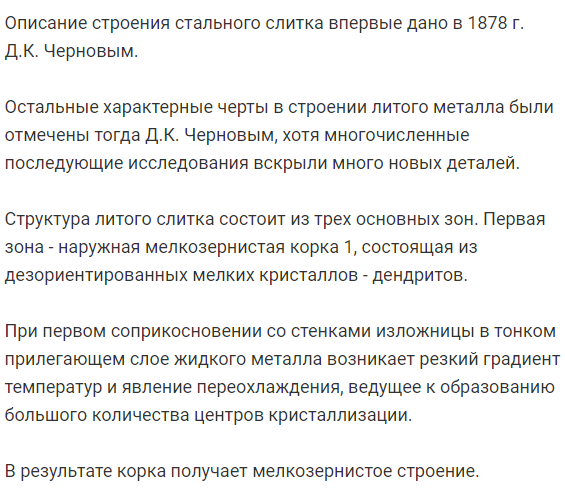
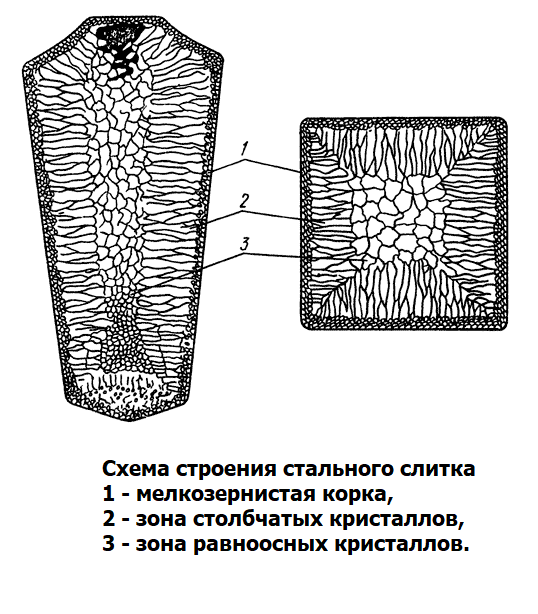
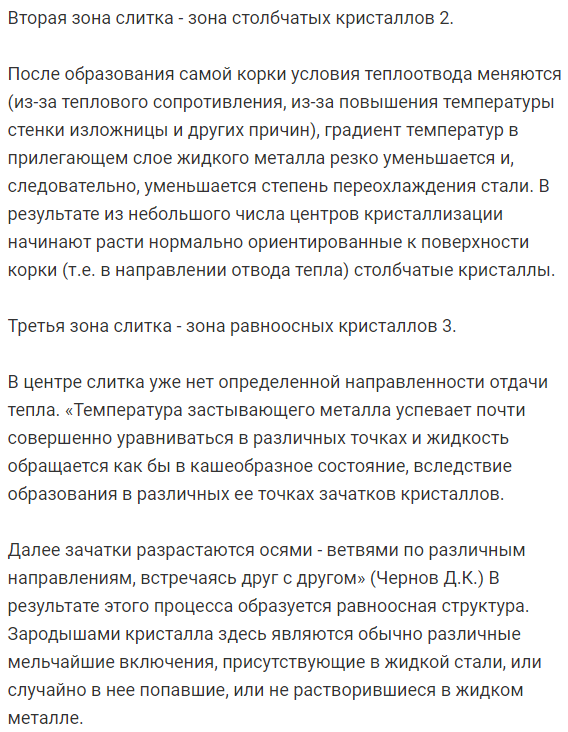
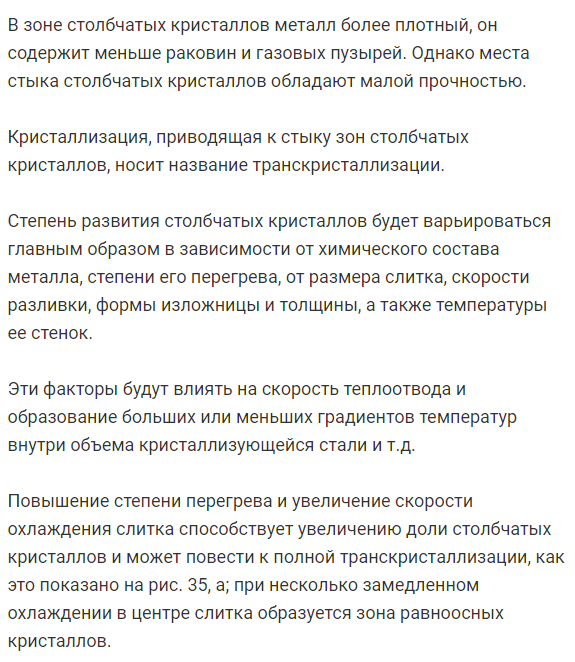
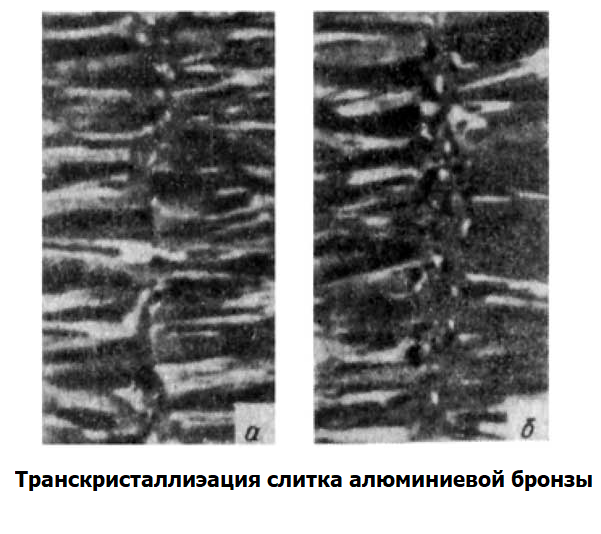
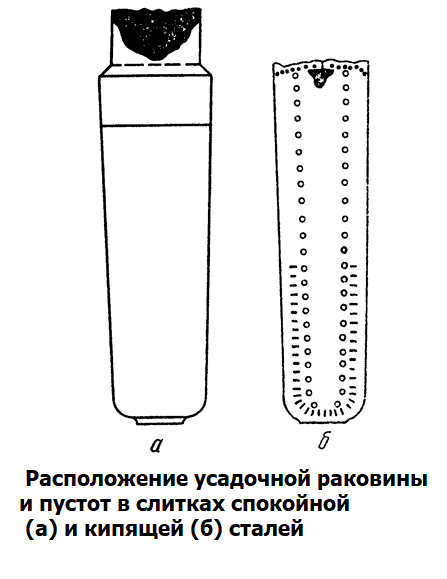
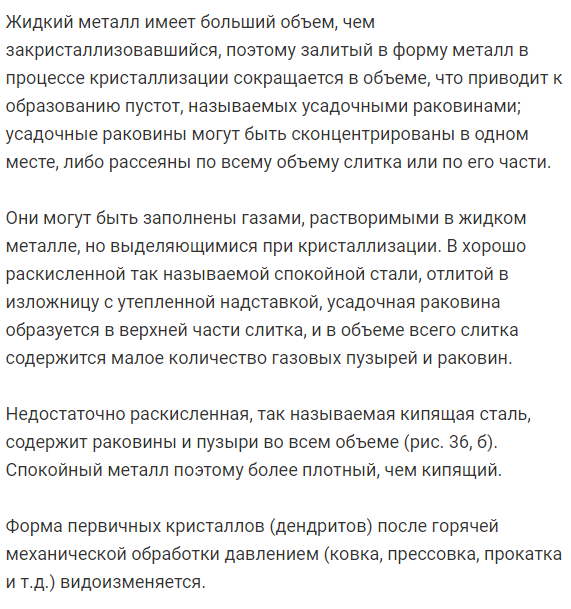
