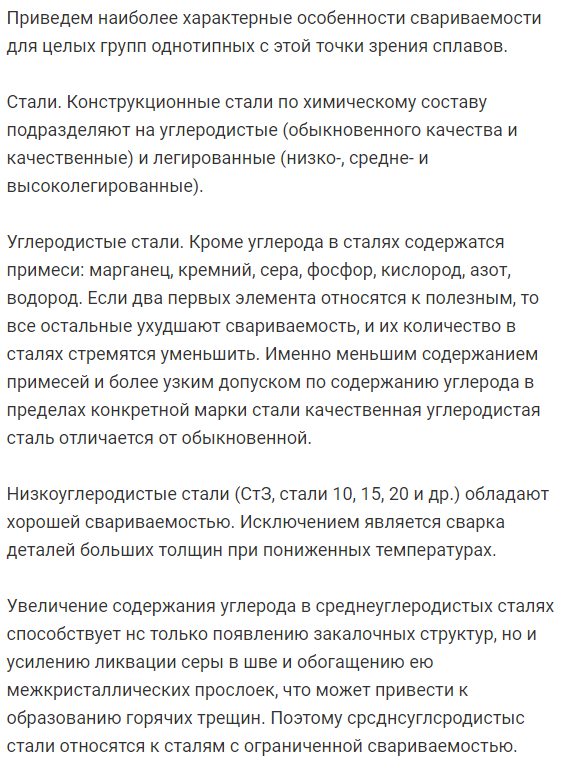
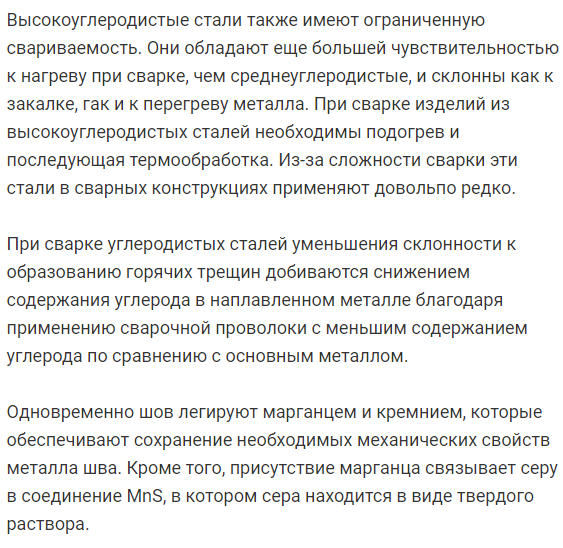
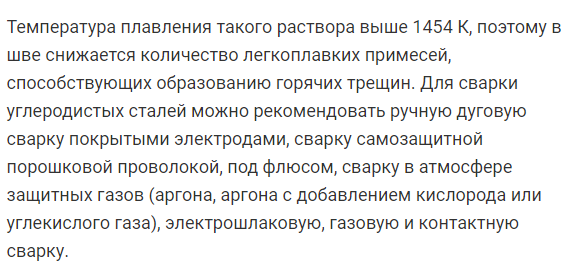
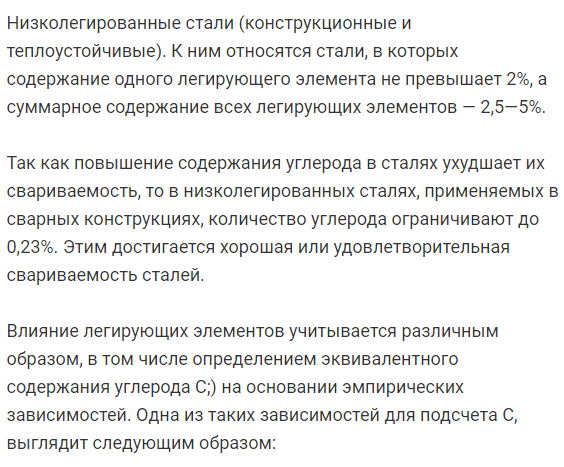

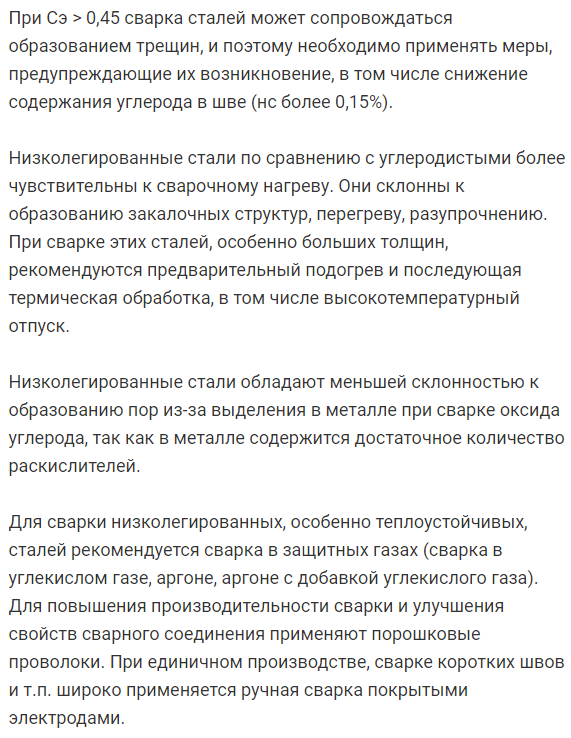
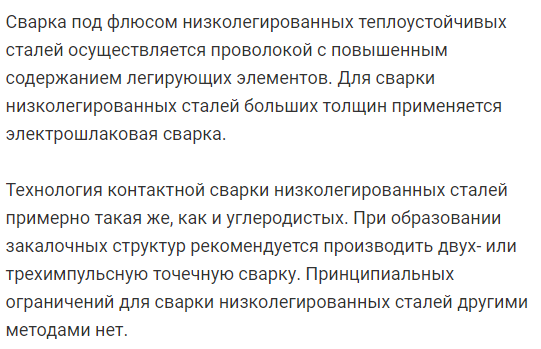

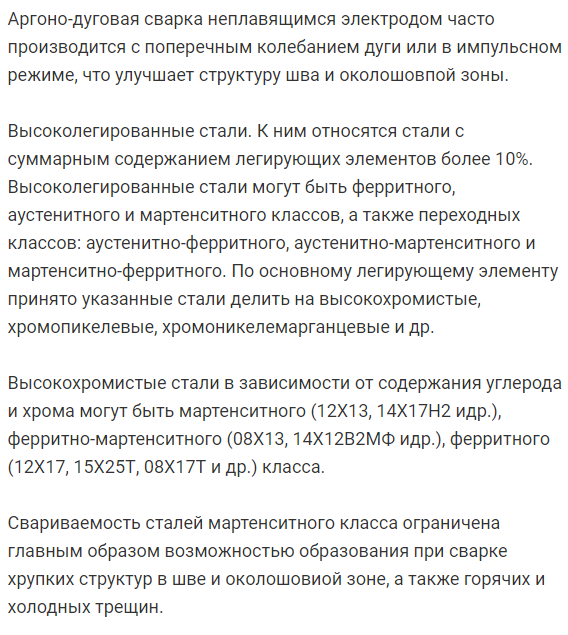
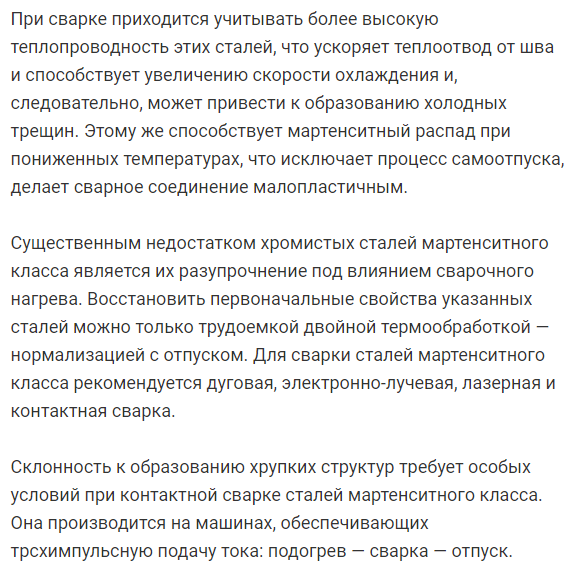
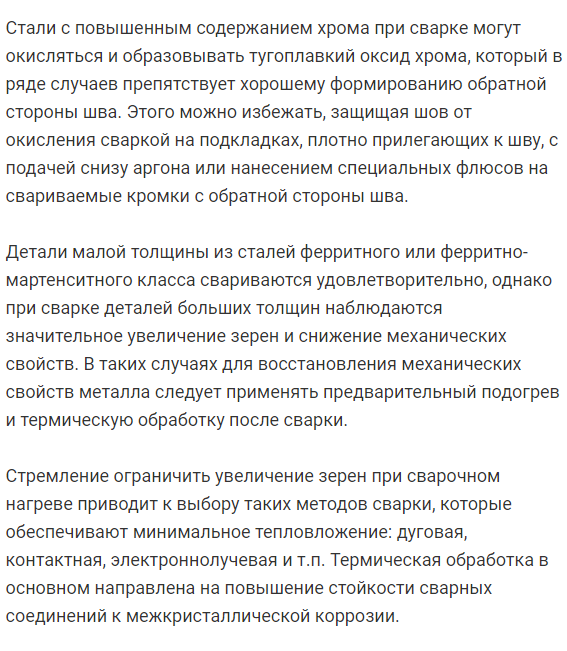
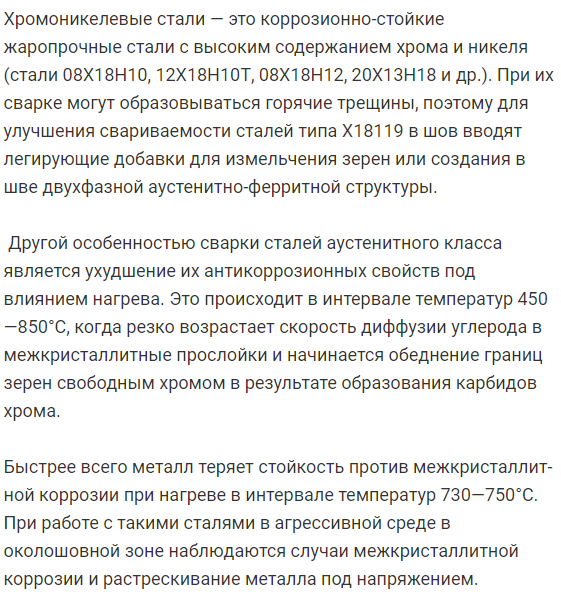
С этой точки зрения он показывает наиболее характерные особенности свариваемости всей группы сплавов одного типа.
- Сталь. Конструкционные стали классифицируются в соответствии с их химическим составом: углерод (нормальное и высокое качество) и легирующие (низкие, средние и высокие сплавы).
