Оглавление:
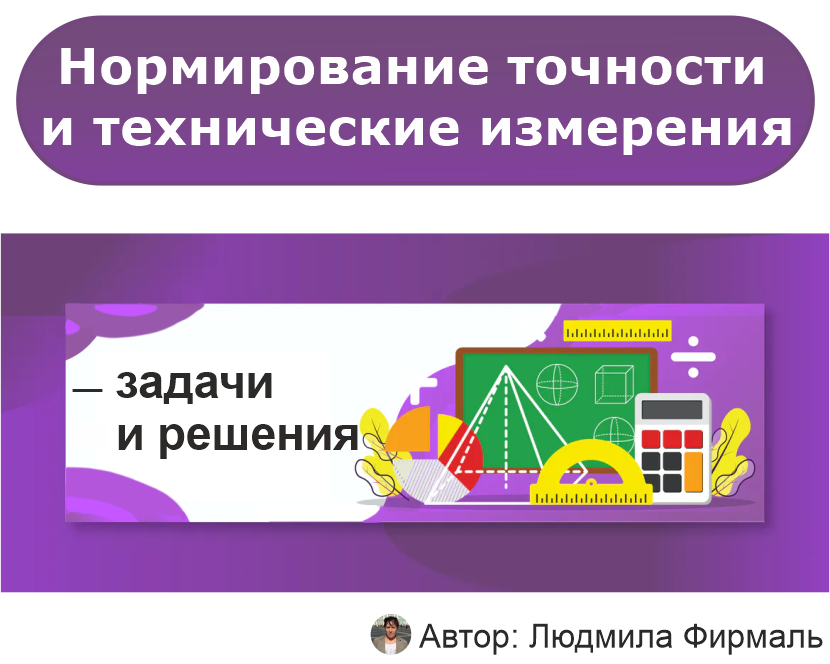
Прежде чем изучать готовые решения задачи по нормированию точности и техническим измерениям, нужно знать теорию, поэтому для вас я подготовила краткую теорию по разделу «нормирование точности и технические измерения» после которых идёт подробный разбор заданий.
Если что-то непонятно — вы всегда можете написать мне в WhatsApp и я вам помогу! |
Нормирование точности и технические измерения
В современных условиях очень важной проблемой является достижение качества продукции при высокой эффективности труда. Одним из условий решения вопросов качества продукции машиностроения служат нормы точности.
Возможно эта страница вам будет полезна:
Предмет метрология |
В пособии рассматривается нормирование точности только линейных размеров гладких поверхностей деталей и соединений, понятия о размерах, сопряжениях, допусках размеров и посадках.
Точность изделий — это степень соответствия действительных параметров изделий их заранее установленным значениям.
Иными словами точность изделий, это в некотором смысле качество изделий.
Качество продукции, эффективность ее производства и использования, а также экономия ресурсов в значительной степени зависят от обеспечения ее взаимозаменяемости. Под взаимозаменяемостью понимают способность объекта быть использованным без модификаций вместо другого для выполнения тех же требований (стандарт ИСО\МЭК2), или свойства единиц продукции заменять любые другие из множества однотипных экземпляров, изготовленных с заданной точностью.
Иллюстрацией геометрической взаимозаменяемости подшипников качения и цапф валов является рис.1 (а — экземпляры подшипников (1,2,3) и валов (1,11,Ш); б — соединение подшипника с валом). Любой из трёх подшипников может быть посажен на любую из трех цапф без подгонки, обеспечивая нормальную работу изделий.
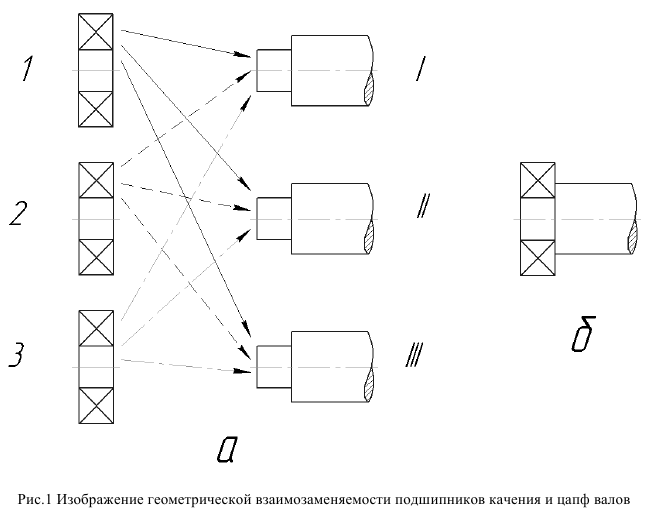
Виды взаимозаменяемости
Полная взаимозаменяемость
Обеспечивает возможность беспригоночной сборки (или замены при ремонте) любых независимо изготовленных с заданной точностью однотипных деталей в сборочные единицы, а последних — в изделия при соблюдении предъявляемых к ним (сборочным единицам или изделиям) технических требований по всем параметрам качества.
Полная взаимозаменяемость возможна только тогда, когда размеры, форма, механические, электрические и другие количественные и качественные характеристики деталей и сборочных единиц после изготовления находятся в заданных пределах. Следовательно, после сборки изделие будет удовлетворять техническим требованиям.
В первую очередь взаимозаменяемыми должны быть такие детали и сборочные единицы, от которых зависят надежность и другие эксплуатационные показатели изделий. Это требование распространяется также на запасные части.
Свойство собираемости и возможности равноценной замены любого экземпляра взаимозаменяемой детали и сборочной единицы любым другим однотипным экземпляром позволяет изготовлять детали в одних цехах машиностроительных заводов серийного и массового производства, а собирать их — в других.
При обеспечении полной взаимозаменяемости имеют место следующие преимущества:
• Упрощается процесс сборки;
• Появляется возможность нормировать процесс сборки во времени, устанавливать необходимый темп работы, применять поточный метод;
• Создаются условия для автоматизации процессов изготовления и сборки изделий;
• Упрощается ремонт изделий, т.к. любая изношенная или поломанная деталь или сборочная единица может быть заменена новой или запасной.
Частичная (неполная) взаимозаменяемость
В некоторых случаях для удовлетворения эксплуатационных требований необходимо изготавливать детали и сборочные единицы с малыми допусками, например, если большой допуск экономически неприемлем или технологически трудно выполним. В этих случаях для получения требуемой точности сборки применяют групповой подбор деталей, компенсаторы, регулирование положения некоторых частей машин и приборов, пригонку и другие дополнительные технологические мероприятия при обязательном выполнении требований к качеству сборочных единиц и изделий. Такую взаимозаменяемость называют неполной.
- Пригонка
изделие по большинству параметров взаимозаменяемо, а по одному или нескольким параметрам разрешается доработка;
- Регулирование или компенсация
регулирование положения некоторых частей машин и приборов (в данном случае в размерную цепочку включается звено, которое может изменять свои размеры;
- Групповой подбор или селективная сборка.
Функциональная взаимозаменяемость
Функциональная взаимозаменяемость осуществляется в несколько этапов:
1) Определяются функциональные параметры, т.е. те параметры, которые влияют на эксплуатационные свойства (геометрические, механические, электрические параметры);
2) Определяется закономерность изменения функциональных параметров во времени и закон их влияния на эксплуатационные характеристики (аналитически и экспериментально необходимо установить степень влияния этих параметров и их отклонений на эксплуатационные параметры; изучаемые связи имеют либо закономерный, либо вероятностный характер);
3) Назначается точность на функциональные параметры так, чтобы эксплуатационные характеристики были оптимальны (т.е. назначается допуск на функциональные параметры).
При функциональной взаимозаменяемости ставится задача создания на стадии проектирования запаса точности.
Значение взаимозаменяемости
- при проектировании появляется возможность использования унифицированных стандартизованных узлов и деталей;
- при изготовлении — возможность серийного производства;
- сокращение числа режущих и измерительных инструментов;
- упрощение сборки и ремонта;
- единообразие методов контроля.
Основой взаимозаменяемости машин, приборов и других изделий служат допуски и посадки (нормы взаимозаменяемости, нормы точности).
Машины и другие изделия чаще всего плохо работают или преждевременно выходят из строя из-за неправильно установленных допусков и посадок при проектировании изделий или из-за несоблюдения их при изготовлении и ремонте изделий.
Сведения об элементах и параметрах изделий
Детали машин и других изделий представляют собой определённые комбинации геометрических тел, в большинстве случаев ограниченные поверхностями простейших форм: плоскими, цилиндрическими, коническими и т.д. Простейшие геометрические тела, их поверхности (в том числе плоскости симметрии), совокупности поверхностей (например, плоскости, образующие прямоугольный паз), линии, образующие поверхности (например, образующая цилиндра), оси симметрии, профили — линии пересечения поверхностей с секущей плоскостью, как правило, направленной нормально к поверхности (например, окружность), точки (например, центр окружности) называют элементами.
Одинаковые элементы, которые качественно не различаются, могут различаться количественно.
Количественные признаки явлений, процессов, тел, изделий и их элементов в технике называют параметрами.
Параметры бывают физические, механические, электрические, геометрические и др. Здесь будут рассмотрены только геометрические параметры изделий.
Геометрические параметры подразделяют на линейные и угловые (углы). К линейным параметрам относят протяженность, расстояние, длину, высоту, диаметр, толщину и т.д. Основным геометрическим параметром является размер. Все остальные геометрические параметры являются производными от размера. Форма поверхности определяется формообразующим размером, расположение поверхностей, профилей и осей определяется координирующими размерами. Параметры волнистости и шероховатостей также определяются размерами.
Размер представляет собой разновидность параметров (в физике, метрологии размер величины или просто величина).
Каждый параметр (размер) имеет определенную структуру. Например, в записи: размер (диаметр) 10 мм, размер (диаметр) — наименование,
— обозначение, 10 мм значение (101 мм, где 10 — числовое значение размера, 1 — числовое значение единицы измерения (не записывается), мм — сокращенное наименование единицы измерения).
В технике имеют дело с именованными величинами (параметрами), а не с отвлеченными числами. Величины имеют размерность, поэтому в текстовых записях единицы измерения обязательно нужно указывать.
Сведения о погрешностях геометрических параметров изделий
Ничего нельзя не изготовить, ни измерить без хотя бы небольшой неточности. Из-за этого при изготовлении изделий числовое значение полученного параметра отличается or заданного значения, т. е. каждый параметр (размер) может быть получен лишь с каким-то приближением, с какой-то неточностью.
Точность — понятие качественное. Количественной оценкой, мерой точности я вляется погрешность.
Погрешность () параметра (
) выражают так:

где — полученное значение параметра
:
— заданное значение параметра
.
Например,

тогда

Перед числовым значением погрешности обязательно ставится знак (плюс или минус).
Связи между разными параметрами и их погрешностями различны. Если говорить о размерах, то погрешность линейного размера зависит от самого размера, а погрешность углового размера не зависит от самого угла.
Для линейных размеров менее 3 мм с уменьшение размера погрешность возрастает. Для размеров от 3 мм с увеличением размера погрешность снова возрастает.
Общая классификации погрешностей при изготовлении изделий и причины их вызывающие
Погрешности по статическому признаку проявления подразделяются на грубые («промахи»- их нужно и можно избегать) и неизбежные (их избежать нельзя, но нужно, по возможности, уменьшать).
Грубые погрешности, как правило, заметны по полученным результатам, так как они резко отличаются от других. Незаметные грубые погрешности выявляются при помощи специальных способов статистической обработки результатов.
Грубые погрешности возникают по следующим причинам:
-невнимательность, небрежность работника, не соблюдение им установленных правил;
-несоответствие квалификации работника сложности выполняемой работы; -неисправность оборудования, оснастки;
-отсутствие нормальных условий для выполнения данной работы (неудобное рабочее место, недостаточная освещенность, отвлекающие факторы и т.д.);
-плохое состояние работника (болезнь, плохое настроение, «эффект понедельника» И др.).
Меры исключений грубых погрешностей: -внедрение систем менеджмента качества; -обучение и повышение квалификации работника; -своевременный контроль за оборудованием, оснасткой и их ремонт;
К неизбежным погрешностям относятся систематические () и случайные (
). Строго говоря, такое разделение условно, так как любая погрешность имеет элемент случайности. Если этот элемент случайности очень мал, то погрешность относят к систематическим. Некоторые погрешности могут иметь переменный характер. Например, до определенного момента износа резца погрешность из-за износа имеет систематический характер, а после — случайный.
Систематические — это такие погрешности, которые проявляются систематически составляющие их можно выявить на каждой детали партий (определить при помощи измерений). Их часто можно предвидеть.
Систематические погрешности имеют две разновидности: постоянные но величине и знаку или изменяющиеся но определённому закону. Последние погрешности, в свою очередь, подразделяются на прогрессирующие и сложные.
Систематические постоянные по величине и знаку погрешности могут возникать по следующим причинам:
-неточность метода изготовления изделия; -конструктивная неточность оборудования, оснастки;
-неточность настройки технологического комплекса при изготовлении и измерении; -постоянные силовые и температурные деформации при изготовлении изделия.
Причины, вызывающие систематические, изменяющиеся по определенному закону прогрессирующие погрешности:
-деформации, связанные с постоянным разогревом или охлаждением оборудования, оснастки,заготовки;
-деформации, связанные со старением и усталостью материалов деталей оборудования, оснастки и другое.
Систематические, изменяющиеся по определенному закону сложные погрешности возникают, например, при износе режущих инструментов, так как сначала износ идет интенсивно (идет приработка), потом стабилизируется, а при достижении определенного значения снова резко возрастает.
Систематические погрешности суммируются алгебраически:

Составляющие систематической погрешности с разными знаками компенсируют друг друга, а с одинаковыми — увеличивают суммарную погрешность.
Случайные — это такие непостоянные погрешности, составляющие которых невозможно, как правило, предвидеть, так как они возникают случайным образом. Их невозможно выявить оп отдельным результатам измерений. Они возникают при одновременном воздействии многих источников, каждый из которых сам оказывает незаметное влияние, но суммарное их воздействие может быть большим.
Невозможно найти жизненную ситуацию, в которой не имел бы место «Его Величество случай». Однако случайности можно выявить, если знать, что достаточно много случайностей вместе дают определенную статическую закономерность, которая поддается изучению и результаты этого изучения можно использовать с пользой. Для этого необходим достаточный массив результатов опытов (как минимум 25, а лучше 100-200 результатов; чем больше результатов, тем точнее можно выявить закономерность).
Причины, вызывающие случайные погрешности:
-неодинаковость механических свойств материалов (например, разная твердость) и припуска заготовок деталей и инструмента;
-деформации вследствие перераспределения внутренних напряжений;
-случайные силовые и температурные деформации;
-случайные изменения зазоров между деталями оборудования и оснастки во время работы.
Случайные погрешности суммируют квадратически:

Так как суммарная случайная погрешность является величиной квадратической, то имеет знак «плюс». Но влиять на результаты измерения она может, увеличивая их как в «плюс», гак и в «минус». Поэтому общая суммарная погрешность:

Систематические и случайные погрешности оказывают влияние одновременно, потому общая погрешность представляет собой величину случайную (если в ряду неслучайных величин есть хотя бы одна случайная величина, то весь ряд превращается в случайный), в результате, как и другие случайные величины, общая погрешность имеет вероятностный характер и подчиняется законам теории вероятностей. В производственных условиях закономерности распределения погрешностей можно определить с помощью статической обработки большого количества полученных результатов.
Величиной и закономерностью погрешностей можно управлять:
-устраняя причины, вызывающие отдельные составляющие систематической погрешности;
-уменьшая влияние отдельных составляющих систематической погрешности (например, повышая износостойкость изнашиваемых деталей оборудования, износостойкость режущих инструментов);
-уменьшая отдельные составляющие систематической погрешности путем компенсации (например, путем регулирования зазоров, в том числе автоматического);
-определяя и учитывая отдельные составляющие систематической погрешности и внося соответствующие поправки в результаты измерений;
-перераспределяя погрешности с противоположными знаками путем смещения центра их группирования соответствующей настройкой технологического комплекса (сдвигая центр группирования к нижней границе поля допуска размера вала, т.е. в сторону исправимого брака, что одновременно способствует увеличению запаса материала на износ детали);
-уменьшая влияние случайных погрешностей путем выполнения многократных измерений и статической обработки результатов.
Теория ошибок с применением аппарата математической статистики (теории вероятностей) позволяет определять закономерности случайных погрешностей.
Влияние погрешностей размеров на собираемость и эксплуатационные свойства изделий
Погрешности размеров затрудняют сборку изделий, снижают ее точность и повышают трудоемкость. Ухудшают некоторые физико-механические свойства изделий (особенно приборов), например, жесткость и чувствительность пружин, электрические свойства электромагнитных устройств (сопротивление и др.). Снижают точность работы механизмов, точность измерений, прочность деталей. Увеличивают массу изделий и расход материалов, увеличивают или уменьшают необходимые зазоры и натяги в соединениях деталей. Например, уменьшение зазора в соединении поршень-цилиндр двигателя внутреннего сгорания или в компрессоре может привести к повреждению сопрягаемых поверхностей, а увеличение зазора — к снижению КПД двигателя и некоторых эксплуатационных показателей компрессора. Увеличение погрешностей размеров деталей металлообрабатывающего оборудования или оснастки ведет к снижению точности изготовляемых с их помощью изделий.
Вероятность и закон нормального распределения вероятностей
Вероятность — действительное число в диапазоне от 0 до 1, приписываемое случайному событию, представляющее отношение количества благоприятных случаев
ко всему количеству возможных случаев
в данной совокупности случаев:

При


при


При событие считается маловероятным, при
— вероятным. Чем больше
,тем больше вероятность и достоверность события. При
, стремящемся к бесконечности,
стремится к 1 (закон больших чисел).
Теория вероятностей содержит несколько законов распределения. Чаще других имеет место закон нормального распределения вероятностей, или закон Гаусса.
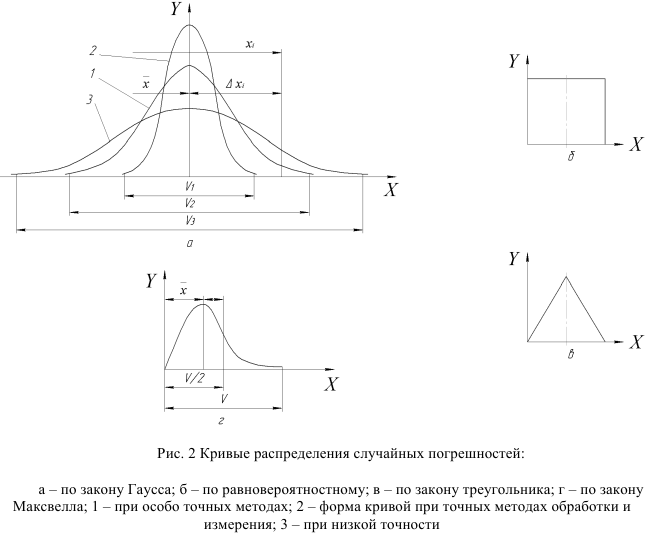
Закон Гаусса действует при большом количестве относительно малых , равнозначных, равновозможных и равновлияющих независимых факторов (т.е. когда нет преобладающих факторов).Этот закон проявляется при изготовлении изделий на настроенном автоматизированном оборудовании в условиях массового и серийного производств, а также при линейных измерениях.
Если учитывать только случайные погрешности в чистом виде, то закон Гаусса можно представить графически (рис.2) в виде теоретической кривой нормального распределения (кривой плотности распределения вероятности), где — плотность вероятности, или частость (отношение количества благоприятных событий к количеству всех событий); в нашем случае частота появления
-й составляющей случайной погрешности:
остаточная
-я погрешность, или погрешность отдельного
-го измерения, характеризующая отклонение случайной величины о центра группирования (центр группирования — ось
), где
-порядковые номера деталей в партии или порядковые номера измерений:
-параметр
-й детали партии или результат
-го измерения;
-средний арифметический параметр партии деталей или средний арифметический результат измерений (опытов), соответствующий центру группирования параметров детали в партии или результатов измерений (которое при неограниченном числе измерений называется математическим ожиданием
).
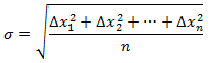
-средняя квадратическая погрешность, которая характеризует зону рассеяния-разброса случайных величин относительно центра группирования (в знаменателе
, если
, если
).
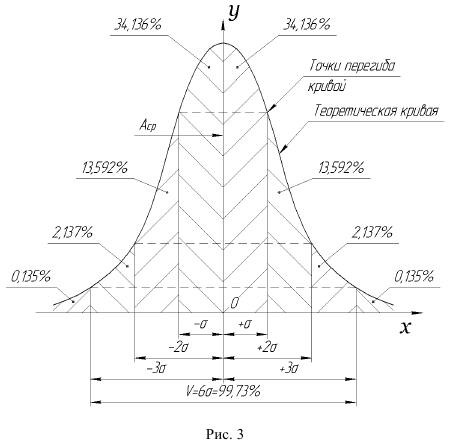
Кривая Гаусса (нормального распределения) описывается уравнением:
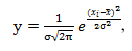
где — основание натурального логарифма.
Из формы кривой видно, что большие отклонения появляются значительно реже, чем малые, а появление очень больших отклонений маловероятно. Поэтому принимаемые в расчет погрешности ограничиваются некоторыми предельными значениями , где
-размах или поле рассеяния случайных погрешностей, определяемое как разность между наибольшими и наименьшими померенными размерами в партии деталей.
Теоретическая кривая нормального распределения обладает таким свойством, что если площадь, заключенную между кривой и осью абсцисс, принять за 100% (или равной 1), то площадь, заключенная между частью кривой и отрезком составит
, между частью кривой и отрезком в пределах
от всей площади (доверительная вероятность измерения), между частью кривой и отрезком
от всей площади (доверительная вероятность технологическая). Распределение этих площадей соответствует распределению случайных величин.
Величина называется предельной (допустимой) случайной технологической погрешностью, в дальнейшем мы будем называть технологическим допуском. А зона рассеяния погрешностей, соответствующая величине
, называется полем рассеяния технологических погрешностей. Площадь, оставшаяся за пределами
, равна 0,27% (за правой и левой ветвями кривой по 0,135%).Следовательно, с вероятностью, весьма близкой к 100% (К1), можно утверждать, что случайные погрешности параметров достаточно большой партии деталей не будут выходить за пределы
, а вероятность появления брака составит 0,27%, что, как правило, допустимо (0,27% составляет 3 детали из 1000 ил 27 из 10000).
Технологические погрешности параметров, превышающие , и погрешности измерений, превышающие
, относят к грубым.
Анализируя кривую Гаусса, можно сделать следующие выводы:
-малые по величине погрешности встречаются значительно чаще, чем большие (сила мелочей в том, что их много, и потому они могут приводить к большим отрицательным последствиям);
-одинаковые по абсолютной величине, но противоположные по знаку погрешности встречаются одинаково часто;
-большинство параметров партии деталей или результатов измерений и их погрешностей группируются около середины поля рассеяния (центра группирования случайных величин, т.е. имеют погрешности, стремящиеся к нулю, но не равные нулю);
-с увеличением количества деталей или измерений среднее арифметическое из случайных величин данного ряда стремится к нулю (благодаря чему, увеличивая количество измерений одной величины, можно уменьшать влияние случайных погрешностей на результаты измерений, практически исключая их);
-наиболее достоверные значения результатов при многократных измерениях представляют собой средние арифметические из полученных результатов;
-технологические погрешности, выходящие за пределы , признаются грубыми; -погрешности измерений, выходящие за пределы
, признаются грубыми и исключаются из результатов измерений.
По форме кривой Гаусса можно сравнивать параметры и результаты измерений по точности. Чем выше и сжата кривая, тем точность выше.

