Оглавление:
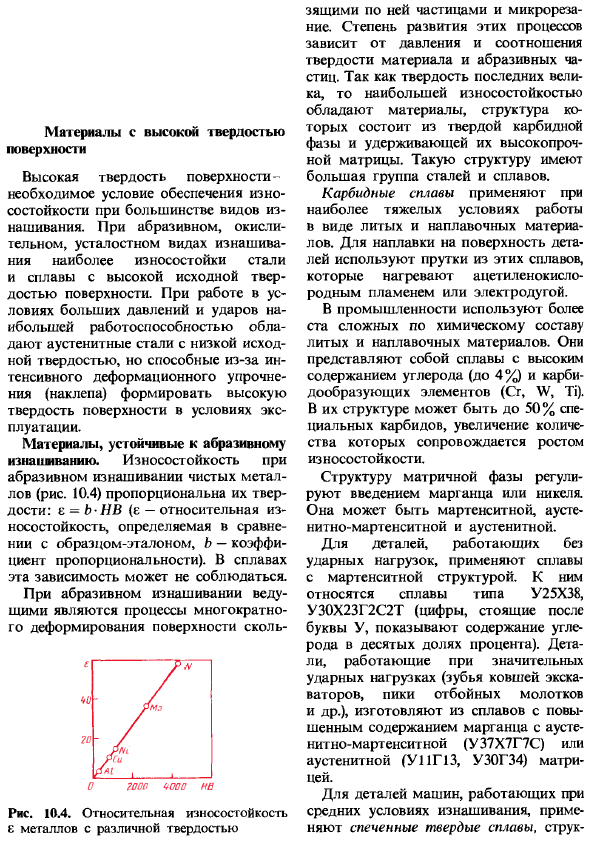
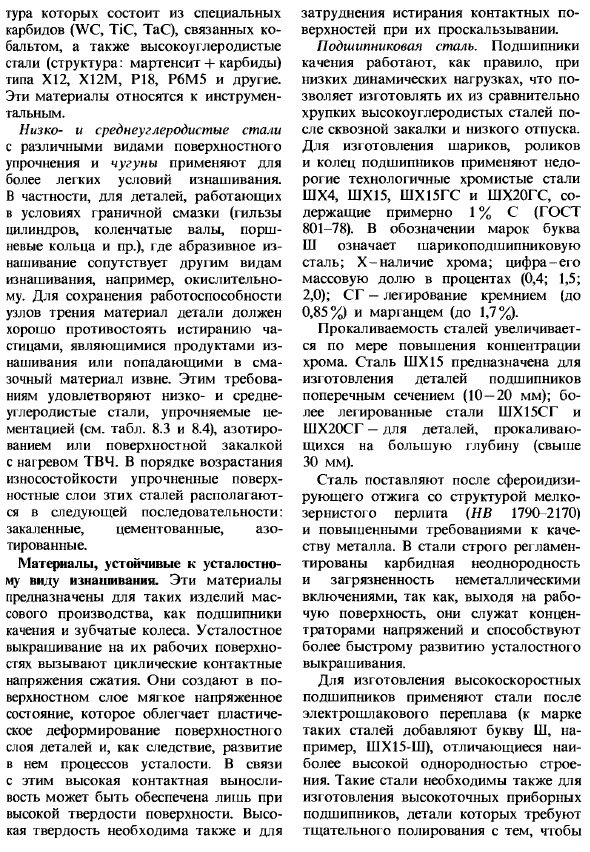
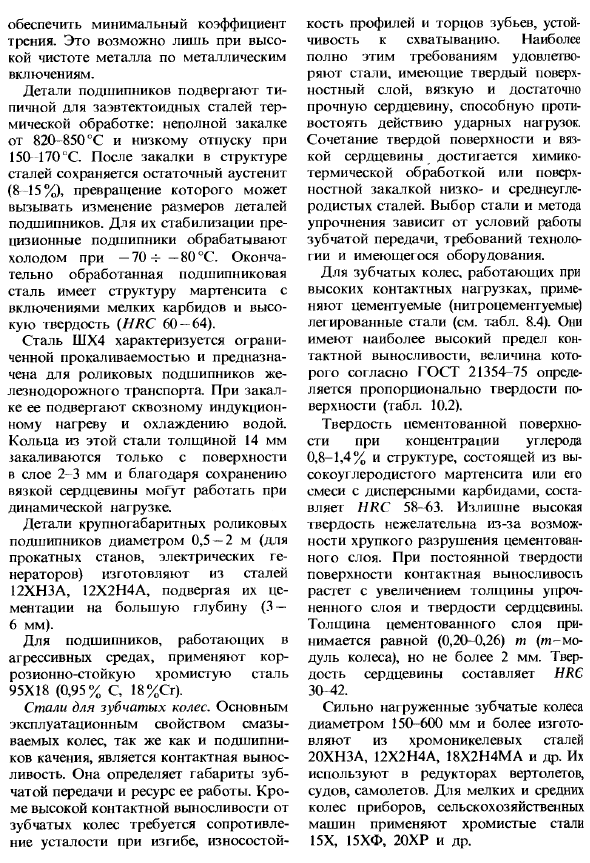
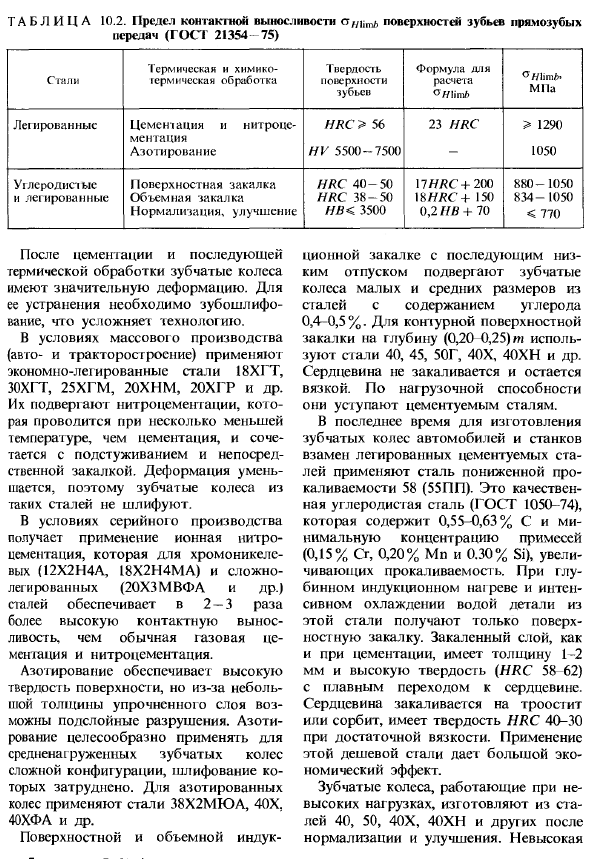
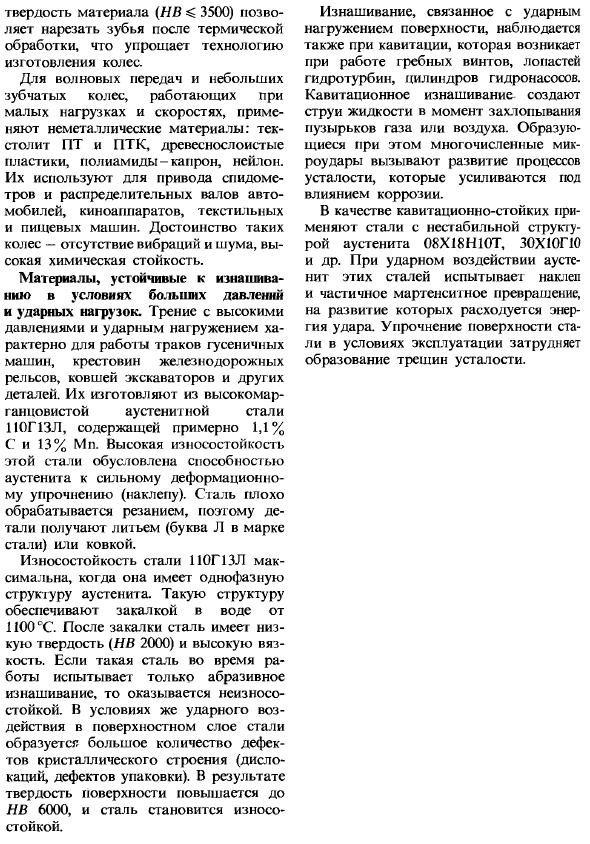

Материалы с высокой твердостью поверхности
- Материал высокой твердости Высокая поверхностная твердость является необходимым условием для обеспечения износостойкости большинства типов wear. In абразивный, окислительный и усталостный износ, наиболее износостойкие стали и сплавы с наибольшей начальной поверхностной твердостью являются наиболее износостойкими.
