Оглавление:
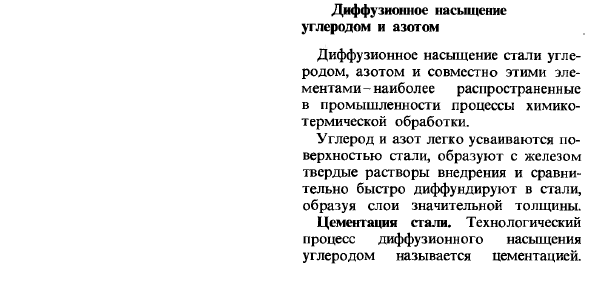
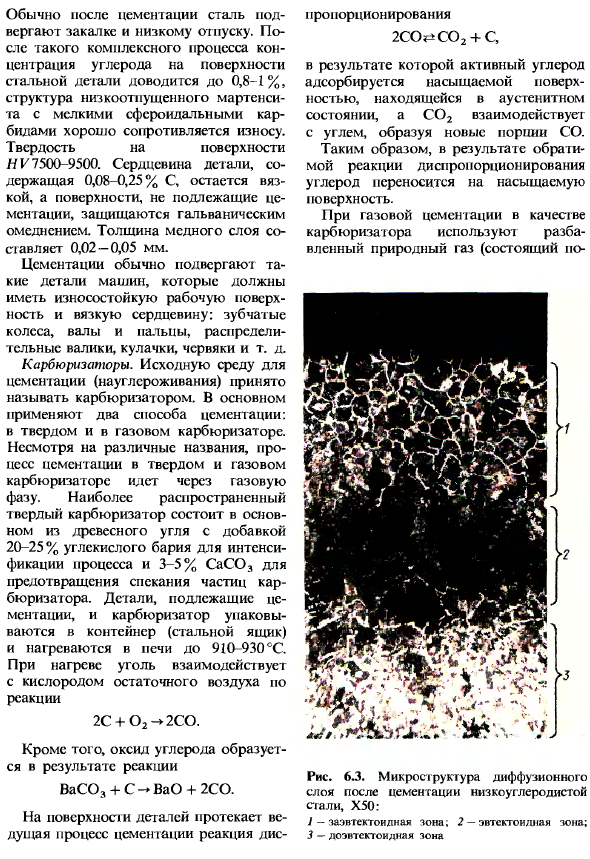
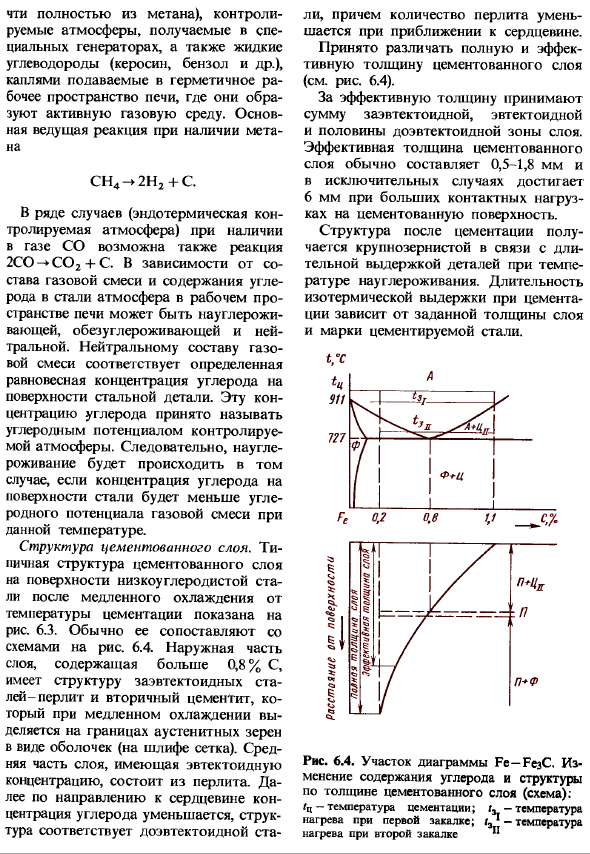
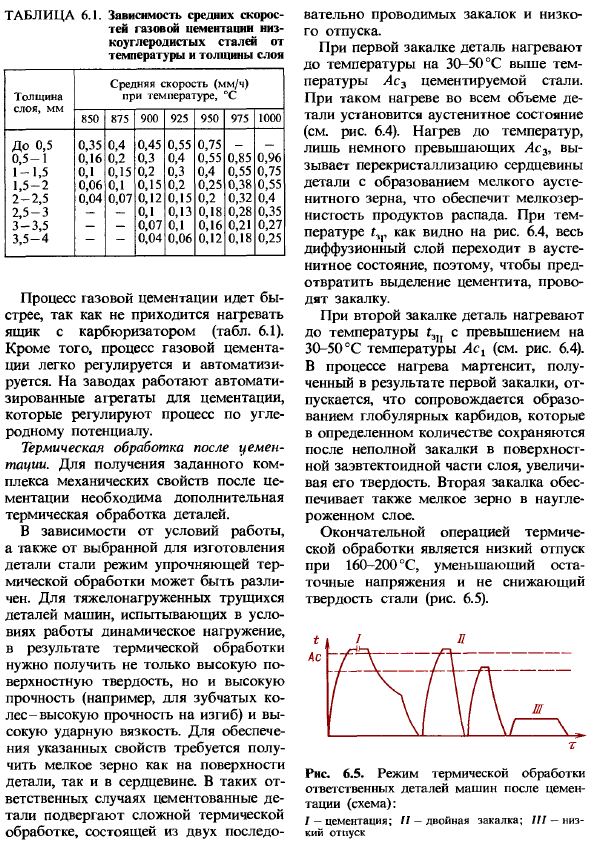
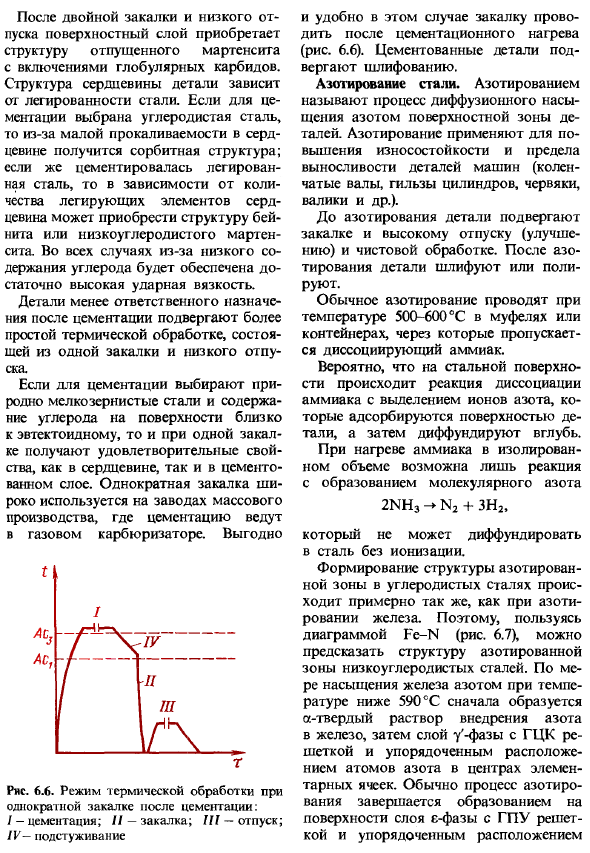
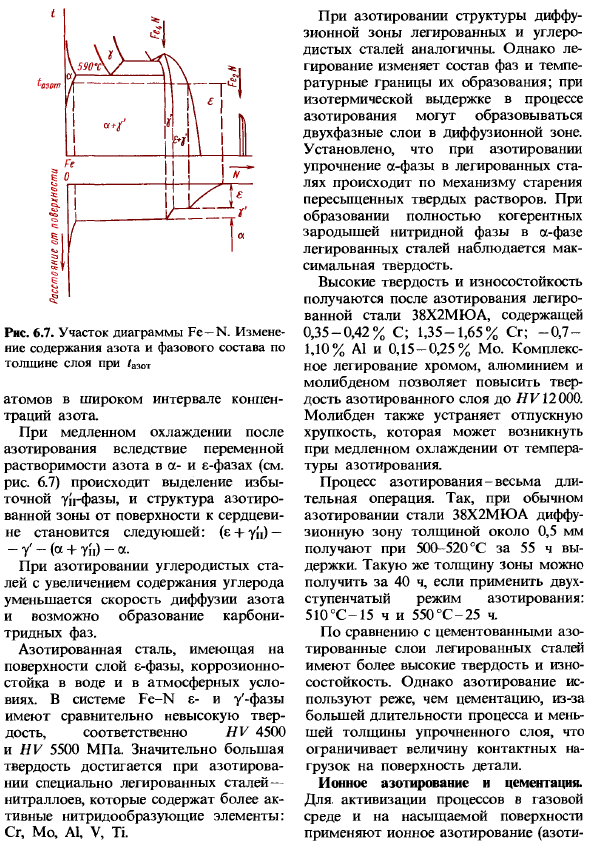
