Оглавление:
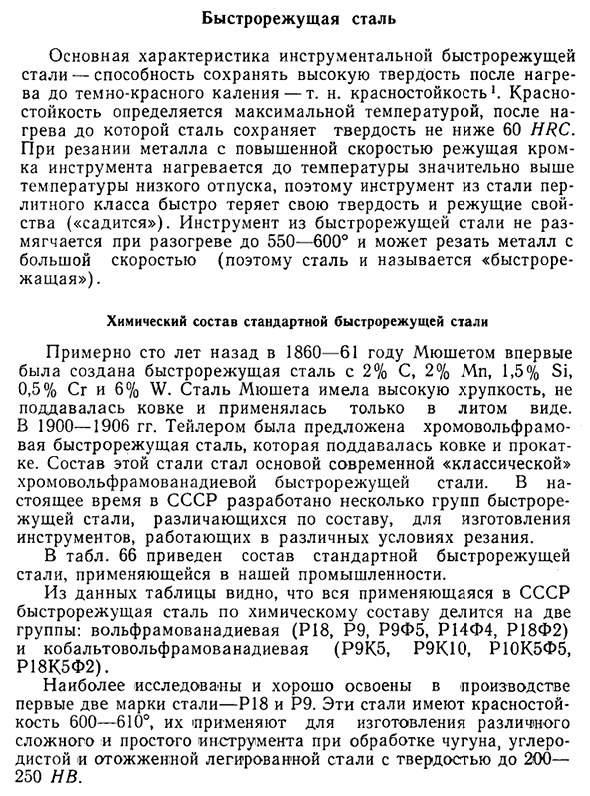
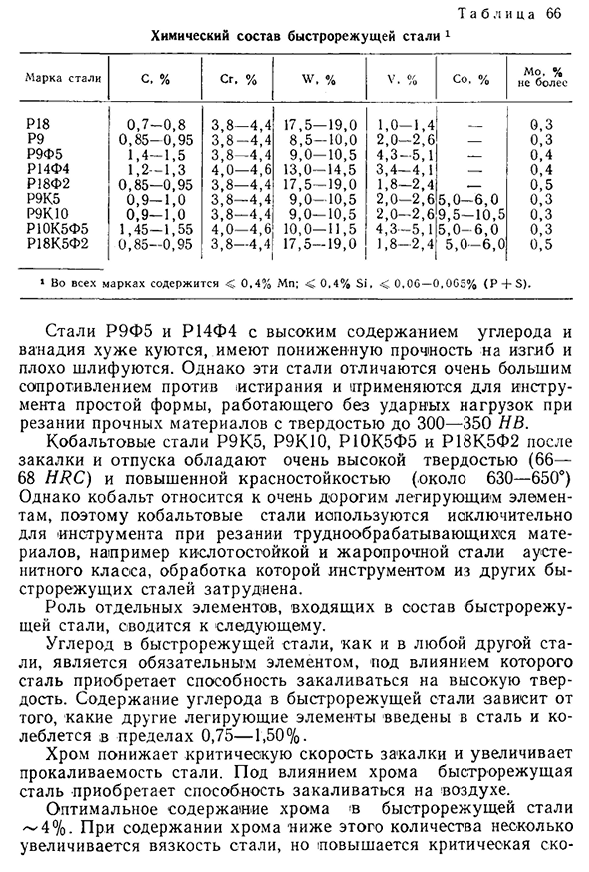
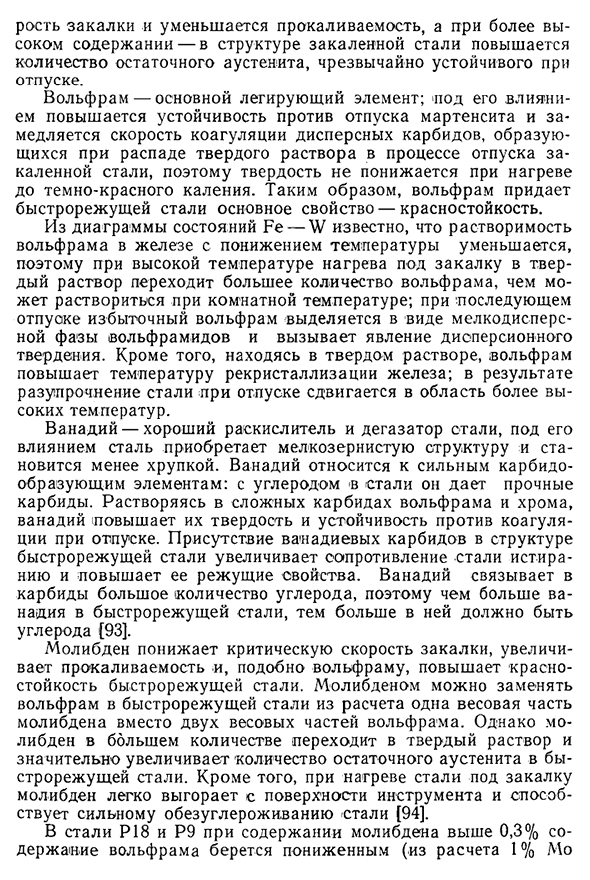
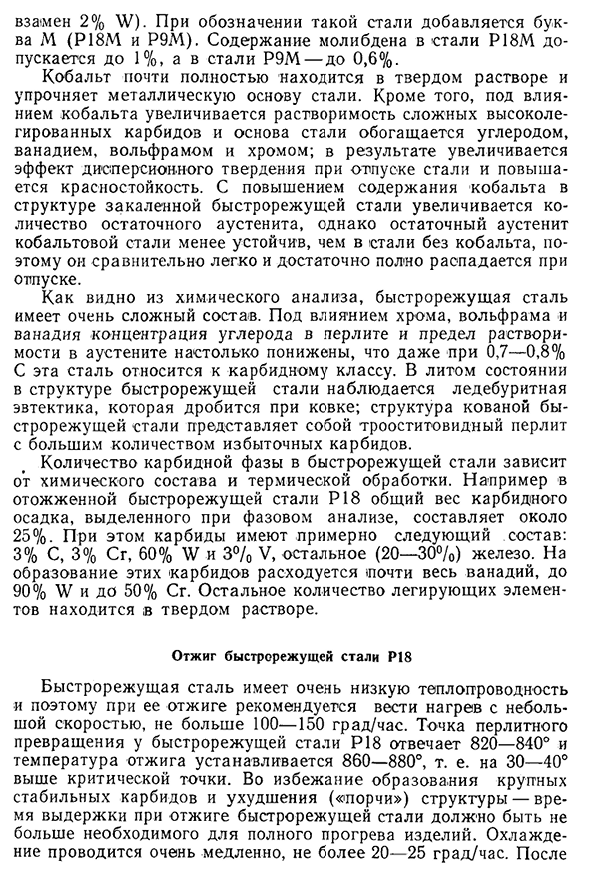
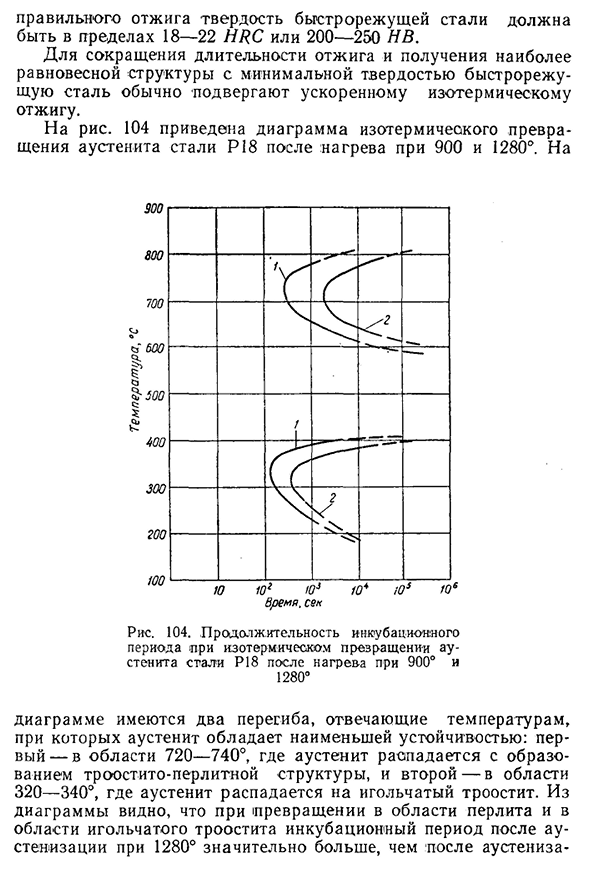
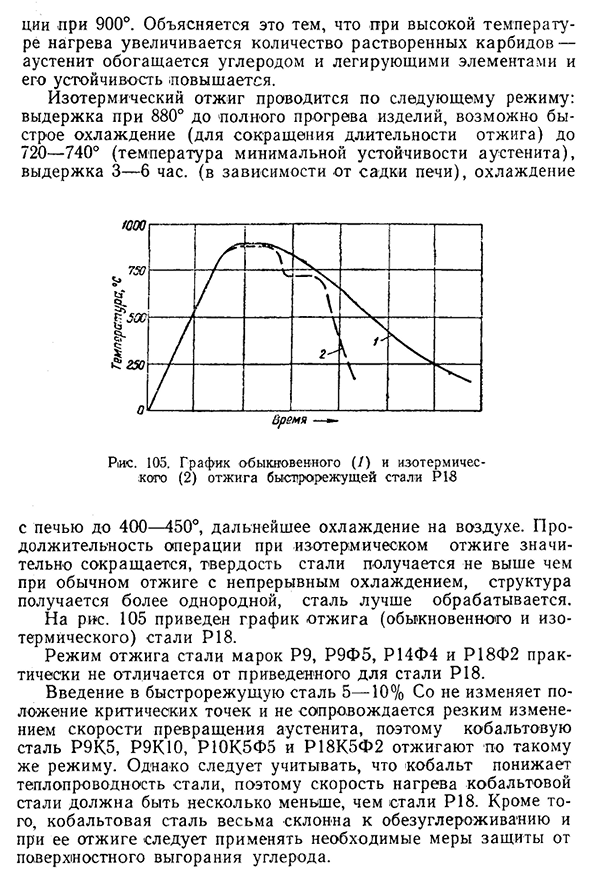
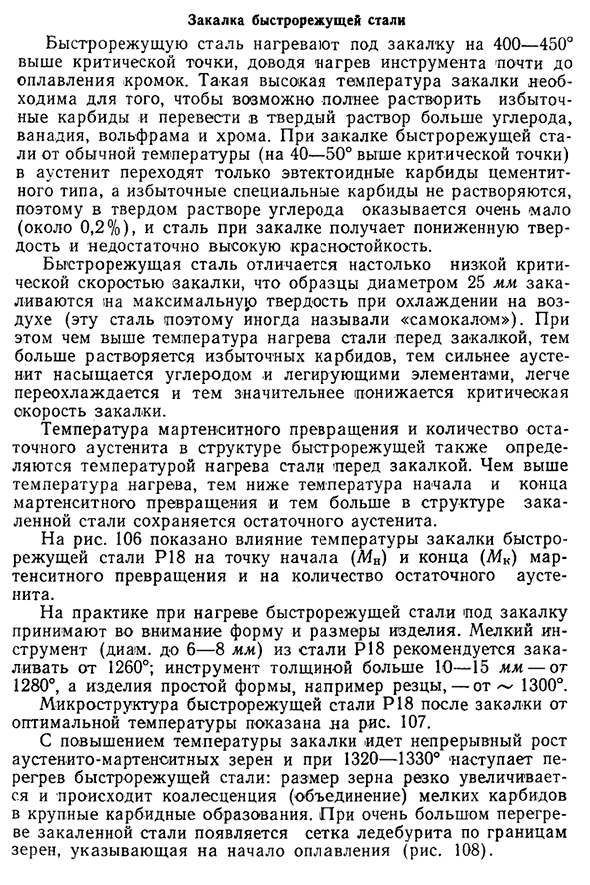
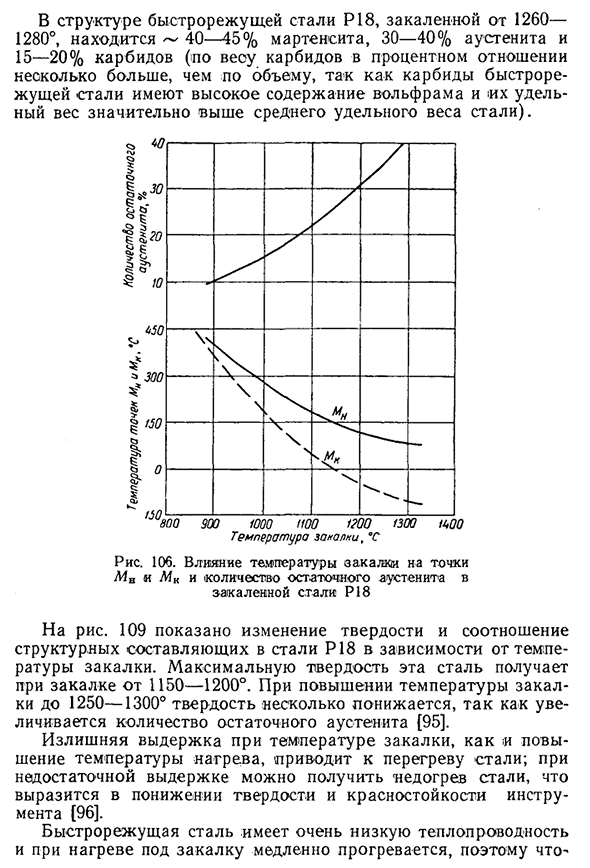
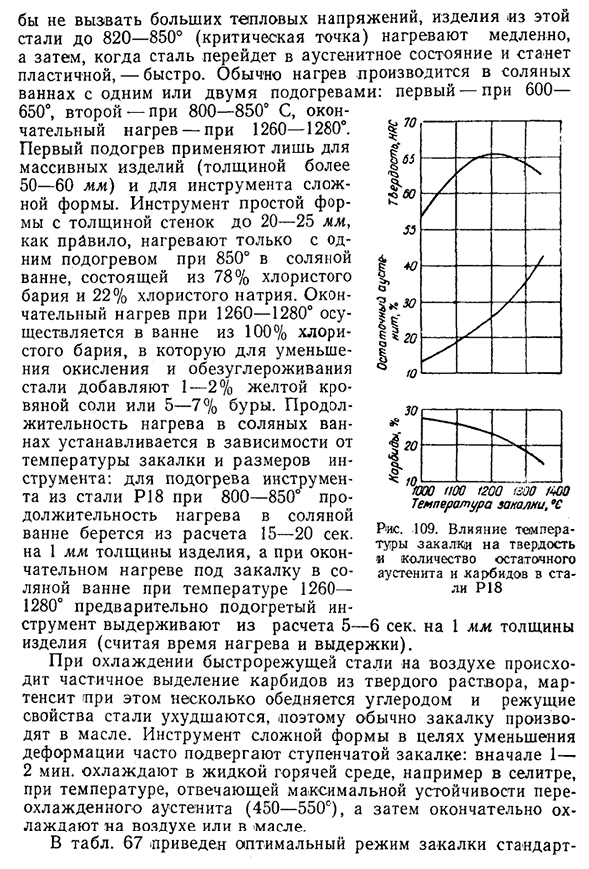
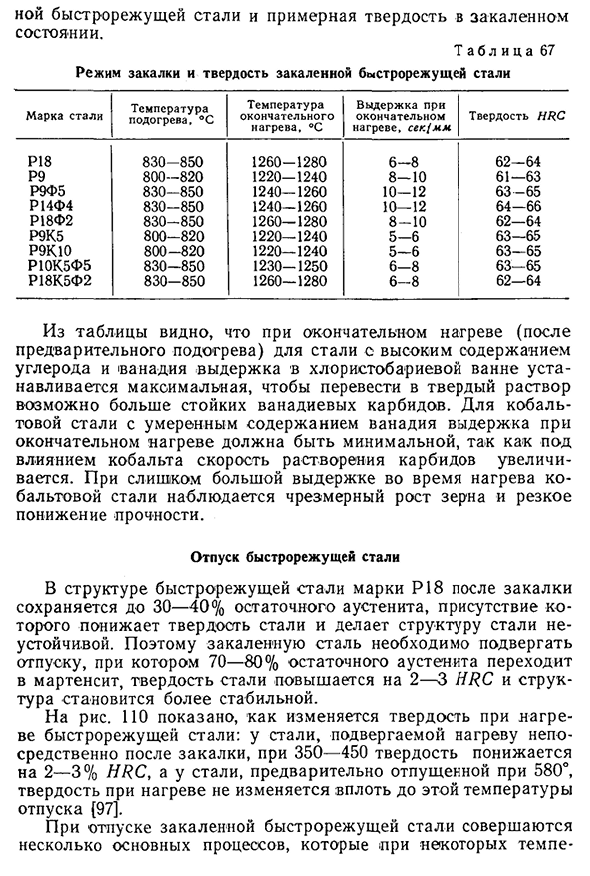
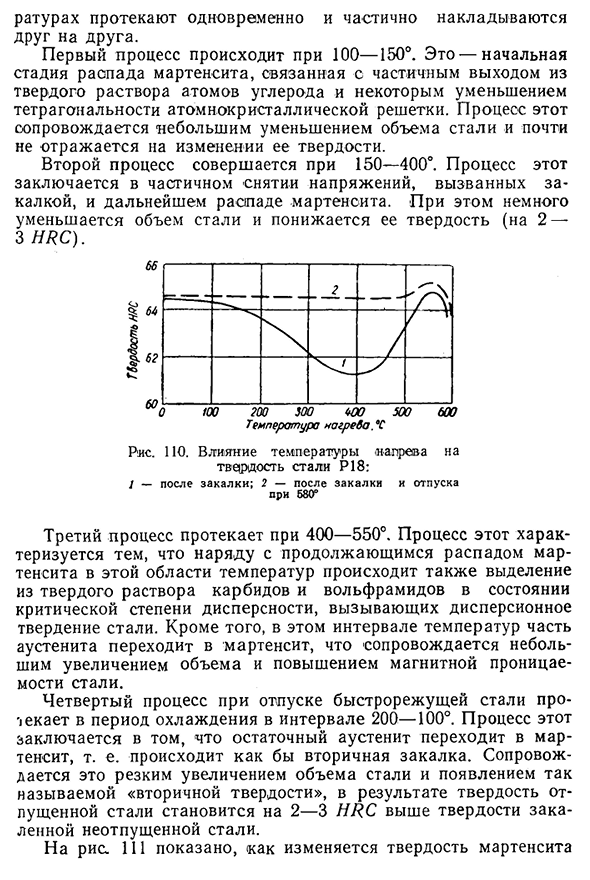
