Факторы, влияющие на величину предела выносливости
На выносливость элементов конструкций, находящихся в реальных условиях эксплуатации, влияет ряд факторов, которые при обычном статическом расчете не играют существенной роли. В частности, предел выносливости зависит не только от свойств материала, из которого изготовлены указанные элементы, но и от их формы, размеров, способа изготовления и условий работы.
Влияние концентрации напряжений. В местах резкого изменения поперечных размеров детали, у отверстий, надрезов, выточек и т. п. возникает, как известно, местное повышение напряжений, снижающее предел выносливости по сравнению с таковым для гладких цилиндрических образцов. Это снижение учитывается эффективным коэффициентом концентрации напряжений (или
), который определяется экспериментальным путем. Указанный коэффициент представляет собой отношение предела выносливости
гладкого образца при симметричном цикле к пределу выносливости
образца тех же размеров, но имеющего тот или иной концентратор напряжений, т. е.

Зависимость между теоретическим и эффективным коэффициентами концентрации напряжений определяется следующим выражением:

где — коэффициент чувствительности материала к концентрации напряжений.
На рис. 2.68 приведен график приближенных значений для стали различных марок в зависимости от коэффициента
и предела прочности
. материала. Как видно из графика, чем выше прочность стали, тем выше ее чувствительность к концентрации напряжений Поэтому применение высокопрочных сталей для изготовления деталей, работающих в условиях переменных напряжений, не всегда оказывается целесообразным.
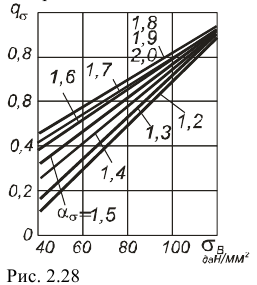
Следует отметить, что все рассуждения, относящиеся к нормальным напряжениям, сохраняют свою силу и для касательных напряжений. Только в соответствующих математических выражениях обозначение необходимо изменить на .
Значения эффективных коэффициентов концентрации и
приводятся в справочниках.
Влияние размеров деталей. Экспериментально установлено, что с увеличением размеров испытуемого образца предел выносливости его понижается. Это объясняется тем, что, во-первых, на образцах больших размеров более вероятны дефекты материала, а во-вторых, при изготовлении малых образцов имеет место упрочнение (наклеп) поверхностного слоя на относительно большую глубину, чем у образцов больших размеров.
Влияние размеров деталей на величину предела выносливости учитывается коэффициентом , представляющим собой отношение предела выносливости детали заданных размеров (диаметром
) к пределу выносливости лабораторного образца подобной конфигурации, имеющего малые размеры
. Это отношение называют коэффициентом влияния абсолютных размеров сечения или масштабным фактором. Применительно к нормальным напряжениям

Масштабные коэффициенты можно определять и на образцах с концентрацией напряжений.
На рис. 2.69 приведена графическая зависимость между диаметром детали и коэффициентом
(шкала
— логарифмическая).
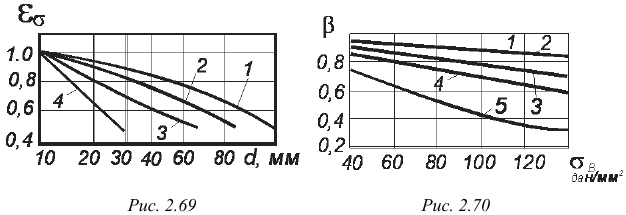
Кривая 1 соответствует детали из углеродистой стали без концентрации напряжений, кривая 2 — то же, но с умеренной концентрацией. При расчете деталей из легированной стали пользуются кривыми 2 и 3 (соответственно при отсутствии и наличии концентрации напряжений). Если деталь имеет большую концентрацию напряжений (типа нарезки), то зависимость для любой стали изображается кривой 4.
Вследствие недостаточного количества экспериментальных данных о коэффициентах (при кручении) приближенно принимают
.
Влияние состояния поверхности. Состояние поверхности деталей зависит от качества механической обработки. Так как разрушение материала от периодически изменяющихся нагрузок начинается с образования на поверхности микроскопических трещин, то очевидно, что их образованию способствует наличие на поверхности острых рисок и царапин. Последнее приводит, естественно, к уменьшению предела выносливости материала.
Влияние состояния поверхности на предел выносливости при симметричном цикле характеризуется коэффициентом состояния поверхности. Этот коэффициент представляет собой отношение предела выносливости
детали с данной обработкой поверхности к пределу выносливости
полированного образца:

Графики изменения коэффициента в зависимости от временного сопротивления материала
и вида обработки поверхности приведены на рис. 2.70.
Кривые на графике соответствуют следующим видам обработки поверхности: 1 — полирование; 2 — шлифование; 3 — тонкое обтачивание; 4 — грубое обтачивание; 5 — наличие окалины. Различные способы поверхностного упрочнения детали могут существенно повысить значение коэффициента качества поверхности (до 1,5-2 и более вместо 0,6-0,8 для деталей без упрочнения). Подробные данные о величине
в зависимости от способа упрочнения поверхностного слоя (наклепа, цементации, азотирования, поверхностной закалки нагревом т.в.ч. и т.д.) приведены в справочниках.
Учитывая изложенное выше, можно определить общий коэффициент изменения предела выносливости при симметричном цикле:

Действительный предел выносливости рассчитываемой детали в этом случае определяется так:
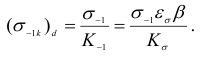