При работе в условиях повышенного давления и ударного воздействия аустенитные стали с наименьшей начальной твердостью могут формировать высокую поверхностную твердость в условиях эксплуатации за счет интенсивного деформационного упрочнения (закалки), приводящего к наибольшему КПД. Износостойкий материал. Износостойкость чистого металла при абразивном изнашивании(рис. 10.4) пропорциональна его твердости: e = L ’HB (e-относительная износостойкость и определяется в сравнении с эталонным образцом, не наблюдаться.
b-коэффициент пропорциональности).в сплавах эта зависимость может Людмила Фирмаль
Для абразивного износа основным процессом является многократная деформация поверхности Рис. 10.4.Относительная износостойкость Твердость различного е-металла Частицы и микро-вырезывание на ем. Степень развития этих процессов зависит от соотношения давления и твердости материала и абразивных частиц. Благодаря большой твердости последних, материал с самой высокой карбидной фазой и высокой прочностью матрицы, удерживающей их, имеет наибольший износ resistance. In таких конструкций существует большая группа из стали и сплавов. Карбидные сплавы применяются в самых сложных условиях эксплуатации в виде литейных и поверхностных материалов.
Используя эти стержни сплава, нагретые ацетиленовым пламенем или электрической дугой, они появляются на поверхности детали. В промышленности используется химический состав отливок и поверхностных материалов более 100 complexes. It представляет собой сплав, содержащий высокое содержание углерода (до 4%) и Карбидообразующих элементов (или, W, Ti).В их структуре может содержаться до 50% специальных карбидов, увеличение их количества сопровождается повышением износостойкости. Структура фазы матрицы регулируется введением марганца или nickel. It может быть мартенсит, аустенит-мартенсит и аустенит.
Для деталей, работающих без ударных нагрузок, используются мартенситные сплавы. К ним относятся сплавы типа U25X38, U30X23G2S2T (на рисунке после буквы U указано содержание углерода в 10 процентах за 1 минуту).Работа при больших ударных нагрузках (зубья ковша экскаватора, скальные сваи и др.), дегаль изготовлен из высокомарганецсодержащих сплавов, включая аустенитный мартенсит (U37X7G7S) или аустенитный (U11G13, U30G34) матрик. Детали машин, работающих в условиях умеренного износа, из спеченных сплавов, для конструкций Его тур состоит из специальных карбидов (WC, TiC, TaC), связанных с кобальтом, и высокоуглеродистых сталей (структура: мартенсит+карбиды) типа X12, X12M, P18, P6M5 и др.
