Оглавление:
Общие положения по выполнению чертежей деталей машин
Чертеж каждой детали выполняют на листе формата, установленного стандартом, и помещают основную надпись (угловой штамп).
• Деталь изображают на чертеже в положении, при котором наиболее удобно его читать, т. е. в положении, в котором деталь устанавливают на станке. В частности, ось детали, представляющей тело вращения (вал, зубчатое колесо, червяк, стакан, втулка и др.), располагают параллельно основной надписи.
• Чертеж детали должен содержать все данные, необходимые для ее изготовления и контроля.
• При выполнении чертежа детали ограничиваются минимальным количеством проекций, видов, разрезов и сечений.
• На чертежах деталей не допускается помещать технологические указания. В частности, центровые отверстия на чертежах деталей не изображаются и в технических требованиях никаких указаний не приводят, если наличие их конструктивно безразлично. Когда обработка отверстий в деталях под винты, штифты и другие крепежные детали должна производиться при сборке, на чертежах эти отверстия не изображают и никаких указаний в технических требованиях не помещают. Все необходимые данные для обработки таких отверстий располагают на чертеже сборочной единицы
Рекомендации по рациональной простановке линейных размеров
При простановке размеров следует учитывать характер производства, методы формообразования заготовок и технологию изготовления деталей [7]. Все номинальные размеры, проставляемые на чертежах, можно разделить на три категории.
Сопряженные — размеры, принадлежащие одновременно двум сопряженным деталям. Цепные — размеры, образующие сборочные размерные цепи. Свободные — размеры, не вошедшие в сопряженные и цепные.
Основной принцип простановки размеров на рабочих чертежах деталей следующий:
• сопряженные и цепные размеры берут из сборочного чертежа и проставляют на рабочих чертежах деталей;
• свободные размеры проставляют с учетом последовательности их получения при формообразовании деталей и удобства контроля.
Ниже даны основные указания по рациональной простановке размеров на рабочих чертежах деталей [ 7 ].
- Количество размеров на чертеже должно быть достаточным для изготовления и контроля деталей.
- Каждый размер следует приводить на чертеже лишь один раз.
- Цепь размеров на чертеже детали не должна быть замкнута. Замыкающий размер получается автоматически при формообразовании детали. В этом размере накапливаются погрешности изготовления детали по составляющим размерам. Поэтому в качестве замыкающего выбирают наименее ответственный размер детали.
- Проставлять размеры надо так, чтобы наиболее точный размер имел наименьшую накопленную ошибку при изготовлении детали.
В машиностроении применяют цепной, координатный и комбинированный методы простановки размеров.
При цепном методе простановки (рис. 5.1, а) ошибки в предыдущих размерах и
не влияют на размер
, но ошибка в ориентации относительно базы
накапливается. Точную ориентацию элементов относительно базы
обеспечивает координатный метод простановки размеров (рис. 5.1, б), но в этом случае ошибка между элементами равна сумме ошибок соответствующих координатных размеров. На рис 5.1, в показан комбинированный метод простановки размеров.
- На чертежах деталей, представляющих собой тела вращения, осевые размеры следует располагать под изображением детали.
- Размеры, относящиеся к одному конструктивному элементу, следует группировать в одном месте, например размеры канавок для выхода шлифовального круга (см. чертежи деталей), что облегчает чтение чертежа, а также профилирование специального режущего инструмента — канавочного резца.
- При наличии у деталей фасок или канавок для выхода инструмента размеры следует проставлять до буртиков или до торцов детали, так как эти элементы, как правило, обрабатываются после получения основных поверхностей (рис. 5.2).
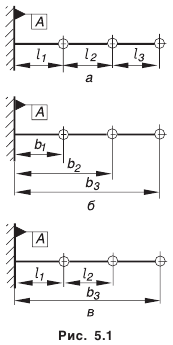
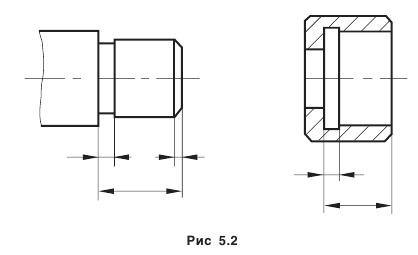
Правила и рекомендации по указанию допусков и предельных отклонений
