Оглавление:
Курс учебной дисциплины «Детали машин» рассматривает основы расчета и конструирования деталей, узлов и агрегатов, встречающихся в различных машинах и механизмах.
Учебными программами среднего профессионального образования предмет «Детали машин» рассматриваются и изучаются, как раздел учебной дисциплины ‘Техническая механика», куда входят, также, ‘Теоретическая механика» и «Сопротивление материалов». В технических и строительных ВУЗах эти предметы изучаются более углубленно и преподаются как самостоятельные учебные дисциплины.
Детали машин должны удовлетворять двум основным условиям: надежности и экономичности. Под экономичностью понимают минимально необходимую стоимость проектирования, изготовления и эксплуатации.
Если что-то непонятно — вы всегда можете написать мне в WhatsApp и я вам помогу! |
Готовая курсовая работа по деталям машин с решением.
Детали машин и основы конструирования
Современное общество отличается от первобытного использованием машин.
Применение предметов, усиливающих возможности рук (палки, камни), и особенно освоение дополнительных источников энергии (костёр, лошадь) не только позволило человечеству выжить, но и обеспечило в дальнейшем победу над превосходящими силами природы.
Жизнь людей, даже самых отсталых племён, теперь немыслима без различных механических устройств и приспособлений (греч. «механа» -хитрость).
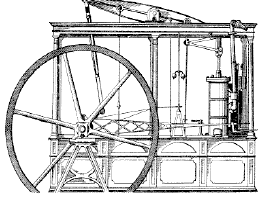
И хотя различные механические хитрости использовались уже в паровая машина уатта 1774 г. древнем Египте при строительстве пирамид,
всерьёз говорить о применении машин можно лишь с эпохи промышленной революции XVIII века, когда изобретение паровой машины дало гигантский технологический рывок и сформировало современный мир в его нынешнем виде. Здесь важен энергетический аспект проблемы.
С тех же пор наметились основные закономерности устройства и функционирования механизмов и машин, сложились наиболее рациональные и удобные формы их составных частей — деталей. В процессе механизации производства и транспорта, по мере увеличения нагрузок и сложности конструкций, возросла потребность не только в интуитивном, но и в научном подходе к созданию и эксплуатации машин.
В ведущих университетах Запада уже с 30-х годов XIX века, а в Санкт-Петербургском университете с 1892 года читается самостоятельный курс «Детали Машин». Без этого курса [9,16,18,22,23,32] теперь невозможна подготовка инженера-механика любой специальности.
Исторически сложившиеся в мире системы подготовки инженеров при всех национальных и отраслевых различиях имеют единую четырёхступенчатую структуру:
- На младших курсах изучаются ФУНДАМЕНТАЛЬНЫЕ НАУКИ, которые представляют собой системы знаний о наиболее общих законах и принципах нашего мира. Это — Физика, Химия, Математика, Информатика, Теоретическая механика, Философия, Политология, Психология, Экономика, История и т.п.
- Далее изучаются ПРИКЛАДНЫЕ НАУКИ, которые изучают действие фундаментальных законов природы в частных областях жизни, таковыми являются Техническая термодинамика, Теория прочности, Материаловедение, Сопротивление материалов, Теория механизмов и машин, Прикладная механика, Вычислительная техника и т.п.
- На старших курсах (3-й и выше) студенты приступают к изучению ОБЩЕТЕХНИЧЕСКИХ ДИСЦИПЛИН, таких как наш курс, а также «Основы стандартизации», «Технология обработки материалов» и т.п.; отраслевые различия здесь ещё сравнительно невелики.
- Обучение завершается освоением СПЕЦИАЛЬНЫХ ДИСЦИПЛИН, которые и составляют квалификацию инженера соответствующей специальности.
При этом подлинно высококвалифицированным специалистом, способным решать конкретные инженерно-технические проблемы становится лишь тот, кто усвоит взаимосвязь и преемственность между фундаментальными, прикладными, общетехническими и специальными знаниями.
Основные понятия и определения курса
Определим базовые понятия [21] в самом начале работы для систематизации учебного материала и во избежание двусмысленного толкования.
Возможно эта страница вам будет полезна:
Предмет детали машин |
Расположим понятия по степени сложности.
ДЕТАЛЬ — (франц. detail — кусочек) — изделие, изготовленное из однородного по наименованию и марке материала без применения сборочных операций (ГОСТ 2.101-68).
ЗВЕНО — группа деталей, образующая подвижную или неподвижную относительно друг друга механическую систему тел.