Как уже отмечалось, одновременно имеют место как систематические, гак и случайные погрешности, поэтому форма и расположение кривой распределения изменяются (рис.4). Систематические постоянные по величине и знаку погрешности смещают центр группирования относительно оси ординат (т.е. -величина смещения).
Нормальный, номинальный и предельные размеры. Условие годности размера
Числовое значение размера любого элемента заготовки, детали, узла, изделия определяют путем расчета, например, на прочность или жесткость или же исходя из каких-то конструктивных, технологических, экономических, эргономических, эстетических и других соображений. Предварительно определенное значение размера, как правило, округляют до ближайшего стандартного значения, которое называют нормальным размером. При расчете, например, на прочность, размер округляют до ближайшего большего нормально размера. ГОСТ 6636-69 устанавливает четыре основных ряда нормальных линейных размеров (есть еще дополнительные и произвольные ряды). Действие этого стандарта не распространяется на технологические межоперационные размеры, на размеры, установленные специальными стандартами на конкретные изделия, на размеры, зависящие от других принятых величин (например, диаметр малого основного конуса зависит or диаметра большого основного конуса). В исключительных случаях, по разрешению службы стандартизации, допускается применение нестандартных размеров.
По ГОСТу 6636-69: каждый ряд чисел представляет собой геометрическую прогрессию со знаменателем , где
равно 5; 10; 20; 40; 80 и 160.
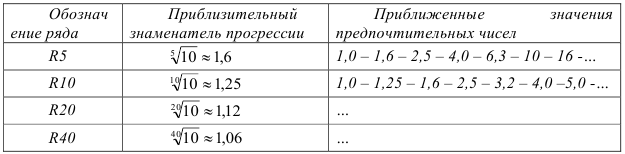
При выборе значения нормального размера, размеры первого ряда (с более крупной градацией ) следует предпочитать размерам второго ряда (с менее крупной градацией).
При выборе нормального размера, размеры первого ряда (с более грубой градацией, например 10; 16; 25…) следует предпочитать размерам второго ряда (с менее крупной градацией, например 10; 12; 16; 20; 25 …), размеры второго ряда — размерам третьего и т.д. Ряды нормальных линейных размеров установлены в целях сокращения количества типоразмеров применяемых заготовок, деталей, изделий, нерегулируемых элементов оснастки (разверток, элементов штампов и др.).
Нормальные размеры, как правило, указывают в чертежах и другой документации в качестве номинальных размеров.
Номинальный размер, или номинал (разные источники применяют разные обозначения: ) — это основной размер, относительно которого определяются отклонения.
Числовые значения номинального размера может представлять собой целое или дробное число. Правильная запись: 10 мм, 10,1 мм. Неправильная запись: 10,0 мм, 10,10мм (нули в конце дробной части не пишут, так как номиналом не определяется порядок-точности).
Так как при изготовлении и измерениях деталей происходит рассеяние числовых значений размеров, то каждый размер, который нужно получить, необходимо задавать двумя предельно допустимыми значениями, между которыми находились бы размеры годной детали . Размер годной детали, имеющий большее предельно допустимое значение, называют наибольшим предельным размером
, а имеющим меньшее значение — наименьшим предельным размером
. Таким образом, предельные размеры устанавливают допустимые колебания задаваемого размера.
Условие годности размера:
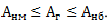
Например, заданы

то деталь будет годной при размерах не более 10,1 мм и не менее 9,9 мм.
Числовые значения предельных размеров записывают с необходимым количеством цифр после запятой, в том числе с нулями в конце, так как количество цифр после запятой определяет порядок точности. Например, могут быть

Если — внутренний размер детали (например, диаметр отверстия), то при
, будет иметь место брак «плюс» (в этом случае говорят, что отверстие «провалено»; как правило, этот брак неисправимый), при
будет иметь место брак «минус» (как правило, брак исправимый). Если
наружный размер детали (например, диаметр вала), то при
будет иметь место брак «плюс» (в этом случае говорят, что вал полнее, чем нужно; как правило, этот брак исправимый), при
будет иметь место брак «минус» (вал провален, как правило, это брак неисправимый).
Наибольший и наименьший предельные размеры (любой из них) могут быть меньше номинального размера, один из них может быть равен номинальному размеру (но никогда оба не могут быть равны номинальному размеру). Например, при предельные размеры могут иметь значения


Допуск и предельные отклонения размера. Исполнительный размер
Погрешность процесса — мера точности или в некотором роде мера качества. Увеличение допустимой погрешности приводит к ухудшению свойств воздействий (точность механизмов, КПД, веса и др.), но снижает себестоимость. Поэтому выбор допустимого уровня погрешностей зависит от состояния цена-качество и назначения продукции.
Допуск — допускаемая погрешность, норма точности, которая устанавливается чертежом или другой нормативно-технической документацией.
Установление допусков (норм точности) называют НОРМИРОВАНИЕМ ТОЧНОСТИ. Допуск определяет допустимый диапазон рассеяния, колебания значений задаваемого параметра. Допуск всегда является величиной положительной (равным нулю быть не может).
Допуск обозначается буквой (первая буква от французского слова Tolerance, что означает допустимый, терпимый).
Допуск размера выражают разность между наибольшим и наименьшим предельными размерами:

где — допуск размера
.
Например, если заданы (если величина всегда положительная, то знак «плюс» не указывают).
Числовое значение допуска записывают с необходимым количеством цифр после запятой, в том числе с нулями в конце, в зависимости от необходимого порядка точности, например: 0,1 мм, 0,10 мм, 0,100 мм.
Чем меньше допуск размера, тем выше норма точности размера, выше эксплуатационные свойства изделия, но труднее и дороже получение такого размера (нужны более точные и дорогие технологическое оборудование, инструменты, трудоемкость получения размера возрастает, необходима более высокая квалификация рабочего, увеличивается возможное количество брака). Например, в зависимости от метода обработки детали с уменьшением допуска размера с 0,1 до 0,05 мм (т.е. в 2 раза) относительная стоимость получения размера может возрасти в 2,8 раза. Поэтому перед конструктором или технологом всегда стоит задача нахождения оптимального решения -разрешения противоречия межу эксплуатационными и конструктивными требованиями с одной стороны и возможностями и экономикой производства с другой. Таким образом, правильно установленным допуском следует считать такой возможно больший допуск, при котором полностью удовлетворяются конструктивные эксплуатационные требования к изделию.
Конструкторский допуск — заданная точность элемента, детали, изделия -устанавливают исходя из условия обеспечения нужного качества продукции и, прежде всего, эксплуатационных требований при длительной эксплуатации изделия, но с учетом технологических, метрологических и экономических возможностей (ориентируясь на передовую технологию). При установлении конструкторского допуска необходимо создавать запас точности на определенную длительность эксплуатации, так как со временем детали изнашиваются и точность снижается. Поэтому
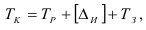
где — конструктивная часть допуска, расчетная, необходимая для нормальной работы конструкции;
— допускаемая погрешность измерения размера;
— запас точности на длительную эксплуатацию.
Необходимо помнить, что допуски элементов деталей станков, приспособлений, инструментов, от которых зависит точность изготовленных с их помощью деталей изделий, должны быть значительно более жесткими, чем допуски деталей изделий.
Технологический допуск — точность, обеспечиваемая технологическим оборудованием — устанавливают на основе конструкторского допуска с учетом технологических требований, метрологических и экономических возможностей.
Технологический допуск рекомендуется устанавливать с некоторым технологическим запасом точности по сравнению с конструкторским допуском (т.е. технологический допуск должен быть более жестким, чем конструкторский). Обычно рекомендуется ., т.е.
должен быть не менее чем на 20% меньше конструкторского.
Как конструкторский, так и технологический допуски линейных размеров должны учитывать допускаемые погрешности измерений, которые составляют 20-40% от допуска линейного размера (т.е. 20-40% допуска идет на компенсацию погрешностей измерения).
Станки, приспособления и обрабатывающие инструменты должны соответствовать технологическому допуску изделия, т.е. рассеяние действительных размеров данным технологическим комплексом не должно превышать технологического допуска изделия.
Таким образом,

В чертежах и других нормативно-технических документах непосредственно допуски размеров, как правило, не указывают. Чаще всего допуски размеров выражают через предельно допустимые отклонения от номинального размера:
— верхнее предельное отклонение размера отверстия вала);
-нижнее предельное отклонение размера отверстия (вала).
Предельные отклонения размера определяются по формулам:
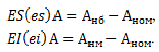
Например, если

то
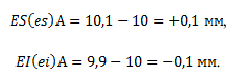
Числовые значения предельных отклонений записываются с необходимым количеством цифр после запятой, в том числе к нулями в конце, в зависимости от необходимого порядка точности (так же, как и допуски).
Верхнее и нижнее предельные отклонения могут быть оба положительными, оба отрицательными, верхнее может быть положительным, а нижнее отрицательным, одно из них может быть равным нулю (оба равным нулю быть не могут!).
Например,
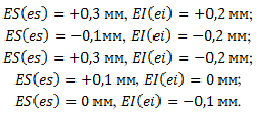
Знаки отклонений, даже если они положительные, обязательно указывают, так как-предельные отклонения представляют собой величины направленные (а не просто положительные числа).
Так как на чертежах допуски, как правило, выражают через предельные отклонения, то допуск размера можно выразить так:

Например,

тогда

Эта формула более удобна для практического применения.
Исполнительный размер, ноле допуска и графическое изображение исполнительного размера
Исполнительный размер — это заданный, нормированный размер, который должен быть получен при изготовлении, т.е. тот размер, который установил, например, конструктор или технолог.
Исполнительный размер — это обобщающее название: если он указан в чертеже, то его называют конструкторским, если в технологической документации — технологическим (например, операционным).
Исполнительный размер может быть записан в разной форме (подробно этот вопрос будет рассмотрен ниже). Например, он может быть записан в следующей форме (при цифровом обозначении поля):
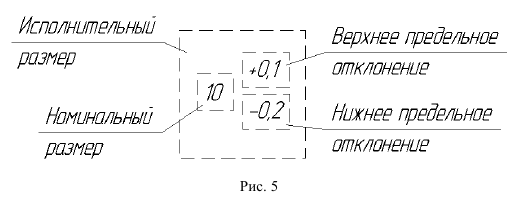
Исполнительный технологический (операционный) размер, чаще всего задается через одно отклонение (второе равно 0). Для отверстия это отклонение имеет знак «плюс», для вала «минус». Для расчета исполнительного технологического размера рассчитывается и допуск
.
Если рассчитывается размер для отверстия, то за номинальный размер принимается , а весь допуск располагается в плюс, т.е. верхнее отклонение равно +
. Если рассчитывается размер для вала, то за номинальный размер принимается
, а весь допуск располагается в минус, т.е. нижнее отклонение равно —
.
Пример перерасчета исполнительного технологического (операционного) размера из конструкторского, приведенного выше.
Конструкторский исполнительный .

Исполнительный — технологический (операционный) будет:
■ в случае отверстия
■ в случае вала
Поле допуска размера — совокупность верхнего и нижнего предельных отклонений или интервал значений размера, ограниченный верхним или нижним предельным отклонением. При графическом изображении поле допуска — это ноле, заключенное между линиями верхнего и нижнего предельных отклонений в виде прямоугольника.
Поле допуска и допуск — понятия разные. Поле допуска включает понятие допуска и о том, как допуск расположен относительно номинального размера.
Для построения ноля допуска проводится нулевая линия, обозначающая номинальный размер, отклонения со знаком плюс откладывается над линией, со знаком минус — под линией. Номинальный размер указывается в миллиметрах, а предельные отклонения в микрометрах. Масштаб произвольный.
На рис.6 показано, как строится графическое изображение исполнительного размера элемента вала
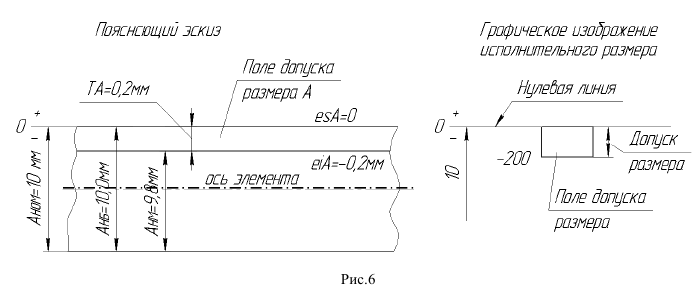
На рис. 7 показано, что поля допусков, в зависимости от предельных отклонений, могут быть по-разному расположены относительно номинала (относительно нулевой линии, которая символизирует номинал). На рисунке видно также, что один и тот же допуск (на рисунке допуск 0,2 мм = 200 мм) может быть задан множеством нар предельных отклонений, а поэтому при одном и том же допуске ноля допусков могут быть разные.
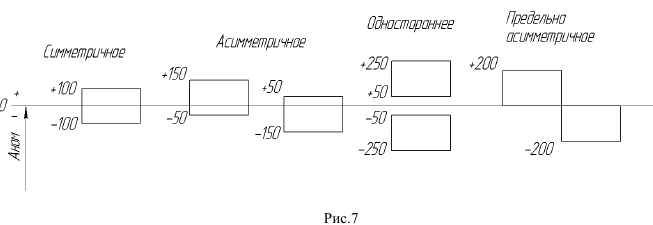
Ниже приведены поля допусков для рассчитанных выше исполнительных размеров:
Исполнительный конструкторский численно графически:
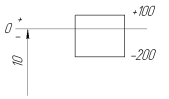
Исполнительный технологический (операционный) * для отверстия: численно графически
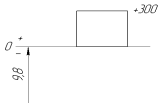
- для вала численно
- графически *
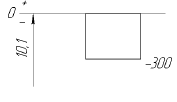
Возможно эта страница вам будет полезна:
Решение задач по метрологии |
Действительный размер и выбор средства измерения по точности
Предположим, конструктор или технолог в нормативно-технической документации установили необходимый исполнительный размер. Деталь изготовили. Как определить, какой размер получился, годен он или негоден? Определить это можно только путем измерения.
Измерение производится для определения соответствия размеров детали установленным требованиям. Под измерением понимают процесс нахождения значений физической величины опытным путем с помощью специальных технических средств, а под погрешностью измерения — отклонение результата измерения от истинного значения измеряемой величины.
Истинный размер — размер, полученный в результате обработки детали.
Значение истинного размера неизвестно, так как невозможно выполнить измерение без погрешности.
Поэтому вместо истинного значения определяют его действительное значение, которое несколько приближается к истинному значению, и для данной цели может быть использовано вместо него. Понятие «истинный размер» заменяется понятием «действительный размер».
Действительный размер () — это размер, полученный и измеренный с допускаемой погрешностью измерения, т.е.

где — истинное значение размера
;
— допускаемая погрешность измерения размера
.
Таким образом, размер нужно измерять так, чтобы соблюдалась допускаемая погрешность измерения этого размера. Допускаемые погрешности измерений установлены соответствующими стандартами.
Допускаемые погрешности измерений линейных размеров учитывают закономерную зависимость погрешности измерения размера от самого размера, погрешности средств измерений, составляющие погрешности от других источников, влияющих на погрешность измерения. Они нормируются независимо от способов измерений. По стандарту ГОСТ 8.051-81, который устанавливает допускаемые погрешности измерений линейных размеров до 500 мм универсальными рабочими средствами измерений, допускаемые погрешности измерений составляют лишь 20-35% от допусков размеров. Принятый процент зависит от квалитета (допуска) размера. Чем меньше допуск (точность выше), тем больший процент от него составляет допускаемая погрешность измерения, т.е. большая часть допуска идет на компенсацию погрешностей измерений.
Для стандартных универсальных средств измерений установлены предельные (наибольшие возможные) погрешности измерений, которые могут возникнуть при работе этими средствами.
Правило выбора средства измерения по точности:
предельная погрешность измерения конкретным средством не должна превышать допускаемой погрешности измерения, т.е.

где предельная погрешность измерения средства;
— допускаемая погрешность измерения размера.
Не следует путать понятия допускаемая погрешность размера (допуск размера), допускаемая погрешность измерения размера и предельная погрешность средства измерения.
Несоблюдение правила выбора средства измерения по точности ведет к нарушению принципа обеспечения единства измерений, к недостоверным результатам измерений, а это, в свою очередь, приводит к тому, что бракованные изделия относят к годным, а годные бракуют.
Если при выборе средства измерения предельная погрешность измерения окажется значительно меньше допускаемой погрешности измерения размера, то это снизит экономическую эффективность применения этого средства. Однако, если другого подходящего по точности средства нет, то следует использовать имеющееся.
Отверстия, валы, прочие элементы. Сопряжения. Посадки
Детали машин и других изделий имеют внутренние (охватывающие) и наружные (охватываемые) элементы. Внутренние элементы называют отверстиями (А), а наружные — валами (В). Если рассматривают элемент-отверстие, то и саму деталь, которой принадлежит этот элемент, называют отверстием; если рассматривают элемент-вал, то и саму деталь, которой принадлежит этот элемент, называют валом (рис. 8, 9). Детали соединяются между собой. В соединении двух деталей, когда одна деталь входит в другую, одна деталь охватывает другую. Охватывающую деталь называют отверстием, охватываемую — валом.
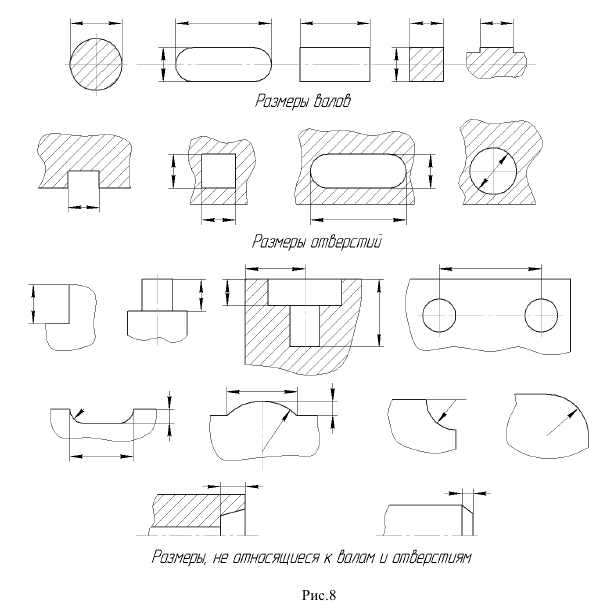
Кроме элементов-отверстий и элементов-валов, есть такие элементы, которые нельзя отнести ни к отверстиям, ни к валам. Их называют прочими (или остальными). К прочим (П) элементам относят уступы, глубины, расстояния между осями или плоскостями симметрии, расстояния между осью и поверхностью, а также радиусы закругления кромок и фаски (последнее неверно, но так принято).
При распознавании элементов по сборочному чертежу отдельные детали сборочной единицы, как правило, нужно представить себе в разобранном виде.
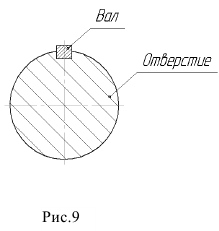
Возможны два типа соединений:
- когда номинальные размеры отверстия
и вала
не равны, т.е. когда
(например,
);
- когда номинальные размеры отверстия
и вала
равны, т.е. когда
(например,
).
Соединение, в котором номинальные размеры отверстия и вала равны, называют сопряжением.
На сборочном чертеже эти типы соединений показывают по-разному (рис. 10).
Если номинальный зазор в соединении настолько мал, что в масштабе чертежа показать его невозможно, то на чертеже его показывают увеличенным (не в масштабе чертежа).
Понимание того, что такое сопряжение необходимо, потому что стандартные посадки устанавливают только для таких соединений, которые представляют собой сопряжения. Они, в основном, и будут рассмотрены.
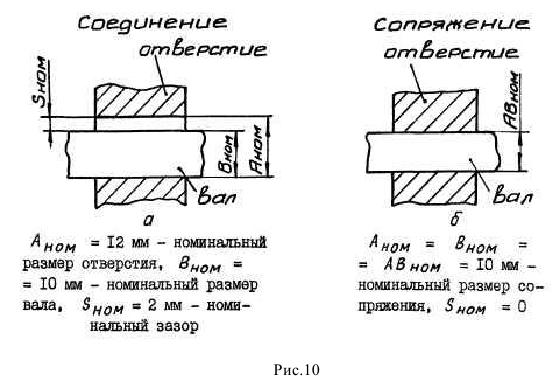
Соединения (в том числе сопряжения) бывают подвижными и неподвижными. Подвижным называют такое соединение, в котором в процессе работы изделия одна деталь должна двигаться относительно другой. Движение может быть вращательным, поступательным, постоянным и периодическим (перемещения деталей в процессе сборки-разборки не учитываются).
Зазор, натяг, посадка, группы посадок
Соединения могут быть с зазором и с натягом.
Зазор выражают разностью между размерами отверстия и вала, когда размер отверстия больше размера вала, т.е.
Натяг выражают разностью между размерами вала и отверстия, когда размер вала больше размера отверстия до сборки, т.е.
Посадкой называют характер соединения (отверстия и вала), который определяется разностью размеров отверстия и вала до сборки, наличием и величиной зазора или натяга.
От посадки зависит степень подвижности или неподвижности одной детали соединения относительно другой.
Посадки образуются сочетанием полей допусков размеров отверстия и вала. В зависимости от взаимного расположения полей допусков размеров отверстия и вала образуются разные посадки.
Посадки подразделяют на три группы (типа):
-с гарантированным зазором;
-с гарантированным натягом;
-переходные (может, как правило, возникнуть небольшой зазор или небольшой натяг).
Взаимное расположение нолей допусков размеров отверстии и вала, предельные зазоры и натяги в посадках разных групп
При конструировании изделия для того, чтобы соединения нормально работали, устанавливают нормы зазоров и натягов:
-Наибольший предельный зазор и наименьший предельный зазор
;
-Наибольший предельный натяг и наименьший предельный натяг
.
В посадке с гарантированным зазором (рис.11) поле допуска размера отверстия всегда расположено выше поля допуска размера вала .
В посадке переходной (рис.12) поля допусков размеров отверстия и вала перекрываются частично или полностью (поле допуска размера отверстия может быть смещено вверх ли вниз относительно поля допуска размера вала). В переходных посадках и
не бывает, так как зазор переходит в натяг, а натяг -в зазор.
В посадках с гарантированным натягом (рис.13) поле допуска размера вала всегда расположено выше ноля допуска размера отверстия. На рис. поля допуска заштрихованы.
Возможно эта страница вам будет полезна:
Допуски и посадки теория и практика |
Посадка с зазором
Пример 1 задачи с решением:
отверстие:
исполнительно-чертежный размер