Эти материалы полезны. Для более сильного износа применяют низкоуглеродистые и среднеуглеродистые стали с различными видами поверхностного упрочнения и чугун conditions. In в частности, абразивный износ связан с другими видами износа (например, окислительный износ) деталей, работающих в условиях граничной смазки (например, гильзы цилиндров, коленчатые валы, поршневые кольца и т. д.). Для поддержания работоспособности узла трения материал детали должен быть достаточно устойчив к износу частицами, являющимися продуктами износа,
а также частицами, входящими в смазку извне. Людмила Фирмаль
Эти требования удовлетворяются цементацией (см. таблицы 83 и 8.4), азотированием или низкоуглеродистой и среднеуглеродистой сталью, закаленной поверхностным упрочнением с нагревом высокой частоты alloys. To повышая износостойкость, упрочненные поверхностные слои этих сталей раскладывают в следующем порядке: закаленные, цементированные, азотированные. Материал устойчив к усталостному износу. Эти материалы предназначены для массового производства таких изделий, как подшипники качения и шестерни. Периодическое контактное сжимающее напряжение возникает из-за усталостного расслоения рабочей поверхности. Они создают мягкое напряженное состояние в поверхностном слое и способствуют пластической деформации поверхности!
О развитии слоев детализации и результирующем процессе fatigue. In в связи с этим высокая контактная прочность может быть достигнута только при высокой поверхностной твердости. Высокая твердость также необходима Износ контактной поверхности затруднен при скольжении контактной поверхности. Подшипниковая сталь. Подшипники качения обычно работают при низких динамических нагрузках, поэтому они изготавливаются из относительно хрупкой высокоуглеродистой стали путем закалки и низкого отпуска.
Шариков, роликов и колец подшипников производства используется примерно 1% с (ГОСТ 801-78), включая дешевые технологии хромовой стали ШХ4,ШХ15,ШХ15ГС и ШХ20ГС это. В обозначении марок буква Ш означает шарикоподшипниковой стали. Х-наличие хрома. Цифра представляет собой процентную массовую долю (0,4; 1,5; 2,0). SG-легирование кремния (до 0,85%) и марганца (до 1,7%). Чем выше концентрация хрома, тем лучше прокаливаемость стали. Стальшх15 предназначена для изготовления несущих деталей с площадью поперечного сечения (10-20 мм).Еще легированные стали Шх15сг и Шх20сг-для деталей, прокаленных вглубь (более 30 мм).
Сталь поставляется после сфероидизирующего отжига в мелкозернистых перлитных структурах (HB 1790 2170), повышая требования к качеству metal. In сталь платная, неоднородность карбидов и загрязнение неметаллическими включениями цементируются. Это связано с тем, что когда они выходят на рабочую поверхность, то действуют как концентратор напряжений, что способствует более быстрому развитию усталостного шелушения. При изготовлении быстроходных подшипников сталь используют после добавления электрошлакового переплава (II-подобный характер Ш, например, II1X15-III) к сорту стали, который характеризуется наибольшей структурной однородностью.
Такая сталь также необходима для изготовления высокоточных измерительных подшипников, детали которых требуют тщательной полировки для минимизации коэффициента трения. Это возможно только с высокочистыми металлами, которые содержатся в металлических включениях. Подшипник компоненты проходят типичный термообработки на за-эвтектоидная сталь.820850 ° C с неполным отверждением от 150 170″C. In низкий темперировать. После упрочнения в стальной конструкции сохраняется остаточный аустенит(8-15%), деформация которого может привести к изменению размеров подшипника parts.
To стабилизируя их, прецизионные подшипники обрабатываются при низкой температуре −70 −80°С. готовая обработанная подшипниковая сталь имеет мартенситную структуру, включающую мелкие карбиды и высокую твердость (HRC 60-64). Сталь ШХ4 имеет ограниченную закалочную способность и предназначена для роликовых подшипников в железнодорожном транспорте. При тушении он обрабатывается индукционным нагревом и охлаждением водой. Кольца этого изделия толщиной 14 мм затвердевают только в слое 2-3 мм от поверхности и служат под динамическими нагрузками, так как вязкая сердцевина сохраняется.
