Оглавление:
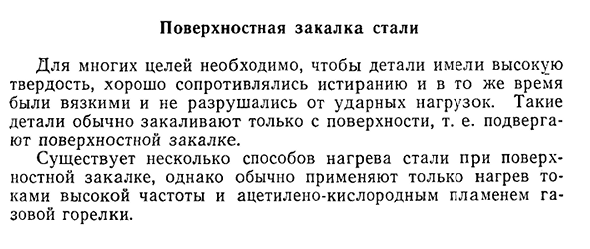
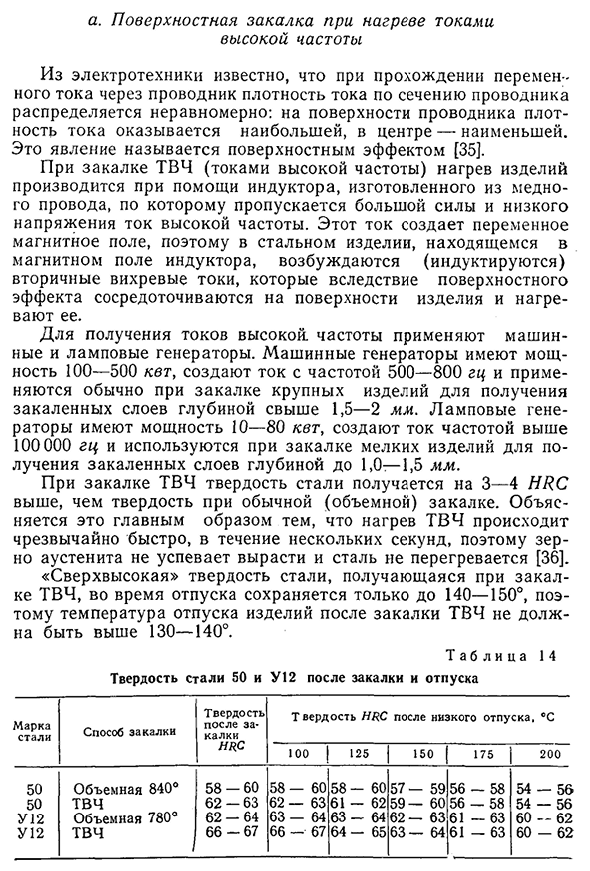
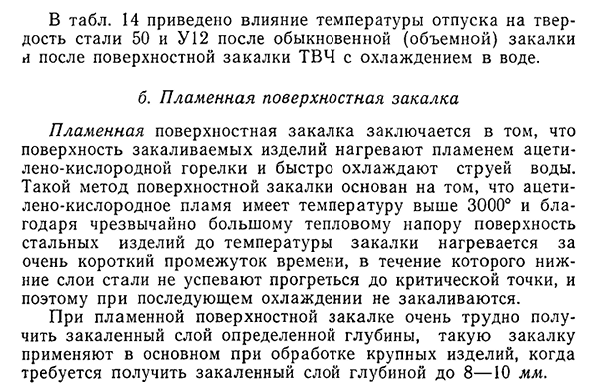

Поверхностная закалка стали
- Поверхностное упрочнение стали Для многих целей необходимо, чтобы детали обладали высокой твердостью, выдерживали износ, и в то же время были вязкими и не разрушались при ударных нагрузках. Такие детали обычно закаляются только с поверхности. То есть, поверхность затвердевает.
Существует несколько способов нагрева стали при поверхностном упрочнении, но обычно используются только высокочастотный ток и нагрев ацетиленокислородным пламенем газовой горелки. a. поверхностное упрочнение при нагреве токами высокой частоты В электротехнике известно, что при прохождении переменного тока через проводник плотность
тока распределяется неравномерно по поперечному сечению проводника. Людмила Фирмаль
Плотность тока на поверхности проводника самая высокая, а в центре-самая низкая. Это явление называется поверхностным эффектом[35]. При отверждении высокочастотным током (high-frequency current) изделие нагревают с помощью индуктора из меди wire. In эта катушка, высокочастотный и высоковольтный ток протекает через большую силу и низкое напряжение. Поскольку этот ток создает переменное магнитное поле, вторичные вихревые токи возбуждаются (индуцируются) в стальных изделиях в магнитном поле индуктора, которые затем нагреваются до концентрации на поверхности изделия за счет поверхностного эффекта.
Для получения высокочастотных токов используются машинные и трубчатые генераторы. Генератор машины имеет мощность 100-500 Кет и вырабатывает ток частотой 500-800 Гц, который обычно используется при отверждении крупных изделий для получения упрочненного слоя глубиной не менее 1,5-2 мм. Выход лампового генератора составляет 10-80 кета, он вырабатывает ток с частотой более 100 000 Гц, используется для отверждения мелких изделий и производит упрочненный слой глубиной 1,0-1,5 мм.
- При упрочнении ТВЧ твердость стали на 3-4 HRC выше, чем при обычном (объемном) упрочнении. Это объясняется главным образом тем, что нагрев ТВЧ происходит очень быстро в течение нескольких секунд, поэтому он не успевает вырасти в аустенитные зерна, а сталь не перегревается[36].«Сверхвысокая» твердость стали, полученной закалкой высокочастотных сплавов при отпуске, остается на уровне 140-150°, поэтому температура отпуска изделия после закалки высокочастотных сплавов не должна превышать 130-140°.
Таблица 14 Твердость стали 50 и U12 после закалки и отпуска Марка стали Пятьдесят Пятьдесят У12 У12 Способ закалки объем 840°HD Объем 780°HD Твердость после зарядки СПЧ 5-8- 6/2- 6/2- Шестьдесят шесть- −60. — 63. — 64. −67. Пятьдесят восемь Шестьдесят два Шестьдесят три Шестьдесят шесть Т приговор Сто −60. — 63. — 64. −67. СПЧ | после минимум 125 150 5-8- 6/1- 6/3- 6/4- −60. — 62. — 64. — 65. 5 7- Пятьдесят девять- Шестьдесят два- Шестьдесят три- Пятьдесят девять 60. Шестьдесят три Шестьдесят четыре Один Пятьдесят шесть- От 5 до 6.- Шестьдесят один- Шестьдесят один- Отпуск Семьдесят пять — Да. — Да. 6-3 6-3 Пятьдесят четыре Пятьдесят четыре 60. 60. °с 200. 55. −56 — 62. — 6 2 закалка поверхности стали 47 В таблице. На рис. 14 показано влияние температуры отпуска на твердость стали 50 и U12 после нормального (объемного)
упрочнения и поверхностного упрочнения ТВЧ охлаждением в воде. B. Людмила Фирмаль
Пылающая поверхностная закалка Упрочнение поверхности горения заключается в том, что поверхность отвержденного продукта нагревается пламенем ацетиленокислородной горелки и быстро охлаждается в потоке воды. Этот способ поверхностного упрочнения основан на том, что температура ацетилен-кислородного пламени превышает 3000°С, и вследствие очень высокого теплового давления поверхность стального изделия нагревается до температуры отверждения за очень короткое время, в течение которого нижний слой стали не нагревается.
При поверхностном упрочнении пламенем очень трудно получить упрочненный слой определенной глубины. Такое упрочнение применяется в основном при обработке крупных изделий, когда необходимо получить упрочненный слой глубиной 8-10 мм.
Смотрите также:
Материаловедение — решение задач с примерами
Цементация стали | Закалка углеродистой стали стандартного состава |
Азотирование стали | Отпуск закаленной стали |