СБОРОЧНАЯ ЕДИНИЦА — изделие, составные части которого подлежат соединению на предприятии-изготовителе посредством сборочных операций (ГОСТ 2.101-68).
УЗЕЛ — законченная сборочная единица, состоящая из деталей общего функционального назначения.
МЕХАНИЗМ — система деталей, предназначенная для передачи и преобразования движения.
АППАРАТ — {лат. apparatus — часть) прибор, техническое устройство, приспособление, обычно некая автономно-функциональная часть более сложной системы.
АГРЕГАТ — (лат. aggrego — присоединять) унифицированный функциональный узел, обладающий полной взаимозаменяемостью.
МАШИНА — (греч. «махина» — огромная, грозная) система деталей, совершающая механическое движение для преобразования энергии, материалов или информации с целью облегчения труда. Машина характерна наличием источника энергии и требует присутствия оператора для своего управления. Проницательный немецкий экономист К. Маркс заметил, что всякая машина состоит из двигательного, передаточного и исполнительного механизмов.
АВТОМАТ — (греч. «аутомотос» — самодвижущийся) машина, работающая по заданной программе без оператора.
РОБОТ — (чешек, robot — работник) машина, имеющая систему управления, позволяющую ей самостоятельно принимать исполнительские решения в заданном диапазоне.
Процесс разработки машин имеет сложную, разветвлённую неоднозначную структуру и обычно называется широким термином.
ПРОЕКТИРОВАНИЕ -создание прообраза объекта, представляющего в общих чертах его основные параметры. Под КОНСТРУИРОВАНИЕМ некоторые авторы понимают весь процесс от идеи до изготовления машин, некоторые — лишь завершающую стадию его подготовки [14, 24, 25, 38]. Но в любом случае цель и конечный результат конструирования — создание рабочей документации (ГОСТ 2.102-68), по которой можно без участия разработчика изготавливать, эксплуатировать, контролировать и ремонтировать изделие.
Здесь также требуется дать базовые понятия:
ТЕХНИЧЕСКОЕ ЗАДАНИЕ — документ, составляемый совместно заказчиком и разработчиком, содержащий общее представление о назначении, технических характеристиках и принципиальном устройстве будущего изделия.
ТЕХНИЧЕСКОЕ ПРЕДЛОЖЕНИЕ — дополнительные или уточнённые требования к изделию, которые не могли быть указаны в техническом задании (ГОСТ 2.118-73).
ТВОРЧЕСТВО — специфическая материальная или духовная деятельность, порождающая нечто новое или новую комбинацию известного.
ИЗОБРЕТЕНИЕ — новое решение технической задачи, дающее положительный эффект.
ЭСКИЗИРОВАНИЕ — процесс создания эскиза (франц. es quisse — из размышлений), предварительного рисунка или наброска, фиксирующего замысел и содержащего основные очертания создаваемого объекта.
КОМПОНОВКА — расположение основных деталей, узлов, сборочных единиц будущего объекта.
РАСЧЁТ — численное определение усилий, напряжений и деформаций в деталях, установление условий их нормальной работы; выполняется по мере необходимости на каждом этапе конструирования.
ЧЕРТЁЖ — точное графическое изображение объекта, содержащее полную информацию об его форме, размерах и основных технических условиях изготовления.
ПОЯСНИТЕЛЬНАЯ ЗАПИСКА — текстовый документ (ГОСТ 2.102-68), содержащий описание устройства и принципа действия изделия, а также технические характеристики, экономическое обоснование, расчёты, указания по подготовке изделия к эксплуатации.
СПЕЦИФИКАЦИЯ — текстовый табличный документ, определяющий состав изделия (ГОСТ 2.102-68).
ЭСКИЗНЫЙ ПРОЕКТ — первый этап проектирования (ГОСТ 2.119-73), когда устанавливаются принципиальные конструктивные и схемные решения, дающие общие представления об устройстве и работе изделия.
ТЕХНИЧЕСКИЙ ПРОЕКТ — заключительный этап проектирования (ГОСТ 2.120-73), когда выявляются окончательные технические решения, дающие полное представление об изделии.
РАБОЧИЙ ПРОЕКТ — полный комплект рабочей документации (текстовой и графической ГОСТ 2.102-68; 2.106-68), в которой содержится полная информация о конструкции, изготовлении, эксплуатации и ремонте машины.
Основные принципы и этапы разработки машин
Машины, как и другие изделия, изготавливаются только по проекту, который, в любом случае, является совокупностью графических и текстовых документов. Правила и порядок разработки, оформления и обращения этих документов устанавливается комплексом стандартов.