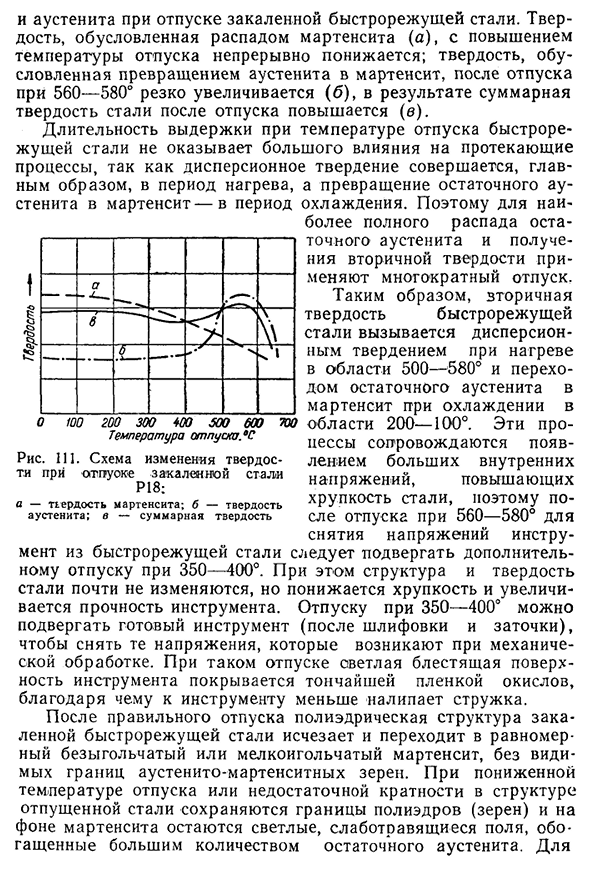
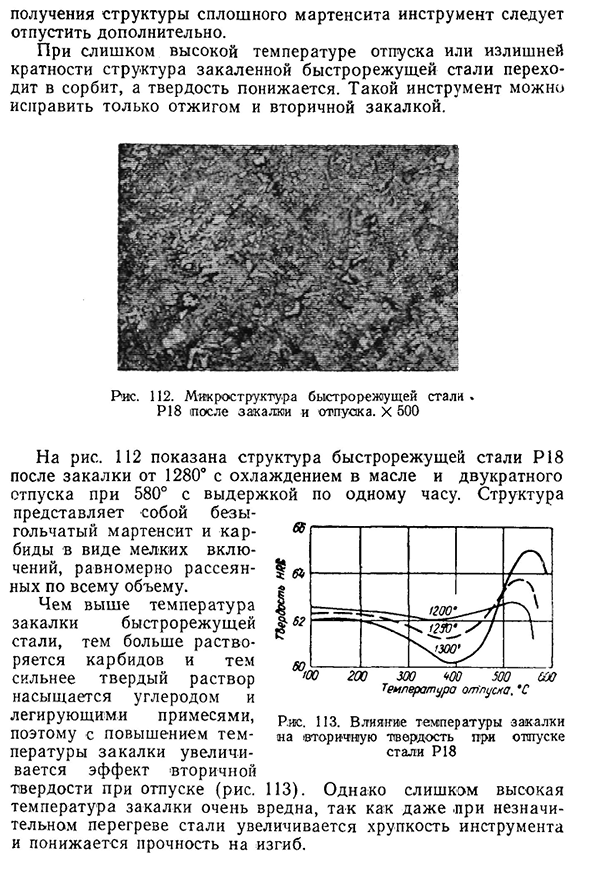
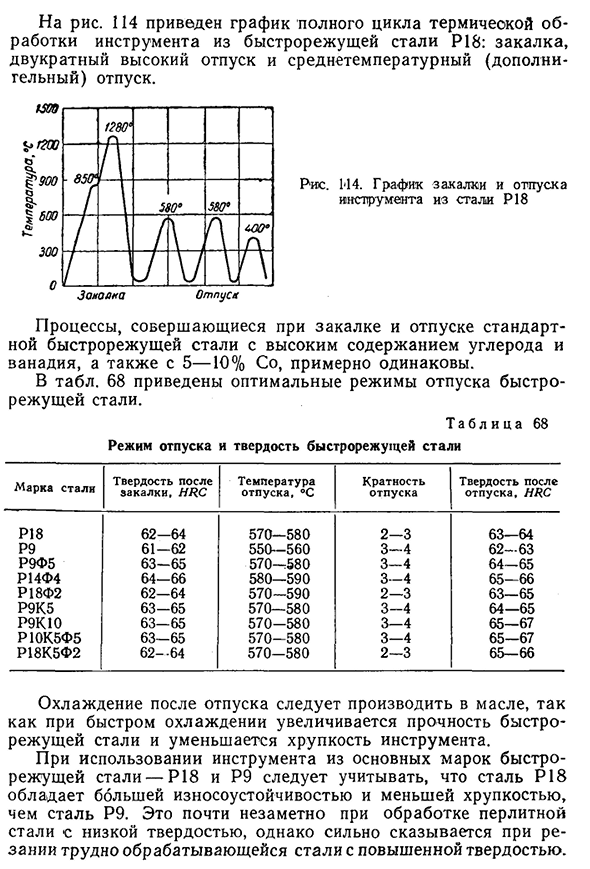


Быстрорежущая сталь
- Быстрорежущая сталь Главной особенностью быстрорежущей стали для инструмента является способность сохранять высокую твердость после нагрева до так называемого темно-красного тепла. Покраснение 1.Сопротивление к Красной стали определено максимальной температурой позже heating.
At при максимальной температуре сталь сохраняет твердость не менее 60 HRC. Если металл режется с высокой скоростью, режущая кромка инструмента нагревается до гораздо более высокой температуры, чем при низкой температуре отпуска. Поэтому инструменты из перлитовой стали быстро теряют твердость и режущие свойства («посадочные места«).Инструменты из быстрорежущей стали, нагретые до 550-600°, не размягчаются и могут резать металл с большой
скоростью(именно поэтому сталь называют «быстрорежущей резкой»). Людмила Фирмаль
Химический состав стандартной быстрорежущей стали Около 100 лет назад, в 1860-61 годах, Мушет впервые создал 2% C, 2% Mn, 1,5% Si, 0,5% Cr, 6% быстрорежущей стали. Сталь мушет была очень хрупкой, не поддавалась ковке и использовалась только в литейной форме. 1900-1906 Тейлор предложил хромисто-вольфрамовую быстрорежущую сталь и поддался ковке и прокатке. Состав этой стали стал основой современного» классического » хрома вольфрама ванадия высокой скорости steel.