Большие роликовые подшипники диаметром 0,5-2 м (для прокатных станков, генераторов) детали изготавливаются из стали 12хнза, 12×2н4а, с глубиной залегания (3-6 мм) цемента. Используйте коррозионностойкую хромистую сталь 95X18 (0,95% C, 18%Cg)для подшипников, работающих в жестких условиях эксплуатации. Сталь для Gears. As с подшипниками качения основным эксплуатационным свойством смазочного колеса является прочность контакта. Определить размеры шестерни и ресурс работы. Помимо высокого контакта Зубцы должны быть устойчивы к изгибу усталости и износу Установите профиль кости и края зуба, сопротивление.
Наиболее полным соответствием этим требованиям являются изделия с твердым поверхностным слоем, вязким и достаточно прочным сердечником, способным выдерживать действие ударных нагрузок. Сочетание твердой поверхности и вязкой сердцевины осуществляется путем химической герметизации или поверхностного упрочнения низкоуглеродистых и среднеуглеродистых изделий. Выбор продукта и способа упрочнения зависит от условий эксплуатации зубчатой передачи, требований технологии и имеющегося оборудования.
Для зубчатых колес, работающих с высокой контактной нагрузкой, используется цементная (Нитроцементная) легированная сталь (см. таблицу 8.4).Они имеют самые высокие пределы контактной выносливости, и согласно ГОСТ 21354-75 их значения определяются пропорционально твердости поверхности (таблица 10.2). HRC 58-63 обеспечивает твердость соединительных поверхностей в конструкциях, состоящих из концентрации углерода от 0,8 до 1,4% и смеси, диспергированной с высокоуглеродистым мартенситом или карбидом. Чрезмерно высокая твердость нежелательна из-за возможности хрупкого разрушения цементного слоя.
При определенной поверхностной твердости прочность контакта увеличивается по мере увеличения толщины упрочненного слоя и твердости сердцевины. Толщина цементного слоя будет равна (0,20 0,26) Т (Модуль zn колеса), но не более 2 мм. Твердость сердцевины составляет HRC 30-42. Шестерни с массой более 150 600 мм в диаметре изготавливаются из хромоникелевой стали 20хнза, 12×2н4а, 18Х2Н4МА и др. и используются в редукторах вертолетов, кораблей и самолетов. Для малых и средних колес устройства, сельскохозяйственной техники, хромистой стали 15Х, 15ХФ, 20ХР и др. не использовать.
После цементировать и последующей термической обработки, шестерня значительно будет deform. To избавляясь от него, необходимо шлифовать шестеренки, что усложняет технологию. Таблица 10.2.Предел контактной выносливости зуба цилиндрической шестерни (ГОСТ 21354 75) Стальная жара и химическая герметичная твердость поверхности обработки 3) Формула 6лкбмпа Сплав цемента и мягкого азотирования HRC> 56 N V 5500-7500 23 HRC> 1290 1050 Закаленные объема из углеродистых и легированных 11 нормализуется, улучшается НRС 40-50 НRС. 38-50 3500 VJ HRC + 200 WHRC + 150 0.2 LH + 70 880-1050 834-1050 <770 В условиях массового производства (автоматическое и тракторное производство) используются экономически легированные стали 18ХГТ, ЗОХГТ, 25ХГМ, 20ХНМ, 20ХГР и др.
Шестерни, изготовленные из такой стали, не полируются, так как уменьшается деформация. В условиях массового производства науглероживание методом ионного азотирования является used. It обеспечивает стойкость контакта 2 до 3 времен против никеля Хромия (12X2H4A, 18X2H4MA) и составного сплава (20X3 IMF A, etc.) Стали. Чем обычный газ обуглероживая или мягкое азотирование. Азотирование обеспечивает высокую поверхностную твердость, но из-за малой толщины упрочненного слоя может произойти разрушение подслоя. Азотирование рекомендуется для винтовочных снастей среднего калибра со сложными конфигурациями, которые трудно полировать.
