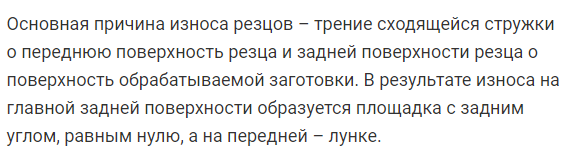
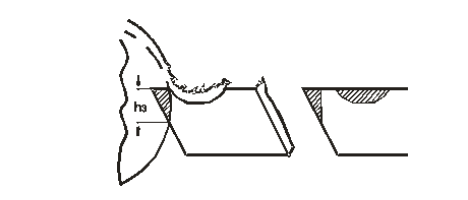
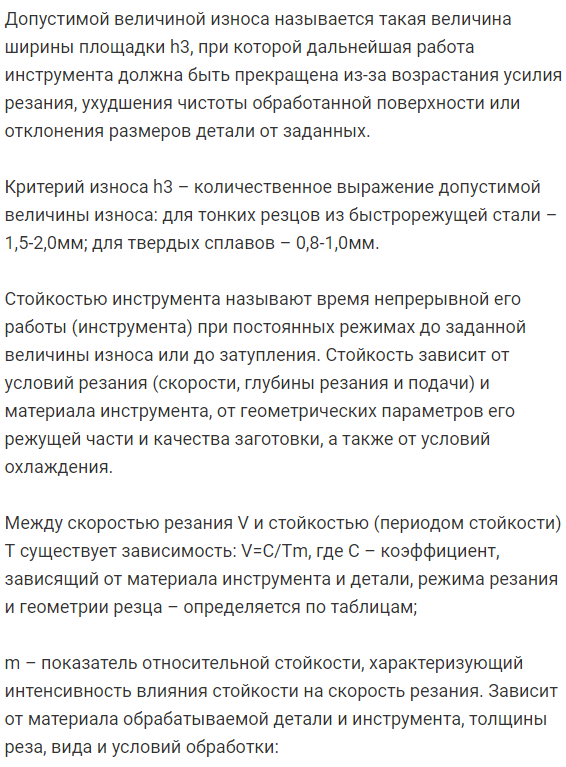
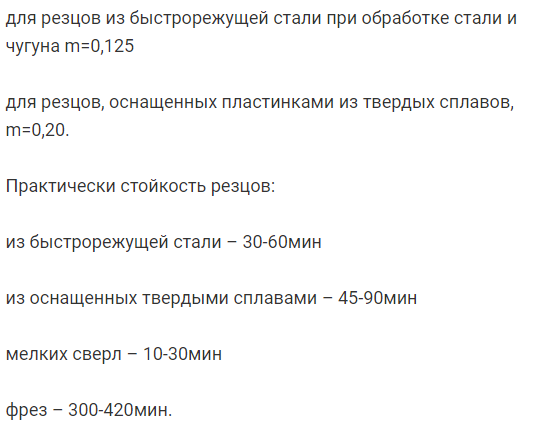
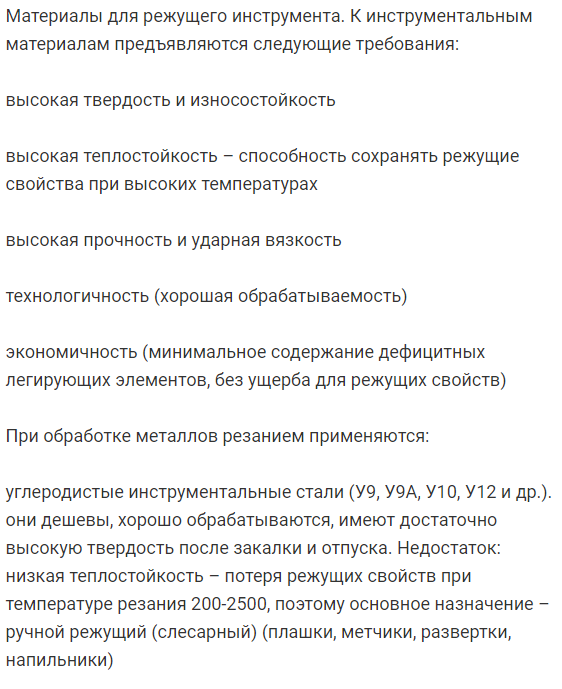
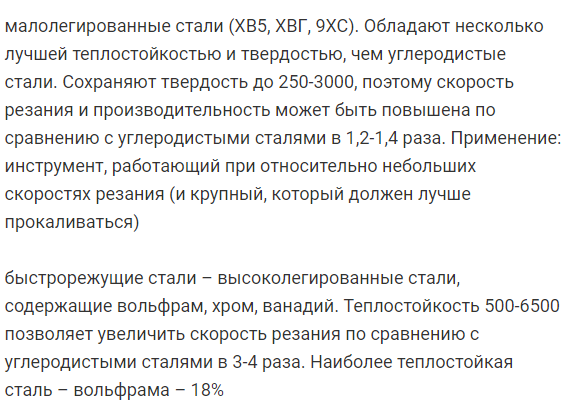
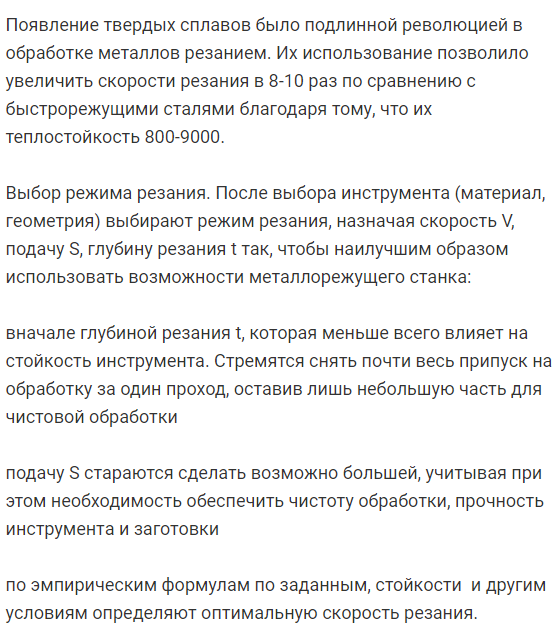
Основными причинами износа фрезы являются сходящийся наконечник на передней части фрезы и трение на задней части фрезы на поверхности заготовки. В результате износа на основной задней поверхности образуется платформа с задним углом, равным нулю, а на передней поверхности — отверстие.