вал:
исполнительно-чертежный размер

При соединении отверстия и вала с одинаковыми номинальными размерами получаем сопряжение с посадкой с зазором (рис. 11).
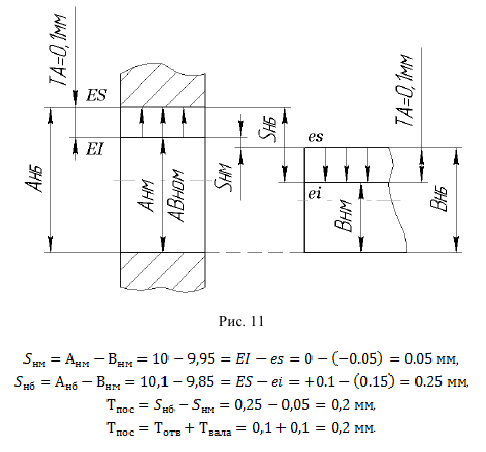
Переходная посадка
Пример 2 задачи с решением:
отверстие:

вал:

При соединении отверстия и вала получаем переходную посадку.
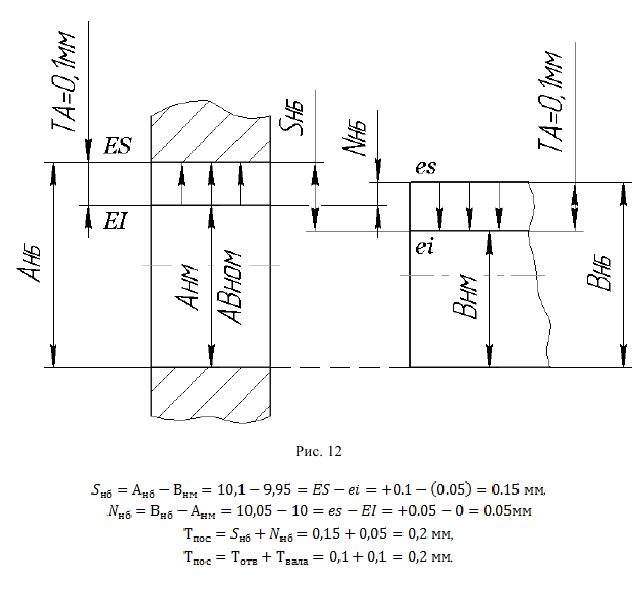
Посадка с натягом
Пример 3 задачи с решением:
отверстие:

вал:

При соединении отверстия и вала получаем посадку с натягом.
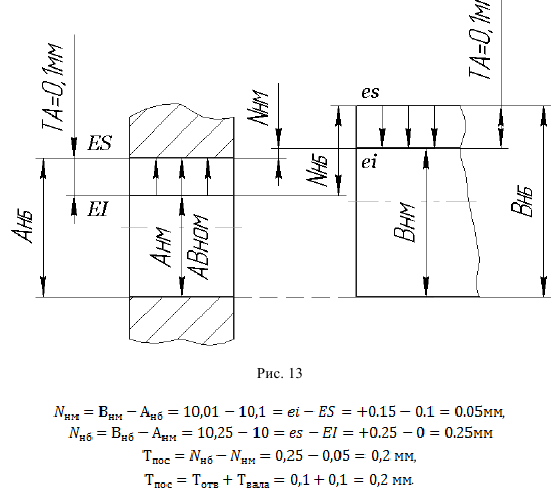
Возможно эта страница вам будет полезна:
Решение задач по допускам и посадкам |
Допуск посадки
Допуск посадки (допуск сопряжения) — это допустимая погрешность посадки (сопряжения), норма точности посадки (сопряжения).
Допуски посадок разных групп (см.рис. 11-13):
допуск посадки с гарантированным зазором (допуск зазора)

допуск посадки с гарантированным натягом (допуск натяга)

Допуск переходной посадки

Допуск любой посадки (сопряжения) всегда равен сумме допусков размеров отверстия и вала:

Под однородностью посадки понимают степень одинаковости (величину колебания) действительных зазоров или натягов, получающихся в сопряжениях разных деталей, изготовленных по одной и той же посадке (по одному чертежу). Чем меньше окажется колебание зазора или натяга в партии деталей, тем посадка будет однороднее, т.е. тем меньше будут отличаться зазоры и натяги в разных парах деталей партии.
Однородность посадки зависит от допуска посадки и настройки технологического комплекса, изготавливающего отверстия или валы Чем допуск посадки меньше, тем более однородной будет посадка.
По однородности посадки подразделяют
-на высокооднородные (размеры отверстий точнее 7-го квалитета, валов — точнее 6-го квалитета);
-однородные (среднеоднородные: размеры отверстия 7-го, 8-го квалитетов, валов -6-го,7-го квалитетов);
-низкооднородные (грубооднородные: размеры отверстий 9-го, 10-го квалитетов, валов — 8-го, 10-го квалитетов);
-неоднородные (размеры отверстий и валов грубее 10-го квалитета).
Необходимую однородность посадки учитывают при выборе квалитета размера.
Понятия о квалитегах будут рассмотрены ниже.
Возможно эта страница вам будет полезна:
Примеры решение задач по допускам и посадкам |
Принципы построения единой системы допусков и посадок
Действующая отечественная единая система допусков и посадок (ЕСДП) принципиально не отличается от международной системы Международной организации по стандартизации (ИСО). В международной системе принято большее количество полей допусков, нет предпочтительных полей допусков и посадок.
Система построена на следующих принципах:
Принцип образования стандартного поля допуска линейного размера
Стандартного поле допуска линейного размера образуется независимым сочетанием основного отклонения и допуска размера (рис.14).
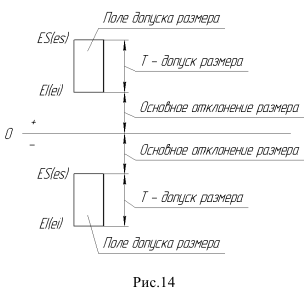
Основное отклонение — то из двух предельных отклонений размера (верхнее или нижнее), которое ближе к номинальному размеру (при графическом изображении ближе к нулевой линии), т.е. то, которое меньше по абсолютной величине. Для полей, расположенных над нулевой линией, — это нижнее отклонение, под нулевой линей верхнее. При симметричном расположении поля относительно нулевой линии безразлично, которое отклонение принимается за основное, но не следует учитывать знак отклонения (отклонения по абсолютной величине будут равны).
Основное отклонение определяет расположение и расстояние поля допуска относительно номинала. От основного отклонения, прежде всего, зависит посадка.
Основные отклонения обозначают буквами латинского алфавита: отклонения размеров отверстий — прописными буквами, валов — строчными (рис.15).

Для образования основных но системе посадок с гарантированным зазором используют основные отклонения размеров:
-отверстий —

-валов —


Для образования основных но системе стандартных переходных посадок используют основные отклонения размеров:
- отверстий —

- валов —
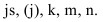
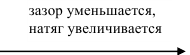
Для образования основных по системе стандартных посадок с гарантированным натягом используют основные отклонения размеров:
-отверстий —

-валов —


В скобках даны основные отклонения, которые не рекомендуется применять для металлических деталей с размерами до 500 мм.
Числовые значения основных отклонений определены по специальным формулам в прямой зависимости от интервалов номинальных размеров и не зависят, как правило, то допусков размеров. Основные отклонения размеров отверстий в и валов, обозначенные одной и той же буквой ,как правило, равны по величине, но противоположны по знаку.
Принцип основных и посадочных отверстий и валов
Основным отверстием называют такое, у которого нижнее предельное отклонение размера является основным и равно нулю. Основное отклонение размера основного отверстия обозначают буквой .
Основным валом называют такой, у которого верхнее предельное отклонение размера является основным и равно нулю. Основное отклонение размера основного вала обозначают буквой .
Все другие отверстия и валы (кроме основных) называют посадочными (неосновными), основные отклонения их размеров обозначаются остальными буквами (кроме и
).
Для допусков размеров основного отверстия и основного вала всегда расположены предельно асимметрично относительно нулевой линии (рис.16), что способствует снижению материалоемкости изделий (облегчению изделий и экономии материалов).
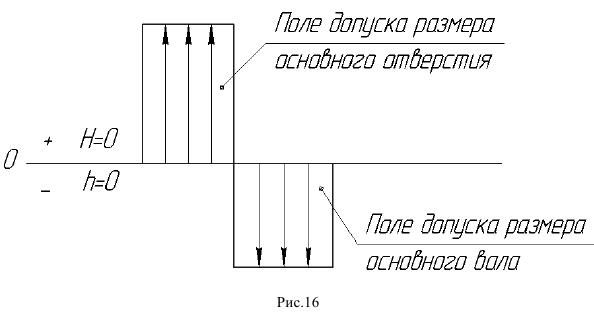
Принцип образования стандартной посадки
Стандартная посадка может быть образована одним из трех способов:
-в системе отверстия (в системе основного отверстия);
-в системе вала (в системе основного вала);
-комбинированной по системе (отверстие в системе вала, а вал в системе отверстия).
В системе отверстия — основное отверстие и посадочный вал.
В системе вала — основной вал и посадочное отверстие.
В системе отверстия расположение поля допуска размера отверстия остается постоянным для всех посадок, а разные посадки получаются за счет разного расположения полей допусков размеров валов (при данных интервале номинальных размеров и квалитете). В системе вала расположение поля допуска размере вала остается постоянным для всех посадок, а разные посадки получаются за счет разного расположения полей допусков размеров отверстий (при данных интервале номинальных размеров и квалитете).
Посадки в системах отверстия вала называют посадками основным по системе (рис. 17,18).
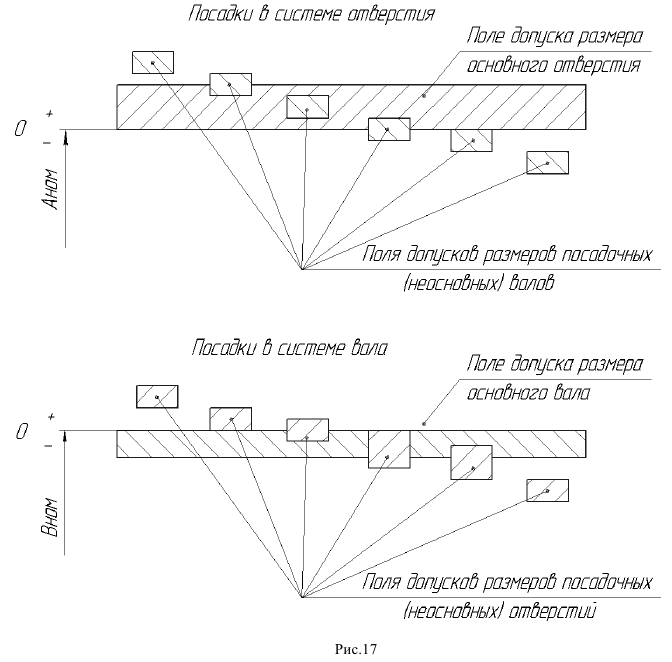
В комбинированных но системе посадках нет основных отверстия и вала, а сочетаются посадочные отверстия и валы. Разные посадки получаются за счет разного взаимного расположения полей допусков размеров посадочных отверстий и валов.
Посадки в системе отверстия применяются значительно чаще других и в большинстве случаев они оказываются более экономичными, так как сокращается количество применяемых типоразмеров сложных и дорогих нерегулируемых инструментов для обработки и контроля отверстий (протяжек, разверток, фрез, калибров-пробок).
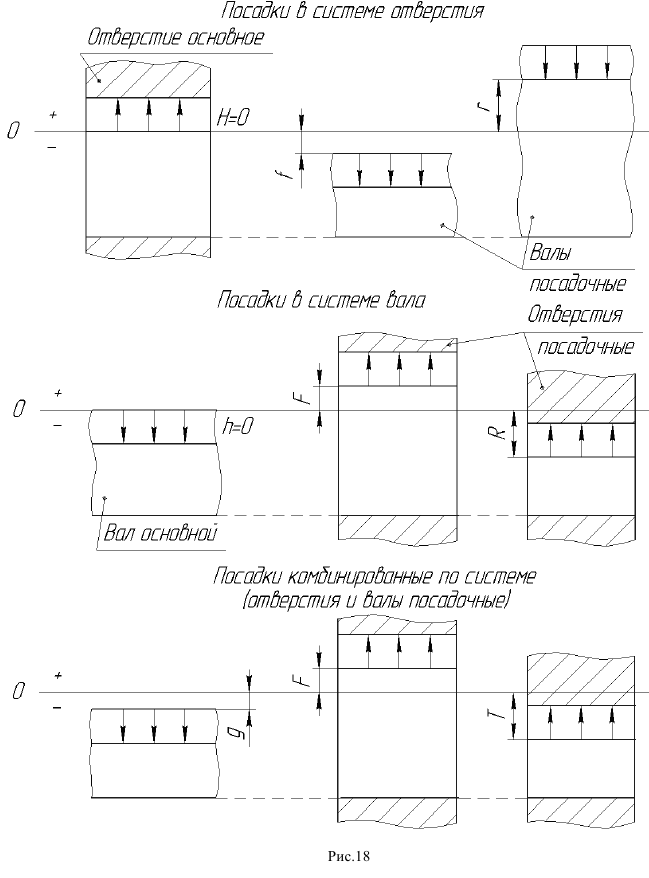
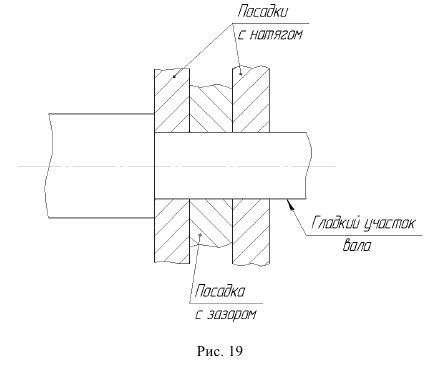
Однако в следующих случаях применение посадок в системе вала оказывается более целесообразным:
а) если гладкий вал или гладкий участок вала входит в несколько сопряжений с разными посадками (рис.19). Например, в сопряжениях поршневого пальца с отверстиями бобышек поршня и головки шатуна в двигателе внутреннего сгорания, в сопряжениях оси с отверстиями вилки и тяги в разных механизмах. Если бы для таких сопряжений устанавливалась система отверстия, то:
-вал оказался бы ступенчатым, что привело бы к снижению его прочности, особенно при больших знакопеременных нагрузках из-за образования дополнительных концентраторов напряжений, особенно при малых радиусах галтелей;
-усложнилась бы обработка и увеличилась трудоемкость обработки вала, так как ступени получились бы высотой всего в несколько сотых или десятых долей миллиметра (такой вал труднее обработать, чем вал со ступенями в несколько миллиметров);
б) если гладкий высокоточный вал (размер вала точнее 6-го квалитета) изготавливают для неизвестного (обезличенного) потребителя (т.е. когда неизвестно, на какое изделие, под какую посадку пойдет вал). Например, в сопряжениях с наружными кольцами подшипников качения, с осями приборов. Если бы для таких сопряжений устанавливалась система отверстия, то:
-потребовалось бы такие валы изготовлять с разными полями допусков размеров посадочных поверхностей, что привело бы к огромному увеличению количества необходимых типоразмеров таких валов (а это значительно затруднило бы производство валов);
-потребовалось бы значительное увеличение количества и объемов складов (так как-разные типоразмеры валов нужно было бы хранить раздельно — в разной таре, на разных полках);
в) если допуск заготовки позволяет изготовить вал без дополнительной обработки посадочных поверхностей. Например, когда вал можно изготовить из пруткового, листового, полосового, ленточного, трубного холоднокатаного проката, особенно из калиброванного проката (горячекатаный прокат непригоден из-за больших допусков).
Если бы для таких валов устанавливалась система отверстия, то часто пришлось бы дополнительно обрабатывать посадочные поверхности под разные посадки, что увеличило бы трудоемкость обработки таких валов.
Есть случаи, когда более целесообразны комбинированные по системе посадки.
Принцип группирования номинальных линейных размеров
Номинальные размеры сгруппированы в диапазоны: до 3 мм — малые размеры; свыше 3 до 500 мм — средние размеры (основной диапазон); свыше 500 до 40000 большие размеры (для размеров свыше 40000 мм стандартные допуски не установлены, но их можно определить экстраполяцией). Необходимость такого группирования вызвана тем, что в разных областях размеров разное влияние оказывают погрешности изготовления и измерений (по-разному влияют на размеры силовые, температурные и другие факторы). Например, температурные деформации меньше влияют на небольшие размеры и существенно — на большие, так как погрешность линейного размера зависит от самого размера, то это должно учитываться допусками размеров.
Кроме диапазонов, номинальные размеры группируются по интервалам. Например, до 3 мм, свыше 3 до 6 мм, свыше 6 до 10 мм и т.д. (для размеров до 1 мм есть вспомогательные интервалы: до 0,01 мм; свыше 0,1 до 0,3 мм; свыше 0,3 до 1 мм). Это сделано с целью сокращения количества допусков размеров. Для всех размеров данного интервала установлен один допуск (единица допуска), что позволяет сократить количество необходимых типоразмеров заготовок, деталей, нерегулируемых инструментов (протяжек, разверток и др.), элементов штампов (пуансонов, матриц) и приспособлений (кондукторных втулок, установочных пальцев и др.). Номинальные размеры сгруппированы так, чтобы допуски, подсчитанные для граничных (крайних) размеров интервалов, отличались бы от допусков, подсчитанных для средних геометрических размеров интервалов, не более чем на 5-8 %, что допустимо (практически не влияет на взаимозаменяемость изделий).
Для номинальных размеров свыше 10 мм установлены две разновидности интервалов: основные (широкие) и промежуточные (узкие). Каждый основной интервал содержит 2 или 3 промежуточных. Например, основной интервал свыше 10 до 18 мм содержит промежуточные интервалы: свыше 10 до 14 мм и свыше 14 до 18 мм. Промежуточные интервалы используют только для полей допусков с основными отклонениями размеров, образующих посадки с большими зазорами и натягам (для повышения их однородности).
Средний размер интервала для размеров свыше 3 мм определяется по формуле:
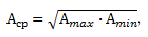
где и
— граничные размеры интервала (для размеров до 3 мм
).
При пользовании таблицами допусков предельные отклонения и допуски для граничных размеров интервалов нужно выбирать из предыдущего интервала. Например, предельные отклонения для номинального размера 6 мм нужно брать в интервале свыше 3 до 6 мм.
Принцип единицы стандартного допуска линейного размера
Единица допуска — единица нормы учитывает зависимость погрешности размера от самого размера, а также влияние конструктивных, технологических, экономических и метрологических факторов на погрешность размера. Единица допуска определена экспериментально при базовом условии — при обработке валов на круглошлифовальных станках по 6-му квалитету. Таким образом, были учтены конструктивная особенность обрабатываемого элемента (вал и отверстие имеют свои особенности обработки), технологическая особенность процесса круглого наружного шлифования, экономическая особенность (6-й квалитет является экономически наиболее выгодным при круглом наружном шлифовании) и влияние погрешности измерения на результаты измерений размеров (увеличение погрешности с увеличением размера, температурные и другие деформации).
Для размеров до 500 мм единица допуска (в мкм) определяется по формуле

Для размеров свыше 500 до 40000 мм единица допуска

В обеих формулах — средний геометрический размер интервала номинальных
размеров в мм. Вторая формула учитывает резкое возрастание погрешностей больших размеров, связанное с большими силовыми и температурными деформациями.
Таким образом, для каждого интервала номинальных размеров установлено одно числовое значение единицы допуска и оно тем больше, чем больше .
Принцип группирования стандартных допусков линейных размеров
Стандартные (табличные) допуски линейных размеров группируются по квалитетам и классам точности.
Слово «квалитет» в смысловом переводе на русский язык означает «степень точности» ( а поэтому встречающееся в литературе словосочетание «квалитет точности» -неверное, так как получается «степень точности точности»).
Каждый квалитет (степень точности или класс точности) представляет собой совокупность (ряд) допусков одного уровня точности для всех размеров (точность и уровень точности — понятия разные). В данном квалитете для разных интервалов номинальных размеров допуски разные (так как для каждого интервала своя единица допуска), а уровень точности одинаков.
Стандартом установлено 20 квалитетов: 01,0,1,2,… 18. Самые маленькие (жесткие) допуски в 01-м квалитете, самые большие (грубые) — в 18-м. Для металлических деталей используют квалитеты по 17-й. для металлических деталей используют квалитеты по 17-й. Для неметаллических деталей используют 6-й квалитет и долее грубые (для некоторых не металлических деталей есть еще 19-й и 20-й квалитеты). Допуски квалитетов 01 — 4-го используют для размеров особо высокоточных изделий, для калибров (I- 5-й квалитеты).
Квалитеты 4-12-й могут быть использованы для посадок. Квалитет 12-й и более грубые используют для размеров относительно низкой точности (большие допуски). Для металлических деталей, обрабатываемых резанием, не рекомендуется применять квалитеты грубее 14-го.
Допуски до 5-го квалитета вычислены по специальным формулам и правилам. Допуски 5-го и более грубых квалитетов определены по формуле

где — международный (интернациональный) допуск, мкм;
— коэффициент точности (количество единиц допуска, не зависит от размера);
-единица стандартного допуска линейного размера, мкм.
Коэффициент точности определяет уровень точности размеров в данном квалитете:

