
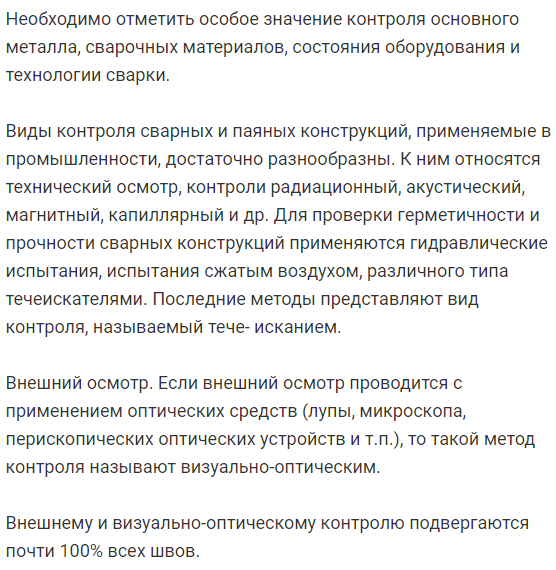
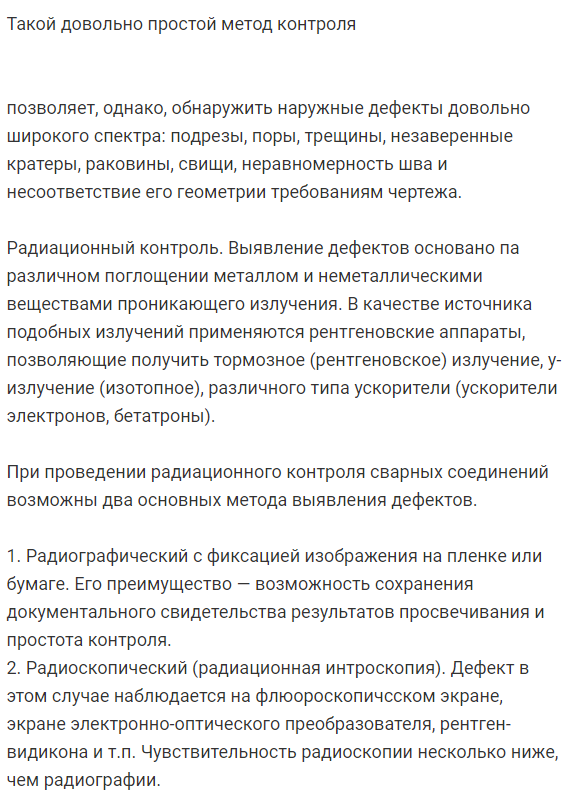
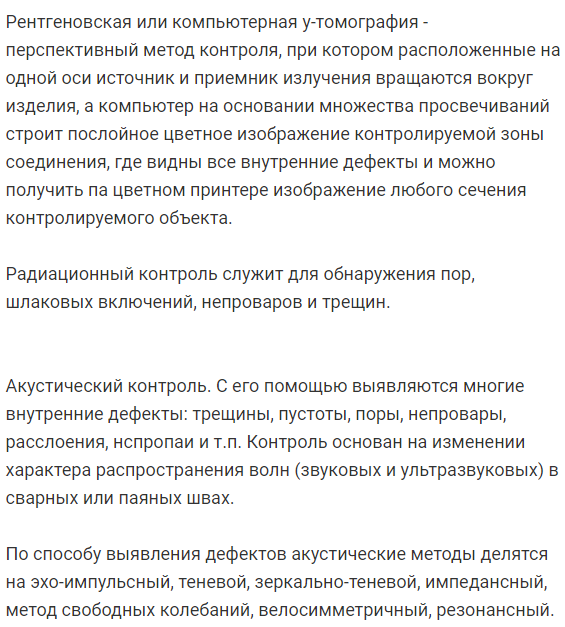
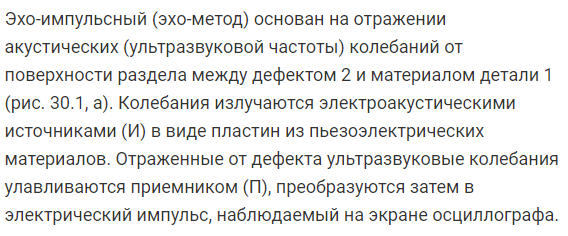
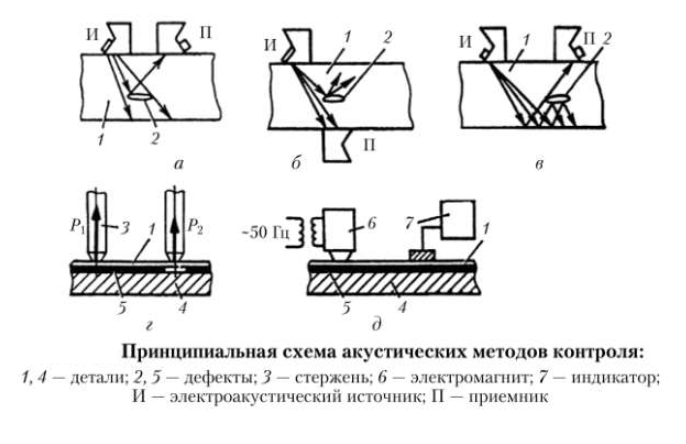
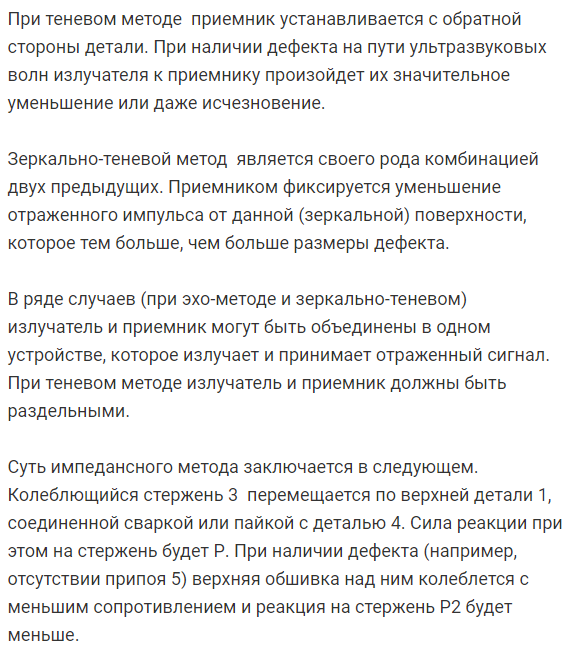
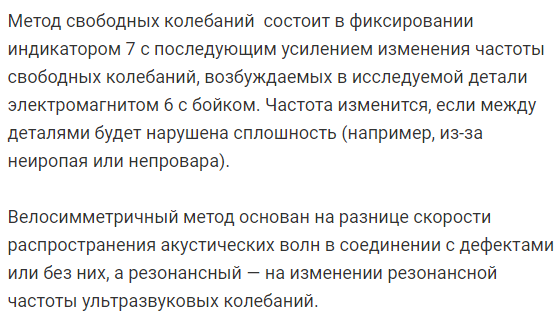
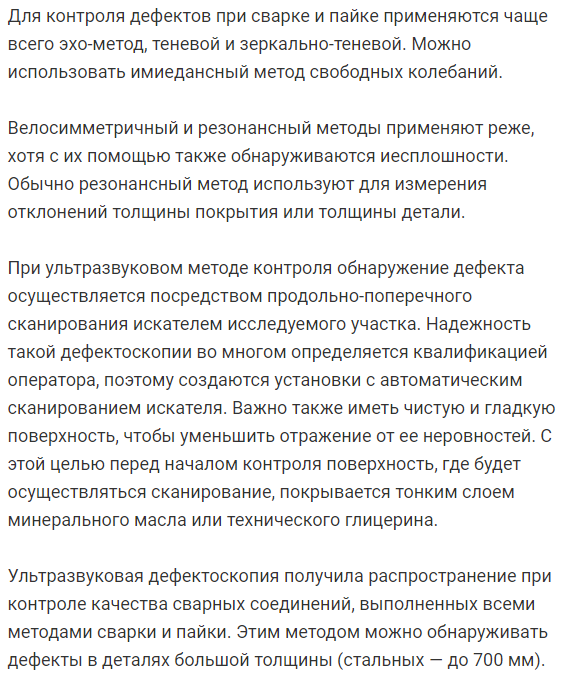
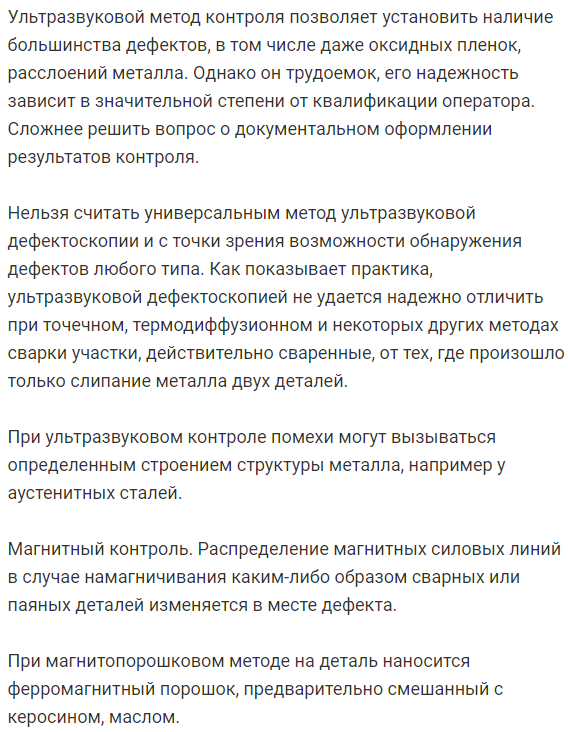
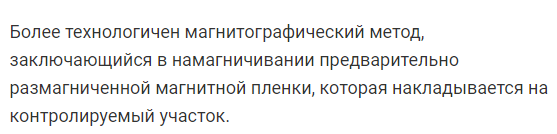
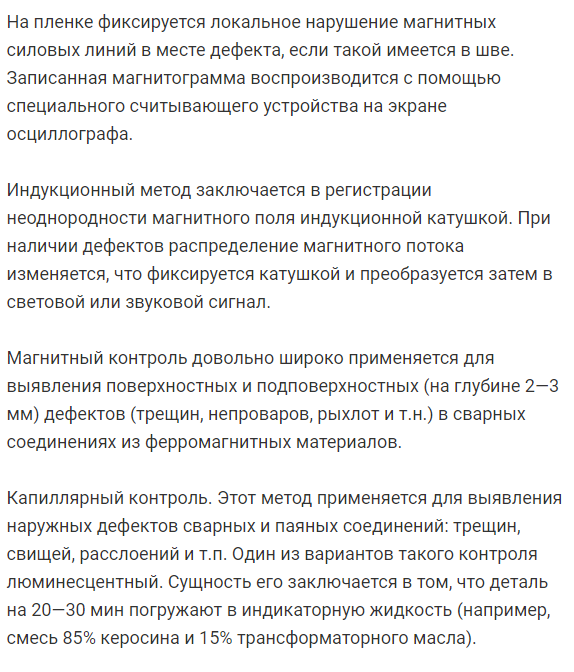
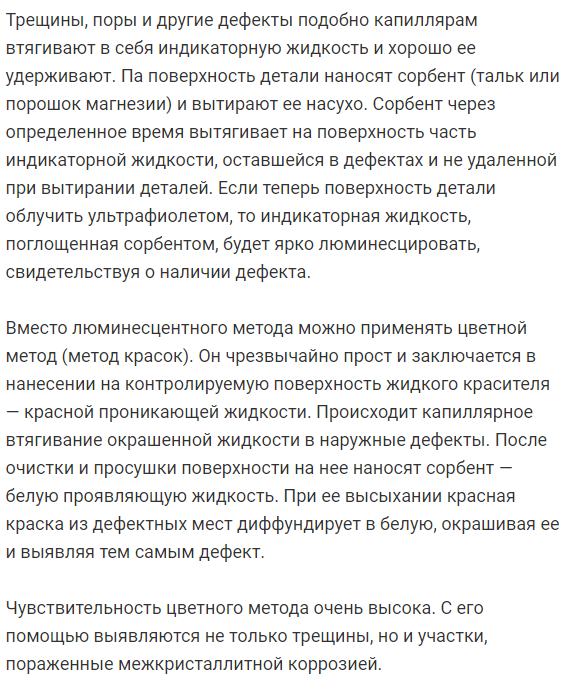
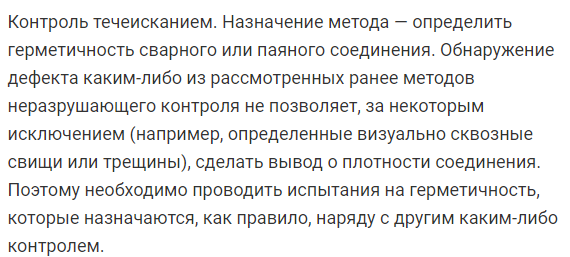
Существует два типа методов контроля: разрушительный и неразрушающий.
Разрушающее испытание включает в себя проверку сварных образцов. Они свариваются при тех же условиях, что и изделие, обычно непосредственно перед сваркой изделия. Комплексное испытание образца может косвенно определить качество сварного соединения изделия.