Единой системой конструкторской документации (ЕСКД), разработанной в 70-е годы XX в [15].
Проектирование машин выполняют в несколько стадий, установленных ГОСТ 2.103-68. Для единичного производства это:
- Разработка технического предложения по ГОСТ 2.118-73.
- Разработка эскизного проекта по ГОСТ 2.119-73.
- Разработка технического проекта по ГОСТ 2.120-73.
- Разработка документации для изготовления изделия.
- Корректировка документации по результатам изготовления и испытания изделия.
Стадии проектирования при серийном производстве те же, но только корректировку документации приходится повторять несколько раз: сначала для опытного экземпляра, затем для опытной партии, затем по результатам изготовления и испытаний первой промышленной партии.
Возможно эта страница вам будет полезна:
Цели и задачи деталей машин |
В любом случае, приступая к каждому этапу конструирования, как и вообще к любой работе, необходимо чётко обозначить три позиции:
Исходные данные — любые объекты и информация, относящиеся к делу («что мы имеем?»).
Цель — ожидаемые результаты, величины, документы, объекты («что мы хотим получить?»).
Средства достижения цели — методики проектирования, расчётные формулы, инструментальные средства, источники энергии и информации, конструкторские навыки, опыт («что и как делать?»). Деятельность конструктора-проектировщика обретает смысл только при наличии заказчика — лица или организации, нуждающихся в изделии и финансирующих разработку.
Теоретически заказчик должен составить и выдать разработчику Техническое Задание — документ, в котором грамотно и чётко обозначены все технические, эксплуатационные и экономические параметры будущего изделия. Но, к счастью, этого не происходит, поскольку заказчик поглощён своими ведомственными задачами, а, главное, не имеет достаточных навыков проектирования. Таким образом, инженер не остаётся без работы.
Работа начинается с того, что заказчик и исполнитель совместно составляют (и подписывают) Техническое Задание. При этом исполнитель должен получить максимум информации о потребностях, пожеланиях, технических и финансовых возможностях заказчика, обязательных, предпочтительных и желательных свойствах будущего изделия, особенностях его эксплуатации, условиях ремонта, возможном рынке сбыта.
Тщательный анализ этой информации позволит проектировщику правильно выстроить логическую цепочку «Задание — Цель — Средства» и максимально эффективно выполнить проект.
Разработка Технического Предложения начинается с изучения Технического Задания. Выясняются назначение, принцип устройства и способы соединения основных сборочных единиц и деталей. Всё это сопровождается анализом научно-технической информации об аналогичных конструкциях. Выполняются кинематический расчёт, проектировочные расчёты на прочность, жёсткость, износостойкость и по критериям работоспособности. Из каталогов предварительно выбираются все стандартные изделия — подшипники, муфты и т.п. Выполняются первые эскизы, которые постепенно уточняются. Необходимо стремиться к максимальной компактности расположения и удобства монтажа-демонтажа деталей.
На стадии Эскизного Проекта выполняются уточнённые и проверочные расчёты деталей, чертежи изделия в основных проекциях, прорабатывается конструкция деталей с целью их максимальной технологичности, выбираются сопряжения деталей, прорабатывается возможность сборки-разборки и регулировки узлов, выбирается система смазки и уплотнения. Эскизный проект должен быть рассмотрен и утверждён, после чего он становится основой для Технического Проекта. При необходимости изготавливаются и испытываются макеты изделия.
Технический Проект должен обязательно содержать чертёж общего вида, ведомость технического проекта и пояснительную записку. Чертёж общего вида по ГОСТ 2.119-73 должен дать сведения о конструкции, взаимодействии основных частей, эксплуатационно-технических характеристиках и принципах работы изделия. Ведомость Технического Проекта и Пояснительная Записка, как и все текстовые документы должны содержать исчерпывающую информацию о конструкции, изготовлении, эксплуатации и ремонте изделия. Они оформляются в строгом соответствии с нормами и правилами ЕСКД (ГОСТ 2.104-68; 2.105-79; 2.106-68).
Таким образом, проект приобретает окончательный вид — чертежей и пояснительной записки с расчётами, называемыми рабочей документацией.
Возможно эта страница вам будет полезна:
Решение задач по деталям машин |
Требования к машинам и критерии их качества
Поскольку человеку свойственно хотеть всего и сразу, то требования к машинам многообразны и часто противоречивы, однако их можно условно разделить на основные взаимосвязанные группы: технологические требования; экономические требования; эксплуатационные требования.