Чем выше номер квалитета, тем больше коэффициент точности, тем больше допуск размера. Квалитет 6-й является базовым (от него получены допуски всех других квалитетов). При переходе от одного квалитета к следующему более грубому коэффициент точности возрастает на 60% (с некоторым округление), соответственно возрастают и допуски размеров.
Для размеров сопряжений от I до 3150 мм не грубее 8-го квалитета, как правило, рекомендуется размеры валов на один квалитет грубее, чем для размеров отверстий (так-как при прочих равных условиях получить точное отверстие труднее из-за меньшей жесткости, худшего направления и большего износа режущего инструмента, худшего отвода тепла из зоны обработки; при этом повышается срок службы сложных и дорогих инструментов для обработки отверстий за счет увеличения допустимого износа и увеличения количества переточек).
Допуски в квалигетах задаются с точностью до тысячных, а в некоторых случаях до десятитысячных долей миллиметра (до 3-4-й цифры после запятой).
Для размеров относительно низкой точности (II-го квалитета и грубее), повторяющихся на чертеже, допуски и предельные отклонения непосредственно на изображении, как правило, не указывают (размеры с неуказанными предельными отклонениями), а указывают специальной записью в технических требованиях чертежа. Такие допуски называются общими (ГОСТ 30893.1-2002). Для таких размеров установлены классы точности: точный , средний
, грубый
, и очень грубый
. Кроме того могут применяться квалитеты. В классах точности установлены округленные допуски, т. е. без тысячных, а в ряде случаев — без сотых и десятых долей миллиметра. Кроме того, допуски заданы для укрупненных интервалов номинальных размеров. Например, для допусков квалитетов установлены интервалы свыше 6 до 10 мм, свыше от 10 до 18 мм, свыше 18 до 30 мм; а для допусков классов точности эти три интервала входят в один интервал — свыше 6 до 30 мм.
Выбор класса точности проводят с учетом возможностей производства и функциональных требований к детали.
Принцип нормальной температуры
Допуски и предельные отклонения относятся к размерам деталей при температуре +20°С (293,15 К), которая называется нормальной. Поэтому размеры должны проверяться при этой температуре. Если размеры проверяются при другой температуре, то они должны приводиться к нормальной температуре, в противном случае будет нарушаться единство измерений, а результаты измерений не будут достоверными. ГОСТ 8.050-73, устанавливающий нормальные условия выполнения линейных и угловых измерений, содержит рекомендации по допускаемым отклонениям температуры от нормальной, по допускаемым кратковременным колебаниям температуры, но времени выдержки объекта и средства проверки в нормальных условиях и др. В литературе приводятся формулы для расчета температурной погрешности при несоблюдении нормальных температурных условий, однако эти формулы пригодны лишь для деталей простой конфигурации, так как тепловое расширение деталей сложной формы не имеет линейного характера, обычно неизвестно распределение температурных полей и т.д. Поэтому надежнее всего проверке размеров деталей соблюдать нормальные условия или температурную погрешность определять опытным путем.
Для некоторых средств измерений, кроме нормальной температуры, установлен нормальный температурный режим- условная, выраженная в градусах Цельсия разность температур объекта и средства измерения при «идеальных» условиях, т.е. если объект и средство измерения имеют постоянную по объекту температуру, а коэффициенты линейного расширения их материалов равны (РД 50-98-86).
Принцип группирования стандартных полей допусков линейных размеров
Из всех стандартных нолей допусков отобрано оптимальное количество полей, которые рекомендуются для предпочтительного применения (первый ряд полей в стандартах и справочниках отмечен особо — в рамочках, выполненных утолщенными линиями, или отмечен цветом). Это не означает, что их нужно применять. Принцип предпочтительности используется только после того, когда обеспечены конструктивные, эксплуатационные, технологические и экономические требования. Остальные поля, кроме предпочтительных, сгруппированы в 2 ряда — основной и дополнительный. В этом случае, если поля первого (предпочтительного) ряда не удовлетворяют, принимают поля 2-го ряда, если и эти поля не удовлетворяют, применяют ноля 3-го (дополнительного) ряда. Поля дополнительного ряда в таблицах отмечены круглыми скобками. В самом крайнем случае, исключительно редко, по согласованию со службой стандартизации применяют нестандартные поля допусков (такое решение должно быть достаточно обосновано). Этот принцип установлен с целью сокращения слишком большого многообразия применяемых типоразмеров заготовок, деталей, изделий, нерегулируемой оснастки.
Обозначение и указание линейных исполнительных размеров
Стандартом установлены три способа обозначения полей допусков линейных размеров и посадок: цифровое, буквенное, комбинированное (сочетание буквенного и цифрового).
Цифровое обозначение удобно, когда известно, что проверка изделий будет выполняться универсальными средствами измерений (штангенинструментами, микрометрическими инструментами и др.). Его применяют преимущественно в единичном и мелкосерийном производствах. Способ обязателен для нестандартных отклонений, отклонений углов, радиусов, межосевых расстояний и др.
Условное обозначение удобно, когда известно, что проверка размеров изделий выполняться специальными средствами измерений (калибрами, шаблонами, контрольными приспособлениями). Его применяют преимущественно в массовом и крупносерийном производствах.
Комбинированное обозначение удобно, когда неизвестно, какие средства применять для проверки размеров или что будут применять и те, и другие средства.
Рассмотрим основные правила обозначения и указания линейных исполнительных размеров.
Цифровое обозначение. Поле допуска записывают за цифрами номинального размера, например: . Знак цифры верхнего предельного отклонения размера
рекомендуется записывать симметрично верхней границе цифр номинала, а знак и цифры нижнего предельного отклонения — симметрично нижней границе номинала. Знаки и цифры предельных отклонений нужно писать четко, оставляя пробел между цифрами верхнего и нижнего отклонений. Цифры предельных отклонений должны быть меньше цифр номинала.
Если одно из предельных отклонений равно нулю, то его не записывают, например: или
.
Если верхнее и нижнее предельные отклонения равны по величине, но противоположны по знаку, то их записывают, например, так: . Высота цифр отклонений при такой записи равна высоте цифр номинала. Знаки записываются между цифрами номинала и отклонений.
У верхнего и нижнего предельных отклонений количество цифр после запятой справа должно быть одинаковым, например: .
Исполнительные размеры указываются в мм. Если исполнительный размер указывают на чертеже, то единицы измерения не пишут. В текстовых записях (в технических требованиях, примечаниях и др.) единицы измерения указывают обязательно.
Посадку записывают за номинальным размером сопряжения, в виде дроби, в числителе которой указывают поле допуска размера отверстия, а в знаменателе — поле допуска размера вала. Например:
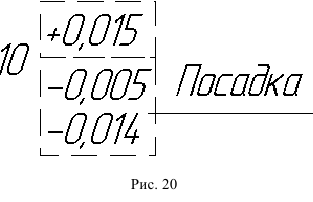
Разделительная черта проводится на уровне середины цифр номинала.
Буквенное обозначение. За цифрами номинального размера записывают обозначение поля допуска размера: сначала обозначение основного отклонения, затем — номер квалитета. Например: (для отверстия высота цифр и букв одинаковая),
(для вала высота цифр одинаковая).
Посадку записывают за цифрами номинального размера сопряжения в виде дроби: в числителе — поле допуска размера отверстия, в знаменателе — поле допуска размера вала. Например:
или
— посадка в системе отверстия,
или
— посадка в системе вала,
или
— посадка комбинированная по системе.
Комбинированное обозначение. После цифр номинального размера записывают сначала буквенное обозначение ноля допуска, а затем, в круглых скобках, цифровое обозначение поля допуска размера, например:


Для сопряжения после цифры номинального размера записывают условное обозначение посадки, за ним в круглых скобках цифровое обозначение посадки. Например:
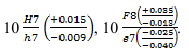
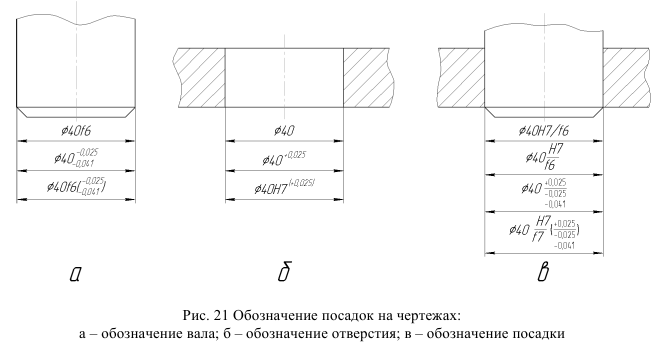
Особенности указании некоторых исполнительных размеров
Для всех размеров должны быть установлены нормы точности. Они могут быть указаны на чертеже, рядом с номинальным размером, или в технических требованиях.
В технических требованиях как правила указывают общие допуски — предельные отклонения, допуски линейных или угловых размеров, указываемые на чертеже или в других технических документах общей записью. Например:
«Общие допуски по ГОСТ 30893.1-» или «ГОСТ 30893.1-
»
«Общие допуски по ГОСТ 30893.1: »
«Общие допуски по ГОСТ 30893.1: »
«Общие допуски по ГОСТ 30893.1: »
Первая запись означает, что все допуски выполнены по среднему классу точности (обозначают либо
, либо
) и все поля допуска симметричны.
Вторая запись означает, что для размеров с неуказанными нолями допусков, если элемент представляет собой отверстие, то его поле допуска выполняется как для основного отверстия, т. е. нижнее предельное отклонение равно нулю, верхнее предельное отклонение со знаком «плюс» и численно равно допуску 14-го квалитета: если элемент -вал, то ноле допуска выполняется как для основного вала, т.е. верхнее предельное отклонение равно нулю, а нижнее — со знаком «минус» и численно равно допуску 14-го квалитета: если элемент относится к прочим, то для него выполняется симметричное поле допуска, т.е. верхнее предельное отклонение со знаком «плюс» и численно равно половине допуска 14-го квалитета, а нижнее со знаком «минус» и числено равно половине допуска 14-го квалитета.
В третьей записи для отверстий и валов установлены те же нормы, что и в первой записи, но и для прочих элементов допуски заданы по ереднему классу точности.
В четвертой все допуски заданы по среднему классу точности.
По таким записям можно определить предельные отклонения для радиусов закругления кромок, фасок и углов, пользуясь специальными таблицами классов точности (ГОСТ 30893.1). Для радиусов закругления кромок и фасок установлены более грубые допуск, чем для других линейных размеров, заданных по классам точности.
При необходимости размер может задаваться с ограничением с одной стороны. Например, или
. В первой записи 10 — одновременно номинальный и наибольший предельный размер; наименьший предельный размер зависит от точности технологической операции по его получения (это не означает, что наименьший предельный размер, может быть, допусти 5 мм; он будет достаточно близким к 10 мм). Во второй записи 10 — номинальный и наименьший предельный размер; наибольший предельный размер зависит от точности технологичеекой операции
. В ряде случаев определенное ограничение таких размеров с другой стороны оговаривается в региональном стандарте или в стандарте предприятия.
Размер, который может быть выполнен приближенным, записывают, например, так: , где 10 — номинальный размер. Это означает, что размер с обеих сторон ограничен технологически (точностью технологической операции). Так задают, например, размер по рифлениям; длину зоны шероховатости поверхности, отличающейся от шероховатости остальной поверхности (на остальной поверхности шероховатость более грубая) и др.
Если на чертеже размер указан в квадратных скобках, то это означает совместную обработку с другой деталью. Если размер указан в круглых скобках, то это означает, что размер должен быть получен в процессе сборки. Справочные размеры отмечают звездочкой (если на чертеже не все размеры справочные).
Методы выбора допусков и посадок
При конструировании применяет расчетные и нерасчетные методы установления допусков и посадок. Расчетный метод применяется, в основном, для наиболее ответственных изделий и сопряжений. В большинстве случаев применяют нерасчетные методы:
- прецедентов или аналогов;
- подобия;
- аналитический.
Метод прецедентов или аналогов заключается в том, что конструктор выбирает посадку и назначает допуск по аналогии с посадкой в надежно работающем узле другой машины. Основная сложность метода — оценка и сопоставление условий работы посадки в проектируемом узле и аналогичном узле, находящемcя, а эксплуатации.
Метод подобии — развитие метода прецедентов. Посадки выбираются на основе рекомендаций отраслевых технических документов и справочников, в которых приведены примеры применения посадок на основе классификации деталей машин по конструктивным и эксплуатационным признакам. Выбор посадок затруднен из-за отсутствия точных количественных условий работы сопряжений.
Общие рекомендации по выбору посадок гладких цилиндрических соединений
Общие рекомендации по выбору посадок:
• в первую очередь следует выбирать посадки для наиболее ответственных и точных сопряжений, определяющих качество узла, например, для узла сначала подшипников, зубчатого колеса на вал, а затем приставочного кольца и крышки подшипников;
• перед выбором посадки необходимо определить:
характер сопряжения (подвижное или неподвижное)
основные конструктивные требования, предъявляемые к сопряжению (величина и характер нагрузок, передаваемых сопряжением, необходимость центрирования сопрягаемых деталей, скорость относительного перемещения деталей, компенсация и огре ш ностей м о нтажа);
• после выбора вида посадки необходимо определить точность выполнения сопряжений. При этом следует учесть, что излишне высокая точность ведет к росту затрат на изготовление.
На выбор квалитета влияют:
• требования точности сопряжения;
• тип выбранной посадки;
• точность, обусловленная эксплуатационным назначением механизма или машины в целом.
Общие рекомендации по выбору квалитетов:
• квалитеты 4-и и 5-й следует применять для особо точных соединений, требующих высокой однородности зазора или натяга (высокоточные зубчатые колеса на валах и оправках в измерительных приборах, приборные подшипники в корпусах и на валах);
• квалитеты 6-и и 7-и необходимо выбирать для ответственных соединений в механизмах, где к посадкам предъявляются высокие требования в отношении определенности натягов и зазоров для обеспечения герметичности соединения, механической прочности сопрягаемых деталей, точности перемещений, плавности хода, а также для обеспечения точной сборки изделий (зубчатые колеса высокой и средней точности на валах, подшипников качения нормальной точности в корпусах и на валах и т.п. );
• квалитеты 8-и и 9-и следует применять для посадок при относительно меньших требованиях к однородности зазоров и натягов, чем 6-й и 7-й квалитеты, и для посадок, обеспечивающих среднюю точность сборки (посадки с большими натягами, опоры скольжения средней точности, посадки с зазором для компенсации погрешностей формы и расположения сопрягаемых поверхностей);
• квалитет 10-и необходимо применять в посадках с зазором, а также в rex же случаях, что и 9-й, если по условиям эксплуатации допускается некоторое увеличение колебания зазоров в соединениях;
• квалитеты 11-и и 12-и применяются в соединениях, где необходимы значительные колебания больших зазоров (грубая сборка).
Эти квалитеты распространены для посадок в неответственных соединениях машин (фланцы, крышки, дистанционные кольца и т.н.).
Характеристика основных посадок дли гладких сопряжений и область применения
Посадки с гарантированным зазором.
Эти посадки применяют в подвижных и неподвижных сопряжениях.
В подвижных сопряжениях одна деталь относительно другой может иметь постоянное или периодическое движение (даже очень редкое движение, например, для регулирования положения детали), образуя пары трения (например ,вал в подшипнике скольжения).
В подвижных соединениях зазор необходим для обеспечения свободы перемещений, размещения слоя смазки (например, в подшипниках скольжения), компенсации отклонений формы и расположения поверхностей, температурных деформаций, погрешностей сборки и т.д.
Посадки имеют гарантированный зазор и предназначены для относительного перемещения деталей сопряжения. Перемещения деталей различны: осевые и вращательные, кратковременные и длительные. Они осуществляются в различных условиях — при различных скоростях, при различной длине сопряжений, с использованием различных смазок, при наличии различного количества опор и при различных температурах.
В неподвижных сопряжениях неподвижность одной детали относительно другой обеспечивается специальными средствами крепления (болтами, винтами, гайками, штифтами, шпонками, сваркой, клеением, за счет натяга в другом сопряжении, за счет передачи крепящего усилия через другие детали).
В сопряжениях нужная точность центрирования (для вращающихся и неподвижных деталей) или направления (для деталей с поступательным движением) обеспечивается за счет соответствующего выбора квалитет. Чем меньше номер квалитета, тем точность центрирования или направления детали выше.
Наименьший предельный зазор зависит от основных отклонений, а наибольший предельный зазор — от квалигета размеров деталей.
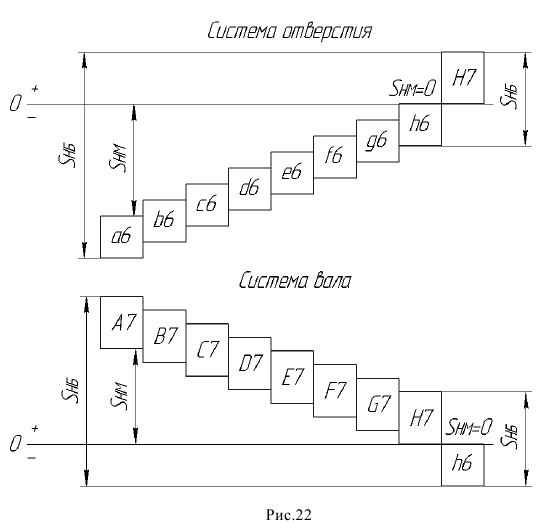
На рис.22 показаны схемы расположения полей допусков размеров с гарантированным зазором в системах отверстия и вала. Здесь и на следующих схемах условно приняты для размеров отверстий 7-й квалитег для размеров валов 6-й квалитег.
Разнообразие условий применения подвижных посадок предопределяют их наибольшее количество по сравнению с другими типами посадок и применение во всех квалитетах с 49-го но 12-й включительно, предназначенных для посадок.
Общие принципы выбора посадок с зазором:
• для осевых перемещений выбираются посадки с большими гарантированными зазорами, чем для вращательных (за исключением особо точных сопряжений).
• Для вращательного вращения зазор выбирается тем больше, чем:
больше скорость вращения;
более вязкая смазка применяется в сопряжении;
больше длина сопряжения и при увеличении количества опор, на которых устанавливается вал;
больше разница температур сопрягаемых деталей или их коэффициентов линейного расширения (при работе сопряжения в условиях повышенных температур);
меньше требования к соосности применяемого сопряжения.
Квалитеты 6,7,8 и 9-й применяются для посадок, в которых детали сопряжения вращаются с большими скоростями ,10,11 и 12-й квалитеты -для тихоходных сопряжений при небольших давлениях и 5-й квалитег для сопряжений, осуществляющих регулярное движение.
В неподвижных соединениях зазор необходим для обеспечения беспрепятственной сборки деталей, что особенно важно при автоматизации сборочных операции. Неподвижность соединения обеспечивается дополнительным креплением штифтами, болтами, шпонками и т.п.
Посадки — скользящие, наименьший зазор в них равен нулю. Они применяются во всем диапазоне точности сопрягаемых размеров (4-12-й квалитеты). Если нет необходимости в более точном центрировании, то в точных квалитетах они применяются как центрирующие посадки. Скользящие посадки применяются для точного медленного продольного перемещения деталей и их медленного вращения (чаще всего при настройках и регулировках).
Посадки высокой точности применяются в неподвижных соединениях при особо высоких требованиях к их центрированию: пиноль в задней бабке токарного станка, измерительные зубчатые колеса на шпинделях зубоизмерительных приборов и др.
Широко распространенная посадка применяется в подвижных соединениях при высоких требованиях к точности центрирования часто разбираемых деталей: центрирующие выступы приспособлений, сменные кондукторные втулки, поршень в цилиндре пневматической дрели, фрезы на оправках, сменные зубчатые колеса на валах.
Посадки и
имеют примерно то же назначение, что и посадка
, но характеризуются более широкими допусками, облегчающими изготовление деталей. Применяютея при большой длине соединения (например, неподвижные соединения зубчатых колес относительно невысокой точности с длинными гладкими валами).
Посадки в более грубых квалитетах (с 9-го по 12-й) предназначены для неподвижных и подвижных соединений малой точности. Применяютея для посадки неответственных шарниров, роликов, муфт, звездочек, шкивов на валы и т.д.
Посадки — движения, обладают наименьшим по сравнению с другими посадками гарантированным зазором. Установлены только в точных квалитетах с 4-го по 7-й. Применяются для главных, чаще всего возвратно — поступательных перемещений, допускают медленное вращение при малых нагрузках.
Посадки применяются в шпинделе делительной головки, в плунжерных и золотниковых парах при перемещении ползуна в направляющих долбежных станков и
Посадки -ходовые, характеризуются умеренным гарантированным зазором. Применяютея для обеспечения свободного вращения в подшипниках скольжения и в посадках общего назначения при легких и средних режимах работы со скоростями не более 150 рад/с и в опорах поступательного перемещения с меньшей точностью центрирования, чем в посадках скользящих и движения.
Посадки и
применяются в точных соединениях: пальцев кривошипов в головках шатунов, в подшипниках скольжения коробок передач различных станков в сопряжениях поршня с цилиндром в компрессорах, в гидравлических прессах и т.п.
Посадки — легкоходовые, обладают значительным гарантированным зазором, который вдвое больше, чем у ходовых посадок. Применяются для свободного вращательного движения при повышенных режимах работы со значительными нагрузками и скоростями свыше 150 рад/с, а также для компенсации погрешности монтажа и деформаций, возникающих во время работы.
Посадки и
применяются для подшипников жидкостного трения, для валов турбогенераторов, больших электромашин, коренных шеек коленчатых валов, центробежных насосов и др.
Посадки — широкоходовые, характеризуются большим гарантированным зазором, который позволяет компенсировать как значительные отклонения расположения сопрягаемых поверхностей и температурные деформации, так и обеспечить свободное перемещение деталей или их регулировку и сборку.
Посадки и
применяются для соединения при невысоких требованиях к точности, для подшипников трансмиссионных валов, холостых шкивов на валах, для поршней в цилиндрах компрессоров.
Посадки переходные
Эти посадки применяют, как правило, в неподвижных, но разборных сопряжениях. Неподвижность сопряжения обеспечивается при помощи болтов, штифтов, шпилек и др. Иногда посадки с основным отклонением посадочного вала применяют в подвижном сопряжении с очень малыми скоростями при условии селективной сборки.
Основное назначение переходных посадок — точное центрирование деталей неподвижных сопряжений. Без специальных крепежных средств они могут обеспечить неподвижность деталей только при сравнительно небольших смещающих силах и крутящих моментах (посадки с основными отклонениями размеров посадочных деталей и
без крепежных средств применять нельзя. Чаще всего эти посадки применяют при наличии специальных средств крепления.
Наилучшее центрирование деталей обеспечивают посадки с основными отклонениями посадочных деталей . В этом случае в действительном сопряжении практически получается небольшой натяг, близкий к нулю.
Для переходных посадок не применяют размеры отверстий грубее 8-го квалитета и размеры валов грубее 7-го квалитета.
На рис. 23 показаны схемы расположения полей допусков размеров отверстий и валов в сопряжениях с переходными посадками в системах отверстия и вала.
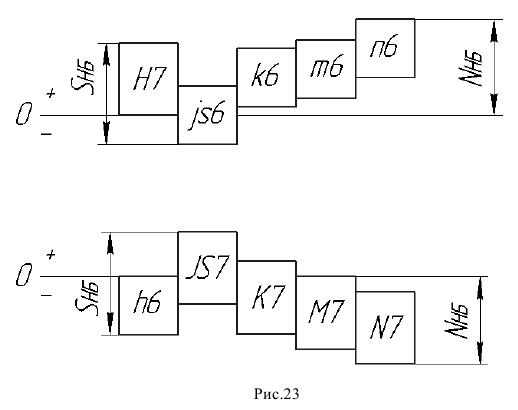
Посадки — плотные, в этих посадках наиболее вероятно получение зазора (вероятность получения натяга
).
Плотные посадки обеспечивают легкую собираемость.
Посадки применяется для сопряжения зубчатых колес шпиндельной головки шлифовальных станков, стаканов подшипников и небольших шкивов с валами.
Посадки — напряженные. Для этих посадок вероятность получения натягов и зазоров примерно равна. Однако из-за влияния отклонений формы, особенно при большой длине соединения, зазоры в большинстве случаев не ощущаются. Небольшой натяг обеспечивает хорошее центрирование деталей. Сборка и разборка производится без значительных усилий , например, при помощи ручных молотков.
Посадка широко применяется для сопряжения зубчатых колес, маховиков, шкивов, муфт с валами, подшипниковых щитков в корпусах крановых электродвигателей.
Посадки — тугие, обеспечивают вероятность получения натяга
. Сборка и разборка осуществляется при значительных условиях. Такие посадки разбираются, как правило, только при ремонтах.
Посадка применяется для сопряжения зубчатых колес, шкивов, маховиков, муфт с валами посадок штифтов, для установки тонкостенных втулок в корпуса, кулачков на распределительном валу.
Посадки -глухие, зазоры при сборке практически не возникают.
Вероятность получения натяга . Сборка и разборка осуществляется при значительных усилиях, применяются прессы, иногда термические методы сборки. Разбираются, как правило, только при капитальном ремонте.
Посадка применяется для сопряжения тяжело нагруженных зубчатых колес, муфт, кривошипов с валами, для установки постоянных кондукторных втулок в корпусах кондукторов, бронзовых венцов червячных колес на чугунных ступицах, штифтов, втулок в корпусах подшипников скольжения и т.п.
Посадки с гарантированным натягом
Эти посадки применяют для неподвижных, как правило, неразборных сопряжений, чаще всего без специальных крепежных средств. Неподвижность одной детали сопряжения относительно другой обеспечивается за счет сил трения и упругих и пластических напряжений, возникающих вследствие деформации контактирующих поверхностей при сборке (запрессовке) деталей. Специальные крепежные средства лишь тогда, когда для обеспечения неподвижности деталей недостаточно натяга ли когда большой натяг недопустим из-за низкой прочности деталей или из-за слишком большой деформируемости деталей.
Для посадок с гарантированным натягом не применяют размеры отверстий грубее 8-го квалитета, размеры валов грубее 7-го квалитега.
Посадку с натягом, как правило, не центрируют.
Эти посадки очень чувствительны к условиям сборки. При одном и том же натяге, но при разных способах и режимах сборки получаются сопряжения с разной прочностью (при прочих равных условиях).
По качеству сопряжений способы сборки можно расположить в следующей последовательности (от лучшего к худшему):
-сборка с глубоким охлаждением вала до температуры -79…196°С (способ наиболее дорогой, применяют для деталей небольших габаритов особо ответственных изделий);
-сборка с небольшим нагревом отверстия в безокислительной среде (для деталей небольших габаритов);
-сборка путем холодной запрессовки вала в отверстие с дополнительным наложением вибраций (для деталей средних размеров);
-сборка путем холодной запрессовки вала в отверстие без наложения вибраций (чаще для деталей малых и средних размеров; неровности шероховатости поверхностей частично срезаются, ослабляя сопряжение);
-сборка с нагревом отверстия до +400″С в окисляющей среде (на воздухе; для деталей средних и больших габаритов; окалина резко снижает прочность сопряжений).
Даже при одном и том же способе сборки, но при разных условиях, получаются разные по прочности сопряжения. Например, при холодной запрессовке вала прочность сопряжения зависит от скорости запрессовки, от применяемой смазки, от наличия у детали заходиых фасок.
Перед массовым применением эти посадки рекомендуется проверять экспериментально в условиях будущего производства и в худших условиях будущей эксплуатации. Для особо ответственных сопряжений конструктор в чертеже должен указать способ и режимы сборки (это одно из исключений, когда в чертеже даются технологические указания).
Посадки с большими натягами применяют для достаточно толстостенных, жестких и прочных деталей, когда невозможно или нецелесообразно применение специальных крепежных средств.
Большими натягами увлекаться не следует, гак как они вызывают большие внутренние напряжения, которые при эксплуатации могут привести к разрушению деталей.
На рис. 24 показаны схемы расположения полей допусков размеров отверстий и валов в сопряжениях с гарантированным натягом в системах отверстия и вала.
Посадки и
— легкопрессовые, имеют минимальный гарантированный натяг, установлены в наиболее точных квалитетах с 4-го по 7-й, обладают высокой степенью центрирования. Применяются для центрирования тяжело нагруженных крупногабаритных деталей, как правило, с дополнительным креплением, когда крутящие моменты или осевые силы малы.
Посадка применяется для сопряжения тяжело нагруженных зубчатых колес, втулок, установочных колец с валами, для установки клапанных седел в гнезда при работе в условиях вибрации тонкостенных втулок и колец в корпуса.
Посадки — прессовые средние, имеют умеренный гарантированный натяг в пределах
. Применяются как с дополнительным креплением, так и без него, установлены для деталей относительно высокой точности 5-7-го квалитетов. При сопряжении возникают, как правило, упругие деформации.
Посадки и
применяются для сопряжения постоянных кондукторных втулок с кондукторными плитами, зубчатых и червячных колес с валами в условиях тяжелых ударных нагрузок с дополнительным креплением, бронзовых зубчатых венцов червячных колес на чугунных ступицах с дополнительным креплением винтами.
Посадки — прессовые тяжелые, имеют большой гарантированный натяг в пределах
. Предназначены для соединений, на которые действуют повышенные, в том числе и динамические нагрузки. Применяются, как правило, без дополнительного крепления соединительных деталей. В сопряжении возникают упруго — пластические и пластические деформации. Детали должны быть проверены на прочность. Сборка осуществляется как методами термических деформаций, так и продольной запрессовки.
Посадки имеют наибольшее распространение из числа тяжелых посадок.
Примеры применения: бурты на валах, вагонные колеса на осях, бронзовые венцы червячных колес на стальных ступицах.
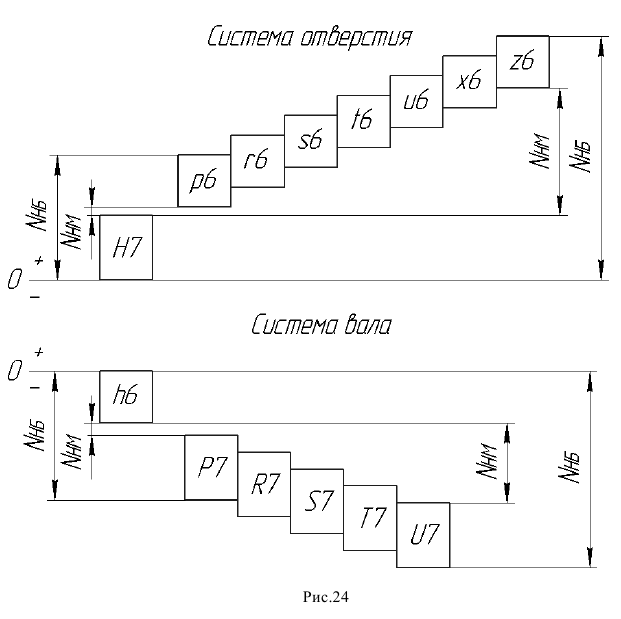
Отклонения, допуски формы и расположения поверхностей и нормы шероховатости поверхности
Допуски формы и расположения поверхностей регламентируются следующими стандартами:
- ГОСТ 24642—81. Допуски формы и расположения поверхностей. Основные термины и определения:
- ГОСТ 24643—81. Числовые значения отклонений формы и взаимного положения;
- ГОСТ 25069—81. Неуказанные допуски формы и расположения поверхностей;
- ГОСТ 2.308—79*. Указание на чертежах допусков формы и расположения поверхностей.
Влияние отклонений формы и расположении поверхностей на качество изделий
Точность геометрических параметров деталей характеризуется не только точностью размеров ее элементов, но и точностью формы и взаимного расположения поверхностей. Отклонения формы и расположения поверхностей возникают в процессе обработки деталей из-за неточности и деформации станка, инструмента и приспособления; деформации обрабатываемого изделия; неравномерности припуска на обработку; неоднородности материала заготовки и т. п.
В подвижных соединениях эти отклонения приводят к уменьшению износостойкости деталей вследствие повышенного удельного давления на выступах неровностей, к нарушению плавности хода, шуму и т. д.
В неподвижных соединениях отклонения формы и расположения поверхностей вызывают неравномерность натяга, вследствие чего снижаются прочность соединения, герметичность и точность центрирования.
В сборках эти погрешности приводят к погрешностям базирования деталей друг относительно друга, деформациям, неравномерным зазорам, что вызывает нарушения нормальной работы отдельных узлов и механизма в целом, например, подшипники качения вееьма чувствительны к отклонениям формы и взаимного расположения посадочных поверхностей.
Отклонения формы и расположения поверхностей снижают технологические показатели изделий. Так, они существенно влияют на точность и трудоемкость сборки и повышают объем пригоночных операций, снижают точность измерения размеров, влияют на точность базирования детали при изготовлении и контроле.
Геометрические параметры деталей. Основные понятия
При анализе точности геометрических параметров деталей оперируют следующими понятиями (рис. 25).
Номинальная поверхность — идеальная поверхность, размеры и форма которой соответствуют заданным номинальным размерам и номинальной форме.
Реальная поверхность — поверхность, ограничивающая деталь и отделяющая ее от окружающей среды.
Профиль — линия пересечения поверхности с плоскостью или с заданной поверхностью (существуют понятия реального и номинального профилей, аналогичные понятиям номинальной и реальной поверхностей).
Нормируемый участок — участок поверхности или линии, к которому относится допуск формы, допуск расположения или соответствующее отклонение. Если нормируемый участок не задан, то допуск или отклонение относится ко всей рассматриваемой поверхности или длине рассматриваемого элемента. Если расположение нормируемого участка не задано, то он может занимать любое расположение в пределах всего элемента.
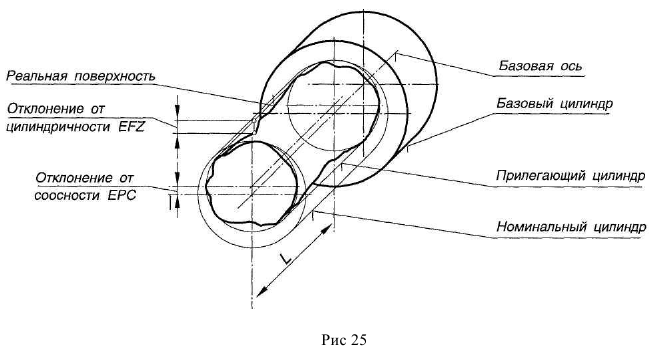
Прилегающая поверхность — поверхность, имеющая форму номинальной поверхности, соприкасающаяся с реальной поверхностью и расположенная вне материала детали так, чтобы отклонение от нее наиболее удаленной точки реальной поверхности в пределах нормируемого участка имело минимальное значение. Прилегающая поверхность применяется в качестве базовой при определении отклонений формы и расположения.
Вместо прилегающего элемента для оценки отклонений формы или расположения допускается использовать в качестве базового элемента средний элемент, имеющий номинальную форму и проведенный методом наименьших квадратов по отношению к реальному.
База — элемент детали или сочетание элементов, по отношению к которым задается допуск расположения рассматриваемого элемента, а также определяются соответствующие отклонения.
Отклонении и допуски формы поверхностей
Отклонением формы называется отклонение формы реального элемента от номинальной формы, оцениваемое наибольшим расстоянием от точек реального элемента по нормали к прилегающему элементу.
Неровности, относящиеся к шероховатости поверхности, в отклонения формы не включаются. При измерении формы влияние шероховатости, как правило, устраняется за счет применения достаточно большого радиуса измерительного наконечника.
Допуском формы называется наибольшее допускаемое значение отклонения формы.
Виды допусков формы
Виды допусков, их обозначение и изображение на чертежах приведены в табл. 1 и 2.
Выбор допусков зависит от конструктивных и технологических требований и, кроме того, связан с допуском размера. Поле допуска размера для сопрягаемых поверхностей ограничивает также и любые отклонения формы на длине соединения. Ни одно из отклонений формы не может превысить допуска размера. Допуски формы назначают только в тех случаях, когда они должны быть меньше допуска размера. Примеры назначения допусков формы, рекомендуемые степени точности и соответствующие им способы обработки указаны в табл. 3.
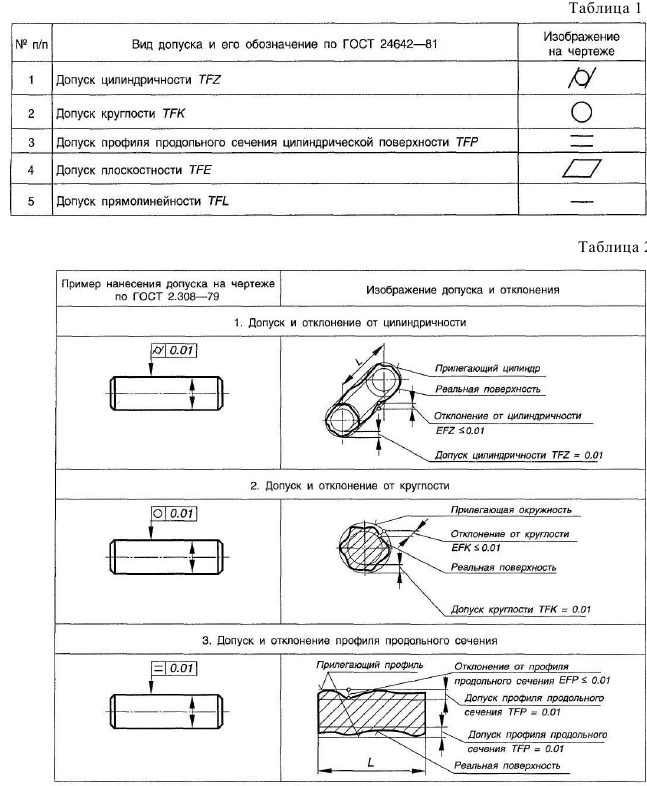
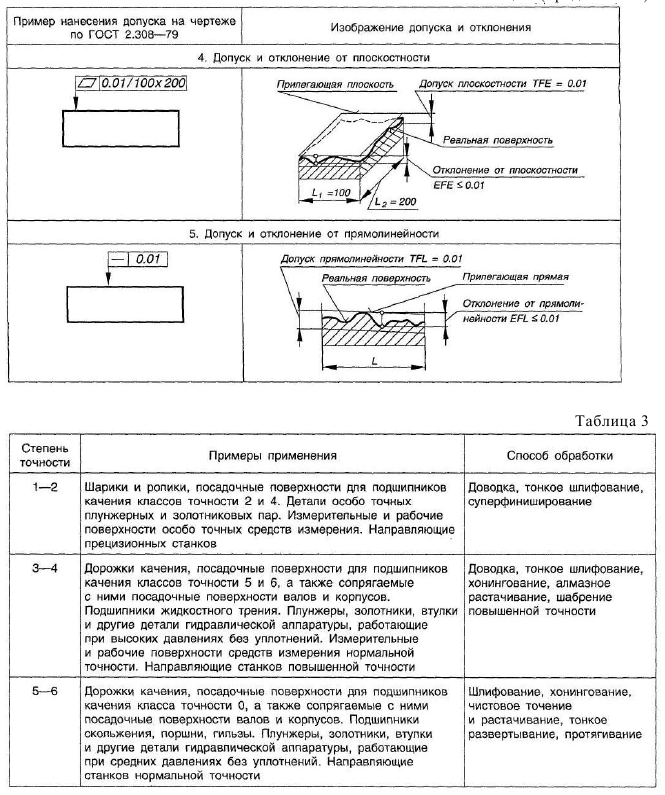
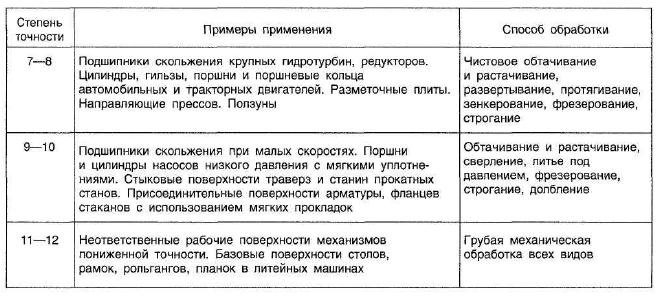
Отклонения и допуски расположении поверхностей
Отклонением расположения называется отклонение реального расположения рассматриваемого элемента от его номинального расположения. Под номинальным понимается расположение, определяемое номинальными линейными и угловыми размерами.
Для оценки точности расположения поверхностей, как правило, назначают базы.
База — элемент детали (или выполняющее ту же функцию сочетание элементов), по отношению к которому задается допуск расположения рассматриваемого элемента, а также определяется соответствующее отклонение.
Допуском расположения называется предел, ограничивающий допускаемое значение отклонения расположения поверхностей.
Поле допуска расположения — область в пространстве или заданной плоскости, внутри которой должен находиться прилегающий элемент или ось, центр, плоскость симметрии в пределах нормируемого участка, ширина или диаметр которой определяется значением допуска, а расположение относительно баз — номинальным расположением рассматриваемого элемента.
Виды допусков расположении
Виды допусков, их обозначение и изображение на чертежах приведены в табл. 4 и 5. В табл. 4 приведены допуски, ограничивающие отклонения расположения между цилиндрическими и плоскими поверхностями.
Оценка величины отклонения расположения производится по расположению прилегающей поверхности, проведенной к реальной поверхности, таким образом, исключаются из рассмотрения отклонения формы.
В графе «Примечание» (см. табл. 4) указаны допуски, которые могут назначаться либо в радиусном, либо в диаметральном выражении. При нанесении этих допусков на чертежах следует указывать соответствующий знак перед числовым значением допуска (см. табл. 5).
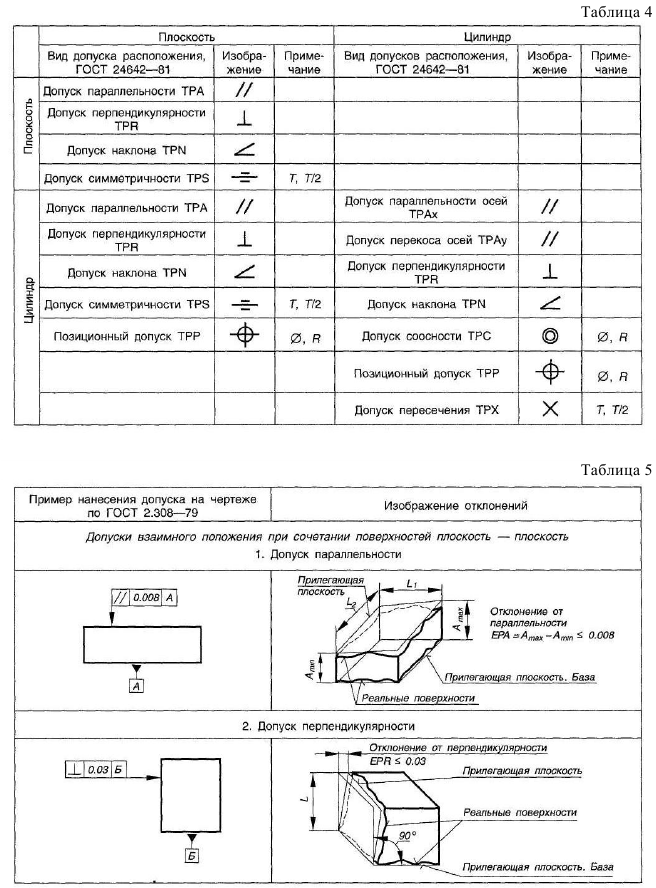