Геометрическая точность деталей оценивается:
- точностью размеров элементов;
- точностью их взаимного расположения;
- точностью формы поверхностей элементов (макрогеометрией поверхностей);
- шероховатостью поверхности (микрогеометрией).
При проектировании деталей задают не только размеры элементов, но и предельные отклонения по всем четырем геометрическим параметрам.
Предельные отклонения размеров:
- Для всех размеров, нанесенных на чертежах, указываются предельные отклонения. Допускается не указывать предельные отклонения на размерах, определяющих зоны одной и той же поверхности с различной шероховатостью, термообработкой и т. п. В этих случаях у размеров ставится знак = (см. чертеж вала, рис. П.8.3, приложение 8).
- Предельные отклонения сопряженных размеров должны соответствовать посадкам, указанным на сборочных чертежах. Их наносят на чертежи одним из трех способов, установленных ГОСТ 25346-82:
- условными обозначениями полей допусков —
;
- числовыми значениями предельных отклонений —
;
- условными обозначениями полей допусков с указаниями в скобках числовых значений предельных отклонений —
.
- Предельные отклонения размеров, входящих в размерные цепи, указываются в соответствии с результатами расчета размерных цепей.
- Предельные отклонения свободных размеров назначаются по одному из четырех классов точности: точный —
средний —
грубый —
очень грубый —
и оговариваются общей записью в технических требованиях, например: «ГОСТ 30893.1 —
», которая означает, что неуказанные предельные отклонения линейных размеров, радиусов скругления, высот фасок, угловых размеров должны иметь симметричные отклонения по классу точности средний.
Числовые значения отклонений определяются по таблицам ГОСТ 30893.1-2002 в зависимости от класса точности, указанного в общей записи.
Отклонения свободных размеров, получаемых обработкой резанием, предпочтительно назначать по классу точности средний.
Допуски формы и расположения
Виды допусков, их обозначение и изображение на чертежах приведены в разделе 3.1, «Допуски формы и расположения поверхностей». Числовые значения допусков в зависимости от степени точности даны в приложении 2.
Выбор допусков зависит от конструктивных и технологических требований к элементам деталей и производится по следующим правилам.
- Непосредственно на чертежах должны указываться лишь те допуски формы и расположения, которые по конструктивным или техническим причинам должны быть меньше, а в отдельных случаях — больше, чем неуказанные.
- Все допуски формы и расположения подразделяются на две группы:
- ограничиваемые полем допуска размера;
- непосредственно не ограничиваемые полем допуска размера.
К первой группе, согласно ГОСТ 24643-81, относятся допуски цилиндричности, круглости, профиля продольного сечения, плоскостности, прямолинейности и параллельности. На допуски первой группы распространяется правило о том, что если допуски формы и расположения не указаны, то они должны быть ограничены полем допуска размера.
Отклонения формы и расположения второй группы не входят составной частью в погрешность размера соответствующих элементов и не выявляются при контроле размера. Поэтому эти отклонения всегда должны быть ограничены отдельными допусками:
- Допуски формы и расположения поверхностей указываются на чертежах в соответствии с ГОСТ 2.308-79 условными обозначениями или в технических требованиях текстом. Применение условных обозначений предпочтительнее.
- При условном обозначении предельные отклонения формы и расположения поверхностей указывают в прямоугольной рамке.
- Числовые значения допусков формы, допусков расположения и суммарных допусков формы и расположения поверхностей должны соответствовать указанным в табл. П.2.1 (см. приложение 2).
- Для отдельных видов допусков формы и расположения поверхностей числовые значения предпочтительнее устанавливать в соответствии со степенями точности, указанными ГОСТ 24643-81.
Технические требования на чертежах деталей машин
