Оглавление:
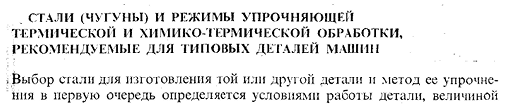
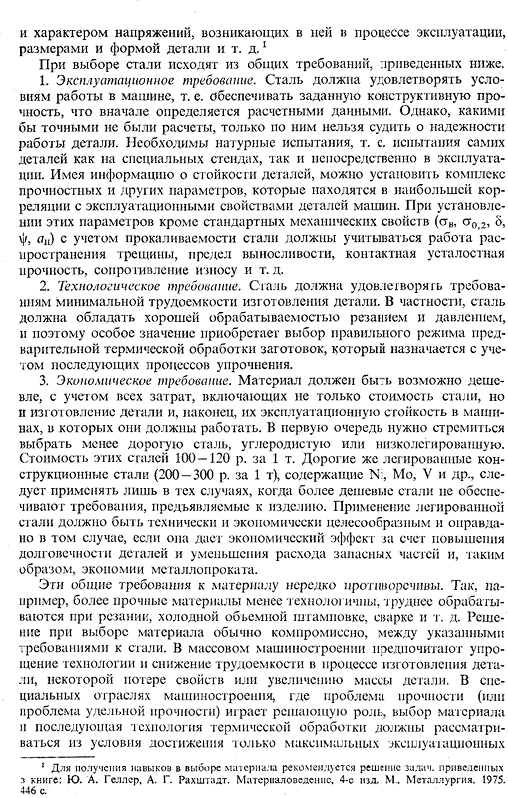
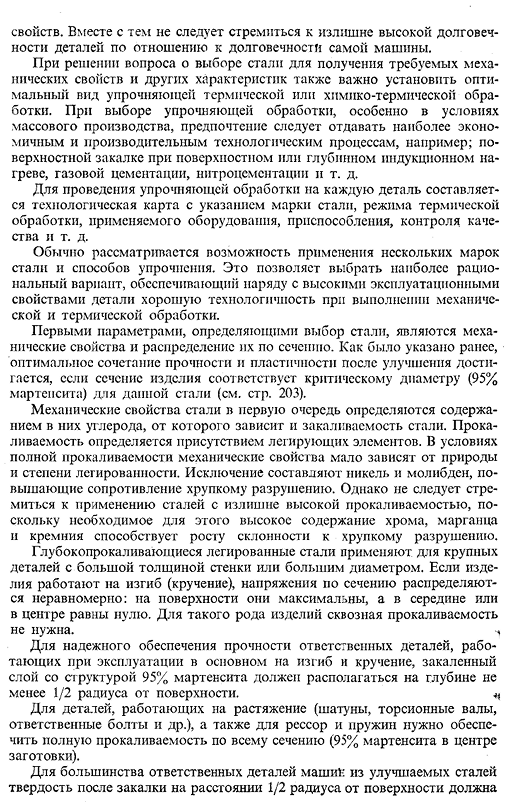
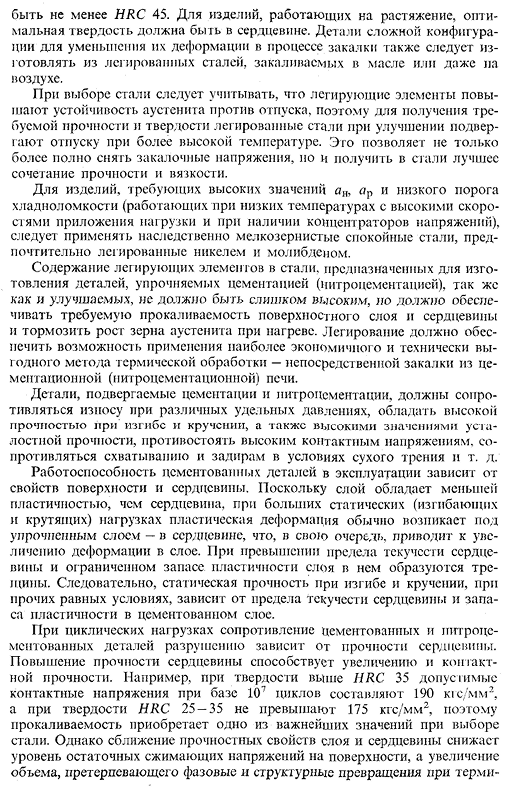
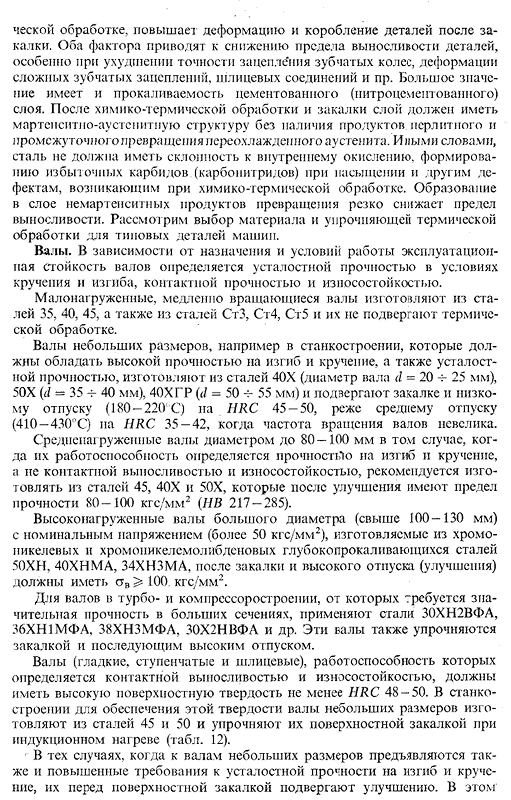
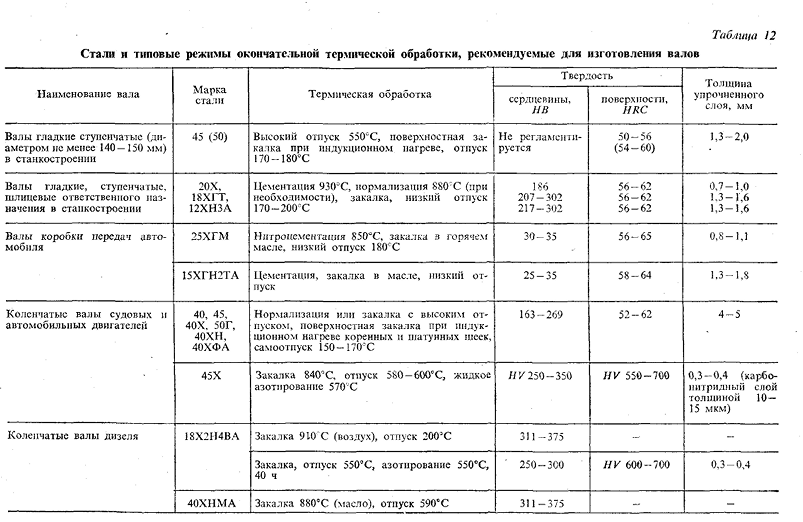
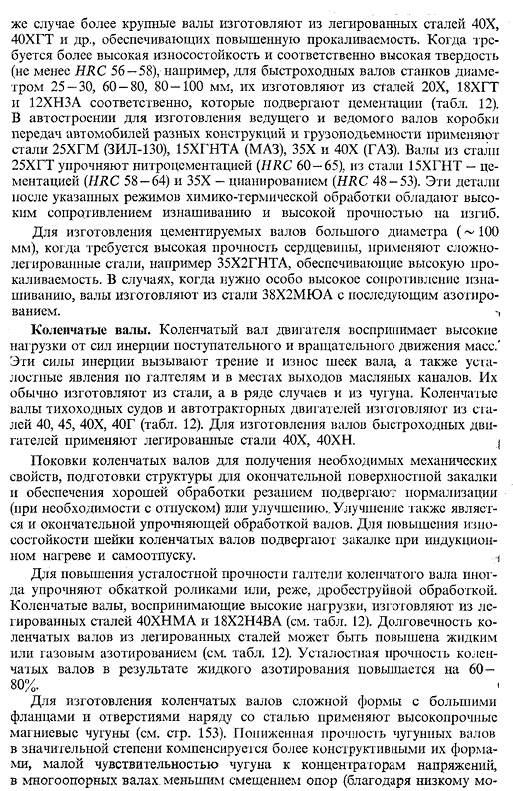

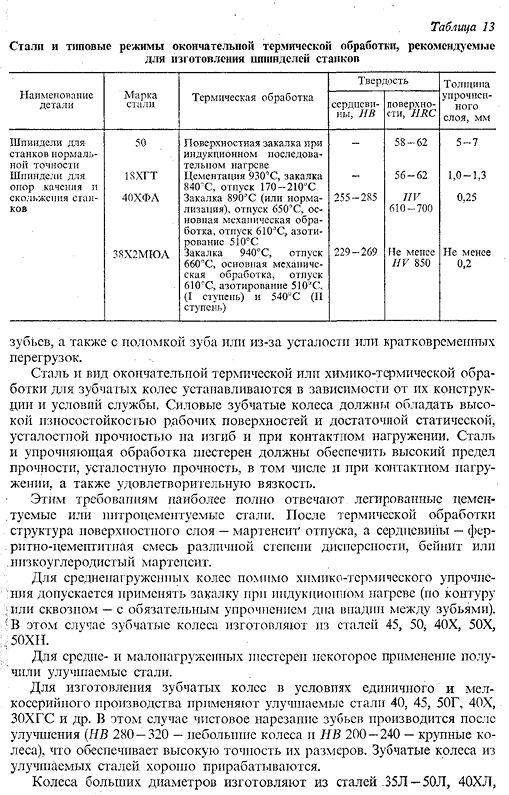
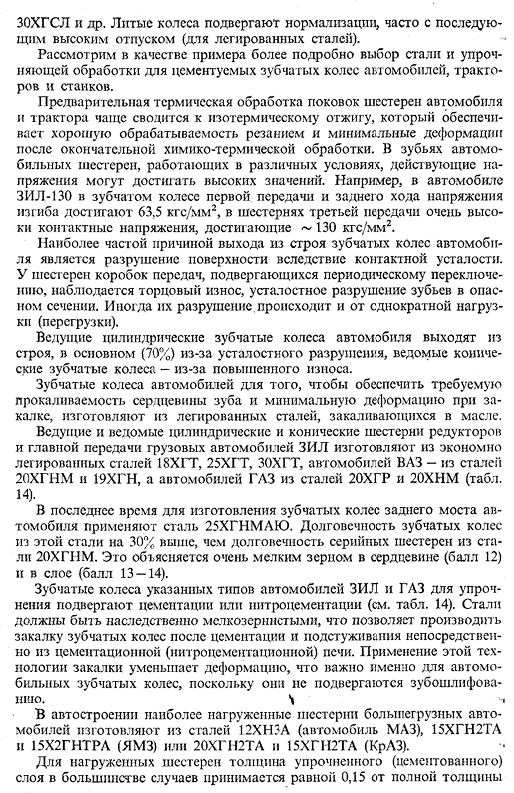
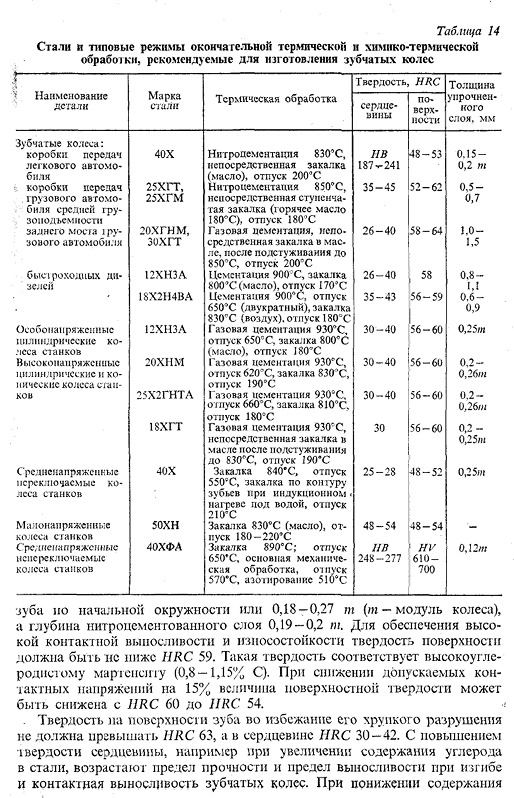
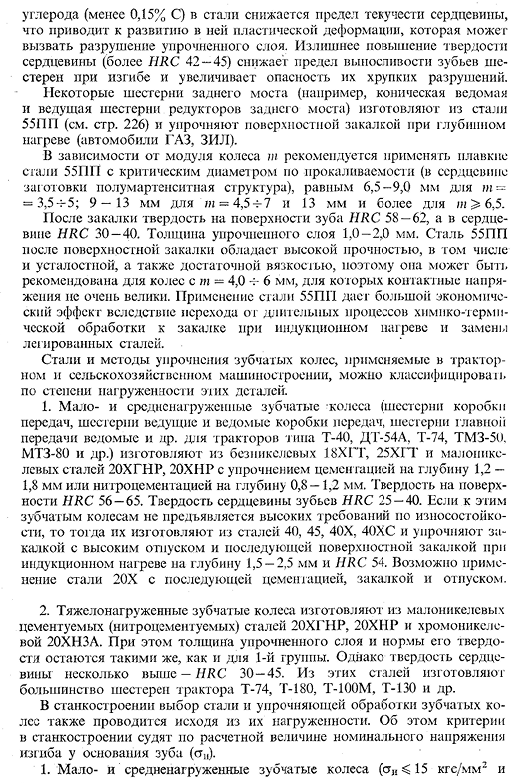
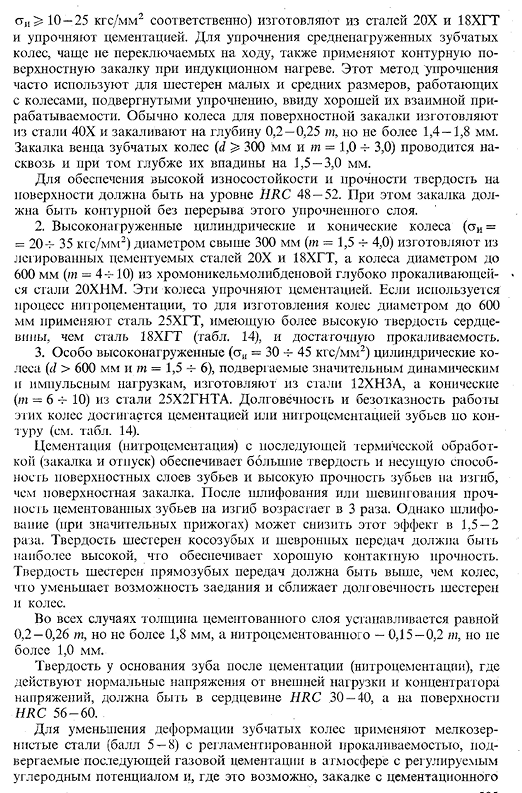
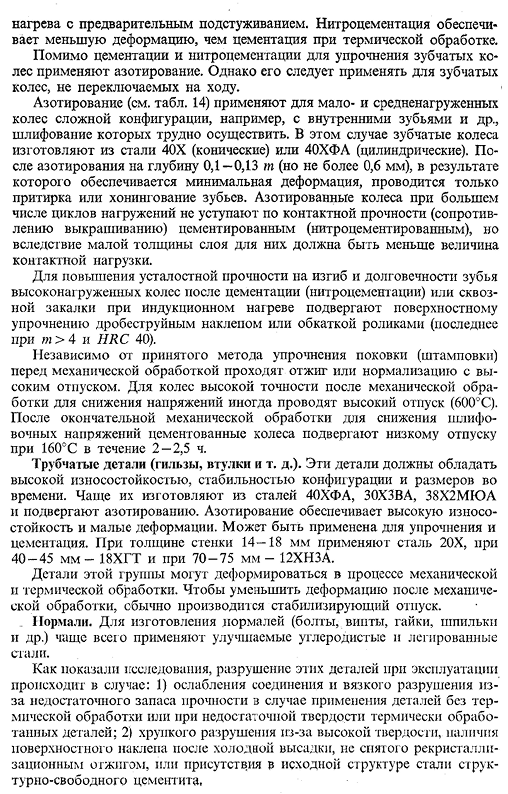
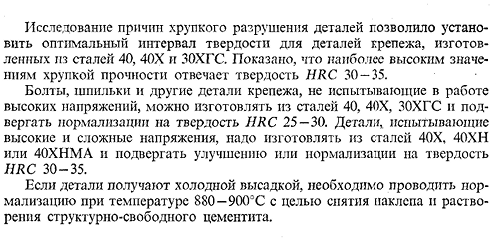

Стали (чугуны) и режимы упрочняющей термической и химико термической обработки, рекомендуемые для типовых деталей машин
- Сталь (литое Железо) и усиленный режим Тепло-и химико-термическая обработка、 ■ Рекомендуется для типовых деталей машин > Выбор и способ упрочнения стали для производства 1 или другой детали в основном определяется условиями труда, стоимостью детали 273 и характер напряжений, возникающих в процессе эксплуатации, размер и форма детали и др.1.Выбирая сталь, они исходят из общих требований, перечисленных ниже. 1.Оперативные потребности. Сталь должна соответствовать условиям работы в машине.
То есть она должна обеспечивать заданную прочность конструкции, которая определяется в первую очередь по расчетным данным. Однако какими бы точными ни были расчеты, только они не могут определить надежность деталей. Необходим полноценный тест. То есть испытание обеих деталей как на специальном стенде, так и в непосредственной эксплуатации. Имея информацию о долговечности детали, можно установить набор прочностных и других параметров, которые наиболее коррелируют с эксплуатационными характеристиками механической детали. При задании этих параметров, помимо стандартных механических свойств (bt, s 0 2, 8,|/, ai), необходимо учитывать упрочнение стали, работу распространения трещин, предел выносливости, прочность на контактную усталость, износостойкость и др. изготовления parts.
Требования. Сталь должна отвечать требованиям минимальной сложности Людмила Фирмаль
In в частности, сталь должна обладать хорошей обрабатываемостью резанием и давлением, поэтому особенно важно правильно выбрать предварительный нагрев заготовки, который назначается с учетом последующего процесса упрочнения. 3.Экономическая потребность. Материал должен быть максимально дешевым, с учетом всех затрат, включая не только стоимость стали, но и изготовление деталей. Прежде всего, нужно приложить усилия, чтобы выбрать дешевую сталь, углеродистую или низколегированную. Стоимость этих сталей составляет 100-120 р. дорогостоящие легированные конструкционные стали, в том числе Ni, Mo, V и др. (1Т при 200-300р.) следует использовать только в том случае, если дешевая сталь не соответствует требованиям изделия. Применение легированной стали должно быть технически и экономически целесообразным и обоснованным при снижении экономического эффекта за счет повышения долговечности деталей и снижения расхода запасных частей для экономии металлопроката. Эти общие материальные требования часто противоречивы.
Например, прочные материалы не являются технологически продвинутыми и трудными в обработке, такие как резка, холодная ковка и сварка. Решение при выборе материала обычно идет на компромисс между обозначением требований к стали. Массовое машиностроение предпочитает упрощение технологии и снижение трудоемкости процесса изготовления деталей, потерю некоторых характеристик или увеличение массы деталей. Проблемы прочности (или специфические проблемы прочности) играют решающую роль в специальной области техники, выбор материалов и последующая технология термообработки должны рассматриваться с условием достижения только максимальной работоспособности. 1. лучше решать задачи, описанные в книге, чтобы получить навыки в подборе материалов. Ю. А. Геллер, А. Г. Рахштадт. Материаловедение, 4-е издание М., «металлургия». 1975.446 сек 274 собственности. Однако в связи с долговечностью самой машины не следует стремиться к чрезмерно высокой долговечности деталей. При определении выбора стали для получения необходимых механических и других свойств также важно установить вид оптимальной закалки или химико-термической обработки.
- При выборе упрочняющей обработки, особенно в условиях массового производства, необходимо отдавать предпочтение наиболее экономичным и производительным технологическим процессам. Поверхностный твердеть поверхностным или глубоким топлением индукции, газ-цементацией, мягким азотированием, etc. Для выполнения процесса закалки для каждой детали создается технологическая схема, показывающая марки стали, режим термообработки, используемое оборудование, приборы, контроль качества и т. д. Обычно рассматривается возможность использования нескольких марок стали и методов упрочнения. Это позволяет выбрать наиболее рациональный вариант.
Это обеспечивает высокие эксплуатационные характеристики детали, а также хорошую обрабатываемость при выполнении механических и термических обработок. Первым параметром, определяющим выбор стали, являются ее механические свойства и распределение в cross-section. As как упоминалось ранее, если поперечное сечение изделия соответствует критическому диаметру конкретной стали (95% мартенсита), то достигается оптимальное сочетание прочности и пластичности после улучшения (см. стр. 203). Механические свойства стали в основном определяются содержанием углерода. Это зависит от прокаливаемости стали.
Прокаливаемость определяется наличием легирующих элементов. Людмила Фирмаль
В условиях полного упрочнения механические свойства практически никогда не зависят от характера и степени легирования. Исключение составляют никель и молибден, которые повышают их стойкость к хрупкому разрушению. Однако высокое содержание хрома, марганца и кремния, необходимое для этого, увеличивает склонность к хрупкому разрушению, не следует стремиться к использованию сталей с чрезмерно высокой отверждаемостью. Сталь сплава глубок-мяса затвердетая использована для больших частей с толщиными или большими диаметрами. Если изделие действует на изгиб (скручивание), то напряжение распределяется неравномерно по всему поперечному сечению.
Они самые большие на поверхности и равны нулю в середине или середине. Этот тип продукта не требует сквозной прокаливаемости. Для обеспечения прочности важных деталей, которые в основном используются для изгиба и скручивания в процессе эксплуатации, упрочненный слой с 95% мартенситной структурой должен располагаться на глубине не менее 1/2 радиуса от поверхности. Для деталей, работающих под напряжением (шатуны, торсионные валы, критические болты и др.) а для пружин и пружин необходимо обеспечить полное упрочнение по всему поперечному сечению (95% мартенсита в центре заготовки). Для наиболее важных деталей станка, изготовленных из улучшенной стали, твердость после закалки на расстоянии радиуса 1/2 от поверхности составляет 275 должно быть не менее HRC 45.
Для растяжимых продуктов, оптимальная твердость должна быть ядром. Сложные по конфигурации детали для уменьшения деформации в процессе упрочнения также должны быть изготовлены из легированной стали, закаленной в масле или на воздухе. При выборе стали следует учитывать, что легирующие элементы повышают устойчивость аустенита к отпуску. Поэтому, чтобы получить необходимую прочность и твердость, легированная сталь закаляется при высокой температуре, когда она улучшается. Эго может не только более полно исключить твердея усилие, но также получить самые лучшие прочность сочетание из и твердость стали.
Изделия, требующие высоких значений ay, ap и низкого порога хрупкости при низких температурах (работающие при низких температурах с высокими скоростями приложения нагрузки и имеющие концентратор напряжений), должны использовать тонкодисперсную мягкую сталь (предпочтительно сплав с никелем и молибденом). Содержание легирующих элементов в стали, предназначенной для производства деталей, упрочненных и улучшенных науглероживанием(карбюризацией), не должно быть слишком высоким, но должно обеспечивать необходимую закаливаемость поверхностного слоя и сердцевины и ингибировать рост зерен аустенита при нагреве.
Легирование должно обеспечивать возможность применения наиболее экономичного и технически выгодного способа термической обработки-прямой закалки из печи цементации (мягкого азотирования). Детали, подвергающиеся науглероживанию и мягкому азотированию, должны выдерживать износ при различных удельных давлениях, выдерживать высокую прочность на изгиб и кручение, высокую усталостную прочность и высокие контактные напряжения, а также выдерживать отверждение и забивание в условиях сухого трения. Производительность цементных деталей в процессе эксплуатации зависит от характеристик поверхности и сердцевины. Поскольку слой менее пластичен, чем сердцевина, то при высоких статических (изгибных и крутильных) нагрузках пластическая деформация обычно происходит в упрочненном слое-в сердцевине, что приводит к повышенной деформации слоя.
Когда предел текучести и ограниченный запас прочности сердцевины превышает пластичность слоя, образуются трещины. Таким образом, статическая прочность на изгиб и кручение при прочих равных условиях зависит от предела текучести сердцевины и запаса пластичности цементного слоя. При циклических нагрузках сопротивление разрушению цемента и цементных деталей зависит от прочности сердцевины. Увеличение прочности сердечника увеличивает прочность контакта. Например, при твердости выше HRC 35 допустимое контактное напряжение в основании 107 циклов составляет 190 кг / мм2, а при твердости HRC 25-35 оно не превышает 175 кг / мм2, поэтому прокаливаемость становится 1 из наиболее важных значений при выборе стали.
Однако сближение прочностных характеристик слоя и сердцевины снижает уровень остаточных сжимающих напряжений на поверхности и увеличивает объем фазового и структурного превращения при термообработке, что приводит к увеличению деформации и деформации детали после закалки. Оба фактора приводят к снижению предела выносливости детали, особенно при повышении точности зубчатого зацепления, деформации сложных зубчатых колес, шлицевой арматуры и др., ухудшается. Упрочнение цементного (цементно-цементного) слоя также очень важно. После химической термической обработки и отверждения, слой должен быть поцарапан Продукты перлита не присутствуют в средних метаморфах напряженного аустенита и переохлаждены austenite. In другими словами, сталь не должна быть подвержена внутреннему окислению, образованию избыточных карбидов (карбонитридов) при насыщении и другим дефектам, возникающим при химико-термической обработке.
Образование слоя немартовых продуктов трансформации резко снижает пределы выносливости. Рассмотрим выбор материала и упрочняющую термообработку для общих деталей машин. Вал. В зависимости от назначения и условий эксплуатации сопротивление рабочего вала определяется усталостной прочностью, контактной прочностью и износостойкостью при кручении и изгибе. Несущие, медленно вращающиеся валы изготавливаются из стали 35, 40, 45 и стали СТЗ, СТ4 и Ст5 и не подвергаются термической обработке. Небольшие размеры валов, таких как станков, следует оборудовать высокую изгибную и крутильную прочность и усталостная прочность, сталь 40Х (вал диаметром d = 20-25 мм), 50х (Дж = 35 ч-40 мм), 40х (Д = 50 −55 мм) и низкий отпуск (45С ~ 50—50С) и получения скорости вращения (180–220 С, СПЧ-35мм). средняя темперируя частота (410 до 430°с) будет более низка если температура низка.
Если производительность определяется прочностью на изгиб и кручение, а не контактной прочностью и износостойкостью, то среднеобъемный вал диаметром до 80-100 мм рекомендуется изготавливать из стали с пределом прочности на растяжение 80-100 кг / / 45, 40х и 50х после доработки (НВ-217-285). Хром-никель и хром-молибден сталь высокой твердости сделанная высокого номинального напряжения (50 кг / мм2 или больше) большого диаметра (100-130 мм или больше) Высокий вал нагрузки после гасить и высокотемпературный закалять (улучшенный), 50ХН, 40хнма, 34ксх3ма,<100. кг / мм2. Для валов с Турбокомпрессорными конструкциями, которые требуют большей прочности в больших сечениях, 30ХН2ВФА, 36ХН1МФА, 38ХНЗМФА, ЗОХ2НВФА и др. не использовать. Производительность контакта определяется прочностью и износостойкостью валы (гладкие, ступенчатые, шлицевые) должны иметь высокую поверхностную твердость не менее HRC 48-50.
In станки, для обеспечения этой твердости, валы малого размера изготовлены из стали 45 и 50 и усилены поверхностным упрочняющим индукционным нагревом (таблица 12). Если большие требования предъявляются также к валам малых габаритов из-за усталостной прочности при изгибе и кручении, то улучшение проводят перед поверхностным упрочнением. С этим. 277т о-о 0 0 Сталь рекомендуется для производства валов и типичного режима окончательной термообработки Таблица 12 Тип термическая обработка стали вала Твердость Толщина упрочненного слоя, мм Ядро, НВ HRC поверхность Гладкие ступенчатые валы в станках (не менее 140-150 мм в диаметре) 45 (50)высокотемпературный закалять 55ОСС, поверхностный твердеть топлением индукции, закаляя 170-180°С Никаких правил 50-56. (54-60) 1.3-2.0 Вал ровн, шагнут и сплайн-подверган механической обработке для критической цели механического инструмента 20 раз.、
18ХГТ、 12HNZA Цементация 930 ° С, нормализованное 880 ′ С (при необходимости), закалка, низкий отпуск 170-200С 186. 207-302 217-302 56-62 56-62 56-62 0.7-1.0 1.3-г, 6 1.3-1.6 Вал шестерни автомобиля 25HGM азотирования, цементации 850°С закалка с горячим маслом, низкий уровень закаляя 180сС 30-35 56-65 0.8-1.1 Цемент 15ХГН2ТА, масл-погашенный, низк-закаленный 25-35 58-64 1.3-1.8 Коленчатые валы для судовых и автомобильных двигателей 40, 45.、 40х. 50г. 40ХН.、 40XFA. Закалять или гасить высокотемпературный закалять, поверхностный гасить, собственн-закалять 150-170’c повсеместно в топление индукции журнала основы и ведущего шатуна 163-269 52-62-4 −5 45X гася 840QC, закаляя 580-600°C, жидкостное азотирование 570 ° С NU 250-350 HV 550-700 0,3-0,4 (толщина 10-15 мкм, карбопитридный слой) Дизельный коленчатый вал 18X2H4VA закалять 910gC(воздух), отпуск 2003С 311-375—закалка, отпуск 550°с, азотирование 550°С, 40 часов 250-300 ну 600-700 0.3-0.4 40кхнма закаляя 880 ° С (масло), закаляя 590 ° С311-375—в таком же случае, большой вал сделан из легированной стали 40Х, 40ХГТ, ЕТК., что улучшает прокаливаемость.
Например, для высокоскоростного вала станка диаметром 25-30, 60-80, 80-100 мм, когда требуется более высокая износостойкость и соответствующая высокая твердость (не менее HRC 56-58), они изготавливаются из стали 20х, 18ХГТ и 12хнза соответственно. Цементацию проводили(таблица 12). В автомобильной промышленности стали 25хгм (ЗИЛ-130), 15ХГНТА (МАЗ), 35х и 40х (газ) применяются для изготовления ведущих и ведомых валов автомобильных редукторов различной конструкции и грузоподъемности. Валы изготовлены из стали 25хгт усилены с мягкого азотирования(НRС 60-65)и валы изготовлены из 15khgnt стали, армированного цемента(ПЦ 58-64) и 35х являются cyanated(НRC 48-53).Эти компоненты после представленной формулы химико-термической обработки являются высокими Сопротивление ссадины и высокая прочность на изгиб.
При производстве цементных валов большого диаметра (-100 мм), где требуется высокая прочность сердцевины, для достижения высокой прокаливаемости используются сложные легированные стали типа 35×2гнта. Если требуется особенно высокая износостойкость, вал изготавливают из стали 38Х2МЮА и затем азотируют. Коленчатый вал. «Коленчатый вал двигателя воспринимает высокую нагрузку от инерционной силы поступательного и вращательного движения массы.」 Эти инерционные силы не только вызывают трение и износ на шейке вала, но и вызывают явление усталости в точке выхода масляного канала вдоль скругления. Они обычно изготавливаются из стали, а в некоторых случаях даже из чугуна. Коленчатые валы низкоскоростных судовых и тракторных двигателей изготавливаются из стали 40, 45, 40х, 40г(таблица 12).
Для изготовления валов для высокоскоростных двигателей используются легированные стали 40х, 40ХЧ. Ковка коленчатого вала для получения необходимых механических свойств, подготовка конструкции к окончательному поверхностному упрочнению, а также нормализация (при необходимости отпуск) или улучшение осуществляется для обеспечения хорошего machining. To увеличьте износостойкость шейки коленчатого вала, она гасится индукционным нагревом и самозатуханием. 1 для повышения усталостной прочности скругления коленчатого вала могут быть упрочнены прокаткой роликом или дробеструйной обработкой в редких случаях. Коленчатые валы, поглощающие высокие нагрузки, изготовлены из легированной стали 40хнма и 18Х2Н4ВА (см. таблицу 12).Прочность коленчатого вала из легированной стали может быть усилена азотированием жидкости или газа(см. таблицу 12).Усталостная прочность коленчатого вала в результате жидкого азотирования повышается на 60-80%.
Для изготовления коленчатых валов сложной геометрии с большими фланцами и отверстиями наряду со Сталью используется высокопрочный магниевый чугун(см. стр. 153).Снижение прочности чугунных валов зависит от более конструктивной формы, меньшей чувствительности чугуна к концентраторам напряжений, многопозиционного вала и меньшего смещения подшипника (в основном за счет меньшего смещения подшипника). 272) и за счет снижения риска возникновения резонансных колебаний за счет увеличения демпфирующей способности.
Например, коленчатый вал легковых автомобилей М-24 (Волга) представляет собой высокопрочный магниевый чугун ВЧ 60-2(3,2-3,4% C, 2,0-2,5% Si,1,15-1,3%,<0,003% S, 0,15-0,25% Cr и 0,02-0,04% mg). Они отлиты в форме раковины. Вал подвергают термообработке по следующим режимам: нагрев до 950°С в течение 8 часов, охлаждение до 600°с, нагрев до 725°с, выдержка в течение 8 часов при этой температуре и в результате термообработки воздушного охлаждения перлит сфероидизируется и таким образом достигается значительное повышение механических свойств (stv = 50-g — 702, 5-HB-8F = 207-241). Коленчатый вал машины Запорожец отлит в оболочковую форму из высокопрочного чугуна ВЧ 50-2.Отливки подвергают холодному отжигу при температуре 640-660°С в течение 3-4 часов, а затем охлаждают на воздухе. Коленчатый вал двигателя ВАЗ из ковкого чугуна нагревается и отпускается при температуре 180-200°в течение 2 часов для обеспечения надлежащего отпуска шатуна и направляющего вала. мм, ХРК больше чем 50.
Высокопрочный магниевый чугун также используется в производстве коленчатых валов тепловозов. Для повышения износостойкости и долговечности, коленчатый вал азотированный. Толщина слоя 0,7 мм, HRC 40.После азотирования вал шлифуется для исправления деформации, а затем шлифуются скругления. Шпиндель. Главным требованием к материалу шпинделя подшипника качения и скольжения является повышение твердости для получения высокой стойкости к истиранию, захвату, зазубринам, вмятинам и др. Сталь шпинделя подбирается с учетом прочности на упрочнение, в зависимости от поперечного сечения изделия.
Чем толще толщина стенки, тем выше легированная сталь для обеспечения необходимой прокаливаемости. Указанный тип шпинделя для нормальных и высокоточных станков упрочняется поверхностным упрочнением при нагреве током высокой частоты (табл. 13) или объемным упрочнением закалкой твердостью HRC 40-50.In использовались материалы, используемые для производства цементных шпинделей, стали 20х, 18ХГТ и 12ХНЗА. Использование легированной стали позволяет гасить масло (расплавленную соль), что снижает деформацию шпинделя. Тот же тип шпинделя с азотированием изготовлен из стали 40хфа и 18ХГТ. После азотирования, деформация шпинделя сводится к минимуму. Высокоточные шпиндели станков для подшипников скольжения часто изготавливаются из стали 38X2MIOA и азотируются (см. таблицу 13) 。
Для нормальных машин точности, шпиндель сделан из стали 50 или стали U8 и затвердет поверхностный твердеть топлением индукции(IIRC 58-62). Шестерни. Наиболее часто поломка зубчатых колес связана с контактно-усталостным разрушением, концевым износом, схватыванием стали и типичным окончательным режимом термообработки, рекомендуемым для производства механических шпинделей Таблица 13 Название запчасти Термическая обработка стальной ранга Толщина упрочненного слоя, мм Сердечник, поверхность HB, ИК 50 шпинделя для закаливания-58-62 поверхность 5-7 шпиндель для нормальной точности 18ХГТ Индукционный последовательный нагрев semension 930 ° С, отверждение 56-62 1,0-1,3 stan-40KhFA 840 подшипник качения и скольжения С«, отпуск 1 7 0 −210°焼 отпуск 890°C(или обычно-255-285 JIV 0, 25 Коф. 38X2MUA. (Дубление), 650°с, закалка, первичную обработку, 610°с закалки, 510 ° с азотирование закалка 940°с, отпуск 660 ° с, первичную обработку, 610nC закалять, 510°с азотирование, (I этап) и 540°с (II этап)) )
229-269. 610-700. По крайней мере HV 850 0,2 или больше Зубы, а также из-за повреждения зубов или усталости или кратковременной перегрузки. Окончательный тип термической обработки или химической термической обработки шестерен и зубчатых колес устанавливается в соответствии с их конструкцией и условиями эксплуатации. Силовые шестерни требуют высокой износостойкости на рабочей поверхности и достаточной статической, усталостной и изгибной прочности при контактных нагрузках. Обработка стальных и закаленных зубчатых колес должна обеспечивать высокую прочность на растяжение, усталостную прочность, включая контактную нагрузку, и достаточную вязкость. Эти требования наиболее полно удовлетворены легированного цемента или нитроцементованном стали.
После термообработки структура поверхностного слоя представляет собой закаленный мартенсит, а сердцевина представляет собой бейнитную или феррито-цементно-плотную смесь различной степени дисперсности. Низкоуглеродистый мартенсит. В случае средних нагрузок колеса, помимо химического термического упрочнения, при индукционном нагреве могут быть упрочнены (по контуру или через-дно полости между зубьями принудительно затвердевает). В этом случае шестерня изготавливается из стали 45, 50, 40х, 50х, 50Х11. Улучшенная сталь имеет применения в шестерне для средств кувшинов и rojags. Улучшения стали 40, 45, 50г, 40х, 30HGS и т. д., применяются для изготовления зубчатых колес в условиях единичного и мелкого производства, при этом окончательная резка зубьев осуществляется после доработки (Я. 280-320-малые колеса и НВ 200-240-большие колеса),
гарантируя высокую точность размеров. Улучшенные стальные шестерни зарабатывают достаточно. Колеса большого диаметра, сталь _35L-50L, 40HL、 281 others другие: Литейный круг нормализуется, и во многих случаях после этого выполняется высокотемпературный отпуск (в случае легированной стали). В качестве примера рассмотрим более подробно выбор стали и упрочняющую обработку цементных зубчатых колес для автомобилей, тракторов и станков. Предварительная термическая обработка автомобильных и тракторных зубчатых поковок часто приводит к изотермической обработке annealing. It обеспечивает хорошую обрабатываемость за счет резки и минимальную деформацию после окончательного химического нагрева treatment. In на зубьях автомобильных шестерен, работающих в различных условиях, действующие напряжения могут достигать высоких значений.
Например, в шестернях ЗИЛ-130 первой передачи и заднего хода напряжение изгиба достигает 63,5 кгс / мм2, а в шестернях 3-й передачи контактное напряжение очень велико, достигая примерно 130 кгс / мм2. Наиболее распространенной причиной отказа трансмиссии автомобиля является повреждение поверхности из-за контактной усталости. В редукторе, где происходит периодическое переключение передач, наблюдается Концевой износ, усталостное разрушение зубьев опасного сечения. Иногда их разрушение происходит даже от одной нагрузки(перегрузки). Привод автомобильных цилиндрических шестерен в основном выходит из строя из-за (70%) усталостного разрушения, а конические шестерни приводятся в движение из-за повышенного износа.
Автомобильные зубчатые колеса изготавливаются из легированной стали, которая закаляется маслом, чтобы обеспечить необходимую закаливаемость сердцевины зуба и минимальную деформацию при закалке. Основные моторизованные цилиндрические шестерни и конические шестерни для грузовых автомобилей ЗИЛ и главных передач изготовлены из экономически легированной стали 18ХГТ, 25хгт, 30хгт, автомобили ВАЗ изготовлены из стали 20ХГНМ и 19ХГН, а автомобили ГАЗ изготовлены из стали 20ХГН и 20нм (таблица 14). В последнее время сталь 25ХГНМАЙ применяется при изготовлении шестерен на заднем мосту автомобиля. Стойкость этой шестерни сделанной сталью 30% более высоко чем стойкость серийных шестерен сделанных стали 20KhGNM. Это объясняется очень тонкой гранулярностью ядра (оценка 12) и слоя (оценка 13-14).
Зубчатое колесо к Колеса указанных типов автомобилей ЗИЛ и газ цементируются или мягко нитруются для упрочнения (см. таблицу 14).Сталь должна быть генетически тонкой. Это позволяет затвердеть шестерни после затравки сразу от печей цементации и нитроцеллюлозы. Использование данной технологии упрочнения снижает деформацию. Это важно именно для зубчатых колес автомобиля, так как зубчатые колеса автомобиля не подвергаются шлифовке зубчатых колес. 1 в автомобильной промышленности наиболее тяжелые редукторы изготавливаются из стали 12хнза (автомобили МАЗ), 15хгн2та и 15×2гнтра(ЯМЗ), либо из стали 20ХГН2ТА и 15ХГН2ТА(КрАЗ). Для нагруженных зубчатых колес, в большинстве случаев, толщина упрочненного (цементного) слоя равна 0,15 в общей толщине (282 табл.14) типичной конечной термической обработки и режим химико-термической обработки 1, рекомендуемый для производства зубчатых колес. ———- ——————— Название детали ) Твердость термической обработки ранга стали, HRC затвердетая толщина слоя, mm Сердечник Поверхность Передач:
Коробка передач 40х Нитроцементация 83°с, НВ 48-53 0. 15 пассажирское автоматическое пожаротушение G-241 0.2 t бит коробка передач 25HGT, (масло), temp 200’c Нитроцемент 850’c, 35-45 52-62 0, 5 задний мост в грузовике 25HGM. 20HGNM、 Сразу шаг леча(горячее масло 180 ° С), закаляя цемент газа 180 ° С, не-26-40 58-64 0.7. 1, 0.- Вызовите автопарк ЗОХГТ. 12HNZA Средний закалки в масле, 850 °, охлаждение С, 200°С закалка 900С затвердевания цемента, 26-40 58 гасить 1,5. 0, 8.- Он зеленый. 18X2H4VA 800℃(масло), отпуск 170℃цементация 900°C, отпуск 35-43 56-59 1.1 0, 6.- 12хнза с большим стрессом 65°с (двойной), закалка 830°С(воздух), отпуск 180 «С впрыском газа 930» С, 30-40 56-60 0.9. 0,25 Т Колесо цилиндра машины V высокое airyazzhsnds 20KHNM Отпуск 650°C, отпуск 800 ° С (масло), отпуск 180 ″ injection впрыска газа 930°С, 30 30-40 56-60 0, 2 цилиндра и скосы машины 25×2гнта Закалять 620 ° С, леча 830 ′ С, закаляя цемент газа 190°С 930°С, 30-40 56-60 0.26 Т 0, 2.-
18ХГТ Закалять 660С, закаляя 810 «С, закаляя 180°С; газ-цемент 930» С, 30 56-60 0.26 ш 0.2- Среднего напряжения 40х Прямое охлаждение масла после охлаждения до 83°с, закалки 190°С, закалка 840°с, закалка 25-28 48 52 0.25 Т 0.2 5Т Переключаемые колеса для станков Низкий стресс, 50КСН Отверждается по контуру зуба при 550°C, индукционно < нагревается в воде, закаляется до 210°C От 830°С (масло), погашенный-48-54 48-54 Усилие колеса машины во время 40khfa начинает 180-220°Hardening твердеть 890 ° с; выйдите колесо механического инструмента HB HV 0.12 t Switchable 650 основной подвергать механической обработке, закаленное 570°С, азотированное 510°窒化 248277 610- 700. Начальный окружной зуб io или 0,18-0,27 т (и колесный модуль), а глубина Нитроуглеродного слоя составляет 0,19-0,2 t. To обеспечьте высокую прочность контакта и износостойкость, твердость поверхности должна быть меньше HRC 59.Твердость эквивалентна высокоуглеродистому мартенситу (0,8-
1,15% C). за счет снижения допустимого контактного напряжения на 15% твердость поверхности может быть снижена с HRC 60 до IIRC 54.Твердость поверхности зуба для предотвращения хрупкого разрушения не должна превышать HRC 63 и core HRC 30-42.Например, предел прочности при растяжении и изгибе и контактная долговечность зубчатого колеса повышаются с увеличением твердости сердечника за счет увеличения содержания углерода в стали. При снижении содержания углерода ’283 (менее 0,15% С) в стали снижается предел текучести сердечника, в результате чего происходит пластическая деформация, которая может привести к разрушению упрочненного слоя. Если твердость сердечника
чрезмерно повышена(HRC превышает 42-45), то прочность зубьев шестерни при изгибе снижается, что повышает риск хрупкого разрушения. Некоторые шестерни на задней оси (например, коническая передача и ведущая шестерня на коробке передач задней оси) изготовлены из стали 55PP(см. стр. 226) и закалены поверхностным упрочнением при глубоком нагреве (автомобиль ГАЗ, ЗИЛ). в зависимости от модуля колеса Т, для Т = 3.54-5, рекомендуется использовать расплавленную сталь 55ПП с критическим диаметром прокаливаемости равным 6.5-9.0 мм(полумартенситная структура сердечника заготовки). При t = 4,54-7, 9-13 мм, а при t 6,5-более 13 мм. После твердеть, твердость поверхности зуба HRC 58 62, и твердость сердечника HRC 30 40.Толщина упрочненного слоя составляет 1,0-2,0 мм. Сталь 55ПГ1 после поверхностного упрочнения обладает
высокой прочностью и достаточной ударной вязкостью, в том числе усталостной, поэтому ее можно рекомендовать для колес с контактным напряжением не слишком высоким м = 4,0-6 мм. Применение стали 55ПГ1 имеет значительный экономический эффект за счет перехода от длительного процесса химико-термической обработки к индукционному упрочнению при обмене сплавов. Сталь. Методы упрочнения стали и зубчатых колес, применяемых в тракторах и сельскохозяйственном машиностроении, можно классифицировать по степени нагруженности этих деталей. 1. Т-40, ДТ-54а, Т-74, ТМЗ-50, МТЗ-80 малой и средней грузоподъемности (редуктор, шестерня и ведомая шестерня, конечная передача и др.) прием.) производятся в нелегированных 18gt плита для, 25gt,
и низкий-никелевой стали 20khtr, 20хгнр, 1, 2khn1, 1, 2, и т. д. цементируется в ММ или науглероживается на глубину 0,8-1,2 мм. Твердость поверхности HRC 56-65.Твердость сердечника зубов HRC 25-40.Если эти шестерни не имеют высоких износостойких требований, то их изготавливают из стали 40, 45, 40х, 40ХС и закаляют при высокотемпературном отпуске и последующих поверхностях. Индукционный нагрев до глубины 1,5〜2,5 мм и закалка при HRC 54.20 X сталь можно использовать для последующей цементации, закалки и отпуска. 2.Сверхмощные колеса шестерни сделаны
из низкой стали 20khgnr цемента никеля (nitrocarburizing), 20KhNR, и никеля Крома 20KhNZA. In кроме того, критерии толщины упрочненного слоя и его твердости остаются такими же, как и в 1-й группе. Однако твердость сердечника несколько выше, HRC 30-45. Большинство тракторных передач, таких как Т-74, Т-180, Т-100М, Т-130 изготовлены из этих сталей. В станкостроении выбор стали и упрочняющая обработка зубчатых колес также осуществляется на основе их нагрузок. Этот стандарт в станкостроении определяется расчетным номинальным напряжением изгиба (cr») в корне зуба. 1.Легкие и средние нагрузки шестерни (НТИ <15 кг / мм2 и 284sui> 10-25 кгс / мм2) изготавливается из стали 20х и 18ХГТ и цементируется цементом. Контурное поверхностное упрочне
ние также используется при индукционном нагреве для упрочнения зубчатых колес средней нагрузки, которые часто не включаются на ходу. Этот метод упрочнения часто используется для малых и средних зубчатых колес, которые работают на закаленных колесах из-за их хорошей взаимной совместимости. Обычно колеса для поверхностного упрочнения изготавливают из стали 40х и затвердевают на глубину 0,2-0,25 тонны, но не превышают 1,4-1,8 мм. Упрочнение обода зубчатого колеса (d 300 мм и m = 1,0-3,0)осуществляется через канавки на глубину всего 1,5-3,0 мм. Для обеспечения высокой износостойкости и прочности, твердость поверхности должна быть на уровне HRC 48-52.In в этом случае упрочнение должно быть контурным, не прерывая этого
упрочненного слоя. 2.Высоконагруженное цилиндрическое и коническое колесо (ОИ = 204-35 кгс / мм2) свыше 300мм (Т = 1,5 4-4, 0) изготовлено из легированных цементных сталей 20х и 18ХГТ, с колесами диаметром до 600 мм (Т = 4 -: 10)из хромоникелево-молибденовой глубоко упрочненной стали 20ХНМ. Эти колеса армированы цементом. При использовании процесса нитроцементации, для производства колес диаметром до 600 мм, твердость сердечника выше, чем у Стали 18ХГТ (таблица 14) и стали 25хгт с достаточной насосной мощностью. 3.Особенно высокие нагрузки (sti = 30 4-45 кгс / мм2) цилиндрические колеса (rf> 600 мм и t = 1,5 4-6), с большими динамическими и импульсными нагрузками, изготовлены из стали 12хнза, конические (t = 6 4-10) из стали
25Х2ГНТА. Долговечность и безотказность работы этих колес достигается путем цементирования или размягчения зубьев по контуру (см. таблицу 14). Цементация(нитроцеллюлозирование) с последующей термообработкой (упрочнение и отпуск) повышает твердость и несущую способность поверхностного слоя зуба, а также высокую прочность зуба на изгиб по сравнению с поверхностным упрочнением. После шлифовки или скашивания прочность цементных зубьев в изгибе увеличивается в 3 раза. Однако измельчение (в несколько этапов) может уменьшить этот эффект в 1,5-2 раза. Твердость винтовых и шевронных зубчатых колес должна быть самой высокой, что обеспечивает хорошую прочность контакта. Твердость шестерни шпоры должна быть выше чем колесо. Это
уменьшает вероятность выгорания и унифицирует долговечность шестерен и колес. Во всех случаях толщина цементного слоя устанавливается на уровне 0,2-0,26 т, но не более 1,8 мм, а Нитроцементного слоя-на уровне 0,15-0,2 т, но не более 1,0 мм. Твердость основания зуба после цементной фиксации (мягкого азотирования), где действует нормальное напряжение от внешней нагрузки и концентратора напряжений, должна быть на сердцевине HRC 30-40 и поверхности HRC 56-60. Для уменьшения деформации зубчатого колеса используют мелкозернистую сталь с регулируемой прокаливаемостью (Марка 5-8), затем проводят газоцементацию в атмосфере с регулируемым углеродным потенциалом и по возможности упрочнение с предварительной вулканизац
ией. Карбонитридная цементация менее деформируется, чем цементация при термической обработке. В дополнение к цементации и нитроцементации используются закаленные шестерни Азотирование. Тем не менее, он должен использоваться для передач, которые не могут быть включены на ходу. Азотирование (см. таблицу 14) применяется для легких и средних нагрузок колес сложной формы. Например, есть внутренние зубы, которые трудно поддаются grind. In в этом случае шестерня изготавливается из стали 40х (конической) или 40ХФА (цилиндрической). При азотировании на глубину 0,1-0,13 т (но не более 0,6 мм) деформация минимальна, и осуществляется только шлифовка или хонингование зубьев.
Азотирующее колесо с большим числом циклов нагружения не уступает цементному (нитроцеллюлозному) по контактной прочности(сопротивлению скалыванию), но величина контактной нагрузки должна быть небольшой, поскольку толщина слоя тонкая. С целью повышения усталостной прочности на изгиб и долговечности зубья высоконагруженного колеса после упрочнения после цементации(науглероживания) или при индукционном нагреве подвергают поверхностному упрочнению путем шарошечного упрочнения или прокатки роликом (последний составляет t> 4 и HRC 40). Нормированный отпуск или отпуск осуществляется перед механической обработкой, независимо
от принятого способа ковки (штамповки).Прецизионные колеса после механической обработки могут подвергаться воздействию высоких температур (600°C) для снижения напряжений. После окончательной обработки для уменьшения напряжения шлифования цементный круг закаляется при низкой температуре 160°C 2-2. 5 часов. Трубчатые детали(втулки, втулки и др.); Эти детали должны иметь высокую износостойкость, стабильность конфигурации и размер с течением времени. Часто они изготавливаются из стали 40хфа, Зохзва, 38Х2МЮА и обрабатываются азотированием. Азотирование обеспечивает высокую износостойкость и малую деформацию. Может использоваться для отверждения и цементирования. Если толщина
стенок составляет 14-18 мм, то используется сталь 20х, 40-45 мм-18ХГТ и 70-75 мм-12хнза. Детали этой группы могут деформироваться в процессе механической и термической обработки processing. To уменьшите деформацию после подвергать механической обработке, закаляя стабилизацию обычно выполнен. 。Нормализовать. Наиболее часто используются при изготовлении нормалей (болты, винты, гайки, шпильки и др.) улучшаются углеродистые и легированные стали. Как показали исследования, разрушение этих деталей в процессе эксплуатации происходит в следующих случаях: 1) хрупкое и вязкое разрушение соединения из-за недостаточного запаса прочности при использовании деталей без термообработки, или когда твердость деталей с термообработкой
недостаточна; 2)хрупкое разрушение из-за высокой твердости, наличия поверхностного упрочнения после холодной ковки, не снятого методом рекристаллизационного отжига, или наличия структурно свободной стали в исходной стальной структуре, например было показано, что наибольшее значение прочности на хрупкость соответствует твердости HRC 30-35. Высокие свободные от стресс болты, стержни, и другие крепежные детали можно сделать из стали на 40, 40С, и 30ХГС и нормализовать к твердости ХРК 25-30.Детали, подверженные высоким комплексным напряжениям, должны быть изготовлены из стали 40х, 40ХН или 40ХМА и подвергнуты улучшению или нормализации твердости HRC 30-35. Если деталь получена методом холодной штамповки, то для удаления затвердевания и растворения структурно свободного цементита необходимо выполнить нормализацию при температуре 880-900°С.
Смотрите также:
Решения задач по материаловедению
Рессорно — пружинные стали общего и специального назначения | Конструкционные (машиностроительные) улучшаемые легированные стали |
Шарикоподшипниковые стали | Мартенситностареющие высокопрочные стали |