At в настоящее время в СССР разработано несколько групп быстрорежущих сталей различного состава для производства инструментов, работающих в различных режимах резания. В таблице. На рисунке 66 показан состав стандартной быстрорежущей стали, используемой в промышленности. Из таблицы видно, что все быстрорежущие стали, применявшиеся в СССР, по химическому составу делятся на 2 группы: вольфрам-ванадиевые (Р18, Р9, Р9Ф5, Р14Ф4, Р18Ф2) и кобальт-вольфрам-ванадиевые (Р9, Р9К10, Р105, Р5Ф). р18к5ф2). Первые 2 марки стали-Р18 и Р9-являются наиболее изученными и хорошо освоенными в производстве. Покраснение этих сталей составляет 600-610°. о
- но применяется при изготовлении различных сложных и простых инструментов из чугуна, углеродистой дистилляции, закаленных легированных сталей с твердостью до 200. 250 HB. Один При определении красного допуска, закалке, темперировании, измерении твердости образца после нагрева 575, 600, 625 и 650°4 раза время выдержки до температур 1 час. Таблица 66 Химический состав быстрорежущей стали1 Марка стали、% 0,7-0,8 0.85-0.95 1.4-1.5 1,2-1,3 0.85-0.95 0.9-1.0 0.9-1.0 1.45-1.55 0.85-0.95 Три Три Три Четыре Три Три Три Четыре Три Кг%, 8-4. Четыре 8-4, 4 вечера. 8-4, 4 вечера. 0-4. Шесть 8-4, 4 вечера. 8-4, 4 вечера. 8-4, 4 вечера. 0-4. Шесть 8-4, 4 вечера. Один МО,%, не более Р18 П9 Р9Ф5 P14F4 Р18Ф2 P9K5 P9K10 Р10К5Ф5 Р18К5Ф2 17.5-19.0 8.5-10.0 9.0-10.5 13.0-14.5 17.5-19.0 9.0-10.5 9.0-10.5 10.0-11.5 17.5-19.0 1,0-1,4 2.0-2.6 4.3-5.1 3.4-4.1 1.8-2.4 2.0-2.65.0-6.0 2.0-2.69.9-10.5 4.3-5.1 1.8-2.4 5.0-6.0 5.0-6.0 0.3 0.3 0.4 0.4 0.5 0.3 0.3 0.3 0.5
Один Содержание < 0, 4% м п В О всехмаркашхс. <0, 4%S i,<0,0 G-0, 0 G 5%(P + S). Стали Р9Ф5 и Р14Ф4 с высоким содержанием углерода и ванадия обладают плохой подковываемостью, низкой прочностью на изгиб и плохим шлифованием. Однако эти стали отличаются очень высокой износостойкостью, что полезно для простых формообразующих инструментов, работающих без ударных нагрузок при резке материалов с высокой твердостью до 300-350 НВ. После гасить и закалять, сталь р9к5,Р9КЮ, Р10К5Ф5, и Р18К5Ф2 кобальта имеют очень высокую твердость(66-68 ХРК),
и увеличивают красное сопротивление(около 630-650°). Людмила Фирмаль
Однако, поскольку кобальт является очень дорогим легирующим элементом, кобальтовая сталь является инструментом, используемым для резки громоздких материалов, таких как кислотоупорные и жаропрочные аустенитные стали, которые трудно обрабатывать инструментами, изготовленными из других быстрорежущих сталей. Роль отдельных элементов, составляющих быстрорежущую сталь, заключается в следующем: Как и любая другая сталь, углерод быстрорежущей стали является незаменимым элементом, и под его воздействием сталь приобретает способность затвердевать с высокой твердостью. Содержание углерода в быстрорежущей стали варьируется от 0,75 до 1,50% в зависимости от других легирующих элементов, вводимых в сталь.
Хром снижает критическую скорость упрочнения и улучшает упрочняющие свойства стали. Под воздействием хрома быстрорежущая сталь приобретает способность затвердевать на воздухе. Оптимальное содержание хрома ’для быстрорежущей стали-4% — если содержание хрома ниже этого количества, вязкость стали немного возрастет, но критическая скорость возрастет.220 кобальтовой стали По мере уменьшения твердения и упрочнения и увеличения содержания упрочненной стальной структуры увеличивается количество остаточного аустенита, который очень стабилен при отпуске. Вольфрам является основным легирующим элементом. Под его воздействием повышается стойкость к мартенситному отпуску и разложению твердого раствора при отпуске уменьшается скорость образования дисперсных карбидов твердого раствора, поэтому твердость не уменьшается при нагревании до темно-красного тепла.
Подобный этому Вольфрам дает быстрорежущей стали красное сопротивление, которое является основным свойством. Фазовая диаграмма Fe-W показывает, что растворимость вольфрама в железе уменьшается с уменьшением температуры. Поэтому при нагревании при высоких температурах в твердый раствор поступает больше вольфрама, чем расплавляется при комнатной температуре. Во время последующего стока избыток вольфрама выделяется в виде фазы тонкодисперсного эльфламида, вызывая явление диспергирования hardening. In кроме того, будучи твердым раствором, вольфрам повышает температуру рекристаллизации Iron. As в результате размягчение стали при отпуске переходит в зоны с более высокой температурой. Ванадий является отличным раскислителем и дегазатором стали, под воздействием которого сталь приобретает мелкозернистую структуру и снижает ее хрупкость.
Ванадий относится к сильными карбидообразующими elements. By углерод в Стали, он производит сильное карбид. Ванадий, который растворяется в композитных карбидах вольфрама и хрома, повышает его твердость и стойкость к затвердеванию при отпуске. Наличие карбида ванадия в структуре быстрорежущей стали повышает износостойкость стали и улучшает режущие свойства. Ванадий связывает большое количество углерода с карбидами, поэтому чем больше ванадия в быстрорежущей стали, тем больше углерода должно содержаться[93]. Молибден снижает критическую скорость отверждения и улучшает свойства отверждения, а также повышает стойкость вольфрама, а также красный цвет быстрорежущей стали. Молибден может быть заменен вольфрамом из быстрорежущей стали из расчета 2 Мас. ч. вольфрама вместо 1 МАС. ч. молибдена.
Однако, чем больше молибдена в твердом растворе, тем больше количество остаточного аустенита высокоскоростного steel. In кроме того, при нагреве стали под закалкой молибден легко выгорает с поверхности инструмента, способствуя сильному обезуглероживанию стали[94]. В стали Р18 и Р9, когда содержание молибдена больше чем 0,3%, содержание вольфрама уменьшено (основанный на 1% МО).Быстрорежущая сталь 221 Вместо 2%W).При указании такой стали добавляются буквы M (P18M и SEM).Содержание молибдена в стали R18M составляет до 1%, а максимальное содержание в стали REM-0,6%. Кобальт является почти полностью твердым раствором и укрепляет металлическую основу iron.
In кроме того, под влиянием кобальта растворимость сложнолегированного карбида увеличивается, и в основе стали появляется богатый углерод, ванадий, вольфрам и др. chromium. As в результате при отпуске стали увеличивается эффект дисперсионного упрочнения, повышается стойкость к красному цвету. increased. As содержание кобальта в закаленных быстрорежущих стальных конструкциях увеличивается, количество остаточного аустенита увеличивается, но остаточный аустенит в кобальтовой стали относительно легче и полностью разлагается при отпуске, поскольку он менее стабилен, чем Кобальтсодержащие стали. Как видно из химического анализа, состав быстрорежущей стали достаточно сложен. Под влиянием хрома, вольфрама и ванадия концентрация углерода в перлите и предел растворения аустенита очень низки, и даже 0,7-0,8% с этой стали относится к карбиду class.