Поведение при нагрузке сварных соединений модельной структуры или самого продукта может быть воспроизведено более точно, и они выборочно подвергаются испытаниям до отказа. Необходимое количество разрушаемых изделий со стороны устанавливается дизайнером в каждом конкретном случае.
Неразрушающие методы контроля включают в себя мониторинг параметров состояния сварки, некоторые испытания свойств сварного шва без разрушения сварного шва (например, измерение твердости, химического состава металла сварного шва без влияния на целостность конструкции). Анализ) и, наконец, методы физического контроля (обнаружение дефектов).
Необходимо обратить внимание на особую важность контроля основного металла, сварочного материала, состояния оборудования и техники сварки.
Виды контроля сварочных и паяных конструкций, используемые в промышленности, очень разнообразны. К ним относятся технический осмотр, контроль радиации, акустики, магнетизма, капилляров и т. Д., А также гидравлические испытания, испытания сжатым воздухом, а также различные типы течеискателей используются для проверки герметичности и прочности сварных конструкций. Будет. Последний метод представляет собой форму контроля, называемую обнаружением утечки.
Внешний осмотр. Когда внешний осмотр выполняется с использованием оптических средств (увеличительное стекло, микроскоп, оптика перископа и т. Д.), Этот метод контроля называется визуальной оптикой.
- Почти 100% всех швов подвергаются внешнему и визуальному контролю оптики.
- Такой довольно простой метод управления
Однако он может обнаруживать довольно широкий спектр внешних дефектов, таких как подрезы, поры, трещины, кратеры без трещин, раковины, свищи, неоднородные швы и несоответствия между их формой и требованиями к вытяжке.
Радиационный контроль. Обнаружение дефектов основано на различном поглощении проходящего излучения металлическими и неметаллическими материалами. Рентгеновское оборудование может быть использовано в качестве такого источника излучения для получения тормозного (рентгеновского) излучения, гамма-лучей (изотопов) и различных типов ускорителей (ускорители электронов, бетатроны).
При проведении радиационного контроля сварных соединений возможны два основных метода обнаружения дефектов.