Качество машины, т.е. её максимальное соответствие всем требованиям [19, 37] невозможно без неустанного внимания инженера на всех стадиях «жизни» машины.
Качество закладывается на стадии проектирования, обеспечивается на стадии производства и поддерживается в процессе эксплуатации.
Степень соответствия требованиям характеризуют критерии качества (греч. «крит эрион» — узкое место) — некие конкретные параметры (греч. «пара мэтрос» — измеряемый), т.е. измеряемые или вычисляемые величины.
Однако известно, что полное удовлетворение всех требований -абсолютно невыполнимая задача, поэтому всегда приходится идти на компромисс, обозначая главные требования и обеспечивая соответствующие им критерии качества.
Отметим поэтому лишь основные требования к деталям и машинам:
ТЕХНОЛОГИЧНОСТЬ — изготовление изделия при минимальных затратах труда, времени и средств при полном соответствии своему назначению.
ЭКОНОМИЧНОСТЬ — минимальная стоимость производства и эксплуатации.
РАБОТОСПОСОБНОСТЬ — состояние объекта, при котором он способен выполнять заданные функции. НАДЁЖНОСТЬ — свойство объекта сохранять во времени способность к выполнению заданных функций (ГОСТ 27.002-83).
Основными критериями качества машин считают: МОЩНОСТЬ — скорость преобразования энергии;
ПРОИЗВОДИТЕЛЬНОСТЬ — объём работы (продукции, информации),выполняемой в единицу времени;
КОЭФФИЦИЕНТ ПОЛЕЗНОГО ДЕЙСТВИЯ — доля дошедшей до потребителя энергии (мощности);
ГАБАРИТЫ — предельные размеры;
ЭНЕРГОЁМКОСТЬ — расход топлива или электричества отнесённый к объёму работы (пройденному расстоянию, произведённой продукции);
МАТЕРИАЛОЁМКОСТЬ — количество конструкционного материала машины, обычно отнесённого к единице мощности;
ТОЧНОСТЬ — способность максимально соответствовать заданному положению (скорости и т.п.);
ПЛАВНОСТЬ ХОДА — минимальные ускорения при работе машины.
Условия нормальной работы деталей и машин
Успешная работа деталей и машин заключается в обеспечении работоспособности и надёжности.
Работоспособность деталей и машин определяется как свойство выполнять свои функции с заданными показателями и характеризуется следующими критериями:
ПРОЧНОСТЬ — способность детали сопротивляться разрушению или необратимому изменению формы (деформации);
ЖЁСТКОСТЬ — способность детали сопротивляться любой деформации;
ИЗНОСОСТОЙКОСТЬ — способность сохранять первоначальную форму своей поверхности, сопротивляясь износу;
ТЕПЛОСТОЙКОСТЬ — способность сохранять свои свойства при действии высоких температур;
ВИБРОУСТОЙЧИВОСТЬ — способность работать в нужном диапазоне режимов без недопустимых колебаний.
Надежность определяется как свойство детали и машины выполнять свои функции, сохраняя заданные показатели в течение заданного времени и, по существу, выражает собой перспективы сохранения работоспособности [30, 33].
В процессе работы детали и машины подвергаются не только расчётным нагрузкам, которые конструктор ожидает и учитывает, но и попадают во внештатные ситуации [13], которые очень трудно предусмотреть, как, например, удары, вибрация, загрязнение, экстремальные природные условия и т.п. При этом возникает отказ — утрата работоспособности вследствие разрушения деталей или нарушения их правильного взаимодействия. Отказы бывают полные и частичные; внезапные (поломки) и постепенные (износ, коррозия); опасные для жизни; тяжёлые и лёгкие; устранимые и неустранимые; приработочные (возникают в начале эксплуатации) и связанные с наличием дефектных деталей; отказы по причине износа, усталости и старения материалов.
Надёжной можно считать машину, имеющую следующие свойства:
БЕЗОТКАЗНОСТЬ — способность сохранять свои эксплуатационные показатели в течение заданной наработки без вынужденных перерывов.
ДОЛГОВЕЧНОСТЬ — способность сохранять заданные показатели до предельного состояния с необходимыми перерывами для ремонтов и технического обслуживания.
РЕМОНТОПРИГОДНОСТЬ — приспособленность изделия к предупреждению, обнаружению и устранению отказов и неисправностей посредством техобслуживания и ремонта.