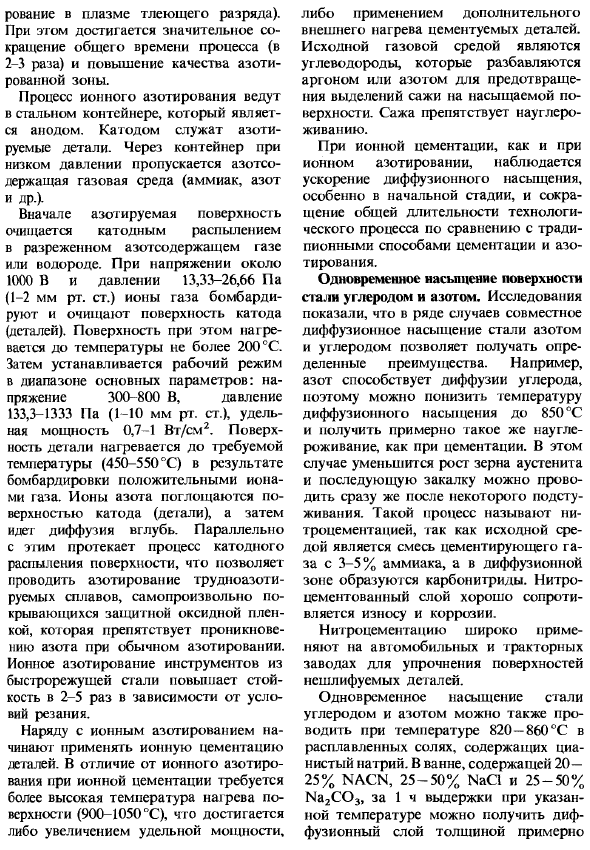
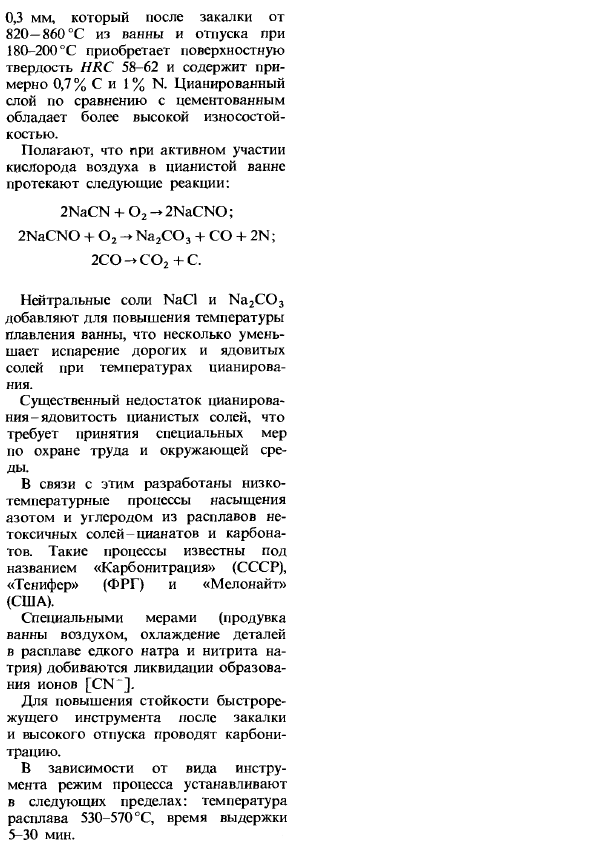

Диффузионное насыщение углеродом и азотом
- Диффузионное насыщение Углерод и азот Диффузионное насыщение углерода, азота и стали, содержащих эти элементы, является наиболее распространенным процессом химико-термической обработки в промышленности. Углерод и азот легко поглощаются на поверхности стали, образуя твердый раствор типа входа с железом, диффундируя в стали относительно быстро, образуя слой значительной толщины. Цементная сталь.