- Сделайте рентгенограмму с изображениями, закрепленными на пленке или бумаге. Его преимущество в том, что он сохраняет документацию о результатах передачи и прост в управлении.
- Радиоскопия (рентгеноскопия). В этом случае дефекты наблюдаются на экранах рентгеновской флюороскопии, экранах электрооптических преобразователей, рентгеновских видиконах и т. Д. Чувствительность рентгенологического исследования несколько ниже, чем у рентгенографии.
Рентген или компьютерная томография является многообещающим методом контроля, при котором источник и приемник излучения находятся на одной оси, вращающейся вокруг изделия, а компьютер расположен в контролируемой зоне соединения на основе большой прозрачности. Создайте цветное изображение. Изображение любого раздела для управления.
Радиационный мониторинг используется для обнаружения пор, загрязнения шлака, отсутствия проникновения и трещин.
Акустический контроль. С его помощью выявляются многие внутренние дефекты: трещины, пустоты, поры, отсутствие проникновения, расслоение, отсутствие сварки и так далее. Этот контроль основан на изменениях характера распространения волн (звука и ультразвука) в сварных или паяных швах.
- В соответствии с методом обнаружения дефектов акустические методы подразделяются на эхо-импульсы, тени, зеркальные тени, импеданс, свободные колебания, симметрию цикла и резонанс.
Импульсное эхо (метод эха) основано на отражении акустической (ультразвуковой частоты) вибрации от границы раздела между дефектом 2 и материалом детали 1 (рис. 30.1, а). Вибрация излучается электроакустическим источником (I) в виде пластины из пьезоэлектрического материала.
Отраженная от дефекта ультразвуковая вибрация регистрируется приемником (P), преобразуется в электрические импульсы и регистрируется на экране осциллографа. В теневом методе приемник прикрепляется к задней части детали. Если ультразвуковой путь от излучателя к приемнику неисправен, они значительно уменьшаются или даже исчезают.
Метод зеркальной тени является своего рода предыдущими двумя методами. Приемник корректирует уменьшение отраженных импульсов от определенной (зеркальной) поверхности.
Это увеличивается с увеличением размера дефекта.
В некоторых случаях (с использованием эхо и зеркальных теней) излучатель и приемник могут быть объединены в одно устройство для отправки и приема отраженного сигнала. В теневом методе необходимо разделить излучатель и приемник.
Суть метода импеданса заключается в следующем. Вибрационный стержень 3 движется вдоль верха 1, соединенного с верхом 4 сваркой или пайкой. Силой реакции на стержень является П. Меньше, если есть дефект (например, если нет припоя 5).
Способ свободной вибрации заключается в прикреплении индикатора 7 и усилении изменения частоты свободной вибрации, возбуждаемой электромагнитом 6, снабженным ударником. Когда непрерывность между частями теряется, частота изменяется (например, потому что она не спаяна или не проникла).
Методы симметрии велосипедов основаны на различиях в скорости распространения акустических волн с дефектами и без них, а резонансные методы основаны на изменениях резонансной частоты ультразвуковых колебаний. Эхо-тени и зеркальные тени чаще всего используются для контроля дефектов во время сварки и пайки. Можно использовать метод колебаний без импеданса.
Методы симметрии скорости и резонанса используются редко, но также обнаруживаются разрывы. Резонансный метод обычно используется для измерения толщины покрытия или отклонений толщины компонента.
В методе ультразвукового контроля дефекты обнаруживаются путем вертикального и горизонтального сканирования с использованием видоискателя в зоне исследования. Надежность такого обнаружения дефектов определяется, прежде всего, квалификацией оператора, поэтому установка создается с помощью автоматического поиска искателя. Также важно иметь чистую и гладкую поверхность, чтобы уменьшить отражения от неровностей. Для этого сканируемая поверхность перед началом контроля покрывается тонким слоем минерального масла или промышленного глицерина.