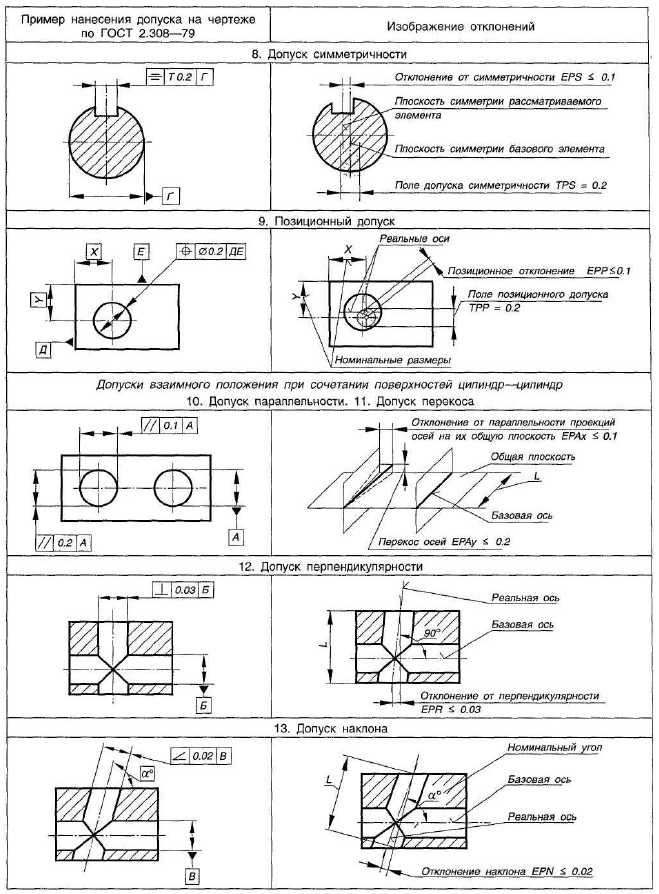
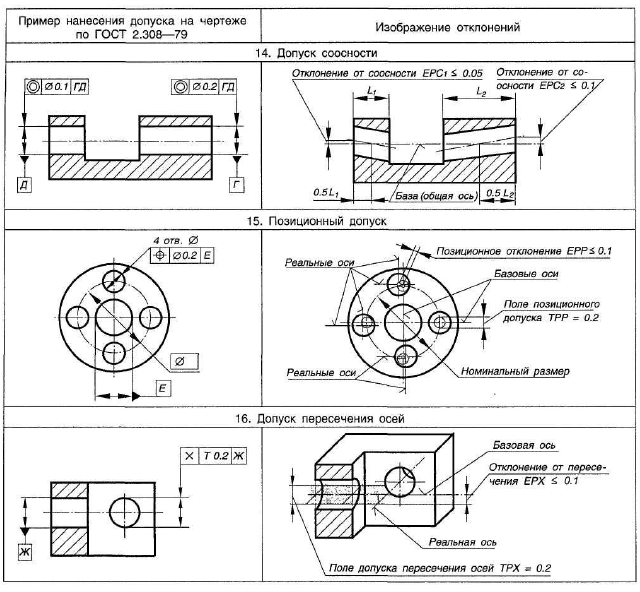
Суммарные отклонении и допуски формы и расположении поверхностей
Суммарным отклонением формы и расположения называется отклонение, являющееся результатом совместного проявления отклонения формы и отклонения расположения рассматриваемой поверхности или рассматриваемого профиля относительно баз.
Поле суммарного допуска формы и расположения — это область в пространстве или на заданной поверхности, внутри которой должны находиться все точки реальной поверхности или реального профиля в пределах нормируемого участка. Это поле имеет заданное номинальное положение относительно баз.
Виды суммарных допусков
Виды допусков, их обозначение и изображение на чертежах приведены в табл. 6. Примеры назначения допусков на чертежах и изображение отклонений приведены в табл. 7.
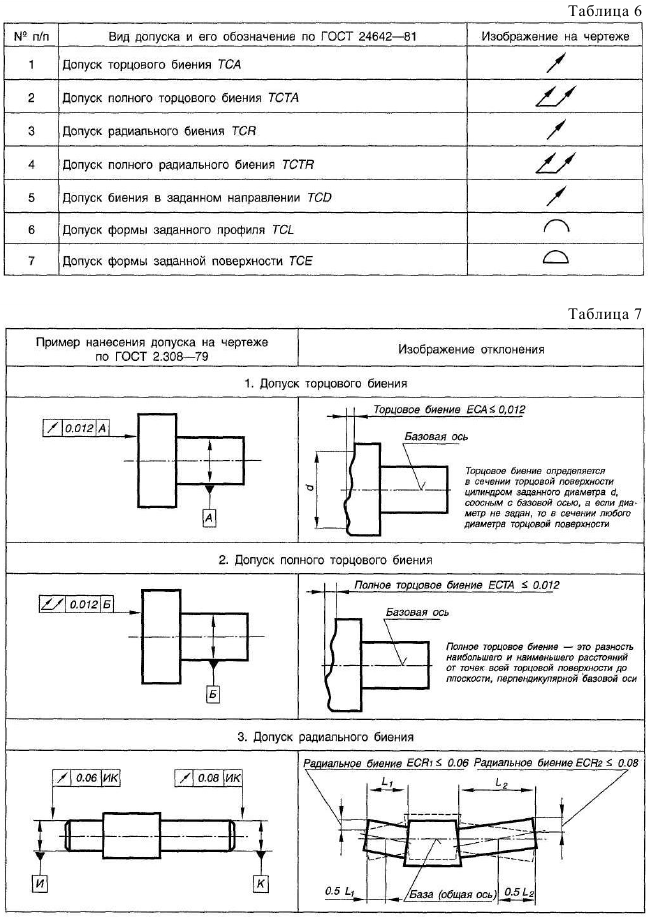
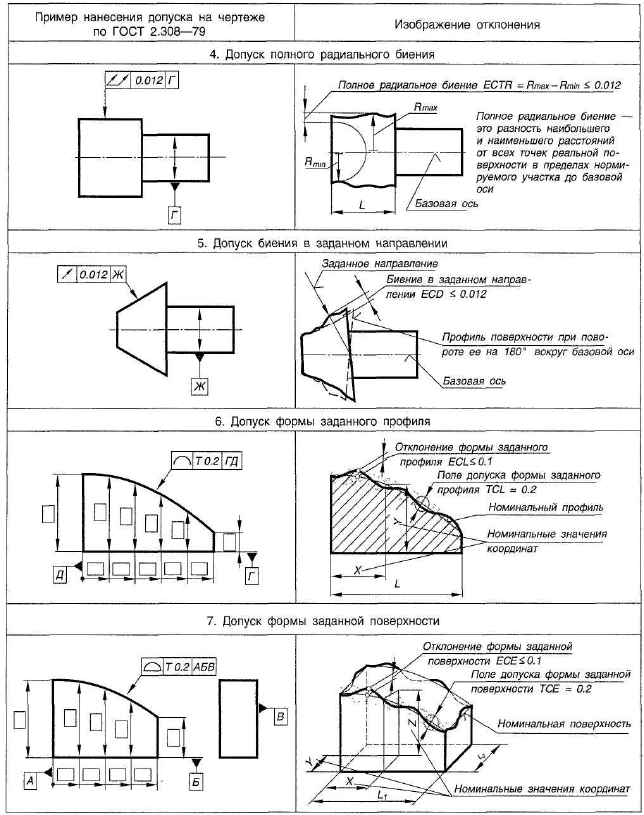
Шероховатость поверхности
Шероховатость поверхности регламентируется следующими стандартами:
- ГОСТ 25142—82. Шероховатость поверхности. Параметры и характеристики;
- ГОСТ 2.309—73*. Шероховатость поверхности. Термины и определения;
- ГОСТ 2789—73*. Обозначение шероховатости поверхностей.
В процессе формообразования деталей на их поверхности появляется шероховатость.
Шероховатость — это ряд чередующихся выступов и впадин сравнительно малых размеров.
Как правило, шероховатость поверхности неизбежна при обработке — это следы обработки, однако волнистость с большим шагом — это результат несовершенства кинематики движения инструмента и, в принципе, ее можно избежать. Название волнистости произошло от ее волнистой природы, возникающей из-за колебаний узлов станка и инструмента при их недостаточной жесткости или балансировке или это результат неправильно движения инструмента, образующего поверхность.
Природа реальной поверхности очень сложна, и ее трудно оценить. Основная проблема, с которой сталкиваются при исследовании поверхностей, заключается в том, что следы механической обработки имеют очень малые размеры.
Итак, шероховатость может быть следом от резца или другого режущего инструмента, копией неровностей форм или штампов, может появляться вследствие вибраций, возникающих при резании, а также в результате действия других факторов.
Влияние шероховатости на работу деталей машин многообразно:
• шероховатость поверхности может нарушать характер сопряжения деталей за счет смятия или интенсивного износа выступов профиля;
• в стыковых соединениях из-за значительной шероховатости снижается жесткость стыков;
• шероховатость поверхности валов разрушает контактирующие с ними различного рода уплотнения;
• неровности, являясь концентраторами напряжений, снижают усталостную прочность деталей;
• шероховатость влияет на герметичность соединений, на качество гальванических и лакокрасочных покрытий;
• шероховатость влияет на точность измерения деталей;
• коррозия металла возникает и распространяется быстрее на грубо обработанных поверхностях и т. п.
Параметры шероховатости поверхности
Шероховатость поверхности оценивается по неровностям профиля (рис. 26), получаемого путем сечения реальной поверхности плоскостью. Для отделения шероховатости поверхности от других неровностей с относительно большими шагами ее рассматривают в пределах базовой длины .
Базой для отсчета отклонений профиля является средняя линия профиля т-т линия, имеющая форму номинального профиля и проведенная так, что в пределах базовой длины среднее квадратичное отклонение профиля до этой линии минимально.
ГОСТ 2789—73* установлены следующие параметры шероховатости (рис. 26).
Среднее арифметическое отклонение профиля — это среднее арифметическое из абсолютных значений отклонений профиля в пределах базовой длины:
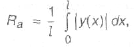
где — базовая длина;
— отклонение профиля (расстояние между любой точкой профиля и базовой линией
).
При дискретном способе обработки профилограммы параметр рассчитывают по формуле;
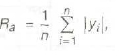
где — измеренные отклонения профиля в дискретных точках;
— число измеренных дискретных отклонений на базовой длине.
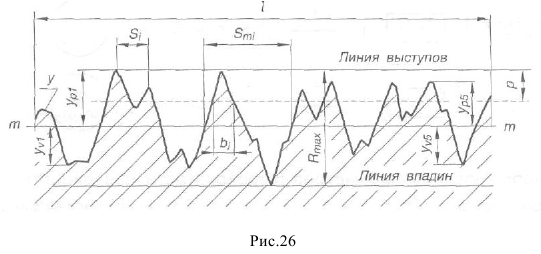
- Высота неровностей профиля по десяти точкам
— сумма средних абсолютных значений высот пяти наибольших выступов профиля и глубин пяти наибольших впадин профиля в пределах базовой длины.
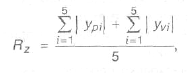
где — высота
-гo наибольшего выступа профиля;
— глубина
-й наибольшей впадины профиля.
- Наибольшая высота неровностей профиля
— расстояние между линией выступов профиля и линией впадин профиля в пределах базовой длины (рис. 26).
- Средний шаг неровностей профиля
— среднее значение шага неровностей профиля в пределах базовой длины (рис. 29).
- Средний шаг местных выступов
— среднее значение шагов местных выступов профиля, находящихся в пределах базовой длины (см. рис. 26).
- Относительная опорная длина профиля
— отношение опорной длины профиля к базовой длине:
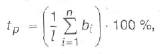
где — опорная длина профиля (сумма длин отрезков, отсекаемых на заданном уровне
в материале профиля линией, эквидистантной средней линии в пределах базовой длины).
Кроме перечисленных шести количественных параметров стандартом установлены два качественных параметра.
- Вид обработки. Указывается в том случае, когда шероховатость поверхности следует получить только определенным способом.
- Тип направлений неровностей. Выбирается из табл. 8. Указывается только в ответственных случаях, когда это необходимо по условиям работы детали или сопряжения.
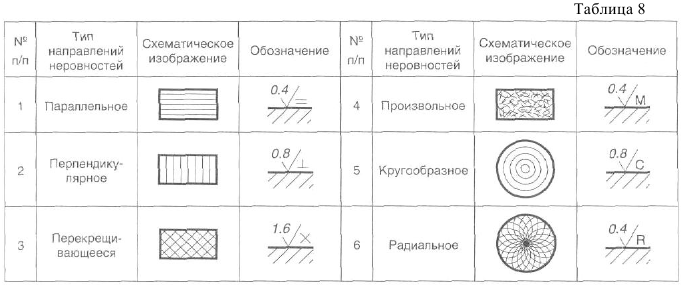
Гладкие калибры
Понятие о калибре
Слово «калибр» произошло от французского «calibre», обозначавшего диаметр канала ствола пушки, ружья, пистолета, ядра или пули.
Калибр — это специальное техническое бесшкальное средство измерений (мера), служащее для альтернативной проверки годности размеров, формы и расположения поверхностей при техническом контроле изделий.
Калибры не используются для арбитражной перепроверки изделий. Арбитражную перепроверку ведут универсальными средствами измерений.
При проверке изделия калибром не определяют числового значения размера величины элемента, а проверяют лишь его годность («годен — не годен», брак «плюс» или «минус», исправимый или неисправимый брак; понятия «исправимый» и «неисправимый» брак — условны). При помощи калибров также разделяют элементы изделий на группы сортировки в пределах нолей допусков размеров этих элементов (под селективную сборку изделий).
Калибры изготовляют для контроля отверстий, валов, глубин, уступов, расстояний между поверхностями и осями и т.д.
Калибры чаще применяют в массовом и крупносерийном производствах, где применение их наиболее экономично.
Преимущества калибров перед универсальными средствами измерений:
- • более высокая производительность контроля;
- • простота применения;
- • простота конструкций, относительная лёгкость изготовления, сравнительно невысокая стоимость;
- • более высокая износостойкость;
- • контроль полными калибрами приближен к условиям сборки изделий;
- • возможность контроля малых отверстий, для которых нет достаточно простых и надёжных универсальных СИ;
- • возможность механизации и автоматизации контроля (автоматизированный контроль применяют только для изделий небольших габаритов и достаточно простой формы).
Применение калибров имеет следующие недостатки:
- на результаты контроля существенно влияют субъективные особенности контролёра, т.е. его квалификация, соблюдение правил контроля, тщательность контроля (например, если калибр не снабжён специальным устройством для ограничения и обеспечения постоянства измерительного усилия, то погрешность контроля резко возрастает, особенно, при контроле размеров более 180 мм точнее 6-8 квалитетов, а также при недостаточной жёсткости конструкции калибра или изделия);
- плохо выявляются отклонения формы в пределах поля допуска размера элемента изделия, особенно, если проходной калибр неполный или имеет меньшую длину, чем длина проверяемого элемента;
- нельзя использовать калибры для проверки отклонений формы и расположения поверхностей, если они должны быть меньше допуска размера;
- при допустимом выходе поля допуска размера на износ проходного предельного калибра за пределы ноля допуска размера проверяемого элемента изделия (за Анм у отверстия и за Внб у вала), особенно, если пробка и скоба одновременно близки к предельному износу, погрешность контроля увеличивается, искажается допуск посадки сопрягаемых деталей (возможен небольшой натяг в посадке с Shm = 0, но вероятность его очень мала);
- несколько искажается допуск посадки сопрягаемых деталей, если неироходные пробка имеет наибольший предельный размер, а скоба — наименьший (Nhm уменьшается, Shm — увеличивается);
- для грубых квалитетов применение новых калибров может сократить наименьший производственный допуск на 10-40%;
- отсутствие числовых данных;
- нельзя проверять легкодеформируемые детали.
Калибры применяют для размеров от 0,1 до 3150 мм:
- для размеров до 500 мм в квалитетах от 6-8 до 17,
- для размеров свыше 500 мм — в квалитетах 12-17.
Для контроля размеров точнее 6 квалитета применение калибров не рекомендуется.
Основные требования, предъявляемые к калибрам:
• точность (достигается соответствующей обработкой рабочих поверхностей и точностью применяемых СИ для их контроля);
• износостойкость, твёрдость и качество рабочих поверхностей (достигаются закалкой, армированием твёрдым сплавом, хромированием и т.д.); хромирование повышает износостойкость в 3 — 4 раза, а армирование — в 35 — 40 раз);
• стабильность рабочих поверхностей (достигается снятием внутренних напряжений при искусственном старении);
- • наибольшая жёсткость при наименьшей массе (достигается за счёт конструктивных решений);
- • коррозионная стойкость (достигается хромированием с последующей доводкой рабочих поверхностей и оксидированием нерабочих).
- Контроль калибрами может быть:
- • поэлементным (каждый элемент изделия проверяется отдельно);
- • комплексным (несколько элементов проверяются одновременно);
- • ручным;
- • механизированным;
- • автоматизированным;
- • автоматическим.
Нормальные и предельные калибры
Нормальный калибр контролирует номинальный контур (размер) элемента изделия. Заключение о годности делается по ощущениям руки (туго — плотно — свободно входит в изделие), по визуальной оценке величины зазора между калибром и элементом изделия (на просвет), по визуальной оценке пятна контакта (на краску).
Нормальные калибры изготавливают в виде цилиндрических и конусных пробок, втулок, колец, скоб, вставок, шаблонов, лекал, щупов, пройм, вкладышей. В основном производстве эти калибры применяют редко. Чаще их применяют в инструментальном производстве, например, при изготовлении пресс-форм.
Предельные калибры проверяют предельные контуры (размеры) элемента изделия (наибольший и наименьший предельные контуры).
Предельные калибры изготовляют в виде цилиндрических или плоскопараллельных пробок, скоб или колец (последние только для строгого контроля отклонений формы).
Калибры могут быть гладкими, ступенчатыми и сложной формы (например, для контроля резьб, шлицев и др.).
Калибры гладкие предельные дли контроля цилиндрических и нлосконараллельных элементов изделий
Принцип применения предельных калибров
Для контроля каждого элемента изделия необходимы два калибра: проходной (ПР) и непроходной (НЕ).
Проходной калибр для размеров 1 мм и более должен проходить в отверстие или по валу под действием собственной силы тяжести или усилия, примерно равного ей, но не менее (100 грамм), а непроходной не должен проходить (допускается небольшое «закусывание» непроходного калибра — до 1,5 мм от фаски, в отдельных случаях до 0,5 длины его рабочей части). Для калибров с размерами менее 1 мм усилие измерения не должно превышать
Рабочую часть проходного калибра желательно смазывать техническим вазелином, с последующей протиркой насухо (без промывки).
Проходной калибр проверяет начало поля допуска элемента изделия, непроходной -его конец (рис. 27, 28).
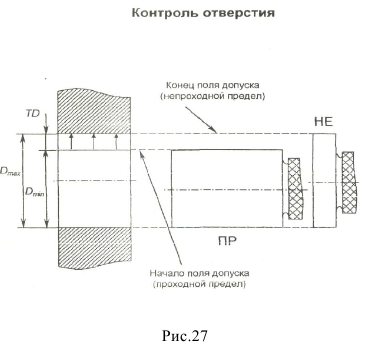
Если пробка ПР не проходит в отверстие, это означает, что действительный контур (размер) отверстия меньше наименьшего предельного контура (размера) отверстия, т.е. имеет место брак «минус» (отверстие меньше, чем нужно). Чаще всего, это брак исправимый. Если пробка НЕ проходит в отверстие, это означает, что действительный контур (размер) отверстия больше наибольшего предельного контура (размера) его, т.е. имеет место брак «плюс» (отверстие больше, чем нужно, «провалено»). Чаще всего, это -неисправимый брак (окончательный).
Если скоба (кольцо) ПР не проходит по валу, это означает, что действительный контур (размер) вала больше наибольшего предельного контура (размера) вала, т.е. имеет место брак «плюс» (вал больше, чем нужно). Чаще всего, это брак исправимый. Если скоба (кольцо) НЕ проходит по валу, это означает, что действительный контур (размер) вала меньше наименьшего предельного контура (размера) вала, т.е. имеет место брак «минус» (вал меньше, чем нужно, «провален»). Чаще всего, это неисправимый брак (окончательный).
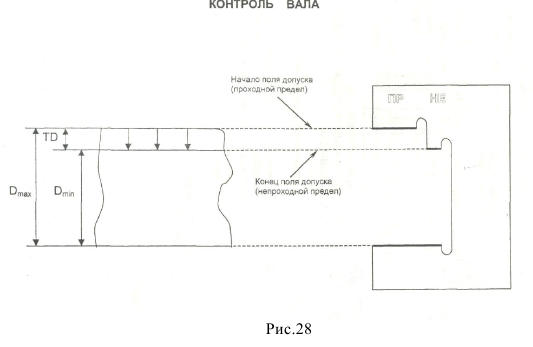
Принципы конструирования калибров
Калибры могут иметь разную конструкцию. Калибры подразделяются, прежде всего, на полные и неполные. Полный калибр в поперечном сечении рабочей части имеет ту же форму, что и проверяемый элемент изделия. Неполный калибр в поперечном сечении рабочей части имеет усечённую форму. К полным калибрам относят полные пробки, шайбы, кольца и втулки. К неполным — неполные пробки и скобы (рис. 29).
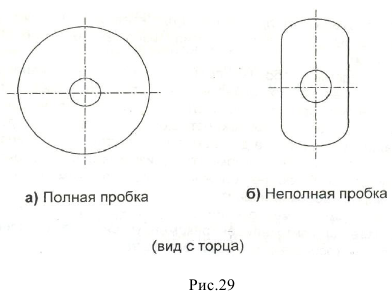
В полных калибрах соблюдается принцип подобия (Тэйлора). Калибры НЕ неполные, например, листовые пробки и скобы, а также штихмасы лучше выявляют отклонения формы деталей, чем полные (если отклонения формы заданы в пределах допуска размера). Калибры ПР полные лучше выявляют форму, чем неполные.
Для выявления отклонений формы, особенно, если проверяемая поверхность достаточно протяжённая, деталь нужно проверять калибром с двух сторон и, если калибр неполный, то и в нескольких сечениях (до 9 сечений).
При изготовлении калибры, для стабилизации внутренних напряжений, подвергаются искусственному старению путём нагрева до 130… 150°С в течение 2…3 часов между предварительным и окончательным шлифованием.
Классификация гладких предельных калибров по назначению
Эти калибры подразделяются на рабочие и контрольные:
- рабочие пробки и скобы-кольца ПР и НЕ для контроля деталей рабочими и контролёрами;
- контрольные пробки (шайбы) для контроля рабочих нерегулируемых скоб и установки регулируемых скоб на размер:
- К-ПР — контрольный проходной для контроля новой рабочей скобы ПР;
- К-НЕ — контрольный проходной для контроля новой рабочей скобы НЕ;
- К-И — контрольный непроходной для контроля полного износа рабочей скобы ПР (для изъятия изношенных скоб ПР из эксплуатации).
Для контроля рабочих пробок контрольные калибры не изготовляют, так как их экономичнее проверять универсальными измерительными средствами. Дело в том, что для измерений наружных размеров (т.е. пробок) есть достаточно простые и дешёвые универсальные средства, а для измерений внутренних размеров (т.е. скоб и колец) таких средств нет. Кроме того, изготовление высокоточных контркалибров-скоб более сложно и дорого, чем изготовление контркалибров-пробок или шайб.
В единичном и мелкосерийном производствах, а также при ремонте изделий, контркалибры рекомендуется заменять концевыми мерами длины (особенно для размеров до 180 мм).
В отечественной промышленности имеют ограниченное применение ещё и приёмные калибры П-ПР и П-НЕ для контроля деталей представителями Заказчика (иногда и работниками ОТК). Эти калибры не изготовляют специально, а отбирают из частично изношенных рабочих калибров ПР и соответственно перемаркировываюг (раньше изготовляли по требованию Заказчика). В настоящее время вместо калибров П-ПР, в спорных ситуациях, рекомендуется использовать концевые меры длины или универсальные СИ.
Допуски гладких предельных калибров
Допуски размеров рабочих калибров в 5-15 раз меньше допусков размеров контролируемых деталей. Допуски размеров контрольных калибров в 1,5-3 раза меньше допусков рабочих калибров.
В качестве исполнительного размера предельной пробки принимают её наибольший предельный размер (он же её номинальный размер) с отрицательным отклонением, а предельной скобы — её наименьший предельный размер (он же её номинальный размер) с положительным отклонением, т.е. отклонения задают в тело калибра, как у основных отверстия и вала.
Рабочий проходной калибр в процессе эксплуатации изнашивается, а непроходной -нет, поэтому калибр ПР, кроме допуска на изготовление, имеет допуск на износ. Поле допуска на износ откладывается or конца поля допуска на изготовление калибра в направлении его износа, причём для 6-8 квалитетов поля износа выходят за линию проходного предела размера изделия, чтобы слишком не ужесточать допуск изделия, а для квалитетов 9-17 — не выходят. Поле допуска на изготовление калибра НЕ расположено симметрично относительно соответствующего предельного размера изделия, а поэтому на 1/2 выходит за линию непроходного предела размера изделия.
Возможно эта страница вам будет полезна:
Заказать работу по метрологии |
Сопряжения с подшипниками качения
Подшипники, являясь опорами для подвижных частей, определяют их положение в механизме и несут значительные нагрузки.
Подшипники качения имеют следующие основные преимущества по сравнению с подшинниками скольжения:
- обеспечивают более точное центрирование вала;
- имеют более низкий коэффициент трения;
- имеют небольшие осевые размеры.
К недостаткам подшипников качения можно отнести:
- повышенную чувствительность к неточностям монтажа и установки;
- жесткость работы, отсутствие демпфирования колебаний нагрузки;
- относительно большие радиальные размеры.
Классы точности подшипников качении
Долговечность подшипников качения определяется величиной и характером нагрузки, точностью изготовления, правильной посадкой на вал и в отверстие корпуса, качеством монтажа.
В зависимости от точности изготовления и сборки для различных типов подшипников установлены следующие классы точности (табл. 9).
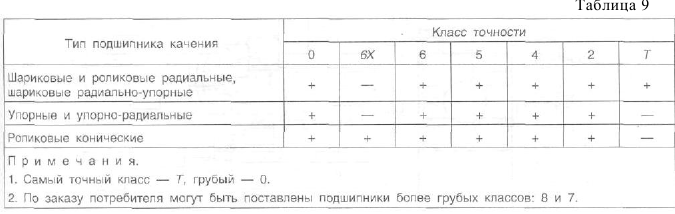
Классы точности определяют:
- • допуски размеров, формы и взаимного положения элементов деталей подшипника качения (дорожек качения, тел качения и т. д.);
- • допуски размеров и формы посадочных поверхностей наружного и внутреннего колец подшипника качения;
- • допустимые значения параметров, характеризующих точность вращения подшипников.
Дополнительные технические требования к подшипникам качения устанавливаются тремя категориями: .
В табл. 10 указаны категории и классы точности подшипников, для которых они предусмотрены, и те дополнительные технические требования, которые они устанавливают.
Обозначение подшипников категорий и 6:
, где
— категория; 1 — ряд момента трения; 2 — группа радиального зазора; 5 — класс точности; 205 — номер подшипника.
Обозначение подшипников категории (в обозначении категорию
не указывают):
6-205, где 6 — класс точности; 205 — номер подшипника.
205, где 205 — номер подшипника; 0 — класс точности (в обозначении 0 класс не указывают).
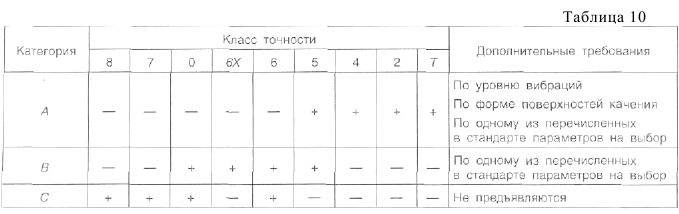
Назначение нолей допусков дли вала и отверстии корпуса при установке подшипников качении
На рис. 30 показана схема расположения рекомендуемых полей допусков посадочных размеров для подшипников классов точности 0 и 6.
Из схемы видно, что поля допусков для внутреннего и наружного колец подшипника качения расположены одинаково относительно нулевой линии, верхнее отклонение равно 0, нижнее — отрицательное.
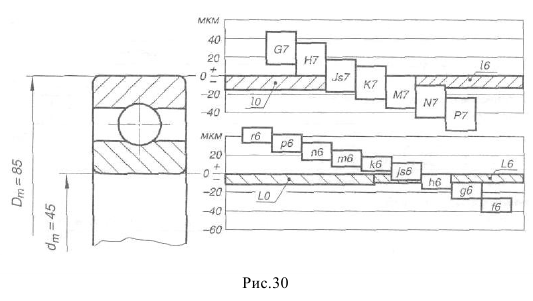
Валы с полями допусков при сопряжении с внутренним кольцом подшипника обеспечивают посадки с натягом.
Вследствие повышенных требований к форме посадочных поверхностей подшипников стандартом устанавливаются следующие поля допусков.
- Поля допусков на средние диаметры
и
, которые ограничивают значения средних диаметров колец, равных
и
, где
выбираются из ряда измерений в разных сечениях соответственно наружного и внутреннего диаметров. Обозначаются поля допусков, например у подшипников нулевого класса —
для наружного кольца и
— для отверстия внутреннего кольца (см. рис. 33).
- Поля допусков для ограничения самих
значения которых больше на величину допустимой погрешности формы.
При выборе полей допусков на вал и отверстие под внутреннее и наружное кольца подшипника необходимо учитывать следующее:
- • класс точности подшипника качения;
- • вид нагружения колец подшипника;
- • тип подшипника;
- • режим работы подшипника;
- • геометрические размеры подшипника.
Возможно эта страница вам будет полезна:
Нормирование точности и технические измерения |
Влияние класса точности подшипника качения на выбор посадок
Как видно из схемы нолей допусков (см. рис. 30), для подшипников классов точности 0 и б рекомендуемый набор полей допусков посадочных поверхностей одинаков. Для более высоких классов точности подшипников качения набор полей допусков посадочных поверхностей несколько изменяется, в частности, применяются поля допусков более точных квалитетов.
Влияние вида нагружения колец подшипника на выбор посадок
Вид нагружения кольца подшипника качения существенно влияет на выбор его посадки. Рассмотрим типовые схемы механизмов и особенности работы подшипников в них.
Первая типовая схема (рис. 31).
Внутренние кольца подшипников вращаются вместе с валом, наружные кольца, установленные в корпусе, неподвижны. Радиальная нагрузка постоянна по величине и не меняет своего положения относительно корпуса (рис. 31, а)
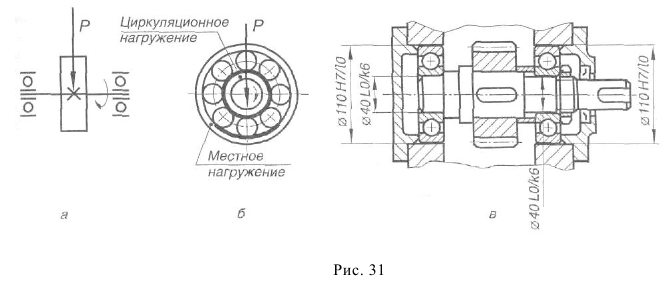
В этом случае внутреннее кольцо воспринимает радиальную нагрузку последовательно всей окружностью дорожки качения, такой вид нагружения кольца называется циркуляционным Наружное кольцо подшипника воспринимает радиальную нагрузку лишь ограниченным участком окружности дорожки качения, такой характер нагружения кольца называется местным (рис. 31,6).
Дорожки качения внутренних колец подшипников изнашиваются равномерно, а наружных — только на ограниченном участке.
При назначении посадок подшипников качения существует правило: кольца, имеющие местное нагружение, устанавливаются с возможностью их проворота с целью более равномерного износа дорожек качения; при циркуляционном нагружении, напротив, кольца сажают по более плотным посадкам.
Рекомендуемые посадки для подшипников классов точности 0 и 6 приведены в табл. 11.
Пример выбора посадок (рис. 31, в).
Вторая типовая схема (рис. 32). Наружные кольца подшипников вращаются вместе с зубчатым колесом. Внутренние кольца подшипников, посаженные на ось, остаются неподвижными относительно корпуса. Радиальная нагрузка Р постоянна по величине и не меняет своего положения относительно корпуса (рис. 32, а).
В этом случае наружное кольцо воспринимает радиальную нагрузку Р последовательно всей окружностью дорожки качения, т. е. имеет циркуляционное нагружение. Внутреннее кольцо подшипника воспринимает радиальную нагрузку лишь ограниченным участком окружности дорожки качения, т. е. имеет местное нагружение (рис. 32, 6).
Рекомендуемые посадки для подшипников 0 и 6 классов точности приведены в табл. 11.
Пример выбора посадок см. рис. 32, в.
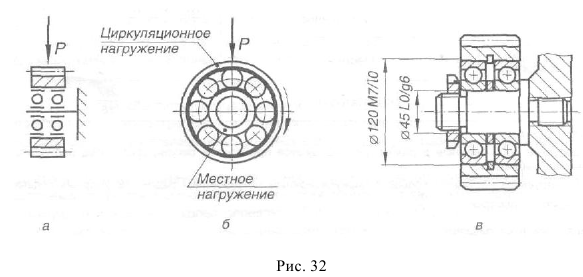
Третья типовая схема (рис. 33). Внутренние кольца подшипников вращаются вместе с валом, наружные кольца, установленные в корпусе, неподвижны.
На кольца действуют две радиальные нагрузки, одна постоянна по величине и по направлению , другая, центробежная
, вращающаяся вместе с валом (рис. 33, а).
Равнодействующая сил и
совершает периодическое колебательное движение, симметричное относительно направления действия силы
. На рис. 33, б штриховыми линиями показано последовательное положение эпюры нагружения наружного кольца подшипника на ограниченном участке дорожки качения, которая смещается справа налево и меняется но величине, такой режим нагружения кольца называется колебательным.
Внутреннее кольцо воспринимает суммарную радиальную нагрузку последовательно всей окружностью дорожки качения, т. е. имеет циркуляционное нагружен ие.
Рекомендуемые посадки приведены в табл. 11. Пример выбора посадок см. рис. 33, в.
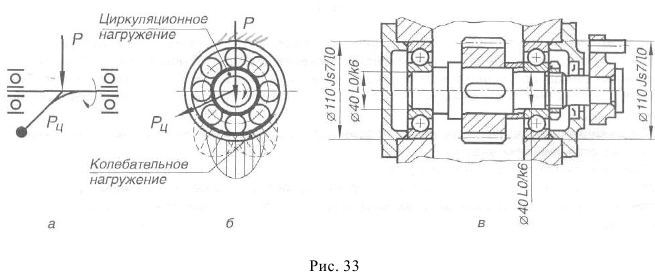
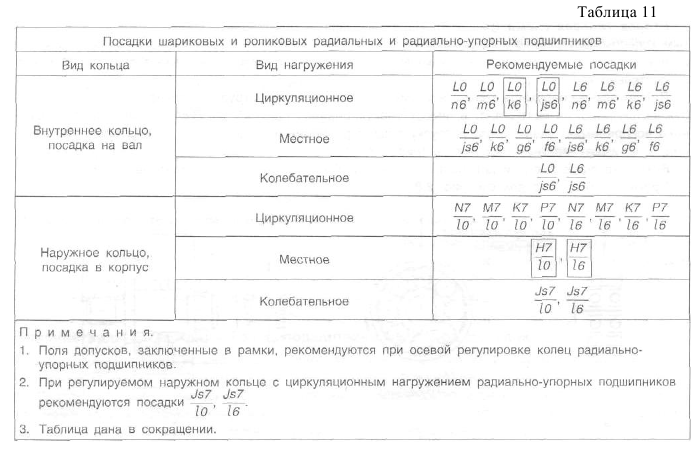
Контрольная работа №1 Выбор допусков размеров и посадок гладких соединений, допусков формы, норм шероховатости поверхностей
Цель работы.
Закрепление знаний по соответствующим разделам дисциплины. Приобретение навыков в нормировании точности деталей.
Содержание и последовательность выполнении работы.
Для каждого из соединений, предусмотренных номером и вариантом задания:
1) Выбрать и обосновать:
- а. тип посадки (с зазором, с натягом, переходная),
- б. систему посадки (система отверстия, система вала, комбинированная),
- в. основные отклонения размеров отверстия и вала,
- г. квалитеты размеров отверстия и вала (для колец подшипников качения класс точности подшипника),
- д. виды допусков формы отверстия и вала (кроме колец подшипников качения),
- е. нормы шероховатости отверстия и вала (кроме колец подшипников качения).
2) Определить числовые значения предельных отклонений и допусков размеров.
3) Определить числовые значения допусков формы и норм шероховатости (Ra).
4) Выполнить в произвольном масштабе условные эскизы соединения, отдельно отверстия и вала (подшипник качения показать упрощенно по ЕСКД):
- а.указать номера деталей по чертежу задания (если номера нет, указать наименование детали),
- б. указать исполнительные размеры (номинальные размеры и поля допусков) соединения комбинированным способом обозначения, исполнительные размеры отверстия и вала — цифровым способом обозначением,
- в.указать допуски формы отверстия и вала, если они меньше допусков размеров (кроме колец подшипников качения),
- г. указать нормы среднего арифметического отклонения профиля шероховатости (Ra) отверстия и вала (кроме колец подшипников качения).
5) Выполнить в произвольном масштабе графическое изображение исполнительного размера соединения (схему расположения полей допусков отверстия и вала):
- а. нанести условные обозначения полей допусков,
- б. указать числовое значение номинального размера (в мм),
- в. указать числовые значения предельных отклонений (в мкм),
- г. показать предельные зазоры или натяги,
- д. заштриховать поля допусков из предпочтительного ряда (кроме колец подшипников качения).
6) Записать формулы предельных зазоров или натягов, допуска посадки (в том числе проверочную), выполнить числовую подстановку и записать ответ.
Выбор и обоснование тина посадки
Приступая к работе, необходимо изучить соответствующий теоретический материал по конспекту лекций или учебнику и рекомендации справочника. Затем внимательно ознакомиться с кратким описанием и чертежом изделия, чтобы получить представления о назначении изделия, взаимодействии его узлов и деталей, условиях работы.
Если соединение подвижное, т. е. одна деталь перемещается относительно другой в процессе работы изделия, то выбирается посадка с зазором. Посадка с зазором выбирается также, если соединение неподвижное, детали надежно закреплены специальными крепежными средствами (болтами, гайками и т.д.), нет необходимости в точном центрировании деталей за счет посадки.
Если соединение неподвижное, необходимо точное центрирование деталей за счет посадки, смещающие силы сравнительно малы или есть надежное специальное крепление деталей, то, как правило, выбирается переходная посадка. Переходная посадка выбирается также, если соединение неподвижное, точного центрирования деталей не требуется, специальное крепление отсутствует, смещающие силы сравнительно малы.
Если соединение неподвижное, нет необходимости в точном центрировании деталей, специальное крепление отсутствует или недостаточно, смещающие силы сравнительно велики, то выбирается посадка с натягом.
В сопряжении с радиальным или радиально-упорным подшипником качения принять нормальный режим работы подшипнике. В этом случае тип посадки зависит, в основном, от вида нагруження соответствующего (наружного или внутреннего) кольца.
При циркуляционном нагружении внутреннего кольца выбирают, как правило, посадку с натягом, при циркуляционном нагружении наружного кольца — переходную посадку.
При местном нагружении внутреннего кольца выбирают переходную посадку, при местном нагружении наружного кольца — посадку с зазором.
При колебательном нагружении кольца выбирают переходную посадку. Переходную посадку также выбирают для сопряжения с тугим кольцом упорного подшипника.
Примеры обоснования типа посадки:
«Принимаю посадку с зазором, т.к. сопряжение подвижное»;
«Принимаю переходную посадку, т.к. сопряжение неподвижное, необходимо точное центрирование деталей, специальное крепление достаточное»;
«Принимаю посадку с натягом, т.к. сопряжение неподвижное, специальное крепление отсутствует, смещающие силы сравнительно велики»;
«Принимаю посадку с натягом, т.к. внутреннее кольцо подшипника качения испытывает циркуляционное нагружение, задан нормальный режим работы подшипника, подшипник радиальный».
Выбор и обоснование системы
В обычном гладком соединении систему вала в основном выбирают:
- если гладкий вал или участок вала входит в несколько сопряжений с разными посадками;
- если валы можно использовать для точной посадки без дополнительной механической обработки;
- если гладкий высокоточный вал (размер вала точнее 6-го квалитета) изготавливают для неизвестного (обезличенного) потребителя (т.е. когда неизвестно под какую посадку пойдет вал), например, в сопряжениях с наружными кольцами подшипников качения.
Если условий для выбора системы вала нет, то выбирают систему отверстия как-более экономичную при прочих условиях.
Для сопряжений с радиальным и раднально-упорным подшипниками качения система установлена стандартом: с внутренним кольцом — система отверстия, с наружным кольцом — система вала. Для сопряжений с тугим кольцом упорного подшипника качения: с валом — система отверстия, с корпусом — система вала.
В ряде случаев применяют комбинированную по системе посадку (отверстие в системе вала, вал в системе отверстия), например, в сопряжении корпуса подшипника качения с крышкой.
Примеры обоснования системы:
«Принимаю систему отверстия, т.к. условий для системы вала нет, а при прочих условиях система отверстия экономичнее»;
«Принимаю систему вала, т.к. гладкий участок вала входит в J сопряжения с рази ыми по с а дками »;
«Принимаю систему отверстия, т.к. сопряжение с внутренним кольцом подшипника качения по стандарту выполняется в этой системе»;
«Принимаю комбинированную по системе посадку, для отверстия — систему вала, т.к. оно представляет собой отверстие корпуса подшипника качения, которое по стандарту выполняется в этой системе. Для вала принимаю систему отверстия, т.к. условий для системы вала нет, а при прочих условиях системы отверстия экономичнее».
Выбор и обоснование основного отклонения
Если выбрана система отверстия, то для размера отверстия принимают основное отклонение (дня внутреннего кольца подшипника качения —
); если выбрана система вала, то для размера вала принимают основное отклонение
(для наружного кольца подшипника качения —
), как для основных отверстия и вала.
Примеры обоснования основных отклонений размеров основных отверстия и вала:
«Для размера отверстия принимаю основное отклонение , т.к. отверстие в системе отверстия является основным»;
«Для размера вала принимаю основное отклонение , т.к. вал в системе вала является основным».
Выбор основного отклонения размера посадочного отверстия или вала зависит от выбранного типа посадки и условий работы деталей рассматриваемого сопряжения.
Приняты следующие нормальные условия, общие для подвижного и неподвижного соединений:
- относительная длина соединения составляет 1-2 его поперечных размера;
- нагрузка спокойная (без существенных ударов, резких толчков, вибраций);
- температура деталей в работе сравнительно мало отличается от нормальной +20°С;
- температурное расширение отверстия и вала во время работы примерно одинаковое;
- детали металлические;
- соединение замкнутое.
Для подвижного соединения приняты следующие дополнительные нормальные условия:
- скорость относительного движения деталей мала;
- движение вращательное;
- количество опор не более двух;
- расстояние между опорами не более 2-3 поперечных размеров соединения;
- длина относительного поступательного движения (хода) детали не более 2-3 поперечных размеров соединения;
- относительное движение детали постоянное;
- общая длина вала не более 10 поперечных размеров соединения.
Для неподвижного соединения приняты следующие дополнительные нормальные условия:
- смещающая сила сравнительно мала или компенсирована специальным креплением;
- деталь не быстросъемная;
- условия, затрудняющие сборку — разборку соединения, отсутствуют.
Если условия работы деталей отличаются от нормальных, то нужно учитывать рекомендации таблицы 1.
Кроме нормальных и корректирующих условий необходимо учитывать следующее:
- условия могут взаимно дополнять или исключать друг друга, требуя увеличения или уменьшения зазора или натяга;
- при длительной эксплуатации в подвижном сопряжении зазор увеличивается, в неподвижном — степень неподвижности уменьшается, крепление ослабляется;
- если деталь по одной поверхности садится с натягом, то по другим поверхностям следует создавать зазоры, что улучшает центрирование деталей, снижает внутренние напряжения, облегчает сборку — разборку изделия.
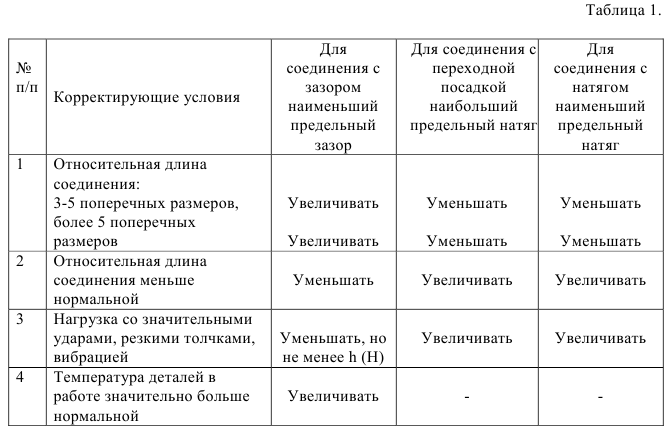
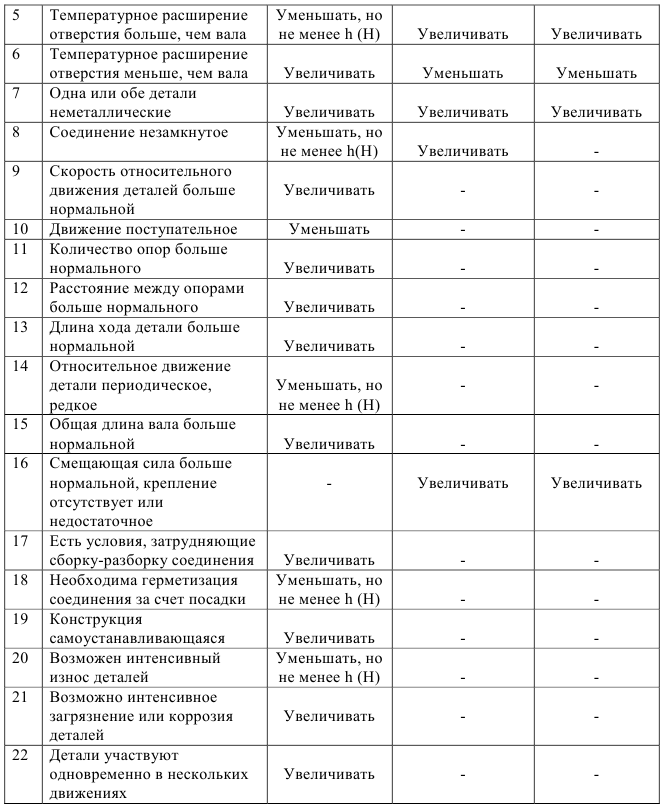
Итак, если выбрана посадка с зазором и все условия нормальные, то для размера посадочного вала (отверстия) принимают основное отклонение . Если некоторые условия отличаются от нормальных, то с учетом рекомендаций таблицы 1 подбирают соответствующее основное отклонение, увеличивающее или уменьшающее наименьший предельный зазор.
Примеры обоснования основного отклонения размера посадочного вала или отверстия:
«Для размера вала (отверстия) принимаю основное отклонение , т.к. соединение подвижное, условия нормальные»;
«Для размера вала (отверстия) принимаю основное отклонение , т.к. соединение подвижное, относительная длина соединения больше нормальной, остальные условия нормальные»;
«Для размера вала (отверстия) принимаю основное отклонение , т.к. соединение неподвижное, точного центрирования деталей не требуется, условия нормальные».
Если выбрана переходная посадка и все условия нормальные, то для размера посадочного вала (отверстия) принимают основное отклонение . Если некоторые условия отличаются от нормальных, то с учетом рекомендаций таблицы 1 подбирают соответствующее основное отклонение, увеличивающее или уменьшающее наибольший предельный натяг (зазор).
Примеры обоснования основного отклонения размера посадочного вала или отверстия:
«Для размера вала (отверстия) принимаю основное отклонение , т.к. соединение неподвижное, необходимо точное центрирование деталей за счет посадки условия нормальные»;
«Для размера вала (отверстия) принимаю основное отклонение , т.к. точного центрирования деталей не требуется, относительная длина соединения меньше нормальной, остальные условия нормальные».
Если выбрана посадка с натягом и все условия нормальные, то для размера посадочного вала (отверстия) принимают основное отклонение . Если некоторые условия отличаются от нормальных, то с учетом рекомендаций таблицы 1 подбирают соответствующее основное отклонение, увеличивающее или уменьшающее наименьший предельный натяг.
Предварительно выбранная посадка с натягом, при окончательном решении с учетом корректирующих условий, может быть заменена на переходную.
Примеры обоснования о сн о ви ого от клонен и я размера посадочного вала или отверстия:
«Для размера вала (отверстия) принимаю основное отклонение , т.к. соединение неподвижное, специальное крепление отсутствует, смещающие силы сравнительно велики, точного центрирования деталей не требуется, остальные условия нормальные»;
«Для размера вала (отверстия) принимаю основное отклонение , т.к. соединение неподвижное, специальное крепление отсутствует, смещающие силы средней величины, остальные условия нормальные».
В сопряжении с радиальным или радиально-упорным подшипником качения при нормальном режиме работы подшипника, как правило, можно пользоваться следующими рекомендациями (с учетом только основных факторов): для размера посадочного вала (отверстия), если кольцо подшипника испытывает циркуляционное нагружение, можно принять основное отклонение , когда подшипник шариковый; основное отклонение,
— когда роликовый; если кольцо испытывает местное нагружение —
; если подшипник упорный —
.
Примеры обоснования основного отклонения размера посадочного вала или отверстия:
«Для размера вала принимаю основное отклонение , т.к. задан нормальный режим работы подшипника, кольцо испытывает циркуляционное нагружение, подшипник радиальный шариковый »;
«Для размера отверстия принимаю основное отклонение , т.к. задан нормальный режим работы подшипника, кольцо испытывает местное нагружение, подшипник радиальный».
- Выбор и обоснование квалитета
Приняты следующие нормальные условия для обычного гладкого соединения:
- средняя точность изделия;
- влияние точности рассматриваемого размера детали (соединения) на точность узла или изделия в целом;
- обеспечение средней точности центрирования или направления деталей за счет посадки;
- обеспечение средней однородности посадки;
- нет необходимости создавать запас точности на износ деталей.
В заданиях нет изделий более высокой точности и нет необходимости в более точном центрировании (направлении) деталей и более однородной посадке.
Если соединение подвижное с вращательным движением или неподвижное, то говорят о центрировании, если подвижное с поступательным движением, то говорят о направлении деталей.
Как правило, для размеров отверстия по 8-й квалитег включительно рекомендуется принимать размер вала на один квалитег точнее размера отверстия.
Если условия нормальные, то для размера отверстия можно принять 7-й квалитет, для размера вала — 6-й квалитет. Если некоторые условия отличаются от нормальных, то нужно учитывать рекомендации таблицы 2.
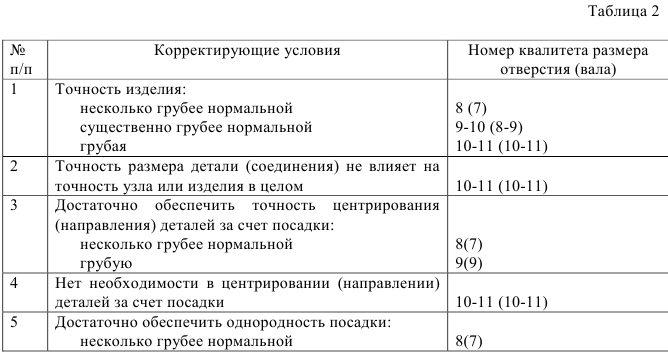
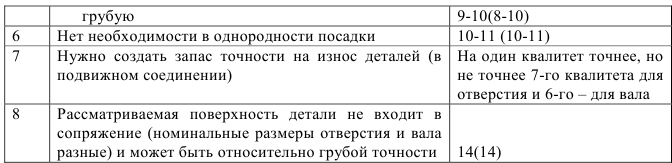
Для сопряжений с подшипниками качения принять:
- для узла металлообрабатывающего станка или приспособления к нему, от которого зависит точность обработки, а также для червячной передачи 6-й класс точности подшипника, для остальных — 0-й класс точности подшипника;
- при указанных условиях для размера вала под подшипник — 6-й квалитет, для размера отверстия цельного корпуса подшипника — 7-й квалитет, для отверстия разъемного корпуса — 8-й квалитет.
Примеры обоснования квалитета размера отверстия и вала:
«Для размера отверстия принимаю 7-й квалитет, для размера вала — 6-й квалитет, т.к. условия нормальные»;
«Для размера отверстия принимаю 8-й квалитет, для размера вала — 7-й квалитет, т.к. центрирование детали не требуется, достаточно обеспечить однородность посадки несколько грубее нормальной, остальные условия нормальные»;
«Для размеров отверстия и вала принимаю 14-й квалитет, т.к. изделие грубой точности, рассматриваемые поверхности не входят в сопряжение, центрирование деталей и однородности посадки не требуется»;
«Для размера вала принимаю 6-й квалитет, т.к. принят подшипник 0-го класса точности»;
«Для размера отверстия принимаю 7-й квалитет, т.к. принят подшипник 0-го класса точности и корпус цельный, а для размера вала — 11-й квалитет, т.к. точность размера вала не влияет на точность узла, центрирования деталей и однородности посадки не требуется, остальные условия нормальные» (речь идет о крышке в корпусе подшипника качения).
После выбора квалитета необходимо обратить внимание на следующие условия:
- в обоснованных случаях точность размеров отверстия и вала может отличаться на несколько квалитетов (если точность размеров отверстия и вала отличается более чем на один квалитет, то обосновать нужно каждый квалитет отдельно);
- предварительно выбранные поля допусков размеров нужно проверять на наличие их по справочнику;
- по возможности следует применять предпочтительные поля допусков (не в ушерб качеству и экономичности).
Выбор и обоснование допусков формы
Допуска формы поверхностей, как правило, устанавливают в зависимости от допуска размера:
- в пределах поля допуска размера рассматриваемого элемента (в этом случае допуски формы на чертеже не указываются);
- меньше допуска размера;
- больше допуска размера (этот случай в заданиях отсутствует).
Допуски формы устанавливают в пределах поля допуска размера, когда детали работают при скоростях и удельных нагрузках, смещающих силах и моментах, вибрациях и ударных нагрузках, температурных деформациях, не превышающих средних значений, и к деталям не предъявляются повышенные требования по форме.
Допуски формы устанавливают меньше допуска размера, когда к деталям предъявляются повышенные требования по точности центрирования, биению, герметичности или прочности сопряжения, равномерности и точности траектории движения, износостойкости, шуму.
При установлении определенного вида допуска формы меньше допуска размера числовое значение его, как правило, определяют по степени точности или по относительной геометрической точности формы (в зависимости от допуска размера).
В работе принять для размеров квалитетов 6, 7, 8, 9 соответственно степени точности 5, 6, 7, 8 при нормальной относительной геометрической точности (А) формы (допуск-формы составляет 60% допуска размера). Для размеров квалитетов грубее 9-го допуски формы принять в пределах ноля допуска размера.
Для посадочных поверхностей вала и корпуса подшипника качения установить допуск цилиндричности в зависимости от номинального размера и класса точности подшипника.
Примеры обоснования допусков формы отверстия и вала:
«Для отверстия и вала принимаю допуски формы в пределах полей допусков размеров, т.к. к ним не предъявляются повышенные требования по форме»;
«Для отверстия принимаю допуск цилиндричности по 6-й степени точности, т. к. принят 7-й квалитет размера, для вала — по 5-й степени точности, т.к. принят 6-й квалитет размера и к деталям предъявляются повышенные требования по форме»;
«Для вала принимаю допуск цилиндричности равным 3 мкм, т.к. подшипник принят 6-го класса точности, размер входит в интервал 10-J8 мм».
Выбор и обоснование норм шероховатости поверхности
Принять, что устанавливается наибольшее предельное значение среднего арифметического отклонения профиля шероховатости (), а другие нормы шероховатости не регламентируются.
Параметр , как правило, рекомендуется согласовывать с номинальным размером, квалитетом размера и процентным соотношением между допуском формы и допуском размера.
Для посадочных поверхностей вала и отверстия под подшипник устанавливают в зависимости от номинального размера и класса точности подшипника.
Примеры обоснования :
«Для отверстия принимаю =3,2 мкм, для вала —
=l,6 мкм, т.к. номинальные размеры входят в интервал 18-50 мм, для размера отверстия принят 7-й квалитет, а вала — 6-й квалитет, допуски формы приняты в пределах допусков размеров»;
«Для отверстия принимаю = l,6 мкм, для вала —
=0,8 мкм, т.к. номинальные размеры входят в интервал 18-50 мм, для размера отверстия принят 7-й квалитет, а вала — 6-й квалитет, допуски формы приняты в пределах 60% допусков размеров»;
«Для вала принимаю =0,63 мкм, т.к. принят 6-й класс точности подшипника, номинальный размер до 80 мм».
Выбор числовых значений предельных отклонений размеров, допусков формы, шероховатости поверхности
Числовые значения предельных отклонений размеров обычных гладких отверстий и валов выбирают в зависимости от интервала номинальных размеров и поля допуска размера по таблицам справочника (например, в [2] табл. 1.27 — 1.43, с. 90 — 157).
Числовые значении предельных отклонении размеров колец подшипников качения выбирают в зависимости от интервала номинальных размеров и класса точности подшипника (для d — средний внутренний диаметр внутреннего кольца, для D — средний наружный диаметр наружного кольца) по таблицам справочника (например, в [3] табл.4.82 — 4.86, с. 320 — 338).
Числовые значения допусков формы обычных гладких отверстий и валов выбирают в зависимости от интервалов номинальных размеров и степеней точности формы или относительной геометрической точности но таблицам справочника (например, в [2] табл. 2.11, с.414, табл. 2.13, с. 415, табл.2.18, с.427, табл.2.20, с.429).
Числовые значения допусков формы посадочных поверхностей валов и корпусов под подшипники качения выбирают в зависимости от интервалов номинальных размеров и класса точности подшипника по таблицам справочника (например, в [3] табл.4.93, с.378).
Числовые значения Ra обычных гладких отверстий и валов выбирают в зависимости от квалитета размера, процентного соотношения между допуском формы и размера и интервалов номинальных размеров по таблице справочника (например, в [2] табл.2.67, с.561).
Числовые значения Ra посадочных поверхностей валов и корпусов под подшипники качения выбирают в зависимости от класса точности подшипника и номинального размера таблице справочника (например, в [3] табл. 4.95, с. 384).
Возможно эта страница вам будет полезна:
Нормирование точности курсовая работа |
Указании но оформлению работы.
- Работа должна быть выполнена на бумаге формата А4.
- Листы работы должны быть сшиты, на лицевой стороне титульного листа следует указать: полное наименование вуза (Пермский национальный исследовательский политехнический университет), наименование кафедры (Металлорежущие станки и инструменты), дисциплины (для разных специальностей она называется по-разному), вид работы («Контрольная работа № _»; «Курсовая работа но дисциплине…»), условное обозначение учебной группы, фамилия и инициалы студента, фамилия и инициалы преподавателя, город и год выполнения работы. На титульном листе также следует указать наименование работы, номер и вариант задания.
- Последовательность изложения и оформления работы должны соответствовать требованиям данных метод, указаний.
- Изложение должно быть кратким, конкретным и логически последовательным.
- Работа должна быть выполнена аккуратно, текст и графический материал должны располагаться только на одной стороне листа, листы должны быть пронумерованы и иметь ноля.
- Текст следует набрать размером не меньше 14pt, эскизы могут быть выполнены карандашом по требованиям ЕСКД.
- Сдавая работу на проверку необходимо вложить в нее задание.
- Если работа возвращена на исправление, то указанные ошибки нужно аккуратно зачеркнуть, а исправления дать на свободной стороне смежного листа или на отдельных листах, вшитых за титульным листом. На первом листе исправлений дать заголовок «Исправления», для каждого исправления указать номер листа, к которому оно относится.
Пример решения задачи и оформлении работы
Сопряжение:
Принимаю посадку с зазором, т.к. сопряжение подвижное.
Принимаю систему отверстия, т.к. условий для системы вала нет, а при прочих условиях система отверстия экономичнее.
Для размера отверстия принимаю основное отклонение , т.к. отверстие в системе отверстия является основным.
Для размера вала принимаю основное отклонение , т.к. сопряжение подвижное, количество опор больше нормального, остальные условия нормальные.
Для размера отверстия принимаю 7-й квалитет, для вала — 6-й квалитет, т.к. нужно запас точности на износ деталей, остальные условия нормальные.
Для отверстия принимаю допуск цилиндричности по 6-й степени точности, т.к. принят 7-й квалитет, для вала 5-й степени точности, т.к. принят 6-й квалитет и к деталям предъявляются повышенные требования по форме поверхностей.
Для отверстия принимаю =l,6 мкм, для вала
=0,8 мкм, т.к. номинальные размеры входят в интервал 18-50 мм, для размера отверстия принят 7-й квалитет, а вала -6-й квалитет, допуски формы приняты в пределах 60% от допусков размеров.
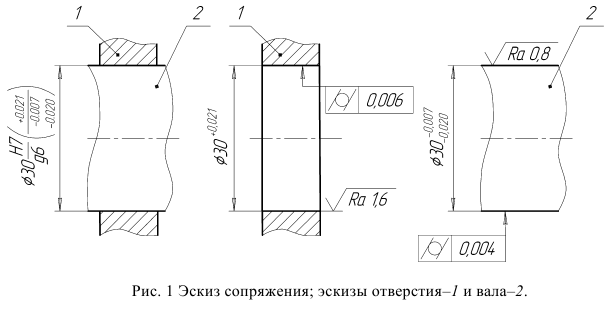
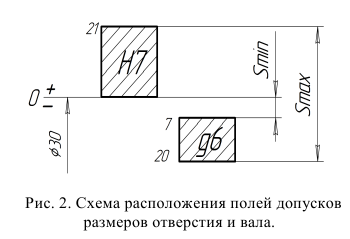
Расчет предельных зазоров и допуска посадки:
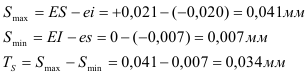
Проверка:

Контрольная работа №2 Расчет размерных цепей
Цели работы
- Закрепление знаний ио разделу «Размерный анализ»
- Приобретение практических навыков в расчетах размерных цепей.
Содержание и последовательность выполнения работы
Эта часть курсовой (контрольной задачи) работы выполняется в полном объеме в соответствии с последовательностью выполнения работы.
- В соответствии с вариантом задания выполнить схему размерной цепи в произвольном масштабе;
- Определить числовые значения предельных отклонений размеров составляющих звеньев, для которых поля допусков заданы условным обозначением (Из списка литературы [2] с. 90-113, 126-145, 154-157; [4] с. 79-100, 113-131, 140-142).
- Определить увеличивающие и уменьшающие звенья.
- Определить звенья-отверстия, — валы, — прочие.
- Внести необходимые данные в таблицу исходных данных.
- Выполнить проектный расчет цепи методом максимума-минимума способом одного квалитета (одного уровня точности). Номинальные размеры составляющих звеньев принять те, которые заданы для проверочного расчета (прим.: для проверочного и проектного расчетов предельные отклонения размеров заданы разные, т.е. одна задача не сводится к другой).
- Выполнить проверочный расчет цепи методом максимума-минимума.
- Выполнить проверочный расчет цени теоретико-вероятностным методом для закона нормального распределения.
Пояснения
- Увеличивающие и уменьшающие составляющие звенья определяются по схеме цепи. Для этого следует представить себе, что произойдет с размером замыкающего звена (увеличится или уменьшится), если размер рассматриваемого звена будет увеличиваться в сторону звена замыкающего. При этом следует считать, что размеры других составляющих звеньев (кроме рассматриваемого) не изменяется. Если с увеличением размера рассматриваемого составляющего звена, размер замыкающего звена будет увеличиваться, то рассматриваемое составляющее звено — увеличивающее. Если размер замыкающего звена будет уменьшаться, то рассматриваемое звено — уменьшающее.
- В данной работе при решении размерной цени теоретико-вероятностным методом по закону нормального распределения принять следующие условия:
- изделие будут изготавливать в условиях крупносерийного или массового производств на настроенных технологических комплексах;
- диапазоны рассеяния размеров (погрешностей) совпадут с нолями допусков размеров;
- центры группирования размеров (погрешностей) совпадут с серединами полей допусков размеров;
- 0,27% риска возможного равновероятностного выхода размера замыкающего звена за обе границы поля допуска.
Принятые обозначения
— номинальный размер замыкающего звена;
— номинальный размер
-го составляющего звена;
— порядковый номер составляющего звена;
— увеличивающее звено;
— уменьшающее звено;
— количество уменьшающих звеньев;
— количество увеличивающих звеньев;
— верхнее предельное отклонение размера звена;
— нижнее предельное отклонение размера звена;
— среднее отклонение размера звена (координата середины поля допуска);
— допуск размера звена;
— единица стандартного поля допуска размера звена;
— количество единица стандартного поля допуска размера звена (коэффициент точности).
Исходные данные (пример)
- Линейная сборочная конструкторская размерная цепь:
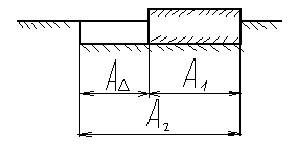
- Схема размерной цепи:
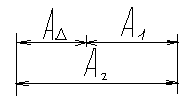
- Таблица исходных данных:
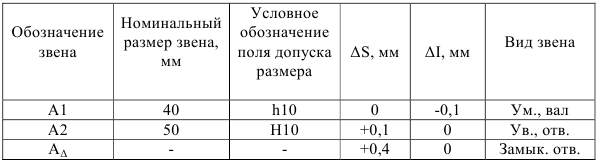
Проектный расчет цепи
- Определение номинального размера замыкающего звена.

