Оглавление:
Одним из основных принципов управления качеством является принятие решений, основанных на фактах. Это наиболее полно решается путем моделирования процессов, как в производстве, так и в управлении, с помощью инструментов математической статистики. Однако современные статистические методы трудно распознать и в значительной степени применить на практике без грамотного математического образования всех участников процесса. В 1979 году Союз японских ученых и инженеров (JUSE) разработал семь довольно простых в использовании визуальных методов анализа процессов. К их чести и, в частности, к чести профессора Исикавы, они сделали эти методы простыми, понятными и описательными, сделав их эффективными инструментами контроля качества. Эти методы можно понять и эффективно использовать без специальной подготовки. Несмотря на свою простоту, они по-прежнему связаны со статистикой и позволяют профессионалам использовать и, при необходимости, улучшать свои результаты.
Контрольный лист — это инструмент для первичной записи данных о продукте или производственном процессе. Контрольные списки могут использоваться для контроля как по качественным, так и по количественным характеристикам. Они заполняются непосредственно человеком, выполняющим работу при оперативном контроле (цех). Заполненные контрольные списки служат входными данными для технологов, участвующих в анализе данных.
Используются следующие типы контрольных списков:
- Контрольный список для записи измерения во время производственного процесса;
- контрольный список для записи типов несоответствий;
- Контрольный список для оценки воспроизводимости и работоспособности процесса и т.д.
Форма контрольного списка должна соответствовать ситуации. В любом случае, это должно указывать:
- объект исследования (например, название и/или чертеж изделия или части);
- таблицу сбора данных для контролируемого параметра (например, размер длины изделия или детали);
- Место проверки (мастерская, стройплощадка);
- Должность и имя сотрудника, осуществляющего сбор данных;
- Дата сбора данных;
- Продолжительность наблюдения и название контрольного устройства (если оно используется во время наблюдения).
Гистограммы — один из вариантов гистограммы, который показывает зависимость частоты показателей качества продукта или процесса, которые попадают в определенный диапазон значений.
Гистограмма построена следующим образом:
- определяется наивысшее значение показателя качества;
- определяется наименьшее значение оценки качества;
- определяет диапазон гистограммы как разницу между наибольшим и наименьшим значениями;
- определяется количество интервалов гистограммы;
- определяется длина интервала гистограммы (как коэффициент диапазона гистограммы)/(количество интервалов);
- делит диапазон гистограммы на интервалы;
- подсчитывается количество попаданий в каждом интервале;
- Частота попаданий в интервале определяется как коэффициент (количество попаданий)/(общее количество качественных показателей);
- записывается гистограмма.
Гистограмма используется для анализа статистических данных. Она дает общую информацию о воспроизводимости и стабильности технологического процесса. Гистограммы создаются технологами цеха на основе данных контрольных листов.
Гистограмма представлена серией баров одинаковой ширины, но разной высоты. Ширина полосы представляет собой интервал в диапазоне наблюдений. Высота полосы представляет собой количество наблюдений (измерений), которые попадают в этот интервал. В нормальном законе распределения данных наблюдается тенденция к тому, что большинство наблюдений находится ближе к центру распределения (по центральному значению), с постепенным уменьшением по мере их удаления от центра. Гистограмма в основном используется для анализа значений измеряемых параметров, но также может быть использована для оценки эффективности процессов.
Систематизируя показатели качества и анализируя созданную для них гистограмму, можно легко понять характер распределения, а определив среднее значение показателя и стандартное отклонение, можно сравнить показатели качества с эталонными, получив информацию высокой точности.