Допустимый уровень износа — это размер ширины h3 платформы, при котором дальнейшее движение инструмента останавливается из-за повышенного сопротивления резанию, пониженной чистоты обрабатываемой поверхности или отклонения размеров детали от этого набора. это.
Норма износа h3- Количественное выражение допустимого износа: -1,5-2,0 мм для тонких резцов из быстрорежущей стали. -0,8-1,0 мм для твердых сплавов.
Долговечность инструмента называется временем непрерывной работы (инструмента) при определенной степени износа или в унылых условиях. Сопротивление зависит от условий резания (скорость, глубина резания и подача) и материала инструмента, геометрических параметров режущей части, качества заготовки и условий охлаждения.
Существует зависимость между скоростью резания V и сопротивлением (цикл сопротивления) T: V = C / Tm, где C — это коэффициент, который зависит от материала инструмента и детали, режима резания, геометрии резца, определяемой таблицей ;
m является показателем относительного сопротивления и характеризует силу влияния сопротивления на скорость резания. Зависит от заготовки и материала инструмента, толщины резания, типа и условий обработки.
- M = 0,125 для высокоскоростных стальных резцов при обработке стали и чугуна
- Для резцов с твердосплавными пластинами m = 0,20.
- Практическая долговечность резцов:
- -30-60 минут из быстрорежущей стали
- От -45 до 90 минут при использовании твердого сплава
- Маленькая тренировка -10-30 минут
- Фрезер-300 ~ 420 минут.
Материал режущего инструмента. К материалам оборудования предъявляются следующие требования:
- Высокая твердость и износостойкость
Высокая термостойкость — способность сохранять режущие свойства при высоких температурах
- Высокая прочность и прочность
- Технологичность (хорошая обрабатываемость)
- Рентабельность (минимальное содержание редких легированных элементов без ухудшения режущих свойств)
Они используются при резке металла:
- Углеродистая инструментальная сталь (U9, U9A, U10, U12 и др.). Они недороги, хорошо обработаны и имеют достаточно высокую твердость после отверждения и отпуска. Недостатки: низкая теплостойкость — характеристики резки теряются при температурах резания 200-2500, поэтому основным назначением является ручная резка (обработка металла) (матрица, метчик, развертка, напильник)
Низколегированная сталь (ХВ5, ХВГ, 9ХС). Они имеют немного лучшую теплостойкость и твердость, чем углеродистая сталь. Поскольку он сохраняет твердость до 250-3000, скорость резания и производительность улучшаются в 1,2-1,4 раза по сравнению с углеродистой сталью. Применение: Инструменты, которые работают на относительно низких скоростях резания (и большие инструменты, которые требуют лучшего прокаливания)
Быстрорежущая сталь — высоколегированная сталь, содержащая вольфрам, хром и ванадий. С жаростойкостью 500-6500, скорость резания в 3-4 раза выше, чем у углеродистой стали. Самая жаростойкая сталь-вольфрам-18%
- Хром — ~ 4%
- Ванадий — до 1,5%.
- Другая сталь этого типа — P12.
- Быстрорежущая сталь также используется: с ванадием -R9F5, R14FU
- Доступны кобальт-P9K5, P9K10 (в 4–4,5 раза выше сопротивления P18)
- -R6M5K8, содержащий молибден и кобальт и др.
Твердые сплавы Cermet (полученные спеканием) основаны на WC из карбида вольфрама, TiC титана и TaC тантала, которые соединены кобальтовой связью.
Наиболее часто используемые сплавы — это ВК8, ВК6, ВК4 и ВК2 (на рисунке показано содержание кобальта).
Появление твердых сплавов стало настоящей революцией в резке металлов. Их использование позволило увеличить скорость резания в 8-10 раз по сравнению с быстрорежущей сталью благодаря тому, что термостойкость составляет 800-9000.
Выберите режим резки. После выбора инструмента (материал, форма) выбирается режим резания и назначаются скорость V, подача S, глубина резания t, и функции металлорежущего станка могут быть полностью использованы.
- Сначала используйте глубину резания t. Это оказывает наименьшее влияние на срок службы инструмента. Они стремятся устранить почти все припуски на обработку за один проход, оставляя только мелкие детали для чистовой обработки.
Они пытаются максимально увеличить подачу S, принимая во внимание необходимость обеспечения чистой обработки, прочности инструмента и заготовки.
Определите оптимальную скорость резания в соответствии с эмпирической формулой для заданных S, t, сопротивления T и других условий где коэффициенты с учетом обрабатываемых материалов, инструментальных материалов и условий обработки (приведены в таблице).
Смотрите также:
Примеры решения задач по материаловедению