Текстовую часть технических требований располагают на поле чертежа над основной надписью в следующем порядке.
- Требования к материалу, заготовке, термической обработке. Если всю деталь подвергают одному виду термической обработки, то в технических требованиях делают запись:
; Цементировать
. Если термической обработке подвергают отдельные участки детали, то их отмечают на чертеже утолщенной штрихпунктирной линией, а значения
и
показывают на полках линий-выносок (рис. 5.3).
- Размеры (формовочные и штамповочные радиусы, уклоны и пр.).
- Предельные отклонения размеров, формы и расположения поверхностей, дисбаланс.
- Требования к качеству поверхностей (шероховатость, отделка, покрытия).
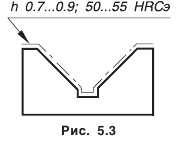
.
Валы
На чертежах валов, валов-шестерен и червяков для облегчения выполнения и чтения чертежа следует располагать:
- осевые линейные размеры — под изображением детали;
- условные обозначения базовых осей — под изображением детали;
- условные обозначения допусков формы и расположения поверхностей — над изображением детали;
- линии-выноски с обозначением элементов — над изображением детали;
- условные обозначения шероховатости поверхности — на верхних частях изображения детали.
Примеры оформления чертежей приведены в приложении 8.
Простановка осевых размеров
Общие рекомендации по простановке линейных размеров даны в подразделе 5.1.2.
На чертеже вала обязательно должны быть указаны габаритный размер Г, необходимый для заготовительной операции, и размер Ц, входящий в размерную цепь (рис. 5.4, а). Остальные размеры проставляются исходя из технологии изготовления вала.
В единичном и мелкосерийном производстве обработку вала обычно производят на токарном универсальном станке с двух сторон. Последовательность получения размеров (рис. 5.4, 6, в) совпадает с номером индексов линейных осевых размеров и номером снимаемого слоя металла. На рис. 5.4, г показан вал с размерами, отвечающими данной технологии.
При применении станков с ЧПУ рекомендуется цепной метод простановки размеров, так как подобные станки, как правило, обрабатывают деталь по контуру одним резцом.
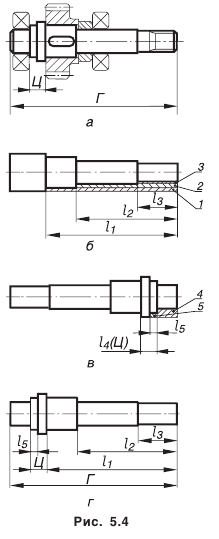
Назначение допусков формы, расположения и шероховатости поверхности
Общие требования при назначении допусков формы и расположения даны в подразделе 5.1.3, а шероховатости поверхности — в разделе 3.4.
При выборе допусков формы и расположения на детали типа валов все требования можно разделить на три группы. Группа 1 связана с установкой подшипников качения — наиболее ответственных, точных и сложных изделий (назначение требований производится в соответствии с разделом 3.2) либо с созданием необходимых условий для работы подшипников скольжения (назначение требований производится в соответствии с разделом 3.3). Группа 2 — это группа требований, которые связаны с обеспечением точности зацеплений в зубчатых и червячных передачах.
Группа 3 — группа требований, ограничивающих неуравновешенность деталей.
При назначении допусков взаимного расположения различных элементов вала прежде всего необходимо выбрать базы, относительно которых они будут задаваться. В качестве баз следует всегда стремиться выбирать конструкторские базы, т. е. те поверхности, которые определяют положение вала в механизме.
На рис. 5.5 приведена схема установки вала в механизме. Рабочей осью вала является ось, проходящая через середины посадочных поверхностей подшипников качения, которая и определяет положение вала. Поэтому в качестве базы используется общая ось двух шеек, обозначенная на рис. 5.5. буквами ДЕ.
Позиция 1. Допуск радиального биения посадочной поверхности для левого подшипника относительно общей оси. Рекомендуется назначать вместо соосности, так как контроль данного параметра осуществляется значительно проще, чем измерение соосности.
Назначение технического требования — обеспечение качественной работы подшипника качения.
Радиальное биение определяется с учетом суммарного допустимого угла взаимного перекоса колец подшипника (см. разд. 3.2):

