Оглавление:
До середины 1960-х годов основное внимание уделялось обеспечению качества продукции. Основная роль была отведена контролю и отбраковке дефектной продукции. Контроль и отбраковка в производственной практике осуществлялись различными методами, которые развивались и совершенствовались под влиянием достижений научно-технического процесса. В организационном плане система обеспечения качества соответствовала структуре производственного процесса и отвечала его требованиям. В этом случае, когда производственный процесс (от закупки сырья до изготовления готовой продукции) осуществлялся на одном предприятии, контроль качества проводился перед отгрузкой потребителю.
Технология производства, возможно, состояла из большого количества операций и может быть сложной. В этом случае приемочный контроль совмещался с оперативным контролем. Важная роль была отведена входному контролю закупаемого сырья. Система управления была основана на следующем принципе: обнаружение дефектов и устранение дефектных товаров из производственного процесса должно осуществляться как можно раньше. Это было вызвано тем, что дальнейшая переработка дефектной продукции привела к значительным потерям и необоснованно высоким производственным затратам. Подход к обеспечению качества только с точки зрения требуемого контроля (со стопроцентным контролем параметров каждой детали или изделия) многие квалифицированные инспекторы. На крупных промышленных предприятиях США количество контроллеров было приведено в соответствие с численностью производственного персонала. Методы математической статистики оказали неоценимую помощь в обеспечении качества.
Методы математической статистики позволили оценить качество продукции с определенной вероятностью методом выборки. Статистические методы контроля качества широко применялись в промышленности развитых капиталистических стран. Они помогли сократить время, необходимое для управления операциями, и повысить эффективность управления. Впоследствии новые условия производства потребовали поиска адекватных и эффективных методов контроля качества. Исследования операций, кибернетика, системный инжиниринг и общая теория систем повлияли на совершенствование методов обеспечения качества. Кибернетический подход послужил основой для появления концепции управления качеством, которая пришла на смену традиционному понятию контроля. Эта концепция появилась в начале 60-х годов, и одним из ее основателей стал американский ученый А.В. Файгенбаум, который предложил учитывать каждый этап в процессе создания продукта (а не только конечный результат).
Производство изделия — это, по сути, создание или рождение качества, т.е. суммы определенных свойств или «функциональной совокупности». Таким образом, процесс создания продукта (качество) является контролируемым процессом. Контроль включает в себя сравнение различных параметров, определяющих качество продукта, с эталонными значениями, записанными в используемых стандартах, нормативах и спецификациях. Информация о несоответствии уровня качества установленным стандартам (сигнал несоответствия) поступает через контур обратной связи (ОС) в специальный блок (управляемый элемент), где проводится анализ и разрабатываются меры по устранению отклонений. Например, усовершенствование конструкции и технологии, замена машин, обучение персонала и т.д. Продукты, прошедшие контроль, поставляются потребителю, который решительно оценивает уровень качества. Отзывы покупателей о качестве и рекламации направляются производителю. В соответствии с ними ведущий элемент также разрабатывает корректирующие действия.
Эта новая концепция прояснила место контроля в обеспечении качества. Контроль все еще является важной и необходимой операцией, но как связующее звено в общей системе обеспечения качества. Главной целью этой системы является обеспечение необходимого уровня качества (а зачастую и его повышение) на протяжении всего периода производства продукции. Эта цель может быть достигнута путем оптимизации всего процесса создания продукта в соответствии с критерием качества.
Процесс обеспечения качества состоит из следующих консолидированных этапов:
- Оценка уровня качества аналогичных продуктов, доступных на рынке, анализ требований заказчика;
- Длительный прогноз;
- Планирование на уровне качества;
- Разработка стандартов;
- Инжиниринг качества в процессе проектирования и разработки технологом;
- контроль качества сырья и закупаемых материалов;
- управление производственным процессом;
- Приемный контроль;
- контроль качества продукции в условиях эксплуатации (после продажи);
- Анализ отзывов и жалоб клиентов.