- Ультразвуковая дефектоскопия широко используется для контроля качества сварных соединений, выполненных всеми методами сварки и пайки. Этот метод может обнаружить дефекты в толстых деталях (сталь до 700 мм).
Ультразвуковой контроль может подтвердить наличие большинства дефектов, таких как оксидная пленка и отслаивание металла. Однако это требует времени, и его надежность в значительной степени зависит от навыков оператора. Сложнее решить проблему документирования результатов контроля.
Ультразвуковая дефектоскопия не считается универсальной с точки зрения возможности обнаружения всех типов дефектов. Как показывает практика, ультразвуковой контроль не может надежно отличить пятна, термодиффузию и другие методы сварки.
При ультразвуковом контроле помехи могут быть вызваны некоторыми структурами металлических конструкций, такими как аустенитная сталь.
Магнитный контроль. Распределение силовых линий магнитного поля в случае намагничивания сваренных или припаянных частей в той или иной мере изменяется в месте расположения дефекта.
В методе магнитных частиц ферромагнитный порошок, смешанный с керосином и маслом, наносится на детали заранее.
Более технологичный метод магнитной записи, который заключается в намагничивании предварительно размагниченной магнитной пленки, наложенной на контролируемую область. На пленке локальные нарушения силовых линий магнитного поля на дефектах обнаруживаются в шве. Записанная магнитограмма воспроизводится с помощью специального считывателя на экране осциллографа.
Индукционный метод заключается в регистрации неоднородности магнитного поля с помощью индукционной катушки. При наличии дефектов распределение магнитного потока изменится. Это фиксируется катушкой и преобразуется в световой или звуковой сигнал.
Магнитный контроль широко используется для обнаружения дефектов (трещин, дефектов, ослабления и т. Д.) На поверхности и под поверхностью (глубина 2-3 мм) сварных соединений из ферромагнитных материалов.
Капиллярный контроль. Этот метод используется для обнаружения внешних дефектов в сварных швах и паяных соединениях: трещин, отверстий, расслоения и т. Д. Одним из таких вариантов управления является люминесцентный. Суть состоит в том, чтобы погрузить деталь в индикаторную жидкость (например, 85% керосина и 15% трансформаторного масла) на 20-30 минут.
Другие дефекты, такие как трещины, поры и капилляры, притягивают индикаторный раствор и крепко его удерживают. Нанесите адсорбент (тальк или порошок магнезии) на поверхность деталей и вытрите насухо. Через некоторое время адсорбент оставляет дефект на поверхности и вытягивает часть индикаторного раствора, которая не удаляется при протирании детали.
Когда поверхность компонента облучается ультрафиолетовым светом, индикаторная жидкость, поглощенная адсорбентом, излучает яркий свет, что указывает на наличие дефектов.
Цветной метод (метод краски) может использоваться вместо метода эмиссии света. Это очень просто и состоит из нанесения жидкого красителя, красного пенетранта на контролируемую поверхность. Цветная жидкость втягивается во внешние дефекты капиллярами. После того, как поверхность вымыта и высушена, наносится адсорбент (белый проявитель). После высыхания красная краска из дефектной области рассеивается на белый и окрашивает ее, чтобы выявить дефект.
Чувствительность цветового метода очень высокая. С этой помощью обнаруживаются не только трещины, но и зоны, подверженные межкристаллитной коррозии.
- Обнаружение утечки Целью этого метода является определение герметичности сварных или паяных соединений. Обнаружение дефектов с помощью любого из ранее рассмотренных методов неразрушающего контроля не позволяет сделать вывод о том, что соединение является надежным, за некоторыми исключениями (например, некоторые визуальные эффекты через свищи и трещины) , Поэтому необходимо провести испытание на утечку. Тесты на утечку в принципе назначаются с другими контролями.
Смотрите также:
Примеры решения задач по материаловедению
Назовите основные параметры режима резания при фрезеровании и типы образующихся стружек. | Инструментальные стали. |
Прямое и обратное прессование. | Основные этапы технологического процесса пайки. |