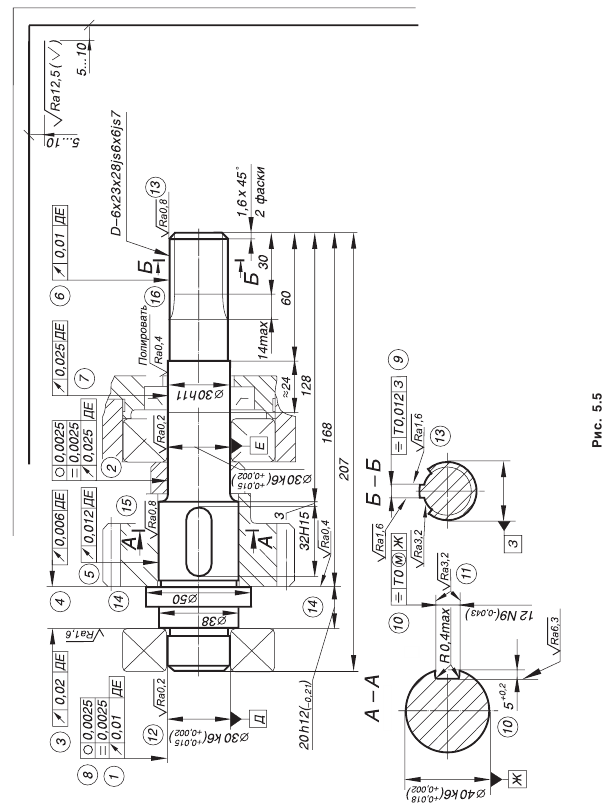
где — допустимый угол взаимного перекоса колец подшипника № 306 класса точности нормальный (см. табл. 3.8);
— угол, вызванный отклонением от соосности посадочной поверхности вала относительно общей оси;
— допустимый угол перекоса, вызванный торцовым биением заплечика вала (см. табл. 3.9);
— угол наклона упругой линии вала под действием нагрузки;
— угол, вызванный отклонением от соосности посадочной поверхности отверстия;
— допустимый угол, вызванный торцовым биением заплечика отверстия либо базовым торцом крышки подшипника (см. табл. 3.10). Допускается принять:
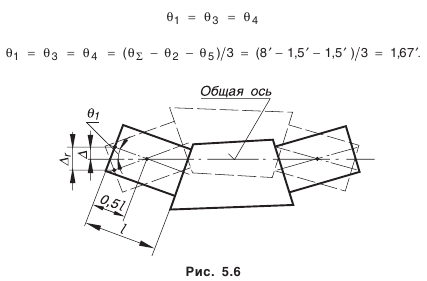
Величина отклонения от общей оси (рис. 5.6):