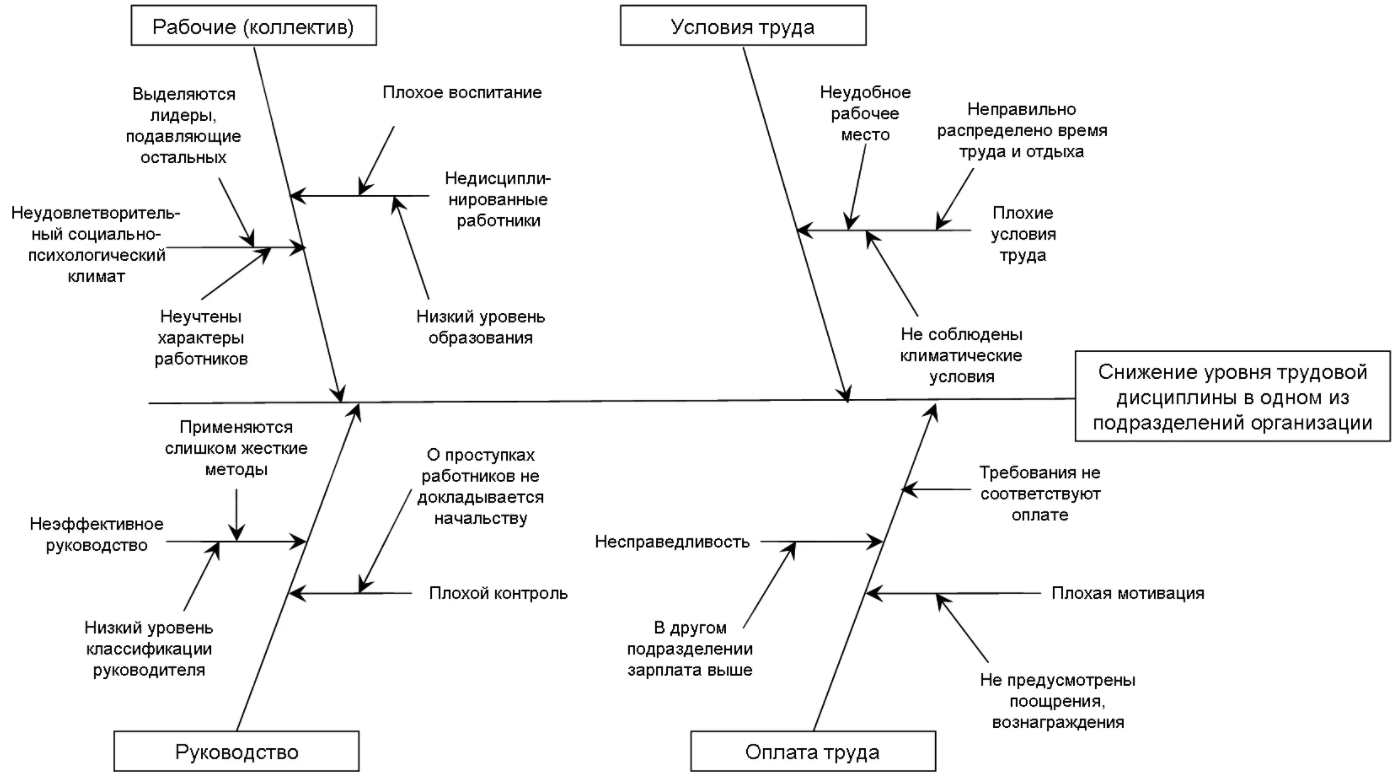
Создание и развитие системы управления качеством
Каждый из перечисленных этапов разбивается на совокупность процессов, операций и действий Исполнителей. В то же время, процессы и действия в рамках процесса управления качеством имеют четко определенные цели, критерии контроля (стандарты), пути обратной связи, процедуры анализа и методы действий. Таким образом, собственно система управления процессами и качеством представляет собой сложный набор взаимосвязанных контуров управления. В настоящее время качество играет важную (хотя и не ведущую) роль. Современный рынок, как показывают исследования отечественных и зарубежных ученых, характеризуется устойчивой тенденцией к повышению роли «неценовых» форм конкуренции, в частности, качественной конкуренции. Характерно, что с ростом количества изделий с длительным сроком эксплуатации все большую роль играет не продажная цена изделия, а «стоимость всего жизненного цикла». Общая стоимость жизненного цикла представляет собой сумму расходов по следующим категориям:
- стоимость всего комплекса исследований и разработок, предшествующего серийному производству;
- стоимость производства необходимого количества продукции;
Затраты, понесенные потребителем на обслуживание, эксплуатацию и ремонт изделия в течение всего срока его службы.
