Оглавление:
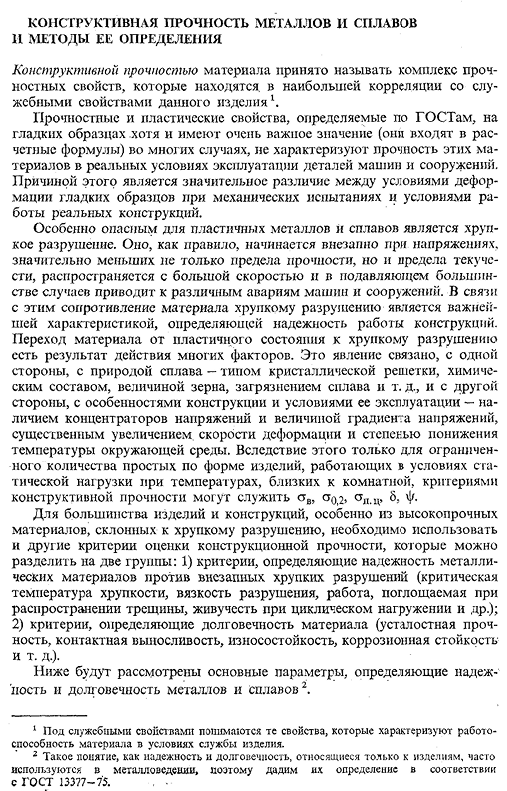
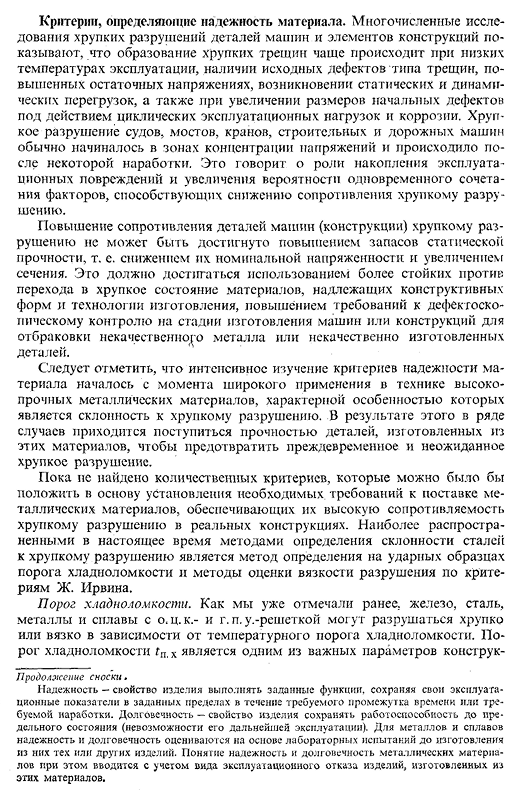
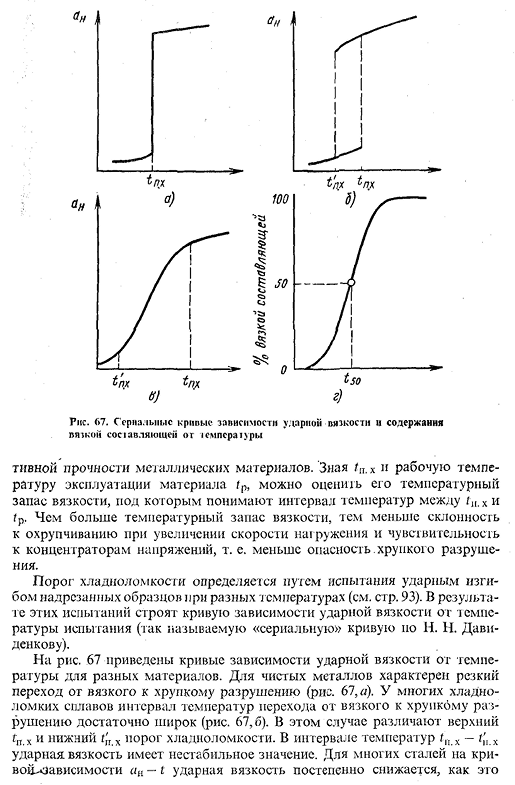
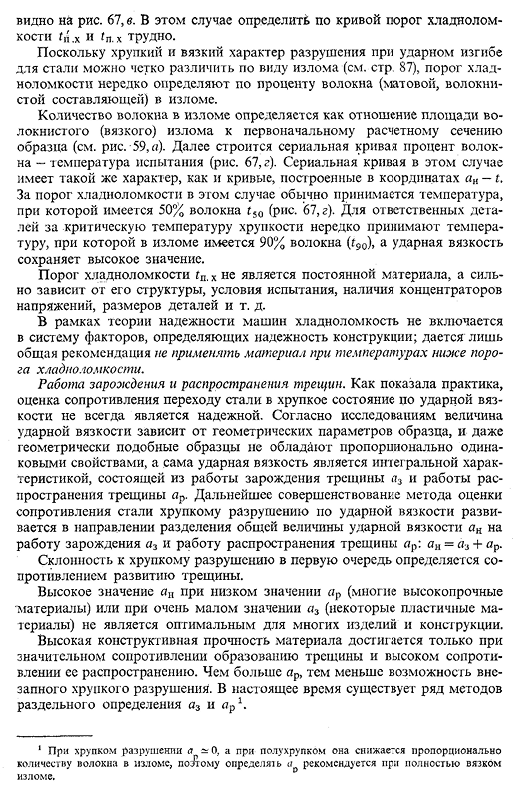
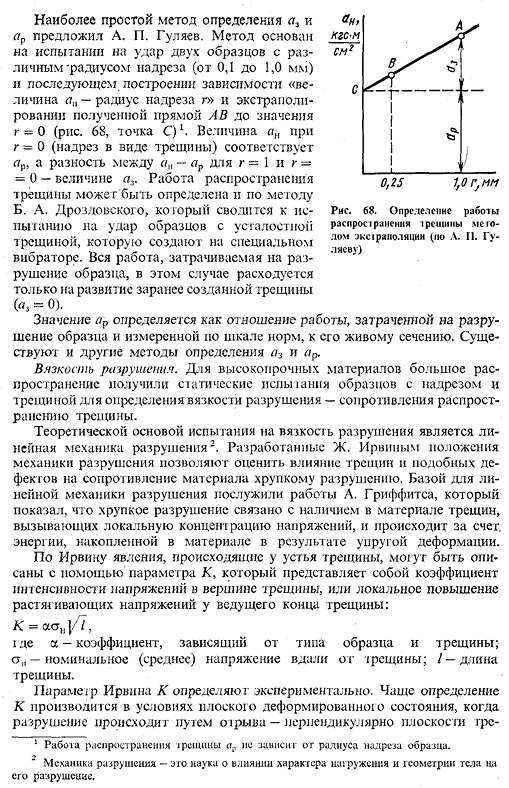
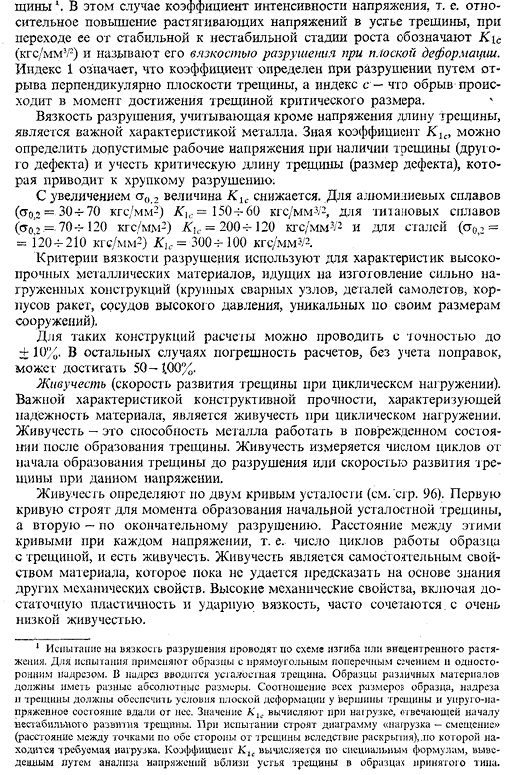
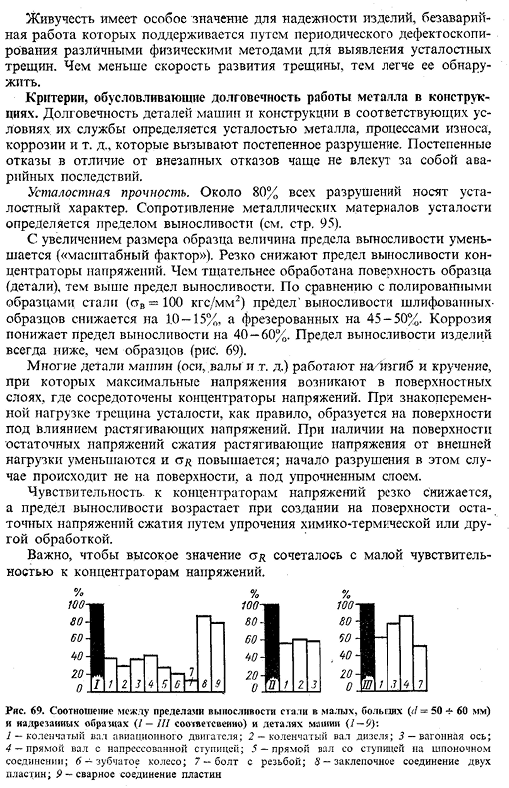
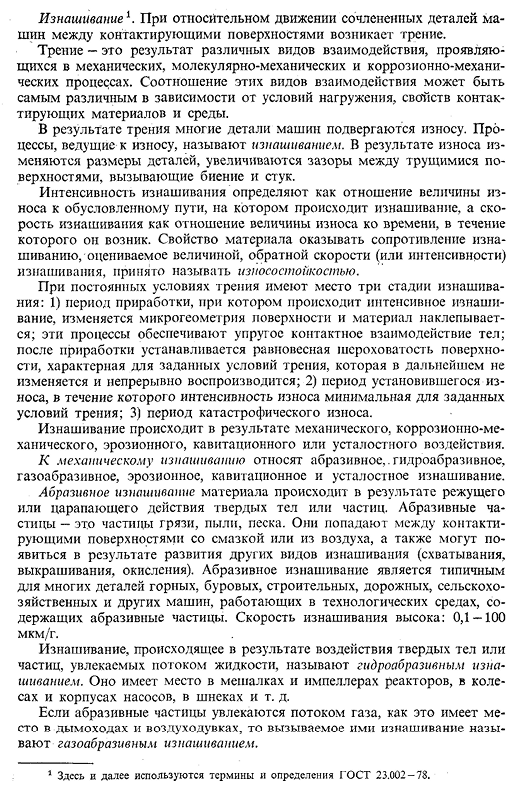
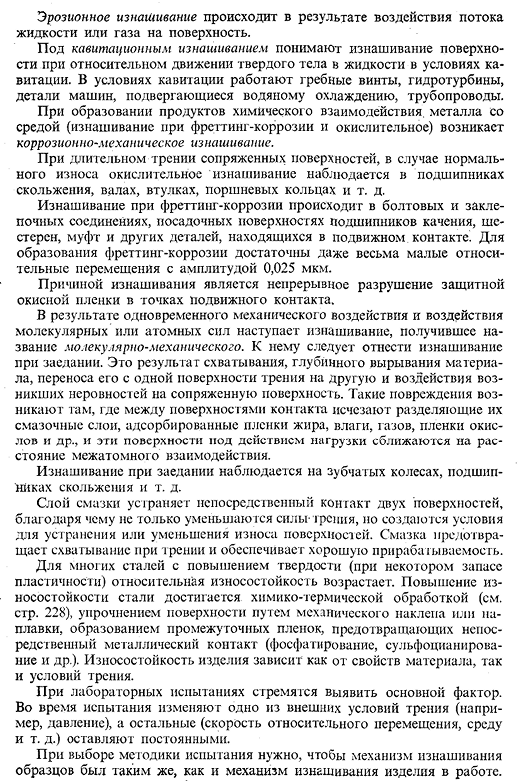
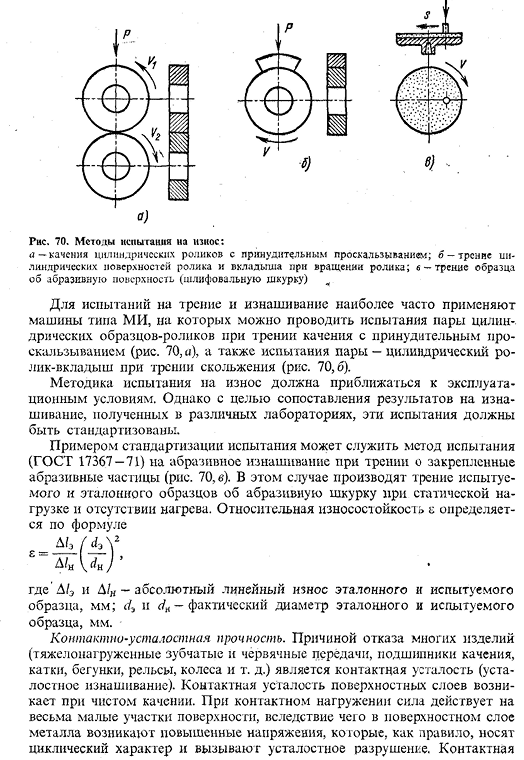
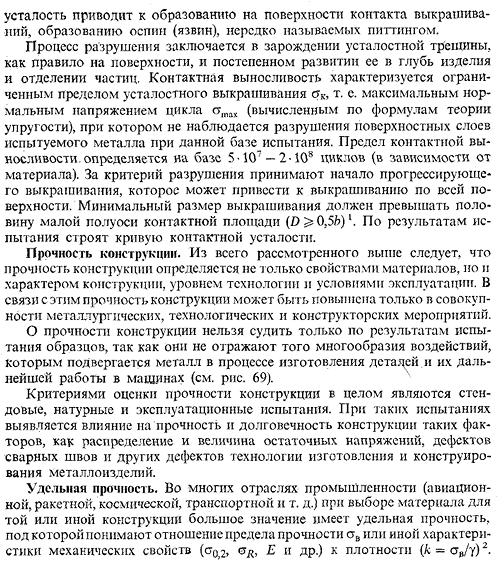

Конструктивная прочность металлов и сплавов и методы ее определения
- Прочность конструкции металлов и сплавов И методы его определения Прочность конструкции материала обычно называют совокупностью прочностных характеристик, существует максимальная корреляция с эксплуатационными характеристиками данного изделия 1. 1. под эксплуатационными характеристиками понимаются характеристики, характеризующие эксплуатационные характеристики материала в условиях эксплуатации изделия. 2. такие понятия, как надежность и долговечность, которые применяются только к изделиям, часто используются в металловедении, поэтому они определены в соответствии с ГОСТ 13377-75. И Ю. М. Лахтин и др.
Прочностные и пластические характеристики, определяемые в соответствии с ГОСТ гладкого образца, часто очень важны(они входят в формулу), но они не характеризуют прочность этих материалов в реальных условиях эксплуатации механических деталей и конструкций. Причиной этого является существенная разница между условиями деформации гладких образцов при механических испытаниях и условиями эксплуатации реальных конструкций. Особенно опасна для пластичных металлов и сплавов хрупкость fracture. As как правило, она начинается внезапно со значительно меньшего напряжения, чем предел прочности при растяжении, а также предела текучести, распространяется с очень большой скоростью,
что в большинстве случаев приводит к различным авариям машин и механизмов. structures. Людмила Фирмаль
In в связи с этим устойчивость материала к хрупкому разрушению является важнейшей характеристикой, определяющей надежность конструкции. Переход материала из пластического состояния в хрупкое разрушение является результатом многих факторов. Это явление, с одной стороны, связано с природой сплава (типом кристаллической решетки, химическим составом, размером частиц, загрязненностью сплава и др.), с другой стороны, с особенностями конструкции и условий эксплуатации-наличием зоны концентрации напряжений и величиной градиента напряжений. В результате происходит значительное увеличение скорости деформации и степени понижения температуры окружающей среды temperature. As в результате, критериями прочности конструкции являются STV, odd, STP. Будет TS, 8, x|/.
Для большинства изделий и конструкций, особенно высокопрочных материалов, склонных к хрупкому разрушению, следует использовать другие критерии оценки конструкционных свойств strength. It можно разделить на 2 группы.1) критерии, определяющие надежность хрупких материалов против внезапного хрупкого разрушения (разрушение, работа, поглощенная при распространении трещины, жизнеспособность при циклическом нагружении и др.); 2) критерии, определяющие долговечность материала (усталостная прочность, контактная прочность, износостойкость, коррозионная стойкость и др.). Ниже мы рассмотрим основные параметры, определяющие надежность и долговечность металлов и сплавов. 2 97 критерии определения надежности материала.
- Многочисленные исследования хрупкого разрушения механических деталей и элементов конструкций показали, что образование хрупких трещин происходит чаще при низких рабочих температурах, наличии начальных дефектов типа трещин, увеличении остаточных напряжений, возникновении статических и динамических перегрузок, а также увеличении размеров начальных дефектов под воздействием циклических эксплуатационных нагрузок. Хрупкое разрушение кораблей, мостов, кранов, строительной техники и дорожной техники обычно начиналось в зоне интенсивного стресса, и только через некоторое время. Это говорит о возросшей роли в накоплении эксплуатационных повреждений и возможности одновременного сочетания факторов, способствующих снижению стойкости к хрупкому разрушению.
Повышение стойкости механических деталей (конструкций) к хрупкому разрушению не может быть достигнуто за счет увеличения запаса силы статической прочности, то есть уменьшения номинального натяжения и увеличения площади поперечного сечения. Это должно быть достигнуто за счет использования материалов, более устойчивых к переходу в хрупкие условия, соответствующих конструкционным формам и технологическим приемам изготовления путем повышения требований к проверке на наличие дефектов на стадии изготовления машин или конструкций для отбраковки некачественного металла или некачественных производственных компонентов. Следует отметить, что интенсивные исследования критериев надежности материалов начались с момента их широкого применения в технологии высокопрочных металлических материалов,
которые характеризуются склонностью к хрупкости fracture. Людмила Фирмаль
As в результате этого, в некоторых случаях, необходимо снизить прочность деталей, изготовленных из этих материалов, чтобы предотвратить преждевременное и неожиданное хрупкое разрушение. До сих пор не найдено количественных критериев, которые служили бы основанием для установления необходимых требований к поставкам металлических материалов, обеспечивающих высокую стойкость к хрупкому разрушению реальных конструкций. Самые распространенные Метод определения склонности к хрупкому разрушению сталей, который сейчас запрещен, называется J. It предложен метод определения низкотемпературного порога хрупкости ударного образца по стандартам Ирвина и метод оценки вязкости разрушения. Порог для низкой температуры brittleness.
As упомянутые ранее железо, сталь, металлы и сплавы с решетками bcc и bp могут вызывать хрупкое или вязкое разрушение в зависимости от температурного порога для низкотемпературной хрупкости. Порог хладноломкости ТН. 1 X является одним из важных параметров конструкции Продолжение сноски » надежность-характеристика изделия, выполняющего указанные функции и поддерживающего эксплуатационные характеристики в заданных пределах в течение требуемого периода или требуемого времени эксплуатации. Долговечность-свойство изделия (невозможность дальнейшей эксплуатации), позволяющее ему оставаться работоспособным до конечного состояния.
Для металлов и сплавов надежность и долговечность оцениваются на основании лабораторных испытаний перед изготовлением тех или иных изделий products. In в данном случае понятие надежности и долговечности металлических материалов вводится с учетом вида неисправности изделий, изготовленных из этих материалов. 98 рисунок 67.Непрерывная кривая ударной вязкости и содержания компонентов температуры и вязкости Прочность металлического материала. Знание ’ 1P, x и рабочей температуры материала (tp) позволяет оценить температурный запас вязкости. Это означает температурный интервал между в/ п. Чем выше температура хранения х и тп, тем выше вязкость, тем меньше склонность к охрупчиванию с увеличением чувствительности к нагрузке скорости и концентратора напряжений.
То есть риск хрупкого разрушения снижается. Порог низкотемпературной хрупкости определяется путем испытания на ударный изгиб образца насечки при различных температурах (см. стр. 93). в результате этих испытаний создается кривая ударной прочности и температуры испытания(N. No. Так называемая»серийная»кривая Давыденкова). На рисунке 67 показаны кривые ударной вязкости и температуры различных материалов. Чистые металлы характеризуются резким переходом от вязкого разрушения к хрупкому (рис. 67, а). во многих холодно-хрупких сплавах температурный диапазон перехода от вязкого разрушения к хрупкому очень широк(рис. 67.6).в этом случае верхний T×x и Нижний t’n x холодно-хрупкого порога являются distinguished. In диапазон температур tn x-t’, X вязкость неустойчива.
Кривая зависимости An-t во многих сталях, ego 4 * 99 67, Как видно в Fig. In в этом случае кривая от холодного до хрупкого порога tfl. х и TN. х трудно определить. Поскольку хрупкий и вязкий характер разрушения при ударном изгибе стали можно четко различить по типу разрушения (см. стр. 87), порог низкотемпературной хрупкости часто определяется соотношением волокон разрушения (мат, волокнистый компонент). Количество волокна в области разрушения определяется как отношение площади волокнистого(вязкого) разрушения к первому расчетному сечению образца (см. рис.59, а).Далее создается непрерывная кривая процентной доли температуры испытания волокна(рис. 67, г).Непрерывная кривая в этом случае имеет те же характеристики, что и кривая, созданная с координатами ay-T.
В этом случае температура t50 (рис.67, d), при которой присутствует 50% волокон, обычно считается порогом для низкотемпературной хрупкости. Для критических деталей критической температурой хрупкости часто считается наличие 90% волокна (t90) в изломе и высокая температура ударной вязкости. Холодный хрупкий порог х не является постоянным материалом, но он во многом зависит от его структуры, условий испытаний, наличия концентраций напряжений, размеров детали и др. В рамках теории надежности машин в систему факторов, определяющих надежность конструкции, не входит холодная хрупкость.
Только общие рекомендации указывают на то, что материал не следует использовать при температурах ниже порога низкотемпературной хрупкости. Генерация ядер и распространение cracks. As практика показала, что оценка стойкости стали к переходу в хрупкое состояние с точки зрения ударной вязкости не всегда достоверна. Согласно исследованию, ударная вязкость зависит от геометрических параметров образца, даже геометрически подобные образцы не имеют одинаковых характеристик пропорционально, а сама ударная вязкость является интегральной характеристикой, состоящей из работы инициирования трещины a3 и работы распространения трещины ap.
Дальнейшее совершенствование метода оценки стойкости к хрупкому разрушению стали по показателям ударной вязкости развивается в направлении деления суммарного значения ударной вязкости ay на зародышевую работу a3 и работу распространения трещины ap: an = a3 + ap. Склонность к хрупкому разрушению во многом определяется его устойчивостью к растрескиванию. Высокие значения aa с низкими значениями ap (многие высокопрочные материалы) или очень маленькие значения a3 (некоторые пластичные материалы) не являются оптимальными для многих продуктов и конструкций. Высокая прочность конструкции Материал достигается только своей замечательной стойкостью к образованию трещин и высокой устойчивостью к их распространению. чем больше ar, тем ниже вероятность внезапного хрупкого разрушения.
В настоящее время существует множество способов определения a3 и ap1 по отдельности. 1 в случае хрупкого разрушения, а〜0, а в случае хрупкого разрушения, определяют, потому что количество волокна в изломе уменьшается пропорционально! А рекомендуется при полностью вязких переломах. 100 рисунок 68.Определение работы распространения трещины методом экстраполяции(А. II. By Гуляев) А. П. А. Самый простой способ определить, например, о, был предложен Гуляевым. Этот метод основан на ударном испытании 2 образцов с различными радиусами надреза (0,1-1,0 мм) и последующем построении зависимости»величина-радиус надреза r«и экстраполяции полученной прямой AB на значение r = 0(рис.68, точка с) 1. «значение n при r = 0 (разрез в виде трещины)» соответствует p, а разность между an-ar при r = 1 и r = 0 соответствует a3.Работа распространения трещины осуществляется Б. А.
Она также может быть определена по методу Дроздовского. Это ограничено к испытанию удара усталост-треснутых образцов созданных с экстренныйым выпуском vibrator. In в этом случае вся работа, затраченная на разрушение образца, тратится только на развитие ранее созданных трещин («3 = 0). 1 работа распространения трещины не зависит от радиуса надреза образца. 2 механизм разрушения — это наука о влиянии формы тела на характер нагрузки и разрушения. величина ar определяется как отношение работы, затраченной на разрушение образца, измеренное в меру нормы для его живого сечения. существуют и другие способы определения a3 и ap. Трещиностойкость.