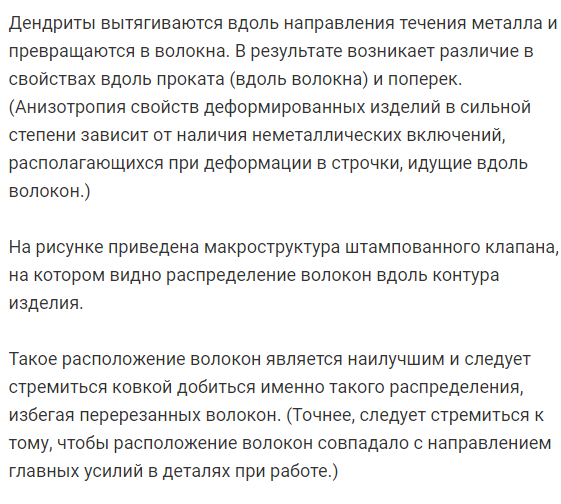
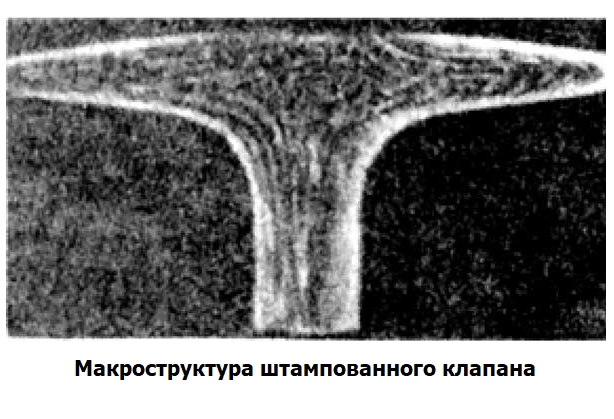
Описание структуры стального слитка было выполнено в 1878 году Д.К. Другой характерной чертой в структуре литого металла является Д.К. Чернов, многие последующие исследования выявили много новых деталей.