Затраты потребителя (которые определяют его выбор конкретного продукта) тесно связаны с качеством и надежностью продукта.
Обеспечение качества (основная цель) разделено на ряд подцелей: Анализ, проектирование, различные виды контроля качества, оценка качества и другие подцели подразделяются на еще более мелкие, и таким образом строится дерево целей, в соответствии с которым осуществляется управление качеством.
Система менеджмента качества, предложенная Файгенбаумом, привела к значительным изменениям во внутреннем управлении. В частности, изменились организационные структуры: созданы центральные отделы «управления» качеством или «обеспечения» качества и соответствующие ячейки (элементы комплексных систем управления качеством) в областях науки, проектирования, производства, поставки и распределения. Возросла важность работы по обеспечению качества. Систему управления качеством возглавил руководитель высшего звена — вице-президент по качеству. С этим, А. В Файгенбауме была создана комплексная система управления качеством продукции. Эта система была полностью внедрена в Японии как часть системы Канбан. Комплексная система менеджмента качества (CQMS) в соответствии с так называемыми циклами W. E. Deming. Цикл Деминга состоит из четырех фаз: Планирование, производство, контроль, совершенствование продукции. Весь жизненный цикл продукта является объектом СМК. Это означает системный подход ко всем фазам жизненного цикла: изучение требований рынка, доставка готового продукта потребителю и его обслуживание в процессе эксплуатации.
События
Научно-исследовательские и опытно-конструкторские работы, проводимые учеными разных стран, подтвердили, что качество конечной продукции определяется и зависит от качества исследований и разработок, инжиниринга и технологий. Никакие организационные меры не могут обеспечить требуемые показатели качества без обеспечения соответствующего уровня развития проектирования, качества инжиниринга и технологии. Концепция управления качеством и практика ее реализации позволили по-новому оценить роль непосредственных исполнителей в обеспечении качества. Прежде всего, изменились взгляды на распределение ответственности за качество. Многочисленные исследования показали количественную связь между ответственностью за ошибки исполнителей и управлением.
В середине 1950-х годов в бывшем Советском Союзе была внедрена саратовская система бездефектного производства и поставок продукции с первой презентацией. Это обеспечило постоянное внимание всего коллектива
В США и Западной Европе в конце 1950-х годов появились различные формы самоконтроля качества. Одна из форм самоконтроля называлась «нулевой дефект» или «бездефектная работа». Внедрение определенных организационных мер и применение специальных мер материального и морального стимулирования позволило создать условия, при которых весь персонал мог бы качественно, без ошибок и доработок выполнять свою работу. Качество работы контролировал сам исполнитель. В системе безупречной работы (FCL) появились различные движения: «передача продукции на первой презентации», «работа с персональным брендингом» и др.