In расплавленное состояние, эвтектика красного Брита наблюдается в структуре быстрорежущей стали, которая дробится при ковке. Кованая быстрорежущая стальная конструкция представляет собой трооститоидный перлит с большим количеством избыточного карбида. Количество карбидной фазы быстрорежущей стали зависит от химического состава и термической обработки. Например, в отожженной быстрорежущей стали Р18 общий вес карбидных осадков, выделенных при фазовом анализе, составляет около 25%.In кроме того, состав карбидов примерно следующий: 3% C, 3% Cr, 60% W, 3% V, остальное (20-30%) — железо. Почти весь ванадий расходуется на образование этих карбидов, до 90% WH, до 50% Cr.
Оставшееся количество легирующего элемента представляет собой твердый раствор iB. Отжиг быстрорежущей стали Р18 Теплопроводность быстрорежущей стали очень низкая, поэтому при отжиге рекомендуется нагревать ее на малых скоростях, не превышающих 100-150 градусов / час. Точка перлитного превращения быстрорежущей стали Р18 соответствует 820-840°, а температура отжига установлена на 860-880°, то есть на 30-40°выше критической point. To во избежание образования крупных стабильных карбидов и ухудшения структуры («порчи»), время выдержки при отжиге быстрорежущей стали должно быть необходимо только для полного нагрева изделия.
Охлаждение осуществляется очень медленно, не превышая 20-25 градусов/час. 222 после кобальтовой стали Подходящий отжиг, твердость быстрорежущей стали должна быть в диапазоне 18-22 HRC или 200-250 HB. Чтобы сократить время отжига и получить наиболее сбалансированную структуру с минимальной твердостью, быстрорежущая сталь обычно подвергается ускоренному изотермическому отжигу. На рисунке 104 представлена схема изотермического превращения аустенита стали Р18 после нагрева при 900 и 1280°С. 900. И затем… 700. Я ж Я 400. 300. 200. В0 Р х Один Один Два 10 10г У3 время, секунд У * / 0 секунд, 10 секунд Рисунок 104.Продолжать Инкубационный период при гидротермическом превращении аустенита стали Р-900 и Р18 после нагрева до 1280°
На рисунке показаны 2 изгиба, соответствующие температуре, при которой аустенит обладает наименьшей стабильностью.1〜й находится в области 720-740°, аустенит растворяется с образованием толстит-перлитовой структуры, а 2 — й-в области 320-340° — игольчатый стоматит. Из рисунка следует, что «при трансформации перлитной области и игольчатой области костного камня инкубационный период после аустенитизации при 1280°значительно дольше, чем после аустенитизации—быстрорежущей стали 223». Вращение на 900°.Это объясняется тем, что при высоких температурах нагрева количество растворенных карбидов увеличивается-аустенит упрочняется углеродом и легирующими элементами, что повышает его стабильность. Изотермический отжиг проводят по следующим режимам: его можно выдерживать при температуре 880°до полного нагрева изделия, выдерживать в течение 3-6 часов и быстро
охлаждать до 720-740°(минимальная стабильная температура аустенита), что сокращает время отжига. (Согласно обязанности печи), охлаждая Мычать. Семьсот пятьдесят &.Z50 управляя Время- Среднеквадратический. 105.Быстрорежущая сталь Р18 обычная (/) и изотермическая (2) отжига по графику / Один / 1 грамм — ч. \ \ Два- В Печах до 400-450°, дальнейшее охлаждение на воздухе. Время работы при изотермическом отжиге значительно сокращается, твердость стали не выше, чем при обычном отжиге за счет непрерывного охлаждения, структура более однородна, а сталь лучше обрабатывается. На рисунке 105 представлен график отжига (нормального и изотермического) стали Р18. В режимы отжига для стали марок Р9,Р9Ф5,Р14Ф4, Р18Ф2 и практически ничем
не отличаются от тех, которые указаны для стали Р18. Введение 5-10%Co в быстрорежущую сталь не изменяет положения критической точки и не влечет за собой резкого изменения скорости превращения аустенита, поэтому кобальтовые стали P9K5,P9KYU, P10K5F5 и R18K5F2 отжигают в одном режиме. Однако следует иметь в виду, что скорость нагрева кобальтовой стали должна быть несколько ниже, чем у Стали Р18, поскольку кобальт снижает теплопроводность steel. In кроме того, кобальтовые стали сильно декарбонизированы, поэтому их необходимо защищать от поверхностного выгорания углерода при отжиге. Упрочнение быстрорежущей стали Быстрорежущая сталь
нагревается с охлаждением 400-450°от критической точки, нагревая инструмент почти до края. Такая высокая температура закалки необходима для полного растворения и перемещения избыточных карбидов как можно дальше. Твердый раствор содержит больше углерода, ванадия, вольфрама и хрома. При закалке быстрорежущей стали от комнатной температуры (40-50°выше критической точки) в аустенит переносится только цементит-эвтектоидный карбид, а избыток специальных карбидов не растворяется, поэтому твердый раствор углерода очень мал(около 0,2%), а твердость стали при закалке снижается, и красная стойкость становится недостаточной. Быстрорежущая сталь характеризуется критической скоростью
закалки, которая ниже, так как она затвердевает, когда образец диаметром 25 мм охлаждается воздухом и имеет максимальную твердость(эту сталь еще называют «самоотверждающейся»).кроме того, чем выше температура нагрева стали перед закалкой, тем больше растворится избыток карбидов, а аустенит будет насыщен углеродом и легирующими элементами, что облегчит охлаждение и сделает скорость закалки более жесткой. Температура мартенситного превращения быстрой ткани и количество удерживаемого аустенита также определяются температурой нагрева стали перед закалкой. Чем выше температура нагрева, тем ниже температура в начале и конце мартенситного превращения, в результате чего в закаленной стальной структуре остается больше аустенита. На рис. 106 показано влияние температуры закалки
быстрорежущей стали Р18 на величину начальной (Mn) и конечной (Mk) точек мартенситного превращения и остаточного аустенита. Дело в том, что при нагреве быстрорежущей стали для закалки учитываются форма и размеры изделия. Небольшие инструменты из стали Р18 (диаметром до 6-8 мм) рекомендуется закалять от 1260°.Инструменты толщиной 10-15 мм и более-от 1280°, а изделия простой формы, например резец-от 1300°. Микроструктура быстрорежущей стали Р18 показана после закалки от оптимальной температуры. 107. По мере повышения температуры закалки аустенитные мартенситные зерна непрерывно растут, что приводит к перегреву быстрорежущей стали при температуре 1320-1330°.Размер зерна быстро увеличивается, мелкие карбиды сливаются в крупные карбиды (Ассоциации).Из-за очень большого перегрева закаленной стали вдоль границ зерен появляется сетка редебрита, указывающая
на начало оплавления(рис.108). Около 40-45% мартенсита, 30-40% аустенита и 15-20% карбидов содержатся в структуре быстрорежущей стали p1260-1280°C (не в весовых процентах).) Карбид быстрорежущей стали имеет высокое содержание вольфрама, и его удельный вес намного выше, чем средний удельный вес стали, поэтому он намного больше, чем объем. Сорок Я Один Пять II」 § 1 £10 в Пять Я I50 \ ч \ \ х х Х / / 80Q 900 1000 1100 1200 1300 Температура в занарии, » C И 00 Рисунок 106.Влияние температуры
закалки на точку Mw и Mk и остаточное содержание аустенита в закаленной стали Р18 На рисунке 109 показано изменение соотношения твердости и конструкционных компонентов стали Р18 в зависимости от температуры отверждения. Эта сталь имеет максимальную твердость 1150-1200°во время hardening. As температура закалки повышается до 1250-1300°, количество удерживаемого аустенита увеличивается, поэтому твердость несколько снижается[95]. Чрезмерная выдержка при температуре закалки, а также повышение температуры нагрева приводит к перегреву стали. При недостаточной экспозиции возможен нагрев
стали, снижается твердость и покраснение инструмента[96]. Быстрорежущая сталь имеет очень низкую теплопроводность, она медленно нагревается при нагреве для закалки. И так оно и есть.、 Рисунок 107. 1280°.Микроструктура стали P250 после заказа от X18 Рисунок 108.Микроструктура стали Р18 после сильного перегрева при закалке. X 250 быстрорежущая сталь 227 о * Тридцать Чтобы не вызвать большого термического напряжения, изделие из этой стали до 820-850°(критической точки) нагревают медленно, после чего сталь переходит в аустенитное состояние, и как только она становится пластичной. Обычно нагрев осуществляется в соляной ванне с 1 или 2 нагревателями.1-я составляет 600-650°с, 2-ой один 800-850°С, последний 1260-180°С. Первый нагрев применяется только для крупных изделий (толщиной 50-60 мм и более) и оборудования
сложной формы. Обычно простой инструмент с толщиной стенки 20-25 мм нагревают только соляной ванной, состоящей из 78% хлорида бария и 22% хлорида натрия, нагретой до 850°. Окончательный нагрев 1260-1280°проводят в ванне с 1-2% желтой кровяной солью или 5-7% бурой 100% хлористым барием для уменьшения окисления и обезуглероживания стали. Время нагрева в соляной ванне устанавливается в зависимости от температуры закалки и размера инструмента. При нагреве инструмента из стали Р18 при 800-850° время нагрева в соляной ванне составляет 15-20 секунд. При окончательном нагреве, закалке в соляной ванне толщиной 1 мм и температурой 1260-180°, предварительно нагретый инструмент
выдерживают со скоростью 5-6 секунд. Толщина изделия на 1 мм (с учетом времени нагрева и выдержки). При охлаждении быстрорежущей стали на воздухе происходит частичное осаждение карбидов из твердого раствора, что приводит к обеднению мартенсита частью углерода, что снижает режущие свойства стали, поэтому закалку обычно проводят в масле. Инструменты сложной формы для уменьшения деформации часто проводят ступенчатую закалку. Первые 1-2 minutes. At температура, соответствующая максимальной стабильности перегретого аустенита (450-550°), охлаждается в высокотемпературной среде жидкостью(например, селитрой), а в конце-воздухом или маслом. В таблице. 67 показывает
оптимальный стандарт режима отверждения. Ноль / В \ ( / — ^ В U00 (100 1200 VOO температура отверждения,£ Рисунок 109. Р18228 влияние температуры закалки на твердость кобальтовой стали и количество остаточного аустенита и карбида Быстрорежущая сталь и приблизительная твердость к затвердетому состоянию. Таблица 67 Режим закалки и твердость отвержденной быстрорежущей стали Марка стали Р18 П9 Р9Ф5 P14F4 Р18Ф2 P9K5 R9KYU Р10К5Ф5 Р18К5Ф2 Температура нагрева,°c 830-850 800-820 830-850 830-850 830-850 800-820 800-820 830-850 830-850 Конечная температура нагрева,°c 1260-1280 1220-1240 1240-1260 1240-1260 1260-1280 1220-1240 1220-1240 1230-1250 1260-1280 Конечное время нагрева, сек{мм 6-8 8-10 10-12 10-12 8-10 5-6
5-6 6-8 6-8 Твердость HRC 62-64 61-63 63-65 64-66 62-64. 63-65 63-65 63-65 62-64. Из таблицы видно, что экспозиция ванны хлорида бария установлена на максимум для того, чтобы при окончательном нагреве (после предварительного нагрева) стали, содержащей высокое содержание углерода и ванадия, перевести в твердый раствор как можно больше стабильного ванадия. При кобальтовой стали с умеренным содержанием ванадия скорость растворения карбидов увеличивается под воздействием кобальта, поэтому выдержка при окончательном нагреве должна быть минимальной. Чрезмерный рост зерен и резкое снижение прочности могут
наблюдаться при слишком сильном воздействии при нагреве кобальтовой стали. УСЗ закаливание После закалки в структуре быстрорежущей стали Р18 сохраняется до 30-40% остаточного аустенита, его присутствие снижает твердость стали и делает структуру стали нестабильной. Поэтому необходимо закалять закаленную сталь.70-80% остаточного аустенита поступает в мартенсит, и твердость стали увеличивается на 2-3 HRC, а организация Он более стабилен. Рисунок PO показывает, как изменяется твердость при использовании быстрорежущей стали.
heated. In сталь, которая нагревается сразу после закалки, при 350-450 ° с твердость уменьшается на 2-3% HRC, а в Стали, которая ранее была закалена до 580° с, твердость при нагреве не изменяется до этой температуры отпуска[97]. Когда закаленная закаленная сталь закалена, несколько основных процессов унесены. Эти процессы, в определенном темпе, являются быстрорежущей сталью Крысы будут течь одновременно и частично перекрывать друг друга. Первый процесс проводят при 100-150°.Это начальная стадия распада мартенсита, которая связана с частичным выходом из твердого раствора атома углерода и незначительным уменьшением площади
атомной кристаллической решетки. Этот процесс сопровождается незначительным уменьшением объема стали, что практически не влияет на изменение твердости. 2-й процесс проводят при температуре 150-400°.Процесс заключается в частичном снятии напряжения, вызванного упрочнением и дальнейшим распадом материала. martensite. At в то же время, объем стали немного уменьшается и твердость уменьшается(2- 3 HRC). Шестьдесят шесть 60. = ’ .с- г / 200 ZOO UOO 500 температура нагрева. °С 600. Рисунок программного обеспечения. Влияние температуры ипрева на твердость стали Р18: — после закалки; — после закалки и отпуска
при температуре 2-680° 3-й процесс протекает при 400-550°.Этот процесс характеризуется тем, что в дополнение к продолжающемуся разложению мартенсита в этом интервале температур карбиды и вольфрамовые стаммы также осаждаются из твердого раствора в критическом дисперсном состоянии, вызывая осаждение твердеющего вещества. steel. In кроме того, в этом диапазоне температур часть аустенита переходит в мартенсит. Это сопровождается незначительным увеличением объема и повышением проницаемости стали. 4-й процесс при отпуске быстрорежущей стали происходит в период охлаждения в диапазоне
200-100°.Этот процесс заключается в том, что остаточный аустенит переходит в мартенсит, то есть происходит вторичная закалка. Это сопровождается резким увеличением объема стали и появлением так называемой «вторичной твердости». в результате твердость закаленной стали на 2-3ВАТА выше, чем у закаленной не закаленной стали. На рисунке 111 показано, как изменяется твердость мартенсита в кобальтовой стали 230. — Но… −1 Это отличный способ начать свой день. 6— «ч» \ \ — Л. Аустенита при отпуске и закалке быстрорежущей стали. Твердость (а) вследствие распада мартенсита непрерывно уменьшается с повышением температуры отпуска. Твердость, обусловленная превращением аустенита в мартенсит, резко возрастает после отпуска при 560-580°(в), в результате чего общая
твердость стали после отпуска увеличивается©. Время выдержки при температуре отпуска быстрорежущей стали существенно не влияет на процесс, так как дисперсионное упрочнение происходит в основном в период нагрева, а остаточный аустенит изменяется на мартенсит в период охлаждения. Поэтому для наиболее полного разложения остаточного аустенита и получения вторичной твердости при −1 I 1 a| p «—I 1 1 1 изменяется многократным отпуском. «• * .* _ — Таким образом, вторичная твердость быстрорежущей стали обусловлена дисперсионным упрочнением при нагреве в области 500-580°с и переходом от остаточного аустенита к мартенситу при охлаждении. Диапазон температур 200-100°.Эти процессы включают большие внутренние напряжения, которые увеличивают хрупкость
стали, поэтому после отпуска при 560-580° напряжение снимается, и инструмент, изготовленный из быстрорежущей стали, дополнительно закаляется при 350°. −400°. в то же время структура и твердость стали практически не требуют 350-400°отпуска с готовым инструментом (после шлифования и заточки) для того, чтобы снять напряжение, возникающее при обработке. Инструмент покрыт тонкой пленкой оксида, что затрудняет прилипание наконечника к инструменту. После надлежащего отпуска многогранная структура закаленной быстрорежущей стали исчезает, и аустенит-мартенситные зерна мигрируют в однородный, безигольный или
мелкоигольный мартенсит без видимой границы. Если температура отпуска низкая или кратность недостаточна, то граница многогранника (зерна) сохраняется в структуре закалочной стали, а мартенситный фон имеет яркое, слегка затухающее поле, и большое количество остаточного аустенита в изобилии. Для Около 100200300400 SOO 600 Отпускная температура.«С» Рисунок 111.Схема изменения твердости при выгрузке закаленной стали Р18: твердость а-мартенсит; б-аустенитная твердость; в-Общая твердость быстрорежущей стали 231 Чтобы получить структуру непрерывного мартенсита, необходимо освободить инструмент дополнительно. При слишком высоких температурах отпуска или чрезмерной кратности
структура закаленной быстрорежущей стали переходит в сорбит, что снижает ее твердость. Такой инструмент может быть исправлен только путем отжига и вторичного упрочнения. Рисунок 112. Микроструктура быстрорежущей стали Р18 после закалки и отпуска. Х 500 На рисунке 112 показана структура быстрорежущей стали Р12, которая закаляется от 1280°, закаляется при 580°с масляным охлаждением в течение 2 часов и подвергается воздействию в течение 1 часа. Структура состоит из мартенсита без гранул и карбидов в виде мелких включений, которые равномерно разбросаны по всему объему. Чем выше температура закалки быстрорежущей стали, тем больше карбидов будет растворено, и твердый раствор будет насыщен примесями углерода и сплава, чтобы увеличить — ^ , 1200 ′ \ t3OO ’/ слишком 200 300 < > 00 500W
температура темперирования. Конечно. Р. является. 113.Влияние температуры закалки на вторичную твердость при отпуске Температура закалки увеличилась на Р18 за счет эффекта вторичной твердости при отпуске (рис. 113).Однако, если температура закалки слишком высока, это очень вредно, так как небольшой перегрев стали приводит к увеличению хрупкости инструмента и снижению прочности на изгиб. Кобальтовая сталь 232 На фиг. 114 представлен график полного цикла термической обработки инструмента из быстрорежущей стали Р18:закалка, в 2 раза более высокая температура отпуска, среднетемпературный (дополнительный)
отпуск. Электроники б 300. О Один ПВО 1 л Один Л / В В . В 580° \ 400° Л Рис. Л4.График закалки и отпуска стальных инструментов Р18 Западные праздники Стандартная быстрорежущая сталь с высоким содержанием углерода и ванадия, а также процесс, происходящий при закалке и отпуске 5-10% Co, практически одинаковы. В таблице. На рисунке 68 показан оптимальный режим отпуска для быстрорежущих сталей. Таблица 68 Режим отпуска и твердость быстрорежущей стали Марка стали Р18 П9 Р9Ф5 P14F4 Р18Ф2 P9K5 P9K10 Р10К5Ф5 Р18К5Ф2 Твердость после закалки, НRС 62-64 61-62 63-65 64-66 62-64. 63-65 63-65 63-65 62-64. Температура отпуска,°C 570-580 550-
560 570-.Пятьсот восемьдесят 580-590 570-590. 570-580 570-580 570-580 570-580 Разнообразие отдыха 2-3 3-4. 3-4. 3-4. 2-3 3-4. 3-4. 3-4. 2-3 Твердость после отпуска, HRC 63-64 62-63 64-65 65-66 63-65 64-65 65-67 65-67 65-66 Охлаждение после темперирования должно производиться маслом. Потому что при быстром охлаждении прочность быстрорежущей стали увеличивается, а хрупкость инструмента уменьшается. При использовании инструментов Р18 и Р9, являющихся основными сортами быстрорежущей стали, следует отметить, что сталь Р18 является более износостойкой и менее
хрупкой, чем сталь Р9.Это мало беспокоит при обработке низколегированных перлитных сталей, но оказывает существенное влияние при резке труднообрабатываемых сталей с более высокой твердостью. Высокованадиевых быстрорежущих сталей Р9Ф5, Р14Ф4, Р18Ф2 и при термообработке менее склонны к перегреву, чем Р18 и Р9 и имеют меньше обезуглероживания.
Смотрите также:
Материаловедение — решение задач с примерами
Новые высокопроизводительные быстрорежущие стали | Влияние кобальта на структуру и свойства перлитной стали |
Обработка холодом закаленной быстрорежущей стали | Кобальтовая магнитная сталь |