СОХРАНЯЕМОСТЬ — способность сохранять требуемые эксплуатационные показатели после установленного срока хранения и транспортирования.
Надёжность трудно рассчитать количественно, она обычно оценивается как вероятность безотказной работы на основании статистики эксплуатации группы идентичных машин.
При всей значимости всех описанных критериев, нетрудно заметить, что прочность является важнейшим критерием работоспособности и надёжности.
Невыполнение условия прочности автоматически делает бессмысленными все другие требования и критерии качества машин [5, 26, 30,36].
Действительно, немногого стоит технологичная, жёсткая, износостойкая, теплостойкая, виброустойчивая, дешевая в эксплуатации, ремонтопригодная конструкция самого передового дизайна, если она сломалась при первой же нагрузке!
Возможно эта страница вам будет полезна:
Контрольная работа по деталям машин |
Общие принципы прочностных расчётов
Все этапы проектирования, каждый шаг конструктора сопровождается расчётами. Это естественно, т.к. грамотно выполненный расчёт намного проще и в сотни раз дешевле экспериментальных испытаний.
Чаще всего конструктор имеет дело с расчётами на прочность [5,12,35].
Различают проектировочные и проверочные расчёты.
Проектировочный расчёт выполняется, когда по ожидаемым нагрузкам, с учётом свойств материала определяются геометрические параметры деталей.
Проверочный расчёт выполняют, когда известна вся «геометрия» детали и максимальные нагрузки, а с учётом свойств материала определяются максимальные напряжения, которые должны быть меньше допускаемых.
Несмотря на такие «провокационные» названия, следует помнить, что оба этих вида расчётов всегда сопутствуют друг другу и выполняются на стадии проектирования деталей и машин.
Математическая формулировка условия прочности любой детали очень проста:

Или, говоря техническим языком:

Всегда, везде, при любых обстоятельствах конструктор обязан учитывать и обеспечивать такие условия работы, чтобы напряжения в материале деталей не превышали допускаемых.
В качестве допускаемых нельзя назначать предельные напряжения, при которых наступает разрушение материала.
Разница между допускаемыми и предельными напряжениями похожа на разницу между краем платформы метро и «белой линией», проведённой примерно в полуметре перед краем. Переход через «белую линию» грозит замечанием от дежурного, а стояние на краю — гибелью.
Допускаемые напряжения следует принимать меньше предельных, «с Запасом»:

где — коэффициент запаса (обычно 7,2 <
<2,5).
В разных обстоятельствах коэффициент запаса может быть либо задан заказчиком, либо выбран из справочных нормативов, либо вычислен с учётом точности определения нагрузок, однородности материала и специфических требований к надёжности машин.
Выполнение всех видов прочностных расчётов для каждой детали займёт очень много времени. Поэтому инженер должен сначала изучить опыт эксплуатации подобных изделий. Это особенно удобно для типовых деталей и машин. Следует обратить внимание на то, какой вид поломок встречается чаще всего. Именно по этому виду поломок, точнее по вызывающим их напряжениям, следует выполнять предварительно проектировочный расчёт. По его результатам строится форма детали, а проверочный расчёт выполняется по напряжениям, вызывающим менее опасные дефекты.
В расчётах не следует гнаться за «абсолютной» точностью и использовать сложные «многоэтажные» формулы. Обширный опыт инженеров-расчётчиков показывает, что усложнение методик расчёта не даёт новых результатов.
Крупнейший советский специалист по прочностным расчётам деталей машин И.А. Биргер заметил [5], что в технических расчётах «всё нужное является простым, а всё сложное — ненужным». Впрочем, похожая мысль высказывалась уже в библейских текстах, хотя и не по поводу машин.
В расчётах необходимо стремиться к корректным упрощениям.
Возможно эта страница вам будет полезна:
Помощь по деталям машин |
Понятие об автоматизированном проектировании
Современные достижения науки и техники, возрастающая функциональность современных изделий требуют выполнения проектных работ большого объема. Требования к качеству проектов, срокам их выполнения оказываются все более жесткими в условиях конкурентной борьбы за потребителя. Удовлетворить эти требования путем количественного увеличения проектировщиков невозможно, так как распараллеливание проектных работ не безгранично.
Решение проблемы возможно путем внедрения в практику инженерного проектирования методов и средств автоматизированного проектирования.
Цель автоматизации проектирования — повышение качества, снижение материальных затрат, сокращение сроков проектирования и повышение производительности труда проектировщиков.
Под автоматизацией проектирования понимается такой способ проектирования при котором весь цикл проектных работ осуществляется рационально распределенным взаимодействием человека и ЭВМ.