где — коэффициент перевода минут в радианы;
— длина левой шейки под подшипник;

Допуск на радиальное биение выбирается из соответствующей таблицы ГОСТ 24643-81:

Примечание. Следует помнить, что радиальное биение включает в себя и погрешность формы, поэтому допуск формы не должен быть по крайней мере больше .
В тех случаях, когда допуск формы больше, чем значение , допуск формы следует ужесточить. В нашем случае
(см. позицию 8), что удовлетворяет высказанному условию.
Позиция 2. Допуск радиального биения посадочной поверхности для правого подшипника относительно общей оси.
Радиальное биение определяется по такой же методике, как и в позиции 1. Только в данном случае необходимо учесть еще угол — угол, вызванный отклонением от соосности базовых поверхностей стакана. Поэтому допускаемый угол перекоса, вызванный радиальным биением,

Допустимая величина отклонения от общей оси:

где — длина правой шейки вала, на которой установлен подшипник.

на радиальное биение выбирается:
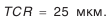
Позиция 3. Допуск торцового биения заплечика вала. Допуск задается на диаметре заплечика вала
Назначение технического требования — обеспечение качественной работы подшипника. Крепление левого подшипника соответствует схеме 1 (см. рис. 3.9, а). Значение допуска торцового биения берется 25 мкм (см. табл. 3.9).
Принимаем в соответствии с табл. П.2.4, приложение 2:
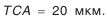
Позиция 4. Допуск торцового биения буртика вала. Допуск задается на диаметре буртика вала .
Назначение технического требования — обеспечение норм контакта зубьев в передаче; обеспечение качественной работы правого подшипника.
При выборе допуска следует рассматривать четыре случая. Случай 1 . Зубчатое колесо сопрягается с валом по одной из рекомендуемых посадок с натягом и имеет длинную ступицу (
рис. 5.7). Положение зубчатого колеса относительно вала полностью определяется его сопряжением по цилиндрической поверхности. В этом случае требования точности к торцу буртика вала не предъявляются.
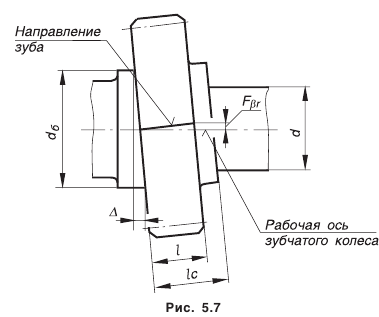
Случай 2. Зубчатое колесо сопрягается с валом по одной из рекомендуемых посадок с натягом, но имеет короткую ступицу . Допуск торцового биения на буртик вала назначают из условия, что при установке зубчатого колеса на вал отклонение от перпендикулярности буртика вызовет перекос колеса (рис. 5.7), а следовательно, и погрешность в направлении зубьев
. Это, в свою очередь, повлияет на контакт зубьев в передаче.
Поскольку погрешность в направлении зубьев зависит не только от торцового биения буртика вала, но и от перпендикулярности базового торца колеса и ряда других технологических причин, то практически можно допустить, чтобы торцовое биение вызывало не более 1/3 допуска на погрешность направления зуба по ГОСТ 1643-81.
Учитывая, что допуск на погрешности направления зуба задается на ширине зубчатого венца а допуск торцового биения — на диаметре буртика вала
, можно написать следующее выражение для торцового биения:

Случай 3. Зубчатое колесо сопрягается с валом по переходной посадке. Торцовое биение буртика вала определяют независимо от длины ступицы по вышеприведенной формуле.
Примечание. Во 2-м и 3-м случаях, когда точно известно, что базовый торец колеса является базовым и при нарезании зубчатого венца, можно увеличить допуск до .
Случай 4. Зубчатое колесо свободно вращается на валу. Буртик вала не является базовым, а биение на него назначается из условия минимально допустимого торцового зазора, необходимого для свободного вращения колеса.
Приведенный пример механизма (см. рис. 5.5) соответствует рассмотренному 3-му случаю. При этом базовый торец колеса вследствие его несимметричности известен, и можно допустить, что во время нарезания зубчатого венца он будет использован в качестве технологической базы.
Наибольшее допускаемое торцовое биение буртика вала, определяемое из условия нормальной работы зубчатого колеса, вычисляется по формуле:

Значение = 9 мкм выбирается по ГОСТ 1643-81 (см. табл. П.4.4, приложение 4) для цилиндрических зубчатых передач либо по соответствующим стандартам для других видов зубчатых колес.
Теперь рассмотрим влияние буртика на качество базирования подшипника качения. Наибольшее допускаемое значение биения буртика из условия нормальной работы правого подшипника определяется в соответствии с рекомендациями, изложенными в разделе 3.2:
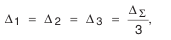
где = 25 мкм (см. табл. 3.9) — допускаемое суммарное торцовое биение;
— торцовое биение заплечика вала;
и
— отклонения от параллельности торцов втулки и зубчатого колеса соответственно.
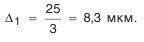
поэтому допуск торцового биения выбирается из условия нормальной работы зубчатого колеса по ГОСТ 24643-81 (см. табл. П.2.4, приложение 2):

Позиция 5. Допуск радиального биения посадочной поверхности для зубчатого колеса.
Назначение технического требования — обеспечение выполнения норм кинематической точности передачи.
Величина допуска радиального биения шейки вала выбирается в зависимости от допуска на радиальное биение зубчатого венца .
Радиальное биение зубчатого венца вызывают три вида погрешностей:
• радиальное биение подшипников качения;
• радиальное биение посадочной поверхности вала относительно общей оси;
• биение зубчатого венца колеса относительно оси посадочного отверстия.
Поэтому можно допустить, чтобы радиальное биение посадочной поверхности вала было не более 1/3.
Наибольшее допускаемое радиальное биение посадочной поверхности вала:

Значение выбирается по ГОСТ 1643-81 (см. разделы 2.6 и 5.4) для цилиндрических зубчатых передач либо по соответствующим стандартам для других видов зубчатых колес.
Допуск радиального биения выбирается по ГОСТ 24643-81 (см. табл. П.2.5, приложение 2):

Примечание. Допускается назначить , что не предусмотрено степенью точности для данного интервала номинальных размеров, но это числовое значение соответствует ряду, указанному в стандарте (см. табл. П.2.1, приложение 2).
Позиция 6. Допуск радиального биения посадочных поверхностей для муфт, шкивов, звездочек. Допуск задается на диаметре посадочной поверхности по табп. 5.1.
Назначение технического требования — ограничение возможного дисбаланса как самого вала, так и вала в сборе с деталью. Принимается, что частота вращения вала равна 1460 мин-1. Допуск радиального биения принимается по ГОСТ 24643-81:
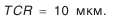

Позиция 7. Допуск радиального биения поверхности вала под манжетное уплотнение. Допуск принимается по данным [8, 9] табл. 5.2.
Назначение технического требования — не допускать значительной амплитуды колебаний рабочей кромки манжеты, вызывающих усталостные разрушения резины. Допуск на радиальное биение:


Позиция 8. Допуск формы посадочных поверхностей для подшипников качения. Допуск круглости и допуск профиля продольного сечения выбираются в соответствии с разделом 3.2.
Назначение технического требования — обеспечение качественной работы подшипников качения. Отклонения от круглости и от профиля продольного сечения не должны превышать :

где — допуск размера посадочной поверхности вала.

Допуск формы:

Позиция 9. Допуск симметричности расположения боковых сторон шлицев.
Назначение технического требования — обеспечение равномерности контакта боковых поверхностей шлицев в сопряжении.
Допуск принимается по табл. 2.7 раздела 2.2.