Для высокопрочных материалов, статическое испытание надрезанных и треснутых образцов широко использовано для того чтобы определить твердость трещиноватости (сопротивление к распространению трещины). Теоретической основой испытаний на вязкость разрушения является линейная механика разрушения 2. J. положения механики разрушения, разработанные Эрвином, позволяют оценить влияние трещин и аналогичных дефектов на сопротивление материала хрупкому разрушению. Основой линейной механики разрушения являются исследования А. Гриффита, А. Согласно Ирвину, явление, возникающее при раскрытии трещины, можно объяснить с помощью параметра K, который представляет собой коэффициент интенсивности напряжений на вершине трещины, или локальное увеличение растягивающего напряжения на вершине трещины: K = acijJ / Y, где a-зависимый коэффициент типа образца и трещины; st-дальнее (среднее) напряжение на вершине трещины. Я-длина трещины. Определяется параметр Irwin K experimentally.
In во многих случаях определение K выполняется в условиях плоской deformation. In в этом случае разрушение является、 101 область\в этом случае коэффициент интенсивности напряжений, то есть относительное увеличение при переходе от устойчивой фазы роста растягивающих напряжений при раскрытии трещины к неустойчивой фазе роста, обозначается K ic (кг / мм3 / 1 2) и называется вязкостью разрушения при плоской деформации. Индекс 1 означает, что модуль упругости определяется при разрушении путем разрушения перпендикулярно плоскости трещины, а индекс С означает, что разрушение происходит, когда трещина достигает критического размера. 1 испытание на трещиностойкость проводится по схеме изгиба или эксцентрикового растяжения.
Для испытания используется прямоугольное поперечное сечение с выемкой на одной стороне. В выемку вводятся усталостные трещины. Образцы различных материалов должны иметь разные абсолютные размеры. Соотношение всех размеров образцов, выемок и трещин должно обеспечивать условия для плоской деформации на вершине трещины и условия упругих напряжений вдали от нагрузки. Значение K1s вычисляется с нагрузкой, соответствующей началу неустойчивой развитой трещины. Во время испытания строится диаграмма нагрузка-перемещение (расстояние между точками по обе стороны трещины от отверстия), вдоль которой размещается необходимая нагрузка.
Коэффициент K 1C рассчитывается по специальной формуле, полученной при анализе напряжений вблизи трещинного отверстия полученного образца бурового раствора. 102. Вязкость разрушения, которая учитывает длину трещины в дополнение к напряжению, является важным свойством металла. Зная коэффициент K1s, можно определить допустимое рабочее напряжение при наличии трещины (другого дефекта) и рассмотреть критическую длину (размер дефекта) трещины, приводящую к хрупкому разрушению. при увеличении σ0> 2 значение K уменьшается. Для алюминиевых сплавов (st02 = 30-g 70 кг / мм2) Kh. = 150-160 кг / мм3—, титановый сплав (cr0-2. 70 -?120 кг / мм2) L%= 2004-120 кг / мм3 / 2 и сталь(steel0,r = 1204-210 кг / мм2)K1s = 3004-100 кг / мм3 / 2.
Критерии трещиностойкости используются для характеристики высокопрочных металлов. Материал, используемый при изготовлении сверхпрочных конструкций (крупных сварочных узлов, деталей самолетов, корпусов ракет, сосудов высокого давления, уникальных по размерам конструкций). Для таких конструкций расчеты могут быть выполнены с точностью+ 10%.В противном случае погрешность расчета, без учета коррекции, может достигать 50-1.00%. Живучесть(скорость распространения трещины при циклических нагрузках). Важным свойством прочности конструкции, характеризующим надежность материала, является его живучесть при многократных нагрузках.
Живучесть-это способность металла функционировать в поврежденном состоянии после образования трещины. Живучесть измеряется числом циклов от начала образования трещины до разрушения, или скоростью роста трещины при заданном напряжении. Сила определяется по 2 кривым усталости (см. стр. 96).Первая кривая создается в момент образования первой усталостной трещины, а вторая кривая — в момент окончательного разрушения. Расстояние между этими кривыми при каждом напряжении, или число циклов движения образца с трещиной, является живучестью. Жизнеспособность-это самостоятельное свойство материала, которое нельзя предсказать до сих пор, основываясь на знании других механических свойств.
properties. It часто сочетается с высокими механическими свойствами, в том числе достаточной пластичностью и ударной вязкостью. Жизнеспособность особенно важна для надежности изделия, где беспроблемная работа поддерживается регулярным осмотром различными физическими методами для обнаружения усталостных трещин. Чем ниже частота возникновения трещин, тем легче их обнаружить. Уровень жизни металла в конструкциях. Долговечность механических деталей и конструкций при соответствующих условиях эксплуатации определяется усталостью металла, процессом износа, коррозией и др., а затем постепенно destroyed. In в отличие от внезапных отказов, пошаговые отказы часто не сопровождаются последствиями чрезвычайной ситуации. Усталостная прочность.
Около 80% всех повреждений-это усталость. Сопротивление металлических материалов усталости определяется пределами их прочности(см. стр. 95). По мере увеличения размера выборки предел выносливости уменьшается («масштабный коэффициент»).Стрессоры значительно снижают пределы выносливости. Чем тщательнее вы обрабатываете поверхность образца (детали), тем выше предел прочности. По сравнению с полированными стальными образцами (бар= 100 кгс / мм2) предел прочности полированных образцов снижается на 1,0-15%, а предел прочности фрезерованных образцов снижается на 45-50%.Прочность снижается на 40-60% из-за коррозии. Предел выносливости продукта всегда ниже предела выносливости образца(рисунок 69).