Процесс диффузионного насыщения углеродом называется цементацией. Как правило, после цементации сталь закаляется и подвергается низкому отпуску. После такого сложного процесса концентрация углерода на поверхности стальных деталей составит 0,8-1%, а структура мартенсита низкотемпературного отпуска с мелкими шаровидными карбидами будет хорошо выдерживать износ. Поверхностная твердость Ч 7500-9500 В. Сердечник выполнен с содержанием 0,08-0,25% с, сохраняя вязкость, поверхность, не подвергнутая науглероживанию,
защищена гальваническим омеднением. Людмила Фирмаль
Толщина медного слоя составляет 0,02-0,05 мм. Такие детали станка обычно подвергаются цементации, которая должна иметь износостойкую рабочую поверхность и вязкий сердечник: шестерни, валы и пальцы, распределительные валы, кулачки, грелки и др. Карбюратор. Начальную среду цементации (цементирования) обычно называют цементирующим агентом. В основном используются 2 вида методов цементирования: твердые и газовые карбюраторы. Несмотря на различные названия, процесс цементации твердого и газового карбюризатора проходит через газовую фазу.
Наиболее распространенный твердый Карбюратор состоит в основном из древесного угля, 20-25% карбоната бария усиливает процесс, 3-5% CaCO3 предотвращает спекание частиц карбюратора. Науглероживающие детали и науглероживающая машина упаковываются в контейнер (стальной ящик) и нагреваются до 910 930°C в печи при нагревании уголь взаимодействует с кислородом остаточного воздуха, но реакции не происходит. 2С + О2-> 2со. Кроме того, в результате реакции образуется монооксид углерода BaCO3 + C-BaO + 2CO.
- Основной процесс цементации протекает на поверхности детали. Репортаж Эндрю обоего в Кэри, Северная Каролина; редактирование Дэвидом Грегорио 2ПК ^ СО2 + С、 В результате активированный уголь адсорбируется на насыщенной поверхности аустенитного состояния, а СО2 взаимодействует с углем, образуя новую часть со. Таким образом, в результате обратимой реакции диспропорционирования углерод перемещается на насыщенную поверхность. В газ-цемент, разбавленный газ( Диаграмма 63.Микроструктура диффузионного слоя после цементации низкоуглеродистой стали, Х50: 1-за-эвтектоидная Зона; 2-эвтектоидная зона; 3-pre-Pied зона Почти полностью из метана), контролируемая атмосфера, получаемая с помощью специального генератора, и жидкие углеводороды(керосин, бензол и др.), капельки, подаваемые в замкнутое рабочее пространство печи, образуют активную газовую среду.
Основная реакция свинца в присутствии метана СН4 — » 2Н2 +С. В присутствии газа CO (эндотермическая контролируемая атмосфера)в некоторых случаях также возможна реакция 2CO- * CO2 + C. В зависимости от состава смешанного газа и содержания углерода в стали, атмосфера в рабочем пространстве печи будет науглероживаться, обезуглероживаться и нейтрализоваться. Нейтральный состав газовой смеси соответствует определенной равновесной концентрации углерода на поверхности стальной детали.
Эта концентрация углерода обычно называется углеродным потенциалом контролируемой атмосферы. Людмила Фирмаль
Поэтому науглероживание происходит тогда, когда концентрация углерода на поверхности стали ниже углеродного потенциала смешанного газа при заданной температуре. Структура цементного слоя. Типичная структура цементного слоя на поверхности мягкой стали после медленного охлаждения от температуры цемента показана на рисунке. 6.3.Обычно ее сравнивают со схемой рисунка. 6.4. Внешняя часть слоя, содержащая более 0,8% С, имеет структуру гиперэвтектоидной перлитной стали и вторичного цементита, и при медленном охлаждении она выделяется на границе аустенитного зерна в виде оболочки (в тонком сечении сегмента).
Средняя часть слоя эвтектоидной концентрации состоит из перлита. Далее по направлению к ядру концентрация углерода уменьшается, и структура соответствует переэвтектоиду Уменьшается ли количество перлита по мере приближения к ядру. Принято различать полную и эффективную толщину цементного слоя(см. рис. 6.4). Эффективная толщина равна сумме половины заэвтектоидного, соосаждение, и заэвтектоидного слоя зон. Эффективная толщина цементного слоя обычно составляет 0,5-1,8 мм, а в исключительных случаях контактная нагрузка цементной поверхности достигает 6 мм в условиях высокой контактной нагрузки.
Поскольку деталь подвергается длительному воздействию температуры цементации, структура после цементации становится крупнозернистой. Время изотермической выдержки при цементации зависит от толщины указанного слоя и марки цементированного карбида. Рисунок 6.4.Черчение мм Fe-FeaC. От Изменение содержания и структуры углерода по толщине цементного слоя (рисунок): Гц-цементирование температура; отопление в течение первых твердения; отопление во время Второй отверждения Ъ-температура < 3Р » tmppeRat > Ра Диффузионное насыщение Углерод и азот Диффузионное насыщение углерода, азота и стали этими элементами является наиболее распространенным процессом химико-термической обработки в промышленности.
Углерод и азот легко поглощаются на поверхности стали, образуя твердый раствор, такой как Железный вход, относительно быстро диффундируя в сталь и образуя слой значительной толщины. Цементная сталь: процесс диффузионного насыщения углеродом называется цементацией. Обычно после цементирования сталь закаляют и подвергают низкому отпуску. После такого сложного процесса концентрация углерода на поверхности стальных деталей составит 0,8-1%, а структура мартенсита низкотемпературного отпуска с мелкими шаровидными карбидами будет хорошо выдерживать износ. H 7500-9500 B.
сердечник создается с содержанием 0,08-0,25% s, а науглероживаемая поверхность защищается гальваническим меднением, сохраняя при этом вязкость. Толщина медного слоя составляет 0,02-0,05 мм. Обычно такие детали машин подвергаются цементации с износостойкой рабочей поверхностью и вязким сердечником: шестерни, валы и пальцы, распределительные валы, кулачки, нагреватели и так далее. Карбюратор: начальное средство цементации обыкновенно названо цементируя агентом. В основном используются 2 типа методов цементирования: твердый карбюратор и газовый карбюратор.
Несмотря на различные названия, процесс цементации твердого и газового карбюратора проходит через газовую фазу.20-25% древесного угля, карбонат бария усиливает процесс, 3-5% CaCO3 предотвращает спекание частиц карбюратора. Нер (стальной ящик) и при нагревании до 910-930°С в печи уголь взаимодействует с кислородом остаточного воздуха, но реакции не происходит. 2С + О2-> 2со. Кроме того, в результате реакции образуется монооксид углерода. BaCO3 + C-BaO + 2CO. Основной процесс цементирования происходит на поверхности деталей.
Репортаж Эндрю Кэри из Северной Каролины; редактирование Лизы Шумейкер редактирование Дэвида Грегорио 2ШТ ^ СО2 + С、 В результате активированный уголь адсорбируется на насыщенной поверхности аустенитного состояния, а СО2 взаимодействует с углем, образуя новую часть со. Таким образом, в результате обратимой реакции диспропорционирования углерод перемещается на насыщенную поверхность. Цементный газ, разбавленный газ( Диаграмма 63.Микроструктура диффузионного слоя после цементации мягкой стали, Х50: 1-Эвтектоидная Зона; 2-эвтектоидная зона; 3 предварительно проложенных зоны Жидкие углеводороды (керосин, бензол и др.), которые управляются с помощью специального генератора (почти полностью из метана), а капельки жидкости, подаваемые в замкнутое рабочее пространство печи, образуют активную газовую среду. СН4- » 2Н2 +С.
В присутствии газа CO (эндотермическая контролируемая атмосфера) в некоторых случаях также возможна реакция 2CO- * CO2 + C. В зависимости от состава смешанного газа и содержания углерода в стали, атмосфера рабочего пространства печи карбонизируется, обезуглероживается, нейтрализуется. Нейтральный состав газовой смеси соответствует определенной равновесной концентрации углерода на поверхности стальной детали, и эту концентрацию углерода обычно называют углеродным потенциалом контролируемой атмосферы. Если концентрация углерода на поверхности стали ниже углеродного потенциала смешанного газа при данной температуре, то она уменьшается.
Структура цементного слоя типичная структура цементного слоя на поверхности мягкой стали после медленного охлаждения от температуры цемента показана на рисунке. 6.3.Обычно его сравнивают с цифрой на рисунке. 6.4. Наружная часть слоя, содержащая более 0,8% С, имеет структуру надэвтектоидной перлитной стали и вторичного цементита, а при медленном охлаждении выделяется на границе аустенитного зерна в виде оболочки(тонкий участок сегмента).Далее по направлению к ядру концентрация углерода уменьшается, и структура соответствует переэвтектоиду Уменьшается ли количество перлита по мере приближения к ядру?
Принято различать полную и эффективную толщину цементного слоя(см. рис. 6.4). Эффективная толщина равна сумме половины зоны заэвтектоидного, соосаждения, и заэвтектоидного слоя. Эффективная толщина цементного слоя обычно составляет 0,5-1,8 мм, а в исключительных случаях контактная нагрузка цементной поверхности достигает 6 мм при высокой контактной нагрузке. Поскольку компоненты подвергаются воздействию температуры цементации в течение длительного времени, структура становится грубой после цементации.
Для цементированного карбида, оно зависит от толщины определенного слоя и ранга цементированного карбида. Рисунок 6.4.После нанесения двойного упрочнения и низкого отпуска поверхностный слой приобретает закалочную мартенситную структуру, содержащую шаровидные карбиды. Структура сердечника детали зависит от легирования сплава. Если для цементации выбрана углеродистая сталь, то сердцевина менее затвердевает, в результате чего образуется сорбитовая структура. Если легированная сталь соединяется, то в зависимости от количества легирующих элементов сердцевина может приобретать структуру бейнита или низкоуглеродистого martensite. In во всех случаях, благодаря низкому содержанию углерода, обеспечивается достаточно высокая степень ударной вязкости.
Детали с меньшей ответственностью после цементации подвергаются простой термической обработке, состоящей из 1 закалки и низкого отпуска. Если для цементации выбрана натуральная мелкозернистая сталь и содержание углерода на поверхности близко к эвтектоидному, то даже 1 закалка даст удовлетворительные характеристики как в сердцевине, так и в цементируемом слое. Однократное отверждение широко применяется на заводах массового производства, где цемент изготавливают с помощью газового карбюратора. Рентабельный Это хорошее место для начала. 6.6.Режим термической обработки закалка после цементации один: Я-цемента; Б-закалка; III-в отпуск; ИЖ-ремонт В данном случае, это удобно, чтобы вылечить его после цементирования отопление (рис. 6.6).Соединяемые детали шлифуются. Азотированная сталь.
Азотирование-это процесс диффузионного насыщения азотом в поверхностной зоне детали. Азотирование применяется для повышения предела износостойкости и долговечности механических деталей (коленчатого вала, гильзы цилиндра, червяка, ролика и др.). Перед азотированием деталь подвергается упрочнению и высокотемпературному отпуску (улучшению) и отделке. После азотирования детали шлифуются или полируются. Обычное азотирование проводят при температуре 500-600 ° С в муфеле или контейнере, через который проходит диссоциированный аммиак.
На поверхности стали происходит диссоциация аммиака и высвобождение ионов азота, и ионы азота могут адсорбироваться на поверхности детали и глубоко диффундировать. Нагревание аммиака в изолированном объеме допускает только реакцию с образованием молекулярного азота 2NH3 — > N2 +ЗН2. ns диффундирует в сталь без ионизации. Формирование структуры зоны азотирования в углеродистой стали происходит примерно так же, как и азотирование железа. Поэтому диаграмма Fe-N (рис. 6.7) может быть использована для прогнозирования структуры зоны азотирования низкоуглеродистой стали.
При измерении насыщения железа азотом при температуре ниже 590°С сначала образуется α-твердый раствор включения азота в железо, затем слой γ ’ — фазы с регулярным расположением атомов азота и решеткой fcc в центре элементарной ячейки. Как правило, процесс нитрирования завершается формированием на поверхности с-фазы слоя с решеткой гхп и регулярным выравниванием. Рисунок 6. 7. График Fc-N. / изменения содержания азота и фазового состава по отношению к толщине слоя под азотом Атомы с широким диапазоном концентраций азота.
По мере изменения растворимости азота в фазах а и Е во время отжига после азотирования (см. рис.6.7) высвобождается избыточная верхняя фаза, и структура зоны азотирования от поверхности к сердцевине становится: (e + uz) -/ — («+Yh»)-a. Азотирование углеродистой стали за счет увеличения содержания углерода снижает скорость диффузии азота и позволяет образовывать карбонатную фазу. Азотированная сталь с с-фазным слоем на поверхности обладает коррозионной стойкостью в водных и атмосферных условиях. В системе Фейна твердость e-фазы и фазы y ’ является относительно низкой твердостью HV 4500 и Il V 55 (X) МПа, соответственно.
Нитридирование специально легированных сталей, т. е. нитроидов, содержащих более активные нитридообразующие элементы, такие как Cr, Mo, Al, V, Ti, значительно увеличит твердость. Для азотирования структура диффузионной зоны легированной стали и углеродистой стали аналогична. Однако легирование изменяет состав фазы и температурную границу ее образования. При изотермическом воздействии в процессе азотирования в диффузии может образовываться двухфазный слой phase.
It установлено, что при азотировании происходит фазовое упрочнение легированных сталей по механизму старения пересыщенного твердого раствора. Максимальная твердость наблюдается при образовании полностью агрегированного ядра нитридной фазы в α-фазе легированной стали. Азотирование легированной стали 38Х2МЮА, содержащей 0,35-0,42%, дает высокую твердость и износостойкость. 1.35-1.65%СГ; — 0.7-1.10%А1 и 0,15-0.25%МО. Комплексное легирование хромом, алюминием и молибденом позволяет повысить твердость азотированных слоев до HV12000.Молибден также устраняет свойство отверждения, которое возникает, когда молибден медленно охлаждается от температуры азотирования.
Процесс азотирования занимает очень много времени operation. So, нормальное азотирование стали 38Х2МЮА д Диффузионная зона толщиной около 0,5 мм получается при 55-часовой выдержке при 500 520 л. с. Толщина же зоны получается путем применения процесса азотирования 510°с-15 часов и 550°С-25 часов в 2 этапа-40 часов. Сравненный с слоем азотирования цемента стали сплава, он имеет высокую твердость и сопротивление носки. Азотирование, однако, применяется не чаще, чем науглероживание, из-за большего времени обработки и меньшей толщины упрочненного слоя, что ограничивает величину контактной нагрузки на поверхность детали. Азотирование ионов и Cementation.
To для активации процесса в газовой среде и на насыщенной поверхности применяют ионное азотирование (азот и цементированный карбид в зависимости от толщины конкретного слоя и ранга цементированного карбида). Рисунок 6.4: после нанесения двойного упрочнения и низкотемпературного отпуска поверхностный слой приобретает закалочную мартенситную структуру, содержащую глобулярные карбиды. Структура сердцевины детали зависит от легирования сплава. При соединении стали, в зависимости от количества легирующих элементов, сердцевина может приобретать структуру бейнита или низкоуглеродистого мартенсита. Благодаря низкому содержанию углерода обеспечивается достаточно высокая степень ударной вязкости.
Детали с меньшей ответственностью после цементации подвергаются простой термической обработке, которая состоит из 1 закалки и низкого отпуска. Если для цемента выбрать натуральную мелкозернистую сталь, а содержание углерода на поверхности близко к эвтектоидному, то даже 1 твердение даст достаточные свойства как в сердцевине, так и в цементном слое. Одиночный лечить широко использован в Фабрике массового производства для произведения цемента используя карбюратор газа. Экономическая эффективность Это хорошее место для начала. 6.6.Режим термической обработки после цементации лечить: Собственн-цемента; Б-отверждения; в III-на отпуск; Ил реставрации В этом случае его удобно затвердевать после фиксации нагрева цементом (рис.6.6).
Азотирование стали азотирование стали — это процесс диффузии и насыщения азотом поверхности детали, который используется для повышения предела износостойкости и долговечности деталей машин (коленчатого вала, гильзы цилиндра, червяка, ролика и др.). Перед азотированием деталь подвергают закалке и горячему отпуску(усовершенствованию) и отделке, после азотирования деталь шлифуют или полируют. Обычное азотирование проводят при температуре 500-600°С в муфеле или контейнере, через который проходит диссоциированный аммиак.
На поверхности стали аммиак диссоциирует и ионы азота высвобождаются, а ионы азота адсорбируются на поверхности детали и глубоко диффундируют. Нагрев аммиака в изолированных объемах допускает только реакцию с образованием молекулярного азота 2NH3 — > N2 +ЗН2. ns диффундирует в сталь без ионизации. Поскольку структура полосы азотирования углеродистой стали примерно такая же, как и при азотировании железа, структуру полосы азотирования низкоуглеродистой стали можно предсказать с помощью диаграммы Fe-N (рис.6.7). При измерении насыщения железа азотом при температуре ниже 590°с сначала образуется α-твердый раствор с включением азота в железо, затем слой γ ’ — фазы с регулярным расположением атомов азота и решеткой fcc в центре элементарной ячейки. фаза c слоя с решеткой ghp и регулярной решеткой. Рисунок 6. 7. График ФК-Н. /
Изменение содержания азота и фазового состава в зависимости от толщины азотсодержащего слоя Атомы с широким диапазоном концентраций азота. При изменении растворимости азота в фазах а и Е в процессе пост-азотирующего отжига (см. рис. 6.7) высвобождается избыточная верхняя фаза, и структура зоны азотирования от поверхности к ядру становится: (e + uz) — / — («+Yh»)- A. Азотирование углеродистой стали за счет увеличения содержания углерода снижает скорость диффузии азота и позволяет образовывать карбонатную фазу.
Азотированная сталь с с-фазным слоем на поверхности обладает коррозионной стойкостью в водных и атмосферных условиях. В системе Fein, твердость e-участка и участка y ’ относительно низкая твердость HV 4500 и Il V 55 (X) MPa соответственно, азотирование нитрида, включая более активный нитрид формируя элементы как специальная сталь сплава, то есть, Cr, Mo, Al, V, Ti значительно улучшает твердость. Для азотирования структура диффузионных полос легированной стали и углеродистой стали аналогична, но легирование изменяет фазовый состав и температурную границу ее образования. При изотермическом воздействии в процессе азотирования образуется двухфазная фаза.
Слои могут быть сформированы во время диффузии. Благодаря механизму старения пересыщенного твердого раствора максимальная твердость наблюдается при образовании полностью агрегированного ядра нитридной фазы α-фазы легированной стали. При азотировании легированной стали 38Х2МЮА, содержащей 0,35-0,42%, можно получить высокую твердость и износостойкость. 1.35-1.65%СГ; — 0.7-1.10%А1 и 0,15-0.25%МО. Композитное легирование хромом, алюминием и молибденом может увеличить твердость азотированного слоя до HV12000.Молибден также удаляет упрочняющие свойства, которые возникают, когда молибден медленно охлаждается от температуры азотирования.
Поскольку процесс азотирования занимает очень много времени, нормальное азотирование 38Х2МЮА д 0,3 мм стали закаляют при 820-860°С от панели и закаляют обратно при 180-200°С, получают поверхностную твердость HRC 58-62, около 0, 7%С и 1% Н. цианидный слой имеет более высокую износостойкость по сравнению с цементным слоем. Считается, что при активном участии кислорода воздуха в цианидных ваннах развивается следующая реакция. 2NaCN + O2 — * 2NaCNO; 2NaCNO + O2-Na2CO3 + CO + 2N; 2СО СО2 + С Добавляют нейтральные соли NaCl и Na2CO3 для повышения температуры плавления ванны и несколько уменьшают испарение дорогостоящих и токсичных солей при цианидных температурах.
Существенным недостатком цианирования является токсичность цианидных солей, что требует специальных мер по защите работников и окружающей среды. В связи с этим разработан процесс низкотемпературного насыщения азотом и углеродом расплавов нетоксичных солей (цианатов и карбонатов).Такие процессы известны под названиями «Карбонитрация»(СССР),»Тенифср»(Германия) и»дыня» (США). Специальными средствами (продувка ванны воздухом, охлаждение охлаждающей части раствором каустической соды и нитрита натрия) удаляют образование ионов[CN-J.
Для повышения стойкости быстрорежущих инструментов после закалки и высокотемпературного отпуска проводят карбонизацию. В зависимости от типа инструмента, режим процесса устанавливается в следующем диапазоне: температура плавления 530-570°с, Время выдержки 5-30 минут.
Смотрите также:
Материаловедение — решение задач с примерами
Диффузионное насыщение сплавов металлами и неметаллами | Основные виды термической обработки стали |
Общие требования, предъявляемые к конструкционным материалам | Общие закономерности |