Круги качества стали активными в Японии в 1950-х годах. Круги качества возникли «естественно» как логическое продолжение и дальнейшее развитие японских концепций и практики управления персоналом и качеством. Создание качественных кругов на промышленных предприятиях столкнулось со значительными трудностями на ранних стадиях и потребовало больших организационных усилий и значительных затрат. Круги стали одной из тех практических форм, в которых реализуются управленческие подходы и концепции повышения эффективности. Важнейшей формой деятельности кружка качества было обучение рабочих и мастеров. Учебные программы пришли из ведущих компаний, такие как программа подготовки мастеров по статистическому контролю качества в Fuji Seitsu Metallurgical Company (1951), подготовка учебных материалов по контролю качества в Tekko Kekam (1952), учебная программа Mitsubishi Denki (1952). В январе 1956 года журнал «Контроль качества» провел круглый стол «Мастера мастерских рассказывают о своем опыте в области контроля качества». Профессор Исикава Каору по праву считается отцом качественных кругов. В апреле 1962 года вышел первый номер журнала «Контроль качества для мастеров», в котором главную роль сыграл Исикава. Журнал призвал к созданию в компаниях кругов контроля качества. В журнале были указаны принципы работы этих кругов. Среди задач, стоящих перед кругами, занимающимися вопросами качества, были названы три основные цели:
- способствовать совершенствованию производства и развитию компании;
- Основанная на уважении к человеку для создания достойной и радостной рабочей обстановки;
- Создать среду, способствующую развитию способностей человека и выявлению его безграничных возможностей.
Звонок журнала был услышан и принят. В мае 1962 года на заводе государственной телефонно-телеграфной компании «Нихон денен кошья» в Мацуяме был зарегистрирован первый качественный круг. В мае 1963 года в городе Сендай состоялся первый конгресс кружков качества. На четвертом конгрессе, состоявшемся в Нагое в 1964 году, присутствовало 149 человек и было представлено 22 доклада, в то время как на четвертом конгрессе, состоявшемся в Нагое в 1964 году, присутствовало 563 участника и было представлено 92 доклада. Круг качества был организован на добровольной основе с самого начала. В начале 1965 года в Японии было зарегистрировано 3700 кружков качества. В 1966 году японские круги по вопросам качества привлекли внимание на десятом конгрессе Европейской организации по контролю качества в Стокгольме. В настоящее время в Японии зарегистрировано более 300 000 кружков качества. Концепция контроля качества не нова, но японцы выдвинули концепцию тотального контроля качества, которая была более широкой и включала в себя движение за улучшение качества на корпоративном уровне. В движении должны были участвовать все — от генерального директора до уборщика. Другими словами, разработанная американскими учеными концепция No-Fault трансформировалась в общенациональное движение в Японии. Движение «No-Fault» было нацелено на достижение определенных стандартов качества; КК было нацелено на постепенное повышение качества сверх определенных стандартов. Программы контроля качества на самом деле были направлены не на качество продукции, а на революцию в работе организации на уровне цеха.
Появление серии международных стандартов ISO 9000 по системам качества стало дальнейшим развитием теории и практики современного менеджмента качества. С конца 1980-х годов компании в странах с рыночной экономикой начали разрабатывать, внедрять и сертифицировать системы менеджмента качества. Появился системный подход к управлению качеством, уделяющий пристальное внимание не только качеству продукции, но и качеству услуг. Это объясняется тем, что последнее десятилетие во многих странах с рыночной экономикой характеризуется быстрым ростом сектора услуг. В этом контексте оказание услуг не отличается от производства продукции.
Предоставление услуг имеет ряд специфических особенностей.
Услуги не всегда ощутимы. В этом случае доказать качество услуги не представляется возможным.
При оказании услуг производство и потребление взаимосвязаны. Производство невозможно без активного сотрудничества сторон. Например, учитель не может передать знания студенту без участия и желания студента. Качество услуг имеет различные аспекты. Это можно объяснить на примере так называемой индустрии гостеприимства. В этой области качество — это то, чего хотят все. Сервисная компания должна это обеспечить. В США и в нашей стране нет рекламы, в которой бы не говорилось о том, что предлагаемые товары или услуги высшего качества. Никогда еще сервисные компании не заботились так сильно о качестве товаров и услуг. Это связано с тем, что качество оказывает наибольшее влияние на жизнеспособность сервисного бизнеса. История многих современных гостиничных компаний доказывает, что именно качество позволило им занять лидирующие позиции в отрасли. Обеспечение качества — консолидация и поддержание системы качества, в том числе демонстрация ее актуальности, является важнейшим результатом развития менеджмента качества.