Многие механические компоненты (такие как оси и валы) действуют на изгиб и кручение, когда максимальное напряжение создается в поверхностном слое, где сосредоточена концентрация напряжений. При знакопеременных нагрузках усталостные трещины обычно образуются на поверхности под действием растягивающих напряжений. Если на поверхности имеется остаточное сжимающее напряжение, то растягивающее напряжение из-за внешней нагрузки увеличивается или уменьшается. Начало разрушения в этом случае происходит не на поверхности, а под затвердевшим слоем.
Чувствительность к концентратору напряжений резко падает, а остаточное сжимающее напряжение на поверхности, вызванное отверждением химическим нагревом или другими обработками, увеличивает предел выносливости. важно сочетать высокие значения od с низкой чувствительностью к концентратору напряжений. И надрезанные образцы (/- III) и механические части (1-9)», соответственно. / — Коленчатый вал авиационного двигателя; 2-коленчатый вал дизельного двигателя. 3-ось; — / — прямой вал, в который была вдавлена ступица. 5-прямой вал со ступицей при соединении с ключом; 6-шестерни; 7-болты с винтами; 8-клепаные соединения из 2 пластин. 9-сварных соединений 103 износ 1.
Трение возникает за счет относительного перемещения соединяемых частей машины между контактирующими поверхностями. 1 далее используются термины и определения ГОСТ 23.002-78. Трение является результатом различных типов взаимодействий, которые проявляются в механических, молекулярных, механических и коррозионных механических процессах. Соотношение этих видов взаимодействия очень различно, в зависимости от условий нагрузки, характеристик материала и контактирующей среды. В результате трения, многие механические детали более подвержены износу. Процесс, который приводит к износу называется Wear.
As в результате износа изменяются размеры деталей, увеличивается зазор между поверхностями трения, что вызывает удар и стук. Скорость износа определяется как отношение величины износа к определенному пути возникновения износа, а скорость износа определяется как отношение величины износа к моменту возникновения износа. Характеристика материала, обеспечивающего износостойкость, которая оценивается величиной обратной скорости изнашивания (или прочности), называется износом Сопротивление. В условиях постоянного трения выделяют 3 стадии износа.1) период привыкания. Происходит интенсивный износ, изменяется тонкая форма поверхности, и материал прилипает.
Эти процессы обеспечивают упругое контактное взаимодействие тела. После операции приучения устанавливается равновесная шероховатость поверхности. Это особенность данных условий трения, которые, к тому же, не изменяются и воспроизводятся непрерывно. 2)стабильный период износа. В течение этого времени скорость износа минимизируется при заданных условиях трения. 3)период катастрофического износа. Износ происходит в результате механических, коррозионных, механических, эрозионных, кавитационных или усталостных воздействий. Механический износ включает полировку, водную полировку, газовую полировку, эрозию, кавитацию и усталостный износ. Абразивный износ материала происходит в результате режущего или царапающего действия твердых веществ или частиц. Абразивные частицы-это частицы пыли, пыли, песка.
Они также могут появиться в результате возникновения других видов износа (упрочнение, сколы, окисление), когда смазка падает с приклеенной поверхности или воздуха. Абразивный износ характерен для многих частей горнодобывающей, буровой, строительной, дорожной, сельскохозяйственной и других машин, работающих в технической среде, включая абразивные частицы. Высокая скорость износа: 0,1-100 мкм / г. Истирание, возникающее в результате воздействия твердых веществ или частиц, переносимых потоком жидкости, называется струей воды abrasion. It сделано агитатора и турбинки реактора, колеса и снабжения жилищем насоса, винта и так далее.
Если абразивные частицы уносятся потоком газа, как в случае дымохода или воздуходувки, то износ, который они вызывают, называется газоабразивным износом. 104 эрозионный износ возникает в результате воздействия потока жидкости или газа на поверхность. Под кавитационным износом понимается поверхностный износ при относительном движении твердых тел в жидкости под действием кавитации conditions. In условия кавитации, пропеллер, гидро турбина, вод-охлаженные части машины и трубопровод будут работать. При образовании продуктов химического взаимодействия металлов и окружающей среды (фреттинг-коррозия и износ при окислении) происходит коррозионно-механический износ.
Из-за длительного трения сопрягаемой поверхности, в случае нормального износа, окислительный износ наблюдается в подшипниках скольжения, валах, втулках, поршневых кольцах и др. Износ при фреттинг-коррозии происходит в болтовых и заклепочных соединениях, посадочных поверхностях подшипников качения, шестернях, муфтах и других деталях с подвижным контактом. Для образования фреттинг-коррозии достаточно очень малого относительного смещения с амплитудой 0,025 мкм. Причиной износа является непрерывное разрушение защитной оксидной пленки в месте контакта с подвижным элементом. Износ возникает в результате одновременного возникновения механических и молекулярных сил или ядерных сил. Это называется молекулярным dynamics. It необходимо включить износ при захвате. Это является результатом эффекта неравномерности сопрягаемой поверхности, схватывания материала, глубокого разрыва и переноса материала с одной поверхности трения на другую.
Такое повреждение возникает, когда адсорбированные пленки, такие как разделяющий их смазочный слой, жир, влага, газ и оксид, исчезают между контактными поверхностями, и эти поверхности сближаются друг с другом под действием нагрузок. Подшипники скольжения и др. Слой смазки исключает непосредственный контакт 2 поверхностей. Это создает условия, которые не только уменьшают силы трения, но и устраняют или уменьшают износ поверхности. Смазка предотвращает затвердевание во время трения и обеспечивает хороший комфорт вождения. Во многих сталях с повышенной твердостью (с некоторым отклонением в пластичности) относительная износостойкость повышается.
Повышенная износостойкость стали достигается путем химико-термической обработки (см. стр. 228), упрочнения поверхности механическим упрочнением или поверхностной обработкой, а также образованием промежуточной пленки, препятствующей непосредственному контакту металла(фосфатирование, сульфотианизация и др.).).Износостойкость изделия зависит как от свойств материала, так и от условий трения. Клиническое обследование постарается выявить основные факторы. Во время испытания изменяется 1 из условий внешнего трения (например, давление), а остальные (относительная скорость перемещения, среда и т. д.) держится на постоянном уровне. При выборе процедуры испытания необходимо, чтобы механизм износа образца был таким же, как и механизм износа изделия в процессе эксплуатации. 105. тереть. Рисунок 70.
Способ испытания на износ: а-цилиндрическая прокатка Лицо с принудительным скольжением; б-трение ролика и цилиндрической поверхности вкладыша при вращении ролика. с-трение образца о полированную поверхность (шлифовальную шкурку), f Для испытания трением и износом, машина MI наиболее часто использована, и может выполнить 1 комплект испытаний cyline на этой машине. Образец барабана-ролик при трении качения с принудительным скольжением (рис. 70, а), а пара тест-ролик цилиндрической вставки при трении скольжения (рис. 70.6) Процедура испытания на износ должна быть близка к условиям эксплуатации. Однако для сравнения результатов износа, полученных в различных лабораториях, эти испытания должны быть стандартизированы.
Примером стандартизации испытания является метод испытания абразивного износа при трении с неподвижными абразивными зернами (ГОСТ 17367-71) (рис. 70, в). в этом случае испытуемый образец и эталонный образец трутся об абразивную кожу без нагрева под статическими нагрузками. Относительная износостойкость формулы Ми= D / N J • Где D /и D / I-абсолютный линейный износ эталонного и испытательного образцов, мм; d3 и^ » — фактический диаметр эталонного и испытательного образцов, мм. Контакт усталостной прочности. Причина выхода из строя многих изделий (тяжелонагруженных зубчатых и червячных передач, подшипников качения, роликов, бегунов, рельсов, колес и др.)- это контактная усталость (усталостный износ).Поверхностная усталость контакта слоя происходит в чисто завальцовке.
При контактной нагрузке сила действует на очень малую часть поверхности, в результате чего возникает повышенное напряжение в поверхностном слое металла. Это, как правило, циклично и вызывает усталостное разрушение. Контактная усталость приводит к образованию сколов на контактной поверхности и образованию естественного по(язвы).Это часто называют питтингом. Процесс разрушения обычно состоит из зарождения усталостных трещин на поверхности, а также постепенного развития и отделения частиц внутрь изделия. Контактная прочность характеризуется ограниченным пределом усталостной корки, то есть максимальным напряжением нормального цикла 0,5 фута) 1.По результатам испытаний создается кривая контактной усталости. 1 для испытания на контактную усталость используется машина, в которой образец подвергается давлению между 2 валами (роликами), 3 роликами и 2 контактными машинами, а также машина с контактной нагрузкой, приложенной к плоскости во время прокатки шарика.
Удельная жесткость (ÅГу) большинства металлов[Fe (сталь), Ti, Al, Mg и др.] и древесина почти такая же (-2700).Этим можно объяснить давнюю конкуренцию между авиационными конструкциями из стали, алюминия, титана и дерева. Конструкционная прочность. Из всего вышесказанного следует, что прочность конструкции определяется не только свойствами материала, но и характером конструкции, уровнем технологии и эксплуатации conditions. In в связи с этим прочность конструкции может быть повышена только в совокупности металлургических, технических и проектных работ. Прочность конструкции не отражает различных воздействий, которым подвергается металл при изготовлении деталей и дальнейших операциях на станке, поэтому определить ее можно только по результатам испытаний образца (см. Рисунок 69).
Критериями оценки прочности всей конструкции являются стендовые, полевые и эксплуатационные испытания. Такие испытания выявляют влияние на прочность и долговечность конструкции таких факторов, как распределение и величина остаточных напряжений, дефекты сварки и другие дефекты технологии изготовления и изготовления металлических изделий. Специфический strength. In многие отрасли промышленности (авиационная, ракетно-космическая, транспортная и др.), при выборе материалов определенной конструкции очень важна определенная прочность. Это отношение конечной прочности ствола или других механических свойств (cr02,<3d, E и др.) К плотности (L = stv / y) 2.
Смотрите также:
Решения задач по материаловедению
Пути повышения прочности металлов | Механические свойства, определяемые при динамических испытаниях |
Возврат | Механические свойства при переменных (циклических) нагрузках |