Позиция 10. Допуск симметричности расположения шпоночного паза отклонения на глубину и длину шпоночного паза.
В основу рекомендаций по выбору того или иного вида технических требований положены результаты анализа стандарта, устанавливающего допуски и посадки на призматические шпоночные соединения (ГОСТ 23360-78), стандартов на калибры для шпоночных соединений (ГОСТ 24109-80…ГОСТ 24121-80), а также рекомендации В. Д. Мягкова и П. Ф. Дунаева [7, 8. 10].
Рекомендации, приведенные в табл. 5.3, в равной степени относятся к шпоночным пазам, расположенным как на валах, так и в отверстиях.
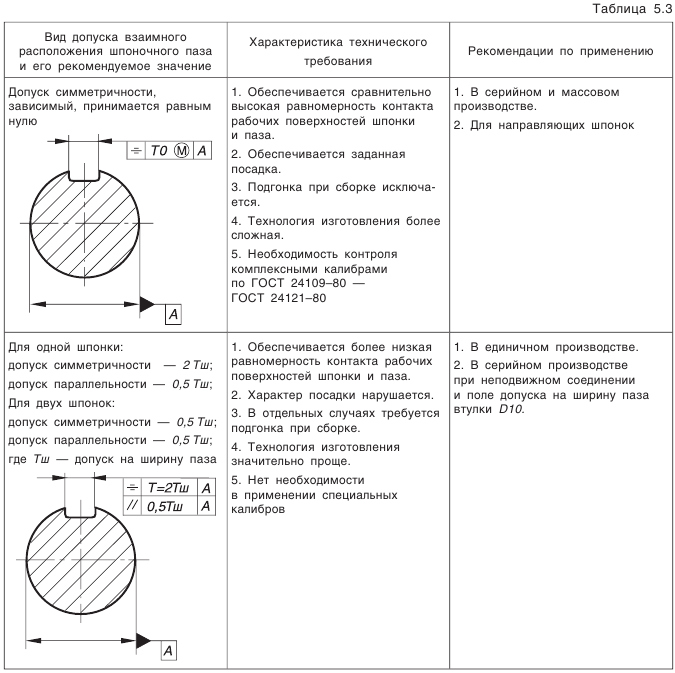
При назначении допуска расположения шпоночного паза рекомендуется учитывать характер производства и конкретные технологические возможности.
Отклонения на глубину шпоночного паза у вала и у втулки см. в табл. 2.4. Предельные отклонения длины шпоночного паза назначаются по в соответствии с ГОСТ 23360-78 (см. раздел 2.1).
Позиция 11. Шероховатость поверхностей в шпоночном соединении.
В соответствии с рекомендациями [10] значение параметра следует выбирать не более:
• для рабочих поверхностей пазов и шпонок — 1,6…3,2 мкм;
• для нерабочих поверхностей — 6,3… 12,6 мкм.
Позиция 12. Шероховатость посадочных поверхностей под подшипники качения.
Назначение технического требования — обеспечение заданного характера сопряжения. Величина шероховатости выбирается по табл. 3.13, .
Учитывая, что допуски формы у посадочных поверхностей составляют (см. позицию 8) , принимаем
.
Позиция 13. Шероховатость поверхностей зубчатых (шлицевых) соединений.
В соответствии с рекомендациями [10] значение параметра следует выбирать по табл. 5.4.
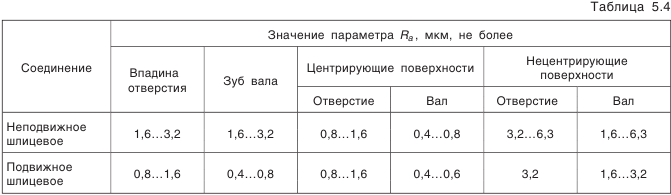
Позиция 14. Шероховатость поверхности заплечика вала.
Назначение технического требования — равномерное распределение нагрузки по поверхности заплечика и обеспечение необходимой точности положения зубчатого колеса. В соответствии с рекомендациями в разделе «Шероховатость поверхности»:
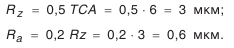
Позиция 15. Шероховатость посадочной поверхности под зубчатое колесо.
Назначение технического требования — обеспечение заданного характера сопряжения. В соответствии с указаниями в разделе 3.4, «Шероховатость поверхности», выбирается наименьшее значение из двух выражений:
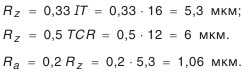
Принимаем
Позиция 16. Шероховатость поверхности под манжетное уплотнение.
Назначение технического требования — предохранение манжеты от преждевременного износа. Назначается в соответствии с табл. 3.12: полировать.
Цилиндрические зубчатые колеса. Простановка размеров
На чертежах зубчатых колес проставляются габаритные размеры (рис. 5.8); размеры, входящие в размерные цепи Ц; ширина венца; размеры фасок или радиусы кривизны линий притупления на кромках зубьев. Остальные размеры проставляются исходя из технологии изготовления зубчатого колеса. Для штампованных и литых заготовок указывают толщину
дисков и связующий размер
.
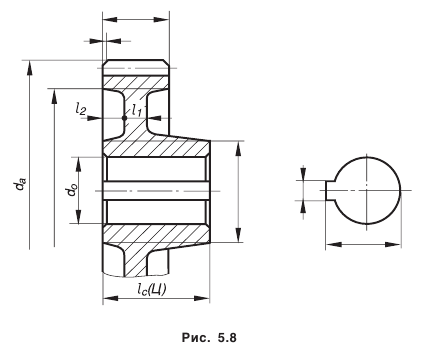
На чертеже зубчатого колеса должна быть таблица параметров зубчатого венца (рис. 5.9), состоящая из трех частей:
• первая часть — основные данные;
• вторая часть — данные для контроля;
• третья часть — справочные данные.
Части отделяются друг от друга сплошными основными линиями.
Эта лекция взята со страницы лекций по допускам и посадкам:
Допуски и посадки: ГОСТы и особенности применения
Возможно вам будут полезны эти страницы: