Оглавление:
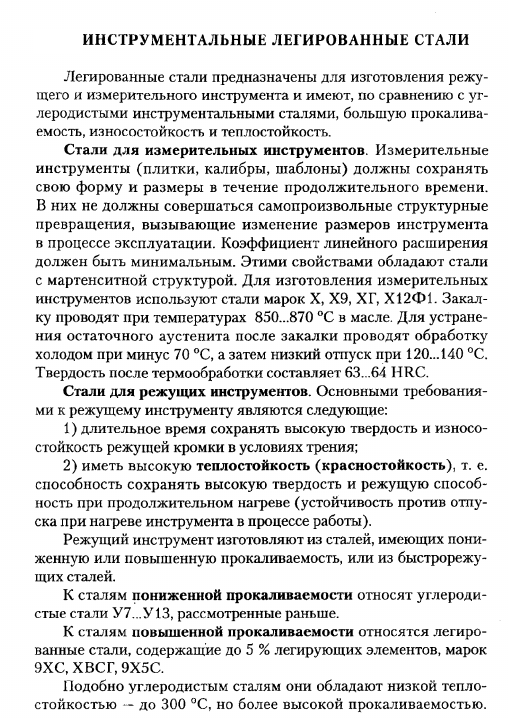
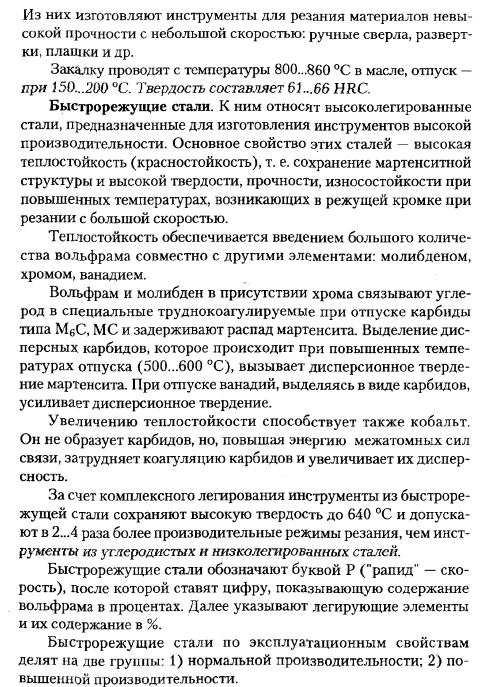
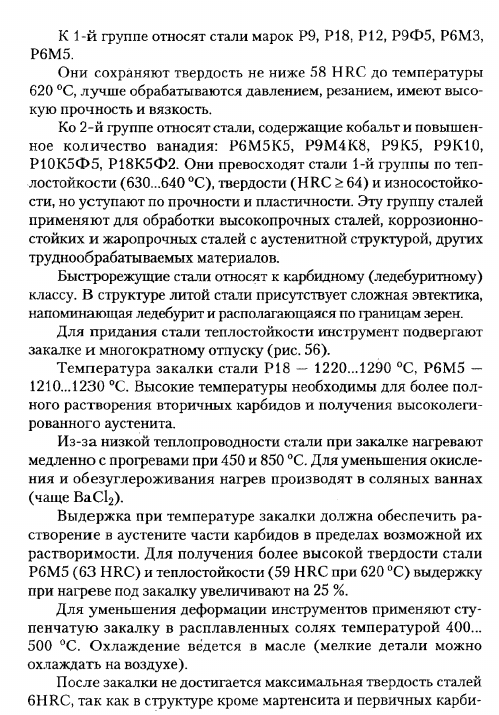
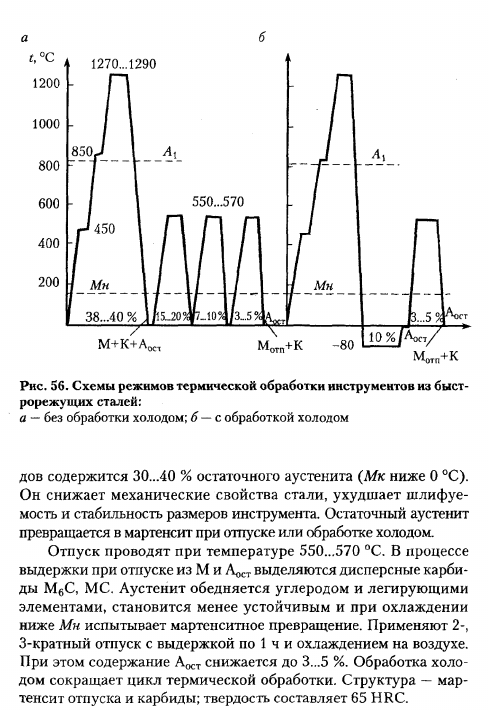

Инструментальные легированные стали
- Легированная сталь для приборостроения Легированная сталь предназначена для изготовления режущего и измерительного инструмента и обладает повышенной рохалимостью, износостойкостью и термостойкостью по сравнению с углеродистой инструментальной сталью.
Сталь для измерительных инструментов. Измерительный прибор (плитка, Калибр, шаблон) должен сохранять свою форму и размеры в течение длительного времени. Они не должны подвергаться спонтанным структурным преобразованиям, вызывающим изменение размеров инструмента в процессе эксплуатации.
Коэффициент линейного расширения должен быть минимальным. Этими свойствами обладают мартенситные стали. Людмила Фирмаль
Используйте стальную ранг X, X9, XI ’и X12F1 для того чтобы изготовить вашу аппаратуру. Закалку проводят при температуре 850-870°С в oil. In для удаления остаточного аустенита после закалки проводят холодную обработку при минус 70°С, а затем низкотемпературный отпуск при 120-140 ° С.
твердость после термообработки составляет 63-64 HRC. Сталь для режущего инструмента. Основными требованиями к режущему инструменту являются: 1)долгое время для поддержания высокой твердости и износостойкости режущей кромки в состоянии трения: 2) обладает высокой термостойкостью (покраснением), то есть способностью сохранять высокую твердость и режущую способность при длительном нагреве(стойкость к отпуску при нагреве инструмента в процессе эксплуатации).
- Режущие инструменты изготавливаются из закаленной или улучшенной стали или быстрорежущей стали. Низкий-закаленная сталь была ранее считались У7… Она включает сталь углерода U 13. Высоко-закаливаемые стали включают легированные стали с до 5% сплавляя рангом, рангом 9ХС, хвсг и 9×5с.
Как и в случае с углеродистой сталью, она обладает низкой термостойкостью и температурой до 300°С, но при этом обладает высокой прокаливаемостью, что создает инструмент для резки материалов с низкой скоростью и низкой прочностью. Сверла руки, reaming, умирают, etc. Тушение проводят в масле при температуре 800… Он работает при температуре 860°C и имеет температуру 150… Закалять на 200 ° C твердость от 61 до 66 HRC. Быстрорежущая сталь. К ним относятся высоколегированные стали,
которые предназначены для производства высокопроизводительного инструмента. Людмила Фирмаль
Основным свойством этих сталей является высокая термостойкость (Красная стойкость), то есть мартенситная структура и высокая твердость, прочность и износостойкость при высоких температурах, создаваемые режущей кромкой при резании на высоких скоростях. Термостойкость обеспечивается введением большого количества вольфрама вместе с другими элементами, такими как молибден, хром и ванадий. В присутствии хрома, вольфрама и молибдена связываются со специальными карбидами типа M6C, MS, с carbon. It затвердевает при отпуске и трудно замедляет распад мартенсита. Осаждение дисперсных карбидов, происходящее при высоких температурах отпуска (500-600 ° С), вызывает дисперсное упрочнение мартенсита.
При отпуске ванадий, который выделяется в виде карбида, усиливает дисперсное упрочнение. Кобальт также способствует улучшению тепла resistance. It не образует карбидов, но увеличивает энергию межатомных сил связи, затрудняет затвердевание карбидов и увеличивает их дисперсность. Благодаря сложному легированию, инструменты из быстрорежущей стали сохраняют высокую твердость до 640°С, что делает режим резания в 2-4 раза более производительным, чем из углеродистой стали и низколегированной стали. Быстрорежущая сталь обозначается буквой P («High Speed» — скорость), после чего приводится цифра, указывающая долю вольфрама. displayed.
In кроме того, он показывает легирующие элементы и их содержание в%. Быстрорежущую сталь по эксплуатационным характеристикам можно разделить на 2 группы.1) нормальная производительность. 2) улучшенная производительность. В 1-й группе относятся стали марок Р9, Р18,Р12,P9F5,P6MZ, Р6М5. Он сохраняет твердость по крайней мере 620 HRC на температуре 58°C, и хорошо обработан давлением, вырезыванием, и имеет высокопрочное и выкостность. 2-ой группе относятся стали, содержащие кобальт и повышенное количество ванадия: р6м5к5,Р9М4К8,Р9К5,Р9К10,Р10К5Ф5,Р18К5Ф2.
Он превосходит группу 1 Сталь по термостойкости (630-640°С), твердость (HRC£64) и износостойкости, но уступают по прочности и пластичности. Эта группа сталей используется для обработки высокопрочных сталей, коррозионно-стойких и жаропрочных сталей аустенитной конструкции и других труднообрабатываемых материалов. Быстрорежущая сталь относится к карбидному (восстанавливаемому) классу.
Структура литой стали имеет сложную эвтектическую, аналогичную восстановительной, расположенную вдоль границ зерен. Чтобы придать стали термостойкость, инструмент закаляют и закаляют многократно (рис. 56). Температура закалки стали составляет P18-1220… 1290°С, Р6М5-1210… 1230°С. Более высокие температуры необходимы для более полного плавления вторичных карбидов и образования высоколегированного аустенита. Благодаря низкой теплопроводности стали, она медленно нагревается во время закалки Однако нагревание при 450 и 850°С для уменьшения окисления и обезуглероживания проводят в соляных ваннах (чаще всего бак^). Выдержка при температурах закалки должна обеспечивать
растворение некоторых карбидов в аустените в пределах возможной растворимости. Для получения более высокой твердости Р6М5 сталь (63 HRC) и теплостойкие (620°C до 59 СПЧ), нагрев для закалки увеличивается на 25%. Для уменьшения деформации инструмента применяют ступенчатую закалку расплавленной соли с температурой 400-500°С. Охлаждение производится в масле(мелкие детали можно охлаждать на воздухе). После гасить, оно не достигает максимальную твердость стали 6HRC. Это кроме мартенсита и первичных карбидов в ткани、 Рис.56.Схема режима
термообработки инструмента из быстрорежущей стали: -нет холодная обработка: б-холодная лечение Вода содержит 30-40% остаточного аустенита (L / C ниже 0°C).Механические свойства стали снижаются, что снижает шлифовальную способность и размерную стабильность инструмента. Остаточный аустенит преобразуется в мартенсит во время отпуска или холодной обработки.
Отпуск — это 550… В процессе обработки старением при отпуске из м выделяются дисперсные карбиды M6C и MS, которые протекают при температурах 570°С. аустенит подвергается мартенситному превращению при обеднении углерода и легирующих элементов, менее устойчив и менее MN охлаждается. Выдержите 2 часа, 3 часа отпуска на 1 час, и после этого охладьте в air. In в этом случае содержание а ^снижается до 3-5%.Обработка низкой температуры сократит цикл термической обработки. Структура-отпущенный мартенсит и карбиды, твердость 65 НRС.
Смотрите также:
Металлокерамические твердые сплавы | Хромоникелевые стали |
Твердые и сверхтвердые материалы | Жаропрочные стали |