Принципы построения единой системы допусков и посадок
Создание современных механизмов, их эксплуатация, ремонт и техническое обслуживание невозможно без использования принципа взаимозаменяемости. Взаимозаменяемость — свойство независимо изготовленных деталей или сборочных единиц обеспечивать у механизмов и машин работоспособное состояние при сборке и ремонте без специальной подгонки. Взаимозаменяемыми могут быть отдельные детали (гайки, винты, болты и др.). сборочные единицы (подшипники качения, некоторые узлы механизмов), а также изделия в целом. Наиболее применимой является полная взаимозаменяемость, когда сборка осуществляется без дополнительной обработки и пригонки. Это дает возможность отдельные детали и узлы изготовлять на одних, специализированных, заводах или цехах серийного или массового производства, а сборку осуществлять на других. При массовом производстве снижается стоимость деталей за счет автоматизации технологических процессов.
Иногда по техническим требованиям допуски на размеры деталей необходимо выдерживать настолько малыми, что это становится нецелесообразным экономически или их трудно выполнить технически. Тогда для получения требуемой точности детали, изготовленные на обычном оборудовании с большими допусками, сортируют на размерные группы, в которых допуски уменьшаются до нужных значений. Сборка деталей осуществляется отдельно по каждой размерной группе (селективная сборка). Такая взаимозаменяемость называется неполной (ограниченной) и может быть использована только по отдельным геометрическим параметрам, например при сборке подшипников качения, резьбовых соединений с натягом и других высокоточных изделий.
Взаимозаменяемость обеспечивается системой допусков и посадок, нормированных системой стандартов. «Единая система допусков и посадок» (ЕСДП) регламентирует допуски размеров гладких элементов деталей и посадки, образуемые при их соединении; «Основные нормы взаимозаменяемости» (ОНВ) устанавливают допуски и посадки соединений (резьбовых, конических, шпоночных, шлицевых) и зубчатых передач и колес.
Основные определения. Основные термины и определения установлены ГОСТом 25346-82.
Две или несколько подвижно или неподвижно соединенных деталей называются сопрягаемыми. В соединении деталей, входящих одна в другую, имеются наружные (охватываемые) и внутренние (охватывающие) поверхности. В соответствии с этим вводятся два термина: вал -для обозначения наружных (охватываемых) поверхностей (), отверстие — для обозначения внутренних (охватывающих) поверхностей (
). Эти поверхности могут быть не только цилиндрическими, но и плоскими параллельными поверхностями (например, шпонка и паз на валу).
Номинальный размер ( и др.) — размер, служащий началом отсчета отклонений, относительно которого определяются предельные размеры. Он является общим для отверстия и вала, образующих соединение, и устанавливается либо из условия обеспечения прочности или жесткости, либо из конструктивных соображений. Для снижения номенклатуры режущего инструмента полученные значения номинальных размеров округляют в большую сторону в соответствии со значениями, указанными в ГОСТе 6636-69 «Ряды нормальных линейных размеров». Предусмотрено четыре ряда нормальных размеров
и
(табл. 3.1), составленных на основе рядов предпочтительных чисел (ГОСТ 8032-84) и представляющих собой десятичные ряды геометрических прогрессий со знаменателями: для ряда
для ряда
для ряда
для ряда
. В табл. 3.1 приведены нормальные линейные размеры в диапазоне 1-380 мм. При выборе размеров предпочтение должно быть отдано рядам с более узкой градацией (ряд
следует предпочесть
и т. д.). Размеры, установленные стандартами на конкретные изделия (средний диаметр резьбы и др.), могут не соответствовать ГОСТу 6636-69.
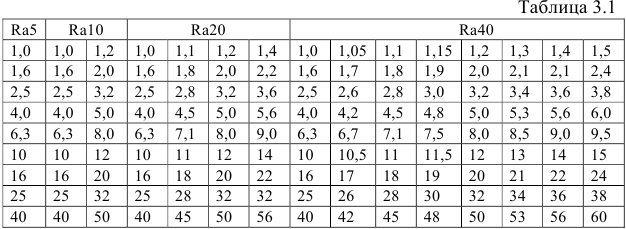