Структура литого слитка состоит из трех основных зон. Первая зона — это внешняя мелкозернистая кора 1, состоящая из мелких кристаллов без ориентационных дендритов.
Первый контакт со стенкой формы с тонким смежным слоем жидкого металла вызывает крутой температурный градиент и переохлаждение, что приводит к образованию многочисленных центров кристаллизации.
В результате кора имеет тонкую структуру.
- Второй зоной слитка является зона столбчатого кристалла 2.
После образования самой коры условия теплоотвода изменяются (из-за повышения температуры стенок кристаллизатора и теплового сопротивления по другим причинам), и градиент температуры в соседнем слое жидкого металла быстро уменьшается, что приводит к чрезмерному Степень охлаждения уменьшится. В результате столбчатые кристаллы, которые обычно ориентированы к поверхности коры (т.е. в направлении отвода тепла), начинают расти из небольшого числа центров кристаллизации.
- Третья зона слитка — зона 3 равноосного кристалла.
Больше нет определенного направления теплопередачи в центре слитка. «Температура затвердевающего металла практически одинакова в разных точках, и жидкость превращается в мутное состояние в результате образования кристаллического зародыша в разных точках.
Кроме того, в зачаточном росте осевые ветви в разных направлениях встречаются друг с другом »(Д. К. Чернов). Этот процесс приводит к равноосной структуре. Ядро кристалла здесь обычно представляет собой множество мелких включений, которые присутствуют в расплавленной стали, случайно попадают в нее или не растворяются в жидком металле.
В столбчатой зоне плотность металла высока, а количество оболочек и пузырьков мало. Однако прочность соединения столбчатых кристаллов низкая.
Кристаллизация, которая приводит к соединению столбчатых кристаллических зон, называется транскристаллизацией.
Степень образования столбчатых кристаллов зависит, прежде всего, от химического состава металла, степени перегрева, размера слитка, скорости разливки, формы и толщины кристаллизатора и температуры его стенок.
Эти факторы влияют на скорость теплоотвода и образование больших или меньших температурных градиентов внутри кристаллизующейся стали.
Увеличение перегрева слитка и увеличение скорости охлаждения может увеличить долю столбчатых кристаллов и вызвать полную рекристаллизацию, как показано на рисунках а и а. Когда охлаждение происходит медленно, в центре слитка образуется равноосная кристаллическая зона.
Поскольку жидкие металлы больше по объему, чем кристаллизованные, объем расплавленного металла уменьшается в процессе кристаллизации, образуя пустоты, называемые усадочными раковинами. Термоусадочные оболочки могут быть сосредоточены в одном месте или разбросаны по всему слитку или частично.
Они растворимы в жидких металлах, но могут быть заполнены газами, выделяющимися при кристаллизации. Так называемая мягкая сталь, которая полностью деоксигенирована, отливается в форму с подогретым удлинением, образуя усадочную оболочку сверху слитка, и небольшое количество пузырьков и раковин входит в общий объем слитка.
- Так называемая вареная сталь с недостаточным раскислением содержит оболочки и пузырьки во всем объеме (рис. 36, б). Поэтому мягкие металлы более плотные, чем кипящие.
- Форма первичного кристалла (дендритного кристалла) после горячей обработки давлением (ковка, прессование, прокатка и т. Д.) Изменяется.
Дендриты врастают в волокна вдоль направления потока металла. В результате существуют различия в свойствах вдоль и по всему прокату (вдоль волокна). (Анизотропия свойств деформированного продукта сильно зависит от наличия неметаллических включений, расположенных во время деформации на линии, проходящей вдоль волокна.)
На этом рисунке показана макроструктура штампованного клапана, которая показывает распределение волокон по контуру изделия.
Такое размещение волокон является оптимальным, и ковка должна стремиться к достижению именно такого распределения, избегая срезанных волокон. (Точнее, должны быть предприняты усилия для обеспечения того, чтобы размещение волокна в работе соответствовало направлению основного усилия деталей.)
Смотрите также:
Примеры решения задач по материаловедению