Контроль качества
Планирование и развитие обеспечения качества включает в себя: Планирование уровня качества продукции, планирование контроля качества и планирование инженерного контроля; Сбор информации по качеству, расчет качества, обработка информации и анализ данных по качеству производства и эксплуатации; Управление качеством поставляемой поставщиками продукции и внутреннее управление качеством; Разработка методов контроля для обеспечения сопоставимости и надежности результатов контроля качества; Разработка системы менеджмента качества для обеспечения сопоставимости и надежности результатов контроля качества; Менеджмент качества поставляемой поставщиками продукции; Разработка системы менеджмента качества для контроля качества поставляемой продукции.
Контроль качества включает в себя: — Поступающий контроль качества сырья, материалов основного и вспомогательного назначения, полуфабрикатов, комплектующих изделий, инструментов, поступающих на склады предприятия; производственный контроль соблюдения установленного технологического режима, а иногда и оперативная приемка продукции; систематический контроль состояния оборудования, станков, режущего и измерительного инструмента, контрольно-измерительных приборов, прецизионных приборов, штампов, моделей испытательного и взвешивающего оборудования, новых и находящихся в эксплуатации, приборов, условий производства и транспортировки изделий и другие виды контроля; контроль моделей и прототипов; контроль готовой продукции (деталей, малых узлов, агрегатов, блоков, изделий).Стимуляция качества включает в себя: Разработка документации, отражающей методы и средства мотивации в области обеспечения качества продукции; разработка положений о вознаграждении сотрудников компании за качественную работу (совместно с отделом организации труда и оплаты труда; обучение и повышение квалификации).
Руководитель ККР подчиняется непосредственно директору Компании. Начальник отдела контроля качества имеет право остановить приемку продукции с повторяющимися дефектами до устранения причин этих дефектов, запретить использование сырья, материалов, компонентов и инструментов, которые не соответствуют указанным требованиям для изготовления новой продукции. В случае выявления дефектов руководитель ККР выдвигает обязательные требования к подразделениям и функционерам предприятия об устранении причин дефектов продукции и вносит предложения руководству предприятия о привлечении к ответственности функционеров и работников предприятия, виновных в производстве дефектной продукции. Совместно с директором и главным инженером предприятия он отвечает за выпуск бракованных изделий или изделий, не соответствующих стандартам и техническим условиям. Структура и штатное расписание ККР предприятия разрабатывается на основе типовой структуры с учетом задач, функций и особенностей производства. Как правило, в отделе создается следующее: Управление технического контроля, которое находится в главном и вспомогательных цехах; Управление внешнего контроля, которое обеспечивает входной контроль материалов и компонентов: Управление финального контроля и испытаний готовой продукции; Управление анализа и учета брака и рекламаций; Центральная измерительная лаборатория и ее контрольно-измерительные приборы, которые контролируют состояние элементов и инструментов, в том числе используемых при контроле качества; Инспекционная группа, которая осуществляет поверочный контроль качества продукции и целевые проверки технологической дисциплины; Блок контроля экспортной продукции; Блок контроля качества лома и отходов цветных и драгоценных металлов.
С деятельностью ККД тесно связаны отдел метрологии, отдел стандартизации, главный технолог, главный металлург, главный конструктор, отдел надежности, отдел гарантийного обслуживания или цех и др. Общее руководство деятельностью по обеспечению качества продукции осуществляет главный инженер предприятия. Для разработки и анализа вариантов управленческих решений он привлекает постоянно действующий комитет по качеству (ПДКК), в состав которого входит большинство основных специалистов компании, в том числе начальник отдела контроля качества. Специалисты Дата-центра системы менеджмента качества контролируют выполнение решений СМК, обрабатывают информацию по анализу и регистрации дефектов, а также расчет показателей качества работы.
Звезда качества
Для графической иллюстрации основных этапов развития систем качества мы использовали известную в российском производстве цифру — «знак качества». Мы заполняем контур этой фигуры, известной как «Пентагон», пятиконечной звездой, и то, что мы получили, называется «Quality Star».
