Оглавление:
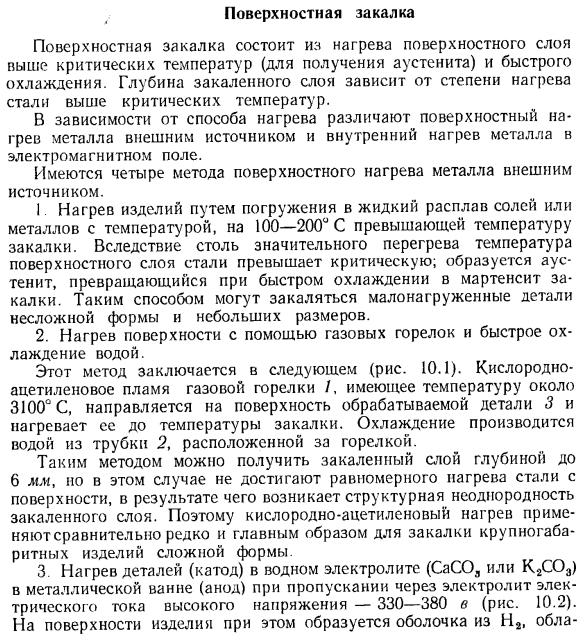
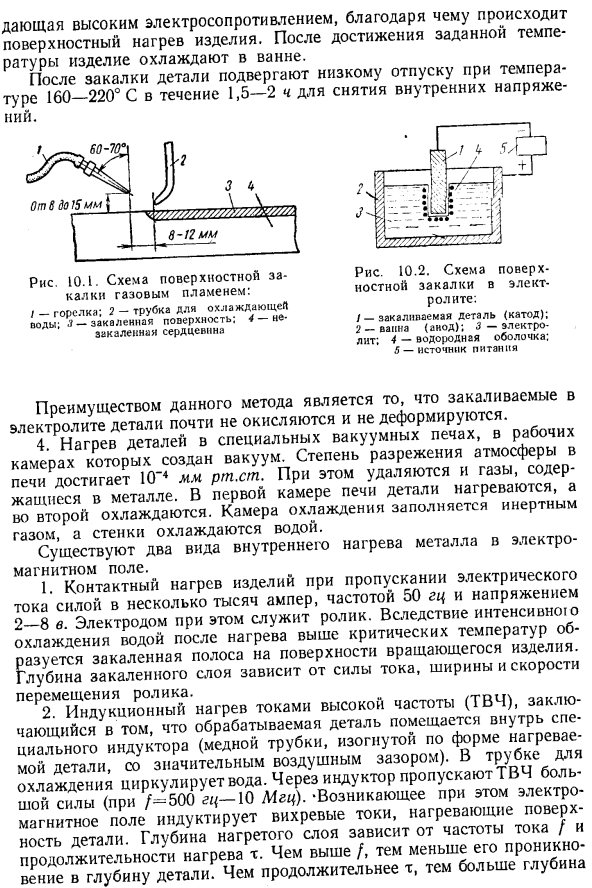
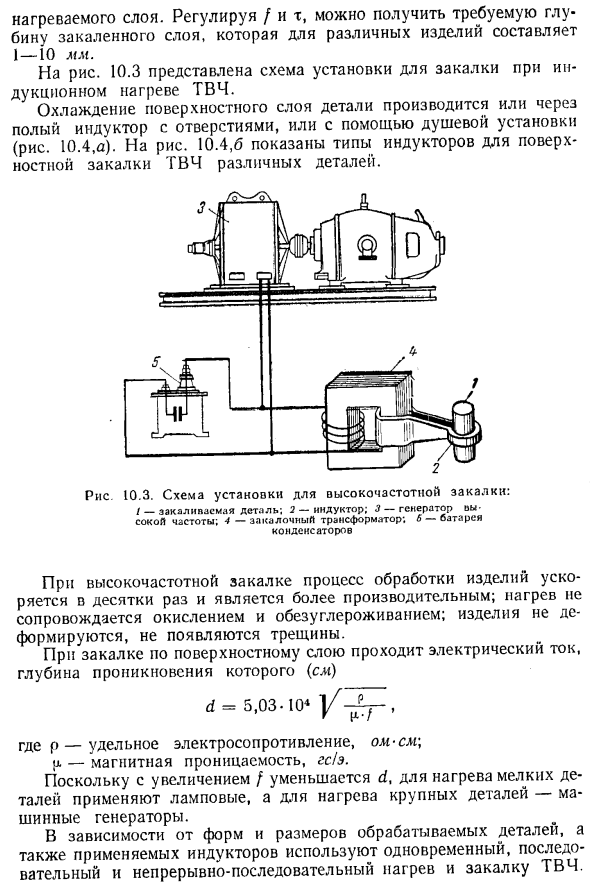
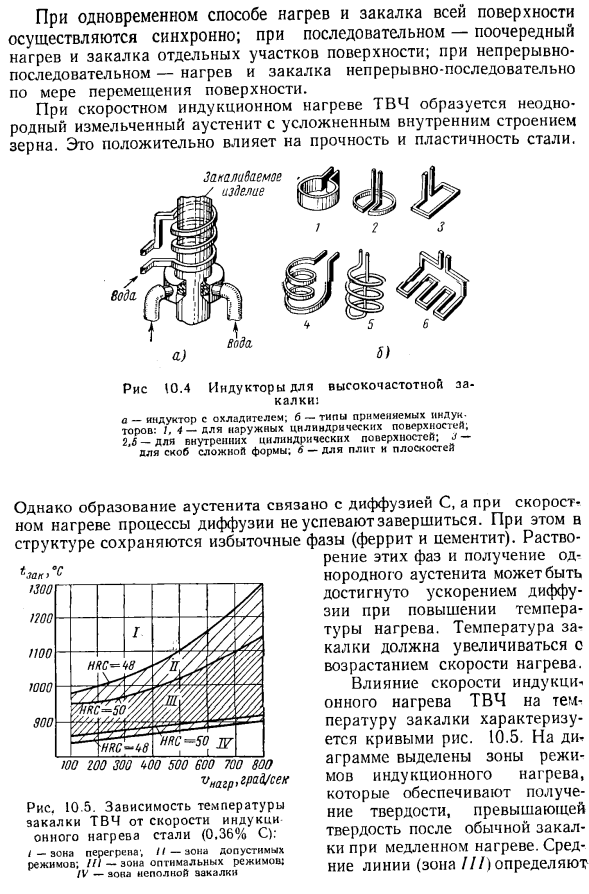
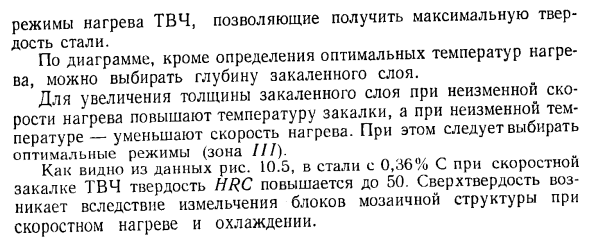

Поверхностная закалка
- Поверхностное упрочнение Поверхностное упрочнение заключается в нагреве и закалке поверхностного слоя выше критической температуры (для получения аустенита).Глубина упрочненного слоя зависит от степени нагрева стали выше критической температуры. В зависимости от способа нагрева, поверхностный нагрев металла различают внешним источником и внутренним нагревом металла в электромагнитном поле. Существует 4 способа поверхностного нагрева металла с помощью внешнего источника. 1.Нагревают изделие, погружая его в жидкий расплав соли или металла при температуре от 100 до 200 ° С выше температуры закалки.
Из-за такого значительного перегрева, температура поверхностного слоя стали превышает критическую температуру. Когда аустенит образуется и быстро охлаждается, он превращается в закаленный martensite. In таким образом, легкие детали простых форм и небольших размеров могут быть закалены. 2.Нагрейте поверхность газовой горелкой и погасите ее водой.
Этот метод заключается в следующем (рис. 10.1). Людмила Фирмаль
Кислородно-ацетиленовое пламя газовой горелки, имеющее температуру около 3100°с, направляется на поверхность заготовки 3 и нагревает КК до температуры закалки. Охлаждение осуществляется водой из трубки 2,которая расположена за горелкой. Используя этот способ, можно получить упрочненный слой с глубиной до 6 лучей, но в этом случае не будет достигнут равномерный нагрев стали с поверхности, в результате чего возникнет структурная неравномерность упрочненного слоя.
Поэтому кислородно-ацетиленовый нагрев применяют сравнительно редко, в основном для отверждения крупногабаритных изделий сложной формы. 3.By пропуская в электролит ток высокого напряжения, нагревают детали (катод) водного электролита (CaCOa или K2CO3) в металлической ванне (аноде)-330-380 В (рис.10.2). при этом на поверхности изделия образуется высокое электрическое сопротивление H2 оболочки, что вызывает нагрев поверхности изделия.
- После достижения заданной температуры изделие охлаждают в ванне. После отверждения детали закаляются при температуре 160-220°С при низкой температуре в течение 1,5-2 часов для снятия внутреннего напряжения. Рисунок 10.1.Схема газопламенного поверхностного упрочнения: I-горелка;2-трубка для охлаждения печей. 。 ’/- Затвердетая поверхность: 4-не-затвердетый сердечник Рисунок 10.2.Схема поверхностного упрочнения электролитов: / — Отвержденная часть (катод); 2-ванна (анод); 3-электролит; 4-водородная оболочка; 5-Источник питания
Преимуществом данного способа является то, что деталь, затвердевшая в электролите, практически не окисляется и не деформируется. 4.Вакуум создается нагревом деталей в специальной вакуумной печи в рабочей камере. . In первая камера печи, 2-я часть нагревается и охлаждается.
Разрежения атмосферы в печи достигает 10 −4 мм рт. Газ, содержащийся в металле, также removed Людмила Фирмаль
Камера охлаждения заполняется инертным газом, а стенки охлаждаются водой. Существует 2 вида внутреннего нагрева металла в электромагнитном поле. 1.Контактный нагрев изделия путем приложения силы в несколько тысяч ампер, частотой 50 Гц, электрическим током с напряжением 2-8 V. In в этом случае ролик будет выступать в качестве электрода. Сильное охлаждение водой после нагрева выше критической температуры приводит к образованию затвердевших полос на поверхности вращающегося изделия.
Глубина затвердевшего слоя зависит от силы тока, ширины и скорости ролика. 2.Индукционный нагрев током высокой частоты (ТВЧ).он заключается в том, что заготовки помещают в специальный индуктор (медную трубку с большим воздушным зазором, изогнутую по форме нагревательного участка).Вода циркулирует в трубе охлаждения. Высокая мощность HDTV проходит через индуктор (/ −500 Гц-10 МГц). Полученное электромагнитное поле индуцирует вихревой ток, который нагревает поверхность детали. Глубина нагревательного слоя зависит от частоты тока/и времени нагрева м. Чем выше / находится, тем меньше проникновение в глубину детали. чем больше Т, тем больше глубина Нагревательный слой.
Регулируя /и М, можно получить необходимую глубину затвердевшего слоя. Это от 1 до 10 Ярсов в различных продуктах. На рисунке 10.3 показана иллюстрация упрочняющего устройства для индукционного нагрева на телевизоре высокой четкости. Поверхностный слой детали охлаждают через выдолбленный полый индуктор или с помощью душевого блока (рис.10.4, а).На рис. 10.4 и 6 показаны типы индукторов для поверхностного упрочнения ТВЧ в различных компонентах. Рисунок 10.3.Схема установки индукционного упрочнения:/ — закалка деталей. 2-индуктор; 3-высокочастотный генератор; 4-гасящий трансформатор; 6-конденсаторная батарея При высокочастотной закалке процесс обработки продукта ускоряется в десятки раз, что повышает производительность.
Нагрев не сопровождается окислением и обезуглероживанием. Изделие не деформируется и не трескается. Во время тушения ток проходит через поверхностный слой, а глубина его проникновения (см) д = 5.03-10 * Где Р-удельное электрическое сопротивление, Ом-см \ И-проницаемость, ГФ / е. поскольку d уменьшается с увеличением f, используйте трубчатый генератор для нагрева мелких деталей и машинный генератор для нагрева крупных деталей. В зависимости от формы и размера обрабатываемой детали и используемого индуктора используются одновременный, непрерывный, непрерывный нагрев и упрочнение ТВЧ.
В одновременном режиме нагрев и упрочнение всей поверхности осуществляется одновременно. Последовательный-чередующийся нагрев и упрочнение отдельных участков поверхности. Если непрерывный непрерывный-по мере движения поверхности, непрерывно нагревается и затвердевает. Высокоскоростной индукционный нагрев высокочастотных частиц приводит к образованию неоднородного трещиноватого аустенита со сложной внутренней структурой частиц.
Это положительно сказывается на прочности и пластичности стали. Рисунок 10.4 индуктор для индукционного упрочнения. а-индуктор с охладителем; б — тип применяемого индуктора: 1,4 — для цилиндрических наружных поверхностей. 2.5 — для внутренних цилиндрических поверхностей; J-скобы сложной формы. 5 — для пластин и плоскостей Однако образование аустенита связано с диффузией С. Быстрый нагрев не успевает завершить диффузию process. In в этом случае избыток фазы (феррит и цементит) сохраняется в структуре.
Решение Чтобы получить рений и однородный аустенит в этих фазах, увеличивают температуру нагрева для ускорения диффузии. Если скорость нагрева увеличивается, температура закалки должна увеличиться. Рисунок 10 5. Зависимость температуры закалки ТВЧ и скорости индукционного нагрева стали (0,36%C): / — Зона перегрева; / / — зона допустимого режима. /// — Зона оптимального режима. / V-зона неполного упрочнения Влияние скорости индукционного нагрева ТВЧ на температуру закалки характеризуется кривой на рисунке 5. 10.5.
На этой схеме показаны зоны системы индукционного нагрева. С методом топления индукции, твердость можно получить больше чем твердость после нормальный гасить во время низкоскоростного топления. Центральная линия (зона///) определяет режим высокочастотного нагрева, который позволяет получить максимальную твердость стали. Согласно рисунку, помимо определения оптимальной температуры нагрева, можно выбрать глубину упрочненного слоя.
Для увеличения толщины упрочняющего слоя при постоянной скорости нагрева увеличивают температуру отверждения и уменьшают скорость нагрева при постоянной temperature. In в этом случае нужно выбрать оптимальный режим (зона///). Как видно из данных на рисунке 10.5 с составляет 0,36% стали при высокоскоростном отверждении ТВЧ, твердость HRC увеличивается до 50.Сверхтвердость возникает за счет шлифования мозаичных структурных блоков при высокоскоростном нагреве и охлаждении.
Смотрите также:
Решения задач по материаловедению
Общая характеристика процессов химико термической обработки стали | Дефекты, возникающие при закалке |
Цементация | Основное оборудование для термической обработки |