Действительный размер — размер, установленный непосредственным измерением с допускаемой погрешностью. С целью исключения брака при механической обработке размеры сопрягаемых поверхностей выполняют с определенным допуском. Для наглядности расположения полей допусков принято их одностороннее расположение (рис. 3.1). Действительный размер лежит между наибольшим и наименьшим
предельными размерами. На чертежах указываются не предельные размеры, а номинальный размер с предельными отклонениями.
Верхнее предельное отклонение — алгебраическая разность между наибольшим предельным и номинальным размерами:

Нижнее предельное отклонение — алгебраическая разность между наименьшим предельным и номинальным размерами:

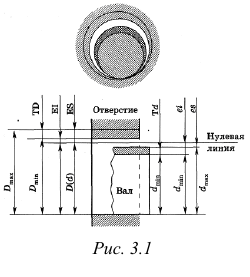
Отклонения могут быть положительными, отрицательными или равными нулю. На чертежах рядом с номинальным размером указываются предельные отклонения в миллиметрах. Отклонения, равные нулю, не указываются; если верхнее и нижнее отклонения равны, т. е. допуск симметричен, их значения указывают после знака «±».
Высота цифр отклонений равна примерно половине высоты цифр номинального размера. Например:
Допуск (от латинского Tolerance) — разность между наибольшим и наименьшим предельными размерами или абсолютное значение алгебраической разности между верхним и нижним отклонениями:

Величина допуска всегда положительна. При графическом изображении поле допуска располагается между верхним и нижним отклонениями и может размещаться выше, ниже или симметрично относительно нулевой линии. За нулевую принимают линию, соответствующую номинальному размеру, которая служит началом отсчета отклонений.
Посадка — характер соединений, определяемый Величиной зазоров или натягов. В зависимости от взаимного расположения полей допусков различают посадки трех видов: с зазором, с натягом и переходную.
Посадка с зазором — посадка, при которой в соединении обеспечивается гарантированный зазор. Это возможно при расположении поля допуска отверстия выше поля допуска вала (рис. 3.2, а).
Посадка с зазором характеризуется величинами наибольшего и наименьшего
зазоров:

К посадкам с зазором относятся также посадка, у которой = 0.
Посадка с натягом — посадка, при которой в соединении обеспечивается гарантированный натяг, поле допуска вала расположено выше поля допуска отверстия (рис. 3.2, б). Значения наибольшего наименьшего
натягов определяют по формулам:

Переходная посадка — посадка, при которой в соединении возможно появление как зазора, так и натяга. Поля допусков отверстия и вала перекрываются полностью или частично (рис. 3.2, в).
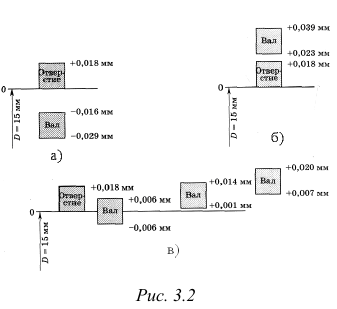
Единая система допусков и посадок — закономерно построенная совокупность допусков и посадок. Система предназначена для выбора рациональных значений допусков, характеризующих точность изготовления деталей. Малые значения допусков затрудняют процесс изготовления деталей и, соответственно, повышают себестоимость изделия, поскольку ужесточаются требования к точности станочного оборудования и квалификации рабочих. По мере уменьшения допуска относительная себестоимость С возрастает по гиперболе. На рис. 3.3 показана зависимость относительной стоимости изготовления детали от величины допуска Т. Буквами отмечены виды обработки детали: А — холодное волочение, В -обтачивание на токарном станке, С — обтачивание и шлифование, Б -обтачивание, шлифование и притирка.
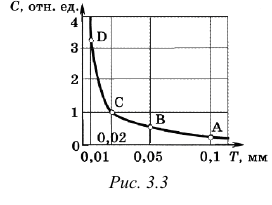
Большие допуски снижают точность изготовления и, как следствие, качество изделия, его надежность и долговечность. Поэтому рациональными значениями допусков являются максимально возможные, при которых изделие полностью соответствует своему функциональному назначению и требованиям, предъявляемым к нему (работоспособности, надежности, технологичности, экономичности и др.). Единая система допусков и посадок позволяет стандартизовать режущие инструменты и калибры, упрощает конструирование, производство изделий и повышает их качество.
Для нормирования уровня точности введены 19 квалитетов в порядке снижения точности, которые обозначаются номерами 0,1; 0; 1; 2;… 17. Самой высокой точности соответствует квалитет 0,1, самой низкой — 17. Квалитет — совокупность допусков с постоянной относительной точностью. Обозначается допуск того или иного квалитета сочетанием букв IT с номером квалитета, например IT7 — допуск седьмого квалитета. Допуски квалитетов 0,1; 0 и 1 предназначены для плоскопараллельных концевых мер длины; 2; 3 и 4 — для гладких калибров пробок и калибров скоб; 5 и 6 — для размеров деталей высокоточных соединений (подшипники качения, шейки коленчатых валов, шпиндели высокоточных станков и т. п.). Наиболее распространенными являются ква-литеты 7 и 8, которые используют для ответственных соединений в машиностроении, авиационной технике, автомобилестроении, станкостроении. Размеры деталей сельскохозяйственной техники, подъемно-транспортного оборудования, текстильных машин выполняют по квалитету 9. Для деталей, изготовленных литьем и штамповкой, а также допусков на свободные размеры деталей механизмов авиационной и космической техники используют квалитет 12. Допуски на размеры в деталях общего машиностроения назначают по квалитетам 13-17.
Величины допусков зависят от номинального размера и для близких измерений мало различаются. Поэтому весь ряд линейных размеров 1-10000 мм разбит на 26 интервалов (1-3, 3-6, 6-10 и т. д.), в пределах которых единица допуска 1 определяется по формуле

где — среднее геометрическое крайних размеров каждого интервала.
Допуск для любого квалитета

где — номер квалитета;
— безразмерный коэффициент, установленный для каждого квалитета.
Расположение поля допуска определяется основным отклонением, за которое в ЕСДП принято отклонение, ближайшее к нулевой линии. Установлено 28 основных отклонений, обозначаемых буквами латинского алфавита (рис. 3.4) прописными буквами (от до
) — отклонения для валов, а строчными буквами (от
до
) — для отверстий. Каждая буква представляет ряд основных отклонений, зависящих от интервала номинальных размеров.
Прочность рассчитываемой детали оценивают по наименьшему из запасов, полученных по соответствующим формулам в том и другом случаях.
Отклонения от до
используют для образования посадок с зазором; от
до
— переходных посадок; от
до
— посадок с натягом.
Поле допуска образуется сочетанием основного отклонения с допуском по выбранному квалитету и обозначается буквой основного отклонения и цифрой квалитета (например, для вала
для отверстия
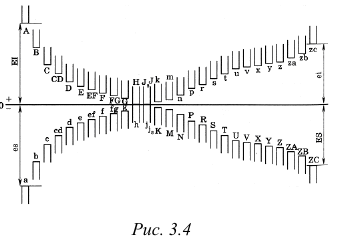
На чертежах предельные отклонения размеров указываются одним из трех способов: условными (буквенными) обозначениями; числовыми значениями в миллиметрах или комбинированным образом, при котором за условным обозначением в скобках указываются числовые значения. Например:

Предельные отклонения должны назначаться для всех размеров, указанных на чертеже, включая несопрягаемые и неответственные. Отклонения для размеров валов и отверстий могут быть как односторонними, так и симметричными, для линейных размеров — только симметричными.
Если предельные отклонения не указаны на чертеже непосредственно после значения размера, они называются неуказанными предельными отклонениями и оговариваются в технических требованиях чертежа. Неуказанные предельные отклонения нормируют либо квалитета-ми (от 12 до 17), обозначенными IT, либо классами точности: «точный» «средний»
«грубый»
«очень грубый»
. В технических требованиях чертежа запись может быть сформулирована следующим образом:
«Неуказанные предельные отклонения размеров: или
Посадки на сборочных чертежах обозначают сочетанием полей допусков отверстия и вала одним из трех способов:
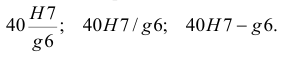
В числителе или на первом месте указывается отклонение для отверстия, в знаменателе или на втором месте — отклонение для вала. Наиболее употребимым является первый способ обозначения.
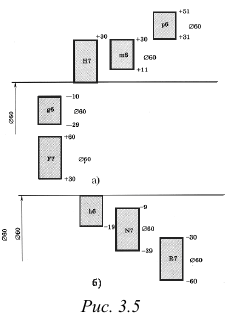
Назначаются посадки в ЕСДП по двум системам: посадки в системе отверстия, в которых различные зазоры и натяги получают соединением различных валов (например, ) с основным отверстием
(рис. 3.5, а); посадки в системе вала, в которых различные зазоры и натяги получают соединением различных отверстий (например,
) с основным валом (рис. 3.5, б). Предельные отклонения на рис. 3.5 указаны в микрометрах.
По экономическим соображениям более предпочтительной является система отверстия. Изготовить вал с любым предельным отклонением можно одним режущим инструментом. При выполнении отверстия заданного номинального размера для каждого отклонения требуется свой режущий инструмент. Поэтому назначение посадок в системе отверстия, когда для образования любой посадки используется только одно отклонение , позволяет сократить число типоразмеров режущего инструмента. Для размеров 1-3150 мм допуск отверстия назначают на один-два квалитета больше допуска вала, так как точное отверстие получить труднее, чем точный вал. При размерах менее 1 мм вал технологически обработать труднее, чем отверстие, в этих случаях допуски отверстия и вала принимают одинаковыми. В некоторых случаях возможно применение комбинированных посадок, образованных из основных отклонений, предусмотренных ЕСДП, например, для соединений с большим зазором
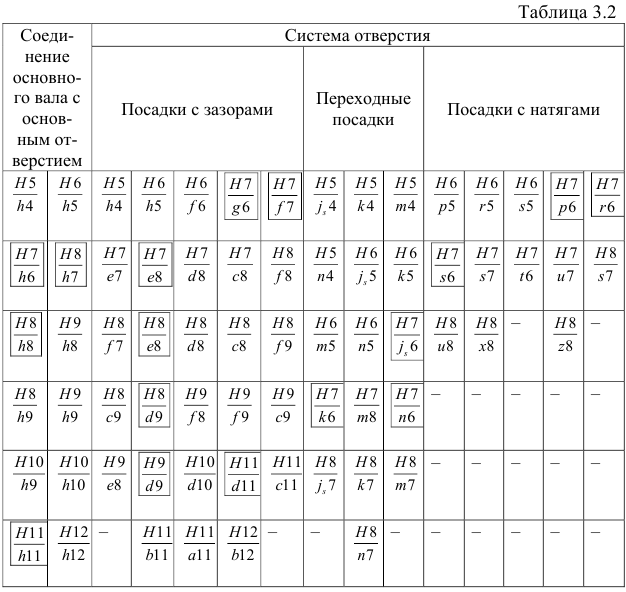
В соответствии с практикой для размеров 1-500 мм рекомендованы предпочтительные поля допусков, которые обеспечивают 90-95% посадок общего применения (табл. 3.2). Использование рекомендуемых посадок сокращает номенклатуру режущих инструментов и калибров и способствует повышению уровня унификации изделий. В рамках указаны предпочтительные посадки. При необходимости допускаются к применению и другие посадки, образованные из полей допусков ЕСДП.
Эта теория взята со страницы лекций по предмету «прикладная механика»:
Возможно эти страницы вам будут полезны:
Концентрация напряжений определение и формулы |
Контактные напряжения: определение и формулы |
Отклонения формы и расположения поверхностей |
Шероховатость поверхностей: определение и формулы |