В основу звезды качества мы хотим положить ту или иную систему менеджмента качества, которая соответствует определенной концепции. Мы предполагаем, что эта система документирована и включает в себя как организационную структуру управления компанией, так и систему управления процессами создания продуктов. Современная философия управления качеством уделяет большое внимание как горизонтальным процессам управления качеством (например, процессам, которые проходят по линии «маркетолог — дизайнер — технолог — производитель — тестер — продавец»), так и вертикальным процессам, которые характеризуются не только направленностью «сверху вниз», но и «снизу вверх». Примеры горизонтального управления включают межфункциональную командную работу, управление статистическими процессами, построение организационных структур из цепей клиент-поставщик, структурирование функции качества и т.д. Примерами противоположного (восходящего) «вертикального управления» являются знаменитые круги качества.
Встроенные на предприятиях системы управления качеством организации могут в той или иной степени охватывать горизонтальное управление, включая управление процессами, и вертикальное — снизу вверх. Но очень важно сразу же понять необходимость учитывать эти сферы управления. На «Звезде качества» две верхние границы — это ее «крыша». Левый уровень «крыши» — это система мотивации за качественную работу, а правый — система обучения персонала. Левый край представляет систему отношений с поставщиками, а правый край — систему отношений с клиентами. В центре звезды мы показываем, какие цели преследуются и, в случае успеха, достигаются созданными системами, а внизу мы указываем время, когда та или иная система была четко сформулирована в документах и/или книгах, статьях (для конкретной системы качества).
Таким образом, для любой спроектированной и документированной системы качества, включая управление процессами, необходимо работать:
- Используйте средства для мотивации сотрудников;
- обучать его как техническим вопросам, так и управлению качеством;
- установить правильные отношения с потребителями;
- научиться управлять поставщиками, с тем чтобы своевременно получать от них продукцию требуемого качества.
Японский профессор Икс. Однажды Цубаки спросили: «В чем секрет успеха Японии в качестве — в использовании статистических методов, методов Тагути, качественных кругов или чего-то еще? «Он ответил: «Все, что вы перечислили, играет свою роль, но, пожалуй, самое главное — это отличная система обучения сотрудников, как внутренних, так и внешних, и особая система мотивации». В то же время он сетует на то, что существуют определенные проблемы с обучением из-за ослабления системы пожизненного труда в Японии. В конце концов, владельцы бизнеса рассматривают обучение как инвестиции в персонал и поэтому не хотят инвестировать в тех, кто может уйти.
В истории развития документированных систем качества, мотивации, обучения и партнерства можно выделить пять этапов и представить их в виде пяти звезд качества.
Пять звезд за качество.
Первая звезда соответствует начальным этапам приближения системы, когда появилась первая система — система Тейлора (1905 г.). Он устанавливает требования к качеству изделий (деталей) в виде зон допусков или определенных шаблонов, которые настраиваются на верхнюю и нижнюю границы допусков — проходных и непроходных калибровок.
Для обеспечения успеха системы Taylor были введены первые специалисты по качеству — инспекторы (в России: технические инспекторы).
Система стимулирования включает в себя штрафы за недостатки и отказ, а также увольнение.
Система обучения была ограничена профессиональной подготовкой и обучением использованию контрольно-измерительного оборудования.
Взаимоотношения с поставщиками и клиентами строились на основе требований, изложенных в технических спецификациях (ТС), соответствие которым проверялось в ходе приемочных испытаний (входящих и исходящих).
Все вышеперечисленные особенности системы Taylor сделали ее системой управления качеством для каждого продукта.
На странице курсовые работы по менеджменту вы найдете много готовых тем для курсовых по предмету «Менеджмент».
Читайте дополнительные лекции:
- Социальная ответственность бизнеса
- Функции управленческого цикла
- Информационный менеджмент
- Сущность стратегического управления
- Правила принятия эвристических решений
- Планирование стратегических изменений
- Стратегия как внутренняя ситуационная переменная и ее влияние на организационную структуру
- Ответственность за качество управленческих решений
- Передача организационной культуры
- Менеджмент персонала