- Определение допуска размера замыкающего звена:

- Определение количества единиц допуска для размеров составляющих звеньев:

где значения в зависимости от интервала номинальных размеров выбираются по таблице справочника (например, [3], с. 22, табл. 3.3).
- Определение номера квалитета для размеров составляющих звеньев в зависимости от количества единиц допуска по таблице справочника (например, [2] с. 52-55, табл. 1.8).
Для 11-го квалитета =100, для 12-го квалитета
=160 ед. допуска. Так как полученные 128 ед. допуска ближе к 11-му квалитету, то принимаем его. Если количество единиц допуска окажется ровно по середине между двумя квалитетами (например,
= 130 ед. допуска), то принимаем более грубый квалитет.
- Предварительное определение предельных размеров составляющих звеньев.
Так как звено А1 вал, а звено А2 — отверстие, то звено А1 рассматривается как-основной вал, а звено А2 как основное отверстие.
Тогда по [2] с. 52-55, табл. 1.8:

Если звено не представляет собой отверстие или вал (прочее), принимается со знаком «+» и равным половине допуска выбранного 6 квалитета, a
— со знаком «-» и равным половине допуска выбранного квалитета.
- Проверка выбранных предельных отклонений размеров составляющих звеньев:

что не удовлетворяет условию задачи (так как задано ).
- Проверка выбранных допусков размеров составляющих звеньев:

что меньше заданного (задано ).
- Отладка цепи.
Так как предварительно полученные и
не удовлетворяют условию задачи, то выбираем звено-компенсатор. Так как
получилось меньше заданного, то
следует увеличить (должно быть
). Если
нужно увеличить, то следует увеличить допуск размера прочего звена (если такое есть) или звена-отверстия (если такое есть), т.е. расширять допуски следует у технологически наиболее трудно получаемого звена. Если при отладке цепи возникает необходимость уменьшить допуск-размера составляющего звена, то уменьшая допуск звена-вала (если такое есть).
В данном случае следует увеличить допуск размера (отверстия).
Тогда принимаем и решаем уравнение относительно
:

Отсюда

Если оба предельных отклонения не удовлетворяют условию задачи, то принимаем и решаем два уравнения (относительно
и
).
- Проверка полученных предельных отклонений размеров составляющих звеньев:

что удовлетворяет условию задачи.
Ответ:

Проверочный расчет цепи методом максимума-минимума
- Определение номинального размера замыкающего звена:

- Определение верхнего отклонения предельного отклонения размера замыкающего звена:

- Определение нижнего отклонения предельного отклонения размера замыкающего звена:

- Определение допуска размера замыкающего звена:

- Проверка допуска размера замыкающего звена:

что удовлетворяет закономерности цепи.
- Определение среднего отклонения размера замыкающего звена:

Ответ:

Проверочный расчет цепи теоретико-вероятностным методом
- Определение номинального размера замыкающего звена:

- Определение средних отклонений размеров составляющих звеньев:
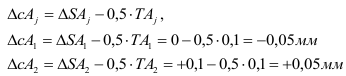
- Определение среднего отклонения размера замыкающего звена:

- Определение допуска размера замыкающего звена:

- Определение верхнего предельного отклонения размера замыкающего звена:

- Определение нижнего предельного отклонения размера замыкающего звена:

Ответ:
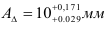