Углеродистая сталь Помимо углерода в стали содержатся примеси: марганец, кремний, сера, фосфор, кислород, азот и водород. Когда первые два элемента полезны, все остальные элементы имеют тенденцию ухудшать свариваемость и уменьшать количество сталей. Что делает высококачественную углеродистую сталь необычной, так это низкое содержание примесей в некоторых марках стали и узкий допуск на содержание углерода.
Свариваемость низкоуглеродистой стали (СтЗ, сталь 10, 15, 20 и т. Д.) Хорошая.
Исключением является сварка толстых деталей при низких температурах.
Увеличение содержания углерода в среднеуглеродистой стали не только способствует появлению закаленной структуры, но также увеличивает сегрегацию серы в сварном шве и тем самым концентрирует межкристаллические слои, тем самым образуя горячие трещины. Есть возможность подключения. Следовательно, сталь srsdnsuglsrodistyss относится к стали с ограниченной свариваемостью.
Свариваемость высокоуглеродистой стали также ограничена. Они более чувствительны к теплу во время сварки, чем среднеуглеродистые, и подвержены закалке, зацеплению и перегреву металла. При сварке изделий из высокоуглеродистой стали требуется нагрев и последующая термообработка. Из-за сложности сварки эти стали редко используются в сварных конструкциях.
При сварке углеродистой стали использование сварочной проволоки с более низким содержанием углерода, чем у основного металла, снижает содержание углерода в наплавленном металле, тем самым уменьшая тенденцию к образованию горячих трещин.
В то же время швы легированы марганцем и кремнием, чтобы обеспечить поддержание требуемых механических свойств металла шва. Кроме того, когда присутствует марганец, сера связывается с соединением MnS, и сера становится твердым раствором.
Поскольку температура плавления таких растворов выше, чем 1454 К, количество легкоплавких примесей, которые способствуют образованию горячих трещин в сварном шве, уменьшается. Для сварки углеродистой сталью, ручной дуговой сварки с использованием покрытых электродов, самоэкранированной порошковой проволоки, дуговой сварки под флюсом, сварки в среде защитного газа (аргон, кислород или диоксид углерода в аргон), электрошлаковой, газовой и контактной сварки я рекомендую
Низколегированная сталь (структура и термостойкость). К ним относятся стали, в которых содержание одного легирующего элемента не превышает 2%, а общее содержание всех легирующих элементов составляет 2,5-5%.
Увеличение содержания углерода в стали ухудшает свариваемость, поэтому в низколегированных сталях, используемых в сварных конструкциях, содержание углерода ограничено 0,23%. Это приводит к хорошей или удовлетворительной свариваемости стали.
- Эффекты легирующих элементов могут быть приняты во внимание различными способами, такими как определение эквивалентного содержания углерода C;) на основе эмпирической зависимости. Одна из этих зависимостей для подсчета C:
Если Ce> 0,45, сварка стали может привести к образованию трещин, поэтому необходимо принять меры для предотвращения таких явлений, как снижение содержания углерода в сварном шве (более 0,15%). ,
По сравнению с углеродистой сталью низколегированная сталь более чувствительна к сварочному теплу. Они склонны к образованию закалочных структур, перегреву и размягчению. При сварке этих сталей, особенно если они толстые, мы рекомендуем предварительный нагрев с высокой температурой отпуска и последующую термообработку.
Поскольку металл содержит достаточное количество поглотителя кислорода, низколегированные стали с меньшей вероятностью будут образовывать поры, потому что окись углерода выделяется в металл во время сварки.
Сварка защитным газом (сварка углекислым газом, аргоном, аргоном с добавлением углекислого газа) рекомендуется для сварки жаропрочных сплавов, особенно жаропрочных сталей. Порошковая проволока используется для повышения производительности сварки и улучшения свойств сварного соединения.
Широко используется для одиночного производства и сварки коротким швом ручная сварка покрытыми электродами.
Дуговая сварка под флюсом из низколегированной жаропрочной стали выполняется с помощью проволоки с высоким содержанием легирующих элементов. Электрошлаковая сварка используется для сварки толстых низколегированных сталей.
- Технология контактной сварки низколегированной стали практически такая же, как и углеродистая. Если сформирована закаленная структура, рекомендуется выполнять 2 или 3 импульсную точечную сварку.
- Не существует принципиальных ограничений для сварки низколегированных сталей другими методами.
- Среднелегированная сталь. Содержание легирующих элементов в этих сталях составляет 2-5%, а общее содержание всех элементов — 5-10%. Эти стали относятся к классу перлитов (25ХГСА, ЗОХГСА, 35ХГСА и др.) Или мартенсита (30ХГ2Н2СВМА, 30Х2НМФА и др.).
В целом, оценивается, что свариваемость легированной стали srsd ограничена. При сварке необходимо учитывать повышенную чувствительность к нагреву сварного шва и склонность к образованию горячих и холодных трещин. В частности, если задача состоит в том, чтобы достичь такой же прочности, как у основного металла, вероятность растрескивания возрастает с увеличением требований к прочности сварного шва.
Основными методами сварки среднелегированной стали являются диоксид углерода, аргонная сварка (включая сварку расходуемыми электродами с добавлением 5-10% кислорода или диоксида углерода), дуговая сварка под флюсом, ручная сварка покрытыми электродами, электрошлаки, электронные Лучевая и плазменная сварка.
Аргонодуговая сварка неплавящимися электродами часто выполняется в режиме поперечных колебаний дуги или в импульсном режиме, что улучшает структуру шва и зоны вблизи сварного шва.
Высоколегированная сталь. К ним относятся стали с общим содержанием легирующих элементов, превышающим 10%. Высоколегированные стали включают феррит, аустенит и мартенсит, а также аустенит-феррит переходного класса, аустенит-мартенсит и мартенсит-феррит. По основным легирующим элементам принято разделять эти стали на хром, никель хром, марганец хромоникель и т. Д.
В зависимости от содержания углерода и хрома высокохромистые стали относятся к классам мартенсита (12X13, 14X17H2 и т. Д.), Феррит-мартенсита (08X13, 14X12V2MF и т. Д.) И феррита (12X17, 15X25T, 08X17T и т. Д.).
- Свариваемость мартенситной стали в основном ограничена образованием хрупких структур во время и вблизи сварного шва и возможностью возникновения горячих и холодных трещин во время сварки.
При сварке необходимо учитывать более высокую теплопроводность этих сталей. Это способствует отводу тепла от сварного шва и способствует увеличению скорости охлаждения и, следовательно, может привести к образованию холодных трещин. Этому способствует также разложение мартенсита при низких температурах, что исключает процесс самообжигания и снижает гибкость сварного соединения.
Серьезным недостатком мартенситной хромистой стали является то, что она размягчается под воздействием тепла сварки. Первоначальные свойства этих сталей могут быть восстановлены только путем громоздкой двойной термической обработки — нормализации путем отпуска. Для сварки мартенситной стали рекомендуется дуговая сварка, электронно-лучевая сварка, лазерная сварка и контактная сварка.
В связи с тенденцией к образованию хрупких конструкций особые условия требуются для контактной сварки мартенситной стали. Это произведено на машине, которая обеспечивает трехимпульсную подачу тока: нагрев, сварка, отпуск.
Стали с высоким содержанием хрома во время сварки могут окисляться с образованием тугоплавкого оксида хрома и в некоторых случаях препятствовать хорошему образованию на задней стороне сварного шва. Этого можно избежать путем сварки подкладки по шву, защиты шва от окисления, подачи аргона снизу или применения специального флюса к кромке сварного шва с обратной стороны шва.
Тонкие срезы ферритных или ферритно-мартенситных сталей хорошо свариваются, но при сварке толстых сечений наблюдается значительное увеличение кристаллических зерен и снижение механических свойств. В таких случаях для восстановления механических свойств металла необходимо использовать предварительный нагрев и термообработку после сварки.
Стремление ограничить рост зерна при сварочном нагреве приводит к выбору способов сварки, обеспечивающих минимальный подвод тепла: дуга, контакт, электронный луч и т. Д. Основное назначение термообработки — повысить устойчивость сварных соединений к межкристаллитной коррозии.
Никель-хромистая сталь — это коррозионно-стойкая и жаростойкая сталь с высоким содержанием хрома и никеля (сталь 08Х18Н10, 12Х18Н10Т, 08Х18Н12, 20Х13Н18 и др.). Следовательно, во время сварки может возникать горячее растрескивание, чтобы улучшить свариваемость стали типа Х18119. Легирующие добавки вводятся в шов для полировки зерен и формирования двухфазной аустенитной ферритовой структуры в шве.
別 Другой характеристикой сварки аустенитной стали является ухудшение антикоррозионных свойств под воздействием нагрева. Это происходит в интервале температур от 450 до 850 ° С, где скорость диффузии углерода в межкристаллический слой резко возрастает, и в результате образования карбида хрома истощение границ зерен начинается со свободного хрома.
Наиболее быстро металлы теряют свою устойчивость к межкристаллитной коррозии при нагревании в диапазоне температур 730-750 °. Когда такие стали используются в агрессивных средах в зонах термического влияния, наблюдаются случаи межкристаллитной коррозии и растрескивания под напряжением металла.
Смотрите также:
Примеры решения задач по материаловедению
Прессование. | В чем преимущества эвтектических композитов по сравнению с искусственными |
Монокристаллическое литье. | Пайка конструкционных сталей. |