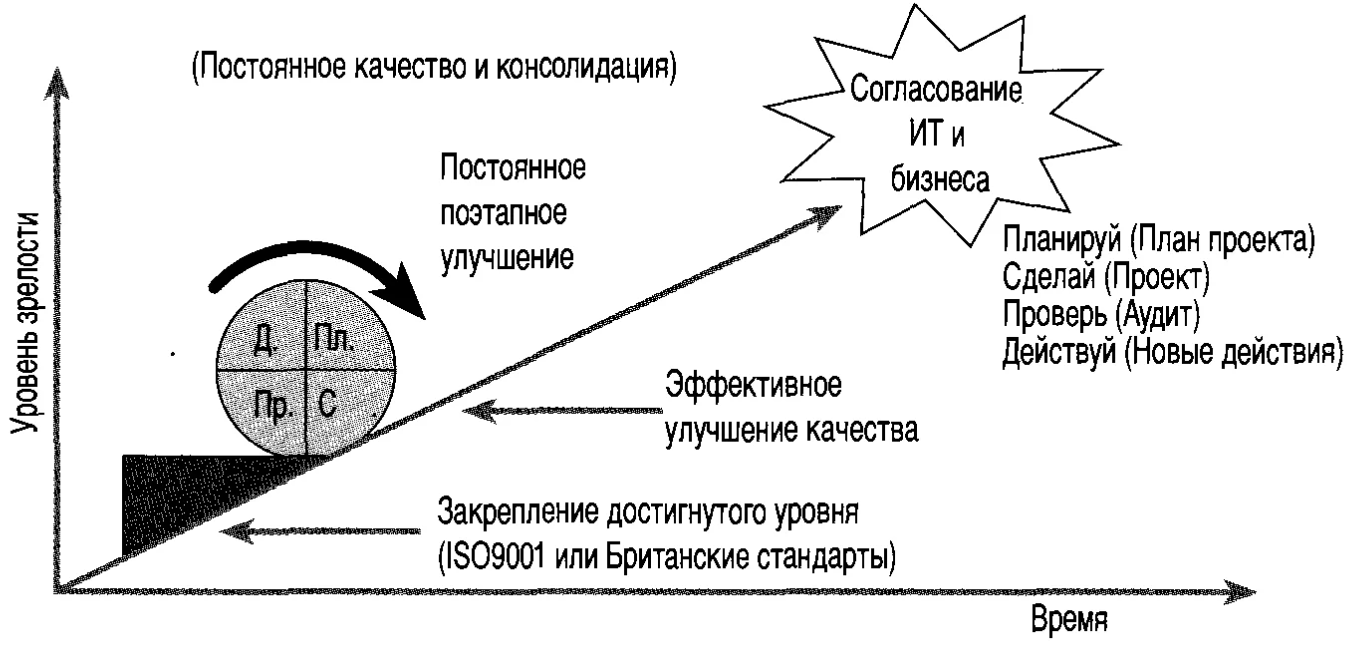
Стратификация (группировка, расслоение) статистических данных
Стратификация — это процесс сортировки данных по некоторым критериям или переменным: Результаты стратификации часто представляются в виде диаграмм и графиков. Таким образом, можно классифицировать набор данных на различные группы (или категории) с общими характеристиками, называемыми переменными стратификации. Важно указать, какие переменные следует использовать для сортировки.
Стратификация является методологической основой для других инструментов, таких как анализ Парето или графики рассеяния. Такая комбинация инструментов делает их еще более мощными. Для разделения дефектов по причинам используется стратификационная диаграмма. В машиностроении очень распространена стратификация «4M», в которой стратификационная диаграмма построена по четырем группам причин неисправностей:
- человеческие — дефекты, возникновение которых связано с действиями работника;
- Машина — дефекты, вызванные несовершенством или неправильной наладкой технологического оборудования;
- Материал — дефекты, вызванные материалами и приобретенной продукцией;
- Метод — дефекты, связанные с особенностями технологии производства или выбором заведомо неуместного метода контроля качества продукции.
Стратификационная диаграмма очень похожа на диаграмму Парето. Разница состоит в том, что в первом случае дефекты сгруппированы по причинам, а во втором — по типу.
Диаграмма причинно-следственных связей (диаграмма Исикавы). Диаграмма описывает такие компоненты качества, как «человек», «машина», «материал», «метод», «управление», «окружающая среда». По решаемой проблеме необходимо выделить для компонента «Человек» факторы, связанные с удобством и безопасностью выполнения операций; для компонента «Машина» — взаимосвязь элементов анализируемой конструкции изделия друг с другом, связанная с выполнением данной операции; для компонента «Метод» — факторы, связанные с выполнением и точностью выполняемой операции; для компонента «Материал» — факторы, связанные с отсутствием изменения свойств материалов изделия в процессе выполнения данной операции; для компонента «Контроль статистического контроля качества Паретто» — факторы, связанные с отсутствием изменения свойств материалов изделия в процессе выполнения данной операции; для компонента «Контроль статистического контроля качества Паретто
Результат процесса построения причинно-следственной диаграммы Исикава зависит от нескольких факторов, между которыми существует причинно-следственная связь. Мы можем определить структуру или природу этих многофакторных отношений посредством систематического наблюдения. Трудно решить сложные проблемы, не зная этой структуры, которая представляет собой цепь причин и результатов. В 1953 году Каоро Исикава, профессор Токийского университета, обсуждая проблему качества на заводе, обобщил мнения инженеров в виде причинно-следственной диаграммы. Ее называют «диаграммой Исикавы» (в японской литературе эту диаграмму часто называют «диаграммой рыбьих костей» или «рыбьим скелетом» из-за ее формы).
Графики рассеяния — это графики. Графики рассеяния показывают корреляцию между двумя различными факторами. Для установления связи между параметрами процесса используется график рассеяния.
Анализ Парето берет свое название от итальянского экономиста Вильфредо Парето, который показал, что большая часть капитала (80%) находится в руках небольшого количества людей (20%). Парето разработал логарифмические математические модели, описывающие это неоднородное распределение, а математик Лоренц предоставил графические представления. Правило Парето — это «универсальный» принцип, который может применяться в самых разных ситуациях, несомненно, в том числе при решении проблем качества. Джозеф Журан отметил «универсальное» применение принципа Парето к любой группе причин, вызывающих определенные последствия, с большинством последствий, вызванных небольшим количеством причин. Анализ по Парето ранжирует каждую область в порядке важности или значимости и призывает в первую очередь выявить и устранить причины, вызывающие наибольшее количество проблем (несоответствий). Анализ по Парето обычно иллюстрируется диаграммой Парето (рис. 6), на которой причины проблем качества наносятся на ось абсцисс в порядке убывания проблем, которые они вызывают, а на ось ординат — количественно — сами проблемы, как в числовом, так и в кумулятивном (накопленном) процентном выражении. График четко показывает область, в которой необходимо первоочередное действие, и разграничивает причины, которые приводят к наибольшему количеству ошибок. Поэтому превентивные меры должны быть направлены прежде всего на решение этих проблем.
Графики парето создаются технологами цехов или технологами OGT на основе данных из контрольных списков.
Налоговые карты
Контрольные диаграммы — это специальный тип диаграммы, впервые предложенный В. Шучартом (рис. 7). Они показывают характер изменений показателя качества с течением времени. Контрольные диаграммы являются важнейшим методом статистического контроля качества. Не будет преувеличением сказать, что управление качеством началось с контрольных карт Шухарта. В основе метода контрольных диаграмм лежит понятие вариабельности в рассматриваемом процессе. Любой процесс, даже хороший, подвержен некоторой вариабельности. Вариабельность может быть различной природы. Если вариабельность обусловлена только присущей ей изменчивостью системы, то можно ожидать, что результаты будут относительно стабильными и предсказуемыми. В таких случаях отклонения некоторых показателей от контрольных показателей можно считать случайными. Нет необходимости вмешиваться в процесс. Иная ситуация складывается, когда естественная вариативность накладывается на конкретную вариативность в результате деятельности людей, вовлеченных в процесс. Здесь вмешательство в процесс не только уместно, но и желательно. Более того, такое вмешательство приводит к желаемому результату самым дешевым и быстрым способом. Такой механизм, основанный на диагностическом анализе с использованием контрольных графиков Шухарта, значительно снижает риск принятия неэффективных управленческих решений.
Геничи Тагути разработал собственную систему, которая сочетает в себе инженерные и статистические методы и направлена на быстрое повышение рентабельности компании и качества продукции за счет оптимизации процессов проектирования и производства продукции. Эта методология, включающая в себя как общую философию, так и набор практических инструментов управления качеством, называется «тагучи-методом».
Тагути не согласен с общепринятым определением качества: «наличие параметров продукта в определенных пределах». Это определение предполагает, что два продукта не сильно отличаются друг от друга, если один из них близок к пределу допуска, а другой слегка выходит за его пределы. Тем не менее, первый считается «хорошим», а второй — «плохим». В отличие от традиционного подхода, методы Тагути направлены на обеспечение минимального отклонения параметров продукта от заданных, при котором не происходит увеличения стоимости за счет качества. Тагути предлагает измерять качество по количеству ущерба, нанесенного компании с момента поставки товара — чем меньше этот ущерб, тем выше качество. Его концепция обеспечения качества основана на теории потерь или ущерба из-за недостаточного качества.
Тагути предложила характеризовать выпускаемую продукцию стабильностью технических характеристик и комбинированными показателями стоимости и качества в так называемой функции потерь, согласно которой качественной продукцией считается только та продукция, показатели качества которой полностью совпадают с ее номинальными значениями, а любое отклонение от номинальной стоимости связано с некоторой потерей качества продукции. Функция одновременно учитывает потери как потребителя, так и производителя.
