца увеличивается. 3-й конверсии. Она будет закончена. 5.29. Изменение содержания углерода в мартенсите при отпуске до 300°C Мартенситное разложение и Карбидное превращение. Весь пересыщенный углерод в виде карбидов высвобождается из мартенсита, тетрагональность решетки твердого раствора удаляется, и мартенсит переносится на феррит. После отпуска при температуре 380-400°C в стальных конструкциях можно обнаружить только карбиды cs-ментатита.
Оба этих процесса увеличивают плотность стали-длина образца уменьшается (см. Рисунок 5.29). Смеси феррита и карбида, образующиеся в конце третьего превращения, являются высокодисперсными и имеют почти такую же твердость, как и торутит(называемый темперирующим труститом).Стальная структура, сформированная при температуре первого и второго превращения, называется закалочным мартенситом. При высоких температурах в углеродистой стали происходят структурные изменения, не связанные с фазовым превращением.
Форма, размер и структура феррита карбида варьируются. В температурном диапазоне 3-го превращения цементит имеет форму гоночной пластины. При повышении температуры происходит затвердевание. Кристаллы цементита будут крупнее(мелкие кристаллы будут разрушаться, а крупные кристаллы расти).Тем временем форма кристалла постепенно приближается к сфероиду. Абляция коаи и сфероидизация карбидов происходят с поразительной скоростью, начиная с температуры 350-400°с. скорость этих процессов возрастает с увеличением температуры.
Изменения в структуре феррита обнаруживаются от температуры около 400°С. Очень высокая плотность дислокаций снижается в мартенсите перед отпуском, и граница между пластинчатыми кристаллами феррита постепенно устраняется, в результате чего частицы феррита становятся крупнее и ближе к Эквиоси по форме; поэтому при повышении температуры отпуска постепенно удаляются фазы затвердевания, которые происходят во время мартенсита. Смесь феррита и карбида, образующаяся после отпуска при температуре 450-650°с, называется отпускным сорбитом. После отпуска при температуре, близкой к Ат, образуется крупнозернистая ферритно-карбидная смесь-гранулированный перлит.
Влияние легирующих элементов на процесс отпуска. Многие легирующие элементы повышают температуру 2-го и 3-го превращения, снижая скорость затвердевания карбидов и влияя на превращение карбидов при отпуске. При легировании стали Cr, Mo, W, V, Co и Si предотвращается разложение мартенсита. При нагревании до температуры 450-500°с, разложение мартенсита завершается. Карбидообразующие элементы (Cr, Mo, W, V) снижают скорость диффузии углерода за счет его химического сродства с углеродом. Увеличьте Co и Si, которые не образуют карбидов в Стали, а также увеличьте большинство Карбидообразующих элементов!
Прочность межатомной связи твердого тела solution. As в результате этого сталь повышает сопротивление отпуску (термостойкость). В стали, содержащей большое количество карбидообразующих элементов, температура отпуска определяет тип карбидных осадков. При температурах до −400°с подвижность атомов легирующих элементов очень мала, поэтому вместо специального карбида*из мартенсита углеродистая сталь выделяет карбид железа, а для его образования необходима только миграция атомов углерода required.
At при более высоких температурах возможно образование специальных карбидов: цементирующих кристаллов o исчезают, а вместо них появляются специальные карбиды, которые более дисперсны. 1 специальное средство карбид, содержащий легирующие элементы. Многие легирующие элементы увеличивают температурный диапазон остаточной деструкции аустенита С 400°С до 580 ° с. C. In сталь с большим количеством карбидообразующих элементов, механизм разложения также changes.
At при температуре отпуска из аустенита осаждаются специальные карбиды, что снижает легирование аустенита и приобретает способность к превращению при охлаждении-при достижении температуры М начинается превращение аустенита в мартенсит. Все карбидообразующие элементы замедляют затвердевание карбида. Наиболее медленно затвердевают специальные карбиды типа M6C и MS, и при температурах, превышающих 550-600°C, происходит заметное расширение таких карбидов.
В зависимости от температурного диапазона принято различать 3 вида отпуска: низкий при 120-250°с, Средний при 350-450°с, Высокий при 500-680 ° с, Время выдержки устанавливается для обеспечения стабильности свойств стали. Если темперирование инструмента низкое, то оно зависит от площади поперечного сечения инструмента, продолжительность которого в большинстве случаев составляет 0,5-2 часа. Если температура низкого темперирования не превышает 100 120°С, то продолжительность темперирования увеличивается до 10-15 hours.
In в этом случае, например, при отпуске инструмента, когда снижение твердости нежелательно, такой длительный отпуск исключает изменение объема во время работы инструмента. Продолжительность среднего и высокотемпературного отпуска обычно составляет 1-2 часа для мелких деталей с площадью поперечного сечения и массой 2 (х) −1000 кг (3-8 часов для дисков газовой и паровой турбин, валов, кованых роторов турбин и других крупных деталей). )
Поскольку структура закаленной стали формируется в течение периода выдержки при температуре отпуска, прочность последующего охлаждения не влияет на структурное состояние стали. Обычно детали охлаждаются температурой праздника в спокойном воздухе. Рассмотрим закалку стали с дисперсной структурой перлита или бейнита. При охлаждении стали из аустенитной области со скоростью меньше gcr образуется сорбит, толуол или бейнит. Эти структуры часто формируются литьем, а также коваными, штампованными и сортовыми изделиями из легированной стали, охлаждаемыми на воздухе от температуры ковки и температуры деформации.
При нагревании до температуры ниже 4 происходит структурное изменение. То есть эти структуры тоже»освобождаются». При нагреве углеродистой стали с дисперсной перлитной структурой происходит затвердевание и сфероидизация карбида. Трансформация карбидов может происходить и в легированной стали: если образование специальных карбидов затруднено, если перлитная структура появляется при значительном переохлаждении аустенита (например, структура троос-Тита), если она закаляется при температуре от 600 до 700°С, то цементит превращается в специальные карбиды.
При отпуске бейнитной структуры, помимо указанного процесса, как и в случае отпуска мартенсита, из твердого раствора выделяется карбид, который изменяет структуру феррита. Характеристики закаленной стали. Твердость закаленной стали определяется несколькими факторами. Уменьшение Тетратональных свойств решетки, степени фазового упрочнения и расширения частиц карбида приводит к снижению твердости. Твердость повышается за счет осаждения когерентных электронных карбидных кристаллов и специальных карбидных дисперсных кристаллов, а также разложения остаточного аустенита.
В конструкционной стали, где содержание углерода обычно не превышает 0,7%, твердость непрерывно снижается, но при температуре 100-120 ° C падение составляет insignificant. In у инструментальных сталей с более высоким содержанием углерода эффект упрочнения доминирует за счет осаждения карбида С, поэтому твердость незначительно повышается при отпуске до 100-120°С. значительное изменение твердости углеродистой стали в температурном диапазоне вторичного превращения зависит от количества удерживаемого аустенита.
Например, для стали с содержанием от 200% до + 300°С в интервале температур 1,2% прочность падения твердости будет уменьшаться (рис. 5.30, i). Как и в случае с углеродистой сталью, твердость изменяется за счет отпуска низколегированных и среднелегированных сталей, содержащих карбидообразующие легирующие элементы. Сильное образование карбида^ель Рис. 5.30.
Изменение твердости закаленной стали при отпуске: а-углеродистая сталь; б — высоколегированная сталь X12 (2% C, 12% Cg), закалочная от 950°C и P18 (0,75% C, 18% W, 4% Cg, 1D% V), закалочная от 1260°C Вследствие возникновения выделения карбида железа твердость несколько снижается при температурах отпуска до 400-500°с (рис.5.30. 6). при температурах, при которых осаждаются специальные карбиды, диспергированные в композитных легированных сталях (Cr-W-V, Cr-Mo-V и др.), увеличение твердости происходит даже при снижении содержания углерода в мартенсите.
Увеличение твердости стали, в том числе хрома, вольфрама (молибдена) и ванадия, соответствует температуре 500-560°С. Для закаливания и отпуска Отличительной особенностью этой стали является достаточно низкое значение Св, предела прочности при растяжении и текучести. Отпуск до 300°C повышает эти прочностные характеристики. При дальнейшем повышении температуры отпуска предел упругости и предел текучести монотонно уменьшаются. Наибольшее соотношение o2 / s в конструкционной стали достигается после отпуска при 300-350°C (рис.5.31).
Характеристики пластичности 6 и V возрастают с увеличением температуры отпуска (см. рис. 5.31).Ударная прочность 5.31.Влияние температуры на механические свойства конструкционной углеродистой стали (0,45% C) Рис. 5.32.Влияние температуры отпуска и скорости охлаждения на вязкость конструкционной легированной стали (рис.): / — Сбросить хрупкость первого вида; II-11-уязвимость характера Ванна есть low. As температура отпуска увеличивается, прочность увеличивается, но есть 2 диапазона температур, в которых прочность конструкционной стали значительно снижается.
250-350 и 500-600°С. снижение вязкости, соответственно, называют закалкой хрупкости 1-го и 2-го видов (рис. 5.32).Характер охрупчивания стали после отпуска при заданных температурах недостаточно ясен. Снижение ударной вязкости после отпуска при 250-350 СС наблюдается во всех конструкционных сталях, независимо от степени легирования. Значительное снижение ударной вязкости после отпуска при 500-600°С наблюдается только в легированных конструкционных сталях типа хрома, марганца, хромоникеля и хромомангана.
При быстром охлаждении от температуры темперирования (в воде или в масле) практически не происходит снижения вязкости. Хрупкость отпуска типа 2 заметно подавляется даже медленным охлаждением от температуры отпуска путем легирования стали молибденом или вольфрамом в количестве 0,3 и 1% соответственно. Комплексная термическая обработка, состоящая из полного упрочнения конструкционной стали и высокотемпературного отпуска, называется улучшением.
Смотрите также:
Материаловедение — решение задач с примерами