Для азотирующего колеса используются 38Х2МЮА, 40х сталь. 40хфа и так далее. Поверхностные и объемные индукторы Малые и средние зубчатые колеса из стали с содержанием углерода 0,4-0,5% после закалки закаляются низко. (0.20 0.25) глубина t к поверхностному контуру твердея, стали 40, 45, 50G, 40X, 40XH, etc. используются, но сердцевина не затвердевает и остается viscous. In по грузоподъемности они уступают цементным сталям. В последнее время, используется в производстве зубчатых колес для автомобилей и станков взамен легированных-цементированная сталь, низкая-уволили сталь 58 (55 пп) -.
Это качественная углеродистая сталь (ГОСТ 1050-74), содержащий 0.55 0.63% C и минимальную концентрацию примесей (0.15% СГ, 0.20% Мп, 0.30% си), что увеличивает прокаливаемость. При глубоком индукционном звуке и интенсивном охлаждении водой часть этой стали подвергается только поверхностному упрочнению. Затвердевший слой, как и цемент, имеет толщину 1-2 мм, с высокой твердостью (HRC 58 62), переход к сердцевине происходит плавно. Ядро отверждается трохитом или сорбитом и имеет твердость iirc 40-30 и достаточную вязкость. Использование этой дешевой стали имеет большой экономический эффект.
Зубчатое колесо, которое работает на низких нагрузках, сделано унифицированной и улучшенной палитры 40, 50, 40X, 40XH, etc. Благодаря низкой твердости материала (HB <3500), зубья могут быть обрезаны после термической обработки, что упрощает технологию изготовления колес. Неметаллические материалы использованы для передачи волны и небольших шестерен работая на низких нагрузке и скорости: текст Освещенные ПТ и ПТК, деревянный пластик, нейлон полиамид-нейлон. Они используются для вождения автомобильных спидометров и распределительных валов, кинематографических камер, текстильных и пищевых машин.
Преимуществом такого колеса является отсутствие вибрации и шума, высокая химическая стойкость. Материал » устойчив к истиранию при высоких давлениях и ударных нагрузках. Трение, вызванное высоким давлением и ударными нагрузками, характерно для работы гусеницы гусеничного транспортного средства, поперечного материала железнодорожного рельса, ковша экскаватора и других деталей. Они изготовлены из высокомарганцевой аустенитной стали с содержанием около 1,1% Cu 13% Mp 110G13L. высокая износостойкость этой стали обусловлена сильной деформационно-упрочняющей способностью аустенита.
Сталь плохо обрабатывается, поэтому детали получают литьем (буквы L в сорте стали) или ковкой. Износостойкость стали 1 юг 13л максимизирована для однофазных аустенитных структур. Эта структура обеспечивается закалка в воде с 1100 СС. Голодать гасит низкой твердости (HB 2000) и большой вязкости. Если такая сталь подвергается абразивному износу только в процессе эксплуатации, то она оказывается неабразивной. В ударных условиях на поверхностном слое образуется большое количество кристаллических дефектов (дислокаций, дефектов штабелирования). steel. As в результате твердость поверхности повышается до HB 6000, и сталь становится износостойкой.
При кавитации, возникающей при работе гребных винтов, лопаток турбин и цилиндров гидронасоса, также наблюдается истирание, связанное с ударной нагрузкой на поверхность. Кавитационный износ создает струю жидкости в момент схлопывания газа или пузырьков. Большое количество микроударов вследствие этого вызывают развитие усталостных процессов, которые усиливаются под воздействием коррозии. Используйте анти-кавитацию! Нестабильной аустенитной структуры стали О8Х18Н1ОТ, ЗОХ1ОГ10 и т. д.
Аустенит этих сталей подвергается упрочнению и частичному мартенситному превращению при ударном воздействии, а его развитие потребляет энергию удара. Упрочнение поверхности стали в условиях эксплуатации затрудняет образование усталостных трещин.
Смотрите также:
Материаловедение — решение задач с примерами
Антифрикционные материалы | Виды изнашивании |
Фрикционные материалы | Закономерности изнашивания деталей, образующих пары трения, и пути уменьшения их износа |