В первом разделе были рассмотрены семь основных (простых старых) инструментов контроля качества, большинство из которых основаны на численном анализе данных. Это соответствует принципу управления качеством «принятия решений на основе фактических данных».
Факты, однако, не всегда являются числовыми.
Принятие решений в этом случае должно основываться на знании моделей поведения человека (поведенческая наука); на знании операционного анализа; на знании статистики; на знании теории оптимизации.
В этом контексте был разработан очень полезный набор инструментов для облегчения проблем управления качеством при анализе различных типов фактов, которые в основном представлены в форме, отличной от числовой, например, словесные (устные) описания. Информацию, представленную в форме устных описаний, часто называют устной информацией.
Новые инструменты управления качеством
Эти инструменты были названы «новыми инструментами управления качеством». Эти новые инструменты включают в себя:
Мозговой штурм (рейд, осада) и атака распространения. «Мозговой штурм» используется как средство генерирования идей для выявления возможных причин ошибок и путей повышения качества. Целью «мозгового штурма» не является устранение возможных причин ошибок или путей повышения качества.
Анализ силового поля за и против процесса совершенствования, который должен быть осуществлен. Важными предпосылками успеха проекта по усовершенствованию процесса в организации являются «создание права условия для надлежащего восприятия предлагаемых изменений, а также создания благоприятного климата для их осуществления».
Когда речь идет о создании благоприятного климата для предстоящих изменений, анализ поля «за» и «против», как правило, является полезным инструментом для обеспечения позитивного восприятия ситуации и разработки плана возможных действий по ее улучшению. Инструмент здесь основан на предположении, что любая ситуация является результатом преимуществ и недостатков. Обычно эти силы находятся в состоянии равновесия до начала проекта по улучшению. Уменьшение или увеличение интенсивности действия одной из этих сил обычно приводит к осознанию (специалистами и руководителями организации и/или ведомств) необходимости инициировать и осуществлять проект по улучшению.
Диаграмма сродства — это инструмент, который идентифицирует ключевые нарушения процесса (или возможности для улучшения) путем объединения данных о вербальном сродстве, собранных в ходе «мозгового штурма». При сборе большого количества данных о различных идеях, мнениях и интересах по той или иной теме, диаграмма близости дает возможность организовать информацию в группы, основываясь на естественных связях, существующих между ними. Этот инструмент призван стимулировать творческий подход и всестороннее участие участников — членов команды. Она более эффективна в небольших группах (5-9 человек), где сотрудники привыкли работать вместе.
Диаграмма сродства — это инструмент, показывающий логические связи между ключевой идеей, проблемой и различными данными. Назначение инструмента — сопоставление причин проблем процесса, выявленных, например, по диаграмме сродства, с проблемами, которые необходимо решить. По этой причине существует некоторое сходство между диаграммой сродства и диаграммой Исикавы.
Классификация причин сбоев процесса в соответствии с их значимостью осуществляется с учетом имеющихся в распоряжении компании ресурсов, а также типовых данных, характеризующих причины. Данные, используемые в связующей диаграмме, могут быть получены (сгенерированы) с помощью сродства и диаграммы мозгового штурма. Связующая диаграмма — это, прежде всего, логический инструмент, который противопоставляет (или дополняет) связующую диаграмму.
Древовидная диаграмма — это инструмент, позволяющий систематически просматривать объект (проблему) с точки зрения составных элементов (причин) и показывающий логические (и последовательные или последовательные) связи между этими элементами (причинами).
Древовидная диаграмма строится как многоуровневая древовидная структура, составными частями которой являются различные элементы (причины, средства, способы) решения проблемы. Древовидная диаграмма используется для идентификации и представления взаимосвязи между рассматриваемым объектом (задачей) и его компонентами (элементами, причинами), например, в следующих случаях:
- когда нечетко сформулированные пожелания потребителя в отношении продукта сначала воплощаются в выявленные и предполагаемые потребности, а затем в спецификации на этот продукт;
- когда все возможные части (элементы, причины) должны быть рассмотрены по отношению к рассматриваемому предмету (проблеме);
- когда краткосрочные цели должны быть достигнуты до результатов работы в целом, например, на этапах планирования продукции, проектирования продукции и т.д.
Матричная диаграмма или таблица качества — это инструмент для определения важности различных взаимосвязей. Такие матричные диаграммы (таблицы качества) часто называют сердцем «инструментов управления качеством» и методологии QFD (Quality House).
Таблица качества используется для организации и представления большого количества данных (элементов) таким образом, что логические связи между различными элементами могут быть отображены графически, в то же время показывая важность (прочность) этих связей.
Стрелочная диаграмма
Целью матричной диаграммы является табулирование логических связей и относительной важности этих связей между большим количеством вербальных (словесных) описаний, относящихся к нижеследующему: Цели (проблемы) качества; Причины проблем качества; Требования потребителей, выявленные и предполагаемые потребности; Характеристики и функции продукции; Характеристики и функции процессов; Характеристики и функции производственных операций и оборудования.
Стрелочная диаграмма — это инструмент, позволяющий планировать оптимальные сроки всех необходимых работ для максимально быстрого и успешного достижения цели.
Использование этого инструмента рекомендуется после определения проблем, которые необходимо решить, необходимых действий, средств, графика и этапов реализации, т.е. после использования, по крайней мере, одного из инструментов, рассмотренных выше: Диаграмма аффинити; Диаграмма связей; Древовидная диаграмма; Матричная диаграмма.
Стрелочная диаграмма обычно представляет ход работы в графическом виде. Стрелочная диаграмма должна четко показывать последовательность и сроки различных этапов работы. В то же время, этот инструмент обеспечивает уверенность в том, что запланированные сроки всех работ и отдельных этапов работы оптимальны для достижения конечной цели.
Process Flow Diagram (Диаграмма потока процесса) — Этот инструмент представляет собой графическое представление этапов процесса, которое полезно для изучения возможностей улучшения путем сбора подробной информации о фактическом потоке процесса. Рассматривая, как различные этапы процесса соотносятся друг с другом, часто можно выявить потенциальные источники ошибок.
В русском переводе ISO 9004-4:93 этот инструмент называется «картой процесса». Карты процессов могут быть применены ко всем аспектам любого процесса, начиная с этапа исследования рынка и заканчивая продажами, установкой и послепродажным обслуживанием.
Программная диаграмма принятия решений по процессу (PDPC). Данный инструмент (PDPC) представляет собой диаграмму, которая очень похожа на диаграмму технологического процесса (карту процесса), рассмотренную выше. Схема технологической программы обычно показывает последовательность действий и решений, необходимых для достижения желаемого результата. Диаграмма PDPC может быть использована для оценки сроков и осуществимости мероприятий по выполнению программы, например, по диаграмме со стрелкой Ганта, как до, так и во время выполнения этих мероприятий (с возможными корректировками графика выполнения).
Матрица приоритетов (матричный анализ данных) — 10, 41] является инструментом обработки больших объемов числовых данных, полученных при построении матричных диаграмм (таблиц качества) с целью идентификации приоритетных данных.
Рассматриваемый здесь инструмент требует серьезных статистических знаний. Поэтому матрица приоритетов (матричный анализ данных) используется гораздо реже, чем новые инструменты управления качеством, рассмотренные выше.
Новые инструменты — это средства для решения задач, рассматриваемых в теории TQM. Эти инструменты можно наиболее успешно использовать в рамках групповой работы в командах, сформированных в организациях для поиска и разработки решений проблем качества. Новые инструменты управления качеством, о которых речь пойдет ниже, являются основой для новой процедуры преобразования требований заказчика сначала в параметры качества продукции, которую он ожидает, а затем в параметры качества процессов, используемых для производства этой продукции. Эта последняя процедура, которая была разработана и впервые применена в Японии на верфи Mitsubishi Heavy Industries в Кобе, теперь называется Развертывание Функции Качества (QFD). Из-за специфической формы матричной диаграммы, используемой в процессе QFD, этот процесс часто называют «Домом качества».
На странице курсовые работы по менеджменту вы найдете много готовых тем для курсовых по предмету «Менеджмент».
Читайте дополнительные лекции:
- Социально-ответственное поведение как основа развития современной компании
- Управленческий контроль, его формы и методы
- Информационные технологии в управлении проектами
- Функции менеджмента в отделе продаж
- Бедо Шарль, исследователь в области производственного менеджмента
- Теория справедливости Дж. Стейси Адамса
- Алгоритм разработки управленческого решения
- Различные модели менеджмента
- Развитие теории и практики менеджмента
- Жизненный цикл организации: сущность и основные этапы