В настоящее время термин «автоматизация проектирования» характеризует целое научно-техническое направление, базирующееся на современных достижениях физики, математики, вычислительной техники и теории проектирования.
Предметом автоматизации проектирования являются формализация проектных процедур, структурирование и типизация процессов проектирования, постановки, модели, методы и алгоритмы, информационная поддержка решения проектных задач, а также технические средства и способы их объединения в единую проектирующую систему.
В первые годы применения ЭВМ в процессе проектирования бытовало мнение о снижении требований к квалификации проектировщиков при использовании автоматизированного проектирования, однако эта точка зрения не получила подтверждения практикой, так как инженер -проектировщик помимо владения предметной областью должен знать модели, методы и методики автоматизированного проектирования. А это предъявляет повышенные требования к уровню профессиональной подготовки инженера, который помимо знания средств автоматизированного проектирования должен уметь отбирать и эксплуатировать эти средства в конкретном процессе создания определенного класса аппаратуры.
Возможно эта страница вам будет полезна:
Заказать работу по деталям машин |
Системный подход при проектировании
Современные методы проектирования деятельности пользователей АСУ сложились в рамках системотехнической концепции проектирования, в силу чего учет человеческого фактора ограничился решением проблем согласования «входов» и «выходов» человека и машины. Вместе с тем при анализе неудовлетворенности пользователей АСУ удается выявить, что она часто объясняется отсутствием единого, комплексного подхода к проектированию систем взаимодействия.
Использование системного подхода позволяет принять во внимание множество факторов самого различного характера, выделить из них те, которые оказывают самое большое влияние с точки зрения имеющихся общесистемных целей и критериев, и найти пути и методы эффективного воздействия на них. Системный подход основан на применении ряда основных понятий и положений, среди которых можно выделить понятия системы, подчиненности целей и критериев подсистем общесистемным целям и критериям и т.д. Системный подход позволяет рассматривать анализ и синтез различных по своей природе и сложности объектов с единой точки зрения, выявляя при этом важнейшие характерные черты функционирования системы и учитывая наиболее существенные для всей системы факторы. Значение системного подхода особенно велико при проектировании и эксплуатации таких систем, как автоматизированные системы управления (АСУ), которые по существу являются человеко-машинными системами, где человек выполняет роль субъекта управления.
Системный подход при проектировании представляет собой комплексное, взаимосвязанное, пропорциональное рассмотрение всех факторов, путей и методов решения сложной многофакторной и многовариантной задачи проектирования интерфейса взаимодействия. В отличие от классического инженерно-технического проектирования при использовании системного подхода учитываются все факторы проектируемой системы — функциональные, психологические, социальные и даже эстетические.
Автоматизация управления неизбежно влечет за собой осуществление системного подхода, так как она предполагает наличие саморегулирующейся системы, обладающей входами, выходами и механизмом управлением. Уже само понятие системы взаимодействия указывает на необходимость рассмотрения окружающей среды, в которой она должна функционировать. Таким образом, система взаимодействия должна рассматриваться как часть более обширной системы — АСУ реального времени, тогда как последняя — системы управляемой среды.
Классификация деталей машин
Не существует абсолютной, полной и завершённой классификации всех существующих деталей машин, т.к. конструкции их многообразны и, к тому же, постоянно разрабатываются новые.
Для ориентирования в бесконечном многообразии детали машин классифицируют на типовые группы по характеру их использования [1,10,11].
- ПЕРЕДАЧИ передают движение от источника к потребителю.
- ВАЛЫ и ОСИ несут на себе вращающиеся детали передач.
- ОПОРЫ служат для установки валов и осей.
- МУФТЫ соединяют между собой валы и передают вращающий момент.
- СОЕДИНИТЕЛЬНЫЕ ДЕТАЛИ (СОЕДИНЕНИЯ) соединяют детали между собой.
- УПРУГИЕ ЭЛЕМЕНТЫ смягчают вибрацию и удары, накапливают энергию, обеспечивают постоянное сжатие деталей.
- КОРПУСНЫЕ ДЕТАЛИ организуют внутри себя пространство для размещения всех остальных деталей, обеспечивают их защиту.
Рамки учебного курса не позволяют изучить все разновидности деталей машин и все нюансы проектирования. Однако знание, по крайней мере, типовых деталей и общих принципов конструирования машин даёт инженеру надёжный фундамент и мощный инструмент для